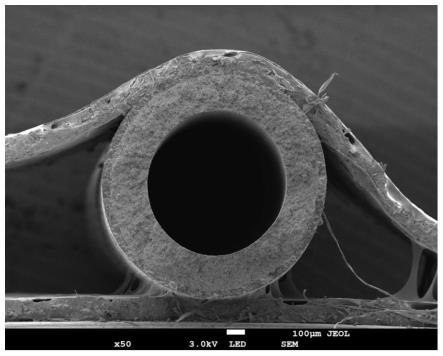
1.本发明涉及聚合物膜材料技术领域,尤其涉及一种聚偏氟乙烯中空纤维膜及其制备方法和应用。
背景技术:
2.臭氧氧化工艺在国内外饮用水生产中得到普遍关注。主要原因是其有效的消毒能力,化学氧化能力、去除痕量污染物的能力以及不会产生传统加氯消毒过程出现的致癌副产物。痕量污染物通常来自农业或工业产生的面源和点源。近年来,臭氧微泡 超滤技术处理微污染水源成为了市政自来水处理技术的一项新选择。
3.由于臭氧具有强氧化性,普通超滤膜的高分子链段很容易被臭氧渗透破坏,因此,市面上大部分超滤膜产品无法满足在具有臭氧的环境中使用的要求。
4.鉴于此,提供一种满足在臭氧环境使用,具有高强度、高结晶度、高断裂伸长率的优良超/微滤膜是目前本领域技术人员迫切需要解决的技术问题。
技术实现要素:
5.基于上述存在的问题,本发明提供了一种聚偏氟乙烯中空纤维膜及其制备方法和应用,该聚偏氟乙烯中空纤维膜具有强耐氧化性,兼具高强度、高结晶度以及高断裂伸长率的优点,能够在含有臭氧的水环境中长期使用。
6.本发明实施例具体内容如下:
7.第一方面,本发明提供一种聚偏氟乙烯中空纤维膜,所述中空纤维膜由外层致密膜结构和内层多孔膜结构组成,所述外层致密膜结构和内层多孔膜结构之间无连接界面;所述外层致密膜结构为紧密堆积的棱形片晶簇结构;所述内层多孔膜结构为通透的海绵状多孔结构;
8.其中,所述外层致密膜结构的孔径为0.02μm~0.1μm,所述外层致密膜结构的厚度为30μm~50μm,所述外层致密膜结构的结晶度大于60%;
9.所述内层多孔膜结构的孔径为1μm~10μm,所述内层多孔膜结构的厚度为150~250μm,所述内层多孔膜结构的结晶度为40%~50%。
10.可选地,所述中空纤维膜的强度大于4mpa,所述中空纤维膜的断裂伸长率大于100%。
11.可选地,所述中空纤维膜是以聚偏氟乙烯均聚物为原料,在稀释剂的作用下制备得到的;所述稀释剂包括第一稀释剂和第二稀释剂;
12.其中,所述第一稀释剂包括:二苯甲酮或水杨酸甲酯;
13.所述第二稀释剂由所述聚偏氟乙烯的溶剂与所述聚偏氟乙烯的非溶剂组成,其中,所述聚偏氟乙烯的溶剂包括:二苯甲酮、碳酸二苯酯、邻苯二甲酸二乙酯、三乙酸甘油酯或苯甲酸甲酯;
14.所述聚偏氟乙烯的非溶剂包括:乙二醇、聚乙二醇200、聚乙二醇400、聚乙二醇
600、二甘醇、三甘醇、己二酸二辛酯、邻苯二甲酸二辛酯、四甘醇和正辛醇中的至少一种。
15.可选地,所述聚偏氟乙烯均聚物的平均分子量为30万-60万,所述聚偏氟乙烯均聚物的熔点为110℃~112℃。
16.第二方面,本发明提供一种制备上述第一方面所述的聚偏氟乙烯中空纤维膜的方法,所述方法包括如下步骤:
17.s1、将第一稀释剂与聚偏氟乙烯均聚物的混合物升温至200℃~250℃,形成均相溶液,静置脱泡,得到表层铸膜液;
18.s2、将第二稀释剂与聚偏氟乙烯均聚物的混合物升温至200℃~250℃,形成均相溶液,静置脱泡,得到内层铸膜液;
19.s3、将所述表层铸膜液、所述内层铸膜液与内芯液分别通过各自的双螺杆挤出机高温剪切熔混挤出,并在三通道喷丝头处与内芯液汇合,形成内腔含高温内芯液的纤维状均相高温铸膜溶液;其中,所述内芯液注入内芯通道,所述内层铸膜液注入内层通道,所述外层铸膜液注入外层通道;
20.s4、将所述内腔含高温内芯液的纤维状均相高温铸膜溶液直接浸入 40℃~60℃的水浴中冷却,停留1~2秒后收卷,得到固化的中空纤维膜;其中,所述内芯液溶于水;
21.s5、用乙醇去除步骤s4中得到的所述固化的中空纤维膜中的所述第一稀释剂和所述第二稀释剂,得到聚偏氟乙烯中空纤维膜。
22.可选地,在步骤s1中,所述表层铸膜液包括重量百分比为20wt%~ 30wt%的聚偏氟乙烯均聚物。
23.可选地,在步骤s2中,所述内层铸膜液包括重量百分比为25wt%~ 35wt%的聚偏氟乙烯均聚物。
24.可选地,在步骤s3中,所述内芯液为丙三醇、1,2-丙二醇或2,3-丁二醇中的一种或多种。
25.可选地,在步骤s4中,所述聚偏氟乙烯均聚物与所述第一稀释剂发生固-液相分离形成所述中空纤维膜的外层致密膜结构;
26.所述聚偏氟乙烯均聚物与所述第二稀释剂发生液-液相分离形成所述中空纤维膜的内层多孔膜结构。
27.第三方面,本发明提供一种制备上述第一方面所述的聚偏氟乙烯中空纤维膜的应用,将所述聚偏氟乙烯中空纤维膜应用于臭氧水处理工程中;其中,所述臭氧水包括含有臭氧微气泡的水环境。
28.与现有技术相比,本发明提供的一种聚偏氟乙烯中空纤维膜及其制备方法包括以下优点:
29.1、传统的邻苯二甲酸增塑剂类的稀释剂,由于体系粘稠度较大,聚偏氟乙烯(pvdf)与这类稀释剂分相之后,生长较慢,晶核较少,更容易形成较松散的球粒堆积状的片晶簇结构,这种结构结晶度稍低,且球晶之前的空隙较大,给了臭氧更大的渗透空间。而本发明提供的聚偏氟乙烯中空纤维膜为双层结构,其外层为致密结构(紧密堆积的棱形片晶簇结构),pvdf 结晶度高达60%以上,具备很强的防臭氧渗透性能;其内层为海绵状多孔结构,有效的保证了聚偏氟乙烯中空纤维膜的强度以及断裂伸长率。本发明通过外层紧密堆积的棱形片晶簇结构与内层海绵状多孔结构相结合,使得聚偏氟乙烯中空纤维膜的外表面
具有很强的臭氧氧化抵抗力,同时聚偏氟乙烯中空纤维膜整体又具有优秀的膜强度以及断裂伸长率,特别适用于有大量臭氧微泡存在的超强臭氧压力快速氧化(aop)水处理过程。
30.2、本发明提供的聚偏氟乙烯中空纤维膜的制备方法,通过选择不同的稀释剂,使得铸膜液在固化过程中,表层铸膜液中的聚偏氟乙烯与稀释剂发生固-液相分离而致密化,内层铸膜液中的聚偏氟乙烯与稀释剂发生液-液相分离而呈现出海绵状多孔结构;此外,由于本发明提供的中空纤维膜是以聚偏氟乙烯均聚物为原料,因此,表层和内层均由聚偏氟乙烯物质组成,之间并不存在连接界面,使得本发明提供的中空纤维膜的具有较好的稳定性,能够在含有臭氧的水环境中长期使用。
附图说明
31.为了更清楚地说明本技术实施例或现有技术中的技术方案,下面将对实施例或现有技术描述中所需要使用的附图作简单地介绍,显而易见地,下面描述中的附图仅仅是本技术的一些实施例,对于本领域普通技术人员来讲,在不付出创造性劳动的前提下,还可以根据这些附图获得其他的附图。
32.图1示出了本发明实施例中的聚偏氟乙烯中空纤维膜的制备方法流程图;
33.图2示出了本发明实施例中的聚偏氟乙烯中空纤维膜截面的结构图;
34.图3示出了本发明实施例中的聚偏氟乙烯中空纤维膜截面外层的放大图;
35.图4示出了本发明实施例中的聚偏氟乙烯中空纤维膜截面内层的放大图;
36.图5示出了本发明实施例中的聚偏氟乙烯中空纤维膜进行耐臭氧测试装置示意图;
37.图6示出了本发明实施例中的聚偏氟乙烯中空纤维膜在臭氧环境中的断裂伸长率变化情况;
38.图7示出了本发明实施例中的聚偏氟乙烯中空纤维膜在臭氧环境中的强度变化情况。
具体实施方式
39.提供下述实施例是为了更好地进一步理解本发明,并不局限于所述最佳实施方式,不对本发明的内容和保护范围构成限制,任何人在本发明的启示下或是将本发明与其他现有技术的特征进行组合而得出的任何与本发明相同或相近似的产品,均落在本发明的保护范围之内。
40.实施例中未注明具体实验步骤或者条件,按照本领域内的现有技术所描述的常规实验步骤的操作或条件即可进行。所用试剂以及其他仪器未注明生产厂商者,均为可以通过市购获得的常规试剂产品。
41.考虑到臭氧环境的特殊性,本发明的发明人仔细研究目前市面上的超滤膜产品发现,现有超滤膜大多通过非溶剂相分离(non-solvent induced phaseseparation,nips)法制备。利用nips法制备的超滤膜的结晶度在20~40%之间。而通过热致相分离法(thermally induced phase separation,tips)制得的超滤膜一般具有海绵状双连续结构,并且具有较高的机械性能。此外,由于tips过程的高温高压,铸膜液粘度较低,在降温分相时,更有利于聚合物的结晶,因此所得到的超滤膜的结晶度一般能达到40~50%。
42.蒸汽诱导相分离法(vapor induced phase separation,vips)是另外一种改良的nips,先将湿膜在一定温度/湿度的空气中暴露一定时间,再将湿膜浸没到非溶剂中完成分相,这样可减缓分相速率,提高结晶度。peng等(appliedsurface science 263(2012)131-144)通过延长在水蒸气中的暴露时间,膜断面的指状孔结构逐渐消失,全部由球节状结晶颗粒组成,膜的结晶度最大增到 10%。但结晶度的提升会大大降低pvdf膜的机械强度(约1mpa),导致其使用价值不高。
43.其他常规提高pvdf的结晶度的方法有拉伸法,例如tang等 (membranes,2020,10,38)将tips法pvdf微孔膜(海绵状多孔结构) 以40mm/min拉伸延长20%以后,其结晶度从43.6%提高到50.8%;继续拉伸延长到100%,其结晶度提高到53.6%,未再有明显的变化。但拉伸后的膜一般孔径会增大,这会降低了膜的分离精度。
44.鉴于对现有技术的研究,本发明为了为解决现有常规手段制备得到的超 /微滤膜不能兼具高强度、高结晶度、高断裂伸长率的优良性能,因而不能在含有臭氧的水环境中长期使用的问题,本发明提出的技术构思为:本发明采用热致相分离法,通过选择不同的稀释剂分别制备表层铸膜液与内层铸膜液,使得铸膜液在固化成膜过程中,表层铸膜液中的pvdf与第一稀释剂在外表面发生固-液相分离,形成紧密堆积的棱形片晶簇结构(该结构可以理解为pvdf形成的大量晶核,经快速生长形成球晶,球晶迅速紧密堆积,形成了如说明书附图3所示的棱形的片晶簇结构),该致密的pvdf膜结构层的结晶度高达60%,具备优秀的防渗透能力,能有效抵抗臭氧的氧化破坏,而内层铸膜液中的pvdf与第二稀释剂在表层以下发生液-液相分离,形成内层海绵状多孔结构,该多孔的pvdf膜结构层有效的保证了聚偏氟乙烯中空纤维膜具有较高的强度(大于4mpa)以及断裂伸长率(大于100%)。通过外层紧密堆积的棱形片晶簇结构与内层海绵状多孔结构相结合,使得聚偏氟乙烯中空纤维膜的外表面具有很强的臭氧氧化抵抗力,同时,聚偏氟乙烯中空纤维膜整体又具有优秀的膜强度以及断裂伸长率,特别适用于有大量臭氧微泡存在的超强臭氧压力快速氧化(aop)水处理过程。基于上述技术构思,发明人提供了一种聚偏氟乙烯中空纤维膜及其制备方法和应用,具体实施内容如下:
45.第一方面,本发明提供一种聚偏氟乙烯中空纤维膜,该中空纤维膜由外层致密膜结构和内层多孔膜结构组成,外层致密膜结构和内层多孔膜结构之间无连接界面;外层致密膜结构为紧密堆积的棱形片晶簇结构;内层多孔膜结构为通透的海绵状多孔结构;
46.其中,棱形片晶簇结构区域的孔径为0.02μm~0.1μm,棱形片晶簇结构区域的厚度为30μm~50μm,棱形片晶簇结构区域的结晶度大于60%;
47.海绵状多孔结构区域的孔径为1μm~10μm,海绵状多孔结构区域的厚度为150~250μm,海绵状多孔结构区域的结晶度为40%~50%。
48.具体实施时,由于臭氧具有强氧化性,含臭氧/臭氧微气泡的水处理过程中使用到的超滤膜应具备高强度的性能,以阻止臭氧对膜结构的渗透破坏。为了提供一种能够用于含臭氧/臭氧微气泡水处理的超滤膜,本发明选择具有较强抗氧化性的聚偏氟乙烯(pvdf)作为制备超滤膜的原材料;此外,本发明还利用热致相分离法(thermally induced phase separation,tips)制备出具有不同结构的聚偏氟乙烯组成的中空纤维膜,使得外层聚偏氟乙烯膜为致密结构,内层聚偏氟乙烯膜为海绵状多孔结构,这种聚偏氟乙烯中空纤维膜具有强耐氧化性,兼具高强度、高结晶度以及高断裂伸长率的优点,能够在含有臭氧的水环境
中长期使用。
49.具体实施时,为有效的阻止臭氧对膜结构的渗透破坏,本发明提供的聚偏氟乙烯膜结构,其外层致密膜结构的孔径控制在0.02μm~0.1μm,结晶度大于60%,厚度为30μm~50μm,能避免臭氧的渗透,从而对聚偏氟乙烯膜的内部结构造成氧化破坏;同时,本发明为进一步增大聚偏氟乙烯膜结构的强度以及断裂伸长率,以提高聚偏氟乙烯膜的使用寿命,将内层制备成海绵状多孔膜结构,其孔径控制在1μm~10μm,结晶度为40%~50%,厚度为 150~250μm,内层海绵状多孔膜结构保证了聚偏氟乙烯膜具备高强度以及高断裂伸长率的性能。
50.可选地,中空纤维膜的强度大于4mpa,中空纤维膜的断裂伸长率大于 100%。
51.可选地,中空纤维膜是以pvdf均聚物为原料,在稀释剂的作用下制备得到的;稀释剂包括第一稀释剂和第二稀释剂;
52.其中,第一稀释剂包括:二苯甲酮或水杨酸甲酯;
53.所述第二稀释剂由所述聚偏氟乙烯的溶剂与所述聚偏氟乙烯的非溶剂组成,其中,所述聚偏氟乙烯的溶剂包括:二苯甲酮、碳酸二苯酯、邻苯二甲酸二乙酯、三乙酸甘油酯或苯甲酸甲酯;
54.所述聚偏氟乙烯的非溶剂包括:乙二醇、聚乙二醇200、聚乙二醇400、聚乙二醇600、二甘醇、三甘醇、己二酸二辛酯、邻苯二甲酸二辛酯、四甘醇和正辛醇中的至少一种。
55.具体实施时,为了得到上述聚偏氟乙烯膜结构,本发明选择使用不同的稀释剂分别制备表层铸膜液和内层铸膜液,使得铸膜液在固化成膜时,铸膜液中的稀释剂与聚偏氟乙烯在降温过程中因分相机理不同而产生不同的分相效果,其中,表层铸膜液在降温固化成膜时,因第一稀释剂的特性,pvdf 与二苯甲酮或水杨酸甲酯这两种稀释剂之间只发生固-液相分离,也就是说 pvdf因结晶固化而从第一稀释剂中析出。此外,不同于其他与pvdf发生固-液相分离的稀释剂,pvdf在这二苯甲酮或水杨酸甲酯中特别容易形成大量的晶核,大量晶核分别极速生长为球晶并迅速最紧密堆积,形成了棱形的片晶簇结构(其他稀释剂与pvdf发生固-液相分离得到的是球粒堆积的结构而非强度和反渗透性能更好的棱形的片晶簇结构);而内层铸膜液在降温固化成膜时,pvdf与第二稀释剂间发生的是液-液相分离,pvdf包裹第二稀释剂,形成pvdf海绵状骨架包裹住稀释剂液滴,最终,随着温度的降低 (120℃以下)pvdf的固化而结束。当pvdf海绵状骨架中包裹的稀释剂液滴被乙醇萃取后,就形成了内层的海绵状多孔结构。
56.可选地,聚偏氟乙烯均聚物的平均分子量为30万-60万,聚偏氟乙烯均聚物的熔点为110℃~112℃。
57.第二方面,本发明提供一种制备上述第一方面的聚偏氟乙烯中空纤维膜的方法,图1示出了本发明实施例中的聚偏氟乙烯中空纤维膜的制备方法流程图,如图1所示,该方法包括如下步骤:
58.s1、将第一稀释剂与聚偏氟乙烯均聚物的混合物升温至200℃~250℃,形成均相溶液,静置脱泡得到表层铸膜液;
59.s2、将第二稀释剂与聚偏氟乙烯均聚物,升温至200℃~250℃,形成均相溶液,静置脱泡得到内层铸膜液;
60.s3、将表层铸膜液、内层铸膜液与内芯液分别通过各自的双螺杆挤出机高温剪切
熔混挤出,并在三通道喷丝头处与内芯液汇合,形成内腔含高温内芯液的纤维状均相高温铸膜溶液;其中,内芯液注入内芯通道,内层铸膜液注入内层通道,外层铸膜液注入外层通道。
61.本实施步骤在具体实施时,内芯液为耐高温液体,且不溶于第一稀释剂和第二稀释剂。
62.s4、将内腔含高温内芯液的纤维状均相高温铸膜溶液直接浸入40℃~ 60℃的水浴冷却,停留1~2秒后收卷,得到固化的中空纤维膜。
63.本实施步骤在具体实施时,表层铸膜液与内层铸膜液中的聚偏氟乙烯均聚物在水浴冷却过程中,温度降低而固化成多孔膜,并将稀释剂包裹在孔隙中,而内芯液溶于水中,便形成了固化的中空纤维膜。
64.s5、用乙醇去除步骤s4中得到的中空纤维膜中的稀释剂,得到聚偏氟乙烯中空纤维膜。
65.具体实施时,制备方法步骤s3中,专用喷丝头为三层结构,内层直径 0.6~0.8mm,为芯液流道;中间层直径1.2~2.0mm,为内层铸膜液流道;这两层分别通过高温计量泵精确计量进入喷丝头的溶体流量;第三层为外层铸膜液流道,直径2.0~2.5mm。
66.具体实施时,pvdf在高温下溶于第一稀释剂(二苯甲酮或水杨酸甲酯),形成表层铸膜液,并在40℃~60℃水浴降温过程中更容易发生pvdf固化结晶析出,并且使得pvdf在这两种稀释剂中可形成大量的晶核,且生长极快,极速生长的球晶迅速最紧密堆积,形成了棱形的片晶簇结构,这种结构的pvdf结晶度高,防渗透性强,具有很强的臭氧氧化抵抗力。相应地,pvdf 在高温下溶于第二稀释剂形成内层铸膜液,并在40℃~60℃水浴降温过程中,由于热传递作用,降温较表层铸膜液慢,降温过程中内层铸膜液更容易发生液-液分离,最终形成内层海绵状多孔结构。本发明构建的外层紧密堆积的棱形片晶簇与内层海绵状多孔相结合的孔结构,在显著提高了膜外表面对于高浓度的臭氧微泡的同时,同时又保障了膜的强度以及断裂伸长率,特别适用于有大量臭氧微泡存在的超强臭氧压力快速氧化(aop)水处理过程。
67.可选地,在步骤s1中,表层铸膜液包括重量百分比为20wt%~30wt%的聚偏氟乙烯均聚物。
68.具体实施时,表层铸膜液中,聚偏氟乙烯均聚物的重量百分比优选为 20wt%~30wt%。
69.可选地,在步骤s2中,内层铸膜液包括重量百分比为25wt%~35wt%的聚偏氟乙烯共聚物。
70.具体实施时,内层铸膜液中,聚偏氟乙烯均聚物的重量百分比优选为 20wt%~25wt%
71.可选地,在步骤s3中,内芯液为丙三醇、1,2-丙二醇或2,3-丁二醇中的一种或多种。
72.可选地,在步骤s4中,聚偏氟乙烯均聚物与第一稀释剂发生固-液相分离形成中空纤维膜的外层致密膜结构;聚偏氟乙烯均聚物与第二稀释剂发生液-液相分离形成中空纤维膜的内层多孔膜结构。
73.第三方面,本发明提供一种上述第一方面的聚偏氟乙烯中空纤维膜的应用,将聚
偏氟乙烯中空纤维膜应用于臭氧水处理工程中;其中,臭氧水包括含有臭氧微气泡的水环境。
74.为使本领域技术人员更好地理解本发明,以下通过多个具体的实施例来说明本发明的聚偏氟乙烯中空纤维膜的制备方法。
75.实施例1
76.具体实施步骤如下:
77.(1)表层铸膜液的准备:将表层稀释剂与聚偏氟乙烯均聚物,升温至 200℃~250℃,形成均相溶液,静置脱泡,得到铸膜液;其中聚偏氟乙烯质量浓度为20wt%,稀释剂为二苯甲酮,质量浓度比为80:20;
78.(2)内层铸膜液的准备:将内层稀释剂与聚偏氟乙烯均聚物,升温至 200℃~250℃,形成均相溶液,静置脱泡,得到铸膜液;其中聚偏氟乙烯质量浓度为25wt%,稀释剂为二苯甲酮与十四醇的共混物,质量浓度比为15: 25;
79.(3)中空纤维膜的挤出:将表层与内层铸膜液分别通过双螺杆挤出机进一步高温剪切熔混,并最终在喷丝头处与内芯液和汇合,一道通过喷丝头挤出,形成内腔含高温内芯液的纤维状均相高温铸膜溶液;内芯液为丙三醇;
80.(4)降温固化成膜:纤维状均相高温溶液直接浸入45℃的水浴冷却,停留2秒后收卷;
81.(5)乙醇除稀释剂:用乙醇去除步骤(4)所得膜丝中的稀释剂,得到高结晶度的聚偏氟乙烯中空纤维膜。图2示出了本发明实施例中的聚偏氟乙烯中空纤维膜截面的结构图,此外,图3进一步示出了本发明实施例中的聚偏氟乙烯中空纤维膜截面外层的放大图;图4进一步示出了本发明实施例中的聚偏氟乙烯中空纤维膜截面内层的放大图;如图2-图4所示,本发明提供的聚偏氟乙烯中空纤维膜的外层致密膜结构为紧密堆积的棱形片晶簇结构,内层多孔膜结构为海绵状多孔结构。
82.(6)膜性能测试:
83.中空纤维膜丝纯水通量:将在浸渍于乙醇之后重复了多次在纯水中的浸渍的约30cm长的湿润中空纤维膜的一端密封、并从另一端将注射针插入中空部内,在25℃的环境中使25℃的纯水从注射针以0.1mpa的压力从中空部内透过至外表面的纯水量,并利用下式确定了纯水通量。
84.纯水通量[l/
㎡
/h(lmh)]=60
×
(透过水量[l])/{π
×
(膜外径[m])
×
(膜有效长度[m])
×
(测定时间[min])}
[0085]
中空纤维膜丝强度:采用电子万能试验机进行测试,测试速度为 25mm/min,测试温度为室温,上下夹具的间距为50mm。膜丝强度的计算公式为:膜丝强度[mpa]=拉力[n])/中空纤维膜横截面面积[
㎡
]。
[0086]
结晶度(xc):采用差示扫描量热仪(dsc)进行测试。首先以从室温升至200℃消除样品中的热历史,再降温至室温获得结晶温度(tc)和结晶焓(δhc),然后再次升温至200℃获得熔融温度(tm)和熔融焓(δhm)。计算试样中pvdf的结晶度:xc=δhf/δh
f*
×
100%。其中,δhf为dsc测试得到的熔融焓,δh
f*
=104.5j/g,为pvdf完全结晶后的熔融焓。
[0087]
耐臭氧性:图5示出了本发明实施例中的聚偏氟乙烯中空纤维膜进行耐臭氧测试装置示意图,反应在室温下进行。高纯氧气(99.9%)通过流量计后被送入臭氧发生器,臭氧
以0.5l/min的流量通过微孔曝气头连续注入超纯水中,在平衡状态下用靛蓝法测得的饱和臭氧水中臭氧浓度为(5
±
0.5)mg/l。含臭氧微泡用臭氧气体浓度比色卡进行测试,含量约为2%。将含有臭氧微泡的水通入小型超滤膜组件中,持续冲刷中空纤维膜丝外表面,每隔5天取1根膜丝进行强度与断裂伸长率测试,实验共进行60天。
[0088]
制备得到膜丝性能检测结果:膜丝外径1.3mm,内径0.1mm,纯水通量 695l/(m2·
h)/0.1mpa,膜丝强度4.61mpa,断裂伸长率121%。外层结晶度 64.1%,内层结晶度48.1%。
[0089]
实施例2
[0090]
具体实施步骤如下:
[0091]
(1)表层铸膜液的准备:将表层稀释剂与聚偏氟乙烯均聚物,升温至 200℃~250℃,形成均相溶液,静置脱泡得到铸膜液;其中聚偏氟乙烯质量浓度为20wt%,稀释剂为水杨酸甲酯,质量浓度比为80:20;
[0092]
(2)内层铸膜液的准备:将内层稀释剂与聚偏氟乙烯均聚物,升温至 200℃~250℃,形成均相溶液,静置脱泡得到铸膜液;其中聚偏氟乙烯质量浓度为25wt%,稀释剂为二苯甲酮与十四醇的共混物,质量浓度比为15: 25;
[0093]
(3)中空纤维膜的挤出:将表层与内层铸膜液分别通过双螺杆挤出机进一步高温剪切熔混,并最终在喷丝头处与内芯液和汇合,一道通过喷丝头挤出,形成内腔含高温内芯液的纤维状均相高温铸膜溶液;内芯液为丙三醇;
[0094]
(4)降温固化成膜:纤维状均相高温溶液直接浸入45℃的水浴冷却,停留2秒后收卷;
[0095]
(5)乙醇除稀释剂:用乙醇去除步骤(4)所得膜丝中的稀释剂,得到高结晶度的聚偏氟乙烯中空纤维膜。
[0096]
(6)膜性能测试:同实施例1
[0097]
制备得到膜丝性能检测结果:膜丝外径1.3mm,内径0.1mm,纯水通量 662l/(m2·
h)/0.1mpa,膜丝强度4.41mpa,断裂生产率112%。外层结晶度 66.5%,内层结晶度51.1%。
[0098]
实施例3
[0099]
具体实施步骤如下:
[0100]
(1)表层铸膜液的准备:将表层稀释剂与聚偏氟乙烯均聚物,升温至 200℃~250℃,形成均相溶液,静置脱泡得到铸膜液;其中聚偏氟乙烯质量浓度为25wt%,稀释剂为水杨酸甲酯,质量浓度比为15:25;
[0101]
(2)内层铸膜液的准备:将内层稀释剂与聚偏氟乙烯均聚物,升温至 200℃~250℃,形成均相溶液,静置脱泡得到铸膜液;其中聚偏氟乙烯质量浓度为30wt%,稀释剂为二苯甲酮与十四醇的共混物,质量浓度比为15: 25;
[0102]
(3)中空纤维膜的挤出:将表层与内层铸膜液分别通过双螺杆挤出机进一步高温剪切熔混,并最终在喷丝头处与内芯液和汇合,一道通过喷丝头挤出,形成内腔含高温内芯液的纤维状均相高温铸膜溶液;内芯液为丙三醇;
[0103]
(4)降温固化成膜:纤维状均相高温溶液直接浸入45℃的水浴冷却,停留2秒后收卷;
[0104]
(5)乙醇除稀释剂:用乙醇去除步骤(4)所得膜丝中的稀释剂,得到高结晶度的聚偏氟乙烯中空纤维膜。
[0105]
(6)膜性能测试:同实施例1
[0106]
制备得到膜丝性能测试结果:膜丝外径1.3mm,内径0.1mm,纯水通量 312l/(m2·
h)/0.1mpa,膜丝强度1.68mpa,断裂伸长率156%。外层结晶度 62.1%,内层结晶度45.3%。
[0107]
实施例4
[0108]
具体实施步骤如下:
[0109]
(1)表层铸膜液的准备:将表层稀释剂与聚偏氟乙烯均聚物,升温至 200℃~250℃,形成均相溶液,静置脱泡得到铸膜液;其中聚偏氟乙烯质量浓度为20wt%,稀释剂为水杨酸甲酯,质量浓度比为15:25;
[0110]
(2)内层铸膜液的准备:将内层稀释剂与聚偏氟乙烯均聚物,升温至 200℃~250℃,形成均相溶液,静置脱泡得到铸膜液;其中聚偏氟乙烯质量浓度为25wt%,稀释剂为邻苯二甲酸二丁酯(dbp)/邻苯二甲酸二辛酯(dop) 共混物,质量浓度比为15:25;
[0111]
(3)中空纤维膜的挤出:将表层与内层铸膜液分别通过双螺杆挤出机进一步高温剪切熔混,并最终在喷丝头处与内芯液和汇合,一道通过喷丝头挤出,形成内腔含高温内芯液的纤维状均相高温铸膜溶液;内芯液为丙三醇;
[0112]
(4)降温固化成膜:纤维状均相高温溶液直接浸入45℃的水浴冷却,停留2秒后收卷;
[0113]
(5)乙醇除稀释剂:用乙醇去除步骤(4)所得膜丝中的稀释剂,得到高结晶度的聚偏氟乙烯中空纤维膜。
[0114]
(6)膜性能测试:同实施例1
[0115]
制备得到膜丝性能测试结果:膜丝外径1.3mm,内径0.1mm,纯水通量 933l/(m2·
h)/0.1mpa,膜丝强度3.96mpa,断裂伸长率101%。外层结晶度 63.5%,内层结晶度52.4%。
[0116]
比较例1:
[0117]
将聚偏氟乙烯共聚物(20wt%)溶解于n-n二甲基甲酰胺(80wt%)中,于10℃油浴中持续搅拌2h形成均相铸膜液。铸膜液静置12h以上脱泡待用。脱泡好的铸膜液通过喷丝头形成中空纤维膜,在空气中停留1s,然后进入水浴中浸泡半小时,取出放入去离子水中浸洗,并保存于去离子水中待用。
[0118]
制备得到膜丝性能:膜丝外径1.3mm,内径0.1mm,纯水通量在341 l/(m2·
h)/0.1mpa,膜丝强度2.31mpa,断裂伸长率168%,结晶度31.2%。
[0119]
比较例2:
[0120]
将聚偏氟乙烯、疏水纳米二氧化硅与稀释剂共混,其中聚偏氟乙烯共聚物质量浓度为30wt%,稀释剂质量浓度为10wt%;稀释剂为邻苯二甲酸二丁酯(dbp)/邻苯二甲酸二辛酯(dop)的混合物,其中dbp与dop质量浓度比为60:40。将上述混合物升温至200℃,静置脱泡得到铸膜液;将铸膜液通过双螺杆挤出机进一步高温剪切熔混,通过喷丝头挤出,并迅速浸入冷却液中冷却,最后固化成膜;先用二氯乙烷萃取掉稀释剂,然后用氢氧化钠将疏水纳米二氧化硅溶解,即得到pvdf中空纤维微孔膜。
[0121]
制备得到膜丝性能:膜丝外径1.3mm,内径0.1mm,纯水通量在1021 l/(m2·
h)/0.1mpa,膜丝强度1.63mpa,断裂伸长率82%,结晶度42.1%。
[0122]
表1示出了本发明实施例与比较例制备的pvdf中空纤维膜的通量、强度、截留率统计表。
[0123]
表1聚偏氟乙烯中空纤维膜的通量、强度、截留率统计表
[0124][0125]
图6示出了本发明实施例中的聚偏氟乙烯中空纤维膜在臭氧环境中的断裂伸长率变化情况,具体为为本发明实施例1分别与比较例1、比较例2在臭氧中的断裂伸长率对比图;图1示出了本发明实施例中的聚偏氟乙烯中空纤维膜在臭氧环境中的强度变化情况,具体为为本发明实施例1分别与比较例1、比较例2在臭氧中的强度对比图。从图6、图1以及上表1中可以分析得出,与现有技术制备的膜材料相比,本发明提供的聚偏氟乙烯中空纤维膜在高浓度臭氧环境中的强度与断裂伸长率随时间的增加,降低程度更低,在高浓度臭氧环境中使用更长久。
[0126]
以上对本发明所提供的一种聚偏氟乙烯中空纤维膜及其制备方法和应用进行了详细介绍,本文中应用了具体个例对本发明的原理及实施方式进行了阐述,以上实施例的说明只是用于帮助理解本发明的方法及其核心思想;同时,对于本领域的一般技术人员,依据本发明的思想,在具体实施方式及应用范围上均会有改变之处,综上所述,本说明书内容不应理解为对本发明的限制。
再多了解一些
本文用于企业家、创业者技术爱好者查询,结果仅供参考。