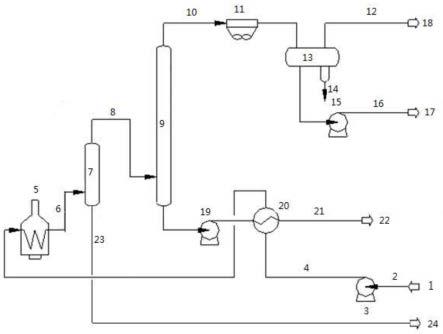
1.本发明涉及由劣质原料生产渣油的领域,具体涉及一种利用加热炉生产渣油的方法。
背景技术:
2.催化裂化柴油(lco)在我国柴油池中的比例较高,约占30%,是主要的二次加工柴油组分。
3.近几年由于原油日益劣质化,越来越多的减压瓦斯油重组分乃至渣油正在成为催化裂化(fcc)装置的原料,加之许多企业为达到提高汽油产率或增产丙烯的目的,对催化裂化装置进行了改造或提高了fcc装置的操作苛刻度,导致lco的质量日益恶化,其中不安定性因素也随之增加,胶质、残渣增多,颜色变深,硫、氮、芳烃含量升高,十六烷值偏低。
4.另一方面,为了减少机动车排气污染,改善空气质量,国内高标准的清洁车用柴油标准陆续出台并实施。而国内催化裂化技术的普遍应用,会生产大量高芳烃含量、低十六烷值的催化裂化柴油。
5.lco的组成特性与清洁车用柴油期望的高饱和烃含量、高氢含量、高十六烷值的要求存在较大的矛盾。
6.在国外,lco主要用于调和燃料油、非车用柴油和加热油等;而在我国,由于石油资源紧缺,lco主要是通过加氢处理后用于调和柴油产品。
7.目前采用常规的加氢精制或加氢改质路径虽能基本脱除lco中的硫和氮,且不同程度提高其十六烷值,但存在氢耗高、操作条件苛刻等问题,并且lco中高芳烃组分也未能得到有效利用。
8.因此,如何压减或转化lco,以适应未来柴、汽油的需求变化,对保证我国成品油市场的供需平衡以及环境保护具有重大意义,寻找新的lco加工路径变得越来越重要。
技术实现要素:
9.本发明的目的是为了提供一种利用加热炉生产渣油的新方法,以期改善减黏渣油的质量,提高减黏裂化效果。
10.为了实现上述目的,本发明提供一种利用加热炉生产渣油的方法,该方法包括:
11.(1)将减黏裂化原料油和催化裂化柴油引入至加热炉i中进行减黏裂化反应,得到减黏裂化反应物流;或者
12.将减黏裂化原料油和催化裂化柴油引入至加热炉ii中进行加热预处理以得到混合原料油,然后再将该混合原料油引入至减黏裂化反应器中进行减黏裂化反应,得到减黏裂化反应物流;
13.(2)将步骤(1)中得到的所述减黏裂化反应物流引入至蒸发塔中进行分离,得到减黏渣油和塔顶油气;
14.在步骤(1)中,以所述减黏裂化原料油的用量为基准,所述催化裂化柴油的用量为
1-30重量%。
15.本发明采用非催化热裂化工艺,通过以上技术方案,将催化裂化柴油与减黏裂化原料油共同作为加热炉进料,解决了催化裂化装置的催化裂化柴油出路的同时,提高了减黏裂化效果,改善减黏渣油的质量,安定性更好。
16.在优选情况下,向炉管内注入水或水蒸气,更有利于避免炉管结焦,延长了加热炉操作周期。
附图说明
17.图1是本发明的一种优选的具体实施方式的利用加热炉生产渣油的工艺流程图。
18.图2是本发明的另一种优选的具体实施方式的利用加热炉生产渣油的工艺流程图。
19.附图标记说明
20.1、混合物料
21.5、加热炉
22.7、蒸发塔
23.7a、减黏裂化反应器
24.9、常压分馏塔
25.11、空冷器
26.13、分液罐
27.17、汽油馏分
28.18、裂化气体
29.18a、第二分馏塔
30.20、23a、24a均为换热器
31.21a、22均为柴油馏分
32.24、26均为减黏渣油
33.2、4、6、8、10、12、14、16、20a、21、23、25均为管道
34.3、15、19、22a均为泵
具体实施方式
35.在本文中所披露的范围的端点和任何值都不限于该精确的范围或值,这些范围或值应当理解为包含接近这些范围或值的值。对于数值范围来说,各个范围的端点值之间、各个范围的端点值和单独的点值之间,以及单独的点值之间可以彼此组合而得到一个或多个新的数值范围,这些数值范围应被视为在本文中具体公开。
36.如前所述,本发明提供了一种利用加热炉生产渣油的方法,该方法包括:
37.(1)将减黏裂化原料油和催化裂化柴油引入至加热炉i中进行减黏裂化反应,得到减黏裂化反应物流;或者
38.将减黏裂化原料油和催化裂化柴油引入至加热炉ii中进行加热预处理以得到混合原料油,然后再将该混合原料油引入至减黏裂化反应器中进行减黏裂化反应,得到减黏裂化反应物流
39.(2)将步骤(1)中得到的所述减黏裂化反应物流引入至蒸发塔中进行分离,得到减黏渣油和塔顶油气;
40.在步骤(1)中,以所述减黏裂化原料油的用量为基准,所述催化裂化柴油的用量为1-30重量%。
41.根据本发明提供的方法,在步骤(1)中,将减黏裂化原料油和催化裂化柴油共同引入加热炉中进行减黏裂化反应或者是先进行加热预处理然后在减黏裂化反应器中进行减黏裂化反应时,本发明的该方法能够提高减黏裂化效果,改善减黏渣油的质量。
42.在一种优选的具体实施方式下,在步骤(1)中,所述催化裂化柴油与减黏裂化原料一起作为加热炉i的进料,在原料缓冲罐内混合后进入加热炉i的对流段。
43.优选地,本发明引入的催化裂化柴油来自于催化裂化装置产生的催化裂化柴油馏分油,具体地,例如可以是催化裂化柴油中的部分馏分油。
44.在步骤(1)中,优选地,以所述减黏裂化原料油的用量为基准,所述催化裂化柴油的用量为5-20重量%。
45.在本发明中,对所述催化裂化柴油的馏程选择范围较宽,优选地,所述催化裂化柴油的初馏点为250-290℃,终馏点为340-370℃。
46.进一步优选地,所述催化裂化柴油的初馏点为260-290℃,终馏点为350-370℃。
47.优选地,在步骤(1)中,通过所述加热炉i得到所述减黏裂化反应物流,所述减黏裂化反应的操作条件包括:加热炉出口温度为450-510℃,加热炉压力为0.2-0.8mpa,平均停留时间为0.5-10min。
48.进一步优选地,在步骤(1)中,通过所述加热炉i得到所述减黏裂化反应物流,所述减黏裂化反应的操作条件包括:加热炉出口温度为460-490℃,加热炉压力为0.2-0.8mpa,平均停留时间为1-5min。在该种优选情况下,更有利于加热炉内减黏裂化反应的进行,提高减黏裂化效果,改善减黏渣油的质量。
49.根据另一种优选的具体实施方式,在步骤(1)中,通过所述减黏裂化反应器得到所述减黏裂化反应物流,所述减黏裂化反应的操作条件包括:减黏裂化反应器入口温度为380-460℃,减黏裂化反应器压力为0.2-0.8mpa,平均停留时间为0.2-1.2h。
50.更优选地,在步骤(1)中,通过所述减黏裂化反应器得到所述减黏裂化反应物流,所述减黏裂化反应的操作条件包括:减黏裂化反应器入口温度为400-440℃,减黏裂化反应器压力为0.3-0.6mpa,平均停留时间为0.3-1h。发明人发现,在该种优选情况下,更有利于反应器中减黏裂化反应的进行,提高减黏裂化效果,改善减黏渣油的质量。
51.优选情况下,在步骤(1)中,通过所述减黏裂化反应器得到所述减黏裂化反应物流,所述加热预处理的操作条件包括:加热炉ii出口温度为380-460℃,加热炉ii压力为0.2-0.8mpa,平均停留时间为0.2-1.2h。更优选地,所述加热预处理的操作条件包括:加热炉ii出口温度为400-440℃,加热炉ii压力为0.2-0.8mpa,平均停留时间为0.3-1h。
52.优选地,在步骤(2)中,所述蒸发塔为常压蒸发塔,所述常压蒸发塔中的操作条件包括:塔顶温度为120-140℃,塔底温度为300-340℃。
53.本发明的方法对所述蒸发塔中的具体操作方式没有特别的要求,本领域技术人员可以采用本领域内常规的操作方式进行。
54.本发明的方法能够提高减黏裂化原料如减压渣油的胶体稳定性,进而改善胶体体
系在加热炉内高温条件下的稳定性,减少了沥青质缩合,降低了结焦倾向,能延长加热炉操作周期。同时,可改善减黏渣油的性质如安定性。
55.本发明提供的方法特别适用于劣质减黏裂化原料非催化热裂化工艺,特别优选情况下,所述减黏裂化原料油的性质包括:硫含量大于2.5重量%,或康氏残炭大于15重量%,或粘度(100℃)大于2000mm2/s,或沥青质含量大于8重量%。参照上述性质,本发明的发明人发现,所涉及的减黏裂化原料性质越差,越有利于显示本发明的技术优势。
56.更优选地,所述减黏裂化原料油选自减压渣油、石油沥青、稠油、稠油的常压馏分、稠油的减压馏分、重馏分油和催化裂化油浆中的至少一种。
57.根据一种优选的具体实施方式,本发明的该方法还包括步骤(3):将所述塔顶油气进行分离处理,得到裂化气体、汽油馏分和柴油馏分。
58.在本发明中,所述裂化气体的组分包括但不限于甲烷、乙烷、乙烯、丙烷、丙烯、丁烷和丁烯等;所述汽油馏分馏程范围为45-180℃;所述柴油馏分馏程范围为160-360℃。
59.优选地,在步骤(3)中,所述分离处理在分馏塔中进行。本发明对所述分馏塔没有特别的限定,只要能够实现对所要处理的物料进行蒸馏或精馏的目的即可。具体地,可以为常压分馏塔、减压分馏塔或加压分馏塔。依据塔内具体设置,可以为填料塔,也可以为板式塔。在一种具体实施情况下,所述分馏塔为板式塔。本发明对板式塔的塔板数没有特别的限定,只要能够实现本发明的目的,将来自蒸发塔的所述塔顶油气进行分离处理即可。
60.根据本发明一种优选实施方式,该方法还包括:在步骤(1)中,向所述加热炉i或所述加热炉ii的炉管中引入含水物流,更优选所述含水物流为水和/或水蒸气。在该种优选实施方式下,更有利于降低加热炉炉管内结焦倾向,延长加热炉操作周期。
61.优选地,以所述减黏裂化原料油的总用量为基准,引入的所述含水物流的重量为0.5-1.5重量%。在本发明中,对所述含水物流的引入方式没有特别的限定,可以与减黏裂化原料油接触后一同引入加热炉,也可以与减黏裂化原料油各自独立的引入加热炉。优选地,所述含水物料与减黏裂化原料油各自独立的引入加热炉,在该种具体实施方式下,可以独立的调节加热炉的各物料的进料流量,从而有利于减黏裂化反应进行,提高减黏裂化效果,改善减黏渣油的质量。
62.根据第一种优选的具体实施方式,本发明的所述利用加热炉生产渣油的方法按照图1所示的工艺路线图进行,具体地:
63.减黏裂化原料油和催化裂化柴油的混合物料1经管线2进入泵3中,经泵3压送后,流经管道4,经常压分馏塔9底部的换热器20加热后,引入至加热炉5,进行减黏裂化反应,反应后的物料经管道6引入蒸发塔7进行分离,经管道23由蒸发塔7的底部得到减黏渣油24,蒸发塔7的顶部得到的塔顶油气由管道8引入常压分馏塔9中进一步分馏,常压分馏塔9的顶部的物料由管道10引入空冷器11,经降温后引入分液罐13进一步分离,经管道12由分液罐13的顶部得到裂化气体18,分液罐13底部的含油水由管道14引出,并且,经泵15和管道16由分液罐13的底部得到汽油馏分17,常压分馏塔9的底部的物料由泵19引入至换热器20,经换热降温后,经管道21得到柴油馏分22。
64.根据第二种优选的具体实施方式,本发明的所述利用加热炉生产渣油的方法按照图2所示的工艺路线图进行,具体地:
65.减黏裂化原料油和催化裂化柴油的混合物料1经管线2由泵3经管线4,在换热器
密度(20℃)/(g/cm3)0.9607运动粘度/(mm2/s) 20℃11.2250℃4.245烃组成/重量% 链烷烃9.0环烷烃10.2总芳烃80.8胶质0.0(元素)/重量% c89.71h9.86s0.18n0.08馏程/℃ 初馏点28910%30750%32890%349终馏点368
76.实施例1
77.采用图1所示的工艺流程进行,本实施例催化裂化柴油与减黏裂化原料油的用量重量比为10:100。
78.具体操作条件和产品分布列于表3,减黏渣油的性质列于表4。
79.实施例2
80.采用图1所示的工艺流程进行,本实施例催化裂化柴油与减黏裂化原料油的用量重量比为5:100。
81.具体操作条件和产品分布列于表3,减黏渣油的性质列于表4。
82.实施例3
83.本实施例采用与实施例1相同的流程进行,所不同的是,本实施例催化裂化柴油与减黏裂化原料油的用量重量比为20:100。
84.具体操作条件和产品分布列于表3,减黏渣油的性质列于表4。
85.对比例1
86.本对比例按照常规管式减黏裂化方法在中型减黏裂化试验装置上进行试验。
87.具体的操作流程为:减粘裂化试验在一套摸拟工业减粘裂化工艺的中型试验装置上进行,装置进料量为8kg/h。原料油称重后进原料油计量罐,由原料油泵连续打入预热炉,同时注入以减黏裂化原料油的总用量为基准的1.2重量%的水蒸汽以提高物料的流速,防止加热炉管结焦;经过预热炉和加热炉两段加热到480℃,压力为0.5mpa,在加热炉中进行热裂化反应,停留时间为4min,反应后得到的物流引入至蒸发塔中进行分离,得到减黏渣油
和塔顶油气,裂化气经采样分析和气表计量后放空,冷凝轻油和减粘重油混合后根据产物分离要求在间歇蒸馏釜中将混合油切割为减粘汽油和减粘渣油。
88.具体操作条件和产品分布列于表3,减黏渣油的性质列于表4。
89.对比例2
90.本对比例采用与实施例1相同的流程进行,所不同的是,本对比例的全部进料均为减黏裂化原料油,且进料总体积与实施例1中相同。
91.具体操作条件和产品分布列于表3,减黏渣油的性质列于表4。
92.表3
[0093] 实施例1实施例2实施例3对比例1对比例2加热炉操作条件
ꢀꢀꢀꢀꢀ
加热炉出口温度,℃480480480480480加热炉压力,mpa0.50.50.50.50.5冷油停留时间,min44444注水a,重量%1.01.00.81.21.2常压蒸发塔操作条件
ꢀꢀꢀꢀꢀ
塔顶温度/℃130130130130130塔底温度/℃335336335334334产品分布/重量%
ꢀꢀꢀꢀꢀ
减黏气体1.321.331.291.351.37减黏汽油2.652.552.732.482.50减黏柴油11.417.6117.873.513.55减黏渣油84.6288.5078.1092.6692.62合计100.00100.00100.00100.00100.00
[0094]
注水a,重量%,即为以所述减黏裂化原料油的总用量为基准,引入的水的重量百分比。
[0095]
表4
[0096]
项目实施例1实施例2实施例3对比例1对比例2安定性,级12133密度(20℃),g/cm31.01151.01211.01081.01251.0128运动粘度(100℃),mm2/s413.7443.5378.2451.3458.2残炭,重量%21.321.820.222.422.6
[0097]
通过上述结果可以看出,采用本发明提供的第一种优选的方法得到的减黏渣油的安定性更好,为1级,达到安定性标准中的最高级;而现有技术中减黏渣油的安定性较差,为3级。采用本发明提供的利用加热炉生产渣油的方法,减黏裂化效果更好,得到减黏渣油的质量更好,效果显著。
[0098]
实施例4
[0099]
采用图2所示的工艺流程进行,本实施例催化裂化柴油与减黏裂化原料油的用量重量比为10:100。
[0100]
具体操作条件和产品分布列于表5,减黏渣油的性质列于表6。
[0101]
实施例5
[0102]
本实施例采用与实施例4相同的流程进行,所不同的是,本实施例催化裂化柴油与减黏裂化原料油的用量重量比为5:100。
[0103]
具体操作条件和产品分布列于表5,减黏渣油的性质列于表6。
[0104]
实施例6
[0105]
本实施例采用与实施例4相同的流程进行,所不同的是,本实施例催化裂化柴油与减黏裂化原料油的用量重量比为20:100。
[0106]
具体操作条件和产品分布列于表5,减黏渣油的性质列于表6。
[0107]
对比例3
[0108]
本对比例按照反应器减黏裂化方法在中型减黏裂化试验装置上进行试验。
[0109]
具体的操作流程为:减粘裂化试验在一套摸拟工业减粘裂化工艺的中型试验装置上进行,装置进料量为8kg/h。原料油称重后进原料油计量罐,由原料油泵连续打入预热炉,同时注入以减黏裂化原料油的总用量为基准的1.2重量%的水蒸汽以提高物料的流速,防止加热炉管结焦;经过预热炉和加热炉两段加热到430℃后,由反应器底部进入减粘反应器进行反应。在0.4mpa,反应40min。反应产物经过闪蒸罐闪蒸分离后,裂化气经采样分析和气表计量后放空,冷凝轻油和减粘重油混合后根据产物分离要求在间歇蒸馏釜中将混合油切割为减粘汽油和减粘渣油。
[0110]
具体操作条件和产品分布列于表5,减黏渣油的性质列于表6。
[0111]
对比例4
[0112]
本对比例采用与实施例4相同的流程进行,所不同的是,所不同的是,本对比例的全部进料均为减黏裂化原料油,且进料总体积与实施例4中相同。
[0113]
具体操作条件和产品分布列于表5,减黏渣油的性质列于表6。
[0114]
表5
[0115] 实施例4实施例5实施例6对比例3对比例4加热炉操作条件
ꢀꢀꢀꢀꢀ
加热炉出口温度,℃430430430430430加热炉压力,mpa0.40.40.40.40.4冷油停留时间,min44444注水a,重量%1.01.00.81.21.2减黏反应器操作条件
ꢀꢀꢀꢀꢀ
反应器入口温度,℃425425425425425冷油停留时间,h0.50.50.50.50.5压力/mpa0.60.60.60.60.6产品分布/重量%
ꢀꢀꢀꢀꢀ
减黏气体1.751.781.681.821.85减黏汽油2.902.802.972.752.70减黏柴油12.668.9718.835.025.10减黏渣油82.6986.4576.5290.4190.35
[0116]
注水a,重量%,即为以所述减黏裂化原料油的总用量为基准,引入的水的重量百
分比。
[0117]
表6
[0118][0119][0120]
通过上述结果可以看出,采用本发明提供的第二种方法得到的减黏渣油的安定性更好,为1级,达到安定性标准中的最高级;而现有技术例如对比例3中减黏渣油的安定性较差,安定性为3级。
[0121]
以上详细描述了本发明的优选实施方式,但是,本发明并不限于此。在本发明的技术构思范围内,可以对本发明的技术方案进行多种简单变型,包括各个技术特征以任何其它的合适方式进行组合,这些简单变型和组合同样应当视为本发明所公开的内容,均属于本发明的保护范围。
再多了解一些
本文用于企业家、创业者技术爱好者查询,结果仅供参考。