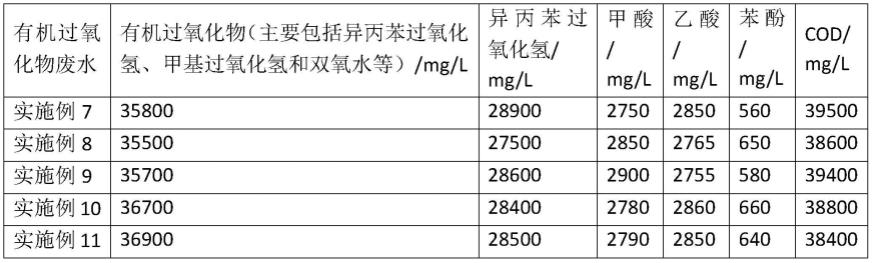
一种催化剂、制备方法和在处理含过氧化物的po/chp废水中的应用
技术领域
1.本发明属于化学工程与环境工程废水处理技术领域,更具体地说,涉及一种催化氧化过氧化物的催化剂,催化剂的制备方法及处理含过氧化物的po/chp废水的处理方法。
背景技术:
2.chp(异丙苯过氧化氢)法是制备环氧丙烷和二甲基苄醇单体的非常重要的一种方法。描述这种方法的基本文献是《chp法生产二甲基苄醇和环氧丙烷的新工艺》。该方法的基本流程是在过氧化阶段,空气作为氧化剂将异丙苯氧化为异丙苯过氧化物,该过氧化物在环氧化阶段与丙烯反应生成环氧丙烷和二甲基苄醇,然后,二甲基苄醇脱水生成异丙苯。
3.装置生产过程中会产生大量的废水,其中,异丙苯过氧化塔顶凝液产水不仅含有大量的酸性物质,主要是甲酸、乙酸和少量的苯酚,还含有大量的过氧化物(主要以甲基过氧化氢和异丙苯过氧化氢的形式存在)。过氧化物对生物具有灭活作用,因此该废水生化性较差,b/c=0(b/c为可生化性指标,0.3<b/c<1说明生化性较好,b/c<0.1说明较难生化)。
4.为提高废水生化性,达到排生化指标要求(b/c>0.3),需将废水中的过氧化物进行预处理,降低对生物的灭活作用。传统的处理方法是用硫代硫酸钠、亚硫酸氢钠等还原剂,过氧化氢分解酶等对过氧化物进行分解,或将ph调解至12以上,提高过氧化物的分解,这些方法都存在分解速度慢,处理成本高,难以达到较低产水浓度的问题。
5.发明专利us5993673公开了一种催化分解过氧化物的方法,其采用固体铁促进的氧化铝作为催化剂处理含过氧化物废水,其采用低浓度的双氧水作为过氧化体系,cn110605124公开了一种处理posm废水中过氧化物的方法,其过氧化物主要为ebhp(乙苯过氧化氢),而实际该pochp废水中过氧化物主要含有异丙苯过氧化氢chp,该过氧化物相对难以分解,并且其浓度可达3.5wt%左右。
6.需要开发一种高处理效率以及不产生二次污染的新的促进过氧化物催化分解的处理工艺。
技术实现要素:
7.本发明的目的之一在于提供一种用于有机过氧化物催化氧化的催化剂,该催化剂对过氧化物处理效果稳定。
8.本发明的另一个目的在于提供所述催化剂的制备方法。
9.本发明的再一个目的在于提供所述催化剂用于处理含过氧化物的pochp废水的方法。
10.为达到以上目的,本发明采用的技术方案如下:
11.一种有机过氧化物催化氧化催化剂,所述催化剂包括载体和活性组分,所述载体为氧化钛;所述活性组分包括以氧化物形态存在的铜、铬、铈、镍和钡。
12.优选地,以载体的重量为基准计,活性组分的金属元素的含量为:
13.铜0.1~1wt%,优选0.5~0.7wt%;
14.铬0.2~0.8wt%,优选0.4~0.6wt%;
15.铈0.1~1wt%,优选0.5~0.7wt%;
16.镍0.3~0.8wt%,优选0.5~0.7wt%;
17.钡0.1~0.8wt%,优选0.4~0.6wt%。
18.本发明中,氧化钛载体的预处理及活化方法包括:将氧化钛原料在研磨设备中研磨至50~60目,放至加有滤纸盖的容量桶中,在110~130℃下干燥5~6h,冷却至室温,得到氧化钛粗粉,将氧化钛粗粉与质量分数为20~22%的hcl溶液以料液质量比为1:10混合,在搅拌器下搅拌20~24h,得到混合料液,将混合料液用蒸馏水稀释、离心5~7次至中性,干燥5~6h,得到处理活化后的氧化钛,再在500~700℃焙烧2~4h,最后通过挤条机成型得到长度在1~2cm,比表面积1000~2000m2/g的载体。
19.作为一种优选的方案,所述载体为经超声改性,并任选通过添加芬顿铁泥进行改性和/或添加聚合氯化铝作为助剂的改性氧化钛,更优选地,所述载体为经超声改性,并通过添加芬顿铁泥进行改性和添加聚合氯化铝作为助剂的改性氧化钛。
20.采用超声技术对载体混合物进行改性预处理后,可有效的去除空隙内的杂质,避免催化剂在氧化分解有机物的过程中,在孔道内部形成聚合性的颗粒物质,堵塞孔道,此外,通过超声预处理可改善载体的比表面积和表面官能团性质,提高催化剂多孔表面对有机物的吸附作用,可延长失活时间,提高废水的处理效果。
21.本发明所述超声改性的方法,包括以下步骤:选择超声改性的超声功率为100~150w,超声的频率为50~80hz,优选60~70hz,超声时间为30~50min,处理后纯水洗涤,115℃~125℃下干燥4~6h,得到经超声改性的氧化钛。
22.进一步优选地,使用芬顿铁泥对经超声改性的氧化钛进行改性,以氧化钛的重量为基准计,芬顿铁泥的含量为1.0~6.0wt%,优选2.0~3.0wt%。
23.芬顿处理工艺是废水处理过程中的一种常用的高级氧化技术,主要通过添加双氧水和硫酸亚铁对废水中的难降解物质进行催化分解,以达到生化性提升的目的,该工艺会产生大量的氢氧化铁和矿化有机物的混合物质,俗称铁泥。铁泥按照一定比例烧制出的载体,硬度高,孔隙率大,耐强碱性,能够有效的提高载体的比表面积和结构强度。
24.本发明所述的使用铁泥对经超声改性的氧化钛进行改性的方法,包括以下步骤:铁泥溶液和经超声改性的氧化钛进行等体积浸渍,浸渍时间为50~250min,优选100~150min;然后将所得固体在60~150℃干燥3~5h,再在450~600℃焙烧3~5h,得到超声和添加铁泥改性的氧化钛。所述的铁泥溶液是将铁泥溶于纯水中,配制成的溶液浓度为0.01~0.02g铁泥/ml纯水。
25.更进一步优选地,添加聚合氯化铝作为助剂,对经超声和芬顿铁泥改性的氧化钛进行改性,以氧化钛的重量为基准计,聚合氯化铝的含量为2.0~7.0wt%,优选4.0~5.0wt%。
26.本发明所述的使用聚合氯化铝对经超声和芬顿铁泥改性的氧化钛进行改性的方法,包括以下步骤:5.0~10wt%的聚合氯化铝水溶液和经超声和铁泥改性的氧化钛进行等体积浸渍,浸渍时间为50~250min,优选100~150min;然后将所得固体在60~150℃干燥3
~5h,再在450~600℃焙烧3~5h,得到超声和添加铁泥改性的并增加聚合氯化铝助剂的氧化钛。
27.本发明所述催化剂的制备方法,包括以下步骤:
28.将含有铜盐、铬盐、铈盐、镍盐和钡盐的溶液加入到载体中,进行等体积浸渍,浸渍时间为100~250min,优选150~200min;然后将所得固体在120~140℃干燥,干燥时间为2~3h,再在550~650℃焙烧3~5h,得到所述催化剂。
29.优选地,在进行等体积浸渍前,将载体进行真空预处理,所述的真空预处理的时间为40~60min,真空度为96.0~98.0kpa,通过真空预处理,除去载体加工过程中的颗粒物杂质,提高活性组分在载体表面的附着效果。
30.优选地,所述铜盐、铬盐、铈盐、镍盐和钡盐分别来源于含有相应金属元素的硝酸盐、醋酸盐和碳酸盐中的一种或多种,优选硝酸盐。
31.本发明还涉及上述催化剂在处理含过氧化物的废水中的应用。
32.一种含过氧化物的po/chp废水的处理方法,包括以下步骤:
33.(1)将含过氧化物的po/chp废水进行催化氧化反应;
34.(2)将步骤(1)得到的废水进行生化处理后排放;
35.所述含过氧化物的po/chp废水是po/chp生产工艺过程产生的废水,满足以下条件:有机过氧化物(包括双氧水和异丙苯过氧化氢、甲基过氧化氢)≤40000mg/l,其中,异丙苯过氧化氢≤35000mg/l;cod(化学需氧量)≤70000mg/l;甲酸≤4000mg/l;乙酸≤7000mg/l;苯酚≤5000mg/l。
36.经过本发明的步骤(1)处理之后,废水中的过氧化物经催化分解后生成具有强氧化性的羟基自由基,并与废水中的有机物接触过程中,分解生成二氧化碳或小分子易生化类物质,进一步提高废水生化性。
37.本发明的步骤(1)的反应条件包括:反应温度60~80℃,空速0.5~3.5h-1
,优选1.5~2.5h-1
。
38.反应温度和反应时间的提高,有利于过氧化物和有机物分解效率的增加,但相应的运行和投资成本会有所升高,此外,随着时间和温度升高,大量有机物转化为二氧化碳或小分子有机物,而小分子物质生化性较高,且难以继续反应,因此,反应温度和时间需要优化的范围。与双氧水类的过氧化物不同,有机过氧化物特别是pochp废水中的甲基过氧化氢,在常温常压无催化剂存在下分解效率较低,无法充分分解为羟基自由基,而在催化剂存在下,催化剂的活性位大大降低反应的活化能,会将有机过氧化物快速分解转化为[oh],进而将有机物分解除去。
[0039]
本发明所述的步骤(2)可以在本领域公知的任意设备中进行,优选采用曝气生物滤池反应器。
[0040]
本发明所述的步骤(2)主要将催化氧化后的易生化的小分子有机物以及原废水含有的甲酸、乙酸等去除,生化条件包括:温度35~45℃、优选37~42℃,进水cod负荷为0.5~1.5kg/(m3*天),优选0.7~1kg/(m3*天),进水ph=6~8,优选6.5~7.5。
[0041]
本发明的有益效果在于:
[0042]
(1)本发明所用的载体、改性剂以及金属氧化物,简单易得,成本低廉。
[0043]
(2)优选方案中,氧化钛经过超声和添加芬顿铁泥改性,并添加聚合氯化铝助剂,
可以降低活性金属流失,避免有机物在催化剂孔道内聚合结焦,增加催化剂的寿命,强化孔道结构,增加催化剂比表面积,提高活性组分与有机物的接触位点,并增加载体对有机物固有的吸附效果。
具体实施方式
[0044]
以下通过具体实施例对本发明技术方案及其效果做进一步说明。以下实施例仅用于说明本发明的内容,并不用于限制本发明的保护范围。应用本发明的构思对本发明进行的简单改变都在本发明要求保护的范围内。
[0045]
超声仪,型号bilon6-180,购自上海比朗仪器制造有限公司;
[0046]
催化氧化塔,购自徐州市龙泰臭氧设备制造有限公司;
[0047]
氧化钛,购自上海汇精亚纳米新材料有限公司;
[0048]
芬顿铁泥,取自万华化学烟台工业园废水处理装置;
[0049]
聚合氯化铝,山东鲁通鑫化工有限公司;
[0050]
含有机过氧化物的po/chp废水,由万华化学中试实验装置生产所得。
[0051]
gc分析条件:采用安捷伦hp-5型号气相色谱柱,色谱柱尺寸为30m*530μm*1.5μm,色谱柱升温方法为:设定初始温度为70℃,保持5min,并按照5℃/min的速度升温至300℃,保持10min,进行水质主组分分析;
[0052]
cod分析:采用国标重铬酸钾氧化分析方法。
[0053]
实施例1:超声改性氧化钛的制备
[0054]
取氧化钛样品20g置于200ml纯水中,然后将其慢慢倒入超声仪中中,选择超声改性的超声功率为150w,超声的频率为80hz,超声时间为50min,处理后纯水洗涤,115℃下干燥5h,得到经超声改性的氧化钛。
[0055]
实施例2:0#催化剂的制备
[0056]
取氧化钛样品20g置于浸渍瓶中,进行真空预处理,真空预处理时间为50min,真空度为97.0kpa;
[0057]
取含铜0.10g/ml的硝酸铜水溶液1.0ml、含铬0.10g/ml的硝酸铬水溶液1.0ml、含铈0.10g/ml的硝酸铈水溶液1.0ml、含镍0.10g/ml的硝酸镍水溶液1.0ml、含钡0.10g/ml的硝酸钡水溶液1.0ml,加入到乙醇浓度为10wt%的乙醇水溶液中,配制成总体积为16.4ml的浸渍液。将上述浸渍液加入到装有上述氧化钛载体的真空浸渍瓶中并混合均匀,浸渍120min后,取出并置于烘箱内130℃干燥2h,然后在马弗炉内600℃焙烧4h,得到0#催化剂。
[0058]
所得0#催化剂中,以其中氧化钛的重量为基准计,活性组分的金属元素的含量如下:铜0.5wt%,铬0.5wt%,铈0.5wt%,镍0.5wt%和钡0.5wt%。
[0059]
实施例3:1#催化剂的制备
[0060]
取实施例1中超声后的氧化钛固体20g置于浸渍瓶中,进行真空预处理,真空预处理时间为50min,真空度为97.0kpa;
[0061]
取含铜0.10g/ml的硝酸铜水溶液1.0ml、含铬0.10g/ml的硝酸铬水溶液1.0ml、含铈0.10g/ml的硝酸铈水溶液1.0ml、含镍0.10g/ml的硝酸镍水溶液1.0ml、含钡0.10g/ml的硝酸钡水溶液1.0ml,加入到乙醇浓度为10wt%的乙醇水溶液中,配制成总体积为16.4ml的浸渍液。将上述浸渍液加入到装有上述氧化钛载体的真空浸渍瓶中并混合均匀,浸渍
120min后,取出并置于烘箱内130℃干燥2h,然后在马弗炉内600℃焙烧4h,得到1#催化剂。
[0062]
所得1#催化剂中,以其中氧化钛的重量为基准计,活性组分的金属元素的含量如下:铜0.5wt%,铬0.5wt%,铈0.5wt%,镍0.5wt%和钡0.5wt%。
[0063]
实施例4:2#催化剂的制备
[0064]
取实施例1中超声改性后的氧化钛固体20g置于浸渍瓶中,进行真空预处理,真空预处理时间为50min,真空度为97.0kpa;
[0065]
取含芬顿铁泥0.01g/ml的芬顿铁泥水溶液40.0ml,加入到乙醇浓度为10wt%的乙醇水溶液中,配制成总体积为80.0ml的浸渍液。将上述浸渍液加入到装有上述氧化钛固体的真空浸渍瓶中混合均匀后对上述固体进行等体积浸渍,浸渍100min后,取出并置于烘箱内80℃干燥4h,然后在马弗炉内550℃焙烧5h,制得芬顿铁泥改性氧化钛载体。所制得的氧化钛载体中,以氧化钛的重量为基准计,芬顿铁泥的含量为2.0wt%。
[0066]
取上述芬顿铁泥改性氧化钛载体20g置于浸渍瓶中;取含铜0.10g/ml的硝酸铜水溶液1.0ml、含铬0.10g/ml的硝酸铬水溶液1.0ml、含铈0.10g/ml的硝酸铈水溶液1.0ml、含镍0.10g/ml的硝酸镍水溶液1.0ml、含钡0.10g/ml的硝酸钡水溶液1.0ml,加入到乙醇浓度为10wt%的乙醇水溶液中,配制成总体积为24.4ml的浸渍液。将上述浸渍液加入到装有上述芬顿铁泥改性氧化钛载体的真空浸渍瓶中并混合均匀,对上述芬顿铁泥改性氧化钛载体进行等体积浸渍,浸渍200min后,取出并置于烘箱内130℃干燥3h,然后在马弗炉内580℃焙烧4h,得到2#催化剂。
[0067]
所得2#催化剂中,以其中以芬顿铁泥改性氧化钛载体的重量为基准计,活性组分的金属元素的含量如下:铜0.5wt%,铬0.5wt%,铈0.5wt%,镍0.5wt%和钡0.5wt%。
[0068]
实施例5:3#催化剂的制备
[0069]
取实施例1中超声改性后的氧化钛固体20g置于浸渍瓶中,进行真空预处理,真空预处理时间为60min,真空度为96.0kpa;
[0070]
取含芬顿铁泥0.01g/ml的芬顿铁泥水溶液40.0ml,加入到乙醇浓度为10wt%的乙醇水溶液中,配制成总体积为80.0ml的浸渍液。将上述浸渍液加入到装有上述超声改性后的氧化钛固体的真空浸渍瓶中混合均匀后对上述超声改性后的氧化钛固体进行等体积浸渍,浸渍100min后,取出并置于烘箱内100℃干燥4h,然后在马弗炉内550℃焙烧5h,制得芬顿铁泥改性超声改性后的氧化钛固体。所制得的芬顿铁泥改性超声改性后的氧化钛固体中,以超声改性后的氧化钛固体的重量为基准计,芬顿铁泥的含量为2.0wt%。
[0071]
10wt%的聚合氯化铝水溶液和经超声和铁泥改性的氧化钛进行等体积浸渍,浸渍时间为120min;然后将所得固体在120℃干燥4h,再在500℃焙烧4h,得到超声和添加铁泥改性的并增加聚合氯化铝助剂的载体。以超声改性后的氧化钛固体的重量为基准计,聚合氯化铝的含量为3.0wt%。
[0072]
取上述增加聚合氯化铝改性后的氧化钛固体载体20g置于浸渍瓶中;取含铜0.10g/ml的硝酸铜水溶液1.0ml、含铬0.10g/ml的硝酸铬水溶液1.0ml、含铈0.10g/ml的硝酸铈水溶液1.0ml、含镍0.10g/ml的硝酸镍水溶液1.0ml、含钡0.10g/ml的硝酸钡水溶液1.0ml,加入到乙醇浓度为10wt%的乙醇水溶液中,配制成总体积为26.2ml的浸渍液。将上述浸渍液加入到装有上述增加聚合氯化铝改性后的氧化钛固体载体的真空浸渍瓶中并混合均匀,对上述增加聚合氯化铝改性后的氧化钛固体载体进行等体积浸渍,浸渍150min后,
取出并置于烘箱内130℃干燥2h,然后在马弗炉内600℃焙烧4h,得到3#催化剂。
[0073]
所得3#催化剂中,以其中增加聚合氯化铝改性后的氧化钛固体载体的重量为基准计,活性组分的金属元素的含量如下:铜0.5wt%,铬0.5wt%,铈0.5wt%,镍0.5wt%和钡0.5wt%。
[0074]
实施例6:4#催化剂的制备
[0075]
取实施例1中超声改性后的氧化钛固体20g置于浸渍瓶中,进行真空预处理,真空预处理时间为60min,真空度为96.0kpa;
[0076]
取含芬顿铁泥0.01g/ml的芬顿铁泥水溶液40.0ml,加入到乙醇浓度为10wt%的乙醇水溶液中,配制成总体积为80.0ml的浸渍液。将上述浸渍液加入到装有上述超声改性后的氧化钛固体的真空浸渍瓶中混合均匀后对上述超声改性后的氧化钛固体进行等体积浸渍,浸渍100min后,取出并置于烘箱内100℃干燥4h,然后在马弗炉内550℃焙烧5h,制得芬顿铁泥改性超声改性后的氧化钛固体。所制得的芬顿铁泥改性超声改性后的氧化钛固体中,以超声改性后的氧化钛固体的重量为基准计,芬顿铁泥的含量为2.0wt%。
[0077]
10wt%的聚合氯化铝水溶液和经超声和铁泥改性的氧化钛固体进行等体积浸渍,浸渍时间为120min;然后将所得固体在120℃干燥4h,再在500℃焙烧4h,得到超声和添加铁泥改性的并增加聚合氯化铝助剂的载体。以超声改性后的氧化钛固体的重量为基准计,聚合氯化铝的含量为3.0wt%。
[0078]
取上述增加聚合氯化铝改性后的氧化钛固体载体20g置于浸渍瓶中;取含铜0.15g/ml的硝酸铜水溶液1.0ml、含铬0.05g/ml的硝酸铬水溶液1.0ml、含铈0.15g/ml的硝酸铈水溶液1.0ml、含镍0.15g/ml的硝酸镍水溶液1.0ml、含钡0.15g/ml的硝酸钡水溶液1.0ml,加入到乙醇浓度为10wt%的乙醇水溶液中,配制成总体积为26.2ml的浸渍液。将上述浸渍液加入到装有上述增加聚合氯化铝改性后的氧化钛固体载体的真空浸渍瓶中并混合均匀,进行等体积浸渍,浸渍150min后,取出并置于烘箱内130℃干燥2h,然后在马弗炉内600℃焙烧4h,得到4#催化剂。
[0079]
所得4#催化剂中,以其中增加聚合氯化铝改性后的氧化钛固体载体的重量为基准计,活性组分的金属元素的含量如下:铜0.75wt%,铬0.25wt%,铈0.75wt%,镍0.75wt%和钡0.75wt%。
[0080]
在以下的实施例中,含有机过氧化物废水的取样分析结果见表1。
[0081]
表1有机过氧化物废水组成
[0082][0083]
实施例7:含有机过氧化物的pochp废水的处理(0#催化剂)
[0084]
步骤(1):取表1所示的含有机过氧化物废水,通入催化氧化塔,反应温度80℃,空速2h-1
,在0#催化剂作用下含有机过氧化物被分解为具有强氧化性的羟基自由基,将废水中
的大分子物质分解为小分子酸,部分小分子羧酸进一步氧化为co2和h2o,反应后有机过氧化物含量降低至12550mg/l,异丙苯过氧化氢含量降低至8895mg/l,甲酸含量降低至1150mg/l,乙酸含量降低至1200mg/l,苯酚处理至280mg/l,cod降低至15500mg/l,有机过氧化物的分解效率为65%,产水铜离子含量0.5mg/l,铬离子0.7mg/l,铈含量0.9mg/l,镍离子0.4mg/l,钡离子1.5mg/l。
[0085]
步骤(2):将步骤(1)催化氧化后的含有机过氧化物废水通入生物反应器中,温度40℃,进水cod负荷为1kg/(m3*天),进水ph=7,经生化反应处理后,有机过氧化物含量降低至2480mg/l,cod降低至7500mg/l,甲酸、乙酸及苯酚未检出。
[0086]
实施例8:含有机过氧化物废水的处理(1#催化剂)
[0087]
步骤(1):取表1所示的含有机过氧化物废水,通入催化氧化塔,反应温度80℃,空速2h-1
,反应后有机过氧化物含量降低至8550mg/l,异丙苯过氧化氢含量降低至6895mg/l,甲酸含量降低至950mg/l,乙酸含量降低至1050mg/l,苯酚处理至270mg/l,cod降低至13500mg/l,有机过氧化物的分解效率为76%,产水铜离子含量0.4mg/l,铬离子0.7mg/l,铈含量0.8mg/l,镍离子0.5mg/l,钡离子1.5mg/l。
[0088]
步骤(2):将步骤(1)催化氧化后的含有机过氧化物废水通入生物反应器中,温度40℃,进水cod负荷为1kg/(m3*天),进水ph=7,经生化反应处理后,有机过氧化物含量降低至2120mg/l,cod降低至6500mg/l,甲酸、乙酸及苯酚未检出。
[0089]
实施例9:含有机过氧化物废水的处理(2#催化剂)
[0090]
步骤(1):取表1所示的含有机过氧化物废水,通入催化氧化塔,反应温度80℃,空速2h-1
,反应后有机过氧化物含量降低至2550mg/l,异丙苯过氧化氢含量降低至1580mg/l,甲酸含量降低至850mg/l,乙酸含量降低至950mg/l,苯酚处理至250mg/l,cod降低至8600mg/l,有机过氧化物的分解效率为93%,产水铜离子含量0.5mg/l,铬离子0.7mg/l,铈含量0.8mg/l,镍离子0.4mg/l,钡离子1.5mg/l。
[0091]
步骤(2):将步骤(1)催化氧化后的含有机过氧化物废水通入生物反应器中,温度40℃,进水cod负荷为1kg/(m3*天),进水ph=7,经生化反应处理后,有机过氧化物含量降低至280mg/l,cod降低至1650mg/l,甲酸、乙酸及苯酚未检出。
[0092]
实施例10:含有机过氧化物废水的处理(3#催化剂)
[0093]
步骤(1):取表1所示的含有机过氧化物废水,通入催化氧化塔,反应温度80℃,空速2h-1
,反应后有机过氧化物含量降低至2450mg/l,异丙苯过氧化氢含量降低至1480mg/l,甲酸含量降低至680mg/l,乙酸含量降低至810mg/l,苯酚处理至230mg/l,cod降低至7800mg/l,有机过氧化物的分解效率为93%,产水铜离子含量0.04mg/l,铬离子0.01mg/l,铈含量0.001mg/l,镍离子0.02mg/l,钡离子0.02mg/l。
[0094]
步骤(2):将步骤(1)催化氧化后的含有机过氧化物废水通入生物反应器中,温度40℃,进水cod负荷为1kg/(m3*天),进水ph=7,经生化反应处理后,有机过氧化物含量降低至260mg/l,cod降低至1375mg/l,甲酸和乙酸及苯酚未检出。
[0095]
实施例11:含有机过氧化物废水的处理(4#催化剂)
[0096]
步骤(1):取表1所示的含有机过氧化物废水,通入催化氧化塔,反应温度80℃,空速2h-1
,反应后有机过氧化物含量降低至2350mg/l,异丙苯过氧化氢含量降低至1380mg/l,甲酸含量降低至670mg/l,乙酸含量降低至800mg/l,苯酚处理至230mg/l,cod降低至
7700mg/l,有机过氧化物的分解效率为94%,产水铜离子含量0.04mg/l,铬离子0.01mg/l,铈含量0.002mg/l,镍离子0.02mg/l,钡离子0.03mg/l。
[0097]
步骤(2):将步骤(1)催化氧化后的含有机过氧化物废水通入生物反应器中,温度40℃,进水cod负荷为1kg/(m3*天),进水ph=7,经生化反应处理后,有机过氧化物含量降低至250mg/l,cod降低至1355mg/l,甲酸、乙酸、苯酚未检出。
再多了解一些
本文用于企业家、创业者技术爱好者查询,结果仅供参考。