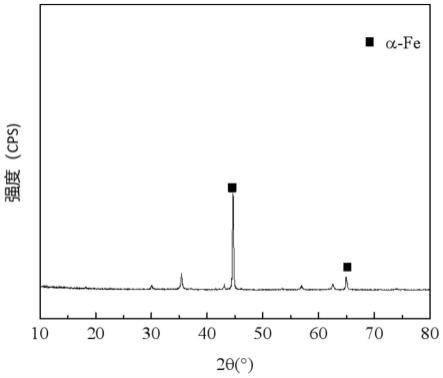
α-fe在煤直接液化中的应用以及煤直接液化的方法
技术领域
1.本发明涉及煤化工及清洁能源技术领域,具体涉及α-fe在煤直接液化中的应用以及煤直接液化的方法。
背景技术:
2.我国煤炭资源丰富,利用煤炭液化制油可以减少原油对外依存度。目前煤直接液化工艺主要分为单反应器液化工艺和多反应器液化工艺(通常是双反应器)。一般来说,单反应器液化工艺的工艺流程短,操作简单,但是可能导致煤液化加氢深度不足,尤其是煤大分子向沥青质转化后其进一步加氢解聚受到限制。双反应器液化工艺相对延长了物料停留时间并加强了煤浆、氢气、催化剂之间的接触,对煤大分子加氢解聚的效果更好,有利于提高煤的整体液化性能。然而,双反应器工艺通常采用两个以完全相同的条件进行液化反应的反应器串联组成,主要目的在于延长反应时间,从而提高加氢深度。而对于低阶煤来说,尤其是高含氧褐煤等高反应活性煤中赋存大量的弱稳定结构,例如羧基、醚键、甲氧基、乙基等,这些结构在300-400℃时会发生显著分解并产生大量自由基,在此阶段煤的大分子结构也逐渐解聚,从而产生以聚合芳烃为主的沥青质。因此,对于低阶煤而言,煤液化温度应更加缓和,过快的升温速率和长时间的高温液化反应可能导致反应过度从而造成结焦,不仅降低了煤液化的转化率,而且还对设备产生不利影响,缩短了设备的运行周期。
3.此外,现有的煤直接液化催化剂通常以铁基催化剂为主,主要通过降低催化剂粒径,提高分散度来提高催化剂活性,降低催化剂用量。但是这些催化剂局限于铁元素衍生物种的催化活性,对芳环的加氢效果还有待提高。另外,现有煤直接液化铁基催化剂,,一般需要过量硫元素的添加以保证形成磁黄铁矿活性相才能发挥催化作用,过量的硫元素无疑增加了液化主要产物油品及液化残渣中的硫含量,这对油品精制及液化残渣的进一步利用如气化、热解及液化残渣制备沥青等产生不利影响。
技术实现要素:
4.本发明的目的是为了克服现有技术存在的现有煤直接液化催化剂的加氢效果有待提高且需要(额外添加的)硫元素配合,同时现有煤直接液化方法的加氢深度仍有不足等问题,提供α-fe在煤直接液化中的应用以及煤直接液化的方法。本发明提供的技术方案中,以α-fe为催化剂催化煤直接液化反应,且在使用α-fe时无需添加硫元素,同时配合本发明提供的煤直接液化方法,能够进一步有效促进低阶煤的液化转化,提高其液化转化率和油产率,防止高温过度反应的结焦问题,延长了反应运行周期。
5.为了实现上述目的,本发明一方面提供α-fe在煤直接液化中的应用,其中,α-fe在煤直接液化过程中用作液化反应催化剂。
6.本发明第二方面提供一种煤直接液化的方法,其特征在于,所述方法包括将油煤浆在液化反应条件下进行液化,其中,所述油煤浆包括煤、催化剂和溶剂,所述催化剂为如前所述的煤直接液化催化剂。
7.通过上述技术方案,本发明能够取得如下有益效果:
8.(1)本发明提供的煤直接液化催化剂(α-fe)的制备方法简单,催化活性高,该催化剂有利于芳环加氢,促进煤大分子结构加氢解聚,促进沥青质向油转化,从而提高了煤液化转化率和油产率。
9.(2)本发明提供的煤直接液化催化剂无需(额外添加的)硫的配合,在使用过程中减少了硫的添加,从而降低了液化残渣的硫含量,有利于液化残渣的进一步利用,同时还减少了气相产物中的硫化氢等含硫气体的含量,减少了含硫气体对环境、设备、人员的伤害,还降低了尾气处理成本。同时,降低了油品中的硫化合物含量,从而有利于油品的进一步精制。
10.(3)本发明提供的煤直接液化催化剂配合本发明的优选煤液化方法,能够防止煤液化高温过度反应结焦,尤其适合低阶煤液化使用。
附图说明
11.图1是实施例1中获得的α-fe的xrd图。
12.图2是实施例1中的液化残渣的xrd图。
具体实施方式
13.在本文中所披露的范围的端点和任何值都不限于该精确的范围或值,这些范围或值应当理解为包含接近这些范围或值的值。对于数值范围来说,各个范围的端点值之间、各个范围的端点值和单独的点值之间,以及单独的点值之间可以彼此组合而得到一个或多个新的数值范围,这些数值范围应被视为在本文中具体公开。
14.本发明的发明人在研究的过程中巧妙地发现,采用α-fe作为液化反应催化剂用于煤直接液化中时,有利于芳环加氢,促进煤大分子结构加氢解聚,促进沥青质向油转化,从而提高煤液化转化率和油产率。而且,采用α-fe作为催化剂还无需添加硫元素配合,减少了煤液化过程的硫添加含量,降低了液化产品油和液化残渣中的硫含量,缓解油品精制条件苛刻度,提高了液化残渣的利用率如气化、热解及液化残渣制备沥青等,提升了煤直接液化工艺整体经济性。,。
15.基于上述发现,本发明一方面提供α-fe在煤直接液化中的应用,其中,α-fe在煤直接液化过程中用作液化反应催化剂。
16.为了提高α-fe的分散性,进而提高在煤直接液化反应中α-fe的催化活性,根据本发明的优选实施方式,其中,所述α-fe的粒径为0.01-1μm,优选为0.05-0.1μm。
[0017]“α-fe”是指通过铁氧化物的原位还原反应生成的α构型fe单质,本发明中用作液化反应催化剂的α-fe可以是商购获得的具有上述特征的α-fe产品,也可以是根据现有技术自行制备获得的相关产品。
[0018]
本发明对于制备所述α-fe的方法没有特别限制。根据本发明的一种优选实施方式,其中,所述α-fe的制备方法包括:在还原性气体存在下,将铁氧化物和供氢溶剂混合并进行还原反应。
[0019]
根据本发明的优选实施方式,其中,所述还原性气体选自h2和/或co,优选为h2。
[0020]
根据本发明的优选实施方式,其中,所述铁氧化物选自γ-fe2o3、α-fe2o3和fe3o4中
的至少一种,优选为γ-fe2o3和/或α-fe2o3。
[0021]
优选地,所述铁氧化物的粒径为0.01-1μm,优选为0.05-0.1μm。
[0022]
根据本发明的优选实施方式,其中,所述供氢溶剂选自四氢萘、十氢萘、二氢蒽、二氢菲和二氢芘中的至少一种,优选为四氢萘和/或十氢萘。
[0023]
本发明提供的制备方法中,对于原料的用量比没有特别限制。为了保证还原反应完全,优选地,所述铁氧化物与供氢溶剂的体积比为1:1-10,优选为1:2-8。
[0024]
根据本发明的优选实施方式,其中,所述还原反应的条件包括:初始压力2-8mpa,反应温度300-450℃,升温速率20-100℃/min,反应时间20-80min(反应时间从达到反应温度时开始计算,后同)。
[0025]
优选地,所述还原反应的条件包括:初始压力4-6mpa,反应温度380-420℃,升温速率50-80℃/min,反应时间30-60min。
[0026]
优选地,所述方法还包括对反应产物进行固液分离和干燥。
[0027]
本发明中对于所述固液分离的方式没有特别限制。根据本发明的一种优选实施方式,其中,所述固液分离的方式选自过滤和/或离心。
[0028]
优选地,所述固液分离的条件使得获得的固相中的液体含量不超过5重量%,优选为1-3重量%。
[0029]
本发明中对于所述干燥的方式没有特别限制。根据本发明的一种优选实施方式,其中,所述干燥的方式包括真空干燥和/或氮气干燥。
[0030]
根据本发明的优选实施方式,其中,所述干燥的条件使得干燥产物中的液体含量不超过1重量%,优选为0.1-0.5重量%。
[0031]
优选地,所述干燥的条件包括温度105-120℃,真空度0至-0.1mpa。
[0032]
本发明的发明人在研究中还发现,以α-fe为催化剂进行煤直接液化反应时,采用低阶煤(主要特征包括含氧量高、反应活性高、含有大量弱稳定结构、易分解、液化反应温度过高时易过度反应产生结焦等)作为原料时也能获得较好的液化效果,同时还能减少结焦,延长反应器运行周期。
[0033]
根据本发明的优选实施方式,其中,所述煤直接液化的原料选自低阶煤,优选为煤化程度较低的烟煤,次烟煤及褐煤中的至少一种。煤化程度是指从泥炭到无烟煤的变化程度,通常可以通过挥发分进行判断。
[0034]
优选地,所述煤的挥发分(v
daf
)≥35重量%。更优选所述煤的挥发分在35-50重量%范围内。
[0035]
优选地,所述煤的水分(m
ad
)≤7重量%。更优选所述煤的水分在2-6重量%范围内。
[0036]
优选地,所述煤的灰分(ad)≤15重量%。更优选所述煤的灰分在5-12重量%范围内。
[0037]
优选地,所述煤的固定碳(fc
daf
)≥50重量%。更优选所述煤的固定碳在55-65重量%。
[0038]
通常可以通过煤的工业分析(具体可参考gb/t 212-2008)确定煤样的挥发分、水分、灰分和固定碳等成分含量。
[0039]
优选地,所述煤的粒度不超过0.15mm,优选不超过0.075mm(即可通过200目筛)。
[0040]
本发明第二方面提供一种煤直接液化的方法,所述方法包括将油煤浆在液化反应
条件下进行液化,其中,所述油煤浆包括煤、催化剂和溶剂,所述催化剂包括α-fe。所述α-fe的参数与制备方法如前所述,在此不再赘述。
[0041]
根据本发明的优选实施方式,所述催化剂中,α-fe的含量≥95重量%、98重量%、99重量%,最优选=100重量%。
[0042]
根据本发明的优选实施方式,其中,所述液化反应体系中的s含量取决于采用的煤中所含的s元素含量。也即,本发明提供的方法中的液化反应体系中不含故意添加的s元素。
[0043]
根据本发明的优选实施方式,其中,所述煤选自煤化程度较低的烟煤,次烟煤及褐煤。所述煤的具体特征如前所述,在此不再赘述。
[0044]
为了提高煤与催化剂的接触,从而提高活性,降低催化剂用量,优选地,所述煤为粒径不超过0.15mm的煤粉,优选所述煤粉的粒径不超过0.075mm。
[0045]
根据本发明的优选实施方式,其中,所述溶剂选自四氢萘和/或十氢萘。
[0046]
优选地,所述油煤浆中,催化剂含量占干燥无灰基煤重量的1-5重量%,优选为2-3重量%。
[0047]
优选地,所述煤油浆中,煤与溶剂用量比(w/v,单位为g/ml)为30-50:70-50,优选为35-45:65-55。
[0048]
本发明的发明人在研究中还发现,采用本发明提供的煤液化方法,以α-fe作为催化剂的同时,配合特定的反应方式/条件时,能够获得更好的反应效果(例如转化率/油收率提高等)。根据本发明的优选实施方式,其中,所述液化反应条件包括:温度420-480℃,压力4-20mpa,反应时间10-60min,升温速率10-50℃/min。
[0049]
为了进一步提高煤液化反应的转化率,根据本发明的一种优选实施方式,其中,所述液化采用分段液化的方式进行,优选所述分段液化的方式包括:
[0050]
低温液化阶段:温度360-430℃,压力5-20mpa,反应时间20-50min,升温速率20-40℃/min;
[0051]
高温液化阶段:温度400-470℃,压力10-25mpa,反应时间20-50min升温速率20-40℃/min。
[0052]
优选地,所述分段液化的方式包括:
[0053]
更优选地,所述高温液化阶段的反应温度比低温液化的反应温度高50-80℃,优选高60-70℃;
[0054]
更优选地,所述高温液化阶段的反应压力比低温液化阶段的反应压力高5-10mpa,优选高6-8mpa。
[0055]
根据本发明的一种实施方式,所述方法中采用的催化剂为通过前述方法制备获得的α-fe。
[0056]
以下将通过实施例对本发明进行详细描述。应当能够理解的是,以下实施例仅用于示例性地进一步解释和说明本发明的内容,而不用于限制本发明。
[0057]
以下实施例中,α-fe2o3(粒径为30nm)、γ-fe2o3(粒径为30nm)和fe2o3(粒径为1μm)均购自上海麦克林生化科技有限公司。未作特殊说明的情况下,以下实施例中采用的试剂均为购自正规化学试剂供应商的市售品,纯度为分析纯。
[0058]
以下实施例中,未作特殊说明的情况下,操作温度均为室温(25
±
5℃)。
[0059]
参考gb/t 212-2008,对以下实施例采用的煤样进行工业分析和元素分析,具体检
测结果如下表1所示。
[0060]
表1煤样工业分析和元素分析
[0061][0062]
实施例1
[0063]
取10重量份α-fe2o3和40重量份四氢萘和加入高压反应釜中,通入氢气至釜内初始压力为4mpa,设定反应温度400℃并以50℃/min的升温速率升温至设定温度,反应时间为45min,反应完成后关闭加热,待温度冷却至室温,取出反应釜中的固体并采用四氢呋喃洗涤后过滤、真空干燥(105℃,48h,真空度-0.1mpa,液体含量0.5重量%),即获得α-fe催化剂(其中α-fe含量为99.5重量%)。
[0064]
采用红柳林煤进行煤液化反应,具体方法如下:
[0065]
将煤粉(过200目筛,粒径约0.075mm)、催化剂(α-fe)和溶剂(四氢萘)按照40:1:60(w/w/v,单位g/g/ml,其中催化剂与煤粉的用量比干燥无灰基煤计算)的比例配制成油煤浆,按照以下条件进行两段液化反应:
[0066]
低温液化阶段:将油煤浆通入第一反应器中,以20℃/min的升温速率升温至反应温度400℃,反应压力10mpa,反应时间30min。反应完成后物料经分离器将轻油和水分离,获得液固物料。
[0067]
高温液化阶段:将液固物料通入第二反应器中,以35℃/min的升温速率升温至反应温度460℃,反应压力18mpa,反应时间30min,获得高温液化产物。
[0068]
采用日本理学公司的d/max-ra12kw转靶x射线衍射仪对α-fe和从高温液化产物中分离获得的液化残渣进行xrd检测。测试条件:衍射角范围10-80
°
,扫描(管电压40kv、管电流100ma、cu靶及石墨单色滤波器)步长0.02
°
。
[0069]
图1和图2中分别示出了α-fe和液化残渣的xrd图谱,从图中可以看出,α-fe在液化反应中的活性相未发生改变(图2中其余峰为煤中杂质峰)。
[0070]
实施例2
[0071]
取10重量份γ-fe2o3、20重量份四氢萘和10重量份十氢萘加入高压反应釜中,通入氢气至釜内初始压力为2mpa,设定反应釜温度380℃并以50℃/min的升温速率升温至设定温度,反应时间为30min,反应完成后关闭加热,待温度冷却至室温,取出反应釜中的固体并采用四氢呋喃洗涤后过滤、真空干燥(105℃,24h,真空度-0.0998mpa,液体含量0.6重量%),即获得α-fe催化剂(其中α-fe含量为99.4重量%)。
[0072]
采用锡林浩特褐煤进行煤液化反应,具体方法如下:
[0073]
将煤粉(过200目筛,粒径0.075mm)、催化剂(α-fe)和溶剂(四氢萘)按照35:1:65(w/w/v,单位g/g/ml,其中催化剂与煤粉的用量比干燥无灰基煤计算)的比例配制成油煤浆,按照以下条件进行两段液化反应:
[0074]
低温液化阶段:将油煤浆通入第一反应器中,以20℃/min的升温速率升温至反应温度380℃,反应压力8mpa,反应时间45min。反应完成后物料经分离器将轻油和水分离,获
得液固物料。
[0075]
高温液化阶段:将液固物料通入第二反应器中,以35℃/min的升温速率升温至反应温度450℃,反应压力15mpa,反应时间45min,获得高温液化产物。
[0076]
实施例3
[0077]
采用实施例1制备的α-fe为催化剂,按照以下方法进行一段液化反应:
[0078]
将红柳林煤粉(过200目筛,粒径0.075mm)、催化剂(α-fe)和溶剂(四氢萘)按照40:1:60(w/w/v,单位g/g/ml,其中催化剂与煤粉的用量比干燥无灰基煤计算)的比例配制成油煤浆,然后将油煤浆通入反应器中,以25℃/min的升温速率升温至反应温度430℃,反应压力8mpa,反应时间45min。获得液化产物。
[0079]
实施例4
[0080]
按照实施例2中的方法,不同的是,按照以下条件进行两段液化反应:
[0081]
低温液化阶段:将油煤浆通入第一反应器中,以20℃/min的升温速率升温至反应温度450℃,反应压力8mpa,反应时间45min。反应完成后物料经分离器将轻油和水分离,获得液固物料。
[0082]
高温液化阶段:将液固物料通入第二反应器中,以35℃/min的升温速率升温至反应温度450℃,反应压力15mpa,反应时间45min,获得高温液化产物。
[0083]
实施例5
[0084]
按照实施例1中的方法,不同的是,采用如下两段液化反应条件:
[0085]
低温液化阶段:将油煤浆通入第一反应器中,以20℃/min的升温速率升温至反应温度360℃,反应压力5mpa,反应时间20min。反应完成后物料经分离器将轻油和水分离,获得液固物料。
[0086]
高温液化阶段:将液固物料通入第二反应器中,以35℃/min的升温速率升温至反应温度400℃,反应压力10mpa,反应时间20min,获得高温液化产物。
[0087]
实施例6
[0088]
按照实施例1中的方法,不同的是,采用如下两段液化反应条件:
[0089]
低温液化阶段:将油煤浆通入第一反应器中,以20℃/min的升温速率升温至反应温度430℃,反应压力20mpa,反应时间50min。反应完成后物料经分离器将轻油和水分离,获得液固物料。
[0090]
高温液化阶段:将液固物料通入第二反应器中,以35℃/min的升温速率升温至反应温度470℃,反应压力25mpa,反应时间50min,获得高温液化产物。
[0091]
实施例7
[0092]
按照实施例1中的方法,不同的是,采用如下两段液化反应条件:
[0093]
低温液化阶段:将油煤浆通入第一反应器中,以20℃/min的升温速率升温至反应温度330℃,反应压力3mpa,反应时间10min。反应完成后物料经分离器将轻油和水分离,获得液固物料。
[0094]
高温液化阶段:将液固物料通入第二反应器中,以20℃/min的升温速率升温至反应温度370℃,反应压力4mpa,反应时间10min,获得高温液化产物。
[0095]
实施例8
[0096]
按照实施例1中的方法,不同的是,采用如下两段液化反应条件:
[0097]
低温液化阶段:将油煤浆通入第一反应器中,以40℃/min的升温速率升温至反应温度460℃,反应压力20mpa,反应时间60min。反应完成后物料经分离器将轻油和水分离,获得液固物料。
[0098]
高温液化阶段:将液固物料通入第二反应器中,以40℃/min的升温速率升温至反应温度480℃,反应压力25mpa,反应时间60min,获得高温液化产物。
[0099]
对比例1
[0100]
选用与实施例2中粒度相同的fe2o3作为煤直接液化催化剂,采用锡林浩特褐煤进行煤液化反应,具体方法如下:
[0101]
将煤粉(粒径0.075mm)、催化剂(fe2o3)和溶剂(四氢萘)按照35:1:65(w/w/v,单位g/g/ml,其中催化剂与煤粉的用量比干燥无灰基煤计算)的比例配制成油煤浆,油煤浆中加入升华硫,调整s/fe(摩尔比)为2,并按照以下条件进行两段液化反应:
[0102]
低温液化阶段:将油煤浆通入第一反应器中,以20℃/min的升温速率升温至反应温度450℃,反应压力8mpa,反应时间45min。反应完成后物料经分离器将轻油和水分离,获得液固物料。
[0103]
高温液化阶段:将液固物料通入第二反应器中,以35℃/min的升温速率升温至反应温度450℃,反应压力15mpa,反应时间45min,获得高温液化产物。
[0104]
对比例2
[0105]
按照实施例2中的方法,不同的是,采用对比例1中的fe2o3作为催化剂,油煤浆中加入升华硫,使得s/fe(摩尔比)为2,其他条件和操作均与实施例2相同。
[0106]
测试例1
[0107]
对以上实施例和对比例获得的(高温)液化产物进行检测,并参考《煤液化技术》(高晋生,张德祥.煤液化技术.化学工业出版社,2005.)计算产品收率和转化率,结果详见表2。
[0108]
表2产品收率和转化率
[0109]
编号油/%水/%气/%沥青质/%残渣/%转化率/%实施例154.913.214.410.76.893.2实施例253.414.814.112.55.294.8实施例351.511.213.515.48.491.6实施例452.715.416.37.97.792.3实施例550.813.712.515.87.292.8实施例652.314.515.311.26.793.3实施例745.710.89.622.514.688.6实施例847.816.819.38.311.190.2对比例148.615.316.68.710.589.2对比例250.215.615.88.99.590.5
[0110]
通过对比例1和实施例2的结果对比可以发现,选用传统fe2o3作为煤直接液化催化剂油收率和转化率分别为48.6%、89.2%,明显低于本发明采用的催化剂并配合采用优选条件的两段液化工艺的油产率(53.4%)和转化率(94.8%),说明本发明催化剂和液化方法有利于低阶煤的液化转化并显著提高油收率。
[0111]
通过对比例2和实施例2的结果对比可以发现,本发明提供的两段式液化工艺在配合本发明选用的α-fe催化剂时才能够获得更高的转化率和油收率,而采用传统fe2o3催化剂时,虽然采用本发明的两段式液化工艺,其转化率和油收率也较低。
[0112]
通过实施例3-6可以发现,两段液化工艺转化率(实施例4-6)高于一段液化工艺(实施例3),说明两段液化工艺更有利于促进煤液化转化,同时可以发现实施例5两段反应中温度均相对较低,导致沥青质较高,油产率偏。通过实施例7和8可以发现过低或过高的两段液化反应温度、反应压力及反应时间导致煤液化转化率及油产率均显著降低,这是由于两段均采用较低的温度导致煤大分子结构加氢不充分,而过高的温度加剧煤液化过程中结焦反应和小分子产物的二次裂解。
[0113]
以上详细描述了本发明的优选实施方式,但是,本发明并不限于此。在本发明的技术构思范围内,可以对本发明的技术方案进行多种简单变型,包括各个技术特征以任何其它的合适方式进行组合,这些简单变型和组合同样应当视为本发明所公开的内容,均属于本发明的保护范围。
再多了解一些
本文用于企业家、创业者技术爱好者查询,结果仅供参考。