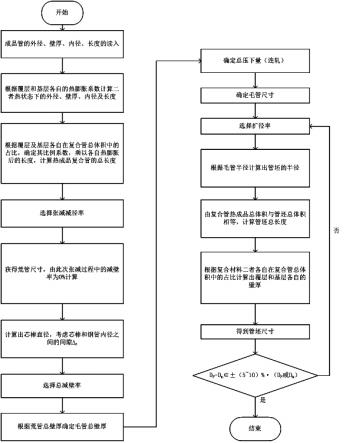
1.本发明涉及无缝钢管热轧领域,具体涉及一种双金属复合无缝钢管的热轧轧制规程优化方法,尤其涉及一种通过穿孔、热连轧、张力减径新型工艺生产的双金属复合无缝钢管,并采用按逆轧制道次方向计算出其无缝钢管管坯尺寸的轧制规程优化方法。
背景技术:
2.不锈钢/碳钢复合材料具有碳钢的耐腐蚀性以及不锈钢优异的强度和韧性的优点,因此,不锈钢/碳钢复合材料在石油化工、海洋工程和建筑领域具有广阔的应用前景。在无缝管行业,对于强腐蚀、高磨损、高工作压力环境下使用的流体管道,通常采用高品质的不锈钢或高合金含量的无缝钢管,这类管材由于大量添加合金元素,其价格是普通无缝钢管的几倍或几十倍。在这种背景下复合无缝钢管应运而生,复合无缝钢管已经在腐蚀性较强的石油、石化行业、核工业以及医药、食品加工等领域获得广泛认同,可通过内层复合耐磨金属,从而满足电厂粉煤、矿山矿粉和尾矿浆输送等高磨损工作环境的要求。
3.热轧钢管生产的轧制表是指计算轧管工艺过程中主要参数的表格,它是轧管工艺过程的基础。编制轧制表是以成品管的钢种、规格为依据,从车间现有的设备、工具和坯料规格出发, 合理分配各道次的变形量,计算出相应的毛管尺寸、坯料尺寸、工具的主要尺寸和轧机的主要调整参数等。轧制表是进行钢管生产和操作的技术指导规范,它在很大程度上决定整个机组的生产能力、钢管质量、工具寿命、能源及其他经济指标。编制后还应验算主要设备强度,测定验算各轧机上的节奏时间。如个别机组的节奏时间过长,或设备强度、能力不足,则应重新分配变形量,消除薄弱环节。由于轧制规程和轧件原始条件、设备条件、工艺条件和目标要求等因素有关,还和轧制过程中物理力学性能变化等因素直接相关,各种因素之间还存在相互作用和相互影响,可见轧制规程的制定的复杂性,所以,轧制生产早期主要是使用经验法和能耗曲线法等来制定轧制规程,这些传统的轧制规程制定方法由于简单有效,所以直到目前还大量使用在轧制生产中。但这种方法很依赖于人工经验,容易造成耗材多,对设备的运行状态和轧制状态缺乏充分的考虑。
4.因此,在如何保证外径、壁厚为目标的前提下,研究以负荷均衡分配为目标,实现对轧制规程进行优化设定。不仅能适用于新产品的开发,而且可以提高尺寸精度和内外表面质量,轧制设备寿命等。这有助于改变目前钢管企业在新产品开发中的瓶颈问题,提高企业的创新能力和核心竞争力。
技术实现要素:
5.鉴于此,本发明的目的在于,提供一种双金属复合无缝钢管的热轧轧制规程优化方法,旨在克服传统的轧制规程过于依赖人工经验,无法均衡分配负荷的缺陷。
6.为了达到上述发明目的,采取如下的技术方案:一种双金属复合无缝钢管的热轧轧制规程优化方法,包括以下步骤:根据成品复合无缝钢管中覆层与基层的尺寸参数并结合覆层及基层各自在成品
复合无缝钢管中的体积占比,获取覆层、基层在各自热膨胀系数下热成品复合无缝钢管在热状态下对应的尺寸参数;其中,所述覆层为不锈钢层,所述基层为碳钢层,且所述成品复合无缝钢管中覆层与基层的尺寸参数包括成品复合无缝钢管的外径与内径、不锈钢层的壁厚及长度、碳钢层的壁厚及长度;根据所述热成品复合无缝钢管在热状态下的尺寸参数,在张力减径过程中,设定减壁率为0%,并同时选择张减减径率,由此获得轧后荒管尺寸参数;其中,所述轧后荒管尺寸参数包括轧后荒管内、外径、轧后荒管壁厚及轧后荒管长度;基于获得的轧后荒管尺寸参数,结合并设定芯棒与荒管内径之间的间隙,确定出芯棒的直径;基于确定的芯棒直径同时选择芯棒穿孔过程中的总减壁率,得出穿孔毛管的尺寸参数;其中,所述穿孔毛管的尺寸参数包括穿孔毛管的外径、穿孔毛管的壁厚及穿孔毛管的长度;根据得出的穿孔毛管的尺寸参数,结合设定的扩径率,由此确定出管坯的半径,随后基于热成品复合无缝钢管的总体积与管坯总体积相等的条件以及根据覆层、基层各自在复合无缝钢管总体积中的占比,最终获得管坯的尺寸参数;其中,所述管坯的尺寸参数包括管坯的半径及直径、管坯的壁厚以及管坯的长度;将管坯直径与毛管外径作差,判断差值结果是否在管坯直径或毛管外径的
±
(5~10) %范围内,若满足则直接得出管坯尺寸;若不在指定范围内,则返回重新选定扩径率,重新确定管坯尺寸。
7.进一步的,所述覆层、基层在各自热膨胀系数下热成品复合无缝钢管在热状态下对应的尺寸参数及公式如下:
ꢀꢀꢀ
公式(1)
ꢀꢀꢀ
公式(2)
ꢀꢀꢀ
公式(3)公式(4)
ꢀꢀꢀꢀ
公式(5)
ꢀꢀꢀꢀ
公式(6)公式(7)其中,—热成品管外径;—成品管内径;—热成品管中不锈钢壁厚;—成品管中不锈钢壁厚;—热成品管中碳钢壁厚;—成品管中碳钢壁厚;—热成品管内径;—热成品管壁厚;—热成品管长度;—热成品管中不锈钢长度;—热成品
管中碳钢长度;—成品管长度;—不锈钢的热膨胀系数;—碳钢的热膨胀系数;—终轧的温度;—覆层的总体积;—基层的总体积;—成品管的总体积。
8.更进一步的,所述不锈钢的热膨胀系数=18.97,碳钢的热膨胀系数=14.9,终轧的温度为700-900℃。
9.优选地,在张力减径过程中,选择张减减径率,并依据以下的公式,获得轧后荒管的外径;
ꢀꢀꢀ
公式(8)其中,—张减减径率,选择24%~60%,—轧后荒管外径,—减径后外径。
10.优选地,设定芯棒与荒管内径之间的间隙为1-3mm。
11.较佳地,选择芯棒穿孔过程中的总减壁率,并依据以下的公式,得出穿孔毛管的壁厚;公式(9)其中,—总减壁率,选择30%~70%,—穿孔毛管壁厚,—轧后荒管壁厚。
12.更佳地,设定的扩径率为110%~115%。
13.优选地,将管坯直径与毛管外径作差,判断差值结果是否在管坯直径或毛管外径的
±
(5~10) %范围内,依据如下的公式:
ꢀꢀꢀ
公式(10)。
14.本发明的有益效果:本发明公开了一种通过穿孔、热连轧、张力减径新型工艺生产的双金属复合无缝钢管,采用按逆轧制道次方向最终获取其无缝钢管管坯尺寸的轧制规程制定方法。通过本发明公开的轧制规程的优化方法,容易获取得到双金属复合无缝钢管的覆层以及基层各自的壁厚进而合理地分配各轧机的变形量,使得穿孔机、轧管机和减径机负担平衡。
附图说明
15.为了更清楚地说明本发明实施例或现有技术中的技术方案,下面将对实施例或现有技术描述中所需要使用的附图作简单地介绍,显而易见地,下面描述中的附图仅仅是本发明的一些实施例,对于本领域普通技术人员来讲,在不付出创造性劳动性的前提下,还可以根据这些附图获得其他的附图。
16.图1为本发明一种双金属复合无缝钢管的热轧轧制规程优化方法的流程图;图2为不同温度下金属材料的线膨胀系数一览表。
具体实施方式
17.下面将结合本发明实施例中的附图,对本发明实施例中的技术方案进行清楚、完整地描述,显然,所描述的实施例仅仅是本发明一部分实施例,而不是全部的实施例。基于本发明中的实施例,本领域普通技术人员在没有做出创造性劳动前提下所获得的所有其他实施例,都属于本发明保护的范围。
18.目前制造复合无缝钢管主要的工艺方法有机械复合法和冶金复合法,机械复合法包括热轧复合方法、热挤压复合法、铸造复合方法、爆炸焊接复合方法、组合式双金属复合无缝钢管生产方法、激光包覆法等。
19.本发明针对碳钢20钢与不锈钢316l的复合材料,采用穿孔、热连轧、张力减径的方式来获得双金属复合无缝钢管,并对生产的复合无缝钢管制定它的轧制规程方法。
20.需要说明的是:编制轧制表之前,首先应该了解生产和设备情况,例如轧机的结构形式、强度和刚度、工具形状和尺寸、管坯尺寸规格、孔型系列以及所轧材料的加工性能等。编制后通过实践不断修正和完成,轧制表的编制一般应遵守下述原则:(1)合理地分配各轧机的变形量,使得穿孔机、轧管机和减径机负担平衡;(2)尽量用最少管坯尺寸种类和工具完成轧制计划;(3)合理选择各轧机的变形参数,保证产品质量和生产力。斜轧穿孔机的延伸系数在1.3~5.7范围内,压缩带处的压缩率为10%~17%,顶头前压缩率在4%~9%之间,合金钢取小值;连续轧管机的延伸系数一般为4~10,斜轧轧管机的延伸系数一般不超过3,顶管机的延伸系数可达15,在一般定径机上,每架直径压缩率不大于3. 5%,斜轧定径机的直径压缩量取1 ~ 2mm;(4)合理地选择管坯尺寸,管坯尺寸应根据毛管外径来选择,圆管坯直径应接近于毛管外径,一般管坯直径与毛管外径之差在
±
(5 ~10) %范围内;(5)了解制管材料的特性以及工艺过程和变形制度对管材力学性能、物理性能和工艺性能的影响,以便获得高性能的产品。
21.另外,编制轧制表的方法大致有两种:一种是按逆轧制道次方向进行编制,即由定径向前推算到坯料尺寸,此法主要适用于新设计车间的典型产品;另一种是从轧管机出发向两头工序推算,此法主要适用于已投产车间的新产品设计,因为投产车间总有一定规格数量的坯料、工具和轧管机孔型系统等,所以设计新产品应首先考虑已有工具和坯料规格,以及轧管机孔型系统是否能满足要求,以尽量减少工具和坯料储备。
22.不管哪种计算方法,思考方法与计算内容是相同的。本发明采用第一种方法按逆轧制道次方向推理得出其无缝钢管管坯的尺寸。具体包括如下的步骤:根据成品复合无缝钢管中覆层与基层的尺寸参数并结合覆层及基层各自在成品复合无缝钢管中的体积占比,获取覆层、基层在各自热膨胀系数下热成品复合无缝钢管在热状态下对应的尺寸参数;其中,所述覆层为不锈钢层,所述基层为碳钢层,且所述成品复合无缝钢管中覆层与基层的尺寸参数包括成品复合无缝钢的外径与内径、不锈钢层的壁厚及长度、碳钢层的壁厚及长度;根据所述热成品复合无缝钢管在热状态下的尺寸参数,在张力减径过程中,设定减壁率为0%,并同时选择张减减径率,由此获得轧后荒管尺寸参数;其中,所述轧后荒管尺寸参数包括轧后荒管内、外径、轧后荒管壁厚及轧后荒管长度;
基于获得的轧后荒管尺寸参数,结合并设定芯棒与荒管内径之间的间隙,确定出芯棒的直径;基于确定的芯棒直径同时选择芯棒穿孔过程中的总减壁率,得出穿孔毛管的尺寸参数;其中,所述穿孔毛管的尺寸参数包括穿孔毛管的外径、穿孔毛管的壁厚及穿孔毛管的长度;根据得出的穿孔毛管的尺寸参数,结合设定的扩径率,由此确定出管坯的半径,随后基于热成品复合无缝钢管的总体积与管坯总体积相等的条件以及根据覆层、基层各自在复合无缝钢管总体积中的占比,最终获得管坯的尺寸参数;其中,所述管坯的尺寸参数包括管坯的半径及直径、管坯的壁厚以及管坯的长度;将管坯直径与毛管外径作差,判断差值结果是否在管坯直径或毛管外径的
±
(5~10) %范围内,若满足则直接得出管坯尺寸;若不在指定范围内,则返回重新选定扩径率,重新确定管坯尺寸。
23.下面将结合具体的实施数据及图1的流程对本发明的一种双金属复合无缝钢管的热轧轧制规程优化方法进行详细的说明。
24.已知给定成品管直径为159mm,不锈钢壁厚 为3mm,碳钢壁厚 =9mm,成品管内径 =135mm,成品管长度 为10m,给出按逆轧制道次方向计算轧制规程的具体制定方法,详细计算过程如下: 热成品管的尺寸计算
ꢀꢀꢀ
公式(1)根据图2所示内容,选取温度在700℃时,不锈钢的热膨胀系数和碳钢的热膨胀系数,并将选取的数据带入公式(1),得到以下数据:数据:
ꢀꢀꢀꢀꢀꢀꢀꢀꢀꢀꢀꢀꢀꢀꢀꢀ
公式(2)公式(2)
ꢀꢀꢀꢀꢀꢀꢀꢀꢀꢀꢀꢀꢀꢀꢀꢀꢀꢀꢀꢀꢀꢀꢀꢀꢀꢀꢀꢀꢀꢀ
公式(3)公式(3)
ꢀꢀꢀꢀꢀꢀꢀꢀꢀꢀꢀꢀꢀꢀꢀꢀꢀꢀꢀꢀꢀꢀꢀꢀꢀꢀꢀꢀꢀꢀꢀꢀꢀꢀꢀꢀꢀꢀꢀ
公式(4)公式(4)
ꢀꢀꢀꢀꢀꢀꢀꢀꢀꢀꢀꢀꢀꢀꢀꢀꢀꢀꢀꢀꢀꢀꢀꢀꢀꢀꢀꢀꢀꢀꢀꢀꢀ
公式(5)公式(5)
ꢀꢀꢀꢀꢀꢀꢀꢀꢀꢀꢀꢀꢀꢀꢀꢀꢀꢀꢀꢀꢀꢀꢀꢀꢀꢀꢀꢀꢀꢀꢀꢀꢀꢀꢀꢀ
公式(6)公式(6)
ꢀꢀꢀꢀꢀꢀꢀꢀꢀꢀꢀꢀꢀꢀꢀꢀꢀꢀꢀꢀꢀ
公式(7)
ꢀ
其中,—热成品管外径;—成品管内径;—热成品管中不锈钢壁厚;—成品管中不锈钢壁厚;—热成品管中碳钢壁厚;—成品管中碳钢壁厚;—热成品管内径;—热成品管壁厚;—热成品管长度;—热成品管中不锈钢长度;—热成品管中碳钢长度;—成品管长度;—不锈钢的热膨胀系数;—碳钢的热膨胀系数;—终轧的温度;—覆层的总体积;—基层的总体积;—成品管的总体积。
25.减径机钢管尺寸计算减径机钢管尺寸计算减径机钢管尺寸计算减径机钢管尺寸计算
ꢀꢀꢀꢀ
公式(8)设定 ,得出 其中, —减径后外径; —减径后不锈钢壁厚; —减径后碳钢壁厚; —张减减径率, —轧后荒管外径。
26.连轧管机钢管尺寸计算此张减过程中减壁率为0%此张减过程中减壁率为0%此张减过程中减壁率为0%此张减过程中减壁率为0%(通过体积不变计算)其中, —轧后荒管外径; —轧后荒管中不锈钢壁厚; —轧后荒管中碳钢壁厚; —轧后荒管壁厚; —轧后荒管内径; —轧后荒管长度(通过体积不变计算); —芯棒直径; —芯棒和荒管内径之间的间隙,取2.35mm
ꢀ
穿孔机钢管尺寸计算 ,设定
ꢀꢀꢀꢀ
公式(9)公式(9)公式(9)公式(9)(通过体积不变计算)其中, —总减壁率; —穿孔毛管壁厚; —穿孔毛管外径; —穿孔毛管长度(通过体积不变原理计算),而且可根据穿孔毛管壁厚与轧后荒管壁厚确定出总压下量。
27.管坯尺寸计算管坯尺寸计算管坯尺寸计算管坯尺寸计算即: 得出 根据覆层、基层各自在复合无缝钢管总体积中的占比,即即同时:
ꢀꢀꢀꢀ
其中, —穿孔毛管半径; —管坯半径; —热成品管的总体积; —管坯的总体积; —管坯长度; —覆层的总体积; —基层的总体积; —管坯中不锈钢壁厚; —管坯中碳钢壁厚。
28.将管坯直径与毛管外径作差,判断差值结果是否在管坯直径或毛管外径的
±
(5~10) %范围内,若满足则直接得出管坯尺寸;若不在指定范围内,则返回重新选定扩径率,重新确定管坯尺寸。
29.ꢀꢀ
公式(10)
其中,—管坯直径; —穿孔毛管外径;其中,; ; ;; 。
30.通过上述逆轧制道次方向公开的轧制规程的优化方法,容易获取得到双金属复合无缝钢管的覆层以及基层各自的壁厚进而合理地分配各轧机的变形量,使得穿孔机、轧管机和减径机负担平衡。
31.最后应说明的是:以上所述仅为本发明的优选实施例而已,并不用于限制本发明,尽管参照前述实施例对本发明进行了详细的说明,对于本领域的技术人员来说,其依然可以对前述各实施例所记载的技术方案进行修改,或者对其中部分技术特征进行等同替换,凡在本发明的精神和原则之内,所作的任何修改、等同替换、改进等,均应包含在本发明的保护范围之内。
再多了解一些
本文用于企业家、创业者技术爱好者查询,结果仅供参考。