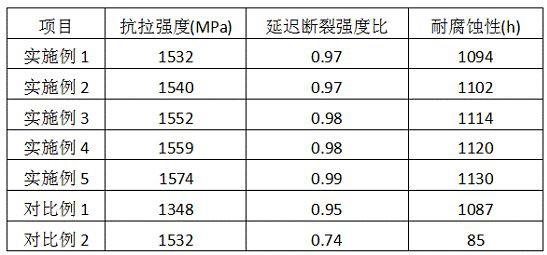
1.本发明涉及紧固件材料制备技术领域,尤其涉及一种紧固件用复合材料及其制备方法。
背景技术:
2.紧固件是用于紧固两个或两个以上零件或构件,使其紧固连接在一起的机械零件的总称,主要包括螺栓、螺母、垫圈、螺钉、销、铆钉等,广泛应用于能源、电子、电器、机械、化工、冶金、模具、液压等等行业。理想的紧固件材料需要同时具有较高的机械力学性能,较好的耐腐蚀性能,优异的性能稳定性和较长的使用寿命。
3.传统的紧固件采用碳素钢材料,比强度低,需要进行镀锌防腐处理才能应用,生产成本高,工艺复杂,对环境具有污染性,无法满足交通运输、海洋工程等行业钢结构等设施上的高强度紧固件使用要求。应用于交通运输、海洋工程等行业钢结构等设施上的紧固件由于长期处于野外暴露环境,尤其是钢结构桥梁和海洋工程,通常位于江、河、湖、海等水面上,湿度高、环境恶劣,紧固件表面容易产生电化学腐蚀吸氢而导致延迟开裂,影响结构应用安全。特别是随着紧固件强度的增加,延迟断裂敏感性显著增加。可见,如何协调强度和延迟断裂敏感性之间的矛盾,制备出综合性能优异的紧固件材料势在必行。
4.为了解决上述问题,专利cn108085544b公开了一种紧固件用高强度铝合金材料及其制备方法,所述紧固件用高强度铝合金材料按重量百分比包含如下元素:铁0.3%-0.5%,硅0.2%-1.0%,铜0.4%-1.2%,钪0.1%-0.6%,锰0.3%-1.1% ,锂0.01%-0.1%,锆0.1%-0.5%,镁0.5%-1.3%,铈0.01%-0.1%,钇0.01%-0.1%,铬0.05%-0.25%,镍0.002%-0.02%,锌0.1%-0.5%,硼0.01%-0.06%,钛0.01%-0.05%,钒0.01%-0.05%,余量为铝;其中,镁和硅的重量百分比的比值不小于1.042,铁和硅的重量百分比的比值不小于0.32,钪和锆的重量百分比合计小于或者等于1.2%,锂、铈、钇以及锌的重量百分比合计小于或者等于0.52%,铬、钛以及钒的重量百分比合计小于或者等于0.3%。该发明实施例的紧固件用高强度铝合金材料,具有高的比强度、高的剪切强度、优异的塑性和韧性及耐腐蚀性能,可以在大幅降低紧固件重量的同时,显著提高安全可靠性。然而,该紧固件材料抗拉强度和耐腐蚀性能有待进一步提高。
5.因此,如何提供一种强度大、抗腐蚀性能佳、耐延迟断裂性能足的紧固件用材料及其制备方法是当前业内研究者们亟待解决的难题。
技术实现要素:
6.本发明的主要目的在于提供一种强度大、抗腐蚀性能佳、耐延迟断裂性能足的紧固件用复合材料及其制备方法。
7.为达到以上目的,本发明提供一种紧固件用复合材料,其特征在于,包括紧固件本体材料以及设于其表面的防腐涂层;所述紧固件本体材料以高性能钢材为基体,在基体中分布着硼纤维,所述硼纤维占紧固件本体材料重量的8-13%;所述高性能钢材包括如下按质
量百分比计的各成分:c 0.1-0.2%、si 0.4-0.8%、mn 1.8-3.0%、mo 2.0-3.0%、ni 1.5-3.5%、co 1.0-2.2%、v 0.05-0.15%、ba 0.001-0.005%、p≤0.02%、s≤0.005%、纳米硅化锆0.005-0.01%、纳米氮化硼0.005-0.01%,余量为fe和其他不可避免的杂质;所述防腐涂层是由如下按重量份计的各组分制成:氨基封端的超支化聚酰亚胺40-50份、9,9-二[(2,3-环氧丙氧基)苯基]芴5-8份、n-[4-氰基-3-(三氟甲基)苯基]甲基环氧丙烯酰胺1-2份、纳米硼纤维3-6份、偶联剂1-3份、溶剂30-40份。
[0008]
优选的,所述防腐涂层的厚度为80-300μm。
[0009]
优选的,所述溶剂为n,n-二甲基甲酰胺、n,n-二甲基乙酰胺、n-甲基吡咯烷酮中的至少一种。
[0010]
优选的,所述偶联剂为硅烷偶联剂kh550、硅烷偶联剂kh560中的至少一种。
[0011]
优选的,所述氨基封端的超支化聚酰亚胺的制备方法参见专利cn107789677b实施例1。
[0012]
优选的,所述纳米硼纤维的平均直径为300-500nm,长径比为(15-25):1。
[0013]
优选的,所述纳米硅化锆的粒径为100-300nm,纳米氮化硼的粒径为300-500nm。
[0014]
本发明的另一个目的,在于提供一种所述紧固件用复合材料的制备方法,其特征在于,包括如下步骤:步骤s1、将硼纤维编织成网格布,后浸泡在水玻璃的水溶液中1-2小时,取出后在95-105℃下干燥至恒重,再将其装于铸型中;步骤s2、将高性能钢材各成分按质量百分比混合均匀后,熔炼成钢水,浇入铸型中,然后冷却凝固,再依次进行退火、淬火、回火处理;步骤s3、将防腐涂层各组分按重量份混合均匀后,涂覆于经过s2处理得到的紧固件本体材料表面,在180-200℃下固化1-2小时。
[0015]
优选的,步骤s1中所述水玻璃的水溶液的质量百分浓度为20-30%。
[0016]
优选的,步骤s1中所述硼纤维的平均直径为3-9μm。
[0017]
优选的,步骤s2中所述退火为二段退火,第一段退火温度为680-720℃,保温时间0.8-1.2小时;第二段退火温度为1030-1070℃,保温时间0.5-0.8小时。
[0018]
优选的,步骤s2中所述淬火的温度为910-950℃,保温2-3小时,油淬。
[0019]
优选的,步骤s2中所述回火的温度为200-250℃,保温时间1-2小时。
[0020]
由于上述技术方案的运用,本发明具有以下有益效果:(1)本发明公开的紧固件用复合材料的制备方法,制备工艺简便,对设备依赖性低,且生产得到的复合材料性能好,便于工业化生产。
[0021]
(2)本发明公开的紧固件用复合材料,所述高性能钢材包括如下按质量百分比计的各成分:c 0.1-0.2%、si 0.4-0.8%、mn 1.8-3.0%、mo 2.0-3.0%、ni 1.5-3.5%、co 1.0-2.2%、v 0.05-0.15%、ba 0.001-0.005%、p≤0.02%、s≤0.005%、纳米硅化锆0.005-0.01%、纳米氮化硼0.005-0.01%,余量为fe和其他不可避免的杂质。通过各成分之间相互配合,共同作用,使得制成的材料强度大、抗腐蚀性能佳、耐延迟断裂性能足;特别是纳米硅化锆、纳米氮化硼的加入,与其它成分协同作用,能明显改善材料的机械力学性能,延长材料使用寿命。
[0022]
(3)本发明公开的紧固件用复合材料,包括紧固件本体材料以及设于其表面的防
腐涂层;所述紧固件本体材料以高性能钢材为基体,在基体中分布着硼纤维;通过这种结构和材料的复合,使得制成的复合材料强度更高,耐腐蚀性更优异,耐延迟断裂性能更佳,使用寿命更长。
[0023]
(4)本发明公开的紧固件用复合材料,所述防腐涂层是由如下按重量份计的各组分制成:氨基封端的超支化聚酰亚胺40-50份、9,9-二[(2,3-环氧丙氧基)苯基]芴5-8份、n-[4-氰基-3-(三氟甲基)苯基]甲基环氧丙烯酰胺1-2份、纳米硼纤维3-6份、偶联剂1-3份、溶剂30-40份;氨基封端的超支化聚酰亚胺上的氨基在固化阶段能与9,9-二[(2,3-环氧丙氧基)苯基]芴、n-[4-氰基-3-(三氟甲基)苯基]甲基环氧丙烯酰胺上的环氧基发生环氧开环反应,形成互穿网络结构,且涂层分子结构中的超支化聚酰亚胺、苯基芴基、氰基、含氟苯基、酰胺基之间在电子效应、位阻效应和共轭效应等多重作用下,使得制成的涂层防腐性能足,耐老化耐温性能够,使用寿命长,且环氧开环反应生成的羟基和氨基封端的超支化聚酰亚胺分子链上的氨基均能提高涂层与紧固件本体之间的粘结性能,进而提高复合材料的使用寿命。
具体实施方式
[0024]
以下描述用于揭露本发明以使本领域技术人员能够实现本发明。以下描述中的优选实施例只作为举例,本领域技术人员可以想到其他显而易见的变型。
[0025]
本发明各实施例中所述氨基封端的超支化聚酰亚胺的制备方法参见专利cn107789677b实施例1。
[0026]
实施例1一种紧固件用复合材料,包括紧固件本体材料以及设于其表面的防腐涂层;所述紧固件本体材料以高性能钢材为基体,在基体中分布着硼纤维,所述硼纤维占紧固件本体材料重量的8%;所述高性能钢材包括如下按质量百分比计的各成分:c 0.1%、si 0.4%、mn 1.8%、mo 2.0%、ni 1.5%、co 1.0%、v 0.05%、ba 0.001%、p≤0.02%、s≤0.005%、纳米硅化锆0.005%、纳米氮化硼0.005%,余量为fe和其他不可避免的杂质;所述防腐涂层是由如下按重量份计的各组分制成:氨基封端的超支化聚酰亚胺40份、9,9-二[(2,3-环氧丙氧基)苯基]芴5份、n-[4-氰基-3-(三氟甲基)苯基]甲基环氧丙烯酰胺1份、纳米硼纤维3份、偶联剂1份、溶剂30份。
[0027]
所述防腐涂层的厚度为80μm;所述溶剂为n,n-二甲基甲酰胺;所述偶联剂为硅烷偶联剂kh550。
[0028]
所述纳米硼纤维的平均直径为300nm,长径比为15:1;所述纳米硅化锆的粒径为100nm,纳米氮化硼的粒径为300nm。
[0029]
一种所述紧固件用复合材料的制备方法,包括如下步骤:步骤s1、将硼纤维编织成网格布,后浸泡在水玻璃的水溶液中1小时,取出后在95℃下干燥至恒重,再将其装于铸型中;步骤s2、将高性能钢材各成分按质量百分比混合均匀后,熔炼成钢水,浇入铸型中,然后冷却凝固,再依次进行退火、淬火、回火处理;步骤s3、将防腐涂层各组分按重量份混合均匀后,涂覆于经过s2处理得到的紧固件本体材料表面,在180℃下固化1小时。
[0030]
步骤s1中所述水玻璃的水溶液的质量百分浓度为20%;所述硼纤维的平均直径为3μm。
[0031]
步骤s2中所述退火为二段退火,第一段退火温度为680℃,保温时间0.8小时;第二段退火温度为1030℃,保温时间0.5小时;所述淬火的温度为910℃,保温2小时,油淬;所述回火的温度为200℃,保温时间1小时。
[0032]
实施例2一种紧固件用复合材料,包括紧固件本体材料以及设于其表面的防腐涂层;所述紧固件本体材料以高性能钢材为基体,在基体中分布着硼纤维,所述硼纤维占紧固件本体材料重量的9%;所述高性能钢材包括如下按质量百分比计的各成分:c 0.12%、si 0.5%、mn 2.0%、mo 2.2%、ni 2%、co 1.2%、v 0.07%、ba 0.002%、p≤0.02%、s≤0.005%、纳米硅化锆0.006%、纳米氮化硼0.007%,余量为fe和其他不可避免的杂质;所述防腐涂层是由如下按重量份计的各组分制成:氨基封端的超支化聚酰亚胺43份、9,9-二[(2,3-环氧丙氧基)苯基]芴6份、n-[4-氰基-3-(三氟甲基)苯基]甲基环氧丙烯酰胺1.2份、纳米硼纤维4份、偶联剂1.5份、溶剂33份。
[0033]
所述防腐涂层的厚度为120μm;所述溶剂为n,n-二甲基乙酰胺;所述偶联剂为硅烷偶联剂kh560。
[0034]
所述纳米硼纤维的平均直径为350nm,长径比为17:1;所述纳米硅化锆的粒径为150nm,纳米氮化硼的粒径为350nm。
[0035]
一种所述紧固件用复合材料的制备方法,包括如下步骤:步骤s1、将硼纤维编织成网格布,后浸泡在水玻璃的水溶液中1.2小时,取出后在98℃下干燥至恒重,再将其装于铸型中;步骤s2、将高性能钢材各成分按质量百分比混合均匀后,熔炼成钢水,浇入铸型中,然后冷却凝固,再依次进行退火、淬火、回火处理;步骤s3、将防腐涂层各组分按重量份混合均匀后,涂覆于经过s2处理得到的紧固件本体材料表面,在185℃下固化1.2小时。
[0036]
步骤s1中所述水玻璃的水溶液的质量百分浓度为23%;所述硼纤维的平均直径为5μm。
[0037]
步骤s2中所述退火为二段退火,第一段退火温度为690℃,保温时间0.9小时;第二段退火温度为1040℃,保温时间0.6小时;所述淬火的温度为920℃,保温2.3小时,油淬;所述回火的温度为215℃,保温时间1.2小时。
[0038]
实施例3一种紧固件用复合材料,包括紧固件本体材料以及设于其表面的防腐涂层;所述紧固件本体材料以高性能钢材为基体,在基体中分布着硼纤维,所述硼纤维占紧固件本体材料重量的11%;所述高性能钢材包括如下按质量百分比计的各成分:c 0.15%、si 0.6%、mn 2.3%、mo 2.5%、ni 2.5%、co 1.7%、v 0.1%、ba 0.0035%、p≤0.02%、s≤0.005%、纳米硅化锆0.007%、纳米氮化硼0.007%,余量为fe和其他不可避免的杂质;所述防腐涂层是由如下按重量份计的各组分制成:氨基封端的超支化聚酰亚胺45份、9,9-二[(2,3-环氧丙氧基)苯基]芴6.5份、n-[4-氰基-3-(三氟甲基)苯基]甲基环氧丙烯酰胺1.5份、纳米硼纤维4.5份、偶联剂2份、溶剂35份。
[0039]
所述防腐涂层的厚度为180μm;所述溶剂为n-甲基吡咯烷酮;所述偶联剂为硅烷偶联剂kh550。
[0040]
所述纳米硼纤维的平均直径为400nm,长径比为20:1;所述纳米硅化锆的粒径为200nm,纳米氮化硼的粒径为400nm。
[0041]
一种所述紧固件用复合材料的制备方法,包括如下步骤:步骤s1、将硼纤维编织成网格布,后浸泡在水玻璃的水溶液中1.5小时,取出后在100℃下干燥至恒重,再将其装于铸型中;步骤s2、将高性能钢材各成分按质量百分比混合均匀后,熔炼成钢水,浇入铸型中,然后冷却凝固,再依次进行退火、淬火、回火处理;步骤s3、将防腐涂层各组分按重量份混合均匀后,涂覆于经过s2处理得到的紧固件本体材料表面,在190℃下固化1.5小时。
[0042]
步骤s1中所述水玻璃的水溶液的质量百分浓度为25%;所述硼纤维的平均直径为6μm。
[0043]
步骤s2中所述退火为二段退火,第一段退火温度为700℃,保温时间1小时;第二段退火温度为1050℃,保温时间0.65小时;所述淬火的温度为930℃,保温2.5小时,油淬;所述回火的温度为230℃,保温时间1.5小时。
[0044]
实施例4一种紧固件用复合材料,包括紧固件本体材料以及设于其表面的防腐涂层;所述紧固件本体材料以高性能钢材为基体,在基体中分布着硼纤维,所述硼纤维占紧固件本体材料重量的12%;所述高性能钢材包括如下按质量百分比计的各成分:c 0.18%、si 0.7%、mn 2.8%、mo 2.8%、ni 3.2%、co 2.0%、v 0.12%、ba 0.004%、p≤0.02%、s≤0.005%、纳米硅化锆0.009%、纳米氮化硼0.009%,余量为fe和其他不可避免的杂质;所述防腐涂层是由如下按重量份计的各组分制成:氨基封端的超支化聚酰亚胺48份、9,9-二[(2,3-环氧丙氧基)苯基]芴7.5份、n-[4-氰基-3-(三氟甲基)苯基]甲基环氧丙烯酰胺1.8份、纳米硼纤维5.5份、偶联剂2.5份、溶剂38份。
[0045]
所述防腐涂层的厚度为270μm;所述溶剂为n,n-二甲基甲酰胺、n,n-二甲基乙酰胺、n-甲基吡咯烷酮按质量比1:2:3混合形成的混合物;所述偶联剂为硅烷偶联剂kh550、硅烷偶联剂kh560按质量比3:5混合形成的混合物。
[0046]
所述纳米硼纤维的平均直径为450nm,长径比为23:1;所述纳米硅化锆的粒径为250nm,纳米氮化硼的粒径为450nm。
[0047]
一种所述紧固件用复合材料的制备方法,包括如下步骤:步骤s1、将硼纤维编织成网格布,后浸泡在水玻璃的水溶液中1.8小时,取出后在103℃下干燥至恒重,再将其装于铸型中;步骤s2、将高性能钢材各成分按质量百分比混合均匀后,熔炼成钢水,浇入铸型中,然后冷却凝固,再依次进行退火、淬火、回火处理;步骤s3、将防腐涂层各组分按重量份混合均匀后,涂覆于经过s2处理得到的紧固件本体材料表面,在195℃下固化1.8小时。
[0048]
步骤s1中所述水玻璃的水溶液的质量百分浓度为28%;所述硼纤维的平均直径为8μm。
[0049]
步骤s2中所述退火为二段退火,第一段退火温度为710℃,保温时间1.1小时;第二段退火温度为1060℃,保温时间0.75小时;所述淬火的温度为940℃,保温2.8小时,油淬;所述回火的温度为240℃,保温时间1.8小时。
[0050]
实施例5一种紧固件用复合材料,包括紧固件本体材料以及设于其表面的防腐涂层;所述紧固件本体材料以高性能钢材为基体,在基体中分布着硼纤维,所述硼纤维占紧固件本体材料重量的13%;所述高性能钢材包括如下按质量百分比计的各成分:c 0.2%、si 0.8%、mn 3.0%、mo 3.0%、ni 3.5%、co 2.2%、v 0.15%、ba 0.005%、p≤0.02%、s≤0.005%、纳米硅化锆0.01%、纳米氮化硼0.01%,余量为fe和其他不可避免的杂质;所述防腐涂层是由如下按重量份计的各组分制成:氨基封端的超支化聚酰亚胺50份、9,9-二[(2,3-环氧丙氧基)苯基]芴8份、n-[4-氰基-3-(三氟甲基)苯基]甲基环氧丙烯酰胺2份、纳米硼纤维6份、偶联剂3份、溶剂40份。
[0051]
所述防腐涂层的厚度为300μm;所述溶剂为n,n-二甲基甲酰胺;所述偶联剂为硅烷偶联剂kh550。
[0052]
所述纳米硼纤维的平均直径为500nm,长径比为25:1;所述纳米硅化锆的粒径为300nm,纳米氮化硼的粒径为500nm。
[0053]
一种所述紧固件用复合材料的制备方法,包括如下步骤:步骤s1、将硼纤维编织成网格布,后浸泡在水玻璃的水溶液中2小时,取出后在105℃下干燥至恒重,再将其装于铸型中;步骤s2、将高性能钢材各成分按质量百分比混合均匀后,熔炼成钢水,浇入铸型中,然后冷却凝固,再依次进行退火、淬火、回火处理;步骤s3、将防腐涂层各组分按重量份混合均匀后,涂覆于经过s2处理得到的紧固件本体材料表面,在200℃下固化2小时。
[0054]
步骤s1中所述水玻璃的水溶液的质量百分浓度为30%;所述硼纤维的平均直径为9μm。
[0055]
步骤s2中所述退火为二段退火,第一段退火温度为720℃,保温时间1.2小时;第二段退火温度为1070℃,保温时间0.8小时;所述淬火的温度为950℃,保温3小时,油淬;所述回火的温度为250℃,保温时间2小时。
[0056]
对比例1本发明提供一种紧固件用复合材料,其配方和制备方法与实施例1相似,不同的是没有添加v、ba和纳米硅化锆。
[0057]
对比例2本发明提供一种紧固件用复合材料,其配方和制备方法与实施例1相似,不同的是没有防腐涂层。
[0058]
为了进一步说明本发明各实施例制成的紧固件用复合材料的有益技术效果,将各例制成的紧固件用复合材料进行相关性能测试,测试结果见表1,测试方法如下:(1)耐腐蚀性:对制得的紧固件用复合材料进行盐雾耐腐蚀试验测试,试验温度为35℃,用5%质量浓度的氯化钠水溶液在试验箱内喷雾,用以模拟环境的加速腐蚀,工程紧固件材料的耐受时间(即保持未生锈的时间)长短决定其耐腐蚀性能的好坏。
[0059]
(2)耐延迟断裂性的评价:通过在15%(质量份数)hcl水溶液中将紧固件用复合材料浸渍30分钟,水洗和干燥后,负荷一定载荷,比较100小时以上不发生断裂的载荷。这时,用酸浸渍后100小时以上未发生断裂的载荷,除以未进行酸浸渍而在抗拉试验时的最大载荷,所得到的值定义为延迟断裂强度比。
[0060]
(3)抗拉强度的测定:根据国家标准gb/t 228-2002进行测试。
[0061]
从表1可见,本发明实施例公开的紧固件用复合材料,与对比例产品相比,具有更加优异的机械力学性能、耐腐蚀性能和耐延迟断裂性能,这是各成分、组分协同作用的结果。
[0062]
表1以上显示和描述了本发明的基本原理、主要特征和本发明的优点。本行业的技术人员应该了解,本发明不受上述实施例的限制,上述实施例和说明书中描述的只是本发明的原理,在不脱离本发明精神和范围的前提下本发明还会有各种变化和改进,这些变化和改进都落入要求保护的本发明的范围内。本发明要求的保护范围由所附的权利要求书及其等同物界定。
再多了解一些
本文用于企业家、创业者技术爱好者查询,结果仅供参考。