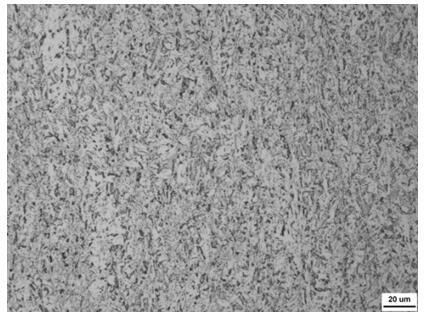
一种高止裂性e51厚钢板的生产方法
技术领域
1.本发明属于冶金技术领域,涉及到一种高止裂性e51厚钢板的轧制生产方法。
背景技术:
2.海上运输业蓬勃发展,集装箱船作为货物贸易的主要运输工具,逐步向着大型化和超大型的方向发展,集装箱船甲板上部结构承载负荷也越来越大。国际上从20世纪90年代开始研发止裂性钢板,2008年成功开发出一种新型高拉力强化钢,并首次在日本造船厂使用这种钢板。2013年,国际船舶联合会(iacs)专门针对大型集装箱船板关键部位制定了集装箱船用钢板标准,并将esso试验和双重拉伸等脆性断裂试验列为检验钢板止裂性能的方法,目前24000teu超大型集装箱船已使用。
3.为保证船舶的安全,关键部位如主甲板、舷顶列板、舱口围板等处要求高强度、高韧性及高止裂性能,舱口围板厚度达到95mm,并有望向30000teu的超级集装箱发展,需要更大厚度或更高强度的止裂钢板。
技术实现要素:
4.本发明的目的在于提供一种厚度50~100mm高止裂性厚钢板e51的生产方法。
5.发明的技术方案:一种高止裂性e51厚钢板的生产方法,钢的化学组成质量百分比为c=0.03~0.05、si=0.10~0.30、mn=1.80~1.90、p≤0.008、s≤0.002、alt=0.020~0.050、ni=0.90~1.00、cu=0.20~0.30、cr=0.10~0.20、nb=0.030~0.040、ti=0.015~0.020、n≤0.0060;其它为fe和残留元素;包括如下工艺步骤:(1)冶炼:按照化学成分要求冶炼400mm厚度铸坯,连铸实行全程保护浇铸,浇注温度按液相线温度 (6-15℃)低过热度控制,凝固末端轻压下结合浇注末端重压下技术,总压下量≥20mm;板坯下线堆冷至室温;(2)板坯加热:板坯采用步进炉进行低温加热,温度控制在t~t 50℃,加热时间350~450min,其中均热段时间不少于30min;(3)第一次轧制:采用双机架四辊可逆式轧机,高压水除鳞后粗轧空过,空冷待温至未再结晶温度≤tnr-20℃,钢板采用低温大压下轧制,道次压下量≥30mm,目标厚度220~300mm;轧制完成后经过预矫直机矫直后进入快速冷却设备muplic采用摆动模式冷却200s至300℃以下,保留细化的晶粒组织;(4)再加热:将第一次轧制后板坯进行超低温加热,发挥第一次轧制的细化晶粒组织对再热奥氏体的细化作用,温度控制在900~930℃,加热时间250~350min,其中均热段时间不少于30min;(5)控制轧制:高压水除鳞后,空冷待温至≤tnr-20℃粗轧机开始轧制,中间坯轧制至100~200mm,中间坯厚度与成品厚度比≥1.5;中间坯空冷,精轧机开始轧制温度≤ar3-20℃,终轧温度640~680℃;
(6)控制冷却:使用预矫直保证板形平直度;超快冷muplic冷却水温≤32℃,开冷温度630~670℃,冷却速率5~10℃/s,返红温度370~430℃。
6.步骤(2)中,t为固溶温度,t=-6770
÷
{-2.26 log10
×
[nb
×
(c 12
÷
14
×
n)] }-273步骤(3)中,tnr为再结晶温度, tnr=877 464
×
c 870
×
ti 363
×
al-357
×
si 6445
×
(nb
×
0.80)-644
×
[sqrt(nb
×
0.80)] [732
×
v-230
×
(sqrt(v)]步骤(5)中,ar3为相变温度,ar3={1670-558
×
[c (mn mo)
÷
3.875 cu
÷
15.5 cr
÷
20.67 ni
÷
5.636 ] 16
×
[ (h
÷
25.4)-0.315 ]-32}
×5÷
9,其中元素符号表示此元素的质量百分比,单位为%;h表示成品钢板的厚度,单位为mm。
[0007]
发明原理:c:碳元素在合金钢中,常与其它合金元素形成碳化物,在室温或较低温度下能起到强化作用。低c含量对韧性、止裂性和焊接性都有决定性作用,同时结合强度要求,控制c含量控制在0.03~0.05%的窄成分范围;si:以固溶体形式存在于铁素体和奥氏体中,提高铁素体和奥氏体的强度和硬度,造成钢韧性下降,本发明si含量控制在0.20~0.30%。
[0008]
mn、ni :淬透性元素,对提高钢板的强度和韧性均有利, 其含量控制在较高水平。
[0009]
nb、ti:碳氮化固溶元素,加热过程中稳定原始奥氏体晶粒度,抑制轧制过程中的动态和静态再结晶,抑制再结晶后晶粒长大细化晶粒,冷却过程中析出强化提高强度。
[0010]
p、s:为有害元素,应尽量降低,上限控制p≤0.008%、s≤0.002%。
[0011]
cr、cu:提高强度,凝固过程中没有成分的偏析,适量添加时对韧性没有明显的影响,为保证强度富裕量,适量添加。
[0012]
本发明采用tmcp工艺生产50-100mm大厚度的止裂钢板e51,低c含量成分设计是低温韧性和焊接性能的保证,细化的晶粒、以针状铁素体为主的显微组织,高的位错密度和晶界面积在保证强度的同时具有良好的低温韧性,有效的阻止裂纹的扩展。大厚度钢板保证压缩比采用400mm铸坯,低温加热工艺充分固溶微合金元素的同时防止原始奥氏体长大。轧制过程避免在再结晶过程轧制,因再结晶生成的再结晶晶粒,比未再结晶晶粒软,在后续的轧制中再结晶晶粒畸变集中难以消除。第一次轧制采用未再结晶区的低温大压下技术均匀细化的晶粒度,通过快速冷却得到细小的晶粒度。超低温再加热,在均匀奥氏体的同时防止奥氏体长大,二阶段轧制,第一阶段在未再结晶区轧制,第二阶段在两相区轧制,充分细化晶粒和形变诱导析出碳氮化物,大大增加晶界和晶内的形核点,超快冷较大的冷速避开珠光体转变区域,使最终组织以细小针状铁素体和贝氏体为主,同时预矫直机投入使用保证平直度,最终e51厚钢板的强度和冲击韧性性能均匀,止裂性良好。
[0013]
本发明的有益效果:此发明通过低温和超低温加热,节约能耗的同时控制原始奥氏体晶粒度,通过第一次低温大压下轧制均匀化铸坯组织细化晶粒,后续全轧制过程未再结晶区和两相区轧制,避免再结晶对道次临界压下率的要求,通过累计压下变形细化晶粒,工艺过程对最终组织的稳定性大大提高,因此可用400mm连铸坯稳定生产最大厚度100mm,最大宽度4000mm的高止裂性e51钢板。
附图说明
[0014]
图1为实施例金相组织图。
具体实施方式
[0015]
一种高止裂性e51厚钢板的生产方法,工艺流程为转炉冶炼
→
精炼
→
连铸
→
板坯加热
→
第一次轧制
→
快冷
→
再加热
→
控制轧制
→
控制冷却
→
精整
→
性能检验;关键工艺步骤包括:(1)冶炼:保证各元素成分满足控制要求。由于轧制大厚度钢板,连铸采用400mm断面,浇注温度液相线温度 (6-13℃)低过热度控制,凝固末端轻压下5mm,浇注末端重压下16,总压下量21mm;板坯下线堆冷至室温。
[0016]
(2)板坯加热:根据炉次成分,计算微合金元素固溶温度以确定加热温度控制范围;如实施例1,固溶温度t=-6770
÷
{-2.26 log10
×
[0.036
×
(0.04 12
÷
14
×
0.0045)] }-273=1048,结合批量生产的控制和效率,确定加热温度为1090℃,加热时间395min,均热段时间35min。
[0017]
(3)第一次轧制:高压水除鳞后,粗轧空过,空冷待温。为最大限度的细化晶粒,计算未再结晶的温度。如实施例1中,tnr=877 464
×
0.04 870
×
0.018 363
×
0.030-357
×
0.17 6445
×
(0.031
×
0.80)-644
×
[sqrt(0.031
×
0.80)] [732
×
0-230
×
(sqrt(0)]=924,保证轧制全过程未再结晶区域轧制,确定第一次轧制温度890℃,轧制厚度240mm;轧制完成后快速冷却至260℃,保证细化的晶粒不会长大。
[0018]
(4)再加热:降低变形抗力在保证可轧性完成奥氏体化的情况下,控制超低温加热900℃,加热时间300min,均热段时间35min。
[0019]
(5)控制轧制:高压水除鳞后粗轧890℃开轧,中间坯120mm。控制未再结晶区域轧制的同时,保证一定道次的两相区轧制,根据成分计算相变温度ar3={1670-558
×
[0.04 (1.81 0)
÷
3.875 0.23
÷
15.5 0.15
÷
20.67 0.91
÷
5.636 ] 16
×
[ (50
÷
25.4)-0.315 ]-32}
×5÷
9=709;确定二阶段开轧温度680℃,保证精轧在两相区轧制。
[0020]
(6)控制冷却:投入使用预矫直机,冷却水温26℃,返红温度400℃。
[0021]
实施例钢的化学成分及质量百分比为如表1,其它为fe和残留元素;工艺参数如表2 ;钢的性能检测结果如表3 。
[0022]
表1 实施例化学成分表。
[0023] 表2 实施例工艺参数表
。
[0024]
表3 实施例钢的性能检测结果。
[0025]
使用本发明所述方法生产50-100mm高止裂性厚钢板e51的产品表面质量优良,外检合格率100%,i级探伤合格率100%,性能合格率100%。钢板厚度位置表面、t/4和t/2处性能均匀性良好,心部位置-60℃低温冲击功180j以上,止裂性kca(-10℃)6000 n/mm
3/2
,性能稳定性良好。
再多了解一些
本文用于企业家、创业者技术爱好者查询,结果仅供参考。