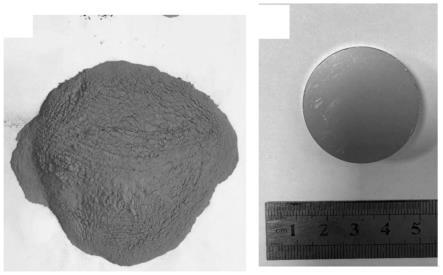
1.本发明属于铜合金材料制备技术领域,具体涉及一种高导电、高耐磨铜硼合金的制备方法。
背景技术:
2.cu(铜)及其合金因其优良的传导性能而被广泛应用于电力、电气等诸多领域。随着长距离特高压电网商业化运行,电压等级不断升高,变电站负载逐渐增大,相关产业对导电cu合金的要求越来越高,负责电网开断的关键核心部件之一的电触头需同时满足高导电、高耐磨的服役需求。研究表明,cu-b合金中溶质元素b(硼)在cu基体中的最大固溶度约为5at.%(约在1400℃),并且cu与b之间不反应形成化合物,导致合金中的b元素点状共晶或多面体初晶的形式分布于cu基体中,对基体的导电性影响较小。此外,b元素具有高硬度(仅次于金刚石)和自润滑的作用,使得合金系本身具有良好的耐磨性。因此,基于cu-b合金的众多优势,其在高导电、高耐磨电触头材料、高铁用导电铜材料等领域具有广泛的应用前景。
3.传统铸造法制备cu-b合金是将cu块与b块按配比加热熔化并保温一段时间,最终冷却凝固后获得铜硼合金,但由于cu元素与b元素的密度(cu:8.9g/cm3;2.34g/cm3)和熔点(cu:1084℃;b:2076℃)相差较大,导致熔炼过程由于溶质元素比重偏析使得b熔化后漂浮于cu液上部。同时,由于b在cu中固溶度较低,二者熔点相差极大,在高于cu熔点200-400℃时,b元素大多以单质颗粒形式存在于合金液中,难以形成合金相,此外,高温下b元素活性较高,易与氮氧等元素反应且易烧损。因此,采用外加b块的传统铸造法难以制备组织性能均一cu-b合金,同时在制备过程中易引入其他杂质导致合金纯净度降低,综合性能较差,难以满足苛刻的服役需求。综上,亟需探索一种新型cu-b合金制备方法,使cu-b合金组织成分均一并且兼具高导电、高耐磨的综合性能。
技术实现要素:
4.本发明的目的是提供一种高导电、高耐磨铜硼合金的制备方法,解决了现有技术中铸造法制备的cu-b合金的组织偏析、成分稳定性以及杂质含量有待进一步优化的问题。
5.本发明所采用的技术方案是,
6.一种高导电、高耐磨铜硼合金的制备方法,具体按照如下步骤进行:
7.步骤1:按照cu-b二元合金相图所设计的cu-b合金中b的含量,分别称量92wt.%~98wt.%的cu粉和2wt.%~8wt.%的b粉;
8.步骤2:将称量好的b粉和cu粉装入混料容器中并加入分散剂,采用v型混料、振动混粉、行星式球磨机混粉三种方式进行混合;然后将混合均匀的cu-b预合金粉体通过冷压模具在四柱式油压机上进行预压制成型,形成坯料;
9.步骤3:将步骤2得到的坯料装入石墨坩锅中,然后将石墨坩锅放入真空感应熔炼炉,采用预抽真空后充氩气的方式进行感应熔炼;待坯料完全熔化后保温,然后采用底注式
浇注方式将cu-b合金液经导流管流入石墨模具中,待随炉冷却凝固后即得到一种高导电、高耐磨cu-b合金。
10.本发明的特点还在于;
11.步骤1中,cu粉为电解铜粉。
12.步骤2中:采用v型混料机进行混粉,设定转速为100~300r/min,球料比为1:3~1:6,混合时间为60~240min,磨球粒径为3~9mm;采用振动混料机进行混粉,设定频率为30~50hz,球料比为1:3~1:6,混合时间为240~480min,磨球粒径3~9mm;采用行星式球磨机进行混粉,设定转速为100~200r/min,球料比为1:6~1:10,混合时间为240~480min,磨球粒径3~9mm。
13.步骤2中,分散剂可为无水乙醇。
14.步骤2中,将混合均匀的cu-b预合金粉体过筛后倒入冷压模具,分若干次倒入粉末并进行摆动振实,然后利用四柱式油压机进行压制,压制压力为300kn,保压20~40s形成cu-b预合金坯体。
15.步骤3具体为:在石墨坩埚内安装内径为3~6mm的熔体导流管,将坯料依次装入坩锅内,保证下紧上松,并将坩埚整体放入感应线圈内进行熔炼,石墨坩锅所装坯料不超过坩锅深度的三分之二,并用刚玉管封堵导流管口;封闭炉体后采用三级泵抽系统对腔室预抽真空,当熔炼室内真空度低于9.0
×
10-3
pa后,向熔炼室内充入保护气体至腔室总压力达到-0.05~0.01mpa;熔炼流程为:使用中频感应电源在20min将温度升至1250~1450℃并保温5~10min使合金液充分均匀化;保温结束后,将刚玉管拔起,坩埚内的金属熔体通过底部导流管浇注至高纯石墨内进行冷却凝固;当冷却到室温时取出cu-b合金坯料,对坯料表面经机加工处理得到cu-b合金。
16.步骤3中,三级泵抽系统包括机械泵、罗茨泵、扩散泵。
17.本发明的有益效果是,本发明一种高导电、高耐磨铜硼合金的制备方法,通过采用粉末冶金与真空感应熔炼相结合的方式,首先利用粉末冶金混粉工艺,将cu粉与b粉两种粉末原料在一定的混粉工艺下混合均匀制备cu-b预合金粉体,并将粉体冷压成型形成坯料,解决了外加b元素的传统铸造法因cu与b密度、熔点等物理性能相差较大,导致cu、b两相单质难以均匀混合形成合金相的问题;
18.然后,通过真空感应熔炼方式,采用预抽真空再加氩气保护进行坯料熔炼获得均匀的cu-b合金液,一方面保证熔体纯净,另一方面熔炼室气压大于b元素在熔炼温度下的饱和蒸汽压,大幅降低了b元素烧损;通过导流管将合金液浇注进高纯石墨坩埚,熔体通过小口径导流管内部时产生一定的扰动效果,提高了合金液混合均匀程度,改善了cu-b合金比重偏析,因此,最终制备出表面质量良好、成分稳定、组织均匀,硬度大于89hv,导电率高于78%iacs,摩擦系数介于0.57~0.69,磨损形貌为粘着磨损的高硬度、高导电、高耐磨的cu-b合金,具有一定的实用意义。
附图说明
19.图1是本发明一种高导电、高耐磨铜硼合金的制备方法的实施例3中采用v型混料机混合后的cu-b预合金粉体与压坯的宏观形貌图;
20.图2是本发明一种高导电、高耐磨铜硼合金的制备方法的实施例1-4中采用粉末冶
金与真空感应熔炼相结合的方式最终制备的cu-b合金宏观形貌图;
21.图3是本发明一种高导电、高耐磨铜硼合金的制备方法的实施例3中制备的cu-b合金组织形貌(om)与(sem)图;
22.图4是本发明一种高导电、高耐磨铜硼合金的制备方法的实施例3中制备的cu-b合金与cu-cr合金在硬度、导电率、摩擦系数,磨损率之间的对比图。
具体实施方式
23.下面结合附图和具体实施方式对本发明一种高导电、高耐磨铜硼合金的制备方法进行详细说明。
24.实施例1;
25.一种高导电、高耐磨cu-b合金的制备方法,具体步骤如下:
26.步骤1:设计cu-b合金中b含量为2wt.%,分别称量电解cu粉和b粉,通过计算可得b粉与cu粉质量比为1:49,称取6gb粉,294g电解cu粉;
27.步骤2:将称量好的b粉和cu粉装入混料容器中并加入分散剂(无水乙醇),在v型机械混料机上进行60min的混粉,转速100r/min,球料比为1:6,磨球粒径9mm;将混合后的cu-b预合金粉体过筛后倒入冷压模具,单次倒入30g粉末并进行倾斜摆动30
°
~50
°
振实,然后利用四柱式油压机进行压制,压制压力为300kn,保压20s形成cu-b预合金坯体;
28.步骤3:在高纯石墨坩埚内安装熔体导流管(内径为6mm),将坯料依次装入坩锅内,保证下紧上松,并将坩埚整体放入感应线圈内进行熔炼,石墨坩锅所装坯料不超过坩锅深度的2/3,并用刚玉管封堵导流管口。封闭炉体后采用三级泵抽系统(机械泵、罗茨泵、扩散泵)对腔室预抽真空,当熔炼室内真空度低于9.0
×
10-3
pa后,向熔炼室内充入保护气体至腔室总压力达到-0.05mpa,保护气体为高纯ar。熔炼流程为:使用中频感应电源在20min将温度升至1350℃并保温5min使合金液充分均匀化;保温结束后,将刚玉管拔起,坩埚内的金属熔体通过底部导流管浇注至高纯石墨内进行冷却凝固;当冷却到室温时取出cu-b合金坯料,对坯料表面经机加工处理得到cu-b合金。
29.经上述工艺,本实施例所制备的cu-b合金硬度、导电率,结果为:89hv和83%iacs。
30.本实施例所制备的cu-b合金摩擦磨损形貌为粘着磨损,载荷为500g,摩擦速度为252mm/min,67min后磨损量为0.0003g,摩擦磨损稳定后摩擦系数平均值为0.69。
31.实施例2;
32.一种高导电、高耐磨cu-b合金的制备方法,具体步骤如下:
33.步骤1:设计cu-b合金中b含量为4wt.%,分别称量电解cu粉和b粉,通过计算可得b粉与cu粉质量比为1:24,称取12gb粉,288g电解cu粉;
34.步骤2:将称量好的b粉和cu粉装入混料容器中并加入分散剂(无水乙醇),在v型机械混料机上进行120min的混粉,转速150r/min,球料比为1:4,磨球粒径6mm;将混合后的cu-b预合金粉体过筛后倒入冷压模具,单次倒入40g粉末并进行倾斜摆动30
°
~50
°
振实,然后利用四柱式油压机进行压制,压制压力为300kn,保压20s形成cu-b预合金坯体;
35.步骤3:在高纯石墨坩埚内安装熔体导流管(内径为5mm),将坯料依次装入坩锅内,保证下紧上松,并将坩埚整体放入感应线圈内进行熔炼,石墨坩锅所装坯料不超过坩锅深度的2/3,并用刚玉管封堵导流管口。封闭炉体后采用三级泵抽系统(机械泵、罗茨泵、扩散
泵)对腔室预抽真空,当熔炼室内真空度低于9.0
×
10-3
pa后,向熔炼室内充入保护气体至腔室总压力达到-0.03mpa,所述保护气体为高纯ar。熔炼流程为:使用中频感应电源在20min将温度升至1250℃并保温8min使合金液充分均匀化;保温结束后,将刚玉管拔起,坩埚内的金属熔体通过底部导流管浇注至高纯石墨内进行冷却凝固;当冷却到室温时取出cu-b合金坯料,对坯料表面经机加工处理得到cu-b合金。
36.经上述工艺,本实施例所制备的cu-b合金硬度、导电率,结果为:104hv和79%iacs。
37.本发明所制备的cu-b合金摩擦磨损形貌为粘着磨损,载荷为500g,摩擦速度为252mm/min,67min后磨损量为0.0004g,摩擦磨损稳定后摩擦系数平均值为0.64。
38.实施例3;
39.一种高导电、高耐磨cu-b合金的制备方法,具体步骤如下:
40.步骤1:设计cu-b合金中b含量为2.5wt.%,分别称量电解cu粉和b粉,通过计算可得b粉与cu粉质量比为1:39,称取7.5gb粉,292.5g电解cu粉;
41.步骤2:将称量好的b粉和cu粉装入混料容器中并加入分散剂(无水乙醇),在振动混粉机上进行240min的混粉,频率40hz,球料比为1:4,磨球粒径3mm;将混合后的cu-b预合金粉体过筛后倒入冷压模具,单次倒入50g粉末并进行倾斜摆动30
°
~50
°
振实,然后利用四柱式油压机进行压制,压制压力为300kn,保压40s形成cu-b预合金坯体;
42.步骤3:在高纯石墨坩埚内安装熔体导流管(内径为4mm),将坯料依次装入坩锅内,保证下紧上松,并将坩埚整体放入感应线圈内进行熔炼,石墨坩锅所装坯料不超过坩锅深度的2/3,并用刚玉管封堵导流管口。封闭炉体后采用三级泵抽系统(机械泵、罗茨泵、扩散泵)对腔室预抽真空,当熔炼室内真空度低于9.0
×
10-3
pa后,向熔炼室内充入保护气体至腔室总压力达到0.01mpa,所述保护气体为高纯ar。熔炼流程为:使用中频感应电源在20min将温度升至1400℃并保温10min使合金液充分均匀化;保温结束后,将刚玉管拔起,坩埚内的金属熔体通过底部导流管浇注至高纯石墨内进行冷却凝固;当冷却到室温时取出cu-b合金坯料,对坯料表面经机加工处理得到cu-b合金。
43.经上述工艺,本实施例所制备的cu-b合金硬度、导电率,结果为:98.98hv和83.34%iacs。
44.本发明所制备的cu-b合金摩擦磨损形貌为粘着磨损,载荷为500g,摩擦速度为252mm/min,67min后磨损量为0.0002g,摩擦磨损稳定后摩擦系数平均值为0.57。
45.实施例4;
46.一种高导电、高耐磨cu-b合金的制备方法,具体步骤如下:
47.步骤1:设计cu-b合金中b含量为5.0wt.%,分别称量电解cu粉和b粉,通过计算可得b粉与cu粉质量比为1:19,称取15gb粉,285g电解cu粉;
48.步骤2:将称量好的b粉和cu粉装入混料容器中并加入分散剂(无水乙醇),在行星式球磨机上进行240min的混粉,转速150r/min,球料比为1:8,磨球粒径7mm;将混合后的cu-b预合金粉体过筛后倒入冷压模具,单次倒入60g粉末并进行倾斜摆动30
°
~50
°
振实,然后利用四柱式油压机进行压制,压制压力为300kn,保压40s形成cu-b预合金坯体;
49.步骤3:在高纯石墨坩埚内安装熔体导流管(内径为3mm),将坯料依次装入坩锅内,保证下紧上松,并将坩埚整体放入感应线圈内进行熔炼,石墨坩锅所装坯料不超过坩锅深
度的2/3,并用刚玉管封堵导流管口。封闭炉体后采用三级泵抽系统(机械泵、罗茨泵、扩散泵)对腔室预抽真空,当熔炼室内真空度低于9.0
×
10-3
pa后,向熔炼室内充入保护气体至腔室总压力达到0.01mpa,所述保护气体为高纯ar。熔炼流程为:使用中频感应电源在20min将温度升至1450℃并保温5min使合金液充分均匀化;保温结束后,将刚玉管拔起,坩埚内的金属熔体通过底部导流管浇注至高纯石墨内进行冷却凝固;当冷却到室温时取出cu-b合金坯料,对坯料表面经机加工处理得到cu-b合金。
50.经上述工艺,本实施例所制备的cu-b合金硬度、导电率,结果为:119hv和78%iacs。
51.本发明所制备的cu-b合金摩擦磨损形貌为粘着磨损,载荷为500g,摩擦速度为252mm/min,67min后磨损量为0.0008g,摩擦磨损稳定后摩擦系数平均值为0.69。
52.本发明一种高导电、高耐磨铜硼合金的制备方法,提高了合金液混合均匀程度,改善了cu-b合金比重偏析,最终制备出表面质量良好、成分稳定、组织均匀,磨损形貌为粘着磨损的高硬度、高导电、高耐磨的cu-b合金,具有一点的实用意义。
再多了解一些
本文用于企业家、创业者技术爱好者查询,结果仅供参考。