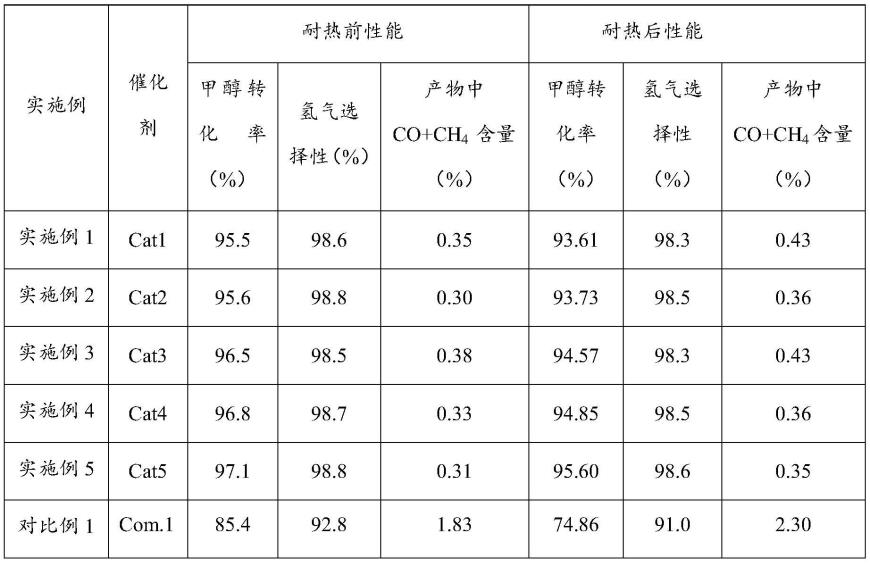
1.本发明涉及催化剂技术领域,具体涉及一种大型化甲醇制氢装置铜基催化剂的制备方法。
背景技术:
2.多年以来,甲醇制氢工艺已广泛用于石化化工、精细化工、制药、有色金属、航空航天及气体等行业。近年来,随着我国汽车保有量快速增长,汽车尾气排放污染的影响日益增加,从而国家要求加快油品质量升级的步伐。全国石油炼制和石油化工产能巨大,由于产业结构等诸多因素,汽柴油加氢装置的氢气缺口巨大,而大型化甲醇制氢技术由于原料来源方便、工艺成熟、装置投资低、生产成本低及节能环保等优势,已成为了国内汽柴油等加氢装置氢气的最有效补充途径之一,且目前国内大型化甲醇制氢装置单套产能规模为1.0亿nm3/年~5亿nm3/年,其整体产能超过80亿nm3/ 年。
3.活性金属铜对甲醇、co、co2等低碳物种具有较好的活化作用,并且对水的解离也具有优良的催化作用,在甲醇制氢技术领域,相比较于pt和 pd等负载型贵金属催化剂及镍基催化剂等金属氧化物催化剂,铜基催化剂是应用最广泛的工业催化剂。
4.相对于中小型甲醇制氢装置,大型化甲醇制氢装置的反应压力相对较高导致甲醇转化率较低,需要在相对更高的反应温度下进行反应以提高催化剂的甲醇转化效率,这会导致氢气选择性下降以及成烃副反应程度增加,从而催化剂使用寿命较短。并且,大量使用的原料甲醇由于运输过程中易带入含硫有毒化合物,会导致催化剂中毒,催化剂反应性能会进一步恶化而导致快速失活。
5.目前,铜基催化剂在大型化甲醇制氢工艺中普遍存在催化活性低、热稳定性差、氢气选择性差、抗毒性能差及使用寿命短等诸多问题。传统的铜基甲醇制氢催化剂中活性金属铜晶粒尺寸分布较大且分散性差,助剂及载体与活性铜晶粒间的相互作用力不强,对失活后催化剂研究发现铜晶粒烧结严重,cu颗粒显著长大且发生团聚,这是导致目前工业催化剂快速失活的主要原因。
技术实现要素:
6.本发明的目的在于提供一种大型化甲醇制氢装置铜基催化剂的制备方法,解决现有技术中铜基催化剂在大型化甲醇制氢工艺中普遍存在催化活性低、热稳定性差、氢气选择性差、抗毒性能差及使用寿命短等技术问题。
7.本发明公开了一种大型化甲醇制氢装置铜基催化剂的制备方法,包括以下步骤,
8.s1.催化剂前驱体化合物共沉淀反应,共沉淀反应的同时加入改性载体化合物;
9.s2.催化剂前驱体化合物的强化均质晶化处理;
10.s3.催化剂前驱体化合物的后处理。
11.进一步的,所述改性载体化合物为al2o3。
12.进一步的,所述改性载体化合物为通过mgo、zro2、ceo2、in2o3中的一种或多种氧化
物改性的al2o3。
13.进一步的,所述al2o3的bet比表面积为200cm2/g~400cm2/g,平均孔径为8nm~20nm,孔容为0.7~1.5cm3/g。
14.进一步的,所述步骤s1中催化剂前驱体化合物共沉淀反应为将预热至反应温度后的铜锌可溶性盐混合溶液与碱溶液同时送入反应釜进行搅拌共沉淀反应。
15.进一步的,步骤s1中所述改性载体化合物的加入体积、加入速度与共沉淀反应中可溶性盐溶液的加入体积、加入速度相同。
16.进一步的,所述步骤s2中强化均质晶化处理具体步骤为:共沉淀反应完成后反应釜升温升压,然后催化剂前驱体化合物浆料在搅拌下进行强化均质晶化处理,处理完成后反应釜降温降压,卸出处理好的催化剂前驱体化合物。
17.进一步的,所述步骤s2中强化均质晶化温度为120℃~250℃,强化均质晶化压力为0.2mpa~4.0mpa,强化均质晶化时间0.5h~2h,搅拌速度 10~200r/min,反应釜升温升压程序中升温速度1.0℃/min~5.0℃/min,升压速度0.01mpa/min~0.25mpa/min。
18.进一步的,步骤s3中所述催化剂前驱体化合物的后处理步骤为:强化均质晶化处理后的前驱体化合物经过滤及洗涤得到滤饼物料,滤饼物料经干燥、煅烧、混料后进行压片成型,即得到铜基催化剂。
19.进一步的,所述滤饼物料干燥为气流干燥或流化床干燥,且干燥后颗粒尺寸为60目~300目。
20.本发明第二个目的是保护一种大型化甲醇制氢装置铜基催化剂的制备方法制得的催化剂,其组分包括,质量份数为50份~80份的活性组分化合物cuo,质量份数为5份~20份的助剂化合物zno,质量份数为5份~30 份的改性载体化合物。
21.本发明的第三个目的是保护一种大型化甲醇制氢装置铜基催化剂的制备方法的应用,用于制备大型化甲醇制氢装置使用的铜基催化剂。
22.进一步的,所述铜基催化剂在大型化甲醇制氢装置中应用条件为:反应压力2.0mpa~3.0mpa;反应温度250℃~300℃;反应液空速为0.5~1.2h-1
;原料水醇摩尔比为1.6~2.5;原料甲醇中总硫含量为0~3ppm。
23.与现有技术相比,本发明具有的有益效果是:
24.1.采用特殊载体化合物对催化剂进行改性,并且在铜锌金属可溶性盐溶液共沉淀过程中等体积、等速加入载体化合物,显著改善了载体内部微孔道环境、提升其对活性组分的支撑和分散作用,以及优化活性组分晶体形貌和尺寸。相比较对比实施例,bet比表面积提升可达31.5%,平均孔径提升可达84.9%,孔容提升可达85.7%;相比较其他处理工艺,bet比表面积提升可达42.4%,平均孔径提升可达128.6%,孔容提升可达100%。
25.2.通过特殊的强化均质晶化过程,大幅缩短了催化剂前驱体晶化时间,强化了铜锌前驱体化合物均质晶化过程,精准调控了催化剂中活性铜晶粒尺寸分布,增强了载体化合物与活性铜晶粒的相互作用力,以及强化了活性铜与氧化锌的协调效应,从而较大程度提升催化剂的甲醇转化效率、氢气选择性、热稳定性、抗毒性及使用寿命。相比较对比例,cuo晶粒尺寸分布显著更窄,调控达到5~20nm,同样反应条件下甲醇转化率提升比例最高可达23.69%,氢气选择性相对提升最高达14.35%,反应气中co等杂质含量显著更低。耐热处理后,甲醇转化率相对提高比例可达最高可达31.21%,氢气选择性相对提升最高可达
21.73%,催化剂cat1~5的转化性能下降比例最低仅为1.5%,而对比例转化下降比例高达9.25%,这说明与现有技术相比,催化剂的热稳定性等综合性能得到了显著提升。另外,催化剂50h抗毒性能对比考察表明,本发明制备的催化剂具有更优的抗毒性能,抗毒实验后催化剂的甲醇转化率和氢气选择性下降比例显著更低。
26.3.本发明操作简单,原料廉价易得,催化剂制备成本低,所制备的催化剂在高温高压等条件下具有较好的催化活性、热稳定性、抗毒性、氢气选择性及使用寿命,是一种适于大型化甲醇制氢装置的铜基催化剂。
具体实施方式
27.为使本发明实施方式的目的、技术方案和优点更加清楚,对本发明实施方式中的技术方案进行清楚、完整地描述,显然,所描述的实施方式是本发明一部分实施方式,而不是全部的实施方式。
28.实施例1:
29.称cu(no3)2·
3h2o 483.20g,zn(no3)2·
6h2o 109.85g溶解在装有1000ml 脱盐水烧杯中,搅拌使其完全溶解,补充脱盐水并定容至4000ml,配制得到盐溶液a。称取na2co
3 279.02g,溶解在装有1000ml脱盐水烧杯中,搅拌使其完全溶解,补充脱盐水并定容至4000ml,配制得到碱溶液b。
30.称载体化合物al2o3(bet比表面积为249cm2/g,平均孔径为9nm,孔容为0.95cm3/g)72.16g加入装有4000ml脱盐水烧杯中,搅拌使其形成均质悬浊液,补充脱盐水并定容至4000ml,配制得到载体悬浊液c。
31.对盐溶液a、碱溶液b及载体悬浊液c进行预热,预热至反应温度80℃,同时控制反应釜温度为80℃,当温度达到要求后,先开启反应釜搅拌器并调整搅拌速度为120r/min,然后盐碱溶液并流加入反应釜中进行等体积并流共沉淀反应,沉淀反应同时等体积等速加入载体悬浊液c。控制沉淀反应过程ph值为8.5,控制沉淀反应时间0.2h,反应完成后提高反应釜内前驱体化合物强化均质晶化温度升至150℃、反应釜压力升至0.5mpa,其升温速度为4℃/min,升压速度0.05mpa/min,搅拌速度为20r/min,强化均质晶化时间1.0h。强化均质晶化完成后的前驱体化合物浆料过滤掉大部分母液,滤饼采用5000ml脱盐水进行再浆,再浆完成后再次进行过滤。多次再浆过滤合格后得到的滤饼中添加适量的热脱盐水进行均质处理。均质处理后的浆料,送至流化床器进行喷雾干燥,控制颗粒尺寸为80目~120目。喷雾干燥完成后取出催化剂前驱体干燥粉料291.37g,放入煅烧炉中进行煅烧,煅烧温度为350℃,煅烧时间为4h,得到催化剂煅烧粉料271.25g,冷却后加入6.0g石墨和17.0g水进行充分混合,然后进行压片成型得到大型化甲醇制氢催化剂样品,记为cat1,其中al2o3的质量分数为24.66%,cuo的质量分数为54.37%,zno的质量分数为10.27%。
32.实施例2:
33.称cu(no3)2·
3h2o 604.00g,zn(no3)2·
6h2o 106.25g溶解在装有1000ml 脱盐水烧杯中,搅拌使其完全溶解,补充脱盐水并定容至3000ml,配制得到盐溶液a。称取na2co
3 329.21g,溶解在装有1000ml脱盐水烧杯中,搅拌使其完全溶解,补充脱盐水并定容至3000ml,配制得到碱溶液b。
34.称mgo改性的al2o3(bet比表面积为250cm2/g,平均孔径为12nm,孔容为0.98cm3/g)
45.73g加入装有800ml脱盐水烧杯中,搅拌使其形成均质悬浊液,补充脱盐水并定容至3000ml,配制得到载体悬浊液c。
35.对盐溶液a、碱溶液b及载体悬浊液c进行预热,预热至反应温度85℃,同时控制反应釜温度为85℃,当温度达到要求后,先开启反应釜搅拌器并调整搅拌速度为200r/min,然后盐碱溶液并流加入反应釜中进行等体积并流共沉淀反应,沉淀反应同时等体积等速加入载体悬浊液c。控制沉淀反应过程ph值为7.5,控制沉淀反应时间0.15h,反应完成后提高反应釜内前驱体化合物强化均质晶化温度升至120℃、反应釜压力升至0.20mpa,其升温速度为2℃/min,升压速度0.025mpa/min,搅拌速度为50r/min,强化均质晶化时间1.5h。强化均质晶化完成后的前驱体化合物浆料过滤掉大部分母液,滤饼采用4000ml脱盐水进行再浆,再浆完成后再次进行过滤。多次再浆过滤合格后得到的滤饼中添加适量的热脱盐水进行均质处理。均质处理后的浆料,送至气流干燥器进行气流干燥,控制干燥后颗粒尺寸120目~180目。气流干燥完成后取出催化剂前驱体干燥粉料364.71g,放入煅烧炉中进行煅烧,煅烧温度为380℃,煅烧时间为3.5h,得到催化剂煅烧粉料 291.77g,冷却后加入6.0g淀粉和18.0g水进行充分混合,然后进行压片成型得到大型化甲醇制氢催化剂样品,记为cat2,其中mgo改性的al2o3的质量分数为14.61%,cuo的质量分数为63.54%,zno的质量分数为11.14%。
36.实施例3:
37.称cu(no3)2·
3h2o 434.88g,zn(no3)2·
6h2o 71.40g溶解在装有1000ml 脱盐水烧杯中,搅拌使其完全溶解,补充脱盐水并定容至4000ml,配制得到盐溶液a。称取na2co
3 235.88g,溶解在装有1000ml脱盐水烧杯中,搅拌使其完全溶解,补充脱盐水并定容至4000ml,配制得到碱溶液b。
38.称zro2改性的al2o3(bet比表面积为268cm2/g,平均孔径为11nm,孔容为1.06cm3/g)40.53g加入装有500ml脱盐水烧杯中,搅拌使其形成均质悬浊液,补充脱盐水并定容至4000ml,配制得到载体悬浊液c。
39.对盐溶液a、碱溶液b及载体悬浊液c进行预热,预热至反应温度80℃,同时控制反应釜温度为80℃,当温度达到要求后,先开启反应釜搅拌器并调整搅拌速度为300r/min,然后盐碱溶液并流加入反应釜中进行等体积并流共沉淀反应,沉淀反应同时等体积等速加入载体悬浊液c。控制沉淀反应过程ph值为8.2,控制沉淀反应时间0.25h,反应完成后提高反应釜内前驱体化合物强化均质晶化温度升至180℃、反应釜压力升至1.0mpa,其升温速度为5℃/min,升压速度0.05mpa/min,搅拌速度为60r/min,强化均质晶化时间1.0h。强化均质晶化完成后的前驱体化合物浆料过滤掉大部分母液,滤饼采用3000ml脱盐水进行再浆,再浆完成后再次进行过滤。多次再浆过滤合格后得到的滤饼中添加适量的热脱盐水进行均质处理。均质处理后的浆料,送至流化床干燥器进行气流床干燥,控制干燥后颗粒尺寸为120 目~180目。流化床干燥完成后取出催化剂前驱体干燥粉料264.76g,放入煅烧炉中进行煅烧,煅烧温度为340℃,煅烧时间为4h,得到催化剂煅烧粉料211.81g,冷却后加入4.0g硬脂酸镁和12.0g水进行充分混合,然后进行压片成型得到大型化甲醇制氢催化剂样品,记为cat3,其中zro2改性al2o3的质量分数为17.81%,cuo的质量分数为62.91%,zno的质量分数为 8.58%。
40.实施例4:
41.称cu(no3)2·
3h2o 362.40g,zn(no3)2·
6h2o 71.40g溶解在装有1000ml 脱盐水烧杯中,搅拌使其完全溶解,补充脱盐水并定容至2000ml,配制得到盐溶液a。称取na2co3197.46g,溶解在装有1000ml脱盐水烧杯中,搅拌使其完全溶解,补充脱盐水并定容至2000ml,配制得到碱溶液b。
42.称ceo2改性的al2o3(bet比表面积为238cm2/g,平均孔径为8nm,孔容为0.90cm3/g)35.63g加入装有500ml脱盐水烧杯中,搅拌使其形成均质悬浊液,补充脱盐水并定容至2000ml,配制得到载体悬浊液c。
43.对盐溶液a、碱溶液b及载体悬浊液c进行预热,预热至反应温度80℃,同时控制反应釜温度为80℃,当温度达到要求后,先开启反应釜搅拌器并调整搅拌速度为120r/min,然后盐碱溶液并流加入反应釜中进行等体积并流共沉淀反应,沉淀反应同时等体积等速加入载体悬浊液c。控制沉淀反应过程ph值为7.8,控制沉淀反应时间0.2h,反应完成后提高反应釜内前驱体化合物强化均质晶化温度升至120℃、反应釜压力升至0.2mpa,其升温速度为4.0℃/min,升压速度0.02mpa/min,搅拌速度为50r/min,水热晶化时间1.8h。强化均质晶化完成后的前驱体化合物浆料过滤掉大部分母液,滤饼采用3000ml脱盐水进行再浆,再浆完成后再次进行过滤。多次再浆过滤合格后得到的滤饼中添加适量的热脱盐水进行均质处理。均质处理后的浆料,送至流化床干燥器进行干燥,控制干燥后颗粒尺寸60目~120目。干燥完成后取出催化剂前驱体干燥粉料227.23g,放入煅烧炉中进行煅烧,煅烧温度为350℃,煅烧时间为4h,得到催化剂煅烧粉料181.79g,冷却后加入4.0g甲基纤维素和12.0g水进行充分混合,然后进行压片成型得到大型化甲醇制氢催化剂样品,记为cat4,其中ceo2改性的al2o3的质量分数为 7.78%,cuo的质量分数为70.05%,zno的质量分数为11.47%。
44.实施例5:
45.称cu(no3)2·
3h2o 483.20g,zn(no3)2·
6h2o 95.20g溶解在装有1000ml 脱盐水烧杯中,搅拌使其完全溶解,补充脱盐水并定容至4000ml,配制得到盐溶液a。称取na2co
3 263.28g,溶解在装有1000ml脱盐水烧杯中,搅拌使其完全溶解,补充脱盐水并定容至4000ml,配制得到碱溶液b。
46.称in2o3改性的al2o3(bet比表面积为255cm2/g,平均孔径为9nm,孔容为1.02cm3/g)74.15g加入装有800ml脱盐水烧杯中,搅拌使其形成均质悬浊液,补充脱盐水并定容至4000ml,配制得到载体悬浊液c。
47.对盐溶液a、碱溶液b及载体悬浊液c进行预热,预热至反应温度80℃,同时控制反应釜温度为80℃,当温度达到要求后,先开启反应釜搅拌器并调整搅拌速度为120r/min,然后盐碱溶液并流加入反应釜中进行等体积并流共沉淀反应,沉淀反应同时等体积等速加入载体悬浊液c。控制沉淀反应过程ph值为8.5,控制沉淀反应时间0.2h,反应完成后提高反应釜内前驱体化合物强化均质晶化温度升至180℃、反应釜压力升至1.0mpa,其升温速度为5.0℃/min,升压速度0.05mpa/min,搅拌速度为30r/min,强化均质晶化时间1.0h。强化均质晶化完成后的前驱体化合物浆料过滤掉大部分母液,滤饼采用3000ml脱盐水进行再浆,再浆完成后再次进行过滤。多次再浆过滤合格后得到的滤饼中添加适量的热脱盐水进行均质处理。均质处理后的浆料,送至流化床干燥器进行干燥,控制干燥后颗粒尺寸为80目~120 目。干燥完成后取出催化剂前驱体干燥粉料336.28g,放入煅烧炉中进行煅烧,煅烧温度为360℃,煅烧时间为4h,得到催化剂煅烧粉料269.02g,冷却加入6.0g甲基纤维素和18.0g水
进行充分混合,然后进行压片成型得到大型化甲醇制氢催化剂样品,记为cat5,其中in2o3改性的al2o3的质量分数为25.54%,cuo的质量分数为54.79%,zno的质量分数为8.97%。
48.参照对比例1:
49.称cu(no3)2·
3h2o 483.20g,zn(no3)2·
6h2o 109.85g,al(no3)2·
9h2o530.95g溶解在装有1000ml脱盐水烧杯中,搅拌使其完全溶解,补充脱盐水并定容至4000ml,配制得到盐溶液a。
50.称取na2co
3 529.04g,溶解在装有1000ml脱盐水烧杯中,搅拌使其完全溶解,补充脱盐水并定容至4000ml,配制得到碱溶液b。
51.对盐溶液a、碱溶液b进行预热,预热至反应温度55℃,同时控制反应釜温度为55℃,当温度达到要求后,先开启反应釜搅拌器并调整搅拌速度为200r/min,然后盐碱溶液并流加入反应釜中进行等体积并流共沉淀反应。控制沉淀反应过程ph值为8.5,控制沉淀反应时间0.2h,反应完成后进行老化反应,老化温度80℃,老化时间4h,老化完成后的前驱体化合物浆料过滤掉大部分母液,滤饼采用3000ml脱盐水进行再浆,再浆完成后再次进行过滤。多次再浆过滤合格后得到的滤饼中添加适量的热脱盐水进行厢式干燥,干燥温度120℃,干燥时间15h,得到催化剂前驱体干燥粉料 343.81g,放入煅烧炉中进行煅烧,煅烧温度为400℃,煅烧时间为3h,得到催化剂煅烧粉料275.05g,冷却后对其进行造粒,颗粒尺寸控制为40目~80目,加入6.0g石墨和18.0g水进行充分混合,然后进行压片成型得到铜系甲醇制氢催化剂对比样品1,记为com.1,其中al2o3的质量分数为24.66%, cuo的质量分数为54.37%,zno的质量分数为10.27%。
52.参照对比例2:
53.称cu(no3)2·
3h2o 483.20g,zn(no3)2·
6h2o109.85g,al(no3)2·
9h2o530.95g溶解在装有1000ml脱盐水烧杯中,搅拌使其完全溶解,补充脱盐水并定容至4000ml,配制得到盐溶液a。
54.称取na2co
3 529.04g,溶解在装有1000ml脱盐水烧杯中,搅拌使其完全溶解,补充脱盐水并定容至4000ml,配制得到碱溶液b。
55.对盐溶液a、碱溶液b进行预热,预热至反应温度55℃,同时控制反应釜温度为55℃,当温度达到要求后,先开启反应釜搅拌器并调整搅拌速度为200r/min,首先加入盐溶液a,然后滴加碱溶液b,当反应浆料ph值为10.0时停止滴加并密封反应釜,在110℃的条件下保温13h,得到共沉淀产物。取出共沉淀产物直接进行干燥,干燥温度105℃,干燥时间3h,然后对干燥物料进行煅烧,煅烧温度600℃,煅烧时间5h,得到催化剂煅烧粉料275.05g,冷却后对其进行造粒,颗粒尺寸控制为40目~80目,加入 6.0g石墨和18.0g水进行充分混合,然后进行压片成型得到铜系甲醇制氢催化剂对比样品1,记为com.2,其中al2o3的质量分数为24.66%,cuo的质量分数为54.37%,zno的质量分数为10.27%。
56.参照对比例3:
57.称cu(no3)2·
3h2o 483.20g,zn(no3)2·
6h2o 109.85g,al(no3)2·
9h2o530.95g溶解在装有1000ml脱盐水烧杯中,搅拌使其完全溶解,配制得到盐溶液a。
58.称取30%氨水溶液500ml,稀释在装有1500ml脱盐水烧杯中并搅拌均匀,配制得到碱溶液b。
59.首先反应釜中加入盐溶液a,然后滴加碱溶液b,当反应浆料ph值为 9.5时停止滴
加并密封反应釜,在110℃的条件下保温13h,得到共沉淀产物。取出共沉淀产物直接进行干燥,干燥温度105℃,干燥时间3h,然后对干燥物料进行煅烧,煅烧温度600℃,煅烧时间5h,得到催化剂煅烧粉料275.05g,冷却后对其进行造粒,颗粒尺寸控制为40目~80目,加入6.0g 石墨和18.0g水进行充分混合,然后进行压片成型得到铜系甲醇制氢催化剂对比样品1,记为com.3,其中al2o3的质量分数为24.66%,cuo的质量分数为54.37%,zno的质量分数为10.27%。
60.参照对比例4:
61.称cu(no3)2·
3h2o 483.20g,zn(no3)2·
6h2o 109.85g溶解在装有1000ml 脱盐水烧杯中,搅拌使其完全溶解,补充脱盐水并定容至4000ml,配制得到盐溶液a。称取na2co
3 279.02g,溶解在装有1000ml脱盐水烧杯中,搅拌使其完全溶解,补充脱盐水并定容至4000ml,配制得到碱溶液b。
62.称载体化合物al2o3(bet比表面积为249cm2/g,平均孔径为9nm,孔容为0.95cm3/g)72.16g加入装有4000ml脱盐水烧杯中,搅拌使其形成均质悬浊液,补充脱盐水并定容至4000ml,配制得到载体悬浊液c。
63.对盐溶液a、碱溶液b及载体悬浊液c进行预热,预热至反应温度80℃,同时控制反应釜温度为80℃,当温度达到要求后,先开启反应釜搅拌器并调整搅拌速度为120r/min,然后盐碱溶液并流加入反应釜中进行等体积并流共沉淀反应,沉淀反应同时等体积等速加入载体悬浊液c。控制沉淀反应过程ph值为8.5,控制沉淀反应时间0.2h,反应完成后进行老化反应,老化温度80℃,老化时间4h,老化完成后的前驱体化合物浆料过滤掉大部分母液,滤饼采用3000ml脱盐水进行再浆,再浆完成后再次进行过滤。多次再浆过滤合格后得到的滤饼中添加适量的热脱盐水进行厢式干燥,干燥温度120℃,干燥时间15h,得到催化剂前驱体干燥粉料343.81g,放入煅烧炉中进行煅烧,煅烧温度为400℃,煅烧时间为3h,得到催化剂煅烧粉料275.05g,冷却后对其进行造粒,颗粒尺寸控制为40目~80目,加入6.0g 石墨和18.0g水进行充分混合,然后进行压片成型得到铜系甲醇制氢催化剂对比样品4,记为com.4,其中al2o3的质量分数为24.66%,cuo的质量分数为54.37%,zno的质量分数为10.27%。
64.参照对比例5:
65.称cu(no3)2·
3h2o 483.20g,zn(no3)2·
6h2o 109.85g溶解在装有1000ml 脱盐水烧杯中,搅拌使其完全溶解,补充脱盐水并定容至4000ml,配制得到盐溶液a。称取na2co
3 279.02g,溶解在装有1000ml脱盐水烧杯中,搅拌使其完全溶解,补充脱盐水并定容至4000ml,配制得到碱溶液b。
66.称载体化合物al2o3(bet比表面积为180cm2/g,平均孔径为6nm,孔容为0.42cm3/g,拟薄水铝石550℃恒温煅烧5h)72.16g加入装有4000ml 脱盐水烧杯中,搅拌使其形成均质悬浊液,补充脱盐水并定容至4000ml,配制得到载体悬浊液c。
67.对盐溶液a、碱溶液b及载体悬浊液c进行预热,预热至反应温度80℃,同时控制反应釜温度为80℃,当温度达到要求后,先开启反应釜搅拌器并调整搅拌速度为120r/min,然后盐碱溶液并流加入反应釜中进行等体积并流共沉淀反应,沉淀反应同时等体积等速加入载体悬浊液c。控制沉淀反应过程ph值为8.5,控制沉淀反应时间0.2h,反应完成后提高反应釜内前驱体化合物强化均质晶化温度升至150℃、反应釜压力升至0.5mpa,其升温速度为4
℃/min,升压速度0.05mpa/min,搅拌速度为20r/min,强化均质晶化时间1.0h。强化均质晶化完成后的前驱体化合物浆料过滤掉大部分母液,滤饼采用5000ml脱盐水进行再浆,再浆完成后再次进行过滤。多次再浆过滤合格后得到的滤饼中添加适量的热脱盐水进行均质处理。均质处理后的浆料,送至流化床器进行喷雾干燥,控制颗粒尺寸为80目~120目。喷雾干燥完成后取出催化剂前驱体干燥粉料291.37g,放入煅烧炉中进行煅烧,煅烧温度为350℃,煅烧时间为4h,得到催化剂煅烧粉料271.25g,冷却后加入6.0g石墨和17.0g水进行充分混合,然后进行压片成型得到铜系甲醇制氢催化剂对比样品5,记为com.5,其中al2o3的质量分数为24.66%, cuo的质量分数为54.37%,zno的质量分数为10.27%。
68.参照对比例6:
69.称cu(no3)2·
3h2o 483.20g,zn(no3)2·
6h2o 109.85g溶解在装有1000ml 脱盐水烧杯中,搅拌使其完全溶解,补充脱盐水并定容至4000ml,配制得到盐溶液a。称取na2co
3 279.02g,溶解在装有1000ml脱盐水烧杯中,搅拌使其完全溶解,补充脱盐水并定容至4000ml,配制得到碱溶液b。
70.称载体化合物al2o3(bet比表面积为249cm2/g,平均孔径为9nm,孔容为0.95cm3/g)72.16g加入装有4000ml脱盐水烧杯中,搅拌使其形成均质悬浊液,补充脱盐水并定容至4000ml,配制得到载体悬浊液c。
71.对盐溶液a、碱溶液b及载体悬浊液c进行预热,预热至反应温度80℃,同时控制反应釜温度为80℃,当温度达到要求后,先开启反应釜搅拌器并调整搅拌速度为120r/min,然后盐碱溶液并流加入反应釜中进行等体积并流共沉淀反应,沉淀反应同时等体积等速加入载体悬浊液c。控制沉淀反应过程ph值为8.5,控制沉淀反应时间0.2h,反应完成后密封反应釜进行晶化处理,在110℃的条件下保温13h,得到共沉淀产物。取出共沉淀产物直接进行干燥,干燥温度105℃,干燥时间3h,然后对干燥物料进行煅烧,煅烧温度600℃,煅烧时间5h,得到催化剂煅烧粉料275.05g,冷却后对其进行造粒,颗粒尺寸控制为40目~80目,加入6.0g石墨和18.0g水进行充分混合,然后进行压片成型得到铜系甲醇制氢催化剂对比样品6,记为com.6,其中al2o3的质量分数为24.66%,cuo的质量分数为54.37%,zno 的质量分数为10.27%。
72.表1.催化剂物化性质测试表
73.实施例催化剂bet比表面积(m2/g)平均孔径(nm)孔容(cm3/g)cuo尺寸(nm)实施例1cat1113.814.20.425~20实施例2cat2114.515.30.416~18实施例3cat3112.016.90.506~15实施例4cat4110.916.30.455~14实施例5cat5120.3517.10.526~13对比例1com.191.59.250.294~38对比例2com.285.87.120.2725~47对比例3com.384.57.480.2627~55对比例4com.4110.213.120.393~42对比例5com.590.38.950.284~22对比例6com.6108.512.800.3626~49
74.表2:实施例催化剂性能评价结果:
[0075][0076][0077]
表3:实施例催化剂毒化实验结果:
[0078][0079]
催化剂综合性能评价:
[0080]
实施例中催化剂物化性质的测试数据如表1。从表中测试数据可以看出,改性氧化铝载体的添加显著改善催化剂的织构性质及物化性能,催化剂的bet比表面积、平均孔径及孔容显著更高,铜晶粒尺寸分布更优。具体地,相对对比实施例com.1,bet比表面积提升可达31.5%,平均孔径提升可达84.9%,孔容提升可达85.7%;相比较对比实施例com.3,bet比表面积提升可达42.4%,平均孔径提升可达128.6%,孔容提升可达100%。
[0081]
另外对比例2中晶化时间过长及晶化温度过低对催化剂的物化性能造成了不利影响,其cuo颗粒尺寸持续长大至25nm~47nm,对比例3中在常温下沉淀且采用氨水作为碱溶液滴加方式,其cuo颗粒尺寸持续长大至 27nm~55nm。对比例4中只采用改性氧化铝对催化剂改性,无浆料均质晶化处理过程,其cuo颗粒尺寸分布较大,对比例5中采用普通氧化铝作为铝源,对浆料进行均质晶化处理,其cuo颗粒尺寸分布得到改善,但催化剂的bet比表面积、孔容及孔径等相对较小,对比例6中采用改性氧化铝对催化剂改性,并采用常规晶化处理过程进行晶化,晶化时间过长及净化温度过低仍对催化剂的物化性能造成了不利影响。
[0082]
采用大型化甲醇制氢工艺条件对上述催化剂进行性能评价,催化剂在性能评价前
需要进行还原,即用2.0%h2/n2在230℃、0.3mpa、气空速1000h-1
等条件下对催化剂进行还原,催化剂还原完成后注入水醇比(摩尔比)为1.6 的甲醇水溶液,控制在反应液空速2.0h-1
、反应温度260℃、反应压力2.80mpa 的大型化甲醇制氢工艺条件下评价催化剂,评价结束后停止进料并在400℃下热处理10h,再评价过热后的催化剂性能,评价结果详见表2。另外,对催化剂进行抗毒性能对比考察,即大型化甲醇制氢反应条件不变,在原料甲醇水溶液中配入硫醇,控制硫醇含量为30ppm,连续运行50h,评价结果见表3。
[0083]
由表2测试结果可知:催化剂cat1~5的催化反应性能明显优于催化剂 com.1~3,耐热处理前,同样反应条件下甲醇转化率提升比例最高可达 23.69%,氢气选择性相对提升最高达14.35%,反应气中co等杂质含量显著更低。耐热处理后,甲醇转化率相对提高比例可达最高可达31.21%,氢气选择性相对提升最高可达21.73%,催化剂cat1~5的转化性能下降比例最低仅为1.5%,而对比例转化下降比例高达9.25%,这说明与现有技术相比,催化剂的热稳定性等综合性能得到了显著提升。
[0084]
并且,由表3中抗毒性能考察结果可知:运行50h以后,cat1~5的甲醇转化率下降比例为5%~7%,氢气选择性下降比例为1%~2%,而对比例的甲醇转化率下降比例为9%~16%,氢气选择性下降比例为4%~8%,这说明本发明制备的催化剂具有更优的抗毒性能。
[0085]
由此可知:采用本发明制备的铜基甲醇制氢催化剂比对比实施例的催化剂具有更为优异的催化活性及氢气选择性,特别是催化剂的热稳定性和抗毒性能得到显著改善,且更适合在大型化甲醇制氢装置上使用。
[0086]
以上所述仅为本发明的较佳实施例而已,并不用以限制本发明,凡在本发明的精神和原则之内所作的任何修改、等同替换和改进等,均应包含在本发明的保护范围之内。
再多了解一些
本文用于企业家、创业者技术爱好者查询,结果仅供参考。