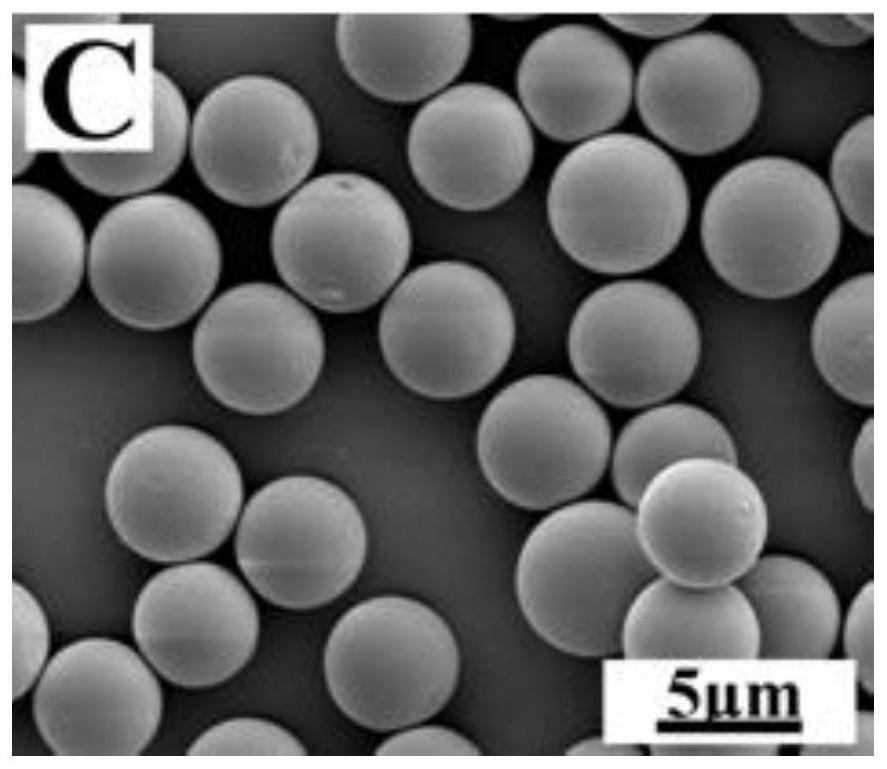
1.本发明涉及功能高分子材料技术领域,具体涉及一种单分散聚酯胺微球的制备方法。
背景技术:
2.溶剂型胶黏剂的固含量大约为30%-50%之间,需要使用大量的有机溶剂,因此环境污染问题较为突出,乳液型胶黏剂固含量约为55%,以水为分散介质,但其耐水性比较差,热熔胶黏剂虽然不使用任何介质,但耐热、耐溶剂性比较差,又容易发生爆聚。不使用有机溶剂而又能避免普通乳液型胶黏剂耐水性差、热熔胶耐热、耐溶剂差、易爆聚的缺点的新型胶黏剂已成为业界追求的目标。uv固化胶黏剂是将可聚合单体、低聚体或聚合物弹性体以及增粘树脂光引发剂和防老剂等其它添加剂组成的混合物均匀涂布于基材上,再通过一定剂量的高能射线(紫外线或电子束)辐射涂层使其聚合、交联并固化,从而获得各种性能的胶黏剂制品。uv固化胶黏剂是环境友好、无污染又节能的绿色胶黏剂。
3.填料是胶黏剂必不可少的组成部分,以改善胶黏剂的机械性能、降低胶接接头应力、降低成本、减小收缩率以及赋予胶黏剂新的功能。这些填料多为白炭黑、碳酸钙等无机微纳米粒子,与胶黏剂基质相容性差,分散性不佳,往往产生应力集中点,影响胶黏剂使用性能,不得不采用偶联剂对无机填料进行修饰改性。
4.针对上述问题,制备一种表面富含可uv激发并与丙烯酸酯基进行自由基反应基团的聚合物微纳米粒子具有重要的研究价值及实际应用价值。聚合物微球不仅具有可设计的化学结构和组成,而且与胶黏剂基质的相容性好。由于聚合过程中无需加入任何稳定剂或表面活性剂,沉淀聚合可制备具有清洁表面的单分散聚合物微球。为此,我们以多元胺和酸酯为反应单体,在溶剂中通过aza-michael加成沉淀聚合制备系列可用于uv固化胶黏剂填料的单分散聚酯胺微球。
技术实现要素:
5.本发明的目的在于提供一种单分散聚酯胺微球的制备方法。本发明的单分散聚酯胺微球的制备方法通过沉淀聚合制备的用于uv固化胶黏剂增韧填料的单分散聚酯胺微球(聚酯-胺微球);该方法无需任何乳化剂、稳定剂或催化剂等组分,直接将多元胺和酸酯(多元丙烯酸酯)单体加入到溶剂中进行沉淀聚合,不仅步骤简单,所得微球非常洁净,制备单分散聚酯胺微球的表面洁净分散性较好,使制备的聚酯胺微球表面具有不饱和羰基化合物,为后续的uv固化提供了良好的活性位点,具有较高的热稳定性。
6.为解决以上技术问题,本发明提供的技术方案是:
7.一种单分散聚酯胺微球的制备方法,包括如下步骤:
8.1)将多元胺和多元丙烯酸酯按照氨基与双键摩尔比溶于反应介质(有机溶剂)中,控温静置进行逐步沉淀聚合;
9.2)离心除去有机溶剂,真空干燥,得到单分散的聚酯胺微球;
10.所述多元胺和多元丙烯酸酯单体的总加入量占反应体系总质量的1~30%;
11.所述将多元胺和多元丙烯酸酯按照氨基与双键摩尔比溶于有机溶剂中为将所述多元胺中亚胺基与所述多元丙烯酸酯中碳碳双键的摩尔比(-nh/c=c)为0.5~1.7﹕0.5~1.7溶于有机溶剂中。
12.优选的,所述酸酯和多元胺单体在反应介质中溶解后,将反应体系密封,于0~50℃、振荡频率0~150osc/min的条件下聚合反应;反应完成后,将产物进行离心分离或抽滤,所得固体经洗涤后干燥,即得单分散聚酯-胺微球。
13.优选的,所述多元胺选自下列中的一种:乙二胺、二乙烯三胺、三乙烯四胺、四乙烯五胺、哌嗪、己二胺、二亚乙基二胺、甲苯二胺。
14.优选的,所述多元丙烯酸酯选自下列中的一种或多种的组合:三丙烯酸丙烷三甲醇酯、二丙二醇二丙烯酸酯、三羟甲基丙烷三丙烯酸酯、羟甲基丙烯酸酯、三甲基丙烷三丙烯酸酯。
15.优选的,所述反应介质为水、丙酮和乙腈中的任意一种或多种的混合物。
16.更优选的,所述反应介质为乙腈。使用该反应介质可使酸酯和多元胺单体完全溶解,提高产率。
17.优选的,所述多元胺和多元丙烯酸酯单体的总加入量占反应体系总质量的2~25%。
18.优选的,所述将多元胺和多元丙烯酸酯按照氨基与双键摩尔比溶于有机溶剂中为将所述多元胺中亚胺基与所述多元丙烯酸酯中碳碳双键的摩尔比(-nh/c=c)为0.7~1.5﹕0.7~1.5溶于有机溶剂中。
19.优选的,所述沉淀聚合的聚合温度为0~50℃,且反应过程中的振频为0~150osc/min。
20.优选的,聚合反应时间为5~150min;更优选的,聚合反应时间为10~30min。
21.优选的,所述沉淀聚合的聚合反应结束后,将产物进行抽滤,或将产物加入离心管中在5000~20000r/min下离心2~8min,将所得固体用丙酮或乙腈洗涤2~3次后在70~100℃下干燥2~8h,即得单分散聚酯-胺微球。
22.优选的,制备方法如下:
23.在室温下,在反应容器中加入15~70g反应介质,所述反应介质为水、丙酮和乙腈中的任意一种或多种的混合物;再分别加入-nh/c=c摩尔比为0.5~1.7﹕0.5~1.7的二亚乙基二胺和三羟甲基丙烷三丙烯酸酯共10~30g,使体系总质量达到100g;随后,将反应瓶密封并置室温静置的条件下反应10~30min;将产物抽滤以去除上清液,所得固体用丙酮或乙腈洗涤两次后在50℃下干燥至恒重。
24.优选的,在室温下,在反应瓶中加入15~70g反应介质,所述反应介质是乙腈,再分别加入-nh/c=c摩尔比为1﹕1的二亚乙基二胺和三羟甲基丙烷三丙烯酸酯共10~30g,使体系总质量达到100g。随后,将反应瓶密封并置于冰箱储藏室中,在温度为4℃静置的条件下反应10~30min。将产物抽滤以去除上清液,所得固体用丙酮或乙腈洗涤两次后在70℃下干燥5h,即得单分散聚酯-胺微球。
25.本发明中,所得单分散聚酯胺微球的平均粒径为3.0~5.0μm,粒径多分散系数为1.006~1.201。所得单分散聚酯-胺微球的产率为50.0~80.0%。
26.本发明与现有技术相比,具有以下优点及有益效果:
27.本发明以二亚乙基二胺和三羟甲基丙烷三丙烯酸酯为单体,在乙腈溶剂中通过沉淀聚合制备单分散聚酯-胺微球。本方法操作简单,且无需任何乳化剂、稳定剂及催化剂等组分,所得微球非常洁净。
28.与现有沉淀聚合体系相比,本发明最突出的特点是成功的将胺-烯反应用于聚合物微球的制备,同时以聚合物微球为载体进行uv固化胶黏剂增韧的应用。本发明使用的单体加入量过多或温度较高时反应速率过快使pea微球出现多胞粘连现象,单体加入量较少或温度较低时,反应速率较慢,形成初级粒子时间较长,导致微球粒径不均一。需要选择特定的反应条件才有可能制得新型的单分散聚酯-胺微球。因此,单体加入量和反应温度是本发明制备新型的单分散聚酯胺微球的关键。本发明人意外发现,当以二亚乙基二胺和三羟甲基丙烷三丙烯酸酯按照特定的配比以乙腈为反应介质时可制备新型的单分散聚酯-胺微球,而以其他摩尔比反应时微球不能呈现很好的形态。
29.本发明方法制备了表面洁净分散性较好的微球,且聚合过程中可以不使用任何搅拌和振荡设备,生产成本和能耗较低,这些是本发明的另一显著特点。通过对本方法聚合过程中的粒子的表征发现,通过控制加入单体的摩尔比可以改性所制备的聚酯胺微球,使制备的聚酯胺微球表面具有c=c活性基团,为后续的uv固化提供了良好的活性位点。通过对搅拌速度或振荡频率的探讨,发现本方法能够在静置不搅拌条件下制得单分散的聚酯胺微球,这使得本发明摆脱了对搅拌或振荡设备的依赖,生产成本和能耗也显著降低。由上可见,本发明使得制备单分散微球的成本和效率得到显著改善。
30.与现有技术相比具有如下优点:
31.1.现有技术制备单分散聚酯胺微球时不仅步骤繁琐,条件苛刻,且需添加乳化剂、稳定剂及催化剂等组分,这些物质吸附至微球表面后难以去除,限制了聚酯胺聚合物微球的应用及发展,尤其是在生物和医药等领域。本发明方法通过沉淀聚合制备单分散聚酯-胺微球,操作简单,且无需任何乳化剂、稳定剂及催化剂等组分,所得微球非常洁净,可用于生物医药等领域。
32.2.现有沉淀聚合技术制备单分散聚酯胺微球时获得的聚合物微球表面不含或很少含有uv活性基团。本发明制备单分散聚酯胺微球表面含有大量的可调控的uv活性基团。
33.3.现有沉淀聚合技术制备单分散聚酯胺微球时需要静置的条件下反应。本发明同时在反应过程中只需将反应瓶密封并置于室温,无需任何搅拌或振荡设备,具有生产效率高、生产成本和能耗低的特点。
34.4.本发明可通过变化加入二亚乙基二胺和三羟甲基丙烷三丙烯酸酯的加入量、反应温度、反应时间等条件调控所得单分散聚酯-胺微球的粒径,满足不同场合对微球的要求。
附图说明
35.图1是实施例1所得单分散聚酯-胺微球的扫描电镜照片。
36.图2是实施例4使得单分散聚酯-胺微球的扫描电镜照片。
具体实施方式
37.为了使本领域的技术人员更好地理解本发明的技术方案,下面结合具体实施例对本发明的优选实施方案进行描述,但是不能理解为对本专利的限制。
38.下述实施例中所述试验方法或测试方法,如无特殊说明,均为常规方法;所述试剂和材料,如无特殊说明,均从常规商业途径获得,或以常规方法制备。
39.室温:具有本领域公知的含义,一般是指25
±
2℃。
40.如无特别说明,本技术中所述的“%”均为质量百分比。
41.使用美国fei公司quantafeg-250型扫描电子显微镜观察所得单分散聚酯-胺微球的形貌。从电镜照片中量取至少100个微球的粒径,根据下式计算微球的平均粒径(dn)及其多分散系数(dw/dn):
[0042][0043]
其中,dn为微球的数均粒径,dw为重均粒径,k为测量的微球总数,di是第i个微球的粒径,ni为粒径为di的微球的数目。
[0044]
实施例1.
[0045]
在室温下,在30ml玻璃反应瓶中,以乙腈18.8g为反应溶剂,加入单体tmpta0.9678 g和哌嗪0.2322g,加入量占体系总质量的6wt%,密封并振摇反应瓶使各组分混合均匀,将反应瓶置于4℃冰箱储藏室中静置反应12h后取出。将产物进行抽滤,所得固体用乙腈溶液洗涤3次,置于70℃鼓风干燥箱中干燥至恒重,得到pea微球。
[0046]
所得聚酯-胺微球的产率为72.44%,微球的扫描电子显微镜照片如图1所示,由此测得微球的平均粒径为4.52μm,粒径多分散系数为1.011。
[0047]
实施例2.
[0048]
在室温下,在30ml玻璃反应瓶中,以乙腈18.8g为反应溶剂,加入单体tmpta0.9398 g和哌嗪0.2602g,加入量占体系总质量的6wt%,密封并振摇反应瓶使各组分混合均匀,将反应瓶置于4℃冰箱储藏室中静置反应12h后取出。将产物进行抽滤,所得固体用乙腈溶液洗涤3次,置于70℃鼓风干燥箱中干燥至恒重,得到pea微球。
[0049]
所得聚酯-胺微球的产率为69.88%,微球的平均粒径为4.01μm,粒径多分散系数为1.025。
[0050]
实施例3.
[0051]
在室温下,在30ml玻璃反应瓶中,以乙腈18.8g为反应溶剂,加入单体tmpta0.9678 g和哌嗪0.2322g,加入量占体系总质量的6wt%,密封并振摇反应瓶使各组分混合均匀,将反应瓶置于30℃冰箱储藏室中静置反应12h后取出。将产物进行抽滤,所得固体用乙腈溶液洗涤3次,置于70℃鼓风干燥箱中干燥至恒重,得到pea微球。
[0052]
所得聚酯-胺微球的产率为67.43%,微球的平均粒径为3.47μm,粒径多分散系数为1.046。
[0053]
实施例4.
[0054]
在室温下,在30ml玻璃反应瓶中,以乙腈18.8g为反应溶剂,加入单体tmpta0.9678 g和哌嗪0.2322g,加入量占体系总质量的6wt%,密封并振摇反应瓶使各组分混合均匀,将反应瓶置于10℃下静置反应12h后取出。将产物进行抽滤,所得固体用乙腈溶液洗涤3次,置
于70℃鼓风干燥箱中干燥至恒重,得到pea微球。
[0055]
所得聚酯-胺微球的产率为71.20%,微球的扫描电子显微镜照片如图2所示,由此测得微球的平均粒径为3.54μm,粒径多分散系数为1.014。
[0056]
实施例5.
[0057]
在室温下,在30ml玻璃反应瓶中,以乙腈18.8g为反应溶剂,加入单体tmpta0.8522 g和哌嗪0.2477g,加入量占体系总质量的5.5wt%,密封并振摇反应瓶使各组分混合均匀,将反应瓶置于4℃冰箱储藏室中静置反应12h后取出。将产物进行抽滤,所得固体用乙腈溶液洗涤3次,置于70℃鼓风干燥箱中干燥至恒重,得到pea微球。
[0058]
所得聚酯-胺微球的产率为67.62%,微球的平均粒径为4.20μm,粒径多分散系数为1.013。
[0059]
实施例6.
[0060]
在室温下,在30ml玻璃反应瓶中,以乙腈18.8g为反应溶剂,加入单体tmpta 1.0072g和哌嗪0.2928g,加入量占体系总质量的6.5wt%,密封并振摇反应瓶使各组分混合均匀,将反应瓶置于4℃冰箱储藏室中静置反应12h后取出。将产物进行抽滤,所得固体用乙腈溶液洗涤3次,置于70℃鼓风干燥箱中干燥至恒重,得到pea微球。
[0061]
所得聚酯-胺微球的产率为73.36%,微球的平均粒径为4.07μm,粒径多分散系数为1.037。
[0062]
实施例7.
[0063]
在室温下,在30ml玻璃反应瓶中,以乙腈18.8g为反应溶剂,加入单体tmpta0.9678 g和哌嗪0.2322g,加入量占体系总质量的6wt%,密封并振摇反应瓶使各组分混合均匀,将反应瓶置于4℃冰箱储藏室中静置反应13h后取出。将产物进行抽滤,所得固体用乙腈溶液洗涤3次,置于70℃鼓风干燥箱中干燥至恒重,得到pea微球。
[0064]
所得聚酯-胺微球的产率为72.56%,微球的平均粒径为4.56μm,粒径多分散系数为1.016。
[0065]
实施例8.
[0066]
在室温下,在30ml玻璃反应瓶中,以乙腈18.8g为反应溶剂,加入单体tmpta0.9678 g和哌嗪0.2322g,加入量占体系总质量的6wt%,密封并振摇反应瓶使各组分混合均匀,将反应瓶置于4℃冰箱储藏室中静置反应15h后取出。将产物进行抽滤,所得固体用乙腈溶液洗涤3次,置于70℃鼓风干燥箱中干燥至恒重,得到pea微球。
[0067]
所得聚酯-胺微球的产率为72.61%,微球的平均粒径为4.55μm,粒径多分散系数为1.023。
[0068]
对比例1.
[0069]
在室温下,在30ml玻璃反应瓶中,以乙腈18.8g为反应溶剂,加入单体tmpta0.9678 g和哌嗪0.2322g,加入量占体系总质量的6wt%,密封并振摇反应瓶使各组分混合均匀,将反应瓶置于4℃冰箱储藏室中静置反应5h后取出。将产物进行抽滤,所得固体用乙腈溶液洗涤3次,置于70℃鼓风干燥箱中干燥至恒重,得到pea微球。
[0070]
该对比例聚合反应时间太短,许多低聚物仍保留在溶剂中,未被初级颗粒捕获,导致粒径减小,从而使球体具有粘性并且在分离过程中有缺陷。
[0071]
对比例2.
[0072]
在室温下,在30ml玻璃反应瓶中,以乙腈18.8g为反应溶剂,加入单体tmpta0.6198 g和哌嗪0.1802g,加入量占体系总质量的4wt%,密封并振摇反应瓶使各组分混合均匀,将反应瓶置于4℃冰箱储藏室中静置反应12h后取出。将产物进行抽滤,所得固体用乙腈溶液洗涤3次,置于70℃鼓风干燥箱中干燥至恒重,得到pea微球。
[0073]
该对比例单体浓度太低,有较长的浊化时间,体系中微球的成核时间较长,导致pea的均匀性变差。
[0074]
对比例3.
[0075]
在室温下,在30ml玻璃反应瓶中,以乙腈18.8g为反应溶剂,加入单体tmpta0.9678 g和哌嗪0.2322g,加入量占体系总质量的6wt%,密封并振摇反应瓶使各组分混合均匀,将反应瓶置于-18℃冰箱储藏室中静置反应12h后取出。将产物进行抽滤,所得固体用乙腈溶液洗涤3次,置于70℃鼓风干燥箱中干燥至恒重,得到pea微球。
[0076]
该对比例聚合反应温度太低,反应速率过慢,成核期过长,形成的微球粒径大小不一。
[0077]
以上仅是本发明的优选实施方式,应当指出的是,上述优选实施方式不应视为对本发明的限制,本发明的保护范围应当以权利要求所限定的范围为准。对于本技术领域的普通技术人员来说,在不脱离本发明的精神和范围内,还可以做出若干改进和润饰,这些改进和润饰也应视为本发明的保护范围。
再多了解一些
本文用于企业家、创业者技术爱好者查询,结果仅供参考。