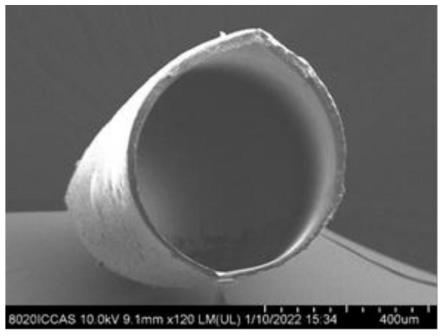
1.本发明涉及聚酰亚胺材料技术领域,尤其涉及一种聚酰亚胺树脂浆料、聚酰亚胺导管及其制备方法与应用。
背景技术:
2.微创手术是在影像引导下经皮穿刺借助聚合物导管通过血管管腔将器械或药物送至病变部位进行介入式治疗的方法,具有组织创伤小、手术精确度高、术后恢复快等优势。
3.介入治疗应用要求聚合物具有良好的生物相容性,同时兼具优异的机械性能以满足抗扭结性的要求,目前聚乙烯、聚丙烯、聚氯乙烯、聚四氟乙烯、聚氨酯等高分子材料已成功应用于医疗导管,但是这些聚合物材料通常只能采用精密挤出工艺进行导管成型,这种挤出导管直径一般在0.5mm以上,管壁厚度在0.1-0.5mm,难以满足介入医疗技术发展对微米级薄壁超细直径管材的应用需求。此外,为了实现在微创手术中实时观察导管的位置,通常将具有x射线显影性的重金属及其氧化物粉体以机械共混的方法复合制备显影导管。为避免显影剂粉体在基体中发生团聚,保证导管具有足够的机械性能,通常显影剂的添加量不超过50wt.%,由此带来导管显影效果不佳的问题。
技术实现要素:
4.鉴于上述的分析,本发明旨在提供一种聚酰亚胺树脂浆料、聚酰亚胺导管及其制备方法与应用,用以解决现有微创介入显影导管良好的力学性能和良好的显影效果难以兼容的问题。
5.本发明的目的主要是通过以下技术方案实现的:
6.一方面,本发明提供了一种具有x射线显影性的聚酰亚胺树脂浆料,所述聚酰亚胺树脂浆料包括聚酰亚胺前驱体树脂溶液和显影剂分散液;所述聚酰亚胺前驱体树脂溶液的制备原料包括芳香二胺单体和芳香二酐单体。
7.可选地,所述聚酰亚胺树脂浆料的粘度为10-30pa
·
s。
8.可选地,所述芳香二胺单体包括对苯二胺(p-pda)、间苯二胺(m-pda)、4,4'-二氨基二苯醚(4,4'-oda)、3,4'-二氨基二苯醚(3,4'-oda)、4,4'-二氨基二苯砜(dds)、4,4'-二氨基二苯酮(4,4'-dabp)、3,3'-二氨基二苯酮(3,3'-dabp)、3,3'-二甲基联苯二胺(tb)、2,2'-二甲基联苯二胺(m-tb)、2,2',3,3'-四甲基联苯二胺(ttb)、3,3'-二羟基联苯二胺(hab)、2,2'-双(三氟甲基)联苯二胺(tfdb)中的至少一种;所述芳香二酐单体包括均苯四酸二酐(pmda)、二苯醚四酸二酐(odpa)、联苯四酸二酐(bpda)、二苯酮四酸二酐(btda)、二苯砜四酸二酐(dsda)、4,4'-六氟异丙基邻苯二甲酸酐(6fda)中的至少一种。
9.可选地,所述显影剂分散液中的显影剂包括钨粉(w)、铋粉(bi)、三氧化钨(wo3)、三氧化二铋(bi2o3)中的至少一种。
10.可选地,所述显影剂的平均粒径为0.5-10μm。
11.另外,本发明还提供了一种具有x射线显影性的聚酰亚胺树脂浆料的制备方法,用于制备上述的聚酰亚胺树脂浆料,包括如下步骤:
12.(1)将芳香二胺与芳香二酐单体在溶剂中室温下搅拌8-12小时,再经40-80℃梯度加热反应3-6小时后降至室温,得到一定固含量和一定粘度的聚酰亚胺前驱体树脂溶液;
13.(2)将显影剂与溶剂混合,通过细胞粉碎机进行超声分散,形成固含量10-30wt.%的显影剂分散液;
14.(3)采用配有齿盘式搅拌桨的高速分散机,将聚酰亚胺前驱体树脂溶液与显影剂分散液以一定转速和时间混合分散,得到一定粘度的聚酰亚胺树脂浆料。
15.可选地,步骤(1)和步骤(2)中的溶剂选自n-甲基吡咯烷酮(nmp)、n,n-二甲基乙酰胺(dmac)和γ-丁内酯中的至少一种。
16.此外,本发明还提供了一种具有x射线显影性的聚酰亚胺导管的制备方法,包括以下步骤:
17.(1)将上述的聚酰亚胺树脂浆料置于浸胶槽中,金属芯线通过浸胶槽使树脂浆料附着于表面,以模头调控上胶量,在一定温度下预烘干处理后,得到树脂包覆的芯线;
18.(2)将所述树脂包覆的芯线经低温亚胺化处理后,冷却至室温,抽出金属芯线,再经高温亚胺化处理,得到单层或多层组成的具有x射线显影性的聚酰亚胺导管。
19.可选地,步骤(1)和步骤(2)之间还包括将所述树脂包覆的芯线按照步骤(1)的方法重复进行多次浸胶与预烘干处理,得到多层树脂包覆的芯线。
20.另外,本发明还提供了一种具有x射线显影性的聚酰亚胺导管,采用上述的制备方法制备得到,所述聚酰亚胺导管中显影剂的含量为50-90wt.%,管壁厚度为20~70μm,导管具有高强韧的特点,拉伸强度≥140mpa,断裂伸长率≥30%,x射线能量在40-120kev范围内时显影性能优异。
21.此外,本发明还提供了一种上述的具有x射线显影性的聚酰亚胺导管在微创介入治疗中的应用。
22.可选地,所述聚酰亚胺前驱体树脂溶液的固含量为10-30wt.%,粘度为100-200pa
·
s。
23.可选地,所述高速分散机的转速为500~2000rpm,混合分散时间为10~30分钟。
24.可选地,步骤(1)中预烘干处理的温度为60-120℃;步骤(2)中的低温亚胺化处理温度为200-250℃,高温亚胺化处理温度为300-400℃。
25.与现有技术相比,本发明至少可实现如下有益效果之一:
26.(1)聚酰亚胺树脂具有优异的力学性能、良好的化学稳定性和耐辐照特性。但是由于聚酰亚胺前驱体树脂溶液通常具有较高的粘度,显影剂粉体难于在树脂溶液中均匀分散,因此制备得到的显影导管力学性能和显影效果均无法满足应用。
27.本发明采用兼具刚性与柔性链段的聚酰亚胺树脂体系,并在聚酰亚胺前驱体树脂溶液制备中利用先室温反应后梯度加热反应的方式,在保证链增长反应的前提下解决聚合物分子链缠结导致聚酰亚胺前驱体树脂溶液粘度过高,不利于显影剂均匀分散的问题。
28.此外,采用超声分散方式,利用液体空化效应产生的冲击波微射流作用,使显影剂重金属及其氧化物粉体不用经过表面处理即可在溶剂中直接形成微米或纳米级显影剂分散液。
29.本发明进一步利用高速分散机产生的强剪切力将聚酰亚胺前驱体树脂溶液与显影剂分散液充分混合分散,获得在高显影剂添加量下金属及其氧化物粉体均匀稳定分散的聚酰亚胺浆料,从而解决显影导管力学性能和显影效果难以兼容的问题。
30.(2)在显影性导管制备过程中,采用显影剂种类与含量相同或不同的聚酰亚胺树脂浆料进行多次浸胶,不但可以获得单层或多层组成的聚酰亚胺导管,实现不同应用场景显影导管的可设计性,而且通过改变导管壁各层中显影剂含量,可以实现对聚酰亚胺导管的力学性能和显影性能的有效调控。
31.(3)聚酰亚胺导管的成型过程采用先低温后高温亚胺化处理的方式,在低温完成部分亚胺化反应后抽出金属芯线,解决了直接高温亚胺化处理后因导管热收缩造成金属芯线难于抽离的问题。经进一步高温亚胺化处理,实现导管材料的完全亚胺化反应,一方面赋予材料优异的机械性能满足导管抗扭结性的要求,同时最大限度地降低聚合物中末端氨基的含量,以满足介入医疗应用对导管材料生物相容性的要求。
32.本发明中,上述各技术方案之间还可以相互组合,以实现更多的优选组合方案。本发明的其他特征和优点将在随后的说明书中阐述,并且,部分优点可从说明书中变得显而易见,或者通过实施本发明而了解。
附图说明
33.附图仅用于示出具体实施例的目的,而并不认为是对本发明的限制,在整个附图中,相同的参考符号表示相同的部件。
34.图1为实施例1制备的聚酰亚胺树脂浆料的扫描电镜能谱(图1中的白色点状物代表钨元素);
35.图2为实施例1制备的显影性聚酰亚胺导管的扫描电镜照片;
36.图3为实施例1制备的聚酰亚胺导管在x射线能量为80kev下的显影照片;其中,左侧为导管,右侧为底板。
具体实施方式
37.下面将结合具体实施例对本发明进一步阐述,但本发明不限于以下实施例。所述方法如无特别说明均为常规方法。所述原材料如无特别说明均能从商业公开途径或者实验室自制获得。本发明中百分比含量如无特别说明,均为质量百分比含量。
38.实施例1
39.在三口烧瓶中加入8.01g(0.04mol)的4,4'-二氨基二苯醚(4,4'-oda)和84.11g的n,n
’‑
二甲基乙酰胺(dmac),在氮气保护下搅拌至完全溶解后,加入8.72g(0.04mol)均苯四酸二酐(pmda)与10.72g dmac,室温搅拌反应12小时后,按照60℃/2小时、70℃/1小时的程序梯度升温反应后降至室温,得到固含量为15wt.%、粘度为170pa
·
s的聚酰亚胺前驱体树脂溶液。在烧杯中将6.0g钨粉和24.0g dmac混合,采用细胞粉碎机进行超声分散,得到固含量为20wt.%的显影剂分散液,钨粉的平均粒径为1.6μm。将30.0g显影剂分散液与40.0g聚酰亚胺前驱体树脂溶液混合,采用配有齿盘式搅拌桨的高速分散机以1500rpm转速混合分散15分钟,得到粘度为18pa
·
s的聚酰亚胺树脂浆料(piv-1)。
40.将piv-1聚酰亚胺树脂浆料置于浸胶槽中,金属芯线通过浸胶槽使树脂浆料附着
于表面,以模头调控上胶量,在60℃下进行预烘干处理,得到单层树脂包覆的芯线,经200℃热烘处理完成部分亚胺化反应后,冷却至室温,抽出金属芯线,再经300℃高温亚胺化处理,得到具有x射线显影性的聚酰亚胺导管pi-1,导管中显影剂含量为50wt.%,管壁厚度为20μm。具有x射线显影性的树脂浆料与导管的主要性能见表1。
41.实施例2
42.在三口烧瓶中加入6.01g(0.03mol)的4,4'-二氨基二苯醚(4,4'-oda)和121.56g的n,n
’‑
二甲基乙酰胺(dmac),在氮气保护下搅拌至完全溶解后,加入8.83g(0.03mol)联苯四酸二酐(bpda)与11.94g dmac,室温搅拌反应12小时后,按照40℃/2小时、60℃/1小时、70℃/1小时的程序梯度升温反应后降至室温,得到固含量为10wt.%、粘度为198pa
·
s的聚酰亚胺前驱体树脂溶液。在烧杯中将3.5g铋粉和10.0g dmac混合,采用细胞粉碎机进行超声分散,得到固含量为26wt.%的显影剂分散液,铋粉的平均粒径为0.5μm。将13.5g显影剂分散液与35g聚酰亚胺前驱体树脂溶液混合,采用配有齿盘式搅拌桨的高速分散机以2000rpm转速混合分散20分钟,得到粘度为30pa
·
s的聚酰亚胺树脂浆料(piv-2)。
43.将piv-2聚酰亚胺树脂浆料置于浸胶槽中,金属芯线通过浸胶槽使树脂浆料附着于表面,以模头调控上胶量,在60℃下进行预烘干处理,得到单层树脂包覆的芯线,经200℃热烘处理完成部分亚胺化反应后,冷却至室温,抽出金属芯线,再经300℃高温亚胺化处理,得到具有x射线显影性的聚酰亚胺导管pi-2,导管中显影剂含量为50wt.%,管壁厚度为50μm。具有x射线显影性的树脂浆料与导管的主要性能见表1。
44.实施例3
45.在三口烧瓶中加入6.01g(0.03mol)的3,4'-二氨基二苯醚(3,4'-oda)和76.56g的n,n
’‑
二甲基乙酰胺(dmac),在氮气保护下搅拌至完全溶解后,加入9.67g(0.03mol)二苯酮四酸二酐(btda)与12.26g dmac,室温搅拌反应12小时后,按照40℃/2小时、60℃/2小时的程序梯度升温反应后降至室温,得到固含量为15wt.%、粘度为100pa
·
s的聚酰亚胺前驱体树脂溶液。在烧杯中将6.8g三氧化钨(wo3)和27.0g dmac混合,采用细胞粉碎机进行超声分散,得到固含量为20wt.%的显影剂分散液,wo3的平均粒径为1.0μm。将33.8g显影剂分散液与30.0g聚酰亚胺前驱体树脂溶液混合,采用配有齿盘式搅拌桨的高速分散机以500rpm转速混合分散10分钟,得到粘度为10pa
·
s的聚酰亚胺树脂浆料(piv-3)。
46.将piv-3聚酰亚胺树脂浆料置于浸胶槽中,金属芯线通过浸胶槽使树脂浆料附着于表面,以模头调控上胶量,在80℃下进行预烘干处理,得到单层树脂包覆的芯线,经200℃热烘处理完成部分亚胺化反应后,冷却至室温,抽出金属芯线,再经350℃高温亚胺化处理,得到具有x射线显影性的聚酰亚胺导管pi-3,导管中显影剂含量为60wt.%,管壁厚度为40μm。具有x射线显影性的树脂浆料与导管的主要性能见表1。
47.实施例4
48.在三口烧瓶中加入12.81g(0.04mol)的2,2'-双(三氟甲基)联苯二胺(tfdb)和86.61g的γ-丁内酯,在氮气保护下搅拌至完全溶解后,加入12.41g(0.04mol)二苯醚四酸二酐(odpa)与14.26gγ-丁内酯,室温搅拌反应12小时后,按照40℃/3小时、50℃/2小时、60℃/1小时的程序梯度升温反应后降至室温,得到固含量为20wt.%、粘度为187pa
·
s的聚酰亚胺前驱体树脂溶液。在烧杯中将24.0g三氧化二铋(bi2o3)和56.0gγ-丁内酯混合,采用细胞粉碎机进行超声分散,得到固含量为30wt.%的显影剂分散液,bi2o3的平均粒径为4.5μm。
将80.0g显影剂分散液与30.0g聚酰亚胺前驱体树脂溶液混合,采用配有齿盘式搅拌桨的高速分散机以2000rpm转速混合分散30分钟,得到粘度为13pa
·
s的聚酰亚胺树脂浆料(piv-4)。
49.将piv-4聚酰亚胺树脂浆料置于浸胶槽中,金属芯线通过浸胶槽使树脂浆料附着于表面,以模头调控上胶量,在120℃下进行预烘干处理,得到单层树脂包覆的芯线,经250℃热烘处理完成部分亚胺化反应后,冷却至室温,抽出金属芯线,再经400℃高温亚胺化处理,得到具有x射线显影性的聚酰亚胺导管pi-4,导管中显影剂含量为80wt.%,管壁厚度为50μm。具有x射线显影性的树脂浆料与导管的主要性能见表1。
50.实施例5
51.在三口烧瓶中加入12.97g(0.06mol)的3,3'-二羟基联苯二胺(hab)和65.31g的n,n-二甲基乙酰胺(dmac),在氮气保护下搅拌至完全溶解后,加入21.50g(0.06mol)二苯砜四酸二酐(dsda)与15.12g dmac,室温搅拌反应12小时后,按照40℃/2小时、60℃/1小时的程序梯度升温反应后降至室温,得到固含量为30wt.%、粘度为200pa
·
s的聚酰亚胺前驱体树脂溶液。在烧杯中将54.0g钨粉和126.0g dmac混合,采用细胞粉碎机进行超声分散,得到固含量为30wt.%的显影剂分散液,钨粉的平均粒径为10.0μm。将180.0g显影剂分散液与20.0g聚酰亚胺前驱体树脂溶液混合,采用配有齿盘式搅拌桨的高速分散机以2000rpm转速混合分散30分钟,得到粘度为10pa
·
s的聚酰亚胺树脂浆料(piv-5)。
52.将piv-5聚酰亚胺树脂浆料置于浸胶槽中,金属芯线通过浸胶槽使树脂浆料附着于表面,以模头调控上胶量,在60℃下进行预烘干处理,得到单层树脂包覆的芯线,经200℃热烘处理完成部分亚胺化反应后,冷却至室温,抽出金属芯线,再经300℃高温亚胺化处理,得到具有x射线显影性的聚酰亚胺导管pi-5,导管中显影剂含量为90wt.%,管壁厚度为20μm。具有x射线显影性的树脂浆料与导管的主要性能见表1。
53.实施例6
54.在三口烧瓶中加入6.01g(0.03mol)的4,4'-二氨基二苯醚(4,4'-oda)和122.64g的n-甲基吡咯烷酮(nmp),在氮气保护下搅拌至完全溶解后,加入8.83g(0.03mol)联苯四酸二酐(bpda)与10.86g nmp,室温搅拌反应12小时后,按照40℃/2小时、60℃/1小时、70℃/1小时的程序梯度升温反应后降至室温,得到固含量为10wt.%、粘度为190pa
·
s的聚酰亚胺前驱体树脂溶液。在烧杯中将8.0g铋粉和25.3g nmp混合,采用细胞粉碎机进行超声分散,得到固含量为24wt.%的显影剂分散液,铋粉的平均粒径为3.0μm。将33.3g显影剂分散液与20g聚酰亚胺前驱体树脂溶液混合,采用配有齿盘式搅拌桨的高速分散机以2000rpm转速混合分散30分钟,得到粘度为15pa
·
s的聚酰亚胺树脂浆料(piv-6)。
55.将piv-6聚酰亚胺树脂浆料置于浸胶槽中,金属芯线通过浸胶槽使树脂浆料附着于表面,以模头调控上胶量,在100℃下进行预烘干处理,得到单层树脂包覆的芯线,经230℃热烘处理完成部分亚胺化反应后,冷却至室温,抽出金属芯线,再经370℃高温亚胺化处理,得到具有x射线显影性的聚酰亚胺导管pi-6,导管中显影剂含量为80wt.%,管壁厚度为50μm。具有x射线显影性的树脂浆料与导管的主要性能见表1。
56.实施例7
57.在三口烧瓶中加入5.01g(0.025mol)的4,4'-二氨基二苯醚(4,4'-oda)、2.70g(0.025mol)的对苯二胺(p-pda)和72.06g的n-甲基吡咯烷酮(nmp),在氮气保护下搅拌至完
全溶解后,加入14.71g(0.05mol)联苯四酸二酐(bpda)与17.62g nmp,室温搅拌反应12小时后,按照40℃/2小时、70℃/1小时、80℃/1小时的程序梯度升温反应后降至室温,得到固含量为20wt.%、粘度为200pa
·
s的聚酰亚胺前驱体树脂溶液。在烧杯中将2.0g钨粉、4.0g铋粉和54.0g nmp混合,采用细胞粉碎机进行超声分散,得到固含量为10wt.%的显影剂分散液。将60.0g显影剂分散液与30.0g聚酰亚胺前驱体树脂溶液混合,采用配有齿盘式搅拌桨的高速分散机以2000rpm转速混合分散15分钟,得到粘度为13pa
·
s的聚酰亚胺树脂浆料(piv-7)。
58.将piv-7聚酰亚胺树脂浆料置于浸胶槽中,金属芯线通过浸胶槽使树脂浆料附着于表面,以模头调控上胶量,在100℃下进行预烘干处理,得到单层树脂包覆的芯线,经230℃热烘处理完成部分亚胺化反应后,冷却至室温,抽出金属芯线,再经370℃高温亚胺化处理,得到具有x射线显影性的聚酰亚胺导管pi-7,导管中显影剂含量为50wt.%,管壁厚度为30μm。具有x射线显影性的树脂浆料与导管的主要性能见表1。
59.实施例8
60.在三口烧瓶中加入10.01g(0.05mol)的4,4'-二氨基二苯醚(4,4'-oda)和75.66g的n-甲基吡咯烷酮(nmp),在氮气保护下搅拌至完全溶解后,加入5.45g(0.025mol)均苯四酸二酐(pmda)、7.36g(0.025mol)联苯四酸二酐(bpda)与15.62g nmp,室温搅拌反应12小时后,按照50℃/2小时、70℃/1小时的程序梯度升温反应后降至室温,得到固含量为20wt.%、粘度为179pa
·
s的聚酰亚胺前驱体树脂溶液。在烧杯中将9.3g三氧化钨(wo3)、4.7g三氧化二铋(bi2o3)和32.7gnmp混合,采用细胞粉碎机进行超声分散,得到固含量为30wt.%的显影剂分散液。将46.7g显影剂分散液与30.0g聚酰亚胺前驱体树脂溶液混合,采用配有齿盘式搅拌桨的高速分散机以2000rpm转速混合分散20分钟,得到粘度为22pa
·
s的聚酰亚胺树脂浆料(piv-8)。
61.将piv-8聚酰亚胺树脂浆料置于浸胶槽中,金属芯线通过浸胶槽使树脂浆料附着于表面,以模头调控上胶量,在100℃下进行预烘干处理,得到单层树脂包覆的芯线,经230℃热烘处理完成部分亚胺化反应后,冷却至室温,抽出金属芯线,再经370℃高温亚胺化处理,得到具有x射线显影性的聚酰亚胺导管pi-8,导管中显影剂含量为70wt.%,管壁厚度为60μm。具有x射线显影性的树脂浆料与导管的主要性能见表1。
62.实施例9
63.将实施例6中得到的piv-6聚酰亚胺树脂浆料置于浸胶槽中,金属芯线通过浸胶槽使树脂浆料附着于表面,以模头调控上胶量,在100℃下进行预烘干处理后,将上述芯线通过装有实施例1中得到的piv-1聚酰亚胺树脂浆料的浸胶槽,以模头调控上胶量,在100℃下进行预烘干处理后,得到双层树脂包覆的芯线,经230℃热烘处理完成部分亚胺化反应后,冷却至室温,抽出金属芯线,再经370℃高温亚胺化处理,得到具有x射线显影性的聚酰亚胺导管pi-9,管壁总厚度为70μm。具有x射线显影性的树脂浆料与导管的主要性能见表1。
64.实施例10
65.将实施例1中得到的piv-1聚酰亚胺树脂浆料置于浸胶槽中,金属芯线通过浸胶槽使树脂浆料附着于表面,以模头调控上胶量,在60℃下进行预烘干处理后,将上述芯线通过装有实施例2中得到的piv-2聚酰亚胺树脂浆料的浸胶槽,以模头调控上胶量,在60℃下进行预烘干处理后,得到双层树脂包覆的芯线,经200℃热烘处理完成部分亚胺化反应后,冷
却至室温,抽出金属芯线,再经300℃高温亚胺化处理,得到具有x射线显影性的聚酰亚胺导管pi-10,管壁总厚度为40μm。具有x射线显影性的树脂浆料与导管的主要性能见表1。
66.实施例11
67.将实施例5中得到的piv-5聚酰亚胺树脂浆料置于浸胶槽中,金属芯线通过浸胶槽使树脂浆料附着于表面,以模头调控上胶量,在60℃下进行预烘干处理后,将上述芯线通过装有实施例2中得到的piv-2聚酰亚胺树脂浆料的浸胶槽,以模头调控上胶量,在60℃下进行预烘干处理后,得到双层树脂包覆的芯线,经200℃热烘处理完成部分亚胺化反应后,冷却至室温,抽出金属芯线,再经300℃高温亚胺化处理,得到具有x射线显影性的聚酰亚胺导管pi-11,管壁总厚度为70μm。具有x射线显影性的树脂浆料与导管的主要性能见表1。
68.对比例1
69.在三口烧瓶中加入8.01g(0.04mol)的4,4'-二氨基二苯醚(4,4'-oda)和85.05g的n,n
’‑
二甲基乙酰胺(dmac),在氮气保护下搅拌至完全溶解后,加入8.72g(0.04mol)均苯四酸二酐(pmda)与9.78g dmac,室温搅拌反应12小时后,得到固含量为15wt.%、粘度为840pa
·
s的聚酰亚胺前驱体树脂溶液。在烧杯中将4.5g钨粉和18.0g dmac混合,采用细胞粉碎机进行超声分散,得到固含量为20wt.%的显影剂分散液,钨粉的平均粒径为1.6μm。将22.5g显影剂分散液与30.0g聚酰亚胺前驱体树脂溶液混合,采用配有齿盘式搅拌桨的高速分散机以1500rpm转速混合分散15分钟,得到粘度为61pa
·
s的聚酰亚胺树脂浆料(piv-1a)。
70.将piv-1a聚酰亚胺树脂浆料置于浸胶槽中,金属芯线通过浸胶槽使树脂浆料附着于表面,以模头调控上胶量,在60℃下进行预烘干处理,得到单层树脂包覆的芯线,经200℃热烘处理完成部分亚胺化反应后,冷却至室温,抽出金属芯线,再经300℃高温亚胺化处理,得到具有x射线显影性的聚酰亚胺导管pi-12,导管中显影剂含量为50wt.%,管壁厚度为20μm。具有x射线显影性的树脂浆料与导管的主要性能见表1。
71.对比例2
72.在三口烧瓶中加入8.01g(0.04mol)的4,4'-二氨基二苯醚(4,4'-oda)和82.78g的n,n
’‑
二甲基乙酰胺(dmac),在氮气保护下搅拌至完全溶解后,加入8.72g(0.04mol)均苯四酸二酐(pmda)与12.05g dmac,室温搅拌反应12小时后,按照60℃/2小时、70℃/1小时的程序梯度升温反应后降至室温,得到固含量为15wt.%、粘度为172pa
·
s的聚酰亚胺前驱体树脂溶液。将4.5g钨粉与30.0g聚酰亚胺前驱体树脂溶液混合,钨粉的平均粒径为1.6μm,采用配有齿盘式搅拌桨的高速分散机以1500rpm转速混合分散15分钟,得到粘度为185pa
·
s的聚酰亚胺树脂浆料(piv-1b)。
73.将piv-1b聚酰亚胺树脂浆料置于浸胶槽中,金属芯线通过浸胶槽使树脂浆料附着于表面,以模头调控上胶量,在60℃下进行预烘干处理,得到单层树脂包覆的芯线,经200℃热烘处理完成部分亚胺化反应后,冷却至室温,抽出金属芯线,再经300℃高温亚胺化处理,得到具有x射线显影性的聚酰亚胺导管pi-13,导管中显影剂含量为50wt.%,管壁厚度为20μm。具有x射线显影性的树脂浆料与导管的主要性能见表1。
74.对比例3
75.在三口烧瓶中加入8.01g(0.04mol)的4,4'-二氨基二苯醚(4,4'-oda)和83.73g的n,n
’‑
二甲基乙酰胺(dmac),在氮气保护下搅拌至完全溶解后,加入8.72g(0.04mol)均苯四
酸二酐(pmda)与11.10g dmac,室温搅拌反应12小时后,按照60℃/2小时、70℃/1小时的程序梯度升温反应后降至室温,得到固含量为15wt.%、粘度为156pa
·
s的聚酰亚胺前驱体树脂溶液。在烧杯中将1.1g钨粉和4.5g dmac混合,采用细胞粉碎机进行超声分散,得到固含量为20wt.%的显影剂分散液,钨粉的平均粒径为1.6μm。将5.6g显影剂分散液与30.0g聚酰亚胺前驱体树脂溶液混合,采用配有齿盘式搅拌桨的高速分散机以1500rpm转速混合分散15分钟,得到粘度为24pa
·
s的聚酰亚胺树脂浆料(piv-1c)。
76.将piv-1c聚酰亚胺树脂浆料置于浸胶槽中,金属芯线通过浸胶槽使树脂浆料附着于表面,以模头调控上胶量,在60℃下进行预烘干处理,得到单层树脂包覆的芯线,经200℃热烘处理完成部分亚胺化反应后,冷却至室温,抽出金属芯线,再经300℃高温亚胺化处理,得到具有x射线显影性的聚酰亚胺导管pi-14,导管中显影剂含量为20wt.%,管壁厚度为20μm。具有x射线显影性的树脂浆料与导管的主要性能见表1。
77.对比例4
78.在三口烧瓶中加入8.65g(0.08mol)的对苯二胺(p-pda)和86.93g的n,n
’‑
二甲基乙酰胺(dmac),在氮气保护下搅拌至完全溶解后,加入8.72g(0.08mol)均苯四酸二酐(pmda)与11.53g dmac,室温搅拌反应12小时后,按照50℃/2小时、70℃/1小时的程序梯度升温反应后降至室温,得到固含量为15wt.%、粘度为164pa
·
s的聚酰亚胺前驱体树脂溶液。在烧杯中将4.5g钨粉和18.0g dmac混合,采用细胞粉碎机进行超声分散,得到固含量为20wt.%的显影剂分散液,钨粉的平均粒径为1.6μm。将22.5g显影剂分散液与30.0g聚酰亚胺前驱体树脂溶液混合,采用配有齿盘式搅拌桨的高速分散机以1500rpm转速混合分散15分钟,得到粘度为16pa
·
s的聚酰亚胺树脂浆料(piv-1d)。
79.将piv-1d聚酰亚胺树脂浆料置于浸胶槽中,金属芯线通过浸胶槽使树脂浆料附着于表面,以模头调控上胶量,在60℃下进行预烘干处理,得到单层树脂包覆的芯线,经200℃热烘处理完成部分亚胺化反应后,冷却至室温,抽出金属芯线,再经300℃高温亚胺化处理,得到具有x射线显影性的聚酰亚胺导管pi-15,导管中显影剂含量为50wt.%,管壁厚度为20μm。具有x射线显影性的树脂浆料与导管的主要性能见表1。
80.表1、聚酰亚胺浆料和聚酰亚胺导管的性能
[0081][0082]
*聚酰亚胺树脂浆料的粘度采用brookfield旋转粘度计测定;
[0083]
聚酰亚胺导管的力学性能采用万能材料试验机按照gb1447-83测定;
[0084]
聚酰亚胺导管的显影性能采用x射线三维分层成像仪以灰度值进行评价,测试电压80kv。
[0085]
对比例1与实施例1相比,未采用加热降粘的方式;对比例2与实施例1相比,未制备显影剂分散液;对比例3与实施例1相比,显影剂的添加量为20wt.%;对比例4与实施例1相比,主链中不含柔性结构。从表1中数据发现,对比例1与对比例2中得到的聚酰亚胺浆料粘度均太高,使得共混过程中显影剂在聚酰亚胺前驱体树脂溶液难以均匀分散,因而导致力学性能明显下降,同时显影效果较差;对比例3中显影剂添加量低于50wt.%,其显影效果显著下降;对比例4中未采用柔性结构,导致导管的刚性太高,断裂伸长率偏低。
[0086]
另外,为了进一步证明本发明的技术效果,还进行了下列测试:
[0087]
图1为实施例1制备的聚酰亚胺树脂浆料的扫描电镜能谱,图中白色点状物代表钨元素,可以证明钨粉在聚酰亚胺树脂浆料中分散均匀。
[0088]
图2为实施例1制备的显影性聚酰亚胺导管的扫描电镜照片,可以证明制备的显影性导管管壁为20μm,管径为0.5mm。
[0089]
图3为实施例1制备的聚酰亚胺显影性导管在x射线能量为80kev下的显影照片,图
中导管(左侧)与底板(右侧)灰度的显著差异证明导管具有良好的显影性。
[0090]
以上所述,仅为本发明较佳的具体实施方式,但本发明的保护范围并不局限于此,任何熟悉本技术领域的技术人员在本发明揭露的技术范围内,可轻易想到的变化或替换,都应涵盖在本发明的保护范围之内。
再多了解一些
本文用于企业家、创业者技术爱好者查询,结果仅供参考。