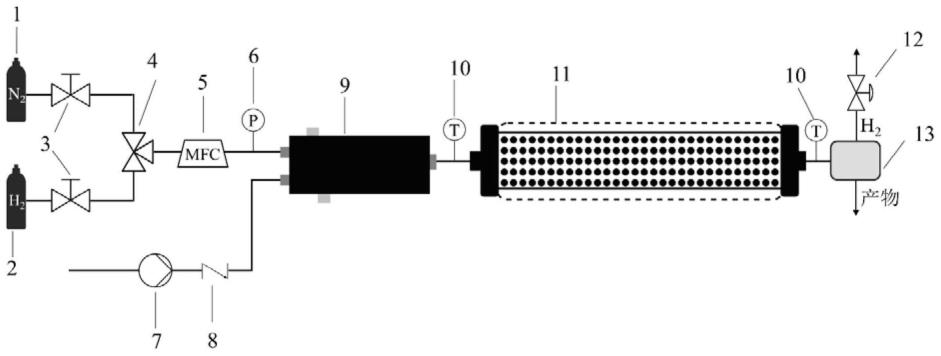
1.本发明涉及2,4-二氨基苯甲醚生产制备领域,具体地说就是一种基于微填充床的连续催化加氢制备2,4-二氨基苯甲醚的方法及装置。
背景技术:
2.2,4-二氨基苯甲醚是一种重要的有机合成中间体,其广泛的应用于染颜料、医药、农药等精细化工领域。
3.2,4-二氨基苯甲醚通过2,4-二硝基苯甲醚加氢还原制备获得。2,4-二硝基苯甲醚含有两个不饱和硝基基团,由于第一硝基(吸电子基团)转化为胺基(给电子基团)会减少环中的电子缺陷,阻碍第二硝基的进一步还原,从而很难实现完全转化为2,4-二氨基苯甲醚。传统工业生产2,4-二氨基苯甲醚的技术为:以雷尼镍为催化剂,氢气作为还原剂,在间歇高压釜中进行加氢还原反应得到产品。但是雷尼镍使用条件比较苛刻,危险性高,同时反应过程会产生一定量的废水和固废,对环境污染严重。赵晓明等采用pd/c 催化剂实现了2,4-二硝基苯甲醚的加氢反应,但该工艺反应时间长,催化剂套用次数少。
4.很多研究表明对于芳香族二硝基化合物在间歇反应器中仅使用催化剂改性的方法很难取得满意的结果。专利cn108218728a公开了一种2,4-二氨基苯甲醚制备方法,该方法以pd/al2o3为催化剂,进行釜式串联连续加氢,并采用膜过滤分离催化剂,具有较高的生产效率和产品质量,但反应过程需要不断补加催化剂,还需繁琐耗时的沉降过滤操作。专利 cn111302949a公开了一种通过微反应技术制备苯二胺的工艺,将待还原的硝基芳烃、溶剂、催化剂和氢气经计量后连续送入加氢微反应器中,进行加氢还原反应,有较好的收率。但催化剂以悬浮液形式进入微反应器中易发生沉降以及堵塞管路且需要繁杂的催化剂分离回收操作。专利 cn113402395a提供了一种基于固定床的微反应器用于间二硝基苯加氢,但间苯二胺收率较低。而且气液物料进入微填充床管路后才被加热,需要一定时间达到反应温度。
技术实现要素:
5.针对上述技术问题以及本领域存在的不足之处,本发明旨在提供一种生产效率高、完全性高、环境友好的基于微填充床的连续催化加氢制备2,4
‑ꢀ
二氨基苯甲醚的方法及装置。
6.为实现上述目的,本发明采用技术方案为:
7.一种连续催化加氢制备2,4-二氨基苯甲醚的装置,包括氮气输入管路、氢气输入管路、三通阀(4)、液体物料输入管路、微混合换热器(9)、微填充床反应器(11)和气液分离器(13),其中微混合换热器(9)设有气体物料入口(901)、液体物料入口(902)和气液混合物出口(905),且所述氮气输入管路、氢气输入管路、气体物料入口(901)分别与所述三通阀 (4)上对应的端口连接,所述液体物料入口(902)与液体物料输入管路连接,所述气液混合物出口(905)、微填充床反应器(11)和气液分离器 (13)通过管路依次串联;2,4-二硝基苯
甲醚溶于有机溶剂中制备成液体物料并经所述液体物料输入管路输入,所述微填充床反应器(11)内部设有催化剂腔和换热介质腔,且所述换热介质腔环绕所述催化剂腔设置,在所述催化剂腔内设有pd(oh)2/c催化剂。
8.所述微混合换热器(9)内部设有混合通道(906)和设于所述混合通道(906)周围的换热介质,所述气体物料入口(901)和液体物料入口(902) 均与所述混合通道(906)的输入端连通,所述混合通道(906)的输出端与所述气液混合物出口(905)连通。
9.所述微混合换热器(9)内的混合通道(906)包括第一混合段和第二混合段,其中第一混合段包括交错设置的分流单元(9061)和汇聚单元 (9062),所述第二混合段内交错设有第一分流块(9064)和第二分流块 (9063),且所述第二分流块(9063)大于第一分流块(9064)。
10.所述微混合换热器(9)上设有第一换热介质入口(903)和第一换热介质出口(904),且所述第一换热介质入口(903)和第一换热介质出口(904) 均与所述微混合换热器(9)内承装换热介质的腔体连通。
11.所述微填充床反应器(11)一端设有反应器入口(1101),另一端设有反应器出口(1106),所述催化剂腔的第一端部与所述反应器入口(1101) 连接,且所述第一端部内设有第一筛板(1102),所述催化剂腔的第二端部与所述反应器出口(1106)连接,且所述第二端部内设有第二筛板(1105)。
12.所述微填充床反应器(11)上设有第二换热介质入口(1103)和第二换热介质出口(1104),且所述第二换热介质入口(1103)和第二换热介质出口(1104)均与所述换热介质腔连通。
13.所述三通阀(4)与微混合换热器(9)之间的连接管路上设有气体质量流量控制器(5)和压力表(6),所述液体物料输入管路上设有高压泵(7) 和单向阀(8),所述气液分离器(13)上设有一背压阀(12),所述微混合换热器(9)与微填充床反应器(11)之间的管路上以及所述微填充床反应器(11)与气液分离器(13)之间的管路上均设有温度计(10)。
14.一种利用所述装置连续催化加氢制备2,4-二氨基苯甲醚的方法,将催化剂pd(oh)2/c填充于权利要求1所述装置的微填充床反应器中;对装置内通过氮气置换其中的空气,而后添加反应物料,在氮气存在下反应物料与氢气在25-125℃,压力为1.0-3.0mpa下反应制备获得2,4-二氨基苯甲醚。
15.所述反应物料为2,4-二硝基苯甲醚溶于有机溶剂,其中,反应物料中 2,4-二硝基苯甲醚终浓度为0.2-0.6mol/l;所述有机溶剂为四氢呋喃或乙酸乙酯;
16.所述pd(oh)2/c催化剂中pd(oh)2占比为7%,载体为微纳米级球形活性炭,平均粒径0.6mm,催化剂平均粒径为600nm,催化剂比表面积不小于800m2/g。
17.所述反应物料按流量为0.4-1.6ml/min的速度加入至反应器内;氢气按流量为40-70ml/min的速度加入至反应器内。
18.本发明的优点与积极效果:
19.1.本发明装置采用微填充床反应器,较于常规釜式反应器,具有更大的气液固三相接触面积以及更高的传热传质能力,能更精确的控制反应过程,并缩短反应周期。
20.2.本发明装置采用微混合换热器,同时具备气液高效混合能力和高效预热能力。高效气液混合能物料气液分布均匀并避免后续由于物料混合不均匀导致的局部过热,高效
预热使得气液混合物料快速达到所需温度。
21.3.本发明采用负载在微纳米级球形活性炭颗粒上的pd(oh)2/c催化剂,催化剂活性高、性能稳定,加氢反应选择性高,该方法应用于2,4-二硝基苯甲醚加氢,转化率为100%,选择性均大于97%,最佳可达99.53%。
22.4.本发明工艺流程简单,催化剂固定于微填充床反应器中,后续无需催化剂分离操作。实现了连续化加氢,提高生产效率,降低劳动强度。反应过程无三废产生,有利于资源节约和环境保护。
附图说明
23.图1为本发明的结构示意图,
24.图2为图1中微混合换热器的外观示意图,
25.图3为图2中微混合换热器的内部结构示意图,
26.图4为图1中微填充床反应器的外观示意图,
27.图5为图4中微填充床反应器的内部结构示意图。
28.其中,1为高压氮气瓶,2为高压氢气瓶,3为气路控制球阀,4为三通阀,5为气体质量流量控制器,6为压力表,7为高压泵,8为单向阀,9 为微混合换热器,901为气体物料入口,902为液体物料入口,903为第一换热介质入口,904为第一换热介质出口,905为气液混合物出口,906为混合通道,9061为分流单元,9062为汇聚单元,9063为第二分流块,9064 为第一分流块,907为连通通道,10为温度计,11为微填充床反应器,1101 为反应器入口,1102为第一筛板,1103为第二换热介质入口,1104为第二换热介质出口,1105为第二筛板,1106为反应器出口,12为背压阀,13 为气液分离器。
29.图6为本发明实施例提供的催化剂电镜图。
具体实施方式
30.下面结合附图对本发明作进一步详述。
31.实施例1
32.如图1~5所示,本发明包括氮气输入管路、氢气输入管路、三通阀4、液体物料输入管路、微混合换热器9、微填充床反应器11和气液分离器13,其中如图2~3所示,所述微混合换热器9设有气体物料入口901、液体物料入口902和气液混合物出口905,所述微混合换热器9内部设有混合通道906和填充于所述混合通道906周围的换热介质,所述气体物料入口901和液体物料入口902均与所述混合通道906的输入端连通,所述混合通道906的输出端与所述气液混合物出口905连通,如图1所示,所述氮气输入管路、氢气输入管路、气体物料入口901分别与所述三通阀4上对应的端口连接,所述液体物料入口902与所述液体物料输入管路连接,所述气液混合物出口905、微填充床反应器11和气液分离器13通过管路依次串联。
33.如图3所示,所述微混合换热器9内的混合通道906包括第一混合段和第二混合段,其中第一混合段包括交错设置的分流单元9061和汇聚单元 9062,本实施例中,所述分流单元9061包括两条呈菱形布置的分流通道,物料流入分流单元9061后分成两股并沿着不同的分流通道流动,然后再重新汇聚流出进入下一个汇聚单元9062的单一通道中,从而实现物
料的不断分流、汇聚,进而实现物料混合。由于第一混合段为液体物料和气体物料的初步混合,因此本发明通过交错设置的分流单元9061和汇聚单元 9062实现两种物料较大幅度的分流和汇聚,保证混合充分。
34.如图3所示,所述第二混合段内交错设有第一分流块9064和第二分流块9063,本实施例中,所述第一分流块9064和第二分流块9063均呈圆形,且所述第二分流块9063直径大于第一分流块9064直径,物料在第二混合段流动时经过第一分流块9064和第二分流块9063时,物料依次由第一分流块9064两侧与第二混合段管壁之间的空隙以及第二分流块9063两侧与第二混合段管壁之间的空隙流过,从而实现物料的不断分流、汇聚,进而实现物料混合。由于物料经过第一混合段充分混合后进入第二混合段中,因此本发明利用直径不同的第一分流块9064和第二分流块9063实现物料相对较小幅度同时幅度还有所变化的分流汇聚,以保证物料在第二混合段内平稳混合以及充分换热。
35.如图3所示,所述微混合换热器9内设有连通通道907,且所述气体物料入口901和液体物料入口902分别通过不同的连通通道907与所述混合通道906输入端连通,所述连通通道907置于所述换热介质中。
36.如图2~3所示,所述微混合换热器9上设有第一换热介质入口903和第一换热介质出口904,且所述第一换热介质入口903和第一换热介质出口 904均与所述微混合换热器9内承装换热介质的腔体连通。本实施例中,所述换热介质为高温水。
37.如图4~5所示,所述微填充床反应器11内部设有催化剂腔,所述催化剂腔内设有pd(oh)2/c催化剂,所述pd(oh)2/c催化剂中,pd(oh)2占比为7%,载体为球形活性炭,平均粒径0.6nm,催化剂比表面积为712.3 m2/g。
38.如图4~5所示,所述微填充床反应器11一端设有反应器入口1101,另一端设有反应器出口1106,所述催化剂腔的第一端部与所述反应器入口 1101连接,且所述第一端部内设有第一筛板1102,所述催化剂腔的第二端部与所述反应器出口1106连接,且所述第二端部内设有第二筛板1105,所述第一筛板1102和第二筛板1105用于避免催化剂流出。如图1所示,所述反应器入口1101通过管路与微混合换热器9的气液混合物出口905连通,所述反应器出口1106与所述气液分离器13连通。
39.如图4~5所示,所述微填充床反应器11内设有换热介质腔,且所述换热介质腔环绕所述催化剂腔设置,所述微填充床反应器11上设有第二换热介质入口1103和第二换热介质出口1104,且所述第二换热介质入口1103 和第二换热介质出口1104均与所述换热介质腔连通。
40.如图1所示,所述氮气输入管路输入端与高压氮气瓶1连接、输出端与所述三通阀4对应端口连接,所述氢气输入管路输入端与高压氢气瓶2 连接、输出端与所述三通阀4对应端口连接,所述氮气输入管路和氢气输入管路上均设有气路控制球阀3。
41.如图1所示,所述三通阀4与微混合换热器9之间的连接管路上设有气体质量流量控制器5和压力表6,所述气体质量流量控制器5和压力表6 用于控制输入微混合换热器9气体物料的流量和压力,所述气体质量流量控制器5和压力表6均为本领域公知技术且为市购产品。
42.如图1所示,所述液体物料输入管路上设有高压泵7和单向阀8,其中高压泵7用于将液体物料泵入所述微混合换热器9中,所述高压泵7和单向阀8均为本领域公知技术且为
市购产品,本实施例中将2,4-二硝基苯甲醚溶于有机溶剂制备成液体物料,所述有机溶剂可采用四氢呋喃或乙酸乙酯。
43.如图1所示,所述微混合换热器9与微填充床反应器11之间的管路上以及所述微填充床反应器11与气液分离器13之间的管路上均设有温度计 10用于检测输入或输出物料的温度,所述温度计10为本领域公知技术且为市购产品。
44.如图1所示,所述气液分离器13上设有一背压阀12,所述背压阀12 为本领域公知技术且为市购产品。
45.实施例2:
46.步骤一:利用上述实施例记载装置,pd(oh)2/c催化剂填充于微填充床反应器中,催化剂填充量为1g,填充至管路中部,其余用空白载体(微纳米级球形活性炭)填充。
47.所述催化剂pd(oh)2/c经沉积-沉淀法制备获得,其中,pd(oh)2/c催化剂中pd(oh)2占比为7%,载体为微纳米级球形活性炭,平均粒径600nm,催化剂比表面积为712.3m2/g(参见图6)。
48.步骤二:随后常压下开启氮气输入管路,设置氮气流量为100ml/min置换3min,利用氮气将管路内的空气吹扫排出,并使催化剂在氮气氛围下保护,并检验系统密封性。
49.步骤三:将2,4-二硝基苯甲醚溶解在乙酸乙酯中配成浓度为0.2mol/l的反应溶液。
50.步骤四:打开冷热循环一体机设定反应温度为60℃。
51.步骤五:设置背压阀压力值为2.0mpa,开启氢气输入管路,打开氢气阀门,并设置气体质量流量控制器的流量参数为50ml/min。
52.步骤六:设定高压泵流量0.5ml/min,当冷热循环一体机达到设定温度 60℃时开启高压泵,将步骤三中制备的液体物料注入反应系统。
53.步骤七:待系统稳定后,从气液分离器液体出口收集样品。
54.反应结束后用甲醇冲洗催化剂及反应器,再用氮气吹扫排出甲醇,在氮气氛围下保护催化剂。本实施例反应产物通过气相色谱分析:反应转化率为100%,选择性为:97.62%。
55.实施例3:
56.与实施例2不同之处在于:
57.步骤一:利用上述实施例记载装置,pd(oh)2/c催化剂填充于微填充床反应器中,催化剂填充量为1g,填充至管路中部,其余用空白载体(微纳米级球形活性炭)填充。
58.步骤二:随后常压下开启氮气输入管路,设置氮气流量为100ml/min置换3min,利用氮气将管路内的空气吹扫排出,并使催化剂在氮气氛围下保护,并检验系统密封性。
59.步骤三:将2,4-二硝基苯甲醚溶解在四氢呋喃中配成浓度为0.2mol/l的反应溶液。
60.步骤四:打开冷热循环一体机设定反应温度为60℃。
61.步骤五:设置背压阀压力值为2mpa,开启氢气输入管路,打开氢气阀门,并设置气体质量流量控制器的流量参数为96ml/min。
62.步骤六:设定高压泵流量为1.6ml/min,当冷热循环一体机达到设定温度 60℃时开启高压泵,将步骤三中制备的液体物料注入反应系统。
63.步骤七:待系统稳定后,从气液分离器液体出口收集样品。
64.反应结束后用甲醇冲洗催化剂及反应器,再用氮气吹扫排出甲醇,在氮气氛围下保护催化剂。本实施例反应产物通过气相色谱分析:反应转化率为100%,选择性为:98.98%。
65.实施例4:
66.与实施例2不同之处在于:
67.步骤一:利用上述实施例记载装置,pd(oh)2/c催化剂填充于微填充床反应器中,催化剂填充量为0.5g,填充至管路中部,其余用空白载体(微纳米级球形活性炭)填充。
68.步骤二:随后常压下开启氮气输入管路,设置氮气流量为100ml/min 置换3min,利用氮气将管路内的空气吹扫排出,并使催化剂在氮气氛围下保护,并检验系统密封性。
69.步骤三:将2,4-二硝基苯甲醚溶解在四氢呋喃中配成浓度为0.6mol/l的反应溶液。
70.步骤四:打开冷热循环一体机设定反应温度为℃。
71.步骤五:设置背压阀压力值为1.0mpa,开启氢气输入管路,打开氢气阀门,并设置气体质量流量控制器的流量参数为60ml/min。
72.步骤六:设定高压泵流量为1.2ml/min,当冷热循环一体机达到设定温度 55℃时开启高压泵,将步骤三中制备的液体物料注入反应系统。
73.步骤七:待系统稳定后,从气液分离器液体出口收集样品。
74.反应结束后用甲醇冲洗催化剂及反应器,再用氮气吹扫排出甲醇,在氮气氛围下保护催化剂。本实施例反应产物通过气相色谱分析:反应转化率为100%,选择性为:98.16%。
75.实施例5:
76.与实施例2不同之处在于:
77.步骤一:利用上述实施例记载装置,pd(oh)2/c催化剂填充于微填充床反应器中,催化剂填充量为1.0g,填充至管路中部,其余用空白载体(微纳米级球形活性炭)填充。
78.步骤二:随后常压下开启氮气输入管路,设置氮气流量为100ml/min 置换3min,利用氮气将管路内的空气吹扫排出,并使催化剂在氮气氛围下保护,并检验系统密封性。
79.步骤三:将2,4-二硝基苯甲醚溶解在四氢呋喃中配成浓度为0.2mol/l的反应溶液。
80.步骤四:打开冷热循环一体机设定反应温度为55℃。
81.步骤五:设置背压阀压力值为2mpa,开启氢气输入管路,打开氢气阀门,并设置气体质量流量控制器的流量参数为60ml/min。
82.步骤六:设定高压泵流量为1ml/min,当冷热循环一体机达到设定温度 55℃时开启高压泵,将步骤三中制备的液体物料注入反应系统。
83.步骤七:待系统稳定后,从气液分离器液体出口收集样品。
84.反应结束后用甲醇冲洗催化剂及反应器,再用氮气吹扫排出甲醇,在氮气氛围下保护催化剂。本实施例反应产物通过气相色谱分析:反应转化率为100%,选择性为:99.53%。
85.实施例6:
86.与实施例2不同之处在于:
87.步骤一:利用上述实施例记载装置,pd(oh)2/c催化剂填充于微填充床反应器中,催化剂填充量为1.0g,填充至管路中部,其余用空白载体(微纳米级球形活性炭)填充。
88.步骤二:随后常压下开启氮气输入管路,利用氮气将管路内的空气吹扫排出,并使催化剂在氮气氛围下保护,并检验系统密封性。
89.步骤三:将2,4-二硝基苯甲醚溶解在四氢呋喃中配成浓度为0.2mol/l的反应溶液。
90.步骤四:打开冷热循环一体机设定反应温度为55℃。
91.步骤五:设置背压阀压力值为3mpa,开启氢气输入管路,打开氢气阀门,并设置气体质量流量控制器的流量参数为60ml/min。
92.步骤六:设定高压泵流量为1ml/min,当冷热循环一体机达到设定温度 55℃时开启高压泵,将步骤三中制备的液体物料注入反应系统。
93.步骤七:待系统稳定后,从气液分离器液体出口收集样品。
94.反应结束后用甲醇冲洗催化剂及反应器,再用氮气吹扫排出甲醇,在氮气氛围下保护催化剂。本实施例反应产物通过气相色谱分析:反应转化率为100%,选择性为:98.07%。
再多了解一些
本文用于创业者技术爱好者查询,仅供学习研究,如用于商业用途,请联系技术所有人。