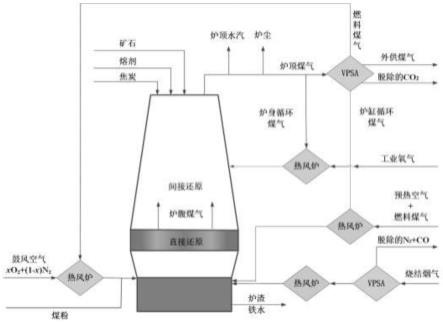
1.本发明属于冶金中烟气处理的技术领域,具体涉及一种烧结烟气的治理方法。
背景技术:
2.烧结是钢铁行业中的一个重要环节,是将各种粉状含铁原料,烧结成块的传统的工艺过程。多年来烧结厂在除尘方面效果显著,但是由于烧结、球团等原料制备过程会产生大量的污染物,尤其对于烟气中的有毒成分,如so2、no
x
、二噁英等,处理工艺效果不佳,对大气环境造成恶劣影响,因而使烧结工艺饱受诟病。据统计,烧结烟气污染物约占钢铁行业六成以上,每生产一吨烧结矿大约产生4000~6000m3的烟气,因此,对烧结烟气的处理是钢铁行业可持续发展的战略需求。
3.在传统的烧结过程中以单质、硫化物形式存在的硫以及以硫酸盐形式存在的硫通常分别在氧化反应和分解反应中大部分以气态硫化物的形式释放。烧结工艺产生的so2约占钢铁行业的40%~60%。so2主要危害有:so2毒性较大,通过光合作用等,会氧化成酸雾,形成酸雨,对金属材料、建筑物造成腐蚀,造成巨大经济损失。其次,会改变植物组织内的ph值,减缓植物生长,造成植物死亡。空气中so2的浓度较高时,会对人体的呼吸系统产生不利的影响,而且会引起心血管疾病,甚至严重中毒、窒息死亡。
4.烧结过程no
x
主要有两个来源:一是烧结点火阶段;二是固体燃料燃烧和高温反应过程。已有研究结果表明,烧结过程中产生的no
x
有80%~90%来源于燃料中的氮。每生产1t烧结矿产生no
x
约0.4~0.65kg。在通常情况下,烧结烟气no
x
中no占95%左右。大气中no会被氧化成no2,进入人体的呼吸系统后会造成肺部疾病,如肺水肿。
5.为了保护环境,防治污染,促进钢铁烧结及球团工业生产工艺和污染治理技术的进步,2019年4月,生态环境部等五部委联合印发《关于推进实施钢铁行业超低排放的意见》中,炼铁工序中热风炉的二氧化硫排放标准为50mg/m3,氮氧化物排放标准为150m3·
t-1
,高炉出铁场、高炉矿槽的氮氧化物排放标准为200mg/m3,烧结工序中二氧化硫排放标准为35mg/m3,氮氧化物排放标准为50mg/m3。
6.烧结烟气中so2和no
x
的脱除技术很多已经实现工业化应用,也在一定程度上取得了较好的减排效果。目前烧结烟气脱硫技术主要分为湿法、半干法以及活性炭吸附法,湿法脱硫技术主要有石灰石-石膏法、氨法等,半干法脱硫技术主要有选择性催化还原技术(scr)、非选择性催化还原技术(sncr)、和sncr-scr联合脱硝技术。但是脱硫率和脱硝率均普遍低于85%,同步运行率大部分低于85%左右。且在实际应用过程中仍存在许多问题和不足,如脱硫副产物难以利用、设备易堵塞和腐蚀、产生废水和废渣、能耗高、一次性设备投入资金大、运行费用高等诸多问题。
技术实现要素:
7.本发明的目的在于针对现有技术的不足之处,提供一种烧结烟气的治理方法,该方法工艺简单,运行费用低且能实现烧结烟气脱硫脱硝协同处理,不仅能处理烧结烟气中
的零排放;
22.(3)本发明采用真空变压吸附装置脱除了烧结烟气中的n2,同时使用富氧甚至全氧鼓风,减少了n2的输入,氧气高炉内部气体的还原势增强,动力学推动力増大,还原条件改善,在高炉炉身限制性环节,气固还原反应的间接还原度更大,生成的炉顶煤气是具有普通高炉2~3倍的高热值气体,一为用作炉身及炉缸处循环喷吹进入氧气高炉,二为用作加热炉缸处循环煤气、烧结烟气、鼓风空气的燃料,三为高热值的外供燃气;
23.本发明提供了一种使用氧气高炉处理及利用烧结烟气的新工艺,实现烧结烟气脱硫脱硝协同处理。不仅能处理烧结烟气中的so2、no
x
的排放问题,而且充分利用了烧结烟气中的co、o2、co2。进一步实现钢铁产业节能减排,绿色冶金的目的。
附图说明
24.图1为本发明实施例烧结烟气的治理方法工艺流程图;
25.图2为本发明实施例1氧气高炉物质流的示意图;
26.图3为本发明实施例2氧气高炉物质流的示意图;
27.图4为本发明实施例3氧气高炉物质流的示意图;
28.图5为本发明实施例4氧气高炉物质流的示意图;
29.图6为本发明实施例5氧气高炉物质流的示意图。
具体实施方式
30.下面将结合本发明实施例对本发明实施例中的技术方案进行清楚、完整地描述,显然,所描述的实施例仅仅是本发明一部分实施例,而不是全部的实施例。基于本发明中的实施例,本领域普通技术人员在没有作出创造性劳动的前提下所获得的所有其他实施例,都属于本发明保护的范围。
31.需要说明的是,在不冲突的情况下,本发明中的实施例及实施例中的特征可以相互组合。
32.下面结合具体实施例对本发明作进一步说明,但不作为本发明的限定。
33.本发明的主体设备为传统高炉,附属设备包括真空变压吸附装置,热风炉。如图1所示,本发明的主要工艺流程是通过真空变压吸附装置(vpsa装置)脱除部分n2,将部分炉顶煤气作为热风炉的燃料。烧结烟气除氮后通过热风炉加热后,从氧气高炉风口处喷吹进入高炉,烧结烟气中的co、o2等在氧气高炉中被利用,同时,在风口处采用富氧或全氧鼓风操作并喷吹煤粉,将部分炉顶煤气与工业氧气混合燃烧后从炉身处喷吹进入氧气高炉,剩余炉顶煤气脱除co2后,一部分从炉缸处喷吹进入氧气高炉,通过高炉本身具有高温、强还原性气氛的特点,烧结烟气中so2、no
x
在氧气高炉中被还原,实现烧结烟气脱硫脱硝协同处理的处理。
34.实施例1
35.利用vpsa装置脱除烧结烟气中95%的n2,vpsa装置中至少具有两个交替工作的分子筛工作床,分子筛的微孔直径为0.346nm《d
孔
《0.352nm,在本实施例中,分子筛可选择碳分子筛,烧结烟气加压后送入至少两个交替工作的分子筛工作床,利用分子筛筛分掉n2,脱氮后的烧结烟气由吸附床进入缓冲罐,以备后续处理,被分离的n2由真空风机抽出。在分子筛
的筛分作用下使n2与其他组分分离,由于co分子动力学直径大于n2,co随n2一起被筛分,烧结烟气中co同样被脱除95%。氧气高炉的操作参数包括:风口鼓风含氧率在40%~100%(鼓风空气中氧气的体积分数)即中、高等富氧高炉或全氧高炉;受热风炉的影响,烧结烟气、炉身炉缸处的循环煤气、富氧鼓风空气的喷吹温度:200℃《t
喷吹
《1300℃,炉渣碱度在1.1~1.2之间,炉顶煤气中的甲烷全部来自焦炭的挥发,但在1200℃条件下会分解为c和h2,所以炉顶煤气中不存在甲烷。在本实施例中,烧结烟气经过除氮预处理前后成分如表1所示,再经过热风炉加热至1250℃后,从高炉风口喷吹进入氧气高炉内,同时在风口出喷吹含氧率为40%的空气及434.05kg煤粉,炉身处循环喷吹200m3的炉顶煤气,剩余炉顶煤气经过除水后,利用vpsa装置脱除98%的co2,脱除co2后的炉顶煤气:一为取200m3用作炉缸处的循环煤气,二为热风炉燃料,三为外供燃料煤气,炉顶煤气脱除co2后,改变了炉顶煤气的成分,提高煤气热值。在氧气高炉中,烧结烟气中的co、o2等气体得到利用,no、so2被c还原,还原产物进入到炉渣、炉顶煤气、铁水当中。考虑到so2、no在高炉中并不能全部还原,因此设定烧结烟气中so2还原率为95%,no还原动力学比so2好,设定no还原率为97%。在此条件下,保证理论燃烧温度不低于1800℃,氧气高炉最大处理烧结烟气量为1814m3,脱除n2后烧结烟气体积为442.81m3,图2为实例1的高炉物质流,表2为喷吹烧结烟气后的氧气高炉(含氧率:40%)炉顶煤气及普通高炉(含氧率:21%)炉顶煤气成分对比。
36.表1烧结烟气成分(vol%)
[0037][0038]
表2实例1与普通高炉炉顶煤气成分对比
[0039][0040][0041]
实施例2
[0042]
利用vpsa装置(vpsa装置中至少具有两个交替工作的分子筛工作床,分子筛的微孔直径为0.347nm《d
孔
《0.350nm,在本实施例中,分子筛可选择mcm-41分子筛)脱除烧结烟气中95%的n2,烧结烟气中co同样被脱除95%,烧结烟气经过除氮预处理前后成分如表1所示,经过热风炉加热至200℃后,从高炉风口喷吹进入氧气高炉,同时在风口处喷吹含氧率
为40%的空气及589.07kg煤粉,炉身与炉缸处不循环炉顶煤气,在氧气高炉中,烧结烟气中的co、o2等气体得到利用,no、so2被c还原,还原产物进入到炉渣、炉顶煤气、铁水当中。考虑到so2、no在高炉中并不能全部还原,因此设定烧结烟气中so2还原率为95%,no还原动力学比so2好,设定no还原率为97%。在此条件下,保证理论燃烧温度不低于1800℃,氧气高炉最大处理烧结烟气量为1273m3,脱除n2后烧结烟气体积为310.75m3,图3为实例2的高炉物质流,表3为喷吹烧结烟气后的氧气高炉(含氧率:40%)炉顶煤气及普通高炉(含氧率:21%)炉顶煤气成分对比。
[0043]
表3实例2与普通高炉炉顶煤气成分对比
[0044][0045]
实施例3
[0046]
利用vpsa装置(vpsa装置中至少具有两个交替工作的分子筛工作床,分子筛的微孔直径为0.357nm《d
孔
《0.364nm,在本实施例中,分子筛可选择改性的lix沸石分子筛)脱除烧结烟气中95%的n2,烧结烟气中co同样被脱除95%,烧结烟气预处理前后成分如表1所示,经过热风炉加热至1300℃后,从高炉风口喷吹进入氧气高炉,同时在风口处喷吹含氧率为70%的空气及775.36kg煤粉,炉身与炉缸处不循环炉顶煤气,在氧气高炉中,烧结烟气中的co、o2等气体得到利用,no、so2被c还原,还原产物进入到炉渣、炉顶煤气、铁水当中。考虑到so2、no在高炉中并不能全部还原,因此设定so2还原率为95%,no还原动力学比so2好,设定no还原率为97%。在此条件下,保证理论燃烧温度不低于1800℃,氧气高炉最大处理烧结烟气量为2845m3,脱除n2后烧结烟气体积为694.48m3,图4为实例3的高炉物质流,表4为喷吹烧结烟气后的氧气高炉(含氧率:70%)炉顶煤气及普通高炉(含氧率:21%)炉顶煤气成分对比。
[0047]
表4实例3与普通高炉炉顶煤气成分对比
[0048][0049]
实施例4
[0050]
利用vpsa装置(vpsa装置中至少具有两个交替工作的分子筛工作床,分子筛的微孔直径为0.349nm《d
孔
《0.351nm,两个交替工作的分子筛分别为碳分子筛、改性的lix沸石分子筛)脱除烧结烟气中95%的n2,烧结烟气中co同样被脱除95%,烧结烟气经过除氮预处理前后成分如表1所示,经过热风炉加热至1250℃后,从高炉风口喷吹进入氧气高炉,同时在风口处喷吹纯氧及512.68kg煤粉,炉身处循环喷吹200m3的炉顶煤气,剩余炉顶煤气经过除水后,利用vpsa装置脱除98%的co2,脱除co2后的炉顶煤气:一为取200m3用作炉缸处的循环煤气,二为热风炉燃料,三为外供燃料煤气。在氧气高炉中,烧结烟气中的co、o2等气体得到利用,no、so2被c还原,还原产物进入到炉渣、炉顶煤气、铁水当中。考虑到so2、no在高炉中并不能全部还原,因此设定烧结烟气中so2还原率为95%,no还原动力学比so2好,设定no还原率为97%。在此条件下,保证理论燃烧温度不低于1800℃,氧气高炉最大处理烧结烟气量为2300m3,脱除n2后烧结烟气体积为561.44m3,图5为实例4的高炉物质流,表5为喷吹烧结烟气后的氧气高炉(含氧率:100%)炉顶煤气及普通高炉(含氧率:21%)炉顶煤气成分对比。
[0051]
表5实例4与普通高炉炉顶煤气成分对比
[0052][0053]
实施例5
[0054]
利用vpsa装置(vpsa装置中至少具有两个交替工作的分子筛工作床,分子筛的微孔直径为0.354nm《d
孔
《0.355nm,两个交替工作的分子筛分别为碳分子筛、mcm-41分子筛)脱
除烧结烟气中95%的n2,烧结烟气中co同样被脱除95%,烧结烟气预处理前后成分如表1所示,经过热风炉加热至1250℃后,从高炉风口喷吹进入氧气高炉,同时在风口处喷吹纯氧及829.41kg煤粉,炉身与炉缸处不循环炉顶煤气,在氧气高炉中,烧结烟气中的co、o2等气体得到利用,no、so2被c还原,还原产物进入到炉渣、炉顶煤气、铁水当中。考虑到so2、no在高炉中并不能全部还原,因此设定so2还原率为95%,no还原动力学比so2好,设定no还原率为97%。在此条件下,保证理论燃烧温度不低于1800℃,氧气高炉最大处理烧结烟气量为3027m3,脱除n2后烧结烟气体积为738.91m3,图6为实例5的高炉物质流,表6为喷吹烧结烟气后的氧气高炉(含氧率:100%)炉顶煤气及普通高炉(含氧率:21%)炉顶煤气成分对比。
[0055]
表6实例5与普通高炉炉顶煤气成分对比
[0056][0057][0058]
以上仅为本发明较佳的实施例,并非因此限制本发明的实施方式及保护范围,对于本领域技术人员而言,应当能够意识到凡运用本发明说明书内容所作出的等同替换和显而易见的变化所得到的方案,均应当包含在本发明的保护范围内。
再多了解一些
本文用于企业家、创业者技术爱好者查询,结果仅供参考。