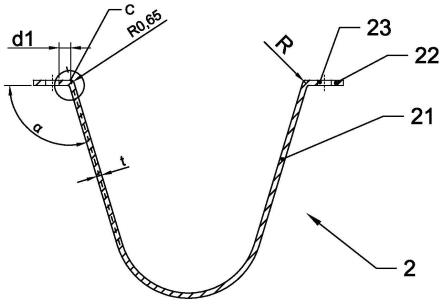
1.本技术涉及桥梁工程领域,尤其是一种桥面结构及用于桥面结构的纵肋。
背景技术:
2.桥梁行业的正交异性钢桥面结构是一种在承受外部荷载的顶板的背部,采用各种加劲构造措施进行结构强化的非单层结构的加劲钢板构造,用于加强构件刚度并保证局部稳定所设置的板状加劲件。传统正交异性桥面结构包括顶板和加劲肋,加劲肋包括纵肋和横肋,顶板、纵肋和横肋组成协同受力的有机整体,板件间主要通过焊接进行连接。
3.正交异性钢桥面结构在相同荷载的作用下,应力比单钢板中的应力低得多,且比单钢板具有较大的截面惯性矩,这意味着比单钢板具有较大的刚度。但其也存在许多弊病,全世界范围内正交异性桥面都发生了大量的开裂和疲劳现象,且以此为主因引起了桥面铺装层的车辙、纵横向裂缝等各类通病,通病已成为其应用近70年以来的世界级顽症,多年以来且一直没有找到较完美的解决方案。
4.正交异性钢桥面结构的众多研究表明,引起疲劳通病的最主要因素有:纵肋尤其是纵肋的构造形式,以及各部件之间焊接或连接结构。
5.首先,现有纵肋侧壁与顶板竖直或倾斜相交布置于顶板的背面,顶板直接承受车轮载荷,纵肋腹板通过焊接与顶板固定连接,该构造形式导致纵肋腹板与顶板连接只能采用类似t形接头对接焊缝,很多高端焊接方式难以应用,现有常用焊接方式多为75%左右部分熔透焊,其熔深浅,焊缝总深度约为8mm左右,焊道截面小,焊材耗材、辅材、热输入量大。
6.如图1所示,现有焊缝位于纵肋200的腹板与顶板100的相交处,该处焊缝位于应力集中的敏感区域,当外部载荷作用在顶板上时,无论作用在相邻纵肋之间的顶板上,或者是作用在闭口纵肋内部的顶板上,顶板均会以相交点为支点发生滚转,在传统做法中,由于焊缝位于支点处,焊根或焊趾到支点的距离小,力臂短,焊根或焊趾承受的拉力大,在外部载荷反复作用下,焊缝极易从焊跟和焊趾萌生向顶板和纵肋腹板的疲劳裂纹。然而,现有纵肋和顶板的对接结构,很难增加焊道截面,焊缝强度不足。
7.虽然近年来发展了的双面焊、纵肋腹板上缘镦厚等方式,这些方式均旨在通过增大该处焊道截面面积,从而提高该处焊缝强度,以解决纵肋与顶板连接处的疲劳开裂问题。如专利cn201210467772.7公开了一种桥梁用热轧u型加强肋,采用矩形钢材胚料,通过多次热轧工艺,轧制出一种变截面的u肋,u肋顶端镦粗形成折翻边,以改善纵肋与桥梁接触面积小,应力集中的问题。现实中,u肋往往为定制产品,用量小,该专利类似热轧成型的工艺,虽然从理论上可以生产出各种断面的纵肋结构,但需要从原材料的源头增加钢厂的热轧工艺,设备投入大,成本高昂,并不适用于实际生产。
技术实现要素:
8.本技术的发明目的是为了解决传统正交异性桥面结构的纵肋与顶板连接的焊缝易疲劳开裂等问题,提供一种远角连接的纵肋和采用该纵肋的桥面结构,纵肋通过翻边与
顶板连接,使其连接位置远离纵肋腹板转动支点,即应力敏感区域,显著降低了顶板与纵肋连接处疲劳开裂发生的概率。
9.为了实现上述发明目的,本技术采用了以下技术方案:
10.本技术第一方面提供了一种远角连接的纵肋,至少包括一个腹板和翻边,所述翻边位于腹板端部,所述纵肋由平钢板折弯或辊压而成,所述翻边和腹板具有转角α,90
°
≤α≤135
°
;
11.所述翻边上具有多个连接孔,所述腹板厚度的中心线与翻边顶面所在平面的交点为c,c点到连接孔的最短距离为d1,腹板板厚为t,t≤d1≤5t。
12.作为优选,所述c点在翻边顶面内。以保证c点不脱空,c点脱空将引起纵肋面外变形的附加弯矩,对纵肋肋臂的屈曲稳定非常不利,且易引起连接部位的长期单向应力,对连接点的疲劳不利。
13.作为优选,所述腹板和翻边的外转角半径r为0.5t~0.75t。该转角半径范围的设置,减少了纵肋腹板向内变形的概率,因纵肋腔内无专项支撑构造,向内屈曲将造成肋壁失稳状态,而上述转角半径增大了肋壁向外变形的概率,尤其在纵肋与横肋交叉处受力更大,而上述部位向外变形是有横肋腹板约束的,这样就确保了纵肋腹板的稳定性和纵肋功能的稳定发挥。而当r小于该范围时,纵肋将因母材蠕变的有限性,容易产生成型缺陷,且该缺陷位于肋内,不易检查、发现、和修复,当r大于0.5t时,该缺陷明显减少。当r大于0.75t时,造成纵肋肋壁在其延伸的投影方向有效支撑截面减少,肋壁产生较大的转动扭矩,当该扭矩超过肋壁高厚比所对应的稳定临界点时,纵肋肋壁将极易发生失稳,本技术有效规避了上述风险的发生。
14.作为优选,所述纵肋为闭口肋。对于闭口纵肋,由于两侧的焊缝外移,相邻纵肋之间实际的间距变小,顶板的跨度减小,纵肋能够突破高厚比、长厚比、宽厚比的制约,向大纵肋发展,增大单肋的惯性矩,不仅能够减少横肋节点、减少焊缝、减少零件数量等,在整体结构连续性更佳、对下部构造不敏感。
15.作为优选,所述纵肋高度与板厚之比大于45。传统设计主要因顶板与纵肋焊缝敏感原因,限制了纵肋效能的发挥,本技术在顶板与纵肋焊缝敏感问题解决之后,突破了传统结构纵肋高厚比的限制,正交异性钢桥面板采用薄肋壁,厚下翼缘的更高性能的高大纵肋成为了现实。
16.作为优选,所述纵肋为开口肋。采用了带翻边的开口肋与顶板的连接方式多样化,可设计性更强,尤其适用于桥梁悬臂段的应用。
17.本技术另一方面,提供了一种远角连接桥面结构,包括顶板和上述任一项所述的纵肋,所述翻边与顶板的底面贴合,所述连接孔内设置连接件,所述纵肋与顶板通过连接件固定连接。
18.作为优选,所述连接件为摩擦焊盘,所述摩擦焊盘通过旋转摩擦焊接将所述纵肋和顶板固定连接。采用摩擦焊盘连接,尤其适用于钢桥面结构,由于钢桥面结构的顶板为直接结构受力件,在顶板上开孔会弱化顶板的刚度,无需在顶板开孔就实现高强度的焊接。其次,多个纵向间隔的焊盘形成独立的焊岛,规避了传统角焊缝抗疲劳性能差、裂缝易延伸发展的缺点,且焊岛与焊岛之间通过工件自身刚度形成岛链结构,既利于整体构造的形成,又利用焊岛之间的母材应变,隔断焊岛与焊岛的裂缝发展的概率;通过该中间体焊盘,只需输
入极小的能量使其旋转,达到将两个大型工件,尤其是长、大、重的工件,以及非圆形的工件焊接的目的,显著拓展了摩擦焊的应用范围,使得该高端焊接工艺应用于桥梁等常用金属构件成为现实;摩擦焊相对于传统熔焊,属于固态焊接,焊接时杂质气孔被打碎挤出,焊缝的初始缺陷是疲劳开裂的主要因素之一,采用摩擦焊,其焊接强度高,抗疲劳性能佳,能有效提高钢桥面的抗疲劳性能。
19.作为优选,所述摩擦焊盘靠近顶板的端面为内凹面。因外侧线速度较大、输入能量大,融化快,中心线速度为0,输入能量小,融化慢,所以传统摩擦焊的纯圆平面不能达到深度嵌入母材的效果,或中心区域限制了其深度嵌入的效能。
20.本技术实施例焊盘端面采用沿着边缘向圆心方向向内倾斜的内凹面,焊接时,端面的边缘成为最先与第二工件接触的部位,高温下该区域的金属首先融化,使得受力最大的外侧的线速度、能量输入、融化速度进一步得到优先级保障;同时,一定斜度的内凹面,加深了外侧的焊接界面嵌入顶板母材的深度,增加了接合强度,提高了焊接接头的抗剪能力。其次,漏斗状凹面有助于熔融的金属向中部流动,通过空腔向外侧挤出。
21.作为优选,所述摩擦焊盘嵌入顶板内部,摩擦焊盘嵌入顶板的距离为d2,d2≥2mm。摩擦焊相对于其他连接方式或其他焊接方式,能够控制焊接界面的深度,除了焊缝本身的连接,形成机械嵌入咬合,能进一步提高摩擦盘的抗剪性能,同时,即使工件板厚和焊盘的高度存在尺寸偏差,通过控制插入深度,可以调节连接焊盘的凸缘到顶板的间距,保证凸缘压紧纵肋,保证纵肋和顶板两者紧密结合,对工件的精度要求更低。
22.作为优选,所述摩擦焊盘具有旋转轴部和台阶部;所述台阶部位于旋转轴部一端,且台阶部的直径大于旋转轴部的直径。利用台阶式的摩擦焊焊盘,通过焊盘外端台阶既压住工件,又在摩擦焊中嵌入,形成机械嵌固力,又通过性能稳定的摩擦焊,不但与顶板焊接,同时与纵肋焊接,增大了焊接面积,使得该构造可完全用于结构件,且具备很高的抗疲劳性能。
23.作为优选,所述摩擦焊盘中部开设沿轴向延伸的通孔。传统圆形端面中心线速度小,焊接性能较周边弱,成为一个焊接缺陷的隐患点,其缺陷发展有可能导致焊盘失效,圆心中心线速度较小的部位开孔,规避了中心焊接性能较弱区域的存在,同时焊接后顶板母材与焊盘内的圆孔相互嵌入,显著提高了抗剪能力。同时,焊盘中间的开孔可以用作排出多余熔材及杂质的通道,摩擦焊的熔材及杂质通过该孔顺利挤出,使摩擦焊的焊接截面纯净无杂质,焊接质量好。
24.作为优选,所述连接件为螺栓,所述顶板与纵肋通过螺栓固定连接。主要适用于组合结构桥面,通过螺栓连接,能够增加与混凝土的锚固作用,提高钢板与混凝土的结合强度。
25.作为优选,所述翻边远离腹板的外缘与顶板焊接连接。除通过连接件固定外,在容易发生疲劳的区域,在翻边外缘焊接可加强该处的连接强度,同时,翻边的外缘也可作为后续维修时的储备空间。
26.与现有技术相比,上述技术方案具有如下有益效果:
27.1、本技术实施例提出了一种新型的远角连接纵肋及桥面结构,创造性的通过折弯的翻边进行连接,并通过控制纵肋与顶板连接点的到支点的距离,既能够保证连接强度,同时连接点远离了支点,连接点到支点的距离相对于传统构造大幅增加,则外力到支点的力
臂与焊缝处拉力到支点的力臂之比大幅减小,从而焊缝处应力和应力幅减小,焊道能够承担更大的自由协同应变,这种新型的纵肋和顶板连接的构造细节,显著有效降低了顶板与纵肋连接处焊缝疲劳开裂的概率。
28.2、与传统构造不同,本技术纵肋在支点处无焊接,支点仅承压,将纵肋与顶板的承托压应力分解出来,由成型转角的母材承担,远离支点的焊缝承担剪力,将支点与焊缝的受力分离,使受力更简洁明确,减轻了焊缝处的应力及应力幅的大小,进一步提高了抗疲劳性能。
29.3、支点即纵肋腹板开合转动处,由抗疲劳性能高的母材转角的代替了传统构造的焊缝,强化了各间隔连接点的协同联系,尤其提高了连接点受力时的吸能效果,且肋转角处的自身抗扭转、抗弯性能提高,及本专利的上述远角连接构造,实现了顶板受力后引起纵肋的母材转角自由协同变化,但却对位于远处翻边上的连接点影响不敏感或迟钝的理想有益效果。
30.4、本技术实施例纵肋在解决了顶板与纵肋焊缝敏感问题后,突破纵肋高厚比、长厚比、宽厚比的制约,更多的截面可用于承担主应力的部位及横隔梁的部位,整个构造的双向的性能趋于平衡和兼顾;同时,翻边与顶板贴合处形成双层板,局部增加了顶板的厚度,且相同受力情况下,顶板可选用更薄板厚的钢板,进一步提高了材料效率。
附图说明
31.图1为本技术现有技术桥面纵肋和顶板焊接的结构示意图;
32.图2为本技术实施例1桥面结构的立体结构示意图;
33.图3为本技术实施例1一种远角连接的纵肋的立体结构示意图;
34.图4为本技术实施例1一种远角连接的纵肋的横截面图;
35.图5为图4的局部放大图;
36.图6为本技术实施例2的桥面结构采用摩擦焊的示意图;
37.图7为本技术实施例2中摩擦焊盘的结构示意图;
38.图8为本技术实施例3中采用螺栓连接的桥面结构的示意图;
39.图9为本技术实施例4中远角连接的开口纵肋的结构示意图。
40.附图标记:1、顶板;2、纵肋;21、腹板;22、翻边;23、连接孔;3、连接件;31、旋转轴部;32、台阶部;33、通孔;34、端面;4、混凝土层。
具体实施方式
41.下面结合附图对本技术做进一步描述。需要说明的是,在本技术的描述中,术语“横向”,“纵向”、“上”、“下”、“前”、“后”、“左”、“右”、“竖直”、“水平”、“顶”、“底”、“内”、“外”等指示的方位或位置关系为基于附图所示的方位或位置关系,仅是为了便于描述本技术和简化描述,并不是指示或暗示所指的装置或元件必须具有特定的方位,以特定的方位构造和操作,因此不能理解为对本技术的限制。
42.实施例1:
43.如图2所示,为一种桥面结构,包括顶板1、纵肋2。顶板1具有顶面和底面,顶面铺设混凝土或沥青等铺装层,承受外界轮载。顶板1底面设置若干纵肋2,纵肋2与顶板1的长度方
向平行,多个纵肋2并排间隔设置。
44.如图3、4所示,纵肋2为闭口肋,纵肋2包含一对轴对称的翻边22和腹板21。翻边22位于腹板21端部,翻边22和腹板21具有转角α,90
°
≤α≤135
°
;翻边22上具有多个沿纵肋2的长度方向间隔设置的连接孔23。翻边22和腹板21由一块等厚平钢板折弯或辊压而成,现有一些纵肋采用热轧等工艺来镦粗腹板端部,成本高昂,而且采用热轧加粗受板厚的影响,端部镦粗的宽度有限,焊缝仍不能远离转角敏感区,无法从根本上解决疲劳开裂问题。
45.如图2所示的桥面结构,还包括连接件3。纵肋2的翻边22与顶板1的底面贴合,连接孔23内设置连接件3,连接件3将顶板1和纵肋2固定连接。顶板1与纵肋2连接后,腹板21与顶板1相交,起到加筋作用。本实施例中,纵肋2的腹板21与顶板1倾斜相交,腹板21既可以承受纵向力,也可以承担横向力。如图4,腹板21厚度的中心线与翻边22顶面所在平面的交点为c,由于连接后顶板1底面与翻边22的顶面贴合,c点也为腹板21厚度的中心线与顶板1底面的交点。c点到连接孔23的最短距离为d1,腹板板厚为t,t≤d1≤5t。由纵肋2受载荷的各种情况可知,无论从顶板1下挠、偏心轮载大概率工况、扭转或畸变、以及各种工况所引起的面外变形、跨中扭转影响、跨中滚动影响等,都会引起一种基本的应变,即纵肋2的腹板21与顶板1焊接位置的夹角不断开合变化,也称畸变角变化,不断作用在焊根或焊趾附近,而畸变角变化的转动中心或支点即为点c。
46.本技术实施例提出了一种新型的远角连接桥面结构,将纵肋2与顶板1连接点的位置远离支点处,并通过控制c点到连接孔23的最短距离d1,即连接部位的力臂,来调整连接点处的应力和应力幅,当d1<t时,远角净距离(d1-0.5t)下限只剩下0.5t,此时,转动时连接部位应力增大,反之,远角净距离(d1-0.5t)上限将达到4.5t,此时连接距离过大,则纵肋和其连接点的连接强度显著削弱,引起纵肋畸变及滚动,起不到很好的固定纵肋的作用。
47.以上性能优势可从以下的计算分析中得出:
48.纵肋以常规开口为300mm、肋厚为8mm的纵肋为例,以传统纵肋与顶板的连接时,端部墩厚至10mm,钝边宽为2mm,则焊道顶面水平宽为9mm,焊接夹角开合的中心转动点理论上位于纵肋腹板21与顶板底板交点,该中心点离焊趾的距离则为9/2=4.5mm,则顶板受荷时,外力的合力的中心点位于纵肋中心,即到支点距离为300/2=150mm。焊趾处受力杠杆力臂比值:(150-4.5):4.5≈32:1。在肋壁转动中心附近即转动支点附近,假设支点离焊根距离为1mm(实际远小于1mm,甚至为0),焊根处受力杠杆力臂比值:(150-4.5):1=145.5:1。可见传统纵肋焊缝受力对外力具有至少32倍-145倍放大倍数。
49.本技术实施例中,假设连接孔与到支点点c的最小距离d1为t,远角净距离为d1-0.5t=4mm,则受荷时连接件受力的杠杆力臂比值:(150-4):4≈36.5:1,假设连接孔与到支点点c的最小距离d1为5t,远角净距离为d1-0.5t=36mm,则受荷时连接件受力的杠杆力臂比值:(150-4):36≈4.06:1。
50.由此可见,本技术实施例中,外力到支点的力臂与焊缝处拉力到支点的力臂之比相比传统纵肋构造大幅减小,且d1越大,该比值越低,因而本结构连接位置处应力和应力幅减小,如在该处焊接,焊缝能够承担更大的自由协同应变,这种新型的纵肋和顶板连接的构造细节,显著降低了顶板与纵肋连接处焊缝疲劳开裂的概率,提高了抗疲劳性能。
51.同时,由于本技术实施例中由于c点位置无焊接,支点仅承压,将纵肋2与顶板1的承托压应力分解出来,由成型转角的母材承担,远离支点点c的连接处焊缝或连接件承担剪
力,将两者受力分离,使受力更简洁明确,进一步减低了连接位置的应力及应力幅的大小,提高抗疲劳性能。
52.进一步的,本技术实施例通过纵肋2上缘设置较宽的翻边22,不仅增加纵肋2的截面惯性矩,通过相邻纵肋之间的顶板的实际跨度减小,能够突破高厚比、长厚比、宽厚比的制约,使得肋的高度增加、经济性增加,使得更多的截面可用于承担主应力的部位及横隔梁的部位,整个构造的双向的性能趋于平衡和兼顾;翻边22与顶板1贴合处形成双层板,局部增加了顶板1的厚度,且相同受力情况下,顶板1可选用更薄板厚的钢板,进一步提高了材料效率。
53.如图4、5所示,若c点脱空或腹板21和翻边22的外转角半径过大,将引起纵肋腹板21产生附加弯矩,对纵肋腹板21的稳定非常不利,容易发生屈曲,易引起连接部位的长期单向应力,(即长期拉应力或长期压应力,对连接点的疲劳不利,在转角处优选c点不脱空,即c点在翻边23顶面内。
54.同时,腹板21和翻边22的外转角半径r优选为0.5t~0.75t,而当r小于该范围时,纵肋2将因母材蠕变的有限性,容易产生成型缺陷,且该缺陷位于肋内,不易检查、发现、和修复,当r大于0.5t时,该缺陷明显减少。当r大于0.75t时,造成纵肋腹板21在其延伸的投影方向有效支撑截面减少,腹板21产生较大的转动扭矩,当该扭矩超过腹板21高厚比所对应的稳定临界点时,纵肋腹板21将极易发生失稳。本范围有效规避了上述风险的发生。
55.如图3所示,连接孔23沿纵肋长度方向课不等距间隔布置。尤其在横肋上方等容易开裂的区域,可以通过小间距密排连接件来强化局部疲劳强度,相对于传统纵肋顶板连接的通长焊缝,通过连接孔连接,在纵长方向可以匹配不同的受力情况,可设计性更强。同时,翻边22侧边与顶板1不焊接或部分段焊,为后续加固留有维护空间。
56.实施例2:
57.如图6所示,实施例2的桥面结构中,连接件3为摩擦焊盘,纵肋2与顶板1采用摩擦焊接进行焊接固定。
58.如图6所示,摩擦焊盘的结构与连接孔23形状相互匹配。连接时,翻边22与顶板1相互贴合,摩擦焊盘设置在所述连接孔23内。以摩擦焊盘旋转行进方向为前,反之为后,摩擦焊盘为旋成体,具有旋转轴部31和台阶部32,台阶部32位于旋转轴部31后端,且直径大于旋转轴部31后端端面的直径。焊接时,摩擦焊盘在连接孔23内,由电机带动高速旋转,摩擦生热,摩擦焊盘与顶板1、纵肋2的接触区域金属发生塑性变形,同时向摩擦焊盘加压,将纵肋2和顶板1焊接连接。焊接后,台阶部31压紧翻边22,形成机械嵌固力,又通过性能稳定的摩擦焊,不但与顶板焊接,同时与纵肋焊接,增大了焊接面积,提高了连接强度。
59.从实施例1可知,由于支点处和连接件3的受力分离,支点处主要承受压应力,因而连接件3主要承受的是横向剪切力,因而在摩擦焊盘设计了多项提高抗剪性能的构造:
60.首先由于圆形端面在旋转时,其中心线速度小,外部线速度大,容易造成中心焊接性能较周边弱,成为一个焊接缺陷的隐患点,如图7所示,在摩擦焊盘前端面34中部开设空腔或通孔33,将圆心中心线速度较小的部位不摩擦,既规避了中心焊接性能较弱区域的存在,焊盘端面开孔形成环形端面,在焊接后不仅能与顶板1相互嵌入,显著提高抗剪能力。同时,摩擦焊盘中间的开孔可以用作排出多余熔材及杂质的通道,摩擦焊的熔材及杂质通过该孔顺利挤出,使摩擦焊的焊接截面纯净无杂质,焊接质量好,该如熔材通过摩擦焊盘和纵
肋2两工件之间的缝隙挤出,不但会扩大两工件的间隙,还会造成部分工件悬空形成缺陷。
61.其次,如图6、7所示,旋转轴部31前端面34为沿边缘向中心方向逐渐向内凹的凹面。因外侧线速度较大、输入能量大,融化快,中心线速度为0,输入能量小,融化慢,所以传统摩擦焊的纯圆平面不能达到深度嵌入母材的效果,或中心区域限制了其深度嵌入的效能。采用沿着边缘向圆心方向向内倾斜的凹面,焊接时,端面的边缘成为最先与第二工件接触的部位,高温下该区域的金属首先融化,使得外侧和圆心的线速度、能量输入、融化速度趋于匹配;同时,一定斜度的内凹面,加深了外侧的焊接界面嵌入顶板母材的深度,进一步增加了摩擦焊盘的抗剪能力。其次,漏斗状斜坡有助于熔融的金属向中部流动,通过空腔向外侧挤出。
62.如图6、7所示,旋转轴部31为锥形,圆柱的焊盘在转动时,转轴的偏心摆动及停车时焊接面的的收缩效应使焊缝界面呈现拉应力状态,不利于疲劳性能的提高。锥形斜面的焊盘与开孔的侧壁形成一个自然的压力载体,其合适的斜率能几何级的提高了对侧壁的压力,提高了焊接性能。同时,旋转轴部31长度略大于翻边22的厚度,保证焊接后摩擦焊盘与顶板1摩擦焊形成的焊接界面位于顶板1内部,且至少嵌入顶板1的距离d2大于等于2mm,进一步提高其抗剪性能。
63.本技术实施例中纵肋通过上缘的翻边22中部开设连接孔去与顶板摩擦焊固定,焊接位置的中心位于焊盘中心位置,达到实施例1焊缝中心远离腹板21与纵肋转动支点的效果,焊缝远离了该受力敏感区域,焊道承受的应力和应力幅减小,能承担更大的自由协同应变。
64.其次,本技术多个纵向间隔的焊盘形成独立的焊岛,规避了传统角焊缝抗疲劳性能差、裂缝易延伸发展的缺点,且焊岛与焊岛之间通过工件自身刚度形成岛链结构,既利于整体构造的形成,又利用焊岛之间的母材应变,隔断焊岛与焊岛的裂缝发展的概率。进一步的,由于钢桥顶板的顶板为结构受力件,在顶板上开孔会弱化顶板的刚度,本技术实施例1通过摩擦焊盘进行焊接,变传统的纵肋和顶板的端面焊接为面面焊接,使得不需要通过墩厚纵肋腹板上缘、或双面焊等方式来增加焊道截面,通过调节翻边平面宽度及焊盘的尺寸可改变焊接面积和容量,焊接质量更加可控。
65.本技术实施例利用摩擦焊盘作为第三中间体,焊盘旋转焊接,穿过纵肋翻边预开设的孔和顶板底面焊接,避免了在顶板开孔,尤其在钢桥面结构中,顶板1为直接承受载荷的构件,现有顶板1通常为14-18mm厚的钢板,在顶板1开孔会大大弱化其刚度和强度,本技术的实施例采用的远角焊结构无需在顶板开孔,也能有效的解决顶板和纵肋连接的疲劳问题。
66.而且,通过该中间体焊盘,只需输入极小的能量使其旋转,达到将两个大型工件,尤其是长、大、重的工件,以及非圆形的工件焊接的目的,显著拓展了摩擦焊的应用范围,使得该高端焊接工艺应用于桥梁等常用金属构件成为现实。摩擦焊相对于传统熔焊,属于固态焊接,焊接时杂质气孔被打碎挤出,焊缝的初始缺陷是疲劳开裂的主要因素之一,采用摩擦焊,其焊接强度高,抗疲劳性能佳,能有效提高钢桥面的抗疲劳性能。
67.同时,在与传统构造的焊接量对比上,本焊接构造与通用纵肋焊接量按每平米焊缝长度对比为2.19:0.99,折算焊缝长度减少55%。一个直径36mm的焊盘由于嵌入效应其抗剪承载力达450kn以上,抗拉强度超母材强度,传统结构主要因顶板与纵肋焊缝敏感原因,
限制了纵肋效能的发挥,实际上6mm厚的纵肋肋壁,在下部支撑稳定的条件下,其纵肋失稳的极限荷载可达900kn以上。本技术的桥面结构在顶板与纵肋焊缝敏感问题解决之后,纵肋的设计突破了传统结构纵肋高厚比不超过40:1的限制,加上闭口肋两侧的焊缝外移,相邻纵肋之间实际的间距变小,顶板的跨度减小,纵肋能够突破高厚比、长厚比、宽厚比的制约,纵肋2高度与板厚之比突破45:1,使得肋的高度增加、经济性增加,使得更多的截面可用于承担主应力的部位及横隔梁的部位,整个构造的双向的性能趋于平衡和兼顾。
68.如下表所示,6mm板厚的薄壁肋肋高可做到320mm以上,高厚比突破50:1;薄壁高肋与传统纵肋对比,惯性矩有明显提升。当正交异性钢桥面板纵肋肋距增大,一方面带来减少横肋节点、减少焊缝、减少零件数量等优点,纵肋间距增大,较密的横肋间距基本相近时,钢桥面板双向性能接近于双向板,传力更趋均匀。
[0069][0070]
实施例3:
[0071]
如图8所示,本实施例提供了一种钢混组合桥面结构,与实施2的区别在于连接件3为螺栓组件,顶板1开孔,顶板1和纵肋2通过螺栓组件进行固定连接。与实施例2的钢桥面结构不同,组合结构桥面会在顶板1顶面铺设高性能的混凝土层4来增厚顶板,承受载荷,通过螺栓连接,能够增加与混凝土的锚固作用,提高钢板与混凝土的结合强度。
[0072]
实施例4:
[0073]
本实施例与实施例1的去切在于,纵肋2采用开口肋,如图9所示的纵肋2,包括一个一体折弯形成的腹板21和翻边22,腹板21与翻边22的转角α为90
°
,采用了翻边22的开口肋可设计性更强,同时在开口肋的下部具有自翻边的下翼缘24。
[0074]
以上所述是本技术的优选实施方式,对于本领域的普通技术人员来说不脱离本技术原理的前提下,还可以做出若干变型和改进,这些也应视为本技术的保护范围。
再多了解一些
本文用于企业家、创业者技术爱好者查询,结果仅供参考。