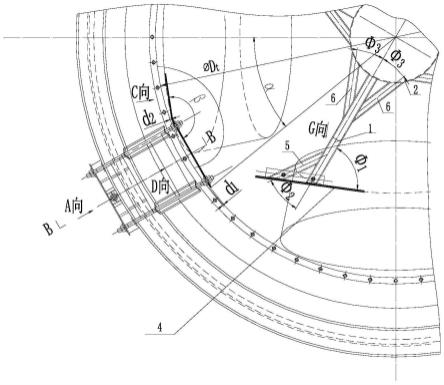
1.本发明属于立式辊磨设计技术领域,尤其涉及一种立式辊磨的内置导流机构的制作方法。
背景技术:
2.立式辊磨简称立磨,其粉磨原理是料层粉磨,即通过颗粒与颗粒之间相互挤压来实现物料的粉磨,粉磨过程可控性好,粉磨效率高。立式辊磨粉磨单元的现有结构原理图见图5。
3.现有结构的工作原理如下:新喂料及选粉机回料在重力作用下由料仓1喂入磨盘中部,磨盘转动带动物料转动,物料在离心力的作用下由磨盘中部向磨盘边缘运动,当物料运动至磨辊下方时,磨辊在力f的作用及挡料圈的共同作用下挤压物料(料层),物料被粉磨,粉磨后的物料在离心力的作用下越过挡料圈,离开磨盘,在重力作用下落入风环,随后被风环内高速气流向上带入磨机上部选粉机,合格成品被选粉机选走,不合格的大颗粒通过料仓同新喂料混合后重回磨继续粉磨,直至粉磨成合格粒度要求的成品。
4.立式辊磨集粉磨、烘干、选粉于一体,结构紧凑、系统简单、烘干能力大,对物料适应性强,因此广泛应用于水泥生料、熟料、工业固废、冶金渣等多种物料的粉磨,但相比于同是“料层粉磨”的辊压机相比,最大的共性问题就是料层的可控性差,唯一控制料层的手段就是磨盘挡料圈高度的调整。增加挡料高度,提高料层可控性,但研磨效率降低;降低挡料高度,研磨效率增加,但料层变薄,可控性降低、磨机振动增加;对料层粉磨原理的设备,料层可控性直接影响磨机的稳定性和研磨效率,因此一般情况下粉磨相同物料,立式辊磨的主机电耗较辊压机高0.5~1kwh/t左右。
5.根据立式辊磨磨盘物料运动离散元仿真的动态计算结果分析,磨盘上物料可以划分为a、b、c三个区域:a区物料是能全部进入磨辊下方能被碾压的物料,b区是直接经两磨辊之间的空隙被磨盘甩出的未经磨辊碾压物料(即旁路物料),c区是磨辊碾压过的物料。由于a区、b区均是未被磨辊碾压过的物料,从提高研磨效率和磨机稳定性的角度,理论上不需要b区存在,即只要是未被碾压的物料,希望全部进入磨辊下方进行碾压,以产生更多的细粉,但实际上磨机越大,相邻两磨辊之间的距离越大,b区越大,同一台磨机,磨盘转速越高,b区就越大。一般而言,随着设备规格的大型化,系统产量就越高,系统电耗就越低,但立式辊磨从台时50~60t/h发展到500~600t/h规模,磨机效率并未出现明显提升的主要原因就在于b区的旁路量的增大致使磨内无效循环量增加,抵消了磨机大型化对磨机效率的贡献。
6.c区物料由于经磨辊碾压过,料层中夹杂大量细粉,从提高料层粉磨效率的角度,理论需要c区物料中的细粉全部排出,但由于磨盘挡料圈的存在,处于挡料圈高度以下料层中夹杂的细粉除通过磨辊转动和挤压排出部分细粉外,大部分细粉残留在研磨区底部,根据工业生产统计数据,c区物料中≤80μm的细粉含量达18~20%。大量的细粉残留于磨盘底部,增加料层的流动性,从而破坏料层稳定性,一方面造成磨机振动,另一方面降低研磨效率、磨机电流下降,导致磨机台时降低、电耗增加,同时因磨内循环负荷增大,出磨成品的颗
粒级配变窄,影响成品的质量和性能。
技术实现要素:
7.针对现有技术存在的问题,本发明提供了一种改善挡料圈以下物料中细粉富集对料层的破坏作用的立式辊磨的内置导流机构的制作方法。
8.本发明是这样实现的,一种立式辊磨的内置导流机构的制作方法,其特征在于包括如下步骤:
9.s1)、根据磨机设计台时、物料易磨性等基础数据,按照磨机选型常规设计方法确定磨盘直径d
t
、磨辊大端直径d
r1
、磨辊小端直径d
r2
、磨辊宽度br;
10.s2)、确定内置导流机构的结构:内置导流机构包括支架主梁,所述支架主梁的一端固定连接中心下料管,另一端安装有导料板基座,所述导料板基座的外侧安装有导料板,所述导料板基座与支架主梁之间连接有支架副梁;在靠近中心下料管侧所述支架主梁与中心下料管之间焊接有支架侧拉筋和/或支架上拉筋;
11.s3)、计算导料板的结构及位置参数:
12.导料板的主要结构位置参数:导料板高度h2、导料板总长l3、l4导料板弧段长度、r2导料板弧段曲率半径、导料板前端距离磨辊轴线距离d5、导料板弧段距离磨辊小端的间隙d6、导料板平面距离磨辊小端所在平面的间隙d7、导料板倾角t、导料板距离衬板的高度h5、挡料圈高度h1、导料板同支架主梁夹角φ1、支架副梁同支架主梁夹角φ2、支架侧拉筋同支架主梁的夹角φ3、支架上拉筋同支架主梁夹角φ4。各参数的计算方法或取值如下:
13.h2=200~350mm
14.l3=(30~35)π(d
t-2br)/360
[0015][0016]
d5=(0.1~0.2)d
r2
[0017]
d6=10~20mm
[0018]
r2=0.5d
r2-d6[0019]
d7=10~20mm
[0020]
h1=(0.02~0.04)(d
r1
d
r2
)
[0021]
h5=h1±
10
[0022]
t=90
±
15
°
,以导料板平行于磨辊内端平面为原则。
[0023]
φ1=65
±
10
°
[0024]
φ2=35
±5°
[0025]
φ3=20
±5°
[0026]
φ4=30
±5°
[0027]
s4)制作导料板及确定安装位置:
[0028]
根据s2)计算得到的导料板工艺结构参数h2、r2、l3、l4下料,导料板材料选用双面耐磨结构,导料板基材后度为12、10、8mm;对应耐磨层单面厚度为6mm、4mm或3mm,表面硬度hrc≥50;导料板同导料板基座的焊接部分不堆焊耐磨层,确保导料板同导料板基座的焊接牢固,导料板倾角t以磨辊压向磨盘理论设计位置时,平行于磨辊内端面为主要原则;导料板定位螺栓孔的中心距=(0.5
±
0.05)(l
3-l4);
[0029]
s5)导料板支架制作及确定安装位置:
[0030]
根据导料板的设计定位,现场测量支架主梁、支架副梁、支架上拉筋、支架侧拉筋的尺寸;支架主梁同导料板夹角φ1=65
±
10
°
,支架主梁与支架副梁夹角φ2=35
±5°
,支架主梁与支架上拉筋夹角φ4=30
±5°
,支架主梁与支架侧拉筯夹角φ3=20
±5°
;导料板基座定位螺栓孔中心距(0.5
±
0.05)(l
3-l4);上拉筯的长度以0.5~0.6倍主梁长度及同主梁夹角φ4估算;支架侧拉筋同支架主梁的夹角φ3以相邻支架侧拉筋不干涉为原则现场确定;
[0031]
s6)安装:
[0032]
将制作完的导料板按设计位置临时定位于磨盘上方,并将支架主梁、支架副梁顶在导料板基座下方,调整支架主梁另一端,使之靠在磨机中心下料管上,先点焊定位主梁,再分别将支架上拉筋、支架侧拉筋点焊定位于中心下料管和主梁上,然后分别焊牢;点焊导料板基座和支架主梁、支架副梁支撑处,现场配钻加工导料板基座和支架主梁、支架副梁的定位螺栓孔,然后用螺栓螺母固定,完成安装。
[0033]
本发明具有的优点和技术效果:采用上述技术方案制作而成的内置导流机构,将离开导料板的物料强制导入挡料板内侧,并全部被挡料板送入磨辊下方碾压。此外,导料板还具有将磨辊碾压后的物料强制排出磨盘进入风环的作用,改善扫料圈以下物料中细粉富集对料层的破坏作用,相同的挡料圈高度下,相比传统立式辊磨技术,平均产量增加12.1%,主机电耗降低18.7%。
附图说明
[0034]
图1是本发明结构示意图;
[0035]
图2是图1中内置导流机构局部安装结构示意图;
[0036]
图3是内置导流机构与磨辊位置结构示意图;
[0037]
图4是导料板结构位置工艺参数示意图;
[0038]
图5是传统立式辊磨粉磨单元结构原理图。
[0039]
图中、1、支架主梁;2、中心下料管;3、导料板基座;4、导料板;4-1、耐磨层;5、支架副梁;6、支架侧拉筋;7、支架上拉筋;8、支架、9、挡料板。
具体实施方式
[0040]
为了使本发明的目的、技术方案及优点更加清楚明白,以下结合实施例,对本发明进行进一步详细说明。应当理解,此处所描述的具体实施例仅仅用以解释本发明,并不用于限定本发明。
[0041]
请参阅图1至图4,一种立式辊磨的内置导流机构的制作方法,其特征在于包括如下步骤:
[0042]
s1)、根据磨机设计台时、物料易磨性等基础数据,按照磨机选型常规设计方法确定磨盘直径d
t
、磨辊大端直径d
r1
、磨辊小端直径d
r2
、磨辊宽度br;
[0043]
s2)、确定内置导流机构的结构:内置导流机构位于两个磨辊之间,并且与中心下料管2固定连接,内置导流机构包括支架主梁1,所述支架主梁的一端固定连接中心下料管2,另一端安装有导料板基座3,所述导料板基座的外侧安装有导料板4,所述导料板4平行于磨辊内端面,且弧段平行于磨辊内端面外圆轮廓;所述导料板基座3、支架主梁1圴依据导料
板位置确定设计和安装位置;所述导料板基座与支架主梁之间连接有支架副梁5;在靠近中心下料管侧所述支架主梁与中心下料管之间焊接有支架侧拉筋6和/或支架上拉筋7,提高支架主梁的连接强度;在导料板的双面设有耐磨层4-1,延长使用寿命,降低维护频率。
[0044]
s3)、计算导料板的结构及位置参数:
[0045]
导料板的主要结构位置参数:导料板高度h2、导料板总长l3、导料板弧段长度l4、导料板弧段曲率半径r2、导料板前端距离磨辊轴线距离d5、导料板弧段距离磨辊小端的间隙d6、导料板平面距离磨辊小端所在平面的间隙d7、导料板倾角t、导料板距离衬板的高度h5、挡料圈高度h1、导料板同支架主梁夹角φ1、支架副梁同支架主梁夹角φ2、支架侧拉筋同支架主梁的夹角φ3、支架上拉筋同支架主梁夹角φ4。各参数的计算方法或取值如下:
[0046]
h2=200~350mm
[0047]
l3=(30~35)π(d
t-2br)/360
[0048][0049]
d5=(0.1~0.2)d
r2
[0050]
d6=10~20mm
[0051]
r2=0.5d
r2-d6[0052]
d7=10~20mm
[0053]
h1=(0.02~0.04)(d
r1
d
r2
)
[0054]
h5=h1±
10
[0055]
t=90
±
15
°
[0056]
φ1=65
±
10
°
[0057]
φ2=35
±5°
[0058]
φ3=20
±5°
[0059]
φ4=30
±5°
[0060]
优选的,所述支架主梁与支架副梁的夹角为35
±5°
,确保导料板4为面支撑,提高支撑的可靠性。
[0061]
优选的,支架主梁与支架侧拉筋的夹角为20
±5°
,一是降低支架侧拉筋的自重,二是避免相邻支架主梁侧拉筋于中心下料管2上交叉重叠。
[0062]
优选的,支架主梁与支架上拉筋的夹角为30
±5°
,避免上拉筋被风环气流冲刷磨损。
[0063]
s4)制作导料板及确定安装位置:
[0064]
根据s2)计算得到的导料板工艺结构参数h2、r2、l3、l4下料,导料板材料选用双面耐磨结构,导料板基材后度为12、10、8mm;对应耐磨层单面厚度为6mm、4mm或3mm,表面硬度hrc≥50;导料板同导料板基座的焊接部分不堆焊耐磨层,确保导料板同导料板基座的焊接牢固,导料板倾角t以磨辊压向磨盘理论设计位置时,平行于磨辊内端面为主要原则;导料板定位螺栓孔的中心距=(0.5
±
0.05)(l
3-l4);
[0065]
s5)导料板支架制作及确定安装位置:
[0066]
根据导料板的设计定位,现场测量支架主梁1、支架副梁5、支架上拉筋7、支架侧拉筋6的尺寸;支架主梁1同导料板4夹角φ1=65
±
10
°
,支架主梁1与支架副梁5夹角φ2=35
±5°
,支架主梁1与支架上拉筋7夹角φ4=30
±5°
,支架主梁1与支架侧拉筯6夹角φ3=20
±5°
;导料板基座3定位螺栓孔中心距(0.5
±
0.05)(l
3-l4);支架上拉筯7的长度以0.5~0.6倍主梁长度及同主梁夹角估算;支架侧拉筋6同支架主梁1的夹角φ3以相邻支架侧拉筋不干涉为原则现场确定;各梁和拉筯材料建议选10#或12#热轧轻型槽钢;支架上拉筋、支架侧拉筋先下好料,现场定位焊接。
[0067]
s6)安装:
[0068]
将制作完的导料板按设计位置临时定位于磨盘上方,并将支架主梁、支架副梁顶在导料板基座下方,调整支架主梁另一端,使之靠在磨机中心下料管上,先点焊定位主梁,再分别将支架上拉筋、支架侧拉筋点焊定位于中心下料管和主梁上,然后分别焊牢;点焊导料板基座和支架主梁、支架副梁支撑处,现场配钻加工导料板基座和支架主梁、支架副梁的定位螺栓孔,然后用螺栓螺母固定,完成安装。
[0069]
应用实施例,上述技术方案,应用于具有挡料板的立式磨辊上,形成外挡内导结构;其挡料板方案主要用于控制被磨辊挤出的物料,具体结构为,磨辊挡料总成包括挡料板和支架总成,其中所述挡料板为向磨辊中心倾斜的v型挡料板,靠近磨辊侧为反射板,远离磨辊侧为拦截板;虽然通过加长拦截板的长度也能挡住一部分未经磨辊碾压由磨盘直接甩出的物料,但拦截板加长后会影响磨辊碾压后物料的排料,尤其是细粉的排出。因此,根据triz创新理论,拦截板的长度同控制旁路物料和排出碾压过物料,构成了物理冲突。为解决此物理冲突,通过triz创新理论求解,得到“分离”方案,即将拦截板的长度分两个部分,一部分仍在现在位置,另一部分移至图1所示的磨辊内侧物料导流板4。物料导流板同外侧挡料板内外配合,将磨盘划分为两个区域,一是喂料区,二是排料区。喂料区完全封死未被碾压而直接旁路的物料;排料区通过缩短拦截板的长度和降低挡料圈两种措施,实现碾压后物料的顺利排料。外挡内导方案的工业试验数据如表1所示。
[0070]
表1 trm53.4生料磨外挡内导物料运动控制方案工业试验数据
[0071][0072]
根据表1trm53.4生料磨外挡内磨盘物料运动控制方案的工业试验数据,相比应用前传统立式辊磨技术,采用外挡内导方案,在挡料圈高度降低35.7%的条件下,磨机振值仍下降1.4mm/s,平均产量增加12.1%,主机电耗降低18.7%,证明了本方案在改善磨机稳定性、提高研磨效率的技术效果。
[0073]
物料运动控制实现过程如下:物料自中心下料管在重力作用下掉落至磨盘,并跟随磨盘一起旋转,受离心力及落料冲击分散作用从磨盘中心向磨盘边缘运动,待运至导料
板处改变方向在旋转磨盘的带动下沿导料板运动至导料板前端进入喂料区,然后跟随磨盘做近似螺旋运动,待运动至挡料板末端,沿挡料板向磨辊下方运动,并被挡料板前端v型反射板强制送至磨辊大端研磨区进行研磨。由于导料板前端同挡料板末端基本处于同一个半径方向上,而离开导料板的物料作近似螺旋运动,因此未被碾压的物料将全部被挡料板送入磨辊下方碾压。此外,导料板还具有将磨辊碾压后的物料强制排出磨盘进入风环的作用,改善挡料圈以下物料中细粉富集对料层的破坏作用,根据天津院某trm53.4生料磨工业试验数据,相同的挡料圈高度下,相比传统立式辊磨技术,平均产量增加12.1%,主机电耗降低18.7%。
[0074]
以上所述仅为本发明的较佳实施例而已,并不用以限制本发明,凡在本发明的精神和原则之内所作的任何修改、等同替换和改进等,均应包含在本发明的保护范围之内。
再多了解一些
本文用于企业家、创业者技术爱好者查询,结果仅供参考。