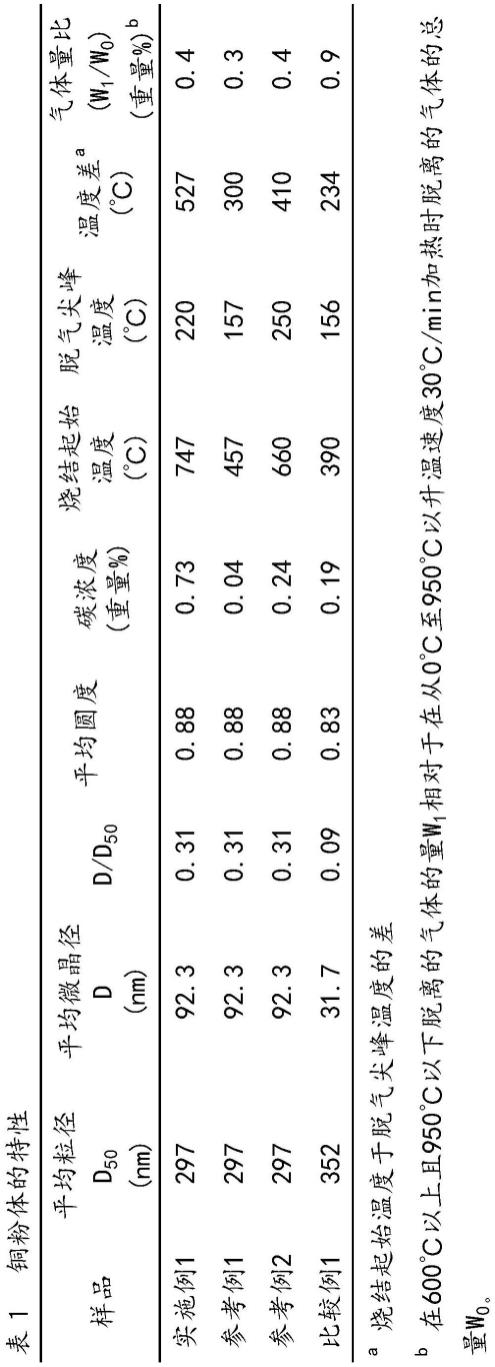
1.本发明的实施方式之一涉及铜粉体和铜粉体的制造方法。
背景技术:
2.作为微细金属粒子集合体的金属粉体或包含金属粉体的糊剂,已作为用于制造低温共烧陶瓷(ltcc)基板的布线或端子、多层陶瓷电容器(mlcc)的内部电极或外部电极等各种电子零件的原材料而被广泛利用。尤其是铜粉体,因铜的高导电性而能够使mlcc的内部电极薄膜化或使外部电极小型化,能够显著地改善频率特性,因此,有望作为替代以往大量使用的镍粉体或银粉体的材料(参见专利文献1至5)。
3.(现有技术文献)
4.(专利文献)
5.专利文献1:日本特开2015-36439号公报
6.专利文献2:国际公开2015/137015号
7.专利文献3:日本特开2018-076597号公报
8.专利文献4:日本特开2016-108649号公报
9.专利文献5:日本特开2004-211108号公报
技术实现要素:
10.发明所要解决的问题
11.本发明的实施方式之一以提供铜粉体及其制造方法作为课题之一。举例而言,本发明的实施方式之一以提供具有高烧结起始温度并且在烧结时的脱气行为受控的铜粉体及其制造方法作为课题之一。
12.解决问题所采用的措施
13.根据本发明的实施方式之一为铜粉体。此铜粉体的平均粒径d
50
为100nm以上且500nm以下,烧结起始温度为450℃以上,脱气尖峰温度为150℃以上且300℃以下。
14.根据本发明的实施方式之一为铜粉体的制造方法。此制造方法包括:通过金属铜与含氯气体反应生成氯化铜气体,通过氯化铜气体与还原性气体的反应生成包含铜的一次粉末,以及利用含氮杂芳族化合物处理一次粉末。
15.发明的效果
16.根据本发明的实施方式之一的铜粉体不仅表现出高的烧结起始温度,而且在烧结时脱离的气体很少。因此,本铜粉体能够通过烧结提供具有明确定义的结构的铜膜,并且能够有助于mlcc等各种功能性元件的薄膜化或小型化,以及电子零件的布线或端子的微细化等。
附图说明
17.图1是根据本发明的实施方式之一的用于制造铜粉体的流程。
具体实施方式
18.以下,参照附图等对本发明的各实施方式逐一进行说明。本发明在不脱离其要旨的范围内可以以各种方式实施,不应解释为限定于以下例示的实施方式或实施例的记载内容。虽然为了更清楚地描述,与实际实施例相比,附图可以示意性地表示各部分的宽度、厚度、形状等,但仅是示例,并不限制对本发明的解释。
19.1.铜粉体的制造方法
20.本发明的实施方式之一是含有多个铜粒子的铜粉体。使用图1所示的流程来说明制造铜粉体的方法的示例。于此,虽然对利用所谓气相生长法的制造铜粉体的方法进行说明,但是铜粉体的制造方法不限于气相生长法,也可以利用湿式法或等离子体法等来制造铜粉体。
21.1-1.氯化铜的生成
22.首先,通过使金属铜与氯气反应生成氯化铜气体。此方法不仅在可以使用比氯化铜便宜的金属铜这点上有成本上的优势,还可以使氯化铜气体的供给量稳定化。作为具体的氯化铜气体的制造方法,通过使金属铜在其熔点以下(例如800℃以上且1000℃以下)与氯气反应使氯化铜气体生成。氯气可以是实质上仅含有氯的气体,也可以是含有稀释用惰性气体的氯和稀释用惰性气体的混合气体。通过使用混合气体,能够容易且精密地控制与金属铜反应的氯的量。
23.1-2.氯化铜的还原
24.使所生成的氯化铜气体与还原性气体反应,以生成铜粉体。作为还原性气体,可以使用例如氢,肼,氨,甲烷等。相对于氯化铜气体,还原性气体可以以化学计量以上的量来使用。例如,在氯化铜气体全部都由一价铜的氯化物组成并且还原性气体为氢气的情况下,还原性气体的导入量可以为相对于氯化铜气体的50摩尔%以上且10000摩尔%以下、500摩尔%以上且10000摩尔%以下、或1000摩尔%以上且10000摩尔%以下。通过此反应,氯化铜被还原为铜,铜元素生长为铜粒子,成为作为集合体的铜粉体。以下将通过此还原反应生成的铜粉体称为一次粉体。
25.1-3.氯成分的降低
26.对于利用上述制造方法获得的一次粉体,可以通过用碱的水溶液或悬浮液处理来进行氯成分的降低。
27.1-4.氧成分的降低
28.对于利用上述制造方法获得的一次粉体,为了氧成分的降低,可以在使用含有抗坏血酸,肼,柠檬酸等的溶液或悬浮液作为清洗液处理之后,以水清洗并进行过滤和干燥。
29.1-5.表面处理
30.对于利用上述制造方法获得的一次粉体,可以进行预定的表面处理。作为表面处理剂,可以使用苯并三唑及其衍生物、三唑及其衍生物、噻唑及其衍生物、苯并噻唑及其衍生物、咪唑及其衍生物、以及苯并咪唑及其衍生物等含氮杂芳香族化合物等。
31.1-6.其它处理
32.对于利用上述制造方法获得的铜粉体,可以进行干燥、分级、碎解、过筛等处理。分级既可以为干式分级,也可以为湿式分级,在干式分级中,可以采用气流分级、重力场分级、惯性力场分级、离心力场分级等任意方式。在湿法分级中也同样可以采用重力场分级和离
心力场分级等方式。碎解可以使用例如喷射磨机进行。过筛可以通过振动具有所期望的筛目尺寸的筛子并使铜粉体通过来进行。通过进行分级、碎解和过筛处理,能够使铜粉体的粒径分布更小。
33.2.铜粉体的特性
34.2-1.粒径
35.通过上述工序制造的铜粉体,由于利用气相生长法生成一次粉末体,而具有小的平均粒径,并且具有窄的分布。于此,铜粉体的平均粒径是指在铜粉体的体积基准的粒径直方图中累积频率为50%时的粒径。所谓铜粉体的体积基准的粒径是以铜粉体所包含的各粒子的体积加权得出的粒径。如下式所示,通过将具有粒径di(i为1至k的自然数,i≤k)的粒子的总体积除以粉体所包含的所有粒子的总体积,获得具有粒径di的粒子的频率f。累积此频率f成为50%时的粒径为中值直径d
50
。于此,平均粒径也表示为d
50
。
36.(数1)
[0037][0038]
于此,vi为具有粒径di的铜粒子的体积,ni为具有粒径di的铜粒子的数量。
[0039]
以下说明体积vi和粒径di的计算方法。在以光学显微镜或电子显微镜观察铜粉体而获得的显微照片中,目视观察确认了轮廓的铜粒子(例如100个至10000个,典型地500个)。接着,根据目视观察到的铜粒子的表面积si,作为具有与该表面积相同面积的假想圆的直径算出该铜粒子的粒径,具体而言,利用下式算出粒径di。
[0040]
si=π(di)2[0041]
接着,根据算出的粒径di,利用下式算出铜粒子的体积vi。
[0042]
vi=4π(di/2)3/3
[0043]
根据本发明的实施方式之一的铜粉体的平均粒径d
50
,具体而言为100nm以上且500nm以下,100nm以上且300nm以上,或100nm以上且200nm以下。由于通过烧结满足此范围的本铜粉体,能够提供具有小厚度的金属膜,因此可以有助于例如mlcc的电极的薄膜化、其它电子零件的布线和端子的微细化。此外,由于可以抑制铜粒子的聚集,因此会使铜粉体易于操作。铜粉体的平均粒径d
50
可以通过适当地设定金属铜的氯化温度,氯气的流量,氯气与稀释气体的比率,氯化铜的还原温度,氯化铜气体与还原气体的流量的比率等条件来控制在上述范围内。
[0044]
2-2.平均微晶径
[0045]
根据本发明的实施方式之一的铜粉体的特征之一为:由于通过气相生长法生成一次粉末,平均微晶径d大。于此,所述微晶是表示可视为单晶的区域的长度的指标。每个铜粒子具有一个或多个微晶。平均微晶径d可以通过将利用对铜粉体x射线衍射的测量获得的各种参数(所使用的x射线的波长λ、衍射x射线的广度的半值宽度β、布拉格角θ)代入以下所示的舍勒公式(式1)计算而获得。于此,k是舍勒常数。例如,可以使用x射线衍射装置获得铜结晶的(111)面、(200)面和(220)面的衍射尖峰的半值宽度,根据下式1算出平均微晶径d。平均微晶径d是反映出单个铜粒子的微晶尺寸的参数。
[0046]
d=(k
×
λ)/(β
×
cosθ)
……
式1
[0047]
基于小的平均粒径d
50
和大的平均微晶径d,根据本发明的实施方式之一的铜粉体
的平均微晶径d相对于平均粒径d
50
的比d/d
50
可以为0.10以上且0.50以下。基于如此大的d/d
50
,本铜粉体表现出较高的烧结起始温度。作为铜粉体的制造方法之一,可以举出将氯化铜、氢氧化铜、硫酸铜或硝酸铜等铜盐的溶液或悬浮液用还原剂处理的方法(湿式法)。然而,湿式法难以获得如此大的d/d
50
。作为其理由可以列举:在气相生长法中铜粒子会在高温下生长,可以通过使用氮气等将生长的铜粒子急速冷却来停止粒子的生长。
[0048]
2-3.平均圆度
[0049]
铜粉体的铜粒子,其形状接近正球形。更具体而言,铜粉体的平均圆度即铜粒子的圆度c的平均为例如0.85以上且0.95以下、或0.87以上且0.95以下。平均圆度是表示铜粉体中所含的每个粒子的形状的参数之一,是分析以显微镜观察粉末而获得的影像,针对多个(例如500个)粒子求出圆度c并对其进行平均而获得的值。圆度c由下式表示。于此,a是在显微镜图像中的每个粒子的投影面的周长,b是与其投影面的面积相同的面积的圆的周长。由于高平均圆度,铜粉体表现出高填充性。因此,通过使用本铜粉体,能够形成高密度且低电阻的电极和布线。
[0050]
(数2)
[0051][0052]
2-4.脱气行为
[0053]
根据本发明的实施方式之一的铜粉体在烧结时的脱气行为是高度受控的,其结果,如后所述能够通过烧结来提供明确定义的结构的铜膜。对于评价脱气行为的方法并无限定,但可以使用称为流量法或电导法的方法。在此方法中,在减压的腔室内在预定温度范围中以固定的升温速度加热铜粉体,基于腔室内的压力变化来估算脱离气体的量。例如,使用升温脱离气体分析(tds)装置,在减压下在预定温度范围(例如60℃至950℃)内以固定的升温速度(例如30℃/min)加热载置有铜粉体的载台,监测压力变化。脱离的气体可以用质量分析装置来分析,从而可以鉴定脱离的气体以求出其组成比。作为脱离的气体,可举出水、氢、二氧化碳、一氧化碳、氮、氰化氢等。此外,由于氮和一氧化碳分子量相同,因此它们是作为混合气体而被评价的。
[0054]
本发明的实施方式之一的铜粉体在相对较低的温度下表现出脱气尖峰。于此,脱气尖峰温度是指当以固定的升温速度加热铜粉体时,在脱离的气体的量相对于温度或加热时间的图表中观察到的尖峰的温度。具体而言,在以30℃/min的升温速度下,自60℃加热至950℃时,本铜粉体的脱气尖峰会在150℃以上且300℃以下或150℃以上且260℃以下观察到。进而,如果以通过在60℃以上且950℃以下的温度范围内加热而脱离的气体的总量(w0)为基准,则在600℃以上且950℃以下脱离的气体的量(w1)的比(w1/w0)为0.6重量%以下,优选为0.4重量%以下,更优选为0.3重量%以下。w1/w0也可以为0.1重量%以上。这些特性意味着从本发明的实施方式之一的铜粉体中于低温(150以上且300℃以下)下大部分的气体会脱离,并且在烧结进行的温度(例如600℃以上)下脱气会大幅受到抑制。
[0055]
2-5.碳浓度和烧结起始温度
[0056]
如上所述,根据本发明的实施方式之一的铜粉体是通过对利用气相生长法获得的一次粉体进行表面稳定化处理来制造的。因此,铜粒子在其表面上含有源自表面处理剂的微量的碳。铜粉体中的碳浓度为例如0.04重量%以上且1.00重量%以下、0.04重量%以上
且0.90重量%以下、或0.04重量%以上且0.80重量%以下。
[0057]
铜粉体中的碳浓度可以通过例如利用燃烧/红外线吸收法来测量,在此情况下,可以遵循jis h1617,jis z2615和astm e1941的方法来测量。具体而言,通过使铜粉体在燃烧炉中在氧气气流下燃烧,由铜粉体中的碳生成二氧化碳。利用氧气将生成的二氧化碳导入红外线分析仪中,以检测器测量其吸收,从而确定二氧化碳的浓度。根据二氧化碳的浓度定量测定铜粉体中的碳浓度。
[0058]
如实施例所示,在本实施方式的铜粉体中,由于在铜粒子的表面中含有微量的碳,因此可以大幅提升铜粉体的烧结起始温度。此外,通过控制残留的碳浓度能够控制烧结起始温度。具体而言,可以提供具有450℃以上或740℃以上的烧结起始温度的铜粉体。此外,对于烧结起始温度的评价方法并无限制,可以例如利用热机械分析测量包含铜粉体的团块的收缩率,采用收缩率成为固定值(例如5%)时的温度。
[0059]
2-6.杂质浓度
[0060]
如上所述,本发明的实施方式之一的铜粉体的制造方法包含一次粒子的表面稳定化处理,并且还可以包含氯成分或氧成分的降低处理。在此制造方法中,不需要包含例如会成为铝、钛、锆和铈等过渡金属或硅等的杂质的混入的原因的工艺。因此,铜粉体实质上不包含可能会对通过烧结而形成的铜膜的电特性造成不利影响的杂质。上述的元素的浓度,举例而言,以在利用电感耦合等离子体(icp)发射光谱等的元素分析测量中未达检测极限值为好。于此,本发明中的“未达检测极限值”是指铝未达1ppm、硅未达1ppm、钛未达10ppm、锆未达1ppm。
[0061]
根据本实施方式的铜粉体的高烧结起始温度在将铜粉体用作mlcc等电子零件的电极、其它布线和端子的材料的情况下,大大有助于电子零件的可靠性的提升和良率的改善。这种特征在用作mlcc的电极材料时特别显著。其理由如下。随着mlcc的小型化要求电极的薄膜化,为此将铜粉体的平均粒径减小是有效的方法之一。然而,如果粉体的平均粒径变小,则比表面积增加,从而烧结起始温度降低。mlcc是通过在交替涂布包含电介质的分散液和包含铜粉体的分散液之后,加热使铜粉体和电介质烧结来制造的;但是铜粉体的烧结起始温度的降低会导致铜粉体和电介质的烧结起始温度的差的增大,其结果,会导致铜粉体和电介质的烧结开始时间的大差异。因此,在电介质的烧结起始之前铜粉体会因烧结而收缩,因铜粉体烧结而会形成的电极和电介质膜之间产生间隙,由于此间隙,在电极和电介质膜之间发生剥离。另一方面,根据本发明的实施方式之一的铜粉体由于即使具有小的平均粒径d
50
,仍然具有高的烧结起始温度,因此与电介质的烧结起始温度的差很小,结果,可以抑制烧结时的电极的剥离。因此,通过使用本铜粉体,能够以高良率提供高可靠性的mlcc。
[0062]
此外,根据本实施方式的铜粉体,如上所述,会在相对较低的温度下出现脱气尖峰,并且在600℃以上且950℃以下脱离的气体的量相对较少。因此,本铜粉体的脱气尖峰会在低于烧结起始温度的温度下观察到。这意味着在开始烧结而形成铜膜的过程开始之前大部分的气体会脱离,而在烧结起始温度附近或者烧结之后几乎不会发生脱气。因此,可以防止由脱气引起的空隙的产生或变形,在烧结前后的形状变化很小。因此,可以提供具有受控结构的铜膜,即具有明确定义的结构的铜膜。
[0063]
作为提升铜粉体的烧结起始温度的方法,已知例如,将包含硅和碳的已熔融的铜通过雾化法来粉体化的方法,在铜粒子的表面上形成含铝、钛、锆、铈、锡或硅的被膜的方
法,以及在铜粒子的表面上形成氧化硅的被膜的方法等。然而,由于这些元素是绝缘性或者与铜相比电阻高,因此对通过烧结铜粉体获得的铜膜的电特性赋予不良影响。并且,如果以在铜粒子内部或表面上相对大量包含这些元素的方式构成铜粉体,则烧结时有大量的气体脱离,因此难以防止由脱气所引起的空隙的产生或铜膜的变形。
[0064]
相对于此,根据本发明的实施方式之一的铜粉体虽然包含源自表面处理剂的微量碳,但上述的过渡金属或硅的含量可以忽略不计。因此,通过烧结而获得的铜膜表现高导电性。这意味着本铜粉体可以作为对于mlcc等各种功能性元件的薄膜化或小型化、电子零件的布线或端子的微细化等有效的材料而得到利用。
[0065]
【实施例】
[0066]
以下说明根据本发明的实施方式的实施例。在本实施例中,依循于上述方法制造铜粉体,描述评价其特性的结果。
[0067]
1.实施例1
[0068]
在氯化炉中设置球状金属铜,将氯化炉加热到900℃。在此温度下,从与氯化炉的上部和下部连接的氯气导入管(以下分别称为上部导入管和下部导入管)供应氯气和氮气的混合气体。通过上部导入管导入的混合气体中的氯气与氮气的体积比(v
cl2
:v
n2
)为29:61,通过下部导入管导入的混合气体中的氯气与氮气的体积比(v
cl2
:v
n2
)为2:98。通过上部导入管导入的混合气体和通过下部导入管导入的混合气体的体积比(vu:v
l
)为1:0.17。
[0069]
将通过金属铜与氯反应产生的氯化铜气体导入到已加热至1150℃的还原炉中,以氢气和氮气相对于氯化铜气体分别成为4600摩尔%和24600摩尔%的方式将氢气和氮气导入还原炉。将通过氯化铜气体与氢气的反应获得的铜粉体用氮气冷却,获得铜的一次粉末。
[0070]
接着,对所获的一次粉末进行氯/氧成分的降低处理。具体而言,对一次粉末,使用40重量%的氢氧化钠水溶液和10重量%的抗坏血酸水溶液进行氧成分降低处理。
[0071]
然后,进行表面稳定化处理。具体而言,对已以抗坏血酸水溶液处理过的一次粉体,在室温下加入包含1.0重量%的苯并三唑作为表面处理剂的水溶液,搅拌所获得的混合物30分钟。搅拌结束后,静置混合物,除去上清液并干燥,得到实施例1的铜粉体。
[0072]
2.参考例1
[0073]
除了将在对铜粉体进行表面处理时的苯并三唑水溶液的浓度设定为0.33重量%以外,以与实施例1相同的条件制备铜粉体。
[0074]
3.参考例2
[0075]
除了将在对铜粉体进行表面处理时的苯并三唑水溶液的浓度设定为0.05重量%以外,以与实施例1相同的条件制备铜粉体。
[0076]
4.比较例
[0077]
比较例1的铜粉体是利用专利文献3所公开的湿式还原法来制备的。
[0078]
5.评价
[0079]
测量实施例1、参考例1和2以及比较例1的铜粉体的平均粒径d
50
,平均微晶径d,平均圆度,烧结起始温度,碳浓度以及铝、硅、钛和锆的浓度。并且,应用流量法来评价脱气行为。
[0080]
平均粒径d
50
如下测量。使用扫描型电子显微镜(sem:株式会社日立高新技术制,su5000,下同),并使用影像分析软件(株式会社mountec制macview 4.0)分析在倍率15000
倍下的铜粉体的sem像的一视野中存在的500个铜粒子的像。通过此分析,由所获得的各个铜粒子的粒径算出平均粒径d
50
。
[0081]
平均微晶径d,使用x射线衍射装置(spectris株式会社制,x'pertpro),由以加速电压45kv、放电电流40ma的条件产生的cukα射线所得到的铜结晶的(111)面、(200)面、(220)面的衍射尖峰的半值宽度和舍勒公式来算出。
[0082]
平均圆度如下测量。使用sem并使用影像分析软件(株式会社mounttec制macview 4.0)分析在倍率15000倍下的sem像的一视野中存在的约500个铜粒子,针对约500个铜粒子的求出圆度c,算出其平均值,也就是平均圆度。
[0083]
脱气行为使用升温脱离气体分析装置(电子科学社制,tds-1200)来评价。具体而言,在设置于升温脱离气体分析装置的腔室内的石英玻璃上配置铜粉体(0.6mg)。在使用涡轮分子泵将腔室内减压至2
×
10-7
pa之后,从室温加热至950℃。加热时的升温温度为30℃/min。使用真空计监测加热中的腔室内的压力,同时使用质量分析装置分析所排出的气体。基于腔室内的压力变化估算气体的脱离量。此外,气体自铜粉体的脱离量的定量分析,是通过在相同条件下在没有铜粉体的情况下将腔室加热而测量的气体的脱离量作为对照并扣除此来进行。并且,使用质量分析装置算出脱离气体的组成。
[0084]
烧结起始温度利用以下方法来决定。将铜粉体填充在直径为5mm,高度约40mm的圆筒状筒体中。从箱体的上部压入冲头,以0.87吨/cm2加压10秒钟,将铜粉体成型为高度约5mm的圆柱状。将此形成体以长轴为铅垂方向的方式配置,在沿长轴方向施加98.0mn的负荷的同时,用升温炉加热。加热是在包含2体积%的氢气的氮气的气流下(流速为300ml/min)以5℃/min的升温速度从室温进行至1000℃。加热中,监视成形体的高度的变化(膨胀/收缩),得到了热机械分析曲线。基于热机械分析曲线,将形成体的高度的变化(收缩)开始且其收缩率达到5%时的温度采用作为烧结起始温度。
[0085]
碳浓度的测量使用碳/硫分析装置(堀场制作所社制,emia-920v2)利用燃烧/红外线吸收法进行。
[0086]
使用sii nano technology株式会社制的icp原子发射光谱分析装置(sps3100)测量铝、硅、钛和锆的浓度。具体而言,将约1.0g的铜粉体加入到超纯水(30ml)、硝酸(10ml)以及盐酸(10ml)的混合液中,一边使用加热板加热一边溶解。在将所获得的溶液冷却至室温之后,加入纯水以总量作成100ml,使用此进行icp原子发射光谱分析。使用发光波长396.15nm、251.61nm、334.94nm、339.20nm分别评价铝、硅、钛和锆的浓度。
[0087]
评价结果总结在表1中。实施例1的铜粉体是利用气相生长法来制造,因此平均粒径d
50
小,平均微晶径d大。其结果,提供大的d/d
50
。此结果与利用湿式法制造的比较例1的铜粉体的结果形成对照。此外,与比较例1相比,实施例1的铜粉体的平均圆度很高。
[0088]
如表1所示,确认到实施例1及参考例1和2的铜粉体以0.04重量%以上且1.00重量%以下的浓度包含碳。如比较实施例1、参考例1和参考例2,可知碳浓度随着包含表面处理剂的水溶液的浓度增大而增大。这表示碳浓度可以通过包含表面处理剂的溶液或悬浮液的浓度来控制。
[0089]
由实施例1以及参考例1和2的结果可知,随着碳浓度的增大,烧结起始温度增大。尤其应该注意的是,即使是碳浓度仅为0.04重量%的参考例1的铜粉体,也显示出450℃以上的高起始温度这一点。与此相比,可知碳浓度为0.19重量%的比较例1的铜粉体即使碳浓
度比参考例1还高,但烧结起始温度较低,未达400℃。此外,实施例1、参考例1和2以及比较例1的铜粉体的铝、硅、钛和锆的浓度均未达检测极限值。这可以认为,烧结起始温度并非仅单纯取决于碳浓度,平均微晶径d相对于平均粒径d
50
的比(d/d
50
)的影响较大,而d/d
50
为0.10以上一事也有助于提高烧结起始温度。这可能是因为d/d
50
越大,以结晶状态存在的铜的比例越高。
[0090]
可知实施例1的铜粉体不仅在烧结起始温度以下表现出脱气尖峰温度,而且它们之间的温度差存在有300℃以上(表1)。这表明,在烧结起始之前,脱气已经几乎结束。因此可以认为,在烧结进行而形成膜的过程中不会有大量的气体脱离,通过使用实施例1至3的铜粉体能够抑制铜膜中的空隙的形成或铜薄膜的变形。相对于此,可知尽管比较例1的铜粉体的脱气尖峰温度低于烧结起始温度,但是其差异小到240℃左右。这表明,在使用比较例1的铜粉体的情况下,即使在烧结进行而形成膜的过程中也会有气体脱离,在所形成的铜膜中产生空隙或发生铜膜的变形的可能性可谓极高。
[0091]
从表1可知,在600℃以上且950℃以下的脱离气体量相对于因60℃以上且950℃以下的加热而脱离的气体总量的比率(w1/w0),在实施例中显著低于比较例1。由此也可认为,在对实施例1的铜粉体进行烧结的情况下,在形成膜的过程中不会有大量的气体脱离,能够有效地防止铜膜的空隙的产生和变形。
[0092]
【表1】
[0093][0094]
作为本发明的实施方式,上述实施方式只要不相互矛盾,就可以适当地组合实施。此外,本领域技术人员基于各实施方式对构成要素进行适当地添加、删除或改变设计,或者
对工序进行添加、省略或改变条件,只要具备本发明的要旨,也包含在本发明的范围内。
[0095]
即使是与由上述各实施方式的方式带来的作用效果不同的其他作用效果,根据本说明书的记载可以明确,或者本领域技术人员可以容易地预测的作用效果,当然可以理解为由本发明带来的作用效果。
再多了解一些
本文用于企业家、创业者技术爱好者查询,结果仅供参考。