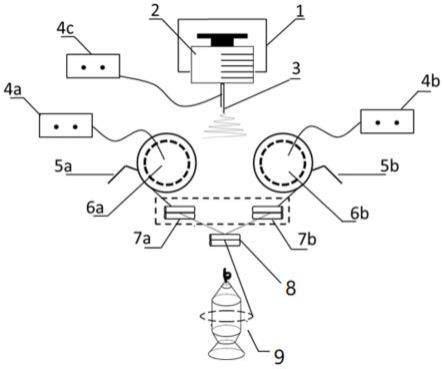
1.本发明属于纺织技术领域,具体涉及一种纳米纤维纱线及其连续成纱方法。
背景技术:
2.随着纳米技术的兴起,20世纪80年代以后,能够纺出纳米纤维的静电纺丝技术受到了广泛的关注,静电纺丝的成型原理是带电荷的高分子溶液或熔体在静电场中流动和变形,当带有相同电荷的液滴之间排斥力大于表面张力时,就能使液滴彼此分离并产生变形,作圆锥状,待溶液蒸发或溶剂冷却后,三维无序液滴经收集可得到纳米级纤维。静电纺丝得到的纤维直径要明显小于常规方式下得到的纤维,这一特点也使单根纤维具有更大的比表面积和吸附能力,通过静电纺丝技术生产的非织造材料能够应用于一些高精密电子器件和过滤防护材料等领域,在生物医学工程中,静电纺丝形成的纳米纤维结构也基本能满足组织工程支架的要求。然而,纳米级尺寸同时也导致静电纺丝纤维的力学性能比传统短纤和长丝差的多,在纺丝和成纱过程中容易发生磨损,不易成型等问题,同时目前纳米纤维的成纱过程基本为间歇式操作,难以连续性生产。
技术实现要素:
3.本发明所要解决的技术问题是克服现有技术中的不足,提供一种新的纳米纤维纱线的生产方法,该方法不仅可以连续生产,而且制成的纳米纤维纱线不借助于其他纤维成纱,使得制成的纳米纤维纱线能够最大化地保留纳米纤维的各项优异性能,同时还克服了现有纳米纤维存在的成纱过程易产生毛羽、力学强度差等问题。
4.本发明同时还提供了上述方法生产的纳米纤维纱线。
5.为解决以上技术问题,本发明采取的一种技术方案如下:一种纳米纤维纱线的连续成纱方法,所述连续成纱方法包括如下步骤:
6.采用静电纺丝方法纺出纳米纤维,使纺出的纳米纤维在运动过程中、在n个电场力作用下分裂为n份,n为大于或等于2的整数;
7.采用多个分别能够转动的集束导轮独立地收集各自对应的每份纳米纤维,并在所述集束导轮的作用下使每份纳米纤维进行取向和牵伸,形成附着在所述集束导轮上的纳米纤维集聚体;
8.在外力作用下从每个所述集束导轮上的所述纳米纤维集聚体中起出一条连续的纳米纤维集束,各条纳米纤维集束在独立地经过初步加捻后进行混合加捻,连续获得纳米纤维纱线。
9.根据本发明的一些优选方面,所述静电纺丝方法采用单针纺丝针头进行静电纺丝,各个所述电场力分别形成在所述单针头与各个所述集束导轮之间。
10.根据本发明的一些优选方面,所述电场力为能够通过所述单针纺丝针头与各个所述集束导轮之间的电压差和/或所述单针纺丝针头与各个所述集束导轮之间的距离大小进行调节的可调形式电场力。
11.根据本发明的一些优选且具体的方面,各个所述集束导轮的中心共面且与水平面平行,所述单针纺丝针头的出口方向的延伸线垂直于所述水平面,且控制所述单针纺丝针头的出口与各个所述集束导轮的中心共同形成的平面之间的距离为10-30cm。
12.根据本发明的一些优选方面,所述集束导轮包括能够沿自身轴心线转动的绝缘套管以及绕设在所述绝缘套管上的导电金属环,所述纳米纤维集聚体附着在所述导电金属环的外侧。
13.根据本发明的一些优选且具体的方面,所述导电金属环的半径为3-10cm。
14.根据本发明的一些优选方面,所述初步加捻采用初捻工作辊,所述混合加捻采用混捻工作辊;
15.所述连续成纱方法还包括通过采用控制系统分别独立地控制:
16.各个所述集束导轮的转速、温度;
17.各个所述初捻工作辊的捻度、温度;
18.所述混捻工作辊的捻度、温度;
19.各个所述电场力。
20.根据本发明的一些优选方面,所述连续成纱方法采用如下连续生产装置进行:
21.所述连续生产装置包括依次设置的静电纺丝机构、多个集束导轮、多个刮刀、多个初捻工作辊、混捻工作辊和纱线连续收集组件,以及多个加压电源;所述静电纺丝机构与一个所述加压电源的正极电连接,每个所述集束导轮分别独立地与一个所述加压电源的负极电连接,所述刮刀的数量与所述集束导轮一一对应且设置在所述集束导轮的旁侧;
22.所述静电纺丝机构包括用于纺出纳米纤维的单针纺丝针头;
23.所述集束导轮包括能够沿自身轴心线转动的绝缘套管以及绕设在所述绝缘套管上的导电金属环;
24.在生产过程中,每个所述集束导轮与所述静电纺丝机构之间均形成一个电场力,由单针纺丝针头纺出的纳米纤维在各个所述电场力的作用下分裂为n份,并朝向各自对应的所述集束导轮运动进而附着在所述导电金属环的外侧,形成纳米纤维集聚体,然后在所述集束导轮转动的过程中,在每个所述刮刀的作用下从对应的所述集束导轮上的纳米纤维集聚体上起出一条连续的纳米纤维集束,各条纳米纤维集束在独立地经过各自对应的所述初捻工作辊进行初步加捻后由所述混捻工作辊进行混合加捻,连续获得纳米纤维纱线,并由所述纱线连续收集组件收集。
25.根据本发明的一些优选方面,所述连续生产装置还包括控制系统,所述控制系统分别与所述静电纺丝机构、所述多个集束导轮、所述的多个初捻工作辊、所述混捻工作辊、所述纱线连续收集组件、所述的多个加压电源通信连接。
26.本发明提供的又一技术方案:一种上述所述的纳米纤维纱线的连续成纱方法生产的纳米纤维纱线。
27.由于以上技术方案的采用,本发明与现有技术相比具有如下优点:
28.在本发明中,创新性地在静电纺丝过程中引入其它电场力,使纺出的纳米纤维不仅可以分裂成多份,而且还能够在电场力的作用下更加紧密地在集束导轮中缠结,并能够通过转动的集束导轮获得一定取向和牵伸,形成附着在集束导轮上的纳米纤维集聚体,然后在外力作用下起出纳米纤维集束,各条纳米纤维集束在独立地经过初步加捻后进行混合
加捻,获得纳米纤维纱线,该过程不仅实现了纳米纤维纱线的连续生产,而且构成纳米纤维纱线的各子组分在混合加捻前均可以独立地控制,进而可以赋予各子组分不同的性能,从而使得混合加捻后纱线具有特殊性能,例如可以赋予纱线更好的弹性回复率,尤其是本发明纳米纤维纱线的生产过程中并未借助于其它纤维,使得制成的纱线能够最大化地保留纳米纤维的各项优异性能,同时还避免了传统纳米纤维成纱过程易产生毛羽、力学强度不够不易成型等问题,提高了静电纺丝的生产效率,提供了制备功能性纱线的新思路,为纳米纤维在产业用领域提供了更多的可能性。
附图说明
29.图1为本发明实施例中纳米纤维纱线的连续成纱方法所采用的的连续生产装置的结构示意图;
30.图2为本发明实施例中采用的集束导轮的结构示意图;
31.图3为本发明实施例中纺丝距离的示意性图示;
32.图4为本发明实施例5所制成的纳米纤维纱线不同状态下结构示意图;
33.图5为本发明实施例中起拱高度的示意性图示;
34.其中,1、推进组件;2、储液注射器;3、单针纺丝针头;4a/4b/4c、加压电源;5a/5b、刮刀;6a/6b、集束导轮;6-1、绝缘套管;6-2、导电铜条;7a/7b、初捻工作辊;8、混捻工作辊;9、纱线连续收集组件;h1、纺丝距离;h2、起拱高度。
具体实施方式
35.以下结合具体实施例对上述方案做进一步说明;应理解,这些实施例是用于说明本发明的基本原理、主要特征和优点,而本发明不受以下实施例的范围限制;实施例中采用的实施条件可以根据具体要求做进一步调整,未注明的实施条件通常为常规实验中的条件。
36.下述中,如无特殊说明,所有的原料基本来自于商购或者通过本领域的常规方法制备而得。
37.实施例1
38.本例提供一种纳米纤维纱线及其连续成纱方法。本例采用的原料聚砜(psf)颗粒(购自东莞市川澳工程塑胶原料有限公司,牌号:p-1710)。
39.本例中,该连续成纱方法包括如下步骤:采用静电纺丝方法纺出纳米纤维,使纺出的纳米纤维在运动过程中、在2个电场力作用下分裂为2份;
40.进一步地,静电纺丝采用的静电纺丝原液通过如下方法制备:将聚砜(psf)颗粒10g溶解于二甲基乙酰胺(dmac)90g中,得到混合溶液,放入磁子,置于容器中密封处理并置于水浴锅中高温加热,水浴锅温度为80℃,加热时间为2h,加热完毕,取出静置0.5h,获得质量分数为10wt%的透明均一的溶液,即为静电纺丝原液。
41.同时,本例中,静电纺丝方法采用单针纺丝针头进行静电纺丝,纺丝参数控制在电压为10kv,喷口孔径为0.5mm,溶液流速2ml/h,环境温度25℃,空气相对湿度65%。
42.采用2个分别能够转动的集束导轮独立地收集各自对应的每份纳米纤维,并在集束导轮的作用下使每份纳米纤维进行取向和牵伸,形成附着在集束导轮上的纳米纤维集聚
体;
43.在外力作用下从每个集束导轮上的纳米纤维集聚体中起出一条连续的纳米纤维集束,各条纳米纤维集束在独立地经过初步加捻后进行混合加捻,连续获得纳米纤维纱线。
44.本例中,各个电场力分别形成在单针头与各个集束导轮之间,电场力为能够通过单针纺丝针头与各个集束导轮之间的电压差和/或单针纺丝针头与各个集束导轮之间的距离大小进行调节的可调形式电场力,各个集束导轮的中心共面且与水平面平行,单针纺丝针头的出口方向的延伸线垂直于水平面,且控制单针纺丝针头的出口与各个集束导轮的中心共同形成的平面之间的纺丝距离为20cm。进一步地,集束导轮包括能够沿自身轴心线转动的绝缘套管以及绕设在绝缘套管上的导电金属环,纳米纤维集聚体附着在导电金属环的外侧,导电金属环的半径为5cm,2个集束导轮的转速均为200r/min,外加电压为-10kv。
45.本例中,初步加捻采用初捻工作辊,混合加捻采用混捻工作辊;
46.该连续成纱方法还包括通过采用控制系统分别独立地控制:各个集束导轮的转速、温度;各个初捻工作辊的捻度、温度;混捻工作辊的捻度、温度;各个所述电场力。进一步地,本例中,控制2个初捻工作辊的捻度均为600t/m,其中一个初捻工作辊的温度为120℃,另一个初捻工作辊的温度为180℃,混捻工作辊的加捻温度为120℃,捻度为800t/m。
47.下面结合附图对本发明上述连续生产方法进行进一步说明。
48.具体地,如图1-3所示,本例的连续成纱方法采用如下连续生产装置进行:
49.该连续生产装置包括依次设置的静电纺丝机构、2个集束导轮(本例中分列于左右两侧,图1中分别采用6a、6b标识)、2个刮刀(本例中分列于左右两侧,图1中分别采用5a、5b标识)、2个初捻工作辊(本例中分列于左右两侧,图1中分别采用7a、7b标识)、混捻工作辊8和纱线连续收集组件9,以及多个加压电源(本例中设置有3个,图1中分别采用4a、4b、4c标识,静电纺丝机构与一个加压电源的正极电连接,2个集束导轮分别独立地与一个加压电源的负极电连接);刮刀设置在集束导轮的旁侧;
50.其中静电纺丝机构包括用于调节静电纺丝原液流出速度的推进组件1、用于导通静电纺丝原液的储液注射器2、用于纺出纳米纤维且与储液注射器2连通的单针纺丝针头3;
51.如图2所示,该图示例性地给出了集束导轮的结构示意图,该集束导轮包括能够沿自身轴心线转动的绝缘套管6-1以及绕设在绝缘套管6-1上的导电金属环(本例采用铜,制成导电铜条6-2);
52.本例中,2个集束导轮的中心共面且与水平面平行,单针纺丝针头的出口方向的延伸线垂直于水平面,且控制单针纺丝针头的出口与各个集束导轮的中心共同形成的平面之间的纺丝距离h1为20cm。
53.在生产过程中,每个集束导轮与静电纺丝机构之间均形成一个电场力,由单针纺丝针头纺出的纳米纤维在各个所述电场力的作用下分裂为n份,并朝向各自对应的集束导轮运动进而在集束导轮转动的过程中附着在导电金属环的外侧并获得了一定的取向和牵伸,形成纳米纤维集聚体,然后在集束导轮转动的过程中,在每个刮刀的作用下从对应的集束导轮上的纳米纤维集聚体上起出一条连续的纳米纤维集束,各条纳米纤维集束在独立地经过各自对应的初捻工作辊进行初步加捻后由混捻工作辊8进行混合加捻,连续获得纳米纤维纱线,并由纱线连续收集组件9收集。
54.进一步地,该连续生产装置还包括控制系统,该控制系统分别与静电纺丝机构、2
个集束导轮、2个初捻工作辊、混捻工作辊、纱线连续收集组件、3个加压电源通信连接,进而可以根据预设程序或者实时输入的数据控制各个部件的运行参数。
55.本例的上述装置实现了从松散的纳米纤维集束到可纺纳米纤维纱线的转变,纱线的强力也进一步得到改善,实现纳米纤维纺纱过程的持续进行,表面毛羽得以改善。
56.对比例1
57.用实施例1中制备的均一静电纺丝原液在相同纺丝条件下进行纺丝,用单集束导轮进行收集,单集束导轮同实施例1中工作参数,制备对照样1。
58.实施例2
59.本例提供一种纳米纤维纱线及其连续成纱方法,基本同实施例1,其区别仅在于:
60.(1)静电纺丝原液通过如下方法获得:将经脱胶后的丝素蛋白(sf,购自北京永康乐业科技发展有限公司,牌号:sp110)粉末10g溶解于六氟丙醇(hfip)90g中,得到混合溶液,放入磁子,置于容器中密封处理并置于水浴锅中加热,水浴锅温度为40℃,加热时间为5h,加热完毕,取出静置1h,获得质量分数为10wt%的透明均一的溶液;
61.(2)静电纺丝条件:电压为20kv,喷口孔径为0.4mm,溶液流速0.5ml/h,纺丝距离h1为25cm;
62.(3)2个初捻工作辊的温度为30℃,混捻工作辊的的加捻温度为20℃。
63.对比例2
64.用实施例2中制备的均一静电纺丝原液在相同纺丝条件下进行纺丝,用单集束导轮进行收集,单集束导轮同实施例2中工作参数,制备对照样2。
65.实施例3
66.本例提供一种纳米纤维纱线及其连续成纱方法,基本同实施例1,其区别仅在于:
67.(1)静电纺丝原液通过如下方法获得:将聚丙烯腈(pan,购自上海阿拉丁生化科技股份有限公司,牌号:p303197)粉末10g溶解于二甲基甲酰胺(dmf)90g中,得到混合溶液,放入磁子,置于容器中密封处理并置于水浴锅中高温加热,水浴锅温度为70℃,加热时间为5h,加热完毕,取出静置1h,获得质量分数为10wt%的透明均一的溶液;
68.(2)静电纺丝条件:喷口孔径为0.4mm;
69.(3)左侧集束导轮的转速为200r/min,导电金属环的半径为5cm;
70.右侧集束导轮的转速为100r/min,导电金属环的半径为10cm;
71.(4)2个初捻工作辊的温度为50℃;
72.(5)混捻工作辊的的加捻温度为60℃。
73.对比例3
74.用实施例3中制备的均一静电纺丝原液在相同纺丝条件下进行纺丝,用单集束导轮进行收集,单集束导轮同实施例3中工作参数,制备对照样3。
75.实施例4
76.本例提供一种纳米纤维纱线及其连续成纱方法,基本同实施例3,其区别仅在于:
77.(1)左侧集束导轮的转速为300r/min,导电金属环的半径为5cm,导轮加热至80℃;
78.右侧集束导轮的转速为100r/min,导电金属环的半径为15cm;
79.(2)混捻工作辊的的加捻温度为70℃。
80.实施例5
81.本例提供一种纳米纤维纱线及其连续成纱方法,基本同实施例3,其区别仅在于:
82.(1)左侧集束导轮的转速为200r/min,导电金属环的半径为5cm,导轮加热至60℃;
83.右侧集束导轮的转速为150r/min,导电金属环的半径为10cm,导轮加热至50℃;
84.(2)左侧初捻工作辊的预加捻度为600t/m,右侧初捻工作辊的预加捻度为800t/m,2个初捻工作辊的温度为50℃;
85.(3)控制初捻工作辊与混捻工作辊之间纱线的牵伸倍数为1.5倍,混捻工作辊的加捻温度为70℃,捻度为500t/m。
86.本例中,右侧纱线在集束过程中由于较慢的集束速度具有更大的纱线直径,有助于在第一道加捻区中承受更高倍数的卷绕,经牵伸后的右侧纱线与左侧纱线经过第二道加捻区的合并后,会带动纱线自身产生捻缩,低倍速左侧纱线收缩变化较右侧纱线大,制备的纳米纤维纱线在拉伸与松弛状态下的结构示意图如图4所示,松弛状态下其中一个纱线组分的起拱高度h2如图5所示。
87.实施例6
88.本例提供一种纳米纤维纱线及其连续成纱方法,基本同实施例5,其区别仅在于:
89.(1)左侧初捻工作辊的预加捻度为800t/m,右侧初捻工作辊的预加捻度为1000t/m;
90.(2)控制初捻工作辊与混捻工作辊之间纱线的牵伸倍数为1.2倍,混捻工作辊的捻度为600t/m。
91.性能测试
92.将实施例1-4以及对比例1-3所获得的纱线进行如下性能测试,具体结果参见表1所示。
93.表1
[0094][0095]
将实施例3、5-6所获得的纱线进行如下性能测试,具体结果参见表2所示。
[0096]
表2
[0097][0098]
上述实施例只为说明本发明的技术构思及特点,其目的在于让熟悉此项技术的人士能够了解本发明的内容并据以实施,并不能以此限制本发明的保护范围,凡根据本发明精神实质所作的等效变化或修饰,都应涵盖在本发明的保护范围之内。
再多了解一些
本文用于企业家、创业者技术爱好者查询,结果仅供参考。