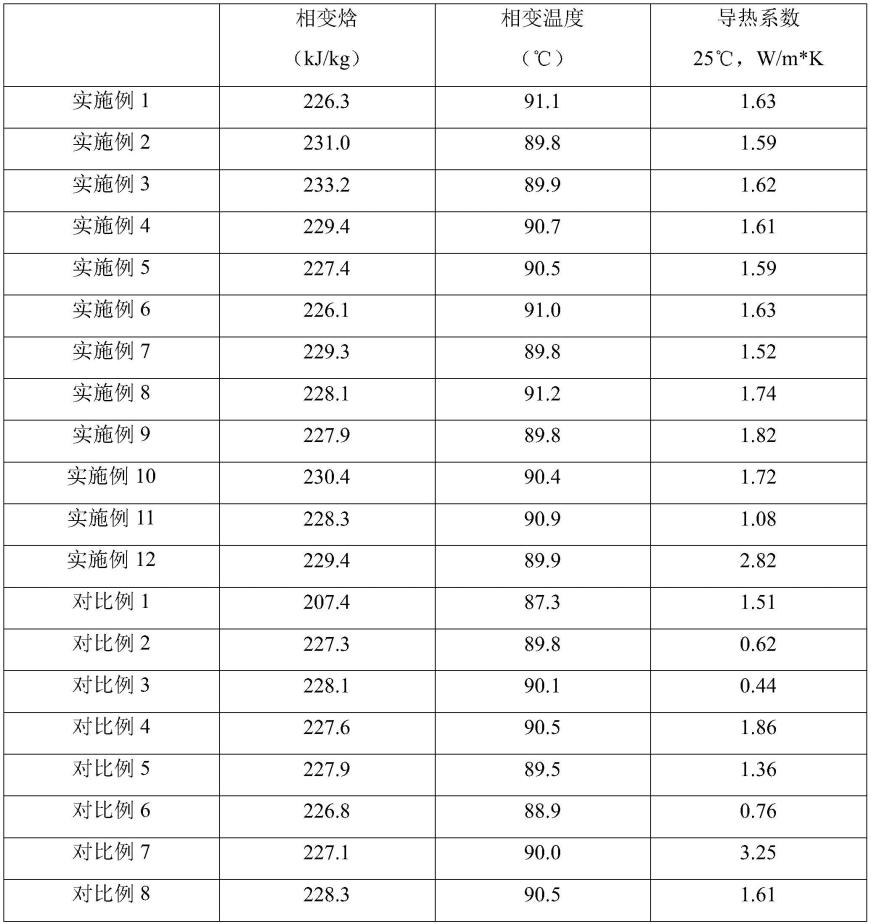
1.本技术涉及相变蜡生产技术领域,尤其是涉及一种系列相变蜡的生产方法。
背景技术:
2.相变储能是热储能的一种,利用相变材料储热特性,来储存或者是释放其中的热量,从而达到一定的调节和控制该相变材料周围环境的温度,以此改变能量使用的时空分布,提高能源的使用效率。相变材料是一种利用相变潜热来贮能和放能的化学材料,其原理是利用所含相变物质随外界温度升高时吸收储存热量,温度降低时放出储存的热量,从而实现温度调节功能。利用这种性质,相变材料可应用于温感温控、航空航天、节能建筑、纤维服装、电子元件、军事伪装和医疗器械等领域。
3.相变材料按化学性质分为无机相变材料和有机相变材料两大类。无机类相变材料稳定性较差,所以在应用上会受到一定限制,有机相变材料稳定性较好,其中,正构烷烃相变材料的性能最为突出也最为稳定,因此也备受国内外专家的关注,有机烷烃类相变材料在军工航天、电子元器件、隐身防护、温感温控等应用领域具有重要作用。由于正构烷烃类相变材料的生产难度较大,采用常规工艺装置和生产手段,高熔点相变蜡产品难以获取(目前市场上的正构烷烃类相变蜡产品的最高熔点为74℃),所以,国内此类产品的生产一直受到限制,重要应用领域一直被进口产品代替。
技术实现要素:
4.为了解决相变蜡产品生产一直受到限制,重要应用领域一直被进口产品代替的问题,本技术提供了一种系列相变蜡的生产方法。
5.第一方面,本技术提供的一种系列相变蜡的生产方法,是通过以下技术方案得以实现的:一种系列相变蜡的生产方法,包括以下步骤:步骤一,原料评价及原料预处理;步骤二,提纯:薄膜蒸发分离技术对步骤一中的原料进行提纯;步骤三,精细分离:采用分子蒸馏切割技术对步骤二中的物料组分进行精细分离;步骤四,对步骤三中物料进行检测,当检测正构烷烃含量大于92%,通过熔融结晶分离技术再提纯,得半成品;步骤五,添加导热填料进行调合改性,筛选,得成品相变蜡。
6.通过采用上述技术方案,本技术将通过采用多种工艺相结合,所制备的有机正构烷烃类中高温系列相变储能材料,具有焓值高、熔程窄、稳定好的优点。且可根据不同的应用场合,生产从40℃~125℃的相变储能材料系列产品,填补了国内正构烷烃类中高温系列相变蜡的市场空白。
7.优选的,所述原料为c21~c120的长碳链烷烃,且c21~c120的长碳链正构烷烃含量不低于85%。
8.通过对原料的优化选择,可保证本技术生产的相变蜡的质量,且可降低生产难度,进而降低生产成本。
9.优选的,所述原料评价包括对原料进行气相色谱分析,检测原料中≤20物质的含量,当检测原料中c20以下物质的含量≤1%,则无须进行预处理,可直接进行提纯操作;当检测原料中c20及以下物质的含量》1%,进行预处理。
10.通过对原料的评价和对不规原料的预处理,可保证所采用原料的质量,进而保证本技术生产的相变蜡的质量,同时可降低生产难度和降低生产成本。
11.优选的,所述原料评价还包括对原料进行气相色谱分析,检测原料中c21~c120的长碳链正构烷烃含量,当c21~c120的长碳链正构烷烃含量大于85%,且原料中c20以下物质的含量≤1%,则无须进行预处理,可直接进行提纯操作;当c21~c120的长碳链正构烷烃含量大于85%,但原料中c20以下物质的含量》1%,则进行预处理;当c21~c120的长碳链正构烷烃含量≤85%,原料中c20以下物质的含量≤1%,则对原料进行异构烷烃转化为正构烷烃处理;当c21~c120的长碳链正构烷烃含量≤85%,原料中c20以下物质的含量》1%,则先进行预处理,后进行异构烷烃转化为正构烷烃处理。
12.通过对原料中c20以下物质的含量和c21~c120的长碳链正构烷烃含量的测定,可有效控制原料的质量,进而保证本技术生产的相变蜡的质量,同时可降低生产难度和降低生产成本。
13.优选的,所述预处理操作具体为,原料进行熔融、加氢、脱轻、分离、精制,得可利用原料。
14.通过采用上述技术方案,可工业化批量制备得到符合本技术要求的原料,保证本技术生产的相变蜡的质量同时降低生产成本。
15.优选的,所述预处理操作中的加氢工段,于230-350℃、压力在4.0-9.0mpa下,采用加氢催化剂,进行处理;所述加氢催化剂是由载体和活性组分构成;所述载体为二氧化硅、氧化铝、氧化铂、分子筛的复合体;所述活性组分为铂;所述活性组分的负载量为0.320-0.330;所述加氢催化剂的尺寸为φ1.8*3-6mm。
16.通过采用特定的催化剂可较为高效除去原料中的烯烃物质,进而改善c21~c120的长碳链正构烷烃含量,提升所需原料的品质。
17.优选的,所述异构烷烃转化为正构烷烃处理,将蜂窝状催化柱装载于固定床反应器,物料稳定控制在300-350℃,压力控制在2.0-2.5mpa,以气体空速v/v≥200h-1,将催化剂进行还原,然后通入c21~c120的长碳链正构烷烃含量≤85%的原料,于反应温度230-350℃下,液时空速为0.2—0.8h-1,循环氢(标况体积)/进料蜡(工况体积)≥为1000,进行异构烷烃转化为正构烷烃;所述蜂窝状催化柱中含有专用催化剂;催化剂是由载体和活性金属构成;所述载体为多孔二氧化硅、氧化铝、纳米二氧化钛、wo3/zro2中的一种;所述活性金属为zn、co、pt中的一种或多种组合;所述载体与活性金属的质量比为(50-150):1;所述活性金属以m-0键结合于载体表面,m为zn、co、pt中的一种。
18.通过采用上述技术方案,可将原料中的异构烷烃转化为正构烷烃,提升原料中正构烷烃的含量,不仅可提升所制备得到的相变蜡的质量,而且可有效降低生产难度,节约生产成本。
19.1.优选的,所述蜂窝状催化柱的蜂窝孔道的直径在1.5-3mm;所述蜂窝状催化柱是
由包括以下质量百分比的原料制备而成:15-20%无机粘合剂、10-20%专用催化剂、2-4%分散剂、0.5-2%脱模剂、10-20%为去离子水、余量为分子筛原粉;所述蜂窝状催化柱的制备方法,包括以下步骤:s1,分子筛原粉活化处理;s2,将完成活化处理的分子筛原粉与专用催化剂混合均匀,得混合料;s3,向所得混合料中加入无机粘合剂、分散剂、去离子水、脱模剂,混合均匀,得泥塑状物料;s4,将所得泥塑状物料注入模具中,于40-60℃下烘干0.5-1h,以1.0-2.0℃/min的加热速度,升温至90-100℃,维持10-15min得半成品;s5,半成品进行焙烧定型处理,于t=300-350℃,p=0.5-1.0mpa,体积比2-10%氢/氩气氛下,进行2-4h的焙烧,自然冷却散热,得成品。
20.通过采用上述技术方案,可批量化生产得到蜂窝状催化柱,降低整体的生产成本。此外,蜂窝状催化柱可有效地将异构烷烃转化为正构烷烃,提升原料中正构烷烃的含量,不仅可提升所制备得到的相变蜡的质量,而且可有效降低生产难度,节约生产成本。
21.优选的,所述步骤五中所述的导热填料占成品相变蜡总质量的0.2-1.0%;步骤五中所述的导热填料为石墨烯、石墨烯表面改性物、碳纳米管、碳纳米管表面改性物、氧化铝、氧化镁、氧化锌、氮化铝、氮化硼、碳化硅、硅微粉中的一种或者多种组合;所述石墨烯表面改性物包括第一负载体和接枝改性于第一负载体表面的石墨烯;所述第一负载体为氧化铝、氧化镁、氧化锌、氮化铝、氮化硼、碳化硅中的一种或多种组合;所述碳纳米管表面改性物包括第二负载体和接枝改性于第二负载体表面的多壁碳纳米管;所述第二负载体为氧化铝、氧化镁、氧化锌、氮化铝、氮化硼、碳化硅中的一种或多种组合;所述填料的粒径控制在0.10-5微米;所述成品相变蜡在25℃下测得的导热系数控制在1.2-3.0w/m*k。
22.通过导热填料的选择,可生产得到导热系数控制在1.2-3.0w/m*k的相变蜡产品,可满足不同客户的需求,更具市场竞争力。
23.优选的,所述步骤五中所述的导热填料是由碳纳米管表面改性物和氧化铝构成;所述碳纳米管表面改性物和氧化铝的质量比为(1-2):5;所述氧化铝是由以下不同粒度的氧化铝组成:《500nm的氧化铝0-5%,500nm-1000nm的氧化铝8-10%;1-2微米的氧化铝15-20%、3-5微米的氧化铝10-15%、余量为2-3微米的氧化铝;所述碳纳米管表面改性物为多壁碳纳米管接枝氧化铝,所述碳纳米管表面改性物中作为第二负载体的氧化铝粒径为200-300nm。
24.通过采用上述技术方案,在成品相变蜡颗粒内形成导热骨架,进而改善成品相变蜡颗粒的导热系数,且成品相变蜡颗粒的导热系数可通过导热填料的量进行调整,可满足不同客户的需求,更具市场竞争力。此外,对导热填料的种类和用量进行优化,在同等导热效果前提下,可降低导热填料用量,进而改善成品相变蜡的可储热热量,进一步提升产品的品质。
25.综上所述,本技术具有以下优点:1、本技术将通过采用多种工艺相结合,所制备的有机正构烷烃类中高温系列相变储能材料,具有焓值高、熔程窄、稳定好等优点。
26.2、本技术可根据不同的应用场合,生产从40℃~125℃的相变储能材料系列产品,
填补了国内正构烷烃类中高温系列相变蜡的市场空白。
27.3、本技术制备的相变蜡具有较高的焓值,在相变储热领域会有更大的市场,是最佳的储热材料。作为储热材料可有效实现工业余热的利用、峰谷电的调配、绿色能源的利用。1吨相变蜡可储热116268kcal的热量,相当于135.0kwh;若作为储热材料得到广泛应用,将在国家碳达峰、碳中和目标的实现过程中起到关键性的作用。
具体实施方式
28.以下结合制备例、对比例和实施例对本技术作进一步详细说明。
29.制备例制备例1专用催化剂的制备,包括以下步骤:步骤一,将26.0gzrocl2·
8h2o溶于250ml蒸馏水中,加入50ml质量百分浓度为25%的一水合氨搅拌均匀后在室温下陈化24h,将所得沉淀过滤、洗涤、100℃下干燥24小时,得到前驱体;步骤二,取11.0g上述得到的前驱体与含1.72g(nh4)6h2w
12o40
·
xh2o的水溶液等体积(浓度为0.14g/ml,体积为12ml)浸渍24h后,干燥、800℃空气气氛下焙烧3小时,得到固体超强酸载体wo3/zro2;步骤三,将0.11gzn(no3)2·
6h2o和0.10gco(no3)2·
6h2o混合后溶于5.0ml水中后采用等体积浸渍法将ni-cu双金属浸渍于wo3/zro2载体上(zn和co的含量为wo3/zro2的1.1%和1.2%),在100℃下干燥24小时,而后与空气气氛下在550℃焙烧3h,得到专用催化剂。(wo3/zro2的质量为催化剂质量的98%;zn和co的含量均为wo3/zro2的1%)制备例2专用催化剂;催化剂是由载体-介孔二氧化硅磁性微球(品牌亚美纳米)和活性金属构成。活性金属为zn、co、pt,且zn、co、pt的摩尔比为1:1:1,活性金属以m-0键结合于载体表面,m-0键为zn-o、co-o、pt-o。介孔二氧化硅磁性微球与活性金属的质量比为50:1。
30.专用催化剂的制备,包括以下步骤:步骤一,介孔二氧化硅磁性微球加入行星球磨机,以300rpm球磨30min,得多孔二氧化硅粉,备用;步骤二,将20g/l硝酸锌、20g/l硝酸钴、20g/l硝酸铂的水溶液加入步骤一中的多孔二氧化硅粉中,物料以过渡金属与载体的质量比为1:50进行配制,所得溶液置于44khz的超声条件下,进行60min超声分散处理,超声分散处理完成后以160r/min搅拌8h,得混合液;步骤三,步骤二中得到的混合溶液油浴加热,升温至100℃,蒸干溶剂,然后所得粉料采用行星球磨机进行球磨处理,球磨机于200r/min转速下充分研磨40min,得到固体粉末,将固体粉末在空气气氛和400℃的温度条件下加热处理2h,冷却到室温,转移至行星球磨机中,于120r/min转速下,研磨10min,即得所需的催化剂。
31.制备例3制备例3与制备例2的区别在于:介孔二氧化硅磁性微球与活性金属的质量比为100:1。
32.制备例4
制备例4与制备例2的区别在于:介孔二氧化硅磁性微球与活性金属的质量比为150:1。
33.制备例5制备例5与制备例2的区别在于:介孔二氧化硅磁性微球与活性金属的质量比为200:1。
34.制备例6蜂窝状催化柱的蜂窝孔道的直径在2.0mm。蜂窝状催化柱是由包括以下质量百分比的原料制备而成:20%无机粘合剂、10%制备例1中的专用催化剂、2.5%分散剂-聚羧酸盐、1.0%脱模剂、20%为去离子水、余量为分子筛原粉。
35.无机粘合剂是由占原料总质量8%的硅藻土、6%的膨润土、6%的凹凸棒土组成。分子筛原粉是由占原料总质量的16.5%的zsm-5分子筛、20%的4a分子筛、10%的5a分子筛粉、10%的13x分子筛粉。脱模剂是由0.4%的微晶蜡和0.6%的3000目滑石粉组成。
36.蜂窝状催化柱的制备方法,包括以下步骤:s1,分子筛原粉活化处理:将165g的zsm-5分子筛、200g的4a分子筛、100g的5a分子筛粉、100g的13x分子筛粉以300rpm混合搅拌30min,混合均匀后输入球磨机中,以300rpm球磨30min,完成球磨后置于200℃下处理30min;期间对硅藻土、膨润土、凹凸棒土进行球磨处理,以300rpm球磨30min,备用;s2,将s1中完成活化处理的分子筛原粉与100g的制备例1中专用催化剂以200rpm混合搅拌30min,得混合料;s3,向s2中所得混合料中加入80g硅藻土、60g膨润土、60g凹凸棒土、25g分散剂-聚羧酸盐、200g去离子水、4g微晶蜡和6g的3000目滑石粉,以120rpm混合搅拌60min,得泥塑状物料;s4,将所得泥塑状物料注入蜂窝状模具中,于60℃下烘干40min,以1.5℃/min的加热速度,升温至98℃,维持15min得半成品;s5,半成品进行焙烧定型处理,于t=350℃,p=0.6mpa,体积比4%氢/氩气氛下,进行4h的焙烧,自然冷却散热,得成品蜂窝状催化柱。
37.制备例7制备例7与制备例6的区别在于:蜂窝状催化柱的蜂窝孔道的直径在2.0mm。蜂窝状催化柱是由包括以下质量百分比的原料制备而成:20%无机粘合剂、15%制备例1中的专用催化剂、2.5%分散剂-聚羧酸盐、1.0%脱模剂、20%为去离子水、余量为分子筛原粉。
38.制备例8制备例8与制备例6的区别在于:蜂窝状催化柱的蜂窝孔道的直径在2.0mm。蜂窝状催化柱是由包括以下质量百分比的原料制备而成:20%无机粘合剂、20%制备例1中的专用催化剂、2.5%分散剂-聚羧酸盐、1.0%脱模剂、20%为去离子水、余量为分子筛原粉。
39.制备例9制备例9与制备例6的区别在于:蜂窝状催化柱的蜂窝孔道的直径在2.0mm。蜂窝状催化柱是由包括以下质量百分比的原料制备而成:20%无机粘合剂、10%制备例2中的专用催化剂、2.5%分散剂-聚羧酸盐、1.0%脱模剂、20%为去离子水、余量为分子筛原粉。
40.制备例10
制备例10与制备例6的区别在于:蜂窝状催化柱的蜂窝孔道的直径在2.0mm。蜂窝状催化柱是由包括以下质量百分比的原料制备而成:20%无机粘合剂、10%制备例3中的专用催化剂、2.5%分散剂-聚羧酸盐、1.0%脱模剂、20%为去离子水、余量为分子筛原粉。
41.制备例11制备例11与制备例6的区别在于:蜂窝状催化柱的蜂窝孔道的直径在2.0mm。蜂窝状催化柱是由包括以下质量百分比的原料制备而成:20%无机粘合剂、10%制备例4中的专用催化剂、2.5%分散剂-聚羧酸盐、1.0%脱模剂、20%为去离子水、余量为分子筛原粉。
42.制备例12制备例12与制备例6的区别在于:蜂窝状催化柱的蜂窝孔道的直径在2.0mm。蜂窝状催化柱是由包括以下质量百分比的原料制备而成:20%无机粘合剂、10%制备例5中的专用催化剂、2.5%分散剂-聚羧酸盐、1.0%脱模剂、20%为去离子水、余量为分子筛原粉。
43.制备例13导热填料是由碳纳米管表面改性物和氧化铝构成。碳纳米管表面改性物和氧化铝的质量比为1:5。
44.氧化铝为集料,是由以下不同粒度的氧化铝组成:《500nm的氧化铝0-5%,500nm-1000nm的氧化铝8-10%;1-2微米的氧化铝15-20%、3-5微米的氧化铝10-15%、余量为2-3微米的氧化铝。
45.碳纳米管表面改性物为多壁碳纳米管接枝氧化铝,多壁碳纳米管接枝氧化铝包括第二负载体-氮化铝和接枝改性于第二负载体表面的多壁碳纳米管,氧化铝粒径分别在200-300nm之间。
46.碳纳米管表面改性物的制备,包括以下步骤:步骤一:在室温条件下,将0.02mol的2-乙基-4-甲基咪唑2e4mi、0.01mol的醋酸银agac加入400ml的二氯甲烷中,磁力搅拌,转速240r/min,磁力搅拌时间控制在1-2小时,直至agac颗粒完全消失,得到澄清透明的ag(2e4mi)2ac络合物溶液;步骤二:在ag(2e4mi)2ac络合物溶液中加入0.5g的cnts、0.5g的pvp,采用超声分散(超声发生器的功率1200w,频率20khz)3小时,加入50克α-氧化铝,继续超声分散0.5小时,得分散液。
47.步骤三:将步骤二中所得分散液进行减压蒸馏处理,去除分散液中的二氯甲烷后将固体物进行高温烧结处理,高温烧结温度控制在210℃,高温烧结的时间为4小时,得固体物。
48.步骤四:将步骤三中所得的固体物置于三辊机(三辊机的辊距30μm)进行3次研磨粉碎,后分散于400ml乙醇,倒入篮式研磨机中进行研磨,以2000r/min的转速研磨0.5小时,然后过滤、干燥,即得al2o
3-cnts杂化材料。
49.制备例14制备例14与制备例13的区别在于:碳纳米管表面改性物和氧化铝的质量比为1.5:5。
50.制备例15制备例15与制备例13的区别在于:碳纳米管表面改性物和氧化铝的质量比为2:5。
51.制备例16
制备例16与制备例13的区别在于:碳纳米管表面改性物为氮化硼纳米片-碳纳米管导热填料。
52.氮化硼纳米片-碳纳米管导热填料的制备方法,包括如下步骤:1.1将12g尿素溶于100ml去离子水中,搅拌混合均匀,得到尿素溶液,向尿素溶液中加入200mg两种不同直径的氧化锆球磨珠和100mg的六方氮化硼粉末,搅拌混合均匀后放入超声机中,在超声频率为60khz的超声条件下进行球磨处理24h;球磨处理完毕后,去除球磨珠,得到球磨液,将球磨液在转速为2500rpm下离心10min,除去上清液后,用水洗涤3次,得到水洗产物,将水洗产物在70℃下真空干燥24h,得到氨基化氮化硼纳米片;其中,氧化锆球磨珠的直径为0.15mm和0.3mm,且直径为0.15mm和直径为0.3mm的氧化锆球磨珠的质量比为1:1;1.2称取80mg上述制得的氨基化氮化硼纳米片分散于45ml甲醇中,得到氨基化氮化硼纳米片溶液,将180mg六水合硝酸钴(以下简称co(no3)2·
6h2o)和5.1g 2-甲基咪唑分别溶于12ml甲醇中,得到硝酸钴溶液和2-甲基咪唑溶液;将硝酸钴溶液加入到氨基化氮化硼纳米片溶液中搅拌8min,得到混合液,向混合液中滴加2-甲基咪唑溶液,滴加完毕后,搅拌反应2h,将搅拌反应产物静置1h,再将搅拌产物在转速为10000rpm下离心8min,除去上清液后,用甲醇洗涤3次,得到醇洗产物,将醇洗产物在70℃下真空干燥24h,得到氮化硼纳米片-碳纳米管前驱体;1.3配制1wt%的聚乙烯醇水溶液作为粘结剂水溶液,按照每毫升粘结剂水溶液中氮化硼纳米片-碳纳米管前驱体的加入量为175mg,将氮化硼纳米片-碳纳米管前驱体和粘结剂水溶液搅拌30min,超声1h后,倒入模具中,再将模具放置在液氮上,利用液氮自下而上进行定向冷冻12h,放置在冻干机中冷冻干燥24h后,得到三维骨架,将三维骨架取出后放置于管式炉中在氩气气氛中进行煅烧,煅烧温度为900℃,煅烧时间为8h,得到氮化硼纳米片-碳纳米管导热填料。
53.制备例17导热填料是由氧化铝构成。氧化铝为集料,是由以下不同粒度的氧化铝组成:《500nm的氧化铝0-5%,500nm-1000nm的氧化铝8-10%;1-2微米的氧化铝15-20%、3-5微米的氧化铝10-15%、余量为2-3微米的氧化铝。
54.制备例18导热填料是由氧化铝构成。氧化铝不为集料,氧化铝的粒度为2-3微米。
55.制备例19制备例19与制备例13的区别在于:碳纳米管表面改性物和氧化铝的质量比为3:5。
56.制备例20制备例20与制备例13的区别在于:碳纳米管表面改性物和氧化铝的质量比为0.5:5。实施例
57.实施例1一种系列相变蜡的生产方法,包括以下步骤:步骤一,原料评价及原料预处理,对原料进行气相色谱分析,检测原料中c21~c120的长碳链正构烷烃含量和c20以下物质的含量;原料为精炼费托蜡(冻凝点:89.5℃;滴
熔点:92.3℃;-32℃的含油量为0.32;赛波特色号: 25;25℃的针入度1.0mm;120℃的运动粘度:9.3mm2/s,且原料不含芳烃、铅、砷等毒害物质,碳原值峰值为c58),选购于浙江皇星化工股份有限公司所售卖的牌号为fr90的精馏费托蜡。
58.当c21~c120的长碳链正构烷烃含量大于85%,且原料中c20以下物质的含量≤1%,则无须进行预处理,可直接进行下一步操作-提纯;当c21~c120的长碳链正构烷烃含量大于85%,但原料中c20以下物质的含量》1%,则进行预处理;预处理操作具体为:s1,将原料加热至145-150℃进行熔融呈液体;s2,加氢反应,将加氢催化剂-型号jy-1013-01催化剂(加氢催化剂是由载体和活性组分-铂构成,载体为二氧化硅、氧化铝、氧化铂、分子筛的复合体,活性组分-铂的负载量为0.320-0.330,且加氢催化剂的尺寸为φ1.8*3mm)装载于固定床反应器中,固定床反应器中的物料温度控制在320℃,压力控制在5.0mpa,以气体空速v/v=200,将加氢催化剂进行还原,然后通入c21~c120的长碳链正构烷烃含量大于85%的原料,于反应温度350℃下,压力为2.0mpa,液时空速为0.8h-1
,循环氢(标况体积)/进料蜡(工况体积)为1000,加氢反应;s3,脱轻、分离、精制,得可利用原料,将可利用原料用于下一步提纯处理;当c21~c120的长碳链正构烷烃含量≤85%,原料中c20以下物质的含量≤1%,则对原料进行异构烷烃转化为正构烷烃处理,异构烷烃转化为正构烷烃处理,将制备例中制备的6蜂窝状催化柱装载于固定床反应器中,物料稳定控制在350℃,压力控制在2.5mpa,以气体空速v/v=220h-1
,将催化剂进行还原,然后通入c21~c120的长碳链正构烷烃含量≤85%且c20以下物质的含量≤1%的原料,于反应温度350℃下,液时空速为0.6h-1
,循环氢(标况体积)/进料蜡(工况体积)为1040,将原料中的异构烷烃转化为正构烷烃,得可利用原料,将可利用原料用于下一步提纯处理;当c21~c120的长碳链正构烷烃含量≤85%,原料中c20以下物质的含量》1%,则先进行预处理,后进行异构烷烃转化为正构烷烃处理;步骤二,将经过加氢预处理的可利用原料输入薄膜蒸发器中进行薄膜蒸发处理,分离得到碳范围≤c20的轻相组分、碳范围>c21的重相组分。具体地,调节刮膜蒸发器的夹套加热温度为260℃,管道伴热温度为180℃,蒸发压力为500pa,打开冷凝器冷却水,调节低温水温度为70℃,调节转速为200rpm;将处于熔融状态的原料通过进料泵送入刮膜蒸发器内,原料中的轻相组分向上蒸发,重相组分b0向下积累,采用气相色谱法检测重相组分b0中碳范围≤c20的含量,直至检测重相组分b0中碳范围≤c20的含量<0.4%,获得碳范围>c21的重相组分b0,当重相组分b0接收槽内的液位累积至20%时,开启出料泵使重相组分b0出料;步骤三,将步骤二中所得重相组分b0输入分子蒸馏装置内,进行多级升温分子蒸馏处理;s3.1、对重相组分b0进行一级分子蒸馏,使一级分子蒸馏器内冷器接通冷凝水,一级分子蒸馏器的下端接冷阱,打开导热油循环泵,调节导热油温度为280℃,导热油将热量传递至一级分子蒸馏的加热面,使导热油的进油温度与出油温度的温差<10℃,降低在分子蒸馏过程中因重相组分b0吸热而使加热面温度降低的可能性,提高传质与传热效率。调节加压冷凝水温度为80℃,加压冷凝水将冷量传递给一级分子蒸馏器的冷凝面。调节转子
转速200rpm,调节真空度为12pa,向一级分子蒸馏器中进料,处于熔融状态的重相组分b0,通过一级分子蒸馏器分离出轻相组分c1、重相组分c2。轻相组分c1接收槽和重相组分c2接收槽的液位开始累积,及时从重相组分c2接收槽内取样,采用气相色谱法检测重相组分c2中c20-c30含量,直至检测重相组分c2中c20-c30含量<0.7%,获得重相组分c2,当重相组分c2接收槽内的重相液位累积至20%时,开启出料泵使重相组分c2出料;s3.2、对重相组分c2进行二级分子蒸馏,使二级分子蒸馏器内冷器接通冷凝水,二级分子蒸馏器的下端接冷阱,打开导热油循环泵,调节导热油温度为290℃,使导热油的进油温度与出油温度的温差<10℃。调节加压冷凝水温度为90℃,调节转子转速200rpm,调节真空度为10pa。将步骤s3.1中处于熔融状态的重相组分c2泵入进料罐,通过进料泵泵入二级分子蒸馏器内,通过二级分子蒸馏器分离出轻相组分d1、重相组分d2,轻相组分d1接收槽和重相组分d2接收槽的液位开始累积。及时从重相组分d2接收槽内取样,采用气相色谱法检测重相组分d2中c30-c40含量,直至重相组分d2中c30-c40含量<1.3%,获得重相组分d2。当重相组分d2接收槽内的重相液位累积至20%时,开启出料泵使重相组分d2出料;s3.3、对重相组分d2进行三级分子蒸馏,使三级分子蒸馏器内冷器接通冷凝水,三级分子蒸馏器的下端接冷阱,打开导热油循环泵,调节导热油温度为300℃,调节转子转速200rpm,使导热油的进油温度与出油温度的温差<8℃。调节加压冷凝水温度为110℃,调节真空度为2pa。将步骤s3.2中处于熔融状态的重相组分d2通过进料泵泵入至三级分子蒸馏器内,通过三级分子蒸馏分离出轻相组分e1、重相组分e2,轻相组分e1接收槽和重相组分e2接收槽的液位开始累积。及时从重相组分e2接收槽内取样,采用气相色谱法分析重相组分e2的碳排布,直至检测重相组分e2的碳原子峰值cmax在c60-c64之间,且重相组分e2中碳含量≥c61占有76%以上,获得重相组分e2、轻相组分e1。当重相组分e2接收槽内的重相液位累积至20%时,开启出料泵使重相组分e2出料;s3.4、轻相组分e1碳原子分布在c38-c64,温控至125-130℃,于加热面温度为300℃、冷却面温度为110℃且绝对压力为10-15pa下进行分子蒸馏处理,得到预处理产品,通过dsc差示扫描量热分析和气相色谱测得其碳分布为c39-c62、相变的碳峰值为c49、正构烷烃含量为93.8%且相变焓值为220kj/kg;分子蒸馏装置内冷凝面与加热面的间距为d0,精炼费托蜡的平均自由程大于d0;步骤四,对步骤三中e1物料进行检测,当检测正构烷烃含量大于92%,通过熔融结晶分离技术再提纯,s41,多级结晶处理,具体包括以下步骤:s411,将s3.4中制得的e1产品以4℃/h的速率降温1h后,保温处理1h;s412,重复步骤s411,直至温度达到t1℃后,保温处理8h制得结晶混合物a,其中t1的温度为t
0-29℃;s42,多级发汗处理,其具体包括以下步骤:s421,第一步升温,将步骤s412中制得的结晶混合物a以3℃/h的速率升温2h后,恒温处理1h;s422,重复步骤s421,直至温度达到t2℃,其中t2的温度为t
0-10℃,即第一滴发汗液出现时,得到粗制产品a;s423,第二步升温,将步骤s422中制得的粗制产品a以1℃/h的速率升温2h后,恒温
处理1h;s424,重复步骤s423,直至dsc差示扫描量热分析检测的相变焓值达到预设相变焓值220kj/kg后,停止反应,制备得到相变温度为t
x
℃的目标产品,本实施例中t
x
为91.1℃,目标产品的产品收率≥50%,且目标产品最终通过dsc差示扫描量热分析和气相色谱测得其相变焓值为226.3kj/kg、熔程为9.6℃、碳分布为c44-c62、碳峰值为c50;s425,脱色精制,s424中的物料置于在固定床反应器内,固定床反应器加入牌号为jy-1012-01的加氢催化剂,调节加氢温度为320℃,加氢压力为5.0mpa,氢油比700,液时空速为2h-1
,使物料通过装有牌号为jy-1013-01的加氢催化剂的固定床反应器,完成加氢反应的物料输入脱色过滤器机中进行脱色处理;步骤五,向步骤四中的物料中添加制备例13中的导热填料,添加导热填的用量为占成品相变蜡总质量的0.6%,搅拌转速为300rpm,搅拌10.0h,造粒筛选,得成品相变蜡颗粒。
59.因此,本技术实施例的工艺中可切分出5种不同系列的相变蜡产品。本技术中用于进行试验测试的是步骤s424中获得的相变蜡产品,碳分布为c44-c62、碳峰值为c50。
60.实施例2实施例2与实施例1的区别在:对原料进行异构烷烃转化为正构烷烃处理中的蜂窝状催化柱为制备例7中的蜂窝状催化柱。
61.实施例3实施例3与实施例1的区别在:对原料进行异构烷烃转化为正构烷烃处理中的蜂窝状催化柱为制备例8中的蜂窝状催化柱。
62.实施例4实施例4与实施例1的区别在:对原料进行异构烷烃转化为正构烷烃处理中的蜂窝状催化柱为制备例9中的蜂窝状催化柱。
63.实施例5实施例5与实施例1的区别在:对原料进行异构烷烃转化为正构烷烃处理中的蜂窝状催化柱为制备例10中的蜂窝状催化柱。
64.实施例6实施例6与实施例1的区别在:对原料进行异构烷烃转化为正构烷烃处理中的蜂窝状催化柱为制备例11中的蜂窝状催化柱。
65.实施例7实施例7与实施例1的区别在:导热填料采用制备例13中的导热填料,导热填料用量为占成品相变蜡总质量的0.4%。
66.实施例8实施例8与实施例1的区别在:导热填料采用制备例14中的导热填料。
67.实施例9实施例9与实施例1的区别在:导热填料采用制备例15中的导热填料。
68.实施例10实施例10与实施例1的区别在:导热填料采用制备例16中的导热填料。
69.实施例11
实施例11与实施例1的区别在:步骤五,向步骤四中的物料中添加制备例12中的导热填料,添加导热填料的用量为占成品相变蜡总质量的0.2%,搅拌转速为300rpm,搅拌10.0h,造粒筛选,得成品相变蜡颗粒。
70.实施例12实施例12与实施例1的区别在:步骤五,向步骤四中的物料中添加制备例12中的导热填料,添加导热填料的用量为占成品相变蜡总质量的1.0%,搅拌转速为300rpm,搅拌10.0h,造粒筛选,得成品相变蜡颗粒。
71.对比例对比例1对比例1与实施例1的区别在:对原料进行异构烷烃转化为正构烷烃处理中的蜂窝状催化柱为制备例12中的蜂窝状催化柱。
72.对比例2对比例2与实施例1的区别在:导热填料采用制备例17中的导热填料。
73.对比例3对比例3与实施例7的区别在:导热填料采用制备例18中的导热填料。
74.对比例4对比例4与实施例7的区别在:导热填料采用制备例19中的导热填料。
75.对比例5对比例5与实施例1的区别在:导热填料采用制备例20中的导热填料。
76.对比例6对比例6与实施例1的区别在:步骤五,向步骤四中的物料中添加制备例12中的导热填料,添加导热填的用量为占成品相变蜡总质量的0.1%,搅拌转速为300rpm,搅拌10.0h,造粒筛选,得成品相变蜡颗粒。
77.对比例7对比例7与实施例1的区别在:步骤五,向步骤四中的物料中添加制备例12中的导热填料,添加导热填的用量为占成品相变蜡总质量的1.5%,搅拌转速为300rpm,搅拌10.0h,造粒筛选,得成品相变蜡颗粒。
78.对比例8对比例8与实施例1的区别在:步骤五,向步骤四中的物料中添加制备例18中的导热填料,添加导热填的用量为占成品相变蜡总质量的3.2%,搅拌转速为300rpm,搅拌10.0h,造粒筛选,得成品相变蜡颗粒。
79.性能检测试验检测方法/试验方法1.相变温度:按astm d4419的标准,对实施例1-12和对比例1-8制得的目标产品进行差示扫描量热检测,测定相应产品的相变温度。
80.2.相变焓值:按astm e-793的标准,对实施例1-12和对比例1-8制得的目标产品进行差示扫描量热检测,测定相应产品的相变温度。
81.3、导热系数的测定:参照gb/t 10297-1998《非金属固体材料导热系数的测定方法热线法》测定。
82.数据分析表1是实施例1-12和对比例1-8的测试参数表2是实施例1-6和对比例1的步骤一中异构烷烃转化为正构烷烃处理后含有长碳链正构烷烃含量对比表面
结合实施例1-12和对比例1-8并结合表1-2可以看出,制备例6-11制备的蜂窝状催化柱可对异构化烷烃进行催化处理,发生异构化烷烃转化为正构烷烃转变,可提升原料的质量,进而降低生产成本。
83.结合实施例1-12和对比例1-8并结合表1-2可以看出,蜂窝状催化柱中专用催化剂含量控制10-20%且专用催化剂中载体与活性金属质量比控制在50-150:1时,不仅可发生异构化烷烃转化为正构烷烃转变,可提升原料的质量,而且可蜂窝状催化柱的生产成本,进而降低整体的生产成本。
84.结合实施例1-12和对比例1-8并结合表1可以看出,实施例1中相变蜡的导热系数大于对比例2中相变蜡的导热系数,且实施例1中相变蜡的相变焓和相变温度与对比例2中相变蜡的相变焓和相变温度相接近,因此,导热填料以碳纳米管表面改性物和氧化铝的质量比为1:5配制添加至相变蜡中所带来的导热性能优于单纯氧化铝集料作为导热填料添加至相变蜡中所带来的导热性能,因此,导热填料以碳纳米管表面改性物和氧化铝复配,赋予了本技术相变蜡较好的导热性能。
85.结合实施例1-12和对比例1-8并结合表1可以看出,对比例2中相变蜡的导热系数大于对比例3中相变蜡的导热系数,且对比例2中相变蜡的相变焓和相变温度与对比例3中相变蜡的相变焓和相变温度相接近,因此,导热填料为氧化铝集料添加至相变蜡中所带来的导热性能优于非氧化铝集料作为导热填料添加至相变蜡中所带来的导热性能,因此,导热填料为氧化铝集料可赋予了本技术相变蜡较好的导热性能。
86.结合实施例1-12和对比例1-8并结合表1可以看出,实施例7-9中相变蜡的导热系数相差较小且皆大于对比例5中相变蜡的导热系数,与对比例4对比例5的导热系数相接近,实施例7-9中相变蜡的相变焓和相变温度与对比例4-5中相变蜡的相变焓和相变温度相接近,因此,碳纳米管表面改性物和氧化铝的质量比为(1-2):5,本技术相变蜡具有较好导热性的同时生产成本较低。
87.结合实施例1-12和对比例1-8并结合表1可以看出,实施例1、11-12中相变蜡的导热系数大于对比例6中相变蜡的导热系数,且与对比例7中相变蜡的导热系数相差不大,实施例1、11-12中相变蜡的相变焓和相变温度与对比例6-7中相变蜡的相变焓和相变温度相接近,因此,导热填料占成品相变蜡总质量的0.2-1.0%时,本技术相变蜡具有较好导热性的同时生产成本较低。
88.结合实施例1-12和对比例1-8并结合表1可以看出,实施例1中相变蜡的导热系数与对比例8中相变蜡的导热系数相近,实施例1中相变蜡的相变焓和相变温度与对比例8中相变蜡的相变焓和相变温度相接近,因此,导热填料由碳纳米管表面改性物和氧化铝的质量比为1:5复配且以占成品相变蜡总质量的0.6%添加至相变蜡中所带来的导热性能等于纯氧化铝集料作为导热填料且以占成品相变蜡总质量的2.8%添加至相变蜡中所带来的导热性能,采用本技术中复配的导热填料,可在保证相变蜡导热性能和相变焓的前提下,减少
导热填料的使用量,进而提升产品整体的相变储能和热敏性。
89.本具体实施例仅仅是对本技术的解释,其并不是对本技术的限制,本领域技术人员在阅读完本说明书后可以根据需要对本实施例做出没有创造性贡献的修改,但只要在本技术的权利要求范围内都受到专利法的保护。
再多了解一些
本文用于企业家、创业者技术爱好者查询,结果仅供参考。