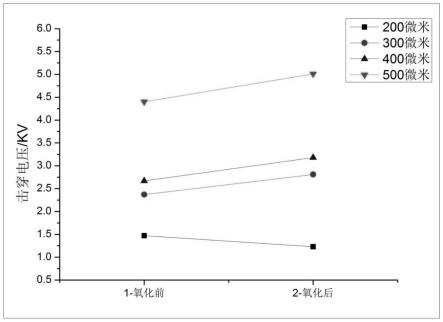
1.本发明涉及钛合金材料表面处理技术领域,尤其涉及一种钛合金材料表面处理方法。
背景技术:
2.钛合金作为一种质轻、高强、耐腐蚀的优异轻型结构材料,能够显著提升舰船装备性能,增强海洋安全保障能力。钛合金在舰船上主要用来制造耐压壳体、热交换器、冷凝器、核反应堆外壳以及海水管路系统。
3.舰船海水管路系统采用了大量不同材质的金属材料,如铜合金、钛合金、船体钢等。不同材质的设备及附件在服役过程中不可避免的存在异种金属接触现象,如铜合金、钛合金和钢之间的连接,在该条件下,不同材料之间较大的电位差易导致电偶腐蚀现象的发生,加速低电位金属的腐蚀,从而导致装备快速腐蚀失效。钛基体本身电位较高,因此作为阀门等部件使用时,易与第二相/外接异种金属发生电偶腐蚀,严重影响了舰船装备服役可靠性。
4.现有的解决钛合金电偶腐蚀问题的主要技术是在钛合金表面制备一层绝缘氧化膜层,通过绝缘保护隔绝接触电位,避免电偶腐蚀的发生。如申请号cn202010283355.1的发明专利《一种钛合金复合氧化膜层的制备方法及其产品》中,制备的微弧氧化膜层摩擦系数在0.3~0.6,且具有较好的结合强度和耐磨性。申请号cn1386917的发明专利《一种钛合金微弧氧化技术》中,制备的微弧氧化膜层厚度为2~10μm,表面硬度可达hv700,电阻可达5
×
106ω。申请号cn102199785的发明专利《一种钛合金耐磨涂层的微弧氧化溶液及其应用》中,制备的微弧氧化膜层厚度为10~40μm,表面硬度可达hv700。采用上述方法在钛合金表面制备的绝缘保护层存在力学性能较差的问题,主要表现在抗拉强度和抗压强度等性能较差,不能满足钛合金阀门法兰部位涂层的高强度和密性使用要求,现多采用等离子喷涂的方法在法兰部位制备绝缘陶瓷涂层,若先进行微弧氧化后进行等离子喷涂,等离子喷涂过程中搬运、工装加持、遮蔽困难和极端高温环境会使微弧氧化膜层难以完整保留,从而起不到绝缘保护效果。目前,尚未有在钛合金表面制备可经受微弧氧化处理的陶瓷涂层的发明专利来解决上述问题。因此,进行本项发明前,按照申请号zl200910227584.5的发明专利《一种涂覆陶瓷绝缘涂层的金属法兰及其制备方法》在钛合金法兰部位制备了陶瓷涂层,经钛合金酸性微弧氧化工艺处理后,陶瓷涂层出现了起皮、脱落现象。
技术实现要素:
5.有鉴于此,本发明旨在提供一种钛合金材料表面处理方法,采用高速等离子喷涂技术制备一层绝缘、耐磨、抗拉、抗压的复合陶瓷涂层,并通过涂层磨抛加工控制涂层表面粗糙度及平面度来满足法兰密性要求,在钛合金阀门阀体部位采用微弧氧化技术制备一层绝缘、耐磨的微弧氧化膜层,解决了钛合金阀门服役过程中面临的电偶腐蚀、磨损泄露等的问题。
6.为达到上述目的,本发明的技术方案是这样实现的:
7.一种钛合金材料表面处理方法,包括:
8.s100、进行材料预处理,根据需要将钛合金材料胚料进行机械加工,制成工件,去除工件表面油脂,遮蔽非喷涂部位,喷砂处理;
9.s200、等离子喷涂,在材料表面喷涂镍基金属过渡层,然后喷涂氧化铝钛陶瓷涂层;
10.s300、对上述涂层进行磨削抛光处理,微晶石蜡封孔,对处理后的表面进行水洗;
11.s400、将除油水洗过的工件作为阳极,不锈钢/石墨板作为阴极进行微弧氧化;
12.s500、对工件进行水洗,烘干。
13.进一步地,在步骤s200中,喷涂镍基金属过渡层的厚度为0.06-0.1mm。
14.进一步地,镍基金属过渡层的材料为15-45μm粒度的球形粉末。
15.进一步地,镍基金属过渡层的化学成分及含量包括70-80重量分的ni、10-20重量分的cr,2-5重量分的b和4-7重量分的si。
16.进一步地,喷涂镍基金属过渡层的工艺参数包括:
17.喷涂电流为650-750a,喷涂电压为30-40v,主气压力为0.6-0.8mpa,主气流量为60-80l/min,辅气压力为0.4-0.6mpa,辅气流量为4-10l/min,载气流量为5-8l/min,送粉速度为10-20g/min,喷涂距离为90-105mm,喷涂角度为60
°‑
90
°
,喷涂速度为420-530mm/s,喷涂步距为2.5-3.5mm。
18.进一步地,在步骤s200中,氧化铝钛陶瓷涂层的厚度为0.2-0.4mm。
19.进一步地,氧化铝钛陶瓷涂层的化学成分及含量包括75-85重量分的al2o3,10-20重量分的tio2,3-8重量分的ceo2,2-4重量分的sio2。
20.进一步地,喷涂氧化铝钛陶瓷涂层的工艺参数包括:
21.喷涂电流为690-800a,喷涂电压为45-60v,主气压力为0.6-0.8mpa,主气流量为60-80l/min,辅气压力为0.4-0.6mpa,辅气流量为4-10l/min,载气流量为5-8l/min,送粉速度为35-45g/min,喷涂距离为90-105mm,喷涂角度为60
°‑
90
°
,喷涂速度为420-530mm/s,喷涂步距为2.5-3.5mm。
22.进一步地,在步骤s400中,用于微弧氧化的电解液成分包括硫酸120-200g/l,磷酸5-10g/l和水。
23.进一步地,微弧氧化控制电参数包括:
24.电流密度:正向6-14a/dm2,负向2-3a/dm2;
25.占空比:正向40%-60%,正向40%-50%;
26.级数:正向1级,负向1级;
27.控制时间为10-20min。
28.相对于现有技术,本发明所述的一种钛合金材料表面处理方法,具有以下优势:
29.本技术方案优点在于在钛合金阀门法兰部位制备一层可经受微弧氧化处理的绝缘、耐磨、抗拉、抗压复合陶瓷涂层,在钛合金阀门阀体部位制备一层绝缘、耐磨的微弧氧化膜层,且复合陶瓷涂层,微弧氧化膜层均完整,无剥落、宏观裂纹等缺陷。引入金属过渡层,提高了涂层与基体的结合强度,减小了应力集中。氧化铝钛陶瓷涂层中添加ceo2提高了涂层的致密度,添加sio2提高了涂层的耐酸性能。经微弧氧化工艺处理后绝缘电阻增大,绝缘
等级上升,在海洋环境下不易发生电偶腐蚀、磨损泄露。
附图说明
30.构成本发明的一部分的附图用来提供对本发明的进一步理解,本发明的示意性实施例及其说明用于解释本发明,并不构成对本发明的不当限定。在附图中:
31.图1为本发明实施例所述的不同厚度陶瓷涂层微弧氧化处理前后扫描及能谱图;
32.图1a为本发明实施例所述的陶瓷涂层微弧氧化处理前微观形貌;
33.图1b为本发明实施例所述的200μm陶瓷涂层处理后微观形貌;
34.图1c为本发明实施例所述的300μm陶瓷涂层处理后微观形貌;
35.图1d为本发明实施例所述的400μm陶瓷涂层处理后微观形貌;
36.图1e为本发明实施例所述的500μm陶瓷涂层处理后微观形貌;
37.图1f为本发明实施例所述的陶瓷涂层处理前后能谱结果;
38.图2为本发明实施例所述的不同厚度陶瓷涂层微弧氧化处理后绝缘电阻的柱状图;
39.图3为本发明实施例所述的不同厚度陶瓷涂层微弧氧化处理后绝缘等级的折线图。
具体实施方式
40.需要说明的是,在不冲突的情况下,本发明中的实施例及实施例中的特征可以相互组合。
41.下面将参考附图并结合实施例来详细说明本发明。
42.一种钛合金材料表面处理方法,包括:
43.s100、进行材料预处理,根据需要将钛合金材料胚料进行机械加工,制成工件,去除工件表面油脂,遮蔽非喷涂部位,喷砂处理;
44.s200、等离子喷涂,在材料表面喷涂镍基金属过渡层,然后喷涂氧化铝钛陶瓷涂层;
45.喷涂镍基金属过渡层的厚度为0.06-0.1mm,材料为15-45μm粒度的球形粉末,化学成分及含量包括70-80重量分的ni、10-20重量分的cr,2-5重量分的b和4-7重量分的si,喷涂镍基金属过渡层的工艺参数包括:喷涂电流为650-750a,喷涂电压为30-40v,主气压力为0.6-0.8mpa,主气流量为60-80l/min,辅气压力为0.4-0.6mpa,辅气流量为4-10l/min,载气流量为5-8l/min,送粉速度为10-20g/min,喷涂距离为90-105mm,喷涂角度为60
°‑
90
°
,喷涂速度为420-530mm/s,喷涂步距为2.5-3.5mm。
46.氧化铝钛陶瓷涂层的厚度为0.2-0.4mm,氧化铝钛陶瓷涂层的化学成分及含量包括75-85重量分的al2o3,10-20重量分的tio2,3-8重量分的ceo2,2-4重量分的sio2,喷涂氧化铝钛陶瓷涂层的工艺参数包括:喷涂电流为690-800a,喷涂电压为45-60v,主气压力为0.6-0.8mpa,主气流量为60-80l/min,辅气压力为0.4-0.6mpa,辅气流量为4-10l/min,载气流量为5-8l/min,送粉速度为35-45g/min,喷涂距离为90-105mm,喷涂角度为60
°‑
90
°
,喷涂速度为420-530mm/s,喷涂步距为2.5-3.5mm。
47.s300、对上述涂层进行磨削抛光处理,微晶石蜡封孔,对处理后的表面进行水洗;
48.s400、将除油水洗过的工件作为阳极,不锈钢/石墨板作为阴极进行微弧氧化;
49.用于微弧氧化的电解液成分包括硫酸120-200g/l,磷酸5-10g/l和水,微弧氧化控制电参数包括:电流密度:正向6-14a/dm2,负向2-3a/dm2;占空比:正向40%-60%,正向40%-50%;级数:正向1级,负向1级;控制时间为10-20min。
50.s500、对工件进行水洗,烘干。
51.以下以具体实施例详细说明上述方法。
52.实施例1
53.一、复合陶瓷涂层的制备:选用牌号为ti80的样件,首先使用无水乙醇进行除油处理,然后使用铝箔胶带将除法兰喷涂区域外非喷涂部位全部保护,后使用16目的棕刚玉进行喷砂。金属过渡层所用材料为ni 74%、cr 16%、b 4%和si 6%球形粉末,粒度为15~45μm,喷涂工艺参数见表1,涂层厚度98μm。陶瓷涂层所用材料为al2o
3 80%,tio
2 12%,ceo
2 8%和,sio
2 3%的球形粉末,粒度为15~45μm,喷涂工艺参数见表2。然后在磨床上使用金刚石砂轮进行磨削,保证粗糙度≤3.2μm,最后将涂层预热到100℃使用微晶石蜡进行封孔处理。
54.表1
[0055][0056]
表2
[0057][0058]
二、微弧氧化电解液的配制:硫酸150g/l、磷酸7g/l和蒸馏水组成,溶液温度应控制在30℃以下。
[0059]
三、微弧氧化膜层的制备:将样件经过除油水洗后连接电源阳极置于配制好的电解液溶液中进行氧化膜的制备,工装与溶液的界面处应采用绝缘胶带隔开,微弧氧化装置为最大平均电流500a的交流脉冲电源。电参数见表3。
[0060]
表3
[0061][0062]
制得的微弧氧化膜层完好,厚度21μm,硬度706hv
0.1
,复合陶瓷涂层厚度303μm,体积电阻率约10
12
ω
·
m,结合强度40mpa,压溃强度>450mpa,显微硬度约905hv
0.1
。
[0063]
实施例2
[0064]
一、复合陶瓷涂层的制备:选用牌号为ti80的样件,首先使用无水乙醇进行除油处理,然后使用铝箔胶带将除法兰喷涂区域外非喷涂部位全部保护,后使用16目的棕刚玉进行喷砂。金属过渡层所用材料为ni 76%、cr 16%、b 3%和si 5%球形粉末,粒度为15~45μm,喷涂工艺参数见表4,涂层厚度98μm。陶瓷涂层所用材料为al2o
3 80%,tio
2 12%,ceo
2 7%和,sio
2 4%的球形粉末,粒度为15~45μm,喷涂工艺参数见表5。然后在磨床上使用金刚石砂轮进行磨削,保证粗糙度≤3.2μm,最后将涂层预热到100℃使用微晶石蜡进行封孔处理。
[0065]
表4
[0066][0067][0068]
表5
[0069][0070]
二、微弧氧化电解液的配制:硫酸150g/l、磷酸7g/l和蒸馏水组成,溶液温度应控制在30℃以下。
[0071]
三、微弧氧化膜层的制备:将样件经过除油水洗后连接电源阳极置于配制好的电解液溶液中进行氧化膜的制备,工装与溶液的界面处应采用绝缘胶带隔开,微弧氧化装置为最大平均电流500a的交流脉冲电源。电参数见表8。
[0072]
制得的微弧氧化膜层完好,厚度22μm,硬度711hv
0.1
,复合陶瓷涂层厚度315μm,体
积电阻率约10
12
ω
·
m,结合强度42mpa,压溃强度>450mpa,显微硬度882hv
0.1
。
[0073]
通过上述方法,不同厚度陶瓷涂层微弧氧化处理前后扫描及能谱结果如图1所示。同厚度陶瓷涂层微弧氧化处理后绝缘电阻如图2所示。不同厚度陶瓷涂层微弧氧化处理后绝缘等级如图3所示。
[0074]
本领域技术人员在考虑说明书及实践这里公开的发明后,将容易想到本发明的其它实施方案。本技术旨在涵盖本发明的任何变型、用途或者适应性变化,这些变型、用途或者适应性变化遵循本发明的一般性原理并包括本公开未公开的本技术领域中的公知常识或惯用技术手段。说明书和实施例仅被视为示例性的,本发明的真正范围和精神由下面的权利要求指出。
[0075]
应当理解的是,本发明并不局限于上面已经描述并在附图中示出的精确结构,并且可以在不脱离其范围进行各种修改和改变。本发明的范围仅由所附的权利要求来限制。
再多了解一些
本文用于企业家、创业者技术爱好者查询,结果仅供参考。