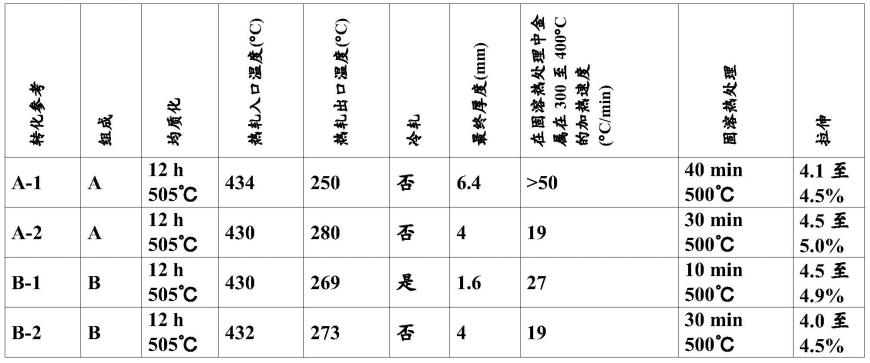
1.本发明涉及由铝-铜-锂合金制成的厚度小于12.7mm的提供了改进韧性的轧制金属板,及其制造方法。这些板材特别是旨在用于航空和航天构造。
背景技术:
2.开发了由铝合金制成的层压产品来制造旨在特别是用于航空工业和航天工业的机身元件。铝-铜-锂合金用于制造这类产品是特别有前景的。
3.专利ep 1 966 402记载了一种合金,该合金包含2.1至2.8重量%的cu、1.1至1.7重量%的li、0.1至0.8重量%的ag、0.2至0.6重量%的mg、0.2至0.6重量%的mn,fe和si的量各自小于或等于0.1重量%,以及不可避免的杂质,所述杂质含量各自小于等于0.05重量%且总计小于等于0.15重量%,该合金基本上不含锆,特别适用于获得重结晶的薄板。
4.专利fr 3014448记载了一种由铝合金制成的轧制和/或锻造产品,其厚度为14至100mm,其组成按重量百分比计,cu:1.8-2.6,li:1.3-1.8,mg:0.1-0.5,mn:0.1-0.5且zr《0.05或者mn《0.05且zr 0.10-0.16,ag:0-0.5,zn《0.20,ti:0.01-0.15,fe:《0.1,si:《0.1,15种其他元素各自《0.05且总计《0.15,其余为铝,其密度小于2.670g/cm3,其特征在于在中等厚度下,具有黄铜型织构(brass texture)的晶粒的体积分数为25至40%,且织构指数为12至18。
5.专利ep 2981632记载了一种制造厚度为0.5至3.3mm的具有基本上未重结晶结构的由铝基合金制成的薄板的方法,其中依次地a)制备包含以下组分的液态金属熔池:2.6至3.4重量%的cu,0.5至1.1重量%的li,0.1至0.4重量%的ag,0.2至0.8重量%的mg,0.11至0.20重量%的zr,0.01至0.15重量%的ti,任选地至少一种选自mn、v、cr、sc和hf的元素,如果选择的话,元素的量为:mn为0.01至0.8重量%,v为0.05至0.2重量%,cr为0.05至0.3重量%,sc为0.02至0.3重量%,hf为0.05至0.5重量%,zn的量小于0.6%重量,fe和si的量各自小于或等于0.1重量%,以及不可避免的杂质含量各自小于或等于0.05重量%且总计小于或等于0.15重量%;b)由所述液态金属熔池浇铸板坯;c)将所述板坯在450℃至515℃的温度下均质化;d)将所述板坯通过热轧轧制为厚度为4至12mm的板;e)将所述板通过冷轧轧制为最终厚度为0.5至3.3mm的薄板,通过冷轧实现的厚度减少量为1至3.5mm;f)进行热处理,在此期间,板至少在30分钟内达到300℃到450℃的温度;g)在450℃至515℃的温度下进行固溶热处理并将所述薄板淬火;h)将所述板以可控的方式以0.5至5%的永久变形率拉伸,固溶热处理后的冷变形率小于15%;i)进行时效处理,包括在130至170℃的温度下优选在150至160℃的温度下加热5至100小时,优选10至40小时。
6.专利ep2981631记载了一种由铝基合金制成的厚度为0.5至8mm的板,所述板包含2.6至3.0重量%的cu,0.5至0.8重量%的li,0.1至0.4重量%的ag,0.2至0.7重量%的mg,0.06至0.20重量%的zr,0.01至0.15重量%的ti,任选地至少一种选自mn、v、cr、sc和hf的元素,如果选择,该元素的量为0.01至0.8重量%的mn,0.05至0.2重量%的v,0.05至0.3重
量%的cr,0.02至0.3重量%的sc,0.05至0.5重量%的hf,zn的量小于0.2重量%,fe和si的量各自小于或等于0.1重量%,以及不可避免的杂质含量各自小于或等于0.05重量%且总计小于或等于0.15重量%,所述板通过包括铸造、均质化、热轧和任选地冷轧、固溶热处理、淬火和时效的方法获得,组成和时效相结合,使得纵向屈服强度rp0.2(l)为395至435mpa。
7.对于某些机身应用,t-l方向的高韧性尤为重要。这是因为机身的主要部分设计用于承受飞机的内部压力。板的纵向方向通常位于飞机长度方向上,这些板在横向方向上受到压力的应力。然后裂纹在t-l方向上受到应力。
8.从专利ep 1 891 247已知,对厚度为4至12mm的板,显微结构完全未重结晶或完全重结晶可能是有利的。
9.申请pct/fr2019/051269记载了一种制造由铝基合金制成的薄板的方法,该薄板包含以重量百分比计,2.3至2.7%的cu、1.3至1.6%的li、0.2至0.5%的mg、0.1至0.5%的mn、0.01至0.15%的ti、zn的含量小于0.3、fe和si含量各自小于或等于0.1%、以及不可避免的杂质含量各自小于或等于0.05重量%且总计小于或等于0.15重量%,其中特别是热轧入口温度为400℃至445℃,热轧出口温度小于300℃。在该申请中,考虑通过描述的方法获得的薄板为特别有利的,其中根据astme112在l/tc截面上在l方向上通过截距法测量的并以μm表示的厚度上的平均晶粒尺寸小于66t 200,其中t是以mm表示的板的厚度。
10.发明人认识到,这种类型的产品不能实现在t-l方向上大于190mpa.m
1/2
的kr
60
韧性值或大于145mpa.m
1/2
的k
app
韧性,在cct760型(2a0=253mm)测试件在测量。
11.需要厚度为0.5mm至12.7mm的由铝-铜-锂合金制成的薄板,其与已知产品相比特别是在t-l方向上的韧性、静态机械强度和耐腐蚀性方面具有改进的性能,同时具有低密度、低的机械性能各向异性和良好的抗时效性。此外,需要一种简单且经济的方法来获得这种薄板。
12.本发明的目的是解决这个问题。
技术实现要素:
13.本发明的第一个目的涉及一种制造厚度为0.5和12.7mm的由铝基合金制成的板的方法,其中,依次地,
14.a)制备液态金属熔池,其包含
15.2.2至2.7重量%的cu,
16.1.3至1.6%重量的li,
17.不超过0.1%重量的ag,
18.0.2至0.5重量%的mg,
19.0.1至0.5重量%的mn,
20.0.01至0.15重量%的ti,
21.zn的量小于或等于0.3重量%,fe和si的量各自小于或等于0.1重量%,其余为铝和不可避免的杂质,所述杂质含量各自小于或等于0.05重量%并且总计小于或等于0.15重量%,其余为铝,
22.b)由所述液态金属熔池浇铸板坯;
23.c)将所述板坯在490℃至535℃的温度下均质化;
24.d)将所述均质化的板坯通过热轧和任选的冷轧轧制成厚度为0.5至12.7mm的板,热轧入口温度为400℃至460℃,热轧出口温度低于300℃,优选低于290℃;
25.e)将所述板在450℃至535℃的温度下进行固溶热处理至少5分钟,优选至少10分钟,所述板在300℃至400℃的平均加热速率至少约为17℃/min,将所述固溶热处理板在水中淬火;
26.f)将所述淬火板以可控的方式以0.5至6%的永久变形率进行拉伸,固溶热处理后的冷变形率小于15%;
27.g)进行时效处理,其包括在130至170℃的温度下加热,持续时间与组成相结合,以使长横向上的屈服强度rp0.2(lt)为350至380mpa,优选为350至370mpa,甚至更优选为355至365mpa。
28.本发明的第二个目的涉及通过根据本发明的第一个目的的方法获得的薄板,其特征在于根据astm e112在l/tc截面上在l方向上通过截距法测量并以μm表示的厚度上的平均晶粒尺寸小于56t 250,其中t为以mm表示的板的厚度,长横向lt方向的rp0.2屈服强度为350mpa至380mpa,优选为350mpa至370mpa,甚至更优选为355mpa至365mpa,以及在cct760型(2ao=253mm)测试件上测量的t-l方向上的k
app
平面应力韧性至少为145mpa.m
1/2
。
29.本发明的第三个目的涉及根据本发明的第二个目的的薄板在飞机机身面板中的用途。
附图说明
30.[图1]图1示出了实施例1的板在lt方向的屈服强度和在cct760型(2ao=253mm)测试件上测量的应力强度因子k
app t-l之间的关系。
[0031]
[图2]图2示出了实施例1中转化的板在l方向上的晶粒尺寸测量值与厚度之间的关系。
[0032]
[图3]图3示出了与实施例1中的编号实例相对应的实施例c-2-28的晶粒结构的示例。
[0033]
[图4]图4示出了与实施例1的发明例相对应的实施例a-2-25的晶粒结构的示例。
[0034]
[图5]图5示出了与实施例1的发明例相对应的实施例e-1-48的晶粒结构的示例。
[0035]
[图6]图6示出了实施例2的板在85℃时效处理1000小时对lt方向的屈服强度和在cct760型(2ao=253mm)测试件上测量的应力强度因子k
app t-l的影响。
具体实施方式
[0036]
除非有相反说明,否则与合金的化学组成相关的所有说明均表示为基于合金总重量计的重量百分比。表述1.4cu意指以重量%表示的铜含量乘以1.4。合金命名符合本领域技术人员已知的铝业协会(aluminium association)的规定。密度取决于组成,并通过计算而不是通过重量测量方法来确定。这些值根据《铝标准和数据》(“aluminium standards and data”)第2-12和2-13页所述的铝业协会的方法计算。除非另有说明,否则适用欧洲标准en 515(1993)中所示的冶金状态的定义。
[0037]
静态拉伸机械特性,换言之,极限拉伸强度rm、在0.2%伸长率下的常规屈服强度rp0.2和断裂伸长率a%,根据nf en iso 6892-1(2016)通过拉伸试验测定,取样和测试方
向由en 485-1(2016)定义。
[0038]
在本发明的上下文中,在整个厚度上测量机械特性。
[0039]
给出有效应力强度因子作为有效裂纹扩展的函数的曲线(称为r曲线)根据astm e 561测定。从r曲线计算出临界应力强度因子kc,换言之,使裂纹不稳定的强度因子。应力强度因子kco还可通过将单调载荷开始时的初始裂纹长度赋值给临界载荷来计算。这两个值针对所需形式的测试件计算。kapp代表与用于进行r曲线测试的测试件相对应的因子kco。keff代表与用于进行r曲线测试的测试件相对应的kc因子。kr60代表与裂纹扩展δaeff=60mm相对应的应力强度因子。δaeff(max)代表r曲线上最后一个点的裂纹扩展,根据astm e561有效。最后一个点要么在测试件突然断裂时获得,要么任选地在未断裂的韧带上的应力平均超过材料的屈服强度时获得。除非有相反说明,否则对于m(t)型测试件,疲劳预裂阶段结束时的裂纹尺寸为w/3,其中w为astm e561(astm e561-10-2)中所定义的测试件宽度。
[0040]
除非另有说明,否则适用en 12258(2012)中的定义。
[0041]
在本发明的上下文中,基本上重结晶的晶粒结构意指在一半厚度处的重结晶度大于70%且优选大于90%的晶粒结构。重结晶度定义为金相截面上重结晶晶粒所占的表面分数。
[0042]
在本发明的上下文中,由术语“约”引领的数值规定的特性表示该特性可以在所公开的数值的 /-10%之间。
[0043]
在本发明的上下文中,薄板是指厚度为0.5mm至12.7mm的板。
[0044]
本发明人使用本发明的方法获得了优选0.5至8mm、甚至更优选1.2mm至6.5mm的薄板,其在机械强度和韧性之间具有有利的折衷,本发明的方法尤其包括以下的组合
[0045]-组成的窄选择,
[0046]-在严格控制的热条件下通过热轧而变形
[0047]-在固溶热处理期间严格控制的平均速率上升
[0048]-为了在lt方向上达到预定屈服强度范围的控制下的时效条件
[0049]
如此获得的薄板具有特别有利的特性,尤其是在t-l方向的韧性方面。
[0050]
在本发明的方法中,制备液态金属熔池,其组成如下:
[0051]
2.2至2.7重量%的cu,
[0052]
1.3至1.6重量%的li,
[0053]
不超过0.1重量%的ag,
[0054]
0.2至0.5重量%的mg,
[0055]
0.1至0.5重量%的mn,
[0056]
0.01至0.15重量%的ti,
[0057]
zn的量小于或等于0.3重量%,fe和si的量各自小于或等于0.1重量%,其余为铝和不可避免的杂质,所述杂质含量各自小于或等于0.05重量%且总计小于或等于0.15重量%,其余为铝。
[0058]
本发明的产品的铜含量为2.2至2.7重量%。当铜含量过高时,无法获得t-l方向很高的韧性值。当铜含量太低时,无法获得最低的静态机械特性。在本发明的一个有利的实施方案中,铜含量为2.45至2.55重量%,以提高t-l方向的韧性值。在另一个实施方案中,铜含量优选为2.20至2.35重量%,以提高抗时效性。在这些铜含量下,可以实现在t8状态下追求
的r0.2(lt)的机械性能。优选地,cu含量为至少2.25重量%,优选至少2.27重量%。优选地,铜含量不超过2.30重量%。在本发明的一个有利实施方案中,铜含量为2.20至2.30重量%,优选2.25至2.30重量%。
[0059]
本发明的产品的锂含量为1.3至1.6重量%。有利地,锂含量为1.35至1.55重量%,优选1.40至1.50重量%。最小锂含量为1.35重量%且优选1.40重量%是有利的。最大锂含量为1.55重量%并且优选1.50重量%是有利的,特别是对于改善韧性和机械强度之间的平衡。添加锂有助于提高机械强度和韧性,过高或过低的含量无法获得t-l方向的非常高的韧性值和/或足够的屈服强度。此外,添加锂可降低密度。有利地,本发明的产品的密度小于2.65。
[0060]
本发明的产品的银含量小于或等于0.1重量%。有利地,银含量小于或等于0.05重量%,甚至更优选小于或等于0.01重量%。当银含量过高时,产品的工业成本过高。降低银含量至低于0.1重量%具有经济优势。
[0061]
本发明的产品的镁含量为0.2至0.5重量%,优选0.25至0.45重量%,优选0.25至0.35重量%。最小镁含量为0.25重量%是有利的。最大镁含量为0.45重量%且优选0.40重量%且优选0.35重量%或甚至0.30重量%是有利的。
[0062]
锰含量为0.1至0.5重量%,优选0.2至0.4重量%,优选0.25至0.35重量%。最小锰含量为0.2重量%且优选0.25重量%是有利的。最大锰含量为0.4重量%且优选0.35重量%或甚至0.33重量%是有利的。
[0063]
钛含量为0.01至0.15重量%。添加钛,任选地与硼和/或碳结合,有助于控制晶粒结构,特别是在浇铸过程中。
[0064]
优选地,铁和硅的含量各自不超过0.1重量%。在一个有利的实施方案中,铁和硅的含量不超过0.08重量%且优选不超过0.04重量%。可控且有限的铁和硅含量有助于改善机械强度和损伤容限之间的折衷。
[0065]
锌含量小于或等于0.3重量%,优选小于0.2重量%,且优选小于0.1重量%。锌含量有利地小于0.04重量%。
[0066]
不可避免的杂质各自保持在含量小于或等于0.05重量%且总计小于或等于0.15重量%。
[0067]
本发明的制造薄板的方法接下来包括以下步骤:浇铸,均质化,热轧和任选地冷轧,固溶热处理,可控的拉伸,淬火和时效处理。
[0068]
所制备的液态金属熔池浇铸成轧制板坯的形式。
[0069]
然后,轧制板坯在490℃至535℃的温度下均质化。优选地,均质化的持续时间为5至60小时。有利地,均质化温度至少为500℃。在一个实施方案中,均质化温度低于515℃。
[0070]
在均质化后,通常将轧制板坯冷却至环境温度,然后预热以使其热变形。预热的目标是使热轧入口温度达到400至460℃且优选420至445℃且甚至更优选420至440℃,从而允许热轧变形。
[0071]
进行热轧以获得厚度通常为3至12.7mm、优选4到12.7mm的板。热轧出口温度低于300℃且优选低于290℃,以控制存储在板中的能量。如果固溶热处理中的速率上升条件也根据本发明进行,则这可获得本发明的晶粒尺寸。
[0072]
热轧后,可以任选地冷轧所获得的板,特别是以获得0.5至4mm的最终厚度。
[0073]
根据本发明,存在介于3和4mm之间的厚度范围,其中产品可以热加工或冷加工。
[0074]
优选地,最终厚度不超过8.0mm,优选不超过7.0mm,甚至更优选不超过6.5mm。有利地,最终厚度为至少0.8mm并且优选地至少为1.2mm。
[0075]
然后,将由此获得的板在450至535℃下、优选在450至525℃下进行至少5分钟、优选至少10分钟的固溶热处理。固溶热处理的持续时间有利地为5分钟至8小时,甚至更优选为10分钟至1小时。在300℃至400℃的温度范围内,在固溶热处理期间对板进行加热的平均速度必须为至少约17℃/min,优选至少约19℃/min,甚至更优选至少约25℃/min。
[0076]
重要的是,同时控制热轧出口温度以及在固溶热处理期间的平均加热速度。控制板在300℃至400℃的平均加热速度对于控制本发明的产品的最终晶粒尺寸为必要的。板在300℃至400℃的平均加热速度可通过用置于板表面的热电偶测量板的升温温度进行计算得到。板在300℃至400℃的平均加热速度是通过金属在300℃至400℃的温度对300℃至400℃的加热时间进行线性回归计算得到。控制在300℃至400℃的平均加热速度尤为重要。本领域技术人员众所周知的是,平均加热速度不仅受炉的热条件(炉内空气温度、炉的技术)的影响,还受装载量(板的数量和在炉内的位置)以及产品厚度的影响。
[0077]
为了控制速度,例如可以在适用于固溶热处理的炉内处理待制备的板的代表性装载量,并根据炉的参数监测这些不同板的温度。处理开始时炉内空气的温度和设定的温度曲线为控制平均加热速度的典型参数。
[0078]
此外,本领域技术人员已知,必须根据厚度和组成来选择精确的固溶热处理条件,即固溶热处理维持平台的持续时间和温度,以便固溶热处理硬化元素。
[0079]
特定的热轧条件与本发明的组成和固溶热处理过程中的板加热速度相结合,特别是可以获得机械强度、韧性和机械性能的低各向异性之间的有利折衷,以及更好的抗时效性。
[0080]
由此固溶热处理的片材然后在水中淬火。优选地,淬火在水中在环境温度下进行。
[0081]
然后,所述板通过可控的拉伸经历冷变形,其永久变形率为0.5至6%、优选3至5%。诸如轧制、整平、矫直和成型的已知步骤可任选地在固溶热处理和淬火之后并且在可控的拉伸之前或之后进行,然而固溶热处理和淬火之后的总冷变形率必须保持低于15%且优选低于10%。固溶热处理和淬火之后高的冷变形率实际上会导致出现大量横穿多个晶粒的剪切带,这些剪切带为不希望的。优选在固溶热处理之后不进行冷轧。
[0082]
进行时效处理,其包括在130至170℃且优选140至160℃且优选145至155℃的温度下加热5至100小时且优选10至50小时,以获得在lt方向上的屈服强度r0.2(lt)为350mpa至380mpa,优选350mpa至370mpa,甚至更优选355mpa至365mpa。
[0083]
本领域技术人员已知,为了确定能够在lt方向上获得350mpa至380mpa的屈服强度的时效条件,本领域技术人员可以实施时效动力学。时效动力学包括在固溶热处理后切割多个坯料、淬火和冷变形,并评估在给定温度下不同时效持续时间下lt方向的屈服强度。因此,对于给定的温度,可以确定屈服强度如何随时效持续时间而变化,并选择能够获得350mpa至380mpa的屈服强度的时效持续时间。
[0084]
优选地,最终的冶金状态为t8状态。
[0085]
在本发明的一个实施方案中,在可控的拉伸之后且在时效处理之前进行短暂热处理,以改善板的可成型性。因此,所述板可在时效处理之前通过诸如拉伸成型的方法来成
型。在专利ep2766503或ep 2984195中记载了短暂热处理的实例。在这种情况下,如果进行短暂处理,则用于确定在lt方向上达到屈服强度r0.2(lt)为350mpa至380mpa所需的时效持续时间的时效动力学,必须在已经过这种短暂处理的坯料上进行。
[0086]
通过本发明的方法获得的薄板具有典型的晶粒尺寸,优选厚度为0.8至8.0mm、甚至更优选为1.2mm至6.5mm的薄板。因此,根据astm e112在l/tc截面上在l方向上通过截距法测量的并以μm表示的厚度上的平均晶粒尺寸小于56t 250,优选小于56t 200且优选小于56t 150,其中t是以mm表示的板的厚度。
[0087]
所述板的晶粒结构有利地为基本上重结晶的。
[0088]
通过本发明的方法获得的薄板在t-l方向上具有特别有利的韧性。特别地,通过本发明的方法获得的薄板具有至少145mpa.m
1/2
、优选大于148mpa.m
1/2
的平面应力韧性k
app
,在cct760型(2ao=253mm)测试件上在t-l方向上测量,并且在lt方向上的屈服强度为350mpa至380mpa、优选为350mpa至370mpa且甚至更优选为355mpa至365mpa。有利地,通过本发明的方法获得的薄板具有至少190mpa.m
1/2
、优选至少195mpa.m
1/2
的平面应力韧性kr
60
,在cct760型(2ao=253mm)测试件上在t-l方向上测量。
[0089]
通过本发明的方法获得的薄板具有根据astm e112的在l/tc截面上在l方向上通过截距法测量并以μm表示的厚度上的平均晶粒尺寸小于56t 250、优选小于56t 200且优选小于56t 150,其中t是以mm表示的板的厚度,在lt方向上的rp0.2屈服强度为350mpa至380mpa,优选350mpa至370mpa,甚至更优选355mpa至365mpa,并且在cct760型(2ao=253mm)测试件上在t-l方向上测量的k
app
平面应力韧性至少为145mpa.m
1/2
。
[0090]
在一个优选的实施方案中,当锂含量为1.40至1.50重量%,铜含量为2.45至2.55重量%且镁含量为0.25至0.35重量%时,获得本发明的薄板在韧性方面的有利性能,优选厚度为1.2mm至6.5mm的薄板。当锂含量为1.40至1.50%,铜含量为2.45至2.55重量%和镁含量为0.25至0.35重量%时,在cct760型(2ao=253mm)试件上测量的k
app
平面应力韧性大于148mpa.m
1/2
。
[0091]
在另一个优选的实施方案中,当锂含量为1.40至1.50重量%,铜含量为2.20至2.35重量%,优选2.20至2.30重量%,且镁含量为0.25至0.35重量%时,获得本发明的薄板在时效方面的有利性能,优选厚度为1.2mm至6.5mm的薄板。当锂含量为1.40至1.50重量%,铜含量为2.20至2.35重量%且镁含量为0.25至0.35重量%时,在85℃下时效处理1000小时前后在cct760型(2ao=253mm)测试件上测量的平面应力韧性k
app
大于135mpa.m
1/2
。
[0092]
本发明的板的耐晶间腐蚀性高。在本发明的一个优选的实施方案中,本发明的板可在未整平的情况下使用。
[0093]
在飞机的机身面板中使用本发明的薄板是有利的。本发明的薄板在航天应用例如制造火箭中也是有利的。
[0094]
实施例1
[0095]
在本实施例中,制备了板坯形式的六个铸件(a-f)。合金元素的重量百分比比例示于下表1中。
[0096]
[表1]
[0097]
组成culimgmntiagfesizna2.511.430.280.300.03《0.010.040.03《0.01
b2.361.540.260.300.04《0.010.040.03《0.01c2.521.460.350.360.04《0.010.040.03《0.01d2.591.460.340.360.04《0.010.040.02《0.01e2.271.410.280.290.03《0.010.040.03《0.01f2.391.430.310.300.030.10.040.030.2
[0098]
根据表2中所示的参数对板坯进行转化。
[0099]
[表2]
[0100][0101][0102]
在这些转化步骤的最后,对板进行时效处理。在某些情况下,进行了数种时效处理条件,从而可以实现多种r0.2(lt)值(参见表3和表4)。
[0103]
[表3]
[0104]
板编号转化后的板进行时效处理a-1-34a-134h 155℃a-2-25a-225h 155℃a-2-34a-234h 155℃b-1-34b-134h 155℃b-2-25b-225h 155℃b-2-34b-234h 155℃c-1-25c-125h 155℃c-1-28c-128h 155℃c-2-28c-228h 155℃
d-1-34d-134h 155℃d-2-25d-225h 155℃d-2-34d-234h 155℃e-1-48e-148h 152℃f-1-48f-148h 152℃
[0105]
在时效处理结束时,对样品进行机械测试以确定其静态机械性能以及其抗疲劳裂纹扩展性。表4中提供了拉伸屈服强度(rp0.2)、极限拉伸强度(rm)和断裂伸长率(a)。表6总结了这些样品的韧性测试结果。
[0106]
[表4]
[0107][0108][0109]
得到的结果如图1所示。
[0110]
样品的晶粒结构使用显微镜观察在l/tc截面上在偏振光下阳极氧化后的横截面进行表征。板的晶粒结构是重结晶的。图3、图4和图5显示了试样c-2-28、a-2-25和e-1-48的观察到的晶粒结构。根据astm e112通过截距法测量的厚度上的平均晶粒尺寸列于表5中。通常,晶粒结构不受时效条件的影响。因此,无论对给定的转变条件实施何种时效条件,预期晶粒尺寸都是相同的。测得的晶粒尺寸如图2所示。
[0111]
[表5]
[0112][0113]
[表6]
[0114][0115]
编号a-2-25、b-2-25和e-1-48是根据本发明制备的。
[0116]
编号a-1-34、a-2-34、b-1-34、b-2-34、c-1-28为本发明之外的记载于申请pct/fr2019/051269中的产品。这些产品在t-l方向上无法实现大于145mpa.m
1/2
的k
app
韧性值。
[0117]
这是因为,即使实施例a-1-34、a-2-34、b-1-34和b-2-34以这样的方式轧制,使得在轧制出料时,温度也低于300℃并且在l方向上具有满足本发明标准的晶粒尺寸:晶粒尺
寸小于56t 250,这些产品也不能在t-l方向上实现大于145mpa.m
1/2
的k
app
韧性值,因为r0.2(lt)值不满足本发明的标准:时效处理后r0.2(lt)为350mpa至380mpa。
[0118]
如果晶粒尺寸不满足本发明的标准:晶粒尺寸小于56t 250,其中t为所讨论的板的厚度;则仅以时效处理后屈服强度r0.2(lt)为350mpa至380mpa为目标时无法在t-l方向上获得大于145mpa.m
1/2
的k
app
韧性值。
[0119]
如果热轧出口温度小于300℃并且如果在固溶热处理期间金属在300至400℃的加热速度大于或等于17℃/min,则特别获得在l方向上的小于56t 250的晶粒尺寸。
[0120]
实施例f-1-48表明,尽管热轧条件符合出口温度低于300℃和时效处理条件可实现位于350mpa至380mpa的r0.2(lt)值,但该产品无法实现在t-l方向上大于145mpa.m
1/2
的韧性值k
app
。这与固溶热处理时金属在300至400℃的加热速度小于约17℃/min和l方向上的晶粒尺寸大于56t 250的事实有关。
[0121]
实施例c-1-25和d-2-25表明,尽管在固溶热处理期间金属在300至400℃的加热速度小于约17℃/min和时效处理条件可实现位于350mpa至380mpa的r0.2(lt)值,然而这些产品无法实现在t-l方向上大于145mpa.m
1/2
的kapp韧性值。这与热轧出料温度不低于300℃,并因此在l方向上的晶粒尺寸大于56t 250有关。
[0122]
实施例2
[0123]
在本实施例中,对在之前实施例中测试过的三个板在85℃低温下进行1000h时效处理后进行测试,所述三个板为根据本发明转化的e-1-48和其他两个作为参考的板a-2-34和c-1-28。这些产品在85℃时效处理1000小时后的屈服强度和t-l方向上的韧性列于下表7中并示于图6中。
[0124]
[表7]
[0125][0126]
根据本发明获得的板e-1-48在时效处理后在t-l方向上显示出大于135mpa.m
1/2
的韧性k
app
。
再多了解一些
本文用于企业家、创业者技术爱好者查询,结果仅供参考。