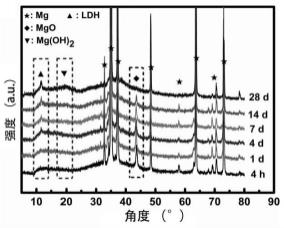
1.本发明涉及一种提高镁合金表面微弧多孔氧化镁涂层抗腐蚀性的方法,具体涉及一种 利用浸泡法在微弧多孔氧化镁涂层表面构建非晶态羟基氧化锰(mnooh)涂层的表面改性 方式,属于金属材料表面改性技术领域。
背景技术:
2.镁及其合金材料由于具有较高的比强度,在航空航天工业、军工、交通、船舶工业领 域等都发挥着重要作用。然而,镁的电化学势太低,在潮湿的空气、水溶液、尤其包含氯离 子的溶液中,极易发生腐蚀。对于工业应用而言,过快的腐蚀使得其容易失去机械支撑性 能,存在极大的安全隐患。
3.镁及其合金表面改性是一种提高其抗腐蚀性的常用方法。如今,微弧氧化涂层的探 索,开发与应用在镁及其表面改性防腐蚀领域占据重要地位,引起了许多研究者的关注。微 弧氧化镁涂层自身仍存在的问题如下:(1)微弧氧化镁涂层表面呈多孔结构,会使腐蚀介质 接触镁合金基底,而降低其腐蚀保护性能;(2)微弧氧化镁涂层的腐蚀产物主要为氢氧化 镁,而氢氧化镁在氯化钠溶液中溶液容易转换为可溶的氯化镁,抗腐蚀性能差;(3)作为屏 障涂层,微弧氧化镁涂层容易发生局部腐蚀,产生裂纹,降低其抗腐蚀性。
4.在当前的研究中,元素以及纳米颗粒掺杂和表面封孔是提高微弧氧化镁涂层抗腐蚀性 的主要方法。元素以及纳米颗粒掺杂可以提高微弧多孔氧化镁涂层的机械稳定性和腐蚀抵抗 力;表面封孔可以阻止腐蚀介质与镁合金基底的接触。然而,这些方法都不能全面的解决上 述微弧多孔氧化镁涂层所存在的全部问题。因此,针对微弧氧化镁涂层所存在的问题,开发 新型的智能防腐方法具有重要意义。腐蚀过程中的腐蚀反应是影响腐蚀快慢的重要因素,针 对腐蚀反应的调控,提高样品抗腐蚀的设计与产品鲜有报道。
技术实现要素:
5.为解决上述技术问题,本发明提供了一种提高镁合金表面微弧多孔氧化镁涂层抗腐蚀 性的方法,以及该方法制备的微弧多孔氧化镁抗腐蚀性涂层。
6.第一方面,本发明提供了一种提高镁合金表面微弧多孔氧化镁涂层抗腐蚀性的方法, 所述微弧多孔氧化镁涂层的物相包括氧化镁;所述方法为:将覆盖微弧多孔氧化镁涂层的镁 合金浸泡于锰离子溶液中,在镁合金表面得到多孔非晶态羟基氧化锰涂层。
7.较佳的,所述锰离子溶液为硝酸锰和/或氯化锰溶液,溶剂为水。
8.较佳的,所述多孔非晶态金属羟基氧化锰涂层在腐蚀中与微弧多孔氧化镁涂层自发反 应生成mg/mn层状双氢氧化物以封住微弧多孔氧化镁涂层的微孔,从而提高微弧氧化涂层 的抗腐蚀性。
9.较佳的,所述腐蚀中的腐蚀液为盐溶液或自来水。
10.本发明提出利用浸泡法在镁合金微弧多孔氧化镁涂层表面制备金属羟基氧化物的表面 改性方式。所述金属羟基氧化物涂层为羟基氧化锰(mnooh)。由于腐蚀反应在很大
程度上 决定改性涂层抗腐蚀性的强弱,所制备金属羟基氧化物会在微弧多孔氧化镁涂层腐蚀过程中 反应生成mg/mn层状双氢氧化物抗腐蚀性涂层,从而提高微弧多孔氧化镁涂层的抗腐蚀 性。
11.更具体地,微弧多孔氧化镁在腐蚀过程中会溶出大量的镁离子(mg
2
)和氢氧根(oh
‑ ),这为层状双氢氧化物相(ldh)的形成提供了条件。在微弧多孔氧化镁的表面形成的羟 基氧化锰层在腐蚀过程中参与腐蚀反应,在室温下与微弧多孔氧化镁涂层溶出的mg
2
和氢氧 根(oh-)发生反应形成mg-mn层状双氢氧化物(ldh)防腐涂层,并封住微弧氧化涂层的微 孔。
12.将微弧多孔氧化镁后的样品,浸泡于硝酸锰和/或氯化锰溶液中时,氧化镁呈碱性, 周围产生大量的氢氧根离子(oh-),与游离的锰离子发生反应生成氢氧化锰(mn(oh)2), 而氢氧化锰不稳定,被周围中的氧气氧化为羟基氧化锰(mnooh),具体反应如下:mn
2 2oh-=mn(oh)2,4mn(oh)2 o2=4mnooh 2h2o。
13.较佳的,所述锰离子溶液的浓度为2~40g/l。当锰离子溶液的浓度过低时,羟基氧 化锰含量少,在腐蚀过程中会形成微弧氧化涂层原本的腐蚀产物氢氧化镁,而氢氧化镁在氯 化钠溶液中溶液容易转换为可溶的氯化镁,抗腐蚀性能差。当锰离子溶液的浓度过高时,容 易在浸泡过程中产生氢氧化镁,可能会导致后续腐蚀过程中不会形成ldh,达不到提高腐 蚀保护的效果。
14.较佳的,所述浸泡的温度为室温20~40℃。所述浸泡的时间为3~9小时。浸泡时 间过短,锰含量降低,达不到提高抗腐蚀性的效果。浸泡时间过长,则会在浸泡过程中生成 氢氧化镁相,如果生成氢氧化镁相,则非晶羟基氧化锰在后续的腐蚀过程中不会生成层状双 氢氧化物涂层,达不到提高腐蚀保护的效果。较佳的,将去掉表面氧化镁的镁合金片作为基 底,使用去离子水配置5~15g/l的甘油磷酸钠和10~15g/l氢氧化钾混合溶液以作为微弧 氧化所用的电解液进行微弧氧化,制得所述微弧多孔氧化镁涂层。
15.较佳的,所述微弧氧化参数为电压320~360v、电流0.6~1.0a、占空比8~12%、频 率800~1200hz。
16.较佳的,所述微弧多孔氧化镁涂层的孔径范围为0.1~1.8μm。
17.第二方面,本发明提供了采用上述方法在镁合金表面制备的微弧多孔氧化镁抗腐蚀性 涂层,所述微弧多孔氧化镁抗腐蚀性涂层包括:微弧多孔氧化镁涂层,以及原位形成在微弧 多孔氧化镁涂层上的非晶态羟基氧化锰涂层。
18.较佳的,所述微弧多孔氧化镁抗腐蚀性涂层中锰元素原子质量百分比为4.35%~15.74%。
19.较佳的,所述微弧多孔氧化镁抗腐蚀性涂层的总厚度为3μm~7μm。
20.有益效果:1、实验在无需复杂设备,实验过程相对安全,而且有利于大规模产业化;2、与其他方法制备的镁及其合金表面涂层相比,本发明提供的涂层与基底之间原位结合, 具有强结合力;3、本发明制备的金属羟基氧化物涂层,能够在微弧多孔氧化镁涂层腐蚀过程中参与腐蚀反 应,生成腐蚀产物片状层状双金属氢氧化物而不是氢氧化镁,并封住微弧多孔氧化镁涂层的 微孔;
4、所制备的在微弧多孔氧化镁涂层腐蚀过程中改变其腐蚀行为的金属羟基氧化物涂层可以 直接作为镁及其合金表面抗腐蚀涂层或者作为预处理层,有望应用在航空航天、交通以及医 用金属材料等领域。
附图说明
21.图1示出了实施例1中样品表面的扫描电镜图(sem)和能谱图:图1中的(a)为 实施例1未经处理的微弧多孔氧化镁显微表面;图1中的(b)为实施例1未经处理的微弧 多孔氧化镁断面;图1中的(c)为实施例1未经处理的微弧多孔氧化镁能谱;从图中可以 看出,样品表面呈多孔结构,涂层厚度为4微米左右。
22.图2示出了实施例1样品表面的能谱面扫图。从图中可以看出,样品表面镁、氧元素 分布均匀,无锰元素。
23.图3示出了实施例2样品表面的扫描电镜图(sem)和能谱图:图3中的(a)为实 施例2浸泡制备的羟基氧化锰(mnooh)显微表面;图3中的(b)为实施例2中的浸泡制 备的羟基氧化锰(mnooh)断面;图3中的(c)为实施例2中的浸泡制备的羟基氧化锰能 谱。从图中可以看出,样品表面呈多孔结构,涂层厚度为4微米左右,与实施例1未经处理 的微弧多孔氧化镁样品没有明显差别,涂层锰元素原子质量百分比为2.246%。
24.图4示出了实施例2样品表面的能谱面扫图;从图中可以看出,样品表面镁、氧、锰 元素分布均匀。
25.图5示出了实施例3样品表面的扫描电镜图(sem)和能谱图:图5中的(a)为实 施例3中的浸泡制备的羟基氧化锰(mnooh)显微表面;图5中的(b)为实施例3中的浸 泡制备的羟基氧化锰(mnooh)断面;图5中的(c)为实施例3中的浸泡制备的羟基氧化 锰能谱图;从图中可以看出,样品表面呈多孔结构,涂层厚度为4微米左右,与实施例1未 经处理的微弧多孔氧化镁样品没有明显差别,涂层锰元素原子质量百分比为4.350%。
26.图6示出了实施例3样品表面的能谱面扫图。从图中可以看出,样品表面镁、氧、锰 元素分布均匀。
27.图7示出了实施例4样品表面的扫描电镜图(sem)和能谱图:图7中的(a)为实 施例4中的浸泡制备的羟基氧化锰(mnooh)显微表面;图7中的(b)为实施例4中的浸 泡制备的羟基氧化锰(mnooh)断面;图7中的(c)为实施例4中的浸泡制备的羟基氧化 锰能谱图;从图中可以看出,样品表面呈多孔结构,涂层厚度为4微米左右,与实施例1未 经处理的微弧多孔氧化镁样品没有明显差别,涂层锰元素原子质量百分比为5.907%。
28.图8示出了实施例4样品表面的能谱面扫图。从图中可以看出,样品表面镁、氧、锰 元素分布均匀。
29.图9中的(a)示出了实施例1-4的x射线衍射图(xrd);图9中的(b)、 (c)、(d)分别示出了实施例4所制备样品表面刮下的粉体测试的xrd图、红外光谱 图、拉曼光谱图;图9中的(e)示出了实施例1-4的x射线光电子能谱全谱图(xps); 图9中的(f)示出了实施例2-4x射线光电子能谱mn 3s高分辨图谱;从图9可以看出, xrd结果表明采用浸泡法制备的含锰涂层为非晶态;红外光谱、拉曼光谱、xps测试结果 表明采用浸泡法制备的含锰涂层为羟基氧化锰(mnooh)。
30.图10中的(a)、(b)、(c)、(d)、(e)、(f)分别示出了实施例1样品在 0.9wt%nacl溶
液中腐蚀4小时、1天、4天、7天、14天以及28天的腐蚀形貌;可以看 出,实施例1样品的腐蚀较快。
31.图11示出了图10中实施例1样品腐蚀的xrd图;可以看出,实施例1样品在腐蚀 过程中生成腐蚀产物氢样化镁。
32.图12中的(a)、(b)、(c)、(d)、(e)、(f)分别示出了实施例2样品在 0.9wt%nacl溶液中腐蚀4小时、1天、4天、7天、14天以及28天的腐蚀形貌;可以看 出,实施例2样品的腐蚀慢于实施例1的样品。
33.图13示出了图12中实施例2样品腐蚀的xrd图;可以看出,实施例2样品在腐蚀 过程中没有生成氢样化镁相。
34.图14中的(a)、(b)、(c)、(d)、(e)、(f)分别示出了实施例3样品在 0.9wt%nacl溶液中腐蚀4小时、1天、4天、7天、14天以及28天的腐蚀形貌;可以看 出,实施例3样品的腐蚀慢于实施例1和实施例2的样品。
35.图15示出了图14中实施例3样品腐蚀的xrd图;可以看出,实施例3样品在腐蚀 过程中没有生成氢样化镁相,且生成ldh相。
36.图16中的(a)、(b)、(c)、(d)、(e)、(f)分别示出了实施例4样品在 0.9wt%nacl溶液中腐蚀4小时、1天、4天、7天、14天以及28天的腐蚀形貌;可以看 出,实施例4样品的腐蚀慢于实施例1、实施例2和实施例3的样品。
37.图17示出了图16中实施例4样品腐蚀的xrd图;可以看出,实施例4样品在腐蚀 过程中没有生成氢样化镁相,且生成ldh相。
38.图18中的(a)示出了实施例1-4样品的极化曲线图(250ml的0.9wt%nacl溶液 中采用ch1760c三电极电化学工作站测试);图18中的(b)示出了实施例1-4样品的氢 气释放曲线。从图中可以看出,实施例1-4样品随着羟基氧化锰(mnooh)含量的上升, 样品的腐蚀电流和氢气释放量降低,样品的抗腐蚀性能依次增强。
具体实施方式
39.下面进一步例举实施例以详细说明本发明。应理解,以下实施例只用于对本发明进行 进一步说明,而不能理解为对本发明保护范围的限制,本领域的技术人员根据本发明的上述 内容作出的一些非本质的改进和调整均属于本发明的保护范围。下述示例具体的工艺参数等 也仅是合适范围中的一个示例,即本领域技术人员可以通过本文的说明做合适的范围内选 择,而并非要限定于下文示例的具体数值。
40.实施例1(1)将厚度为2mm,长宽都为10mm的az31镁合金片,用600目的sic砂纸去掉表面氧 化层,再用酒精超声干净,作为基底。(2)使用去离子水配置10g/l的甘油磷酸钠和12.5g/l氢氧化钾混合溶液,作为微弧多孔 氧化镁所用的电解液。(3)对镁合金片采用恒压模式电解,参数为:截至电压340v、电流0.8a、占空比10%、 频率1000hz。所制备的样品表面覆盖微弧多孔氧化镁涂层,标记为peo。
41.实施例2(1)使用去离子水配置12g/l的mncl2.4h2o溶液。
(2)将实施例1微弧多孔氧化镁后的镁合金样品放入到所配置的氯化锰溶液中3小时。 所制备的样品标记为peo-mn1。sem结果表明样品的显微结构和断面厚度与未处理的微弧 多孔氧化镁样品相比并没有明显地改变;xrd、xps结果表明表面形成非晶羟基氧化锰; 能谱结果表明该涂层的锰元素原子质量百分比为2.24%,且涂层分布均匀;xrd结果表 明,制备的改样品在腐蚀过程中形成了层状双氢氧化物相;极化曲线、浸泡实验、析氢实验 表明改涂层提高了样品的耐腐蚀性。
42.实施例3(1)使用去离子水配置12g/l的mncl2.4h2o溶液。(2)将实施例1微弧多孔氧化镁后的镁合金样品放入到所配置的氯化锰溶液中6小时。 所制备的样品标记为peo-mn2。sem结果表明样品的显微结构和断面厚度与未处理的微弧 多孔氧化镁样品相比并没有明显地改变;xrd、xps结果表明表面形成非晶羟基氧化锰; 能谱结果表明该涂层的锰元素原子质量百分比为4.35%,且涂层分布均匀;xrd结果表 明,制备的改样品在腐蚀过程中形成了层状双氢氧化物相;极化曲线、浸泡实验、析氢实验 表明改涂层提高了样品的耐腐蚀性。
43.实施例4(1)使用去离子水配置12g/l的mncl2.4h2o溶液。(2)将实施例1微弧多孔氧化镁后的镁合金样品放入到所配置的氯化锰溶液中9小时。 所制备的样品标记为peo-mn3。sem结果表明样品的显微结构和断面厚度与未处理的微弧 多孔氧化镁样品相比并没有明显地改变;xrd、xps结果表明表面形成非晶羟基氧化锰; 能谱结果表明该涂层的锰元素原子质量百分比为11.89%,且涂层分布均匀;xrd结果表 明,制备的改样品在腐蚀过程中形成了层状双氢氧化物相;极化曲线、浸泡实验、析氢实验 表明改涂层提高了样品的耐腐蚀性。
44.实施例5(1)使用去离子水配置2g/l的mncl2.4h2o溶液。(2)将实施例1微弧多孔氧化镁后的镁合金样品放入到所配置的氯化锰溶液中9小时。 sem结果表明样品的显微结构和断面厚度与未处理的微弧多孔氧化镁样品相比并没有明显 地改变;xrd、xps结果表明表面形成非晶羟基氧化锰;能谱结果表明该涂层的锰元素原 子质量百分比为4.320%,且涂层分布均匀;xrd结果表明,制备的改样品在腐蚀过程中形 成了层状双氢氧化物相;极化曲线、浸泡实验、析氢实验表明改涂层提了样品的耐腐蚀性。
45.实施例6(1)使用去离子水配置40g/l的mncl2.4h2o溶液。(2)将实施例1微弧多孔氧化镁后的镁合金样品放入到所配置的氯化锰溶液中9小时。 sem结果表明样品的显微结构和断面厚度与未处理的微弧多孔氧化镁样品相比并没有明显 地改变;xrd,xps,结果表明表面形成非晶羟基氧化锰;能谱结果表明该涂层的锰元素原 子质量百分比为15.74%,且涂层分布均匀;xrd结果表明,制备的改样品在腐蚀过程中形 成了层状双氢氧化物相;极化曲线、浸泡实验、析氢实验表明改涂层提了样品的耐腐蚀性。
再多了解一些
本文用于企业家、创业者技术爱好者查询,结果仅供参考。