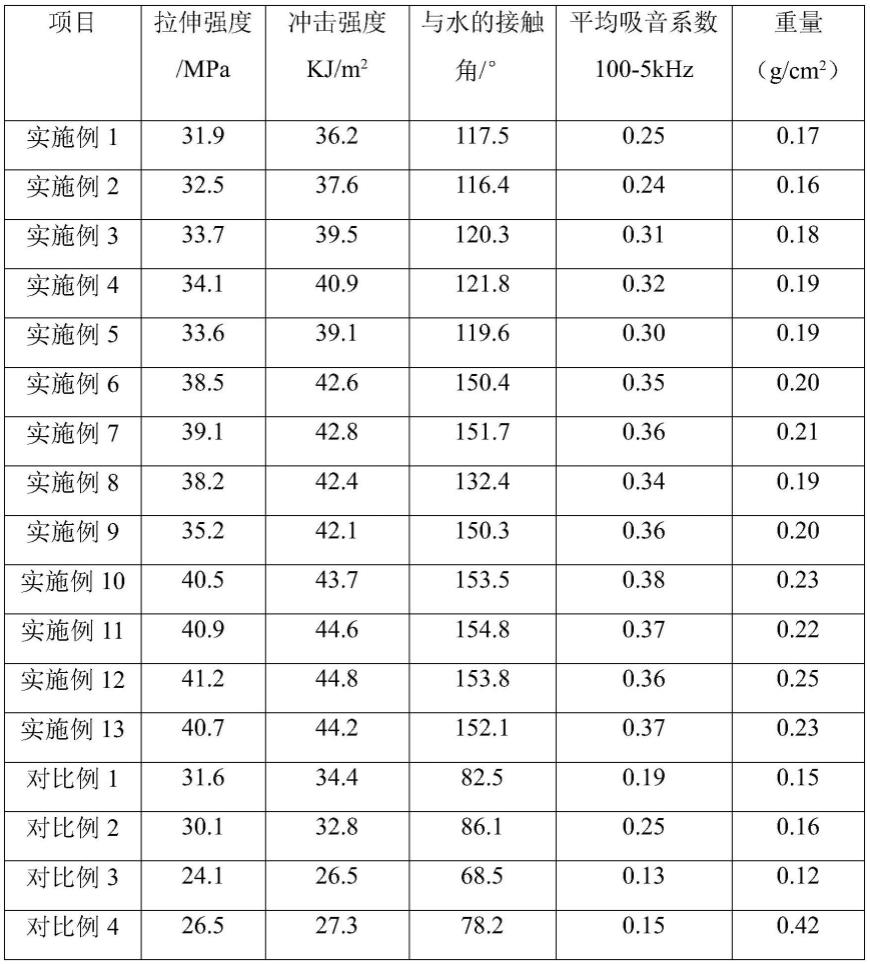
1.本技术涉及汽车配件技术领域,更具体地说,它涉及一种轻量化高强度汽车轮罩板及其制备方法。
背景技术:
2.随着经济的快速发展,人们生活水平的不断提高,汽车工业发展迅速,人们对汽车的要求不仅仅是汽车本身的质量、功能及外观的优美,对汽车的外用零部件的要求来越来越高。汽车轮罩板是指与车轮同心,加装在钢轮型车轮轮毂外侧的塑料装饰罩,主要起到装饰和防泥水的作用,还能防止砂石等飞溅而引起的车身损伤等。
3.目前,国内外对汽车轮罩板的研究与报告多限于结构部件,而对其材质成分的关注较少。因聚丙烯材料具有质轻、厚度均匀、表面光滑平整、化学性能稳定等优点,成为最常用的汽车轮罩板材料,但聚丙烯材料易发生熔体破裂,长期与热金属接触易分解,易发生缩孔、凹痕、变形。目前为改善聚丙烯材料的这一缺陷,最为常见的方法是通过添加碳酸钙、滑石粉等无机矿物粉对聚丙烯进行填充,增强其耐热性和尺寸稳定性等,但经过填充改性的聚丙烯材料密度增大,用于轮罩板时,增加了车辆的重量,使用一段时间后强度下降;且汽车在行驶过程中,砂石敲打噪声大,现有聚丙烯车轮罩板对噪音的吸收能力很小,且会产生噪音反射,无法满足使用者的实际需求。
4.针对上述中的相关技术,发明人发现目前聚丙烯材料的改性方法增大了车辆的重量,且强度和吸音性能较差。
技术实现要素:
5.为了使汽车轮罩板具有较好的吸音效果,且质量轻,强度高,本技术提供一种轻量化高强度汽车轮罩板及其制备方法。
6.第一方面,本技术提供一种轻量化高强度汽车轮罩板的制备方法,采用如下的技术方案:一种轻量化高强度汽车轮罩板的制备方法,包括以下步骤:将增强纤维经开纤后交叉铺网,经辊压和层叠后获得增强纤维网;将丝素蛋白、聚乳酸、乙二醇二缩水甘油醚、peo和溶剂混合均匀,制成分散液,加入分散液重量0.15-0.2倍的石墨烯,超声处理,浓缩至浓度为6-15wt%,制成纺丝溶液;将纺丝溶液进行静电纺丝,将所纺的丝素纳米纤维用增强纤维网一侧接收,得到增强纤维网上均匀沉积丝素纳米纤维,然后进行针刺,得到复合纤维网,增强纤维网接受纺丝的时间为30-40min;在复合纤维网未接收丝素纳米纤维的一侧喷涂聚氨酯粘胶剂,然后在聚氨酯粘胶剂上依次放卷无纺布和聚酯膜,无纺布和聚酯膜之间涂覆有聚氨酯粘胶剂,冷压,裁切,冲压,制成轮罩板。
7.通过采用上述技术方案,以增强纤维交叉铺网制成的增强纤维网,增强纤维具有
强度高、耐腐蚀、隔热等优点,制成增强纤维网后能在改善轮罩板的基础强度;然后利用丝素蛋白、聚乳酸、peo等制备分散液,加入石墨烯,然后纺丝制成丝素纳米纤维,丝素蛋白是一种从蚕丝中提取的天然高分子纤维蛋白,具有良好的机械性能和理化性质,如良好的柔韧性和抗拉伸强度,聚乳酸是半结晶高聚物,具有一定的耐热性,随着聚乳酸的加入,丝素纳米纤维的热稳定性提高,热分解温度升高,且力学性能较好的聚乳酸混入丝素蛋白中不影响丝素蛋白基本的分子结构,起到增强效果;乙二醇二缩水甘油醚进行交联作用时,环氧基开环形成-c-o-c-结构,与丝素蛋白中的氨基反应形成-ch
2-nh-,形成交联结构,改善丝素纳米纤维的强度,且加入的石墨烯,石墨烯具有片层结构和疏水性,能增大丝素纳米纤维的孔隙率和疏水性,且石墨烯的加入能改善丝素蛋白纤维的耐热性,使轮罩板长期与热金属接触也不会产生变形现象。
8.使用增强纤维网接收纺丝液经过静电纺丝形成的丝素纳米纤维,通过纺丝时间控制丝素纳米纤维在增强纤维网上的厚度,经过双面针刺形成复合纤维网,然后用聚氨酯粘胶剂连接无纺布和聚酯膜,制成强度高且质量轻,且吸音效果好、疏水性强、耐热性好、在汽车行驶过程中不易粘附泥浆的轮罩板。
9.优选的,所述增强纤维网经过以下预处理:将增强纤维网置于质量浓度为10-20%的盐酸中,浸渍60-70min,清洗,干燥后用质量浓度为2-3%的kh500水溶液浸泡20-30min,烘干后浸入质量分数为1-2%的牛血清蛋白水溶液中,室温搅拌60-70min,然后加入到ph值为5-6,且质量分数为1-1.5%%的氧化石墨烯分散液中,浸渍30-40min后,烘干,然后将增强纤维网置于按照1:2-2.5的质量比配成的氢碘酸和乙酸混合液的蒸汽中,还原3-5h。
10.通过采用上述技术方案,将增强纤维网置于盐酸中浸渍,盐酸中的氢离子与增强纤维网中阳离子相互扩散,使增强纤维网的硅氧键羟基化;kh550水解时si-o键断裂,与水反应生成硅醇,从而与增强纤维网表面的硅羟基发生缩合反应,生成稳定的si-o-si键结构,使增强纤维网的亲水性降低,疏水性增大;然后加入牛血清蛋白溶液,其对无机材料具有较好的吸附性能,因此能吸附在经过kh550处理后的增强纤维网上,当加入氧化石墨烯分散液时,牛血清蛋白改善了氧化石墨烯与增强纤维网的结合力,氧化石墨烯表面的-cooh基团在水中显示负电性,而kh550显示正电性,溶液中的正负电荷相互吸引,使得氧化石墨烯牢固的自组装在增强纤维网表面,经过氢垫酸和乙酸的混合蒸汽还原后,氧化石墨烯被还原成石墨烯,石墨烯包覆在增强纤维网上。
11.经石墨烯修饰的增强纤维网,因表面包覆有片层状的石墨烯,具有较好的褶皱效果,增大了吸音效果,且石墨烯的耐冲击性好,能改善增强纤维网的强度和吸音效果。
12.优选的,所述分散液中还含有增强疏水改性液,分散液与增强疏水改性液的质量比为1:0.4-0.6,所述增强疏水改性液包括质量比为1:0.3-0.5:2-3:5-7的聚苯乙烯、二氧化硅、聚丙烯腈和n,n-二甲基甲酰胺。
13.通过采用上述技术方案,在分散液中加入含有聚苯乙烯、二氧化硅和聚丙烯腈等形成的增强疏水改性液,经静电纺丝后,形成丝素纳米纤维,因聚苯乙烯本身为低表面能的物质,为进一步提高其疏水性,在聚苯乙烯中引入二氧化硅颗粒,在二氧化硅的存在下,丝素纳米纤维表面粗糙度增大,使得丝素纳米纤维表面所占的复合界面单位表观面积分散下降,同时空气部分所占的复合界面面积分数增大,因此丝素纳米纤维表面可与液滴接触的
面积下降,从而提高了纤维的疏水性,使纤维具有较大的水接触角;二氧化硅的加入使得丝素纳米纤维薄膜存在多孔、沟槽、褶皱及二氧化硅颗粒,多孔结构的存在增大了丝素纳米纤维的比表面积,从而改善了丝素纳米纤维的吸音系数,但多孔结构会降低丝素纳米纤维的力学性能,因此加入具有一定稳定性和机械性能的聚丙烯腈,作为增强体,提高丝素纳米纤维的力学强度,进而改善汽车轮罩板的强度。
14.优选的,所述二氧化硅的粒径为210-300nm。
15.通过采用上述技术方案,二氧化硅粒径较大,纺丝液在形成丝素纳米纤维的过程中,溶剂挥发速率减小,在丝素纳米纤维上形成孔洞、沟壑、褶皱等结构,从而增强丝素纳米纤维的吸音效果。
16.优选的,将复合纤维网在涂覆聚氨酯粘胶剂前,在100-110℃下热交联1.5-2h。
17.通过采用上述技术方案,复合纤维网是由增强纤维网表面负载丝素纳米纤维制成,丝素纳米纤维中乙二醇二缩水甘油醚对丝素蛋白进行一次交联,而热空气能使丝素蛋白发生二次交联,二次交联增强了未完全反应的乙二醇缩水甘油醚进行开环交联作用,热空气交联促进作用明显,能改善纤维强度和耐水性,使丝素蛋白侧链基团上的羧基和氨基之间形成化学交联键,提高丝素纳米纤维的结晶度,从而使丝素纤维结构更加稳定,改善其热稳定性、力学强度以及耐水性。
18.优选的,所述复合纤维网经过热交联后,浸渍在超细纳米纤维分散液中,悬挂烘干,再涂覆聚氨酯粘胶剂,超细纳米纤维在复合物纤维网上的沉积厚度为20-150nm;所述超细纳米纤维分散液包括质量比为1:2-3:0.01-0.5的聚乙烯醇缩丁醛、溶剂、超细纳米纤维。
19.通过采用上述技术方案,经过热交联后的复合纤维网表面浸渍超细纳米纤维分散液,以聚乙烯醇缩丁醛作为黏附剂,在复合纤维网浸渍过程中,超细纳米纤维黏附在复合纤维网的表面,另外聚乙烯醇缩丁醛具有疏水性,浸渍后,能增加复合纤维网的疏水性,防止汽车形式过程中,泥浆黏附在轮罩板上;超细纳米纤维在复合纤维网上乱向分布,相互搭接,增强了复合纤维网的强度,且乱向分布的超细纳米纤维相互搭接形成孔隙,从而提升了轮罩板的吸音效果。
20.优选的,所述超细纳米纤维选自聚苯乙烯纤维、聚醋酸乙烯纤维、聚醚砜纤维中的一种或几种。
21.通过采用上述技术方案,聚苯乙烯纤维具有较低的表面能,且力学强度高,聚醋酸乙烯纤维具有强度、模量高的优点,力学性能好,聚醚砜纤维具有出色的力学性能和自润滑性,超细纳米纤维的选用能改善复合纤维网的力学强度。
22.优选的,所述超细纳米纤维的直径为10-150nm,长度为100-150nm。
23.通过采用上述技术方案,使超细纳米纤维的直径和长度适宜,能防止超细纳米纤维直径过大,在复合纤维网表面沉积厚度较大,导致复合纤维网质量较大,又能防止超细纳米纤维直径过小,在复合纤维网上难以相互搭接,形成吸音孔隙。
24.优选的,所述增强纤维为玻璃纤维和碳纤维中的一种或两种。
25.通过采用上述技术方案,玻璃纤维的耐热性强,抗腐蚀性好,机械强度高,能改善汽车轮罩板的强度,且使轮罩板在于热金属接触时,不易产生变形,碳纤维具有耐高温、抗摩擦、耐腐蚀性能,能改善汽车轮罩板的耐冲击性和耐磨性。
26.优选的,所述静电纺丝电压为12-22kv,针尖距金属板距离为10-18cm,溶液注射速度为0.01-0.05ml/min。
27.通过采用上述技术方案,使静电纺丝制成的纤维连续且表面光滑,并且纤维的直径适宜。
28.第二方面,本技术提供一种轻量化高强度汽车轮罩板,采用如下的技术方案:一种轻量化高强度汽车轮罩板,由轻量化高强度汽车轮罩板的制备方法制成。
29.通过采用上述技术方案,轮罩板具有较强的耐冲击性和强度,且吸音系数小,能有效吸收汽车行驶过程中因砂石敲打产生的噪音,提高乘车者的舒适度,并且轮罩板靠近轮胎的一侧疏水性好,能有效防止雨雪天气行驶时,污泥在轮罩板上的粘附。
30.综上所述,本技术具有以下有益效果:1、由于本技术采用增强纤维交叉铺网后制成增强纤维网,然后用增强纤维网接收纺丝液制成的丝素纳米纤维,制成复合纤维网后与无纺布和聚酯膜复合,形成轮罩板,由丝素蛋白、聚乳酸、石墨烯等制成的纺丝液经静电纺丝形成的丝素纳米纤维具有孔隙率高,强度大,疏水性好的优点,因此制成的轮罩板质量轻、强度高、吸音效果好,且不易粘附泥水,长期与热金属接触不易变形。
31.2、本技术中优选采用石墨烯对增强纤维网进行包覆,依次经过羟基化、kh550处理、牛血清蛋白处理和氧化石墨烯包覆、还原,增强纤维网上均匀包覆石墨烯,石墨烯具有多孔结构,能改善增强纤维网的吸音效果,且石墨烯具有疏水性和较好的力学效果,能同时改善增强纤维网的防泥水粘附效果和强度。
32.3、本技术中优选向纺丝液中加入由聚苯乙烯、二氧化硅和聚丙烯腈等制成的增强疏水改性液,二氧化硅能增大丝素纳米纤维表面的粗糙度,改善丝素纳米纤维的疏水性,而聚苯乙烯本身就是低表面能物质,聚丙烯腈的加入能改善因加入二氧化硅后,丝素纳米纤维产生孔洞、沟槽而下降的力学性能。
33.4、本技术中优选将复合纤维网进行热空气交联后浸入超细纳米纤维分散液中,在聚乙烯醇缩丁醛的粘接作用下,超细纳米纤维分散在复合纤维网上,乱向分布并相互搭接,增大复合纤维网的力学强度,并改善孔隙率,增强吸音效果。
具体实施方式
实施例
34.除特殊说明外,以下实施例中原料均可通过市售获得。
35.实施例1:一种轻量化高强度汽车轮罩板的制备方法,包括以下步骤:s1、将玻璃纤维和碳纤维经开纤后交叉铺网,经辊压和层叠后获得厚度为15mm的增强纤维网,增强纤维为质量比为6:4的玻璃纤维和碳纤维;s2、将0.6kg丝素蛋白和0.3kg聚乳酸加入到溶剂六氟异丙醇中,搅拌至完全溶解,在搅拌情况下加入0.075kg peo和0.37kg乙二醇二缩水甘油醚,搅拌4h,脱泡,制成分散液,向分散液中加入分散液重量0.2倍的石墨烯,超声60min,浓缩至浓度为15wt%,制成纺丝液;s3、将纺丝溶液进行静电纺丝,将所纺的丝素纳米纤维用增强纤维网一侧接收,得到增强纤维网上均匀沉积丝素纳米纤维,然后进行针刺,丝素纳米纤维一侧的针刺密度为
150针/cm2,得到厚度为20mm的复合纤维网,增强纤维网接受纺丝的时间为40min,静电纺丝电压为22kv,针尖距金属板距离为10cm,溶液注射速度为0.05ml/min;s4、在复合纤维网未接收丝素纳米纤维的一侧涂覆聚氨酯粘胶剂至无滴流,然后在聚氨酯粘胶剂上放卷无纺布,在无纺布上涂覆聚氨酯粘胶剂至无滴流,然后再聚氨酯粘胶剂上放卷聚酯膜,在5mpa下保压60s,55℃下干燥,裁切,制得轻量化高强度汽车轮罩板,无纺布的面密度为400g/m2,厚度为2mm,聚酯膜的厚度为12mm。
36.实施例2:一种轻量化高强度汽车轮罩板的制备方法,包括以下步骤:s1、将玻璃纤维和碳纤维经开纤后交叉铺网,经辊压和层叠后获得厚度为15mm的增强纤维网,增强纤维为质量比为6:4的玻璃纤维和碳纤维;s2、将0.6kg丝素蛋白和0.3kg聚乳酸加入到溶剂六氟异丙醇中,搅拌至完全溶解,在搅拌情况下加入0.075kg peo和0.37kg乙二醇二缩水甘油醚,搅拌4h,脱泡,制成分散液,向分散液中加入分散液重量0.15倍的石墨烯,超声60min,浓缩至浓度为6wt%,制成纺丝液;s3、将纺丝溶液进行静电纺丝,将所纺的丝素纳米纤维用增强纤维网一侧接收,得到增强纤维网上均匀沉积丝素纳米纤维,然后进行针刺,丝素纳米纤维的针刺密度为200针/cm2,得到厚度为15mm的复合纤维网,增强纤维网接受纺丝的时间为30min,静电纺丝电压为12kv,针尖距金属板距离为18cm,溶液注射速度为0.01ml/min;s4、在复合纤维网未接收丝素纳米纤维的一侧涂覆聚氨酯粘胶剂至无滴流,然后在聚氨酯粘胶剂上放卷无纺布,在无纺布上涂覆聚氨酯粘胶剂至无滴流,然后再聚氨酯粘胶剂上放卷聚酯膜,在5mpa下保压60s,55℃下干燥,裁切,制得轻量化高强度汽车轮罩板,无纺布的面密度为400g/m2,厚度为2mm,聚酯膜的厚度为12mm。
37.实施例3:一种轻量化高强度汽车轮罩板的制备方法,与实施例1的区别在于,增强纤维网经过以下预处理:将增强纤维网置于质量浓度为10%的盐酸中,浸渍70min,清洗,干燥后用质量浓度为2%的kh500水溶液浸泡30min,烘干后浸入质量分数为1%的牛血清蛋白水溶液中,室温搅拌70min,然后加入到ph值为5,且质量分数为1%的氧化石墨烯分散液中,浸渍40min后,烘干,然后将增强纤维网置于支架上,在支架下方放置按照1:2的质量比配成的氢碘酸和乙酸混合液,35℃水浴加热混合溶液,用混合溶液的蒸汽对增强纤维网还原5h。
38.实施例4:一种轻量化高强度汽车轮罩板的制备方法,与实施例1的区别在于,增强纤维网经过以下预处理:将增强纤维网置于质量浓度为20%的盐酸中,浸渍60min,清洗,干燥后用质量浓度为2%的kh500水溶液浸泡20min,烘干后浸入质量分数为2%的牛血清蛋白水溶液中,室温搅拌60min,然后加入到ph值为6,且质量分数为1.5%的氧化石墨烯分散液中,浸渍30min后,烘干,然后将增强纤维网置于支架上,在支架下方放置按照1:2.5的质量比配成的氢碘酸和乙酸混合液,35℃水浴加热混合溶液,用混合溶液的蒸汽对增强纤维网还原3h。
39.实施例5:一种轻量化高强度汽车轮罩板的制备方法,与实施例4的区别在于,氧化石墨烯质量分数为2%。
40.实施例6:一种轻量化高强度汽车轮罩板的制备方法,与实施例4的区别在于,纺丝液中还含有增强疏水改性液,将增强疏水改性液加入到分散液中,然后超声60min,浓缩至
浓度为15wt%,增强疏水改性液包括质量比为1:0.3:2:5的聚苯乙烯、二氧化硅、聚丙烯腈和n,n-二甲基甲酰胺,二氧化硅的粒径为210nm。
41.实施例7:一种轻量化高强度汽车轮罩板的制备方法,与实施例4的区别在于,纺丝液中还含有增强疏水改性液,将增强疏水改性液加入到分散液中,然后超声60min,浓缩至浓度为15wt%,增强疏水改性液与分散液的质量比为0.6:1,增强疏水改性液包括质量比为1:0.5:3:7的聚苯乙烯、二氧化硅、聚丙烯腈和n,n-二甲基甲酰胺,二氧化硅的粒径为300nm。
42.实施例8:一种轻量化高强度汽车轮罩板的制备方法,与实施例7的区别在于,增强疏水改性液中未添加二氧化硅。
43.实施例9:一种轻量化高强度汽车轮罩板的制备方法,与实施例7的区别在于,增强疏水改性液中未添加聚丙烯腈。
44.实施例10:一种轻量化高强度汽车轮罩板的制备方法,与实施例7的区别在于,复合纤维网在涂覆聚氨酯粘胶剂前,在100℃下热交联2h,然后将复合纤维网浸渍在超细纳米纤维分散液中,浸渍16min后,在40℃下悬挂烘干,复合纤维网表面的超细纳米纤维沉积厚度为150nm;超细纳米纤维分散液的制备方法为:将聚乙烯醇缩丁醛分散在乙醇中,然后加入超细纳米纤维,以5000r/min的转速搅拌均匀,聚乙烯醇缩丁醛、乙醇和超细纳米纤维的质量比为1:2:0.01,超细纳米纤维为聚苯乙烯纤维,直径为150nm,长度为150nm。
45.实施例11:一种轻量化高强度汽车轮罩板的制备方法,与实施例7的区别在于,复合纤维网在涂覆聚氨酯粘胶剂前,在110℃下热交联1.5h,然后将复合纤维网浸渍在超细纳米纤维分散液中,浸渍5min后,在40℃下悬挂烘干,复合纤维网表面的超细纳米纤维沉积厚度为20nm;超细纳米纤维分散液的制备方法为:将聚乙烯醇缩丁醛分散在乙醇中,然后加入超细纳米纤维,以5000r/min的转速搅拌均匀,聚乙烯醇缩丁醛、乙醇和超细纳米纤维的质量比为1:3:0.5,超细纳米纤维为聚醚砜纤维,直径为10nm,长度为100nm。
46.实施例12:一种轻量化高强度汽车轮罩板的制备方法,与实施例11的区别在于,超细纳米纤维在复合纤维网表面的沉积厚度为300nm。
47.实施例13:一种轻量化高强度汽车轮罩板的制备方法,与实施例11的区别在于,复合纤维网在涂覆聚氨酯粘胶剂前,未进行热空气交联。
48.对比例对比例1:一种轻量化高强度汽车轮罩板的制备方法,与实施例1的区别在于,纺丝液中未添加石墨烯。
49.对比例2:一种轻量化高强度汽车轮罩板的制备方法,与实施例1的区别在于,纺丝液中未添加聚乳酸。
50.对比例3:一种轻量化高强度汽车轮罩板的制备方法,与实施例1的区别在于,将增强纤维经开纤后交叉铺网,经辊压和层叠后获得增强纤维网,在增强纤维网的一侧喷涂聚氨酯粘胶剂,然后在聚氨酯粘胶剂上依次放卷无纺布和聚酯膜,无纺布和聚酯膜之间涂覆有聚氨酯粘胶剂,冷压,裁切,冲压,制成轮罩板。
51.对比例4:一种隔音降噪汽车外轮罩的加工工艺,汽车外轮罩由针刺无纺布和pp复合材料加工而成;汽车外轮罩的加工工艺包括如下步骤:
(1)首先将待使用的模具放置在模温机内,将模温机加热至245℃,使模具的温度达到170℃,模温机的加热时间控制在20s;(2)在加热板上铺上汽车外轮罩成型面料,然后合上加热板对汽车外轮罩成型面料进行加热,加热板的加热温度控制在200,加热时间保持在50s;(3)取出步骤(2)中加热成熟后的面料,将面料挂在步骤(1)中的模具的下模周边的挂钉上面之后,启动模压机并带动上模下压合模,模压机的主缸压力为14mpa,保压时间为40s;(4)将步骤(3)中成型的汽车外轮罩的表面增加发泡层。
52.(5)待成型之后,将制成的半成品拿到水切割设备上进行水切割处理,切割成所需要的形状,并对需要打孔的位置进行打孔操作,最终获得所需尺寸的汽车外轮罩产品,切割水压力3250ba;(6)包装入库,在本实施例中,针刺无纺布的厚度为2mm,pp复合材料粘结在针刺无纺布的表面加热后并通过模压机冲模。
53.性能检测试验按照上述方法制备汽车轮罩板,并参考以下方法对汽车轮罩板进行性能检测,将检测结果记录于表1中。
54.1、拉伸强度:按照gb/t1040-2018《塑料拉伸性能额测定第1部分总则》进行检测;2、冲击强度:按照gb/t1843-2008《塑料悬臂梁冲击强度的测定》进行检测;3、与水的接触角:使用接触角仪检测轮罩板上复合纤维网一侧与水的接触角,每个实施例或对比例取三组数据取平均值;4、吸音测试:采用“小型混响舱(alpha cabin)法,在扩散声场中的吸音性”的测试方法,检测在100-5khz声音频率范围内的平均吸音系数。
55.5、质量检测:取相同体积的汽车轮罩,采用常规称量工具进行称量。
56.表1实施例和对比例制备的汽车轮罩板的性能检测
实施例1和实施例2中使用增强纤维网接收丝素纳米纤维,然后针刺制成复合纤维网,在复合纤维网上依次连接有聚氨酯粘胶剂、无纺布、聚氨酯粘胶剂和聚酯膜,制成的汽车轮罩板的拉伸强度高,耐冲击性强,质轻轻,且对噪音的吸音效果较好,能防止汽车行驶时,砂石敲打轮罩板,导致客户体验感不佳;并且复合纤维网一侧具有较好的疏水性,能防止汽车在行驶过程中,泥水粘附在轮罩板内侧。
57.实施例3和实施例4中使用氧化石墨烯对增强纤维网进行预处理,然后再对氧化石墨烯进行还原,从而将石墨烯包覆在增强纤维网上,表1内显示,实施例3和实施例4制备的轮罩板虽然重量有所增加,但拉伸强度和冲击强度有所增大,且疏水性增强,吸音系数增大显著,说明使用石墨烯包覆增强纤维网能有效改善汽车轮罩板的力学性能和降噪、防污泥粘附的效果。
58.实施例5与实施例4相比,氧化石墨烯浓度增大,汽车轮罩板的力学强度下降,且冲击强度和疏水性、吸音效果均下降,可能是石墨烯浓度较大,影响了氧化石墨烯层的分散性,使得氧化石墨烯片层在增强纤维网易出现团聚,不能达到均一、稳定的效果,厚层的石
墨烯偏与增强纤维网的结合性较弱,包覆效果变差。
59.实施例6和实施例7相较于实施例4的区别在于,在纺丝液中加入增强疏水改性液,表1内显示,增强疏水改性液增大了轮罩板的拉伸强度、抗冲击性和疏水性,且仍能使轮罩板具有较好的吸音效果。
60.实施例8与实施例7相比,增强疏水改性液中未添加二氧化硅,复合纤维网一侧的疏水性降低,吸音效果效果减弱。
61.实施例9与实施例7相比,增强疏水改性液中未添加聚丙烯腈,轮罩板的拉伸强度下降,疏水性和吸音系数变化不大,说明聚丙烯腈的加入,能增强丝素纳米纤维的拉伸强度,从而增大汽车轮罩板的强度。
62.实施例10和实施例11与实施例7相比,复合纤维网涂覆聚氨酯粘胶剂前,进行热空气交联,并在其表面浸渍超细纳米纤维,实施例10和实施例11制备的轮罩板的拉伸强度和耐冲击性增强,疏水性变化不大,重量有所增大,但仍比对比例4中使用pp等浸渍体与碳纤维网复合模压制成的轮罩板质量轻。
63.实施例12与实施例11相比,超细纳米纤维在复合纤维网上的沉积厚度增大,虽然轮罩板的力学性能增强,但质量增大明显,且吸音系数降低。
64.实施例13与实施例11相比,复合纤维网未经热空气交联,增强纤维网的疏水性下降,且力学强度降低。
65.对比例1与实施例1相比,未在纺丝液中添加石墨烯,表1内显示,对比例1制备的汽车轮罩板质量有所减轻,但吸音系数降低,与水的接触角减小,耐冲击强度减弱,说明加入石墨烯能改善轮罩板的强度和吸音效果,还能防止污泥粘附。
66.对比例2与实施例1相比,纺丝液中未添加聚乳酸,对比例2制备的汽车轮罩板的拉伸强度降低,力学强度减弱,疏水性变差,防污泥粘附效果降低。
67.对比例3与实施例1相比,在增强纤维网上涂覆聚氨酯粘胶剂,复合无纺布和聚酯膜,对比例3制备的轮罩板虽然质量很轻,但其拉伸强度和耐冲击强度下降显著,疏水性差,吸音系数小,降低了使用体验感。
68.对比例4为使用针刺无纺布和pp复合材料加工制成的汽车轮罩板,表1内显示,对比例4制成的轮罩板的重量较大,且力学强度并不高,另外疏水效果差,易粘附泥浆,且吸音系数小,降低噪音的效果不佳。
69.本具体实施例仅仅是对本技术的解释,其并不是对本技术的限制,本领域技术人员在阅读完本说明书后可以根据需要对本实施例做出没有创造性贡献的修改,但只要在本技术的权利要求范围内都受到专利法的保护。
再多了解一些
本文用于企业家、创业者技术爱好者查询,结果仅供参考。