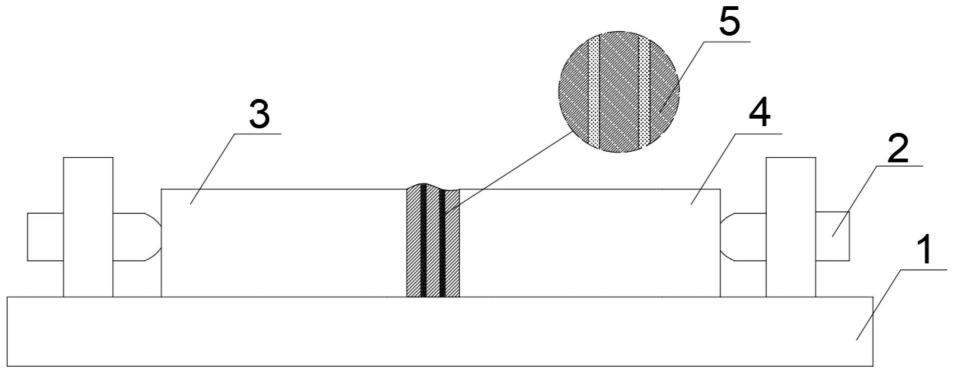
1.本发明属于搅拌摩擦焊技术领域,尤其是一种4米以上超长薄板的搅拌摩擦焊接技术,具体地说是一种降低超长薄板搅拌摩擦焊接变形的方法。
背景技术:
2.铝合金具有较好的强度、耐腐蚀性能好、加工性能好、质地轻且柔软等优势,目前已经大规模使用于航空航天、轨道交通等领域。
3.目前,铝合金焊接主要采用氩弧焊焊接方法,其成本高,绿色性差,氩气电离势较高,引弧困难,需要采用高频引弧以及稳弧装置。焊接后的焊缝不平整,晶粒粗大。现阶段,节能减排和绿色环保的标准进行新一轮提高,传统的焊接技术已经不能满足于绿色标准化制造要求,搅拌摩擦焊作为新兴焊接技术,其焊接过程不需要熔化金属,能一次完成较长焊缝、较大截面的焊接,不会产生弧光、烟雾等污染的优点完全好于传统焊接。
4.航空航天领域广泛使用搅拌摩擦焊焊接长尺寸铝合金贮箱,轨道交通领域使用搅拌摩擦焊焊接长尺寸车厢箱体。一般在焊接这些超长且较薄的铝合金板材时,大多使用定制化夹具进行装夹紧固,通常预紧力较大,使两铝合金板材能够边对边贴紧,以此防止在焊接过程中板材错动影响焊接质量。但是一方面由于超长薄板受到夹具夹紧,内部会有比较大的应力,在焊接完成过后撤去夹具时会有很大的残余应力,会影响板材的抗拉强度。另一方面,超长薄板在夹紧时由于尺寸长,对接尺寸精度要求一致性差。同时由于板材是长尺寸的板材,夹具的力会在缝隙方向上随距离的增加而分散,这就导致了夹紧不足,缝隙增加。一般情况下,设计人员会进行夹具设计来提高夹紧的精度,对工艺上的要求大大增加的同时,对于长尺寸板材的夹紧精度还是很难保证。
5.为了解决这一问题,专利号为cn106735860b的专利中提出在对接焊接中使用mg粉和al粉机械混合的粉末进行缝隙填补,弥补因对接精度的不足带来的焊接质量影响。但是这样的方式存在缺陷,首先是使用粉末填充焊接缝隙,当焊接表层时,机械混合后的粉末芯层在搅拌摩擦焊时会出现“团聚”现象,产生空洞缺陷,造成焊接质量的下降。其次是使用粉末填充焊接缝隙,粉末填充定位效果差,即便使用滚压的方法,也会在焊接微小振动下产生分散,会产生内部空洞缺陷。同时,粉末状填充材料会出现在对接缝隙填充率较低的问题,在长尺寸焊接中更难达到填充率的标准。其次在专利号为cn111299803a的专利中提出泡沫铝合金三明治板搭接拼焊方法,在两待焊接泡沫铝中间加入发泡粉末混合体,这种方法使得粉末均匀不分散,但是发泡剂本身会携带气孔,两板材放置也会存在空隙,气孔难以排出,使用搅拌摩擦焊后,会在焊接接头内部留下空洞缺陷,同时在工艺要求上该方法大多适用搭建焊接,对接焊接形式不太适用。
技术实现要素:
6.本发明的目的是针对现有的长薄板搅拌摩擦焊接过程中易出现变形及克服变形操作复杂,产生空洞缺陷的问题,发明一种降低超长薄板搅拌摩擦焊焊接变形的方法。
7.本发明的技术方案是:
8.一种降低超长薄板搅拌摩擦焊焊接变形的方法,其特征是使用覆粉(铝粉与锡粉的混合体)铝箔作为焊板对接中间层的焊接方法,能够有效地解决长尺寸薄板夹紧易变形以及焊接质量在线性焊缝上参差不齐的问题,不仅降低了对板材尺寸精度一致性要求,改善了工艺,也降低了板材因夹紧引起的残余应力,提高了板材的抗拉强度。这种方式,比全粉末形式简单方便。全粉末方式在焊之前要有刮粉过程。而如果只单纯几层铝箔,其调整间隙能力有限。本发明使用几层涂粉覆盖在铝箔上的方式,定位放置也相对简单,能极大降低焊接过程中的横向夹紧力(即垂直于接口方向),也能降低因横向夹紧力导致的残余应力,从而提高接口疲劳强度,同时,由于粉末涂抹技术具有柔性化的优势,可以在夹紧力的作用下,自动调整,实现完全填充缝隙。
9.本发明综合搅拌摩擦焊焊接长尺寸薄板的问题解决方案,在薄铝箔片上均匀粘黏多层细密铝粉,通过滚压的方法,制作不同厚度的铝箔片。依据预装夹的板材缝隙大小,匹配相应的薄铝箔片,将薄铝箔片放置在板材对接缝隙中,再进行弱装夹,依靠弱预紧力使得铝箔片上的铝粉层能够变形,使得在缝隙中的填充率提高,形成夹心拼接件。最后再进行搅拌摩擦焊焊接对接板材。本方法可以有效的解决粉末填充焊缝技术的定位不准确的问题,同时也改善了夹紧工艺,降低了板材的变形,有效地提高了焊接质量,具有很强的新颖性和创造性。
10.具体步骤是:
11.(1)将两块厚度为2~6mm的铝合金待焊接板材上下横置叠放,将对接靠近的边同步打磨平整。按《铝合金薄板搅拌摩擦焊工艺规范》要求,针对2~6mm铝合金薄板,打磨效果应使得对接缝隙小于0.2mm。
12.(2)取标准化制造轧制成型铝箔片为覆粉基体,其厚度取0.03~0.05毫米。
13.(3)利用型号为qm-3sp2行星球磨机对铝合金进行粉末研磨,在研究中发现加入锡可以强化金相,降低脆性,所以在球磨机中也加入锡。锡和铝的粉末比为0.28~0.44,球料比为13:3,旋转速度为300~1000rpm,球磨后的混合粉体尺寸为0.5~1微米;球磨时间在38h~52h之间。
14.(4)分层覆膜。将0.5~2g混合粉末用丙酮(高温易挥发)稀释成糊状,混合粉末质量选择参考如下式,粉末质量:覆膜面积=1:20(即0.1g混合粉末用丙酮稀释能够涂抹在20mm2的铝箔片上),使用上浆机均匀涂抹在铝箔片上,覆膜厚度为0.01~0.03mm,覆膜面积为(搅拌摩擦焊焊接板材厚度 h)mm
×
(0.01~0.03)mm,h为覆膜余量,其值范围为0.8倍待焊接板材厚度~1.5倍待焊接板材厚度。长度依据焊接板材长度进行截取确定,一般确定长度大于对接长度40~80mm,便于操作人员在板材两头取放。
15.(5)将两铝合金薄板放在垫板上,使用配套夹具进行弱夹紧。测量对接缝隙的最大值。
16.(6)依据测量的缝隙最大值,对铝箔片夹层进行叠放形成焊接辅助材料,辅助焊接材料的厚度应该大于对接缝隙宽度的最大值。加层量可以视对接缝隙的大小进行匹配。定义匹配系数为夹紧后的对接缝隙宽度和辅助焊接材料宽度之比,该匹配系数为0.67,即对接缝隙宽度:辅助焊接材料宽度为2/3。
17.(6)使用滚压工艺,对辅助焊接材料进行弱滚压,排去气孔。
18.(7)对弱夹紧的板材进行卸荷,抬起一块板材,将选择好的辅助焊接材料夹放在两板材之间,使用夹具重新进行弱夹紧,使得辅助焊接材料能够变形,材料充分填充再对接缝隙中。
19.(8)调整上压板,压紧待焊接板材。
20.(9)设置搅拌摩擦焊焊接参数,进行长薄板焊接。
21.在上述技术方案中,对于母材厚度为t(2~6mm)的待焊接板材,搅拌摩擦焊焊接参数设置如下:搅拌头是圆台螺纹型搅拌头,6~10mm轴肩直径,搅拌针长度为[t-(0.1~0.2)]mm,0
°
~2
°
搅拌头倾角,搅拌头的转速为100~2000rpm,进给速度为50~1000mm/min,轴向下压量为0.1~0.3mm。
[0022]
本发明的有益效果是:
[0023]
①
在对接缝隙中使用粉末,可以有效填充缝隙,使焊接质量提高,但定位差,填充率难以保证。在缝隙中使用铝箔,可以改善焊接形貌,提高抗拉强度,但焊接有空洞缺陷,影响焊接质量。本发明将铝箔与粉末结合,使用铝粉、锡粉和硬脂酸镁组成亚稳态粉末,利用丙酮稀释成浆体,涂抹在铝箔片上形成组合。针对不同缝隙大小,辅助焊接材料可以叠加适应,是更好的柔性方案。
[0024]
②
针对长薄铝板焊接夹紧易变形且对接缝隙尺寸精度一致性差的问题,采用柔性辅助焊接材料,依靠弱夹紧力充分填充对接缝隙,提高焊接质量,减少焊接空洞缺陷。
[0025]
③
通常对于长薄铝板焊接,其夹具设计要求很高,既要保证适合的夹紧力,又要保证全长度的对接宽度一致。本发明提出使用粉体均匀分散的浆料涂覆柔性方法,焊缝间隙调整余量适应性广,降低了对板材尺寸精度一致性要求,也降低了板材因夹紧引起的残余应力。
[0026]
④
改善了粉末填充对接缝隙定位性差的问题,提高了粉末填充率。
[0027]
⑤
锡铝混合的亚稳态粉末,抑制了脆性相生成,焊接后飞边减少,表面成型更好。
[0028]
⑥
本发明不仅仅适用于国家对接搅拌摩擦焊标准缝隙,也可以扩展使用于非标准缝隙。对于对接缝隙超出国家标准缝隙的情况,任然可以通过本方法,提高焊接质量。
附图说明
[0029]
图1为铝合金薄板对接形式下填充焊接辅助材料的正视图。
[0030]
图2为相同厚度铝合金薄板搅拌摩擦焊焊接工艺示意图。
[0031]
图3为不同厚度铝合金薄板搅拌摩擦焊焊接工艺示意图。
[0032]
图4为本发明的搅拌头的结构示意图。
[0033]
图中:1-焊接工作台;2-夹具;3、4-薄铝板;5-焊接辅助材料;6-铝箔片;7-搅拌头;8-压板。
具体实施方式
[0034]
下面结合附图和实施例对本发明作进一步的说明。
[0035]
实施例1。
[0036]
如图1所示为两相同5a06-h112铝合金母材搅拌摩擦焊为例进行搅拌摩擦焊,铝合金母材的厚度为4mm,长度为5.5m的铝合金长薄板。步骤如下:
[0037]
①
将两板材上下横置叠放,将对接靠近的边同步打磨平整。同时去除打磨中产生的毛刺。将待焊接水平放置在焊接平台上,使用夹具进行预夹紧,测量对接最大缝隙为0.2mm,达到国家标准。松开夹具,对板材卸荷。
[0038]
②
利用型号为qm-3sp2行星球磨机对铝合金进行粉末研磨,在研究中发现加入锡可以强化金相,降低脆性,所以在球磨机中也加入锡。锡和铝的粉末比为11:27,球料比为13:3,旋转速度为400rpm。由于存在粉末团聚,在机械合金化时加入硬脂酸镁,防止粉末团聚。通过对原始粉末的球磨处理,使得在完成粉末成型后的混合粉末达到亚稳态,可以实现焊接后飞边较少,使得表面成型更好。经研究发现,研磨时间在40小时为最佳,所以选择研磨时间在40小时的混合粉末作为覆膜材料。
[0039]
③
取标准化制造轧制成型铝箔片为覆粉基体,其厚度取0.04毫米。将两铝合金板材分别放置在前进侧和后退侧。
[0040]
④
根据测量得到的最大缝隙值:0.2mm。取匹配系数为0.67,算得辅助焊接材料宽度为0.3mm。
[0041]
⑤
将2.76g混合粉末用丙酮稀释成糊状,使用上浆机均匀涂抹在铝箔片上,覆膜厚度为0.04mm,覆膜体积为10mm
×
0.02mm
×
5550mm。进行5层铝箔,4层粉末的叠加铺设,铺设后的辅助焊接材料宽度为0.36mm(注5层铝箔厚度为0.2mm,4层粉末的厚度为0.16mm,合计0.36)。
[0042]
⑥
使用滚压工艺,对辅助焊接材料进行弱滚压,排去气孔。对上述的三层铝箔,滚压前的厚度为0.36mm,滚压后的厚度为0.30mm。
[0043]
⑦
将选择好的辅助焊接材料夹放在两板材之间,使用夹具进行弱夹紧,使得辅助焊接材料能够变形,材料充分填充再对接缝隙中。
[0044]
⑧
调整上压板,向下压紧待焊接板材。调整辅助压紧装置,将辅助焊接材料压紧,如图2所示。
[0045]
⑨
如图4,采用fsw-lm2-1012搅拌摩擦焊机。设置搅拌摩擦焊焊接参数:搅拌头是圆台螺纹型搅拌头,搅拌针长3.8mm,5mm轴肩直径,3.8mm长搅拌针,2
°
搅拌头倾角,搅拌头的转速为900rpm,进给速度为100mm/min,轴向下压量为0.2mm。进行长薄板搅拌摩擦焊工艺加工。
[0046]
⑩
使用刮板,将底部多余的铝箔刮出,取下板材。
[0047]
本实例结果表明,焊接接头的飞边少,表面成型好。对于直接焊,接头的抗拉强度为94.5mpa,采用本发明焊接,接头强度达到146mpa,与直接焊相比,接头强度提高了55%。同时相比直接焊,板材的变形更小。
[0048]
实施例2。
[0049]
如图3,两不同厚度5a05铝合金母材搅拌摩擦焊,以一块厚度为4mm,一块厚度为5mm,长度均为4m的铝合金长薄板待焊接板材为例,进行搅拌摩擦焊(板材厚度2~5mm,厚度允许差值为1mm)。
[0050]
①
将两板材横置叠放,将对接靠近的边同步打磨平整。同时去除打磨中产生的毛刺。将待焊接放置在焊接平台上,使用夹具进行预夹紧,测量对接最大缝隙为0.13mm,达到国家标准。松开夹具,对板材卸荷。
[0051]
②
利用型号为qm-3sp2行星球磨机对铝合金进行粉末研磨,在研究中发现加入锡
可以强化金相,降低脆性,所以在球磨机中也加入锡。锡和铝的粉末比为26:59,球料比为13:3,旋转速度为400rpm。研磨时间42小时。
[0052]
③
取标准化制造轧制成型铝箔片为覆粉基体,其厚度取0.05毫米。
[0053]
将两铝合金板材分别放置在前进侧和后退侧。
[0054]
④
根据测量得到的最大缝隙值:0.13mm。取匹配系数为0.67,算得辅助焊接材料宽度为0.2mm。
[0055]
⑤
将1.62g混合粉末用丙酮稀释成糊状,使用上浆机均匀涂抹在铝箔片上,覆膜厚度为0.01mm,覆膜体积为8mm
×
0.01mm
×
4050mm。进行4层铝箔,3层粉末的叠加铺设,铺设后的辅助焊接材料宽度为0.23mm。
[0056]
⑥
使用滚压工艺,对辅助焊接材料进行弱滚压,排去气孔。对上述的三层铝箔,滚压前的厚度为0.23mm,滚压后的厚度为0.13mm。
[0057]
⑦
将选择好的辅助焊接材料夹放在两板材之间,使用夹具进行弱夹紧,使得辅助焊接材料能够变形,材料充分填充再对接缝隙中。
[0058]
⑧
调整上压板,压紧待焊接板材。调整辅助压紧装置,将辅助焊接材料压紧。
[0059]
⑨
如图4,采用fsw-lm2-1012搅拌摩擦焊机。设置搅拌摩擦焊焊接参数:搅拌头是圆台螺纹型搅拌头,搅拌针长4.8mm,6mm轴肩直径,3.8mm长搅拌针,2
°
搅拌头倾角,搅拌头的转速为1000rpm,进给速度为60mm/min,轴向下压量为0.3mm。进行长薄板搅拌摩擦焊工艺加工。
[0060]
⑩
使用刮板,将底部多余的铝箔刮出,取下板材。
[0061]
在本实例中,本方法可以焊接不同厚度的铝合金薄板,薄板对接。本实例结果表明,焊接接头的飞边较少,表面成型较好。对于直接焊,接头的抗拉强度为82.1mpa,采用本发明焊接,接头强度达到108.3mpa,与直接焊相比,接头强度提高了32%。
[0062]
本发明未涉及部分与现有技术相同或可采用现有技术加以实现。
再多了解一些
本文用于企业家、创业者技术爱好者查询,结果仅供参考。