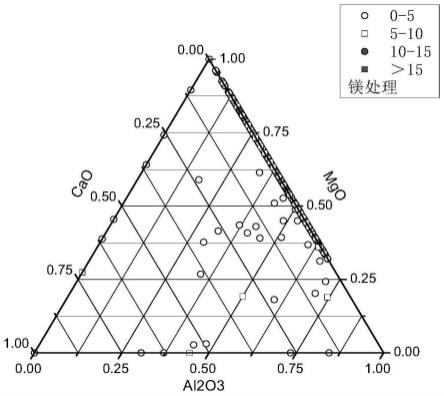
1.本发明涉及钢铁生产技术领域,特别是涉及一种低碳低硫钢镁处理工艺。
背景技术:
2.随着厚板内部质量需求提高以及国家能标探伤标准的逐渐推广,大部分钢种需要能标特级标准进行检验,有些重点品种,如管线钢,为了保证出厂内部质量,同时由于厚板坯管线钢低碳低磷设计,转炉终点过氧、连铸夹杂物上浮时间短,轧钢压缩比、展宽比和钢板堆冷等因素影响,探伤合格率始终低于薄板坯。
3.在炼钢温度下,镁处理相关的夹杂物ca
12
al7、ca3o两种钙铝酸盐为液态,因此镁的加入量存在一个合适的范围。对于镁对夹杂物的改性,镁处理改性内部夹杂物,弥散大颗粒夹杂物是可行的,需要注意的是在镁处理过程中硫的作用,并指出不同类型cas的来源。过多的镁加入形成的大量的mgo,塑性 al2o3夹杂物的去除,镁与氧的结合能力强于硫,但在较低的氧势下,对于喂镁线过程,如何将镁加入到钢水深处提高镁的使用效率成了研究的关键。
技术实现要素:
4.本发明针对上述技术问题,克服现有技术的缺点,提供一种低碳低硫钢镁处理工艺,采用铁水倒罐
→
铁水预处理
→
转炉高碳低氧留氧操作
→
rh炉真空脱碳
→
rh炉合金化及真空脱气
→
rh镁处理
→
ccm流程,具体:(1)铁水预处理操作:入炉铁水须经脱硫预处理并扒渣干净,s≤0.002%;(2)挡渣操作:严格控制出钢过程中的下渣量,控制下渣量≤2kg/t;(3)温度和碳含量控制:吹炼终点温度1640~1680℃,终点[o]≤800ppm;(4)钢包底吹氩气控制:出钢过程钢包底吹气体流量为800nl/min,出钢时间控制在4~8min;(5)lf炉前期操作:钢水到处理工位后,调整钢包底吹流量300~400nl/min;供电化渣2~3min后加入石灰2kg/吨钢、铝丝0.2kg/吨钢,取样分析,下电极升温;(6)lf炉中期过程控制:根据lf炉第一个钢样成分和渣况粘稠情况,加入合适石灰和铝丝造渣脱硫,石灰加入量吨钢小于3kg,铝丝0.2kg/吨钢,脱硫过程氩气流量200~300 nl/min,喂铝线调整钢液铝含量,喂铝线控制氩气流量30~50nl/min,铝线喂入量以冶炼过程钢水中铝含量保持在0.035%~0.045%范围来控制,根据目标钢种的成分进行合金化,升温6~8min取样分析,下电极继续升温脱硫;(7)lf炉后期过程控制:根据lf炉第二个钢样成分和渣况粘稠情况,加入合适石灰和铝丝造渣脱硫,石灰加入量吨钢小于1kg,铝丝0.3kg/吨钢,渣色变白,钢水温度升高至1600~1610℃,提升电极,盖上精炼炉炉盖,钢包底吹氩气调整至800nl/min,进行大氩气搅拌深脱硫4~5min,取样分析;(8)rh真空脱气处理:rh合金化后进行真空脱气处理,真空度<0.3mbar,保持时间
>20min,rh整个过程中钢包底吹氩气流量控制在5~10nl/min,真空结束喂入镁线,喂线后静搅>15min。
[0005]
本发明进一步限定的技术方案是:前所述的一种低碳低硫钢镁处理工艺,步骤(6),lf炉第一个钢样成分处理时间10min。
[0006]
前所述的一种低碳低硫钢镁处理工艺,步骤(7),lf炉第二个钢样成分处理时间25min。
[0007]
前所述的一种低碳低硫钢镁处理工艺,步骤(7),渣色变白时feo mno≤1.0%。
[0008]
前所述的一种低碳低硫钢镁处理工艺,步骤(8),镁线最佳喂入量为300m。
[0009]
前所述的一种低碳低硫钢镁处理工艺,钢板2.0级以内夹杂物含量控制在100%。
[0010]
本发明的有益效果是:(1)本发明通过转炉出钢留氧制度和造渣制度的优化,稳定钢水中氧含量, lf炉扩散脱氧造渣和沉淀脱氧达到快速脱氧造渣的目的,充分发挥脱硫的冶金热力学和动力学条件,rh 炉真空循环降低钢水中夹杂物,降低钢水中大颗粒夹杂物,通过喂入镁线再次细化大颗粒夹杂物,同时钢水纯净度提高,铸坯质量良好,钢板2.0级以内夹杂物含量控制在100%;(2)本发明中镁线喂入工艺与原喂钙线工艺相同,喂线过程镁线反应程度、喷溅及烟尘情况与原钙线相差不大,过程塞棒正常,水口无明显蓄瘤物;(3)本发明中镁处理对钢板力学性能、低温冲击、落锤等无影响,低温冲击优于钙线工艺;(4)本发明中钢板夹杂物总数及大尺寸夹杂物数明显减少,探伤合格率高于钙线工艺。
附图说明
[0011]
图1-3为本发明实施例中aspex检测钢板夹杂物成分组成图。
具体实施方式
[0012]
本实施例提供的一种低碳低硫钢镁处理工艺,主要对钢水中t.o分析,通过跟踪各环节钢水中增氧情况,达到定点控制定点去除方式,同时对内部检测t.o较低,但夹杂物中cao较高;对特定炉次进行了取样, 开展工业调研试验,了解管线钢洁净度、夹杂物控制现状,最终做到连铸坯质量控制现状;工业试验开展前,对管线钢轧板中夹杂物进行了分析,提升钢水纯净度,为了验证镁处理对钢中夹杂物的控制效果并与钙处理进进行比较,采用工业试验以及取样分析的方法,分别对管线钢进行镁处理和钙处理试验,综合比较二者对钢水洁净度和夹杂物特征的影响,为镁处理大规模工业化应用奠定研究基础。
[0013]
选择管线钢种,在150吨转炉、150吨钢包炉冶炼。其x80管线钢化学成分见表1,整个冶炼过程控制如下:表1
ꢀꢀ
x80主要化学成份(%)
采用铁水倒罐
→
铁水预处理
→
转炉高碳低氧留氧操作
→
rh炉真空脱碳
→
rh炉合金化及真空脱气
→
rh镁处理
→
ccm流程,具体:(1)铁水预处理操作:入炉铁水须经脱硫预处理并扒渣干净,s≤0.002%;(2)挡渣操作:严格控制出钢过程中的下渣量,控制下渣量≤2kg/t,降低转炉出钢顶渣脱氧的困难;(3)温度和碳含量控制:吹炼终点温度1640~1680℃,终点[o]≤800ppm;(4)钢包底吹氩气控制:出钢过程钢包底吹气体流量为800nl/min,出钢时间控制在4~8min;(5)lf炉前期操作:钢水到处理工位后,调整钢包底吹流量300~400nl/min;供电化渣2~3min后加入石灰2kg/吨钢、铝丝0.2kg/吨钢,取样分析,下电极升温;(6)lf炉中期过程控制:根据lf炉第一个钢样成分(处理时间10min左右)和渣况粘稠情况,加入合适石灰和铝丝造渣脱硫,石灰加入量吨钢小于3kg,铝丝0.2kg/吨钢,脱硫过程氩气流量200~300 nl/min,喂铝线调整钢液铝含量,喂铝线控制氩气流量30~50nl/min,铝线喂入量以冶炼过程钢水中铝含量保持在0.035%~0.045%范围来控制,根据目标钢种的成分进行合金化,升温6~8min取样分析,下电极继续升温脱硫;(7)lf炉后期过程控制:根据lf炉第二个钢样成分(处理时间25min左右)和渣况粘稠情况,加入合适石灰和铝丝造渣脱硫,石灰加入量吨钢小于1kg,铝丝0.3kg/吨钢,渣色变白(feo mno≤1.0%),钢水温度升高至1600~1610℃,提升电极,盖上精炼炉炉盖,钢包底吹氩气调整至800nl/min,进行大氩气搅拌深脱硫4~5min,取样分析;(8)rh真空脱气处理:rh合金化后进行真空脱气处理,真空度<0.3mbar,保持时间>20min,rh整个过程中钢包底吹氩气流量控制在5~10nl/min,真空结束喂入镁线,喂线后静搅>15min。
[0014]
(9)试验结果及分析
①
轧制钢板探伤表2 钢板探伤结果300m镁线喂入量实验炉次轧制的钢板探伤合格率最高,350m镁线喂入量炉次次之,400m镁线喂入量炉次最差,这与低熔点夹杂物的影响一致。
[0015]
②
轧制钢板夹杂物检测
表3 钢板夹杂物检测按astm e45方法a进行测定,3种镁线喂入量工艺夹杂物评级结果无明显差别。
[0016]
③
钢板夹杂物aspex检测如图1-3,aspex检测显示,3种镁处理工艺下,扫描30mm2夹杂物总数400-600,个数有明显差异。夹杂物成分组成上400m、350m和300m镁线工艺夹杂物主要基本相同。结合n厂铁水、生产工艺、现场条件等因素, 300m镁线为合适喂入量。
[0017]
④
钢板性能表4 钢板性能同期生产钢板正样-30℃横向冲击检测,镁处理炉次的冲击功优于钙处理炉次;取3炉镁处理炉次轧制钢板进行系列温度冲击、落锤检测,结果显示4个温度点镁处理钢板的冲击功、落锤剪切面积均高于钙处理钢板。
[0018]
通过对管线钢进行镁处理,改变内部夹杂物的分布、类型,解决此类缺陷内部质量问题。此外,务必保证软吹时间,软吹时间过短,夹杂物不能充分上浮,有可能导致水口蓄瘤,镁加入量越高,软吹时间应相应延长。
[0019]
除上述实施例外,本发明还可以有其他实施方式。凡采用等同替换或等效变换形成的技术方案,均落在本发明要求的保护范围。
再多了解一些
本文用于企业家、创业者技术爱好者查询,结果仅供参考。