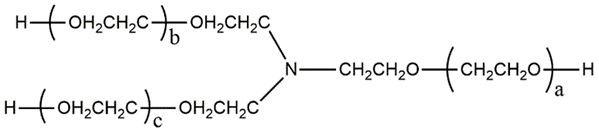
一种固化剂组合物及其应用
1.本技术要求申请号为2021115544643专利申请的优先权(在先申请的申请日为2021年12月17日,发明名称为一种胶黏剂及其应用)。
技术领域
2.本发明涉及胶黏剂技术领域,尤其涉及一种固化剂组合物及其应用。
背景技术:
3.目前常用的人造板用合成胶黏剂为以甲醛为基础的胶黏剂,包括以脲醛树脂、酚醛树脂和三聚氰胺-甲醛树脂等胶黏剂为代表的“三醛胶”。这三类胶黏剂均采用甲醛为合成原料,所述胶黏剂得到的胶接制品在生产和使用过程中都有甲醛逸出,甲醛被视为室内空气污染的主要源头之一,污染周期长,而且难以根本去除。
4.出于环境因素的考虑,无醛胶黏剂近年来得到了越来越广泛的应用,胶黏剂中的固化剂是重要的组分。
5.cn111154069a公开了一种聚氨酯固化剂、水性聚氨酯、涂料及其制备方法和应用。其公开的聚氨酯固化剂主要由以下质量份的组分制备而成:异氰酸酯三聚体95份~110份、亲水单体1份~10份、以及第一中和剂0~2份。其公开的聚氨酯固化剂通过异氰酸酯三聚体、亲水单体以及第一中和剂的配比,将固化剂中的亲水基团控制在合适的范围,避免因大量亲水基团的引入而降低水性聚氨酯产品的耐水性能,很好地兼顾了亲水基团的数量、耐水性能以及交联性能三者之间的平衡。通过其公开的聚氨酯固化剂与水性聚氨酯配合制得的涂料具有硬度高、耐水性和耐腐蚀性良好等优点,并且在使用过程中,涂料能够在常温下就完成固化成型,不需要进行高温烘烤处理。
6.cn112625538a公开了一种用于双组份美缝剂的环氧树脂固化剂及其制备方法。其公开的用于双组份美缝剂的环氧树脂固化剂包括下述重量份的组分:环氧树脂100份,羟基胺40-60份,脂肪族多胺25-40份,酚类3-8份。
7.目前的胶黏剂用于无醛添加人造板,有许多问题,如固化速率慢、生产无醛添加人造板时易出现容易崩边,贴面后易龟裂的现象。
8.以无醛的异氰酸酯胶黏剂为例,除不含甲醛外,异氰酸酯胶黏剂还有许多优点,如胶接强度高,胶黏剂用量低,对木质秸秆材料含水率要求不严格、优异的板材物理性能等。
9.然而,在人造板中使用异氰酸酯作为胶黏剂也具有劣势。热压制板过程涉及复杂的能量变化,包含传热传质过程。具体表现为表层优先受热,单元内的水分受热变成水蒸汽,携带热量向芯层传递。随着时间的延长,芯层温度上升,达到胶黏剂的固化温度后,在压力的作用下,固化成型。由于木质材料是热的不良导体,热压过程中主要的热量传递为水汽携带。生产同样密度的板材情况下,由于木质原料的用量不同,采用异氰酸酯胶黏剂的板坯传热更慢。一般情况下,同样铺装含水率时,采用三醛胶板坯芯层温度升至100℃的时间较采用异氰酸酯胶的时间短5-10s。制约热压效率主要因素除了芯层升温速度,胶黏剂固化速度也是一个重要因素,异氰酸酯胶黏剂在100℃时固化速度相较脲醛树脂慢30s左右。
10.因此,综合上述两点,采用异氰酸酯胶黏剂的刨花板的热压效率相较采用脲醛树脂的刨花板下降35-50%。这个问题会大大影响生产工厂的生产效率和效益,严重阻碍了采用异氰酸酯胶黏剂生产无醛添加人造板行业的发展和扩大。
11.要解决该问题,通过调整铺装含水率梯度和提高热压温度能够有效提高芯层传热速度,一定程度上提高热压效率。但如何提高异氰酸酯胶黏剂固化速度仍是制约该类板材生产效率的主要问题。
12.cn1196374a公开了一种木质纤维素压制板用粘合剂的制备方法,其公开的方法包含将由(a)有机异氰酸酯化合物组成的第一种液流和由(b)一种反应性乳化剂与(c)一种乳化介质以及选择性的脱模剂组成的第二种液流,在高压40-300kg/cm2下喷射到混合腔中,然后将它们混合。由于其公开的粘合剂在热压时具有优良脱离性,该粘合剂适合工业生产高质量且廉价的具有优良生产率的木质纤维素压制板。该方案b剂和c剂主要合成乳化剂,提前与a剂发生反应,生成可乳化异氰酸酯胶黏剂,之后与水混合,以提高施胶均匀性,但是此方案会导致胶黏剂体系预固化严重,板材未成形时胶黏剂有效成分已大量反应,会严重影响板材生产效率。
13.同时,采用异氰酸酯胶黏剂生产刨花板时,由于胶黏剂本身用量低,且固化后硬度高等问题,导致采用异氰酸酯胶黏剂生产无醛添加人造板时易出现容易崩边,贴面后易龟裂的现象。
14.综上,急需开发一种固化剂组合物,其形成的胶黏剂用于生产无醛添加人造板时,兼具固化速度快、不崩边,贴面后不易龟裂的特点。
技术实现要素:
15.针对现有技术的不足,本发明的目的在于提供一种固化剂组合物及其应用,所述固化剂组合物形成的胶黏剂用于生产无醛添加人造板时,兼具固化速度快、不崩边,贴面后不易龟裂的特点。
16.为达此目的,本发明采用以下技术方案:第一方面,本发明提供一种固化剂组合物,所述固化剂组合物包括三乙醇胺、二乙醇胺、一乙醇胺和三乙醇胺衍生物的组合。
17.本发明中,所述固化剂组合物包括三种醇胺和一种醇胺的衍生物,在实际应用中,能够形成梯度催化活性,同时软化固化产物的硬度,优化板材加工性能。所述固化剂组合物各组分反应活性不同,能有效提高固化速度,进一步形成的胶黏剂用于生产无醛添加人造板时,兼具固化速度快、不崩边,贴面后不易龟裂的特点。
18.优选地,所述三乙醇胺衍生物的结构如式ⅰ所示:式ⅰ;其中,a、b和c均为0-20的整数(例如2、4、6、8、10、12、14、16、18等),且a、b和c中至
少有一个不为0,进一步优选a、b和c中至少有一个为2-5(例如3、4等)。
19.本发明中,所述三乙醇胺衍生物的结构如式ⅰ所示,此结构中至少含有一个醚键,其是固化剂组合物的组分之一,进一步形成的胶黏剂用于人造板时,固化后的板材在受到外力作用时,醚键能旋转,对外力有较好的吸收缓冲作用,提高胶黏剂的柔韧性,改善进一步形成的板材在切割加工过程中,遇到的崩边等工艺现象,提高板材的加工性能。
20.优选地,所述三乙醇胺衍生物的数均分子量为200-3000 g/mol(例如500 g/mol、1000 g/mol、1500 g/mol、2000 g/mol、2500 g/mol等),进一步优选300-1500 g/mol(例如400 g/mol、500 g/mol、600 g/mol、700 g/mol、800 g/mol、900 g/mol等)。
21.优选地,以所述固化剂组合物的总质量为100%计,所述三乙醇胺、二乙醇胺和一乙醇胺的总质量百分数为30%-98%(例如35%、40%、45%、50%、55%、60%、65%、70%、75%、80%、85%、90%、95%等);进一步优选50%-98%,更进一步优选75%-90%。
22.所述三乙醇胺衍生物的质量百分数为2%-70%(例如5%、10%、15%、20%、25%、30%、35%、40%、45%、50%、55%、60%、65%等),进一步优选2%-50%,更进一步优选10%-25%。
23.本发明中,所述固化剂组合物各组分在特定比例下配合时,能够有效提高固化速度,三乙醇胺、二乙醇胺和一乙醇胺的总质量占比过重,会使固化产物的硬度过大,不利于进一步加工;占比过轻,固化速度较慢。
24.本发明中,所述三乙醇胺衍生物的制备原料包括三乙醇胺和环氧乙烷。
25.示例性地,所述三乙醇胺衍生物的制备方法由三乙醇胺跟环氧乙烷经过聚合反应,再经过聚醚吸附剂后处理制得。
26.优选地,所述三乙醇胺和环氧乙烷的质量比为1:(1-20),其中,1-20可以为2、4、6、8、10、12、14、16、18等,进一步优选1:(3-10)。
27.第二方面,本发明提供一种胶黏剂,所述胶黏剂包括a组分和b组分;所述a组分包括多亚甲基多苯基多异氰酸酯和/或多亚甲基多苯基多异氰酸酯基衍生物;所述b组分包括第一方面所述的固化剂组合物。
28.本发明中,所述胶黏剂包括a组分和b组分,a组分是胶黏剂的主体成分,包括多亚甲基多苯基多异氰酸酯和/或其多元醇改性物(聚氨酯),;b组分包括三种醇胺和一种醇胺的衍生物,配合a组分使用。由于b组分中各组分反应活性不同和反应后产物不同,能够有效提高胶黏剂体系固化速度,b组分与a组分形成的胶黏剂用于生产无醛添加人造板时,兼具固化速度快、不崩边,贴面后不易龟裂的特点。
29.优选地,所述a组分中包括钠离子,所述钠离子的质量浓度为0.1-20 ppm,例如0.5 ppm、1 ppm、2 ppm、4 ppm、6 ppm、8 ppm、10 ppm、12 ppm、14 ppm、16 ppm、18 ppm等。
30.本发明中,a组分中钠离子来源于多亚甲基多苯基多异氰酸酯和/或多亚甲基多苯基多异氰酸酯基衍生物,是制备中中和酸性的氢氧化钠提供的。
31.优选地,所述a组分的平均官能度为2.1-3.2(例如2.4、2.6、2.8、3.0等),异氰酸根在所述a组分中的质量百分数为16%-33%(例如18%、20%、22%、24%、26%、28%、30%、32%等)。所述异氰酸根的质量百分数指的是a组分所涉及的异氰酸酯的总占比。
32.优选地,所述a组分在25℃下的粘度为30-3000 cp,例如500 cp、1000 cp、1500 cp、2000 cp、2500 cp等。
33.优选地,所述多亚甲基多苯基多异氰酸酯包括二苯基甲烷二异氰酸酯、三苯基甲烷三异氰酸酯或官能度大于三的多亚甲基多苯基多异氰酸酯中的任意一种或至少两种的组合,其中典型但非限制性的组合包括:二苯基甲烷二异氰酸酯和三苯基甲烷三异氰酸酯的组合,三苯基甲烷三异氰酸酯和官能度大于三的多亚甲基多苯基多异氰酸酯的组合,二苯基甲烷二异氰酸酯、三苯基甲烷三异氰酸酯和官能度大于三的多亚甲基多苯基多异氰酸酯的组合等。
34.优选地,所述多亚甲基多苯基多异氰酸酯基衍生物由多亚甲基多苯基多异氰酸酯与二元醇反应得到。
35.示例性地,所述a组分中的多亚甲基多苯基多异氰酸酯及其衍生物选自万华化学集团股份有限公司的wannate系列多异氰酸酯,包括pm-100、pm-200、pm-400、pm-600、pm-700、cw20、cw30、pm300e或9132fc中的任意一种或至少两种的组合,其中典型但非限制性的组合包括:pm-100和pm-200的组合,pm-400、pm-600和pm-700的组合,cw20、cw30、pm300e和9132fc的组合等。
36.优选地,所述二元醇的数均分子量为300-10000 g/mol,例如500 g/mol、1000 g/mol、2000 g/mol、4000 g/mol、6000 g/mol、8000 g/mol等。
37.优选地,所述a组分和b组分的质量比为(3-15):1其中,3-15可以为4、6、8、10、12、14等。
38.本发明中,a组分和b组分的质量比为(3-15):1,选择此范围的原因是根据使用效果跟生产成本平衡,二者的质量比过高,胶黏剂体系固化慢,影响生产产能;二者的质量比过低,胶黏剂体系固化速度过快,易出现预固化现象,造成胶黏剂体系有效成分提前反应,反而降低生产效率,增加胶黏体系整体用量。
39.优选地,所述a组分按照总质量为100%计,所述a组分包括如下组分:40%-60%(例如42%、44%、46%、48%、50%、52%、54%、56%、58%等)的二苯基甲烷二异氰酸酯和/或其聚氨酯,25%-35%(例如26%、28%、30%、32%、34%等)的三苯基甲烷三异氰酸酯和/或其聚氨酯,官能度大于三的多亚甲基多苯基多异氰酸酯和/或其聚氨酯至100%。
40.第三方面,本发明提供一种无醛添加人造板,所述无醛添加人造板包括第二方面所述的胶黏剂、木质材料和/或秸秆材料。
41.示例性地,本发明所述无醛添加人造板,由木质材料和/或秸秆材料制成,所述无醛添加人造板包括至少三层(例如四层、五层、六层等)基材;所述的木质材料和/或秸秆材料之间由第一方面所述的胶黏剂粘结。
42.优选地,以所述基材的总质量为100%计,所述胶黏剂中a组分的总质量为1%-10%(例如2.5%、3%、3.5%、4%、4.5%、5%、6%、7%、8%、9%等)。
43.第四方面,本发明提供一种第一方面所述的无醛添加人造板的制备方法,所述制备方法包括如下步骤:(1)分别单独将第三方面所述的胶黏剂中的a组分、以溶剂稀释或不稀释的b组分添加到木质材料和/或秸秆材料上,混合均匀;(2)将步骤(1)所得的材料铺装成板坯;(3)将所述板坯预压和热压,得到所述无醛添加人造板。
44.优选地,步骤(1)中,所述混合均匀的方式包括搅拌混合。
45.优选地,步骤(3)中,所述预压结束后,所述板坯的厚度减少30%以上,例如32%、34%、36%、38%等。
46.优选地,所述热压的温度为180-240℃,例如190℃、200℃、210℃、220℃、230℃等。
47.优选地,所述热压的压力为0.5-5 mpa,例如1 mpa、1.5 mpa、2 mpa、2.5 mpa、3 mpa、3.5 mpa、4 mpa、4.5 mpa等。
48.优选地,步骤(1)中,所述溶剂包括水。
49.优选地,所述b组分与溶剂的质量比为(0.2-1):1,其中,0.2-1可以为0.3、0.4、0.5、0.6、0.7、0.8、0.9等。
50.优选地,步骤(1)中,所述a组分和b组分的添加方式包括雾化。
51.优选地,所述雾化包括旋转雾化和/或高压雾化。
52.优选地,所述高压雾化的压力为2-30 bar(例如4 bar、5 bar、10 bar、15 bar、20 bar、25 bar等)。
53.优选地,旋转雾化转速在9000r/min-11000r/min(例如9500 r/min、1000 r/min、10500 r/min等)。
54.本发明中,所述a组分和b组分的添加场所选择可以完成搅拌混合的密闭的滚筒或带有搅拌桨的密闭腔体内,使相应的胶黏剂体系与人造板中木质材料和/或秸秆材料混合更加均匀。
55.优选地,所述板坯的层数为至少三层(例如四层、五层、六层等)。
56.优选地,将所述添加过胶黏剂的木质和/或秸秆材料进行分层铺装制板。
57.实验室操作时,将底层物料铺装在经过脱模剂处理的金属垫板上,并用限制大小的箱体模具进行限制,防止多余物料在边缘散落。在胶黏剂施加后,应尽可能维持较低温度进行铺装环节。在压制之前,木质和/或秸秆材料作为基材和胶黏剂体系充分接触并暴露在空气中,时间越长,异氰酸酯预固化的程度就越大,直接导致有效粘接基材的胶黏剂的含量降低,成型板材力学性能降低。由于进行制板操作的每个过程都需要一定的时间,优选的热压在施胶后1小时之内(例如0.8小时、0.7小时、0.6小时、0.5小时、0.2小时等)进行,更优选地在0.5小时之内进行,进一步优选在15分钟之内进行。
58.在工业生产中,胶黏剂体系通过旋转雾化器、有气雾化喷头或者高压雾化喷头分别单独施加至滚筒拌胶机、环式拌胶机或者蘑菇头式拌胶机内部,优选地,将稀释后的b组分与工艺水经过静态混合器混合后再经过施胶喷头或旋转雾化器施加至干燥后的木质材料和/或秸秆材料上。物料进入铺装箱后,物料温度保持在30-50℃(例如32℃、34℃、36℃、38℃、40℃、42℃、44℃、46℃、48℃等),更优地温度保持在35-45℃。物料在铺装箱内部时间不超过0.5小时(例如0.4小时、0.3小时、0.2小时等),更优地不超过20分钟,更优地时间为5-10分钟。
59.利用铺装头或者铺装辊对木质材料和/或秸秆材料进行铺装,铺装含水率为表层在12%-20%(例如14%、16%、18%等),芯层2%-6%(例如3%、4%、5%等),更优地表层铺装含水率为16-18%,芯层为3.5-4.5%。
60.铺装后板坯进入热压机前,需要对板坯进行预压,使板材结构相对紧密,排出内部气体,压缩厚度不低于30%(例如32%、34%、36%、38%等)。
61.更优地,板坯在进行预压前通过微波设备、高温蒸汽设备、高温空气设备进行加
热,芯层温度提升至50-70℃(例如52℃、56℃、58℃、60℃、62℃、64℃、66℃、68℃等),更优地提升至55-60℃。
62.经过铺装预压后的板坯,进入压机内部进行热压,热压温度为180-240℃(例如190℃、200℃、210℃、220℃、230℃、240℃等),热压压力为0.5-5mpa(1 mpa、1.5 mpa、2 mpa、2.5 mpa、3 mpa、3.5 mpa、4 mpa、4.5 mpa等),优选地压力为0.5-3mpa。
63.板坯热压后进行边部毛边裁切,并依据要求,裁剪成固定尺寸进行陈放处理,随后经过砂光、贴面等后续处理得到最终制品。
64.作为优选的技术方案,所述制备方法包括如下步骤:(1)分别单独将第二方面所述的胶黏剂中的a组分、以溶剂稀释或不稀释的b组分添加到木质和/或秸秆材料上,搅拌均匀;(2)将步骤(1)所得的材料铺装成板坯;(3)将所述板坯预压至所述板坯的厚度减少30%以上,在温度为180-240℃和压力为0.5-5 mpa的条件下热压,得到所述无醛添加人造板。
65.本发明的固化剂组合物在实际应用中,梯度催化活性具体表现为一乙醇胺施胶后先与异氰酸酯胶黏剂发生反应,初步形成预聚体,建立板坯初强度;二乙醇胺在温度初升时与异氰酸酯胶黏剂发生反应,产生热量,促进体系快速升温;三乙醇胺在建立强度阶段与异氰酸酯胶黏剂反应,快速建立体系强度,快速提高固化速度;三乙醇胺衍生物在最后阶段与异氰酸酯胶黏剂反应,提升体系强度,并且引入软段,优化板材加工性能。
66.相对于现有技术,本发明具有以下有益效果:(1)采用本发明所述固化剂组合物形成的胶黏剂体系,可以大幅度地减少热压时间来提高生产效率,生产效率可以提升15%-40%,同时有效解决无醛添加人造板的板坯边部虚边、偏软和暗分层等问题,能够有效降低铺装宽度4-8 cm,节约原料用量2%-8%。还能够大大提高生产效率,降低原料、生产和财务成本,同时解决边部锯切时易崩边的问题,贴面后浸渍纸龟裂问题。
67.(2)本发明所述固化剂组合物形成的胶黏剂与木质材料和/或秸秆材料的内结合强度在0.21-0.71 mpa之间,2h-ts在2.98%-5.38%之间,静曲强度在10.52-14.38 mpa之间,弹性模量在1905-2132 mpa之间,热压因子在5s/mm时,30块板材出现的龟裂个数在5块以下,30cm长度范围内,崩边个数在5个以下。
具体实施方式
68.下面通过具体实施方式来进一步说明本发明的技术方案。本领域技术人员应该明了,所述实施例仅是帮助理解本发明,不应视为对本发明的具体限制。
69.本发明具体实施方式中所涉及的含钠离子多异氰酸酯和/或其多元醇改性衍生物及醇胺和小分子多元醇的来源具体如下:a1:含钠离子多官能度异氰酸酯与二苯基甲烷二异氰酸酯的混合物,nco含量为30.5-32.0%,官能度3.1-3.3,25℃粘度150-250 cp,铁分含量≤20ppm,钠离子含量5-15 ppm,万华化学集团股份有限公司,牌号为cw20;a2:含钠离子多官能度异氰酸酯衍生物,nco含量为28.5%-30.0%,官能度2.9-3.1,25℃粘度300-400cp,钠离子含量5-10 ppm,万华化学集团股份有限公司,牌号为9132fc;
醇胺:三乙醇胺:工业纯,湖北仙粼化工有限公司;二乙醇胺:工业纯,湖北仙粼化工有限公司;乙醇胺:工业纯,湖北仙粼化工有限公司;环氧乙烷:工业纯,湖北仙粼化工有限公司;氢氧化钠:工业纯,山东鸿祥化工有限公司;硅酸镁:工业纯,湖北兴东诚化工有限公司;木质原料:刨花板,超强刨花板用表芯层原料,水含量约2-3wt%,杨木,杂木,桉木等,购于万华禾香板(荆门)有限公司,牌号为20210125;脱模剂:牌号为kc201,万华化学;增粘剂:牌号为kc367,万华化学。
70.本发明具体实施例中的制备方法包括试验室刨花板制备和工厂生产刨花板两种。
71.试验室刨花板制备步骤:将一定质量的刨花倒入带搅拌设备的密封筒内,利用有气雾化的方式进行物料添加。a组分单独添加,b组分利用需要添加的工艺水稀释后进行添加。确保胶黏剂组分能均匀的施加到刨花内。表层刨花水含量为17-18wt%,芯层刨花水含量为3.5-4.5wt%。
72.将50
×
50cm不锈钢金属垫板放到热压机预热后喷洒脱模剂,采用手工铺装的方式在35
×
35
×
30cm的箱体模具内进行刨花板的铺装,表芯层,铺装量分别为320g、970g、320g。铺装后进行热压,厚度为18mm。热压过程采用3段式压力,分为高中低三段,热压压力分别为3mpa、1.5mpa、0.5mpa保压时间比为4:4:3,热压因子为5s/mm(根据板材不同进行调整),热压温度为230℃。
73.工厂生产刨花板制备步骤:将表芯层刨花含水率干燥至2%左右,之后刨花经过筛分后分别被传送至表芯层施胶机中,a组分单独通过施胶喷头或者旋转雾化器添加至拌胶机内,b组分经稀释单独或者与工艺水或其他助剂,经过静态混合器后通过施胶喷头或者旋转雾化器添加至拌胶机内。施胶后刨花经过刮板或者皮带运输机输送至铺装仓内,经过铺装头或者铺装辊铺装至皮带上,以18mm厚度板材为例,下表层、芯层和上表层的铺装比例分别17.2%、65%、17.8%。铺装后的板材经过预压后进入热压机,热压机温度根据温度区间分布,从240-190℃逐渐降低,热压压力根据框架分布由3.5-0.5mpa进行调整,热压速度根据板材热压具体情况进行调整。
74.实施例1本实施例提供一种胶黏剂,所述胶黏剂包括质量比为3.2:0.6的a组分和b组分;a组分:含钠离子多官能度异氰酸酯与二苯基甲烷二异氰酸酯的混合物,原料a1;b组分:由三乙醇胺、二乙醇胺、一乙醇胺和三乙醇胺衍生物组成;所述三乙醇胺、二乙醇胺和一乙醇胺的质量百分数为90%(以三者的总质量为100%计,三乙醇胺92%,二乙醇胺6%和一乙醇胺2%);所述三乙醇胺衍生物的质量百分数为10%,其结构式如下:
其中,a、b和c的平均值各自为13.55。
75.所述三乙醇胺衍生物合成过程如下所述,在反应釜中加入三乙醇胺和氢氧化钾配的50%的水溶液,升温到130℃,真空脱水2小时后,再加入环氧乙烷,在135-140℃反应完全后,降温到80℃加入蒸馏水、磷酸、聚醚吸附剂,升温到120℃脱水2小时后降温到80℃出料。各物质的重量比如下表所示表1实施例2本实施例提供一种胶黏剂,所述胶黏剂包括质量比为3.2:0.6的a组分和b组分;a组分:含钠离子多官能度异氰酸酯与二苯基甲烷二异氰酸酯的混合物,原料a1;b组分:由三乙醇胺、二乙醇胺、一乙醇胺和三乙醇胺衍生物组成;所述三乙醇胺、二乙醇胺和一乙醇胺的质量百分数为85%(以三者的总质量为100%计,三乙醇胺92%,二乙醇胺6%和一乙醇胺2%);所述三乙醇胺衍生物的质量百分数为15%,其结构式如下:其中,a、b和c的平均值各自为9.03。
76.所述三乙醇胺衍生物合成过程如下所述,在反应釜中加入三乙醇胺和氢氧化钾配的50%的水溶液,升温到130℃,真空脱水2小时后,再加入环氧乙烷,在135-140℃反应完全后,降温到80℃加入蒸馏水、磷酸、聚醚吸附剂,升温到120℃脱水2小时后降温到80℃出料。各物质的重量比如下表所示表2实施例3本实施例提供一种胶黏剂,所述胶黏剂包括质量比为3.2:0.6的a组分和b组分;a组分:含钠离子多官能度异氰酸酯与二苯基甲烷二异氰酸酯的混合,原料a1;所述三乙醇胺、二乙醇胺和一乙醇胺的质量百分数为80%(以三者的总质量为100%
计,三乙醇胺92%,二乙醇胺6%和一乙醇胺2%);所述三乙醇胺衍生物的质量百分数为20%,其结构式如下:其中, a、b和c的平均值各自为4.52。
77.所述三乙醇胺衍生物合成过程如下所述,在反应釜中加入三乙醇胺和氢氧化钾配的50%的水溶液,升温到130℃,真空脱水1小时后,再加入环氧乙烷,在135-140℃反应完全后,降温到80℃加入蒸馏水、磷酸、聚醚吸附剂,升温到120℃脱水1小时后降温到80℃出料。各物质的重量比如下表所示。
78.表3实施例4本实施例提供一种胶黏剂,所述胶黏剂包括质量比为3.2:0.6的a组分和b组分;a组分:含钠离子多官能度异氰酸酯与二苯基甲烷二异氰酸酯的混合,原料a1;含钠离子多官能度异氰酸酯衍生物,原料a2,二者的质量比为1.4:1.8,a1施加于表层原料中,a2施加于芯层物料中;b组分与实施例1相同。
79.实施例5本实施例提供一种胶黏剂,所述胶黏剂包括质量比为3.2:0.6的a组分和b组分;a组分:含钠离子多官能度异氰酸酯与二苯基甲烷二异氰酸酯的混合,原料a1;含钠离子多官能度异氰酸酯衍生物,原料a2,二者的质量比为1.4:1.8,a1施加于表层原料中,a2施加于芯层物料中; b组分与实施例2相同。
80.实施例6本实施例提供一种胶黏剂,所述胶黏剂包括质量比为3.2:0.6的a组分和b组分;a组分:含钠离子多官能度异氰酸酯与二苯基甲烷二异氰酸酯的混合,原料a1;含钠离子多官能度异氰酸酯衍生物,原料a2,二者的质量比为1.4:1.8,a1施加于表层原料中,a2施加于芯层物料中;b组分与实施例3相同。
81.实施例7本实施例提供一种胶黏剂,所述胶黏剂包括质量比为3.2:0.5的a组分和b组分;a组分:含钠离子多官能度异氰酸酯与二苯基甲烷二异氰酸酯的混合,原料a1;b组分与实施例3相同。
82.实施例8
本实施例提供一种胶黏剂,所述胶黏剂包括质量比为3.2:0.5的a组分和b组分;a组分:含钠离子多官能度异氰酸酯与二苯基甲烷二异氰酸酯的混合,原料a1;含钠离子多官能度异氰酸酯衍生物,原料a2,二者的质量比为1.3:2.0,a1施加于表层原料中,a2施加于芯层物料中;b组分与实施例3相同。
83.实施例9-14实施例9-14与实施例1的区别在于三乙醇胺衍生物的质量百分数不同,具体如下:实施例9:三乙醇胺衍生物的质量百分数为2%,三乙醇胺、二乙醇胺和一乙醇胺三者的总质量百分数为98%,其余均与实施例1相同。
84.实施例10:三乙醇胺衍生物的质量百分数为50%,三乙醇胺、二乙醇胺和一乙醇胺三者的总质量百分数为50%,其余均与实施例1相同。
85.实施例11:三乙醇胺衍生物的质量百分数为55%,三乙醇胺、二乙醇胺和一乙醇胺三者的总质量百分数为45%,其余均与实施例1相同。
86.实施例12:三乙醇胺衍生物的质量百分数为70%,三乙醇胺、二乙醇胺和一乙醇胺三者的总质量百分数为30%,其余均与实施例1相同。
87.实施例13:三乙醇胺衍生物的质量百分数为1%,三乙醇胺、二乙醇胺和一乙醇胺三者的总质量百分数为99%,其余均与实施例1相同。
88.实施例14:三乙醇胺衍生物的质量百分数为75%,三乙醇胺、二乙醇胺和一乙醇胺三者的总质量百分数为25%,其余均与实施例1相同。
89.对比例1本对比例与实施例3的区别在于不包括b组分,其余均与实施例3相同。
90.对比例2本对比例与实施例6的区别在于不包括b组分,其余均与实施例6相同。
91.对比例3本对比例与实施例1的区别在于三乙醇胺衍生物的质量百分数为0%,以三乙醇胺、二乙醇胺和一乙醇胺的总质量为100%计,三乙醇胺92%,二乙醇胺6%,一乙醇胺2%,其余均与实施例1相同。
92.对比例4本对比例与实施例1的区别在于体系中b组分三乙醇胺、二乙醇胺、一乙醇胺质量为90%(以三者的总质量为100%计,三乙醇胺93%,二乙醇胺7%,一乙醇胺0%),其余均与实施例1相同。
93.对比例5本对比例与实施例1的区别在于体系中b组分三乙醇胺、二乙醇胺、一乙醇胺质量为90%(以三者的总质量为100%计,三乙醇胺95%,二乙醇胺0%,一乙醇胺5%),其余均与实施例1相同。
94.对比例6本对比例与实施例1的区别在于体系中b组分三乙醇胺、二乙醇胺、一乙醇胺质量为90%(以三者的总质量为100%计,三乙醇胺0%,二乙醇胺75%,一乙醇胺25%),其余均与实施例1相同。
95.应用例1本应用例提供一种人造板,所述人造板为木质刨花,木质刨花由表层和芯层组成;所述木质材料之间由实施例1所述的胶黏剂粘结,其中,b组分的添加质量为木质刨花的0.6%。
96.所述人造板的制备采用试验室刨花板制备方案压制板材,热压因子为5s/mm。
97.应用例2-6本应用例与应用例1的区别在于所述胶黏剂为实施例2-6所述胶黏剂,详见表1,其余均与应用例1相同。
98.应用例7本应用例提供一种人造板,所述人造板为木质刨花,木质刨花由表层和芯层组成;所述木质材料之间由实施例7所述的胶黏剂粘结,其中,b组分的添加质量为木质刨花的0.5%。
99.所述人造板的制备采用工厂生产刨花板制备方案压制板材。
100.应用例8本应用例与应用例7的区别在于所述胶黏剂为实施例8所述胶黏剂,其余均与应用例7相同。
101.应用例9-14、应用对比例1-6应用例9-10、应用对比例1-6与应用例1的区别在于所述胶黏剂分别为实施例9-10、对比例1-6所述胶黏剂,其余均与应用例1相同。
102.应用对比例7本应用对比例与应用对比例1的区别在于所述制备方法不同,其余均与应用对比例1相同,本应用对比例的方法与应用例7相同。
103.应用对比例8本应用对比例与应用对比例2的区别在于所述制备方法不同,其余均与应用对比例2相同,本应用对比例的方法与应用例7相同。
104.性能测试将应用例1-14和应用对比例1-8所述人造板按照gb/t17657-2013进行测试,板材具体参数汇总于表1中,测试结果汇总于表4-6中。
105.表4
注:a组分和b组分的用量均为绝干刨花的重量比,表芯层刨花绝干重量比例为4:6。
106.以上热压因子为生产时,产品性能达到工厂质量标准时,能够连续稳定生产时的热压因子,热压因子反应胶黏剂体系固化效率,热压因子越低,胶黏剂体系固化效率越高。
107.表5
表6
胶黏剂的固化程度,主要的体现在板材的内结合强度和厚度中,关于静曲强度和弹性模量有一定的相关性,但影响没有内结合强度明显。
108.板材加工性能主要体现在贴面后是否崩边和是否出现龟裂,加工性能好的板材不应出现崩边和龟裂的情况。
109.分析表4-5数据可知,本发明所述胶黏剂用于基材,尤其是用于木质材料中时,兼具固化速度快、不崩边,贴面后不易龟裂的特点,本发明所述胶黏剂与基材的内结合强度在0.21-0.71 mpa之间,2h-ts在2.98%-5.38%之间,静曲强度在10.52-14.38 mpa之间,弹性模量在1905-2132 mpa之间,热压因子在5s/mm时,30块出现的龟裂个数在5块以下,30cm长度范围内,崩边个数在5个以下。
110.分析应用例1和应用例2及应用对比例1可知,在不添加胶黏剂b组分的情况下,使用本发明所述的胶黏剂,固化速度更快,板材性能更优,但不添加b组分的情况下,板材加工性能差,易出现崩边和龟裂的问题。
111.分析应用例4和应用例5及应用对比例2同样能得到上述结论。
112.分析应用例1及应用对比例3-6可知,本体系中固化剂组合物b组分中任意一种组分均会影响体系的固化效果,板材不易成型或者成型后力学性能和加工性能变差,易出现崩边和龟裂问题。
113.分析应用例7-8和应用对比例7-8可知,如表6数据所示,使用本发明所述胶黏剂体系,可应用于工业化生产人造板工艺中,且不添加b组分的情况下,板材加工性能差,易出现崩边和龟裂的问题。
114.通过应用例7和应用对比例7可知,根据热压因子的结果,所述胶黏剂体系中芯层a组分选用a2时,再添加b组分剂量为刨花干重的0.5%时,热压效率相比仅使用a组分为胶黏剂时提升33%左右。
115.分析应用例9-14可知,应用例13-14不如应用例9-12,证明三乙醇胺衍生物的质量百分数在2%-70%范围内形成的胶黏剂性能更佳。
116.应用例9-12可知,应用例11-12不如应用例9-10,证明三乙醇胺衍生物的质量百分数进一步优选在2%-50%范围内形成的胶黏剂性能更佳。
117.本发明通过上述实施例来说明本发明的详细方法,但本发明并不局限于上述详细方法,即不意味着本发明必须依赖上述详细方法才能实施。所属技术领域的技术人员应该明了,对本发明的任何改进,对本发明产品各原料的等效替换及辅助成分的添加、具体方式的选择等,均落在本发明的保护范围和公开范围之内。
再多了解一些
本文用于创业者技术爱好者查询,仅供学习研究,如用于商业用途,请联系技术所有人。