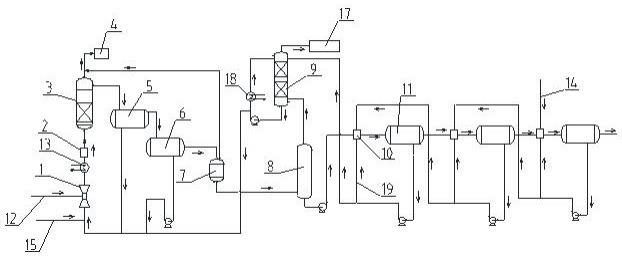
1.本发明属于有机硅生产工艺技术领域,具体涉及一种具有脱吸功能的二甲基二氯硅烷水解工艺。
背景技术:
2.有机硅产品素有“科技发展催化剂”和“工业催化剂”的美誉,应用广泛,发展迅速,其主要为甲基氯硅烷单体制成甲基硅氧烷衍生的系列产品,占有机硅产品总量的90%wt以上。甲基氯硅烷单体主要以二甲基二氯硅烷为主,占比为甲基氯硅烷单体90%wt以上。甲基硅氧烷衍生的系列产品也就是将二甲基二氯硅烷通过水解等技术,转变为上百种化工基础产品,广泛应用于航空航天、电子电气、建筑、运输、化工、纺织、食品、轻工、医疗等行业。水解过程本身就是脱氯过程,产物聚硅氧烷中氯含量理论上为不存在,但因聚硅氧烷与水的密度差很小,很难完全分离,一般要求低于5ppm,氯越低,水解物质量越好,氯资源回收越高,企业环保和经济效益越好。二甲基二氯硅烷经水解形成二甲基聚硅氧烷水解物,其反应方程式为:生成的氯化氢循环用于氯甲烷生产,硅氧烷用盐酸、纯水或碱(钠、钾)洗涤去除水解物油相中的氯,得到杂质含量尽可能低的硅氧烷。生产实践表明,二甲基二氯硅烷水解过程需要尽可能满足以下条件:(1)尽量完全地除去≡si-cl键,提高一级反应效率;(2)产生的hcl尽可能以气相形式且带有压力回收,直接用于氯甲烷合成;(3)聚有机硅氧烷水解产物氯含量尽可能低或不含;(4)生产既不引入新的杂质如碱洗引入钠,也不对外产生废酸排放;(5)水解物分子结构均一性、分子量及其分子量分布稳定,粘度始终处于可控状态,油酸或油水容易分离,不出现乳化或粘稠物堵塞设备。目前,行业主要再对二甲基二氯硅烷进行水解时,还存在成本高、回收率低等诸多的不足,如中国专利“cn201410347205”提出一种平衡状态下的二甲基二氯硅烷浓酸水解工艺,该工艺有效的把握了系统反应的氯元素平衡、水平衡和热量平衡,反应生成的氯化氢以气态形式回收,回收率达99%wt以上,该工艺控制难度大,当后续补充的洗酸含量稍微波动,都会造成系统系统不平衡,同时理论上只能将氯化氢的回收率做到100%wt;又如中国专利“cn201910978705”提出一种反应转化效率高且产品纯度高的有机氯硅烷水解和盐酸精制系统及方法。减压罐内压力控制为微正压,并使用压缩机提压后供氯甲烷使用,水解物采用萃取塔处理。氯化氢夹带一定水分,易造成压缩设备腐蚀,萃取塔属于复杂动设备,投资大,操作难度大;再如中国专利“cn200610113260”提出采用釜式搅拌器、管道混合器及特殊结构的相分离器来提高水解反应速度和分离效率,同时增加脱气及吸收系统,用于解吸一级出来的带压粗水解物中氯化氢气体,形成的低压氯化氢气体并加以吸收,最终聚有机硅氧烷产品的粘度低,氯含量低,没有含盐废水和尽
量少的多余稀酸产生,但工艺过程采用搅拌釜及多个内循环,对二甲反应过程仍达不到充分混合,且设备复杂,不利用过程控制,最终产品只能做到聚有机硅氧烷粘度《100cp,氯含量《500ppmwt;还有中国专利“cn100577713c”提出在水解过程外部加入高浓度盐酸,内部排出低浓度盐酸,可以做到氯化氢回收理论量的104%,但该专利进行对外排酸,仍然增加废水处理费用和难度。因此,研制开发一种工艺路线合理、反应过程可控、氯化氢回收率高、运行成本低的具有脱吸功能的二甲基二氯硅烷水解工艺是客观需要的。
技术实现要素:
3.为了解决背景技术中存在的二甲基二氯硅烷中氯化氢回收效率低,水解过程控制难度大等技术问题,本发明的目的在于提供一种工艺路线合理、反应过程可控、氯化氢回收率高、运行成本低的具有脱吸功能的二甲基二氯硅烷水解工艺。
4.本发明所述的一种具有脱吸功能的二甲基二氯硅烷水解工艺,包括水解反应、脱气处理和多级水洗反应步骤,二甲基二氯硅烷单体与盐酸先经过水解系统的水解混合器混合、解析塔解析分离氯化氢气体、油水分离器分离稀盐酸后,二甲基二氯硅烷水解物在脱气系统中再次分离氯化氢气体,脱气系统分离出的氯化氢气体进入到吸收塔内洗涤吸收,二甲基二氯硅烷水解物再进入多级水洗系统进行多级水洗脱氯,在多级水洗反应步骤的最后一级水洗系统上设置有脱盐水进口,利用从脱盐水进口进入的脱盐水对最后一级水洗系统内的二甲基二氯硅烷水解物进行水洗后形成稀盐酸,形成的稀盐酸依次返回到前几级水洗系统内再次对前几级水洗系统内的二甲基二氯硅烷水解物进行多级水洗,从第一级水洗系统排出的稀盐酸返回到脱气处理步骤的吸收塔内,对进入到吸收塔内的氯化氢气体洗涤吸收后形成浓盐酸,形成的浓盐酸再返回到水解反应步骤的水解混合器内循环使用,在水解系统的水解混合器的入口设置有补酸口,利用补酸口向水解系统外补浓度为31%wt的新鲜盐酸,补充新鲜盐酸带入的水量与最后一级水洗补充的脱盐水水量等于二甲基二氯硅烷水解的理论用水量。
5.进一步的,脱气系统包括第一脱气罐和第二脱气罐,所述解析塔和第一脱气罐分离出的氯化氢气体均进入到氯化氢净化系统内,从第二脱气罐分离出的氯化氢气体进入吸收塔内,经过吸收塔洗涤吸收后,从吸收塔的顶部排出的气体进入碳化系统。优选地,第一脱气罐的工作压力为0.18~0.3mpa,第二脱气罐的工作压力为0.05~0.08mpa,第二脱气罐排出的二甲基二氯硅烷水解物的粘度为10~15cp,氯含量为1~6%wt。
6.进一步的,吸收塔底部排出的浓盐酸浓度需控制在22~31%wt,从吸收塔底部排出的浓盐酸有一部分通过循环管返回到吸收塔内循环使用,循环管上设置有冷凝器,冷凝器内通入-15℃以下冷冻水,利用冷冻水对返回到吸收塔内的浓盐酸进行循环冷凝。
7.进一步的,水解混合器包括第一混合器和第二混合器,补酸口设置在第一混合器的入口端,第一混合器采用文丘里混合器,第二混合器采用管道混合器或静态混合器,第一混合器和第二混合器之间设置有换热器,油水分离器包括预分离器和相分离器,经预分离器和相分离器分离出的稀盐酸也返回到第一混合器内循环使用,解析塔采用填料塔,填料塔内的顶部设置有除沫器,第一混合器上设置有供二甲基二氯硅烷单体与盐酸进入的进料管,从进料管进入到第一混合器内的盐酸浓度为40~47%wt,进入第一混合器内的二甲基二氯硅烷单体与盐酸的体积比为1:15~20,解析塔3的工作压力为0.18~0.30mpa,工作温
度为20~50℃,反应停留时间为80~120min。
8.进一步的,多级水洗反应的水洗级数为3~5级。优选地,多级水洗反应的水洗级数为3级,其中,一级水洗的稀盐酸浓度为10~18%wt,温度为50~85℃,油酸比为1:4~10,一级水洗后的二甲基二氯硅烷水解物的粘度为15~25cp,氯含量为0.5~2.5%wt;二级水洗的稀盐酸浓度为0.05~2%wt,温度为50~85℃,油酸比为1:4~10,二级水洗后的二甲基二氯硅烷水解物的粘度为15~25cp,水解物氯含量为0.02~0.05%wt;三级水洗的稀盐酸浓度为0.02~0.2%wt,温度为50~85℃,油酸比为1:4~10,三级水洗后的二甲基二氯硅烷水解物的粘度为15~25cp,氯含量为1~10ppmwt。
9.本发明产生的的有益效果是:一是先对二甲基二氯硅烷单体进行水解,在水解的工艺过程中,增加了混合的次数和水解的时间,通过强化水解反应,提高水解反应效率,降低水解物中的氯含量,让二甲基二氯硅烷单体中的氯化氢气体能够完全分离,其水解反应的分离效率能够达到97%以上;二是将水解分离出来的二甲基二氯硅烷水解物进行两次脱气处理,经过两次脱气处理后能够彻底的将氯化氢气体分离出来,且分离出来的氯化氢气体能够全部以气相形式且带有压力回收,可直接用于氯甲烷的生产;三是将脱气后的二甲基聚硅氧烷水解物经过多级的稀盐酸水洗后,其油酸或油水比较容易分离,且在水洗的过程中,二甲基聚硅氧烷水解物的粘堵可控,不易存在乳化或粘稠物堵塞的情况,经过多级水洗后得到的目标产品二甲基聚硅氧烷水解物的氯含量较低,另外,最后一级水洗时补充脱盐水,脱盐水的补水量小于用水量,用水量不够时向水解系统补充新鲜盐酸,在能实现水解的同时,又具备脱吸功能。与现有的技术相比,本发明的优点在于,通过对水解、脱气和多级水洗过程中的控制,本发明不仅可以大幅的提高氯化氢的回收率,氯化氢的回收率能够达到102%以上,而且能够有效的控制产品的质量,大幅的降低了二甲基聚硅氧烷水解物的氯含量,可以将二甲基聚硅氧烷水解物的氯含量控制在1~10ppmwt,同时整个反应过程中实现了稀盐酸的循环使用,不存在酸液外排的情况,避免了废水排放和处理难的问题,可有效的降低运行的成本,具有工艺路线合理、反应过程可控、氯化氢回收率高、运行成本低的优点,能够产生较好的经济效益和社会效益,易于推广使用。
附图说明
10.图1为本发明的的工艺流程示意图;图中:1-第一混合器,2-第二混合器,3-解析塔,4-氯化氢净化系统,5-预分离器,6-水解相分离器,7-第一脱气罐,8-第二脱气罐,9-吸收塔,10-水洗混合器,11-水洗相分离器,12-进料管,13-换热器,14-脱盐水进口,15-补酸口,17-碳化系统,18-冷凝器,19-旁通管。
具体实施方式
11.下面结合实施例和附图说明对本发明作进一步的说明,但不以任何方式对本发明加以限制,基于本发明教导所作的任何变换或替换,均实施例属于本发明的保护范围。
12.实施例1本实施例1所述的具有脱吸功能的二甲基二氯硅烷水解工艺,包括水解反应、脱气处理和多级水洗反应步骤,二甲基二氯硅烷单体与盐酸先经过水解系统的水解混合器混
合、解析塔3解析分离氯化氢气体、油水分离器分离稀盐酸后,二甲基二氯硅烷水解物在脱气系统中再次分离氯化氢气体,脱气系统分离出的氯化氢气体进入到吸收塔9内洗涤吸收,二甲基二氯硅烷水解物再进入多级水洗系统进行多级水洗脱氯,在多级水洗反应步骤的最后一级水洗系统上设置有脱盐水进口14,利用从脱盐水进口14进入的脱盐水对最后一级水洗系统内的二甲基二氯硅烷水解物进行水洗后形成稀盐酸,形成的稀盐酸依次返回到前几级水洗系统内再次对前几级水洗系统内的二甲基二氯硅烷水解物进行多级水洗,从第一级水洗系统排出的稀盐酸返回到脱气处理步骤的吸收塔9内,对进入到吸收塔9内的氯化氢气体洗涤吸收后形成浓盐酸,形成的浓盐酸再返回到水解反应步骤的水解混合器内循环使用,在水解系统的水解混合器的入口设置有补酸口15,利用补酸口15向水解系统外补浓度为31%wt的新鲜盐酸,补充新鲜盐酸带入的水量与最后一级水洗补充的脱盐水水量等于二甲基二氯硅烷水解的理论用水量,脱盐水水洗形成后形成的稀盐酸在循环使用的过程中,其补水量小于用水量,向水解系统外补新鲜盐酸,可以对整个系统进行补水,这样既能实现二甲基二氯硅的高效水解,又能实现氯化氢的高效脱吸分离。
13.具体地,本实施例1中水解反应、脱气处理和多级水洗反应的具体工艺流程如下:
①
水解反应:将硅粉和氯甲烷合成工艺中产生的二甲基二氯硅烷单体与盐酸依次送入水解混合器内混合后进入到解析塔3内,水解混合器包括第一混合器1和第二混合器2,第一混合器1采用文丘里混合器,第二混合器2采用管道混合器或静态混合器,第一混合器1上设置有供二甲基二氯硅烷单体与盐酸进入的进料管12,从进料管12进入到第一混合器1内的盐酸浓度为40%wt,进入第一混合器1内的二甲基二氯硅烷单体与盐酸的体积比为1:15,二甲基二氯硅烷的进料量为14600kg/h,第一混合器1和第二混合器2之间设置有换热器13,利用换热器13可以对第二混合器2内物料的温度进行控制,所述解析塔3采用填料塔,填料塔内的填料可以采用现有技术中使用的鲍尔环填料,填料塔内的顶部设置有除沫器,在解析塔3内实现氯化氢气体和二甲基聚硅氧烷的分离,解析塔3的工作压力为0.18mpa,工作温度为20℃,反应停留时间为80min,分离出的氯化氢气体从解析塔3的顶部排出后进入到氯化氢净化系统4,氯化氢气体经过净化后,直接供氯甲烷合成使用,分离出的二甲基聚硅氧烷水解物从解析塔3的塔侧排出进入油水分离器进行油酸分离,油水分离器包括预分离器5和相分离器6,经预分离器5和相分离器6分离出的稀盐酸也返回到第一混合器1内循环使用,分离后的二甲基聚硅氧烷水解物需进行脱气处理;
②
脱气处理:将水解相分离器6脱出的二甲基聚硅氧烷水解物引入到第一脱气罐7内所述第一脱气罐7的工作压力为0.18mpa,从第一脱气罐7顶部排出的氯化氢气体进入到氯化氢净化系统4,从第一脱气罐7底部排出的二甲基聚硅氧烷水解物进入到第二脱气罐8内,第二脱气罐8的工作压力为0.05mpa,第二脱气罐8将二甲基聚硅氧烷的压力降低至微正压,脱出因压力变化产生的氯化氢气体,从第二脱气罐8顶部排出的氯化氢气体进入到吸收塔9内利用稀盐酸进行洗涤吸收,进入吸收塔9内的氯化氢气体与稀盐酸进行逆流接触后,从吸收塔9的顶部排出的气体进入碳化系统17,而从吸收塔9底部排出的浓盐酸有一部分通过循环管返回到吸收塔9内循环使用,从吸收塔9底部排出的浓盐酸浓度需控制在22%wt,循环管上设置有冷凝器18,冷凝器18内通入-15℃以下冷冻水,利用冷冻水对返回到吸收塔9内的浓盐酸进行循环冷凝,另一部分返回到第一混合器1内循环使用,而从第二脱气罐8底部排出的二甲基聚硅氧烷水解物则需进行多级水洗,第二脱气罐8排出的二甲基二氯硅烷
水解物的粘度为10cp,氯含量为1%wt;
③
多级水洗反应:多级水洗反应的每级水洗系统均包括水洗混合器10和水洗相分离器11,水洗混合器10采用管道式混合器、搅拌釜混合或静态混合器,水洗混合器10的工作压力为常压,多级水洗的过程是先将从第二脱气罐8排出的二甲基聚硅氧烷水解物与第二级水洗相分离器11排出的稀盐酸在第一级水洗混合器10混合后,再送入到第一级水洗相分离器11内进行油水分离,第一级水洗相分离器11分离出的稀盐酸一部分通过旁通管19返回到第一级水洗混合器10内循环使用,另一部分返回到吸收塔9内使用,而第一级水洗相分离器11分离出来的二甲基聚硅氧烷水解物再次与第三级水洗相分离器11排出稀盐酸按照上述方法进行多级混合、分离后即可得到粘度更低、含氯量更低的二甲基聚硅氧烷水解物,脱盐水进口14设置在最后一级水洗系统的水洗混合器10上,最后一级水洗系统采用脱盐水对二甲基聚硅氧烷水解物进行水洗,脱盐水对最后一级水洗系统内的二甲基二氯硅烷水解物进行水洗后形成稀盐酸,再依次返回到上几级水洗系统、吸收塔9和水解系统循环使用后,其脱盐水的补水量会小于用水量,整个系统不够的水量就利用补酸口15向水解系统外补浓度为31%wt的新鲜盐酸,让其进入到水解系统,以维持整个的系统平衡,多级水洗反应的水洗级数为3~5级,优选地多级水洗反应的水洗级数为3级,其中,返回到一级水洗的稀盐酸浓度为10,温度为50℃,油酸比为1:4,一级水洗后的二甲基二氯硅烷水解物的粘度为15cp,氯含量为0.5%wt;二级水洗的稀盐酸浓度为0.05%wt,温度为50℃,油酸比为1:4,二级水洗后的二甲基二氯硅烷水解物的粘度为15cp,水解物氯含量为0.02%wt;三级水洗的稀盐酸浓度为0.02%wt,温度为50℃,油酸比为1:4,三级水洗后的二甲基二氯硅烷水解物的粘度为15cp,氯含量为1ppmwt。
14.本实施例1不仅可以大幅的提高氯化氢的回收率,氯化氢的回收率能够达到102.42%,而且能够有效的控制目标产品二甲基二氯硅烷水解物的质量,可大幅降低二甲基二氯硅烷水解物的氯含量,将二甲基二氯硅烷水解物的氯含量控制在1ppmwt,二甲基二氯硅烷水解物的粘度为15cp,同时整个反应过程中实现了稀盐酸的循环使用,不存在酸液外排的情况,避免了废水排放和处理难的问题,可有效的降低运行的成本,能够产生良好的经济效益和社会效益。
15.实施例2本实施例2所述的具有脱吸功能的二甲基二氯硅烷水解工艺,包括水解反应、脱气处理和多级水洗反应步骤,二甲基二氯硅烷单体与盐酸先经过水解系统的水解混合器混合、解析塔3解析分离氯化氢气体、油水分离器分离稀盐酸后,二甲基二氯硅烷水解物在脱气系统中再次分离氯化氢气体,脱气系统分离出的氯化氢气体进入到吸收塔9内洗涤吸收,二甲基二氯硅烷水解物再进入多级水洗系统进行多级水洗脱氯,在多级水洗反应步骤的最后一级水洗系统上设置有脱盐水进口14,利用从脱盐水进口14进入的脱盐水对最后一级水洗系统内的二甲基二氯硅烷水解物进行水洗后形成稀盐酸,形成的稀盐酸依次返回到前几级水洗系统内再次对前几级水洗系统内的二甲基二氯硅烷水解物进行多级水洗,从第一级水洗系统排出的稀盐酸返回到脱气处理步骤的吸收塔9内,对进入到吸收塔9内的氯化氢气体洗涤吸收后形成浓盐酸,形成的浓盐酸再返回到水解反应步骤的水解混合器内循环使用,在水解系统的水解混合器的入口设置有补酸口15,利用补酸口15向水解系统外补浓度为31%wt的新鲜盐酸,补充新鲜盐酸带入的水量与最后一级水洗补充的脱盐水水量等于二
甲基二氯硅烷水解的理论用水量,脱盐水水洗形成后形成的稀盐酸在循环使用的过程中,其补水量小于用水量,向水解系统外补新鲜盐酸,可以对整个系统进行补水,既能实现二甲基二氯硅的高效水解,又能实现氯化氢的高效脱吸。
16.具体地,本实施例2中水解反应、脱气处理和多级水洗反应的具体工艺流程如下:
①
水解反应:将硅粉和氯甲烷合成工艺中产生的二甲基二氯硅烷单体与盐酸依次送入水解混合器内混合后进入到解析塔3内,水解混合器包括第一混合器1和第二混合器2,第一混合器1采用文丘里混合器,第二混合器2采用管道混合器或静态混合器,第一混合器1上设置有供二甲基二氯硅烷单体与盐酸进入的进料管12,从进料管12进入到第一混合器1内的盐酸浓度为45%wt,进入第一混合器1内的二甲基二氯硅烷单体与盐酸的体积比为1:18,二甲基二氯硅烷的进料量为14600kg/h,第一混合器1和第二混合器2之间设置有换热器13,利用换热器13可以对第二混合器2内物料的温度进行控制,所述解析塔3采用填料塔,填料塔内的填料可以采用现有技术中使用的鲍尔环填料,填料塔内的顶部设置有除沫器,在解析塔3内实现氯化氢气体和二甲基聚硅氧烷的分离,解析塔3的工作压力为0.23mpa,工作温度为42℃,反应停留时间为105min,分离出的氯化氢气体从解析塔3的顶部排出后进入到氯化氢净化系统4,氯化氢气体经过净化后,直接供氯甲烷合成使用,分离出的二甲基聚硅氧烷从解析塔3的塔侧排出进入油水分离器进行油酸分离,油水分离器包括预分离器5和相分离器6,经预分离器5和相分离器6分离出的稀盐酸也返回到第一混合器1内循环使用,分离后的二甲基聚硅氧烷水解物需进行脱气处理;
②
脱气处理:将水解相分离器6脱出的二甲基聚硅氧烷引入到第一脱气罐7内所述第一脱气罐7的工作压力为0.23mpa,从第一脱气罐7顶部排出的氯化氢气体进入到氯化氢净化系统4,从第一脱气罐7底部排出的二甲基聚硅氧烷水解物进入到第二脱气罐8内,第二脱气罐8的工作压力为0.06mpa,第二脱气罐8将二甲基聚硅氧烷的压力降低至微正压,脱出因压力变化产生的氯化氢气体,从第二脱气罐8顶部排出的氯化氢气体进入到吸收塔9内利用稀盐酸进行洗涤吸收,进入吸收塔9内的氯化氢气体与稀盐酸进行逆流接触后,从吸收塔9的顶部排出的气体进入碳化系统17,而从吸收塔9底部排出的浓盐酸有一部分通过循环管返回到吸收塔9内循环使用,从吸收塔9底部排出的浓盐酸浓度需控制在25%wt,循环管上设置有冷凝器18,冷凝器18内通入-15℃以下冷冻水,利用冷冻水对返回到吸收塔9内的浓盐酸进行循环冷凝,另一部分返回到第一混合器1内循环使用,而从第二脱气罐8底部排出的二甲基聚硅氧烷水解物则需进行多级水洗,第二脱气罐8排出的二甲基二氯硅烷水解物的粘度为12cp,氯含量为3%wt;
③
多级水洗反应:多级水洗反应的每级水洗系统均包括水洗混合器10和水洗相分离器11,水洗混合器10采用管道式混合器、搅拌釜混合或静态混合器,水洗混合器10的工作压力为常压,多级水洗的过程是先将从第二脱气罐8排出的二甲基聚硅氧烷水解物与第二级水洗相分离器11排出的稀盐酸在第一级水洗混合器10混合后,再送入到第一级水洗相分离器11内进行油水分离,第一级水洗相分离器11分离出的稀盐酸一部分通过旁通管19返回到第一级水洗混合器10内循环使用,另一部分返回到吸收塔9内使用,而第一级水洗相分离器11分离出来的二甲基聚硅氧烷水解物再次与第三级水洗相分离器11排出稀盐酸按照上述方法进行多级混合、分离后即可得到粘度更低、含氯量更低的二甲基聚硅氧烷水解物,脱盐水进口14设置在最后一级水洗系统的水洗混合器10上,最后一级水洗系统采用脱盐水对
二甲基聚硅氧烷水解物进行水洗,脱盐水对最后一级水洗系统内的二甲基二氯硅烷水解物进行水洗后形成稀盐酸,再依次返回到上几级水洗系统、吸收塔9和水解系统循环使用后,其脱盐水的补水量会小于用水量,整个系统不够的水量就利用补酸口15向水解系统外补浓度为31%wt的新鲜盐酸,让其进入到水解系统,以维持整个的系统平衡,多级水洗反应的水洗级数为3~5级,优选地多级水洗反应的水洗级数为3级,其中,一级水洗的稀盐酸浓度为14.49%wt,温度为60℃,油酸比为1:5,一级水洗后的二甲基二氯硅烷水解物的粘度为22.1cp,氯含量为0.5%wt;二级水洗的稀盐酸浓度为1.12%wt,温度为60℃,油酸比为1:5,二级水洗后的二甲基二氯硅烷水解物的粘度为23.1cp,水解物氯含量为0.04%wt;三级水洗的稀盐酸浓度为1%wt,温度为50℃,油酸比为1:5,三级水洗后的二甲基二氯硅烷水解物的粘度为24cp,氯含量为5ppmwt。
17.本实施例2不仅可以大幅的提高氯化氢的回收率,氯化氢的回收率能够达到102.51%,而且能够有效的控制目标产品二甲基二氯硅烷水解物的质量,可大幅降低二甲基二氯硅烷水解物的氯含量,将二甲基二氯硅烷水解物的氯含量控制在5ppmwt,二甲基二氯硅烷水解物的粘度为24cp,同时整个反应过程中实现了稀盐酸的循环使用,不存在酸液外排的情况,避免了废水排放和处理难的问题,可有效的降低运行的成本,能够产生良好的经济效益和社会效益。
18.实施例3本实施例3所述的具有脱吸功能的二甲基二氯硅烷水解工艺,包括水解反应、脱气处理和多级水洗反应步骤,二甲基二氯硅烷单体与盐酸先经过水解系统的水解混合器混合、解析塔3解析分离氯化氢气体、油水分离器分离稀盐酸后,二甲基二氯硅烷水解物在脱气系统中再次分离氯化氢气体,脱气系统分离出的氯化氢气体进入到吸收塔9内洗涤吸收,二甲基二氯硅烷水解物再进入多级水洗系统进行多级水洗脱氯,在多级水洗反应步骤的最后一级水洗系统上设置有脱盐水进口14,利用从脱盐水进口14进入的脱盐水对最后一级水洗系统内的二甲基二氯硅烷水解物进行水洗后形成稀盐酸,形成的稀盐酸依次返回到前几级水洗系统内再次对前几级水洗系统内的二甲基二氯硅烷水解物进行多级水洗,从第一级水洗系统排出的稀盐酸返回到脱气处理步骤的吸收塔9内,对进入到吸收塔9内的氯化氢气体洗涤吸收后形成浓盐酸,形成的浓盐酸再返回到水解反应步骤的水解混合器内循环使用,在水解系统的水解混合器的入口设置有补酸口15,利用补酸口15向水解系统外补浓度为31%wt的新鲜盐酸,补充新鲜盐酸带入的水量与最后一级水洗补充的脱盐水水量等于二甲基二氯硅烷水解的理论用水量,脱盐水水洗形成后形成的稀盐酸在循环使用的过程中,其补水量小于用水量,向水解系统外补新鲜盐酸,可以对整个系统进行补水,既能实现二甲基二氯硅的高效水解,又能实现氯化氢的高效脱吸。
19.具体地,本实施例3中水解反应、脱气处理和多级水洗反应的具体工艺流程如下:
①
水解反应:将硅粉和氯甲烷合成工艺中产生的二甲基二氯硅烷单体与盐酸依次送入水解混合器内混合后进入到解析塔3内,水解混合器包括第一混合器1和第二混合器2,第一混合器1采用文丘里混合器,第二混合器2采用管道混合器或静态混合器,第一混合器1上设置有供二甲基二氯硅烷单体与盐酸进入的进料管12,从进料管12进入到第一混合器1内的盐酸浓度为47%wt,进入第一混合器1内的二甲基二氯硅烷单体与盐酸的体积比为1:20,二甲基二氯硅烷的进料量为14600kg/h,第一混合器1和第二混合器2之间设置有换热器
13,利用换热器13可以对第二混合器2内物料的温度进行控制,所述解析塔3采用填料塔,填料塔内的填料可以采用现有技术中使用的鲍尔环填料,填料塔内的顶部设置有除沫器,在解析塔3内实现氯化氢气体和二甲基聚硅氧烷的分离,解析塔3的工作压力为0.30mpa,工作温度为50℃,反应停留时间为120min,分离出的氯化氢气体从解析塔3的顶部排出后进入到氯化氢净化系统4,氯化氢气体经过净化后,直接供氯甲烷合成使用,分离出的二甲基聚硅氧烷从解析塔3的塔侧排出进入油水分离器进行油酸分离,油水分离器包括预分离器5和相分离器6,经预分离器5和相分离器6分离出的稀盐酸也返回到第一混合器1内循环使用,分离后的二甲基聚硅氧烷水解物需进行脱气处理;
②
脱气处理:将水解相分离器6脱出的二甲基聚硅氧烷引入到第一脱气罐7内所述第一脱气罐7的工作压力为0.3mpa,从第一脱气罐7顶部排出的氯化氢气体进入到氯化氢净化系统4,从第一脱气罐7底部排出的二甲基聚硅氧烷水解物进入到第二脱气罐8内,第二脱气罐8的工作压力为0.08mpa,第二脱气罐8将二甲基聚硅氧烷的压力降低至微正压,脱出因压力变化产生的氯化氢气体,从第二脱气罐8顶部排出的氯化氢气体进入到吸收塔9内利用稀盐酸进行洗涤吸收,进入吸收塔9内的氯化氢气体与稀盐酸进行逆流接触后,从吸收塔9的顶部排出的气体进入碳化系统17,而从吸收塔9底部排出的浓盐酸有一部分通过循环管返回到吸收塔9内循环使用,从吸收塔9底部排出的浓盐酸浓度需控制在31%wt,循环管上设置有冷凝器18,冷凝器18内通入-15℃以下冷冻水,利用冷冻水对返回到吸收塔9内的浓盐酸进行循环冷凝,另一部分返回到第一混合器1内循环使用,而从第二脱气罐8底部排出的二甲基聚硅氧烷水解物则需进行多级水洗,第二脱气罐8排出的二甲基二氯硅烷水解物的粘度为15cp,氯含量为6%wt;
③
多级水洗反应:多级水洗反应的每级水洗系统均包括水洗混合器10和水洗相分离器11,水洗混合器10采用管道式混合器、搅拌釜混合或静态混合器,水洗混合器10的工作压力为常压,多级水洗的过程是先将从第二脱气罐8排出的二甲基聚硅氧烷水解物与第二级水洗相分离器11排出的稀盐酸在第一级水洗混合器10混合后,再送入到第一级水洗相分离器11内进行油水分离,第一级水洗相分离器11分离出的稀盐酸一部分通过旁通管19返回到第一级水洗混合器10内循环使用,另一部分返回到吸收塔9内使用,而第一级水洗相分离器11分离出来的二甲基聚硅氧烷水解物再次与第三级水洗相分离器11排出稀盐酸按照上述方法进行多级混合、分离后即可得到粘度更低、含氯量更低的二甲基聚硅氧烷水解物,脱盐水进口14设置在最后一级水洗系统的水洗混合器10上,最后一级水洗系统采用脱盐水对二甲基聚硅氧烷水解物进行水洗,脱盐水对最后一级水洗系统内的二甲基二氯硅烷水解物进行水洗后形成稀盐酸,再依次返回到上几级水洗系统、吸收塔9和水解系统循环使用后,其脱盐水的补水量会小于用水量,整个系统不够的水量就利用第二补酸口16向吸收塔内外补浓度为31%wt的新鲜盐酸,让其以充足的水量进入到水解系统,以维持整个的系统平衡,多级水洗反应的水洗级数为3~5级,优选地多级水洗反应的水洗级数为3级,其中,一级水洗的稀盐酸浓度为18%wt,温度为85℃,油酸比为1:10,一级水洗后的二甲基二氯硅烷水解物的粘度为18.9cp,氯含量为2.5%wt;二级水洗的稀盐酸浓度为2%wt,温度为85℃,油酸比为1:10,二级水洗后的二甲基二氯硅烷水解物的粘度为23.7cp,水解物氯含量为0.05%wt;三级水洗的稀盐酸浓度为0.2%wt,温度为85℃,油酸比为1:10,三级水洗后的二甲基二氯硅烷水解物的粘度为25cp,氯含量为10ppmwt。
20.本实施例3不仅可以大幅的提高氯化氢的回收率,氯化氢的回收率能够达到103.35%,而且能够有效的控制目标产品二甲基二氯硅烷水解物的质量,可大幅降低二甲基二氯硅烷水解物的氯含量,将二甲基二氯硅烷水解物的氯含量控制在10ppmwt,二甲基二氯硅烷水解物的粘度为25cp,同时整个反应过程中实现了稀盐酸的循环使用,不存在酸液外排的情况,避免了废水排放和处理难的问题,可有效的降低运行的成本,能够产生良好的经济效益和社会效益。
再多了解一些
本文用于企业家、创业者技术爱好者查询,结果仅供参考。