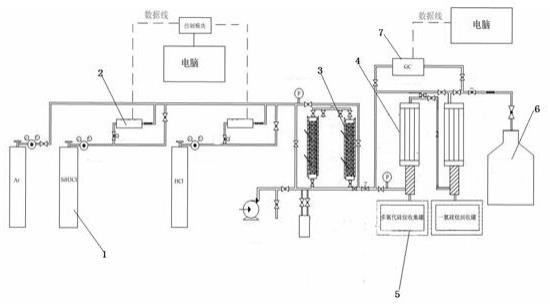
1.本发明涉及氯硅烷合成技术领域,尤其涉及一种催化合成制备多氯硅烷的装置及其方法。
背景技术:
2.氯代硅烷作为半导体工业重要的外延沉积硅源,在沉积制备微电子器件上的二氧化硅以及氮化硅薄膜上有着显著的应用。随着半导体工业的快速发展,氯代硅烷尤其是低氯代硅烷需求和应用不断增长。
3.氯代硅烷的制备方法:一、氯代硅烷歧化法在催化剂条件下,三氯硅烷和二氯硅烷在催化剂的条件下分别可以歧化生成其他氯代硅烷,其中催化剂种类对反应产率及选择性有较大影响,胺、酰胺类催化剂对催化生成二氯硅烷有较高的收率。选择歧化反应制备氯代硅烷,本身需要将氯代硅烷作为原料,同时该反应为可逆反应,并不利于单氯硅烷的产生,方法上有一定的局限。
4.反应式:2sihcl3=sih2cl2 sicl4反应式:2sih2cl2=sihcl3 sih3cl二、硅烷催化合成法在选用沸石分子筛、含alcl3的二氧化硅载体等做催化剂的条件下,在一定温度条件下由硅烷和一氯甲烷气体合成氯代硅烷。
5.反应式:sih4 hcl=sih3cl h2反应式:sih4 2hcl=sih2cl2 2h2值得注意的是,在一定条件下,虽然会有合适的氯代硅烷产出,但反应过程中具有一定的热效应,部分产物分解形成颗粒堵塞分子筛孔道,且温度越高,催化剂老化趋势越明显,通常在最高效温度条件下,7天时间催化效率就会降低至最初的50%,且老化后通过高温活化难以恢复催化活性,催化剂需要较为频繁的更换,这是工业化额一大难点。
6.同时可以根据实验结果可以发现,选用硅烷和氯化氢为原料合成更多的多氯代硅烷效果较差,二氯硅烷转化率较低,其他多氯代硅烷转化率基本低于10%,其中取代越多,产物转化率越低。
7.三、合成法以铜硅粉、一氯甲烷和氯气作为原料,在250-300℃条件下合成氯硅烷。其中三氯硅烷的选择性较高,可以通过先通氯气形成sicl*而提高二氯硅烷的选择性,值得注意的是该方法不适合制备一氯硅烷。
8.反应式:2si 5hcl=sihcl3 sih2cl2 h2四、回收法在多晶硅合成过程中,有大约1%左右的二氯硅烷,以及部分未反应的三氯硅烷,可以通过冷凝精馏回收,该制备方法更多的依赖于产品的回收。
9.综上所述,现有的多氯化硅的制备效率较低,产物转化率低的缺点,因此这个问题亟待解决。
技术实现要素:
10.本发明的目的是提供一种催化合成制备多氯硅烷的装置及其方法,通过一氯硅烷和氯化氢在一定配比、压力、温度及停留时间条件下通过装有分子筛催化剂的催化柱中进行反应,生成一定含量的多氯硅烷,在通过冷凝器进行产物的分离和原料回收,解决了背景技术中心制备效率低、产能低的问题。
11.本发明提供一种催化合成制备多氯硅烷的装置,包括储气罐,储气罐通过管路连接有催化柱,催化柱内填充有填料,催化柱一侧通过循环管路连接有冷凝器,冷凝器下侧设有分离柱,分离柱下侧通过气管连接有收集罐,冷凝器一侧通过管路连接有尾气炉。
12.进一步改进在于:所述储气罐设有三个,三个储气罐内分别氩气、氯化氢、一氯硅烷;储气罐上设有流量控制阀,流量控制阀通过控制模块控制气体的出气量。
13.进一步改进在于:所述冷凝器和收集罐都设有两个,冷凝器之间通过管路连接,冷凝器和收集罐对应连接,冷凝器通过制冷机进行制冷,收集罐分别为原料收集罐和成品收集罐。
14.进一步改进在于:填料包括催化剂和金属丝网;催化剂和金属丝网混合体积比例为1-2:1-3。
15.进一步改进在于:所述催化剂为分子筛催化剂,催化剂中硅铝比例为25:100,催化剂为球形,催化剂直径尺寸为2-10mm,催化剂孔径为0.3-1nm。
16.进一步改进在于:冷凝器上通过管路连接有检测仪,检测仪采用气相色谱检测。
17.本发明还提供一种催化合成制备多氯硅烷的方法,包括以下步骤,步骤1,将催化剂与金属丝网混合填充到催化柱内,进行活化预处理;步骤2,向催化柱内通入氯化氢和一氯硅烷,通过催化剂催化反应;步骤3,将反应产物通入到冷凝器中分离收集;步骤4,对尾气进行处理。
18.进一步改进在于:步骤2中,氯化氢和一氯硅烷的体积比为1-2:1-3;反应压力为1-3bar;反应温度为30-80℃;反应时间为10-90s。
19.进一步改进在于:步骤3中,反应产物依次通过两个冷凝器进行冷凝分离,第一冷凝器控制温度在-20~-15℃,第二冷凝器控制温度在-70~-50℃。
20.本发明的有益效果:1、本发明通过采用一氯硅烷和氯化氢通过催化剂催化反应产生多氯硅烷,区别于现有的氯硅烷制备方法,大大提高了多氯硅烷的反应转化率,提高了多氯硅烷产品的收率;并且在催化合成反应中,合成产生的热效应交底,对催化剂相对较为温和,从而提高了催化剂的使用寿命,避免了平凡更换催化剂,大大降低了资源的使用,从而减少了生产成本。
21.2、本发明对反应产物通过多个冷凝器进行分级冷凝分离,反应产物通过冷凝器之间的温度差进行逐步分离,同时可以将原料一氯硅烷进行分离,对一氯硅烷进行回收利用,提高了一氯硅烷的利用率,提高资源利用率,降低生产成本。
22.3、本发明通过向催化柱内按比例填充催化剂和金属丝网,并且催化剂采用球形沸石分子筛催化剂,使催化反应效率更高,提高了反应生产效率,同时也减少了粉末沸石分子
筛催化剂带来的管道堵塞问题。
23.4、本发明通过设置尾气炉,反应产物通过冷凝器冷凝分离后,剩余的尾气通过输送到尾气炉内进行焚烧处理,对尾气快速处理,减少尾气排放污染,有效的保护了生产环境。
附图说明
24.图1是本发明装置结构图。
25.图2是本发明的方法流程图。
26.其中:1-储气罐,2-流量控制阀,3-催化柱,4-冷凝器,5-收集罐,6-尾气炉,7-检测仪。
具体实施方式
27.为了加深对本发明的理解,下面将结合实施例对本发明作进一步详述,该实施例仅用于解释本发明,并不构成对本发明保护范围的限定。
28.实施例1如图1所示,本实施例提供一种催化合成制备多氯硅烷的装置,包括储气罐,所述储气罐1设有三个,三个储气罐1内分别氩气、氯化氢、一氯硅烷;储气罐1上设有流量控制阀2,流量控制阀2通过控制模块控制气体的出气量。储气罐1通过管路连接有催化柱3,储气罐1内的气体沿管路进入到催化柱3内进行催化反应。催化柱3内填充有填料,填料由催化剂和金属丝网混合组成,催化剂和金属丝网之间的混合体积比例为1-2:1-3,催化剂为分子筛催化剂,催化剂中硅铝比例为25:100,催化剂为球形,催化剂直径尺寸为2-10mm,催化剂孔径为0.3-1nm;通过催化柱3一侧通过循环管路连接有冷凝器4,冷凝器4上通过管路连接有检测仪7,检测仪7通过气相色谱对反应产物进行分析。冷凝器4设有两个,冷凝器4之间通过管路连接,冷凝器4之间存在温度差,冷凝器4下侧设有分离柱,分离柱下侧通过气管连接有收集罐5,收集罐5设有两个,收集罐5分别为原料收集罐和成品收集罐,冷凝器4和收集罐5对应连接,反应产物进入到冷凝器4中冷凝分离,分离的产物通过分离柱分离分别进入到收集罐5中分类收集。冷凝器4一侧通过管路连接有尾气炉6,尾气炉6采用焚烧炉或液排处理,减少废气污染。
29.如图2所示,本实施例还提供了一种催化合成制备多氯硅烷的方法,包括以下步骤;步骤1,将催化剂与金属丝网混合填充到催化柱内,进行活化预处理;步骤2,向催化柱内通入氯化氢和一氯硅烷,氯化氢和一氯硅烷的体积比为1-2:1-3,通过催化剂催化反应,反应压力为1-3bar;反应温度为30-80℃;反应时间为10-90s;步骤3,将反应产物通入到冷凝器中分离收集,反应产物依次通过两个冷凝器进行冷凝分离,第一个冷凝器控制温度在-20~-15℃,第二个冷凝器控制温度在-70~-50℃,通过温度差依次对反应产物进行分离,通过原料收集罐和成品收集罐进行分类收集;步骤4,剩余气体排入到焚烧炉内,对尾气进行处理,减少尾气污染。
30.实施例2
搭建设备,并进行保压检漏,检漏方法:使用吸枪法正压10bar氦检,漏率<2*10-9
pa
·
m3/s,合格后待用。将200g沸石分子筛催化剂h-zsm-5,(催化剂si:al=25:280,催化剂颗粒为球形,直径=2-3mm)放置于110℃烘箱中24h,将相同体积的金属丝网填料与之混合均匀后装填入催化柱中。在350℃条件下进行抽烘,对催化剂进行活化预处理。通过质量流量计控制一氯硅烷和氯化氢混合气体进料体积比为1:1,调整反应压力为2bar,反应环境温度为50℃,调整反应停留时间为60s,当反应连续运行2hr后,通过气相色谱对反应后气相产物进行分析,一氯硅烷转化率为59.3%,二氯硅烷收率41.5%,三氯硅烷收率15.3%,四氯硅烷收率为2.5%。当反应运行稳定后,控制第一个冷凝器温度为-20~-15℃,将产物气流通过第一个冷凝器将多氯代硅烷(sih2cl2、sihcl3、sicl4)液化收集于成品收集罐,后续可再进行精馏将三中组分进行分离。经过第一个冷凝器后剩余气体中一氯硅烷、氢气及氯化氢气体随后进入第二个冷凝器,控制第二个冷凝器温度在-70~-50℃,将一氯硅烷液化收集于原料收集罐,剩余气体通过焚烧炉进行处理;回收的一氯硅烷进行重复利用。
31.实施例3将150g沸石分子筛催化剂h-zsm-5(其中催化剂si:al=25:200,催化剂颗粒为球形,直径=2-3mm)放置于110℃烘箱中24h,将2倍于分子筛催化剂体积的金属丝网填料与之混合均匀后装填入催化柱中。在350℃条件下进行抽烘,对催化剂进行活化预处理。通过流量控制阀控制一氯硅烷和氯化氢混合气体进料体积比为1:1,调整反应压力为2bar,反应环境温度为80℃,调整反应停留时间为90s,当反应连续运行2hr后,通过检测仪气相色谱对反应后气相产物进行分析,一氯硅烷转化率为64.6%,二氯硅烷收率37.6%,三氯硅烷收率23.7%,四氯硅烷收率为3.3%。当反应运行稳定后,控制第一个冷凝器温度为-20~-15℃,将产物气流通过第一个冷凝器将多氯代硅烷(sih2cl2、sihcl3、sicl4)液化收集于成品收集罐,后续可再进行精馏将三中组分进行分离。经过第一个冷凝器后剩余气体中一氯硅烷、氢气及氯化氢气体随后进入第二个冷凝器,控制第二个冷凝器温度在-70~-50℃,将一氯硅烷液化收集于原料收集罐,剩余气体通过焚烧炉进行处理;回收的一氯硅烷进行重复利用。
32.实施例4将150g沸石分子筛催化剂h-zsm-5(其中催化剂si:al=25:100,催化剂颗粒为球形,直径=2-3mm)放置于110℃烘箱中24h,将2倍于分子筛体积的金属丝网填料与之混合均匀后装填入催化柱中。在350℃条件下进行抽烘,对催化剂进行活化预处理。通过质量流量计控制一氯硅烷和氯化氢混合气体进料体积比为1:1,调整反应压力为2bar,反应环境温度为40℃,调整反应停留时间为30s,当反应连续运行2hr后,通过检测仪气相色谱对反应后气相产物进行分析,一氯硅烷转化率为57.9%,二氯硅烷收率46.4%,三氯硅烷收率10.3%,四氯硅烷收率为1.2%。当反应运行稳定后,控制第一个冷凝器温度为-20~-15℃,将产物气流通过第一个冷凝器将多氯代硅烷(sih2cl2、sihcl3、sicl4)液化收集于成品收集罐,后续可再进行精馏将三中组分进行分离。经过第一个冷凝器后剩余气体中一氯硅烷、氢气及氯化氢气体随后进入第二个冷凝器,控制第二个冷凝器温度在-70~-50℃,将一氯硅烷液化收集于原料收集罐,剩余气体通过焚烧炉进行处理;回收的一氯硅烷进行重复利用。
33.实施例5将200g沸石分子筛催化剂h-zsm-5(其中催化剂si:al=80:200,加工颗粒为球形,直径=2-3mm)放置于110℃烘箱中24h,将1倍于分子筛催化剂体积的金属丝网填料与之混合
均匀后装填入催化柱中。在350℃条件下进行抽烘,对催化剂进行活化预处理。通过流量控制阀控制一氯硅烷和氯化氢混合气体进料体积比为1:2,调整反应压力为2bar,反应环境温度为40℃,调整反应停留时间为90s,当反应连续运行2hr后,通过检测仪气相色谱对反应后气相产物进行分析,一氯硅烷转化率为73.4%,二氯硅烷收率53.2%,三氯硅烷收率15.5%,四氯硅烷收率为4.5%。当反应运行稳定后,控制第一个冷凝器温度为-20~-15℃,将产物气流通过第一个冷凝器将多氯代硅烷(sih2cl2、sihcl3、sicl4)液化收集于成品收集罐,后续可再进行精馏将三中组分进行分离。经过第一个冷凝器后剩余气体中一氯硅烷、氢气及氯化氢气体随后进入第二个冷凝器,控制第二个冷凝器温度在-70~-50℃,将一氯硅烷液化收集于原料收集罐,剩余气体通过焚烧炉进行处理;回收的一氯硅烷进行重复利用。
再多了解一些
本文用于企业家、创业者技术爱好者查询,结果仅供参考。