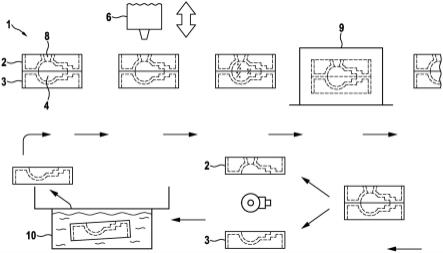
1.本发明涉及一种利用多个射芯模具的射芯方法,这些射芯模具分别具有至少两个在打开位置和关闭位置之间可调节的模具轮廓壳或模具半部,其中,射芯模具在关闭位置分别形成在几何形状上与待射的芯匹配的空腔。例如由fr3047429a1已知一种射芯方法。
背景技术:
2.为了铸造复杂的部件或成型件时,经常需要芯,其可以插入在铸模中,以便例如形成部件或成型件的空腔。这种芯可以利用射芯模具制造。在此,通常将由砂和粘合剂制成的芯成型材料注入射芯模具中。在此,芯成型材料呈现由模具包围的空腔的形状并且接着可以被硬化。为了硬化芯材料,例如可以对芯进行充气或者使气体流过该芯。替代地,可以通过热作用,特别是通过加热射芯模具来硬化芯。
3.由现有技术已知的方法具有的缺点是,为了硬化,在射芯机内,芯保留在射芯模具中并且由此对于芯的批量生产来说要把较高的周期时间计算在内。在此,芯必须在模具中被“烘烤”,直到其具有足够厚的壁。此外,不利的是,为了降低周期时间,需要高的硬化温度,然而,由此提高了模具磨损。
技术实现要素:
4.因此,本发明的目的是提供一种射芯方法,该方法实现以缩短的周期时间批量制造芯。
5.该目的通过根据权利要求1所提出的射芯方法来解决。并列的权利要求12涉及一种相应的射芯模具。本发明的有利实施方式分别是从属权利要求的主题。
6.因此,提出一种使用多个射芯模具的射芯方法,这些射芯模具分别在打开位置和关闭位置之间是可调节的,其中射芯模具在关闭位置分别形成在几何形状上与待射的芯匹配的空腔,其中该方法具有以下步骤顺序:
7.将第一射芯模具引入射芯机中;
8.将芯成型材料和粘合剂引入第一射芯模具中;
9.将第一射芯模具从射芯机排出;
10.将在第一射芯模具中的芯硬化;
11.利用至少一个另外的射芯模具重复前述步骤,其中,将另外的射芯模具引入射芯机中与将之前的射芯模具从射芯机排出同时进行或者与将在之前的射芯模具中的芯硬化同时进行。
12.本发明的主要优点在于,通过使用多个射芯模具并且将已经用芯成型材料填充的射芯模具从射芯机排出,一方面,不再依赖唯一的射芯模具,而是可以在第一射芯模具还位于机器中时就已经与之并行地为射芯过程准备好了另外的射芯模具。另一方面,存在很大的时间节约潜能,即,从机器中移出硬化过程并且转移到硬化炉中。同时,通过接受因降低硬化温度而延长的硬化时间,能够减少各个模具的负荷或使用环保的无机粘合剂。此外,已
磨损的模具可以逐渐地通过新的模具来替换,使得功能正常的射芯模具持续可供使用并且可以使机器停机时间最小化。
13.在此,可以在将芯成型材料和粘合剂引入第一射芯模具中之前将粘合剂设置到空腔的内面上。
14.可以规定,将第一射芯模具引入射芯机中包括:引入两个模具轮廓壳以及借助于曲柄杠杆装置将它们锁定到关闭位置。
15.特别是可以规定,将芯成型材料和粘合剂引入第一射芯模具中包括:将芯成型材料注入第一射芯模具中,并且将粘合剂注射到所注入的芯成型材料中。这例如可以通过具有多个注射喷嘴的注射装置来实现,该注射装置在将芯成型材料引入射芯模具的空腔中之后通过模具轮廓壳之一的相应的开口被引入,以便在该位置将粘合剂注射到成型材料中。例如可以通过射芯模具的通风喷嘴来实现注射装置的粘合剂的引入。替代地,可以设置用于通过蒸汽相或气相来引入粘合剂的装置。
16.还可以规定,将芯成型材料和粘合剂引入第一射芯模具中包括:将芯成形材料-粘合剂混合物注入射芯模具中。这特别是可以通过按照连续活塞原理工作的计量泵来实现,其中,粘合剂在喷嘴尖端中才能够与芯成型材料混合。
17.此外可以规定,为了硬化射芯模具中的芯,将射芯模具转移到硬化炉、特别是连续硬化炉中。射芯模具可以停留在炉中,直到粘合剂被硬化成使得能够移除的程度。在此,模具优选地在炉中被加热,直至形成稳定的边缘壳。炉例如可以是红外炉,以便快速加热。替代地,射芯模具可利用火焰加热或感应加热。在使用水泥粘合剂时,可以将炉子中的空气湿度保持在高水平。优选地,炉子可以具有循环空气机构,以便使空气湿度循环。
18.替代地,该方法通过气体硬化同样可执行。为此,模具在关闭之后可以被引入密封的腔室中,而不是炉中。在那里,例如用co2或胺气环绕冲扫模具,直至气体侵入整个芯。接着,模具可以从密封的腔室中被取出并且被打开,使得可以取出硬化的芯。
19.还可以考虑,该方法是一种壳模法(maskenform)或是壳型铸造工艺(croning-prozess)。在此,包覆有粘合剂的芯成型材料可以被注入射芯模具中。接着,模具可以在炉中被加热,直到形成稳定的边缘壳,其中,炉例如可以是红外炉以便快速加热,替代地,射芯模具可以通过火焰加热或感应加热。松散材料特别是可以从芯排出以改进气体渗透性。
20.替代地可以规定,该方法利用冷硬化的粘合剂例如减缓的呋喃树脂、水泥粘合剂或石膏粘合剂来执行。在此,可以将模具在注射芯之后引入炉中并且在那里在适当的温度下停留,直到粘合剂硬化到能够进行提取的程度。在此,在使用水泥粘合剂的情况下,炉中的空气湿度可以保持在高水平。
21.此外可以规定,该方法是冷箱方法。与热箱方法相比,冷箱方法的优点特别在于可以使用更轻的模具。通过较低的工艺温度,还可以实现通过热箱方法所实现的较小的磨损和的明显的成本优势。同样可以考虑,该方法作为热箱工艺利用无机的或其他热硬化的粘合剂系统来执行。
22.此外可以规定,粘合剂是无机粘合剂。无机粘合剂的优点特别是,它们比有机粘合剂更加环保,并且在浇注时产生较少的烟雾。由此通过减少气味的产生来减轻工作人员的负担并且避免浇注模具上的冷凝物沉积。
23.在此可以规定,在芯硬化时的硬化温度小于或等于110℃,优选小于或等于100℃,
特别优选小于或等于90℃。这一方面使得能够使用无机粘合剂,另一方面使得能够使用塑料制成的模具壳或实现较低的模具磨损。
24.特别是可以规定,在芯硬化之后打开射芯模具并且取出硬化的芯。
25.此外可以规定,在取出芯之后清洁射芯模具,将其设置回可注入的状态,并且接着重新将其引入射芯机中。通过清洁“离线”地完成,也可以从周期时间中减去这个生产步骤的持续时间。此外,将尽可能多的功能从射芯机中移出来的优点是,减少射芯机的功能范围并且使射芯机从根本上减少了简单的砂输送装置。此外,通过有规律地从机器中取出模具,可以有规律地控制模具状态,使得从根本上改善模具状态。这导致,可以以较低的压力注射芯,这又有利地减少模具磨损和能量消耗。此外,射芯机零件的单个失效不会导致整个设备失效。此外,质量保证措施可以更简单地执行。可以规定,在清洁工位上对射芯位置大概地进行清洁。在此,特别是可以进行注射喷嘴的清洁和/或对成型面的清洁和/或对连接面、密封面和靠置面的清洁。
26.此外可以规定,在多个射芯模具中的每一个中形成相同的在几何形状上匹配的空腔。通过使用相同的模具壳可以避免在各个射芯过程之间的耗费时间的改装过程。此外,由于许多相同的可供使用的模具壳,芯的硬化在保持较低的周期时间的情况下需要更多的时间。因此,通过多个相同的射芯模具的这种冗余能够实现耗费时间的并且不是强制性地在机器内部待实施的步骤的移出,例如硬化、取芯、清洁和重新设置回可注射的状态。
27.此外,公开了一种用于执行射芯方法的射芯模具,该射芯模具具有:第一模具轮廓壳和第二模具轮廓壳,这两个模具轮廓壳在关闭位置和打开位置之间来回可调节,其中,在关闭位置,在射芯模具中形成在几何形状上与待射的芯匹配的空腔;至少一个用于将芯成型材料和/或粘合剂引入空腔中的注入孔;以及至少一个框架,其用于将射芯模具移入射芯机和从射芯机移出,该框架具有至少一个水平和/或竖直地支撑的支撑元件,用于接收作用在模具轮廓壳上的力。
28.为此,可以设置至少一个用于自动关闭的关闭元件,特别是至少两个在关闭位置将模具轮廓壳固定的关闭夹具。关闭夹具特别是可以构造为c形型材,它们包围下模具轮廓壳和上模具轮廓壳并且在此产生预定的夹紧力。在此,c形型材可以构造为通过轨道引导侧向可调节。此外,c形型材可以通过液压装置而高度可调节,使得通过该液压装置可调节型材宽度。关闭元件还可以构造为安装在射芯模具上的曲柄杠杆关闭元件。替代地,可以规定,这些模具轮廓壳被拧接在一起。
29.可以规定,模具轮廓壳分别具有小于20毫米、优选小于10毫米、特别优选小于5毫米的壁厚。使用薄的模具轮廓壳特别是有利地影响材料消耗。此外,薄的模具轮廓壳具有的优点是,容纳在壳中的芯可以在硬化炉中更快地且以更少的能量输入被带到预定的硬化温度。
30.模具轮廓壳特别是可以基本上由塑料形成。在此,所谓的“浇注复制方法”可以用于制造模具。塑料特别是具有如下优点,即,其可更有利地且以更少的能量损耗来制造。此外,简化了操作,因为模具轮廓壳具有更小的重量。塑料例如可以具有聚合物。聚合物例如可以是热塑性塑料或热固性塑料。热塑性塑料可以具有以下组中的一种或更多种:聚酰胺、聚甲醛、聚丙烯、聚乙烯、丙烯腈-丁二烯-苯乙烯、聚苯硫醚、聚砜、聚甲基丙烯酸甲酯、聚苯乙烯、聚碳酸酯、聚碳酸酯/丙烯腈-丁二烯-苯乙烯、聚乙烯醚酮、聚乙烯丙烯酰酮、聚四氟
乙烯。热固性塑料可以包括以下组中的一种或更多种:聚氨酯、浇注聚酰胺、环氧树脂、三聚氰胺树脂、脲树脂、酚醛树脂、呋喃树脂。
31.此外,在模具轮廓壳中的至少一个上可以设置通风喷嘴。模具的通风可以替代地通过多个喷嘴实现,因为不必存在明确的排气通道。通过通风喷嘴一方面可以实现射芯模具的通风。此外可以考虑,通过通风喷嘴实现粘合剂的引入。替代地,可以附加地设置专门的进口喷嘴,通过该进口喷嘴将粘合剂引入射芯模具中。此外,替代地可以考虑,通过注入孔引入粘合剂。粘合剂可以作为气溶胶、气态或以其蒸汽相被引入射芯模具中。
32.替代地,模具轮廓壳可以是多孔的或打孔的。在这种模具轮廓壳中,粘合剂的引入可以通过浸渍工艺来实现。
附图说明
33.参考以下附图阐述本发明的示例性的实施方式。在此示出:
34.图1示出了待制造的铸件的实施例;
35.图2示出了下模具轮廓壳的实施例;
36.图3示出了在关闭位置借助夹具被夹紧的射芯模具的实施例;
37.图4示出了在设有夹具(未示出)的射芯模具中的射芯过程;
38.图5示出了在硬化炉中对被注射并且被夹紧的射芯模具进行加热;
39.图6示出了在使用多个射芯模具的情况下的示例性的循环系统;
40.图7a示出了一个实施例,其中粘合剂被设置在模具轮廓壳的内面;
41.图7b示出了根据图7a的实施例,其中在设置粘合剂之后将无粘合剂的砂注入/填充到射芯模具中;
42.图8a示出了另一实施例,其中在引入砂之后,通过在下模具轮廓壳中的通风喷嘴将粘合剂引入砂中;
43.图8b示出了根据图8a的实施例,其中注射器系统通过通风喷嘴将粘合剂引入砂中;
44.图9示出了具有侧向推移件的射芯模具的实施例。
具体实施方式
45.图1示例性地示出用于铸件16的砂芯,该砂芯对应于铸件的内轮廓的区段的凹形(negative)。在不使用芯的情况下将液态金属浇注到模子中导致实心的铸件16。但是如果铸件16出于复杂的几何构造的原因(例如为了减轻重量或允许介质通过)应当是空心的,则存在不同的方法,这借助于通过射芯方法产生的芯来实现。在此,待产生的空腔的模子用专门制备的成型材料制造。然后将砂芯置于模子内的应当产生空腔或底切的位置处。如果需要,该芯可用芯铁加强,以便在浇注过程中不会损坏该芯。
46.图2示出下模具轮廓壳3,其代表图1中的砂芯的轮廓的下半部。下模具轮廓壳3分别在其下侧、其上侧以及在侧壁上至少区段地具有平面支撑面,使得下模具轮廓壳可以容易地放入和移动到射芯机中,或者使得上模具轮廓壳2可以以特别简单的方式放置到下模具轮廓壳3上,或者实现紧固夹具5的毫无问题的紧固,以便将两个模具轮廓壳2、3抵靠彼此夹紧。
47.图3示出具有两个在其关闭位置的模具轮廓壳2、3的射芯模具1。模具轮廓壳2、3彼此上下叠放,使得在其内部形成在几何形状上与待制造的砂芯匹配的空腔4。优选地,在轮廓壳2、3中的靠置面可以构造成,使得这些靠置面具有自对中的功能,并且由此使轮廓壳2、3自动地相对彼此正确地对齐。例如,两个模具轮廓壳2、3的靠置面可以相对彼此互补地成角度。例如,下模具轮廓壳3的靠置面在此可以咽喉状地或漏斗形地以环绕的方式成角度并且上模具轮廓壳2的靠置面相对应地构造。在上模具轮廓壳2的上侧上构造有注入孔8,通过该注入孔可以将芯成型材料以及必要时还有粘合剂引入射芯模具1中。两个c形的夹具5从左边和右边侧向地包围射芯模具1的两个半部并且使它们在确定的预紧力下相对彼此保持。
48.图4示出在利用夹具5(未示出)关闭的射芯模具1中的射芯过程。射芯模具1被支撑在支承板7上。此外,射芯模具1通过该支承板7可移入射芯机中并且从射芯机中可移出。在射芯模具1上方示出竖直可调节的注射头6,该注射头利用相应的喷嘴对接到注入孔8,以便将必要的材料如砂和/或粘合剂注入射芯模具1的空腔4中。在此,借助于夹具5或曲柄杠杆装置来关闭模具可以在机器外部已经完成。替代地,两个模具轮廓壳2、3可以单独地引入机器中并且在该机器中才被关闭并且彼此夹紧。射芯模具通过支承板7的水平移动被定位在注射头6下方,注射头6接着竖直地行进到注入孔8中并且将砂和/或粘合剂注入空腔4中。
49.接着将射芯模具1连同关闭装置5和被注入的砂粘合剂混合物从射芯机转移到在图5中示出的硬化炉9中。在硬化炉9中,射芯模具1在预定的时间段内被加热到预定的温度,使得芯可以硬化。
50.图6示意性地示出用于制造芯且同时具有硬化工艺的根据本发明的射芯方法的流程。在此示出了射芯模具1经过该工艺的流程。在此,首先将下模具轮廓壳2以及上模具轮廓壳3彼此上下叠放,使得它们在内部形成在几何形状上匹配的空腔4。接着将模具轮廓壳2、3借助夹具5在预定的夹紧力下相互固定。接着将这样准备好的射芯模具1转移到射芯机中,在射芯机中将砂和/或粘合剂借助于注射头6经由注入孔8注入空腔4中。接着将射芯模具1连同被注入的砂-粘合剂-混合物一起转移到硬化炉9中,以便在那里硬化。在芯硬化之后,将射芯模具1从硬化炉9中取出并且将两个模具轮廓壳2、3彼此分开,使得可以取出芯。然后将两个模具轮廓壳2、3转送到清洁装置10处,在该清洁装置中,砂和粘合剂残余被去除并且将模具轮廓壳2、3恢复到可注入的状态。接着,准备两个模具轮廓壳2、3,以便注入另外的芯并且再次开始循环。与所示的射芯模具1并行地,多个另外的射芯模具1处于同一过程中,例如20件,以便实现射芯机的尽可能高的负荷程度。在此,每次一旦之前的射芯模具1已经离开射芯机并且被转送到硬化炉9中,另外的射芯模具1就被转移到射芯机中。硬化炉9在此优选是连续作业炉,它按照射芯机的周期时间接收各个后续的射芯模具1。
51.图7a示出了本发明的替代实施方式,其中,不是同时将砂粘合剂混合物注入空腔4中,而是在关闭模具轮廓壳2、3之前将粘合剂分别施加到空腔半部的内轮廓上。接着将壳关闭并且将芯成型材料经由注入开口8注入空腔4中,如图7b所示。
52.图8a和图8b示出了本发明的实施方式,其中,粘合剂既不通过注入孔8也不通过预先施加到空腔半部上而是通过单独的注射器系统15来引入,该注射器系统借助多个注射器喷嘴13可选地通过在模具轮廓壳之一中的通风喷嘴12或通过附加设置的开口被注射到空腔4中。在该实施方式中,首先将砂通过注射头6经由注入孔8注入空腔4中。接着,将注射器
系统15的注射喷嘴13通过相关联的孔插入空腔4中并且然后将粘合剂注射到被注入的砂中。
53.图9示出射芯模具1的另一实施方式,其中,下模具轮廓壳3和上模具轮廓壳2构造成,使得它们共同构成附加的开口16,通过该开口从射芯模具1的外侧提供至空腔4的入口。该开口16用于容纳侧向推移件14。在砂注入空腔4之前,该侧向推移件侧向地行进到空腔4中并且用于构成砂芯的底切轮廓。
54.在上述说明书、附图以及权利要求书中公开的本发明的特征不仅可以单独地而且可以以任意组合的方式对于实现本发明是重要的。
55.附图标记列表
[0056]1ꢀꢀꢀꢀ
射芯模具
[0057]2ꢀꢀꢀꢀ
上模具轮廓壳
[0058]3ꢀꢀꢀꢀ
下模具轮廓壳
[0059]4ꢀꢀꢀꢀ
几何形状上匹配的空腔
[0060]5ꢀꢀꢀꢀ
夹具
[0061]6ꢀꢀꢀꢀ
注射头
[0062]7ꢀꢀꢀꢀ
支承体
[0063]8ꢀꢀꢀꢀ
注入孔
[0064]9ꢀꢀꢀꢀ
硬化炉
[0065]
10
ꢀꢀꢀ
清洁装置
[0066]
11
ꢀꢀꢀ
用于粘合剂的注射器
[0067]
12
ꢀꢀꢀ
通风喷嘴
[0068]
13
ꢀꢀꢀ
注射器喷嘴
[0069]
14
ꢀꢀꢀ
侧向推移件
[0070]
15
ꢀꢀꢀ
注射器系统
[0071]
16
ꢀꢀꢀ
铸件
再多了解一些
本文用于企业家、创业者技术爱好者查询,结果仅供参考。