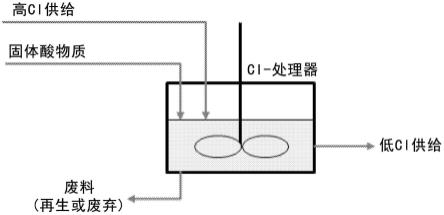
1.本发明涉及一种利用固体酸物质去除含有高含量氯的废油馏分中的氯的方法。
背景技术:
2.通过废塑料热解油等废料的裂化(cracking)、热解(pyrolysis)反应生成的油馏分(废油馏分)中包含来自废料的大量的杂质,因此,当将其用作燃料时,会有排放so
x
、no
x
等大气污染物质的可能性,特别是存在cl成分在高温处理过程中转化为可能引发装置腐蚀的hcl并排放的问题。
3.以往,通过使用精炼(refinery)技术的加氢处理(hydrotreating,hdt)工艺将cl转化为hcl并去除,但废塑料热解油等废油馏分包含高含量的cl,因此,据报道,存在hdt工艺中形成的过量的hcl引起的装备腐蚀、反应异常和产品性状变差的问题,并且难以将未进行预处理的废油馏分引入到hdt工艺中。为了使用现有的精炼工艺去除cl油馏分,需要一种将cl含量减少至可以引入到精炼工艺中的水平的cl含量(数ppm的cl)的减少废油馏分的cl的处理技术。
4.现有技术1(日本公开专利1999-504672a)涉及一种由废橡胶和/或废塑料材料制备汽油、柴油机油和炭黑的方法。具体地,该现有技术1的特征在于,作为将废橡胶和废塑料进行热解而获得的热解油的一次杂质去除工艺,使用koh、naoh等碱性物质,通过结合去除cl、n和s等,并且二次催化裂化工艺(catalytic cracking)中包括进行热解油的裂化的同时去除cl、n和s,之后分离裂化(cracked)的油馏分,从而制备最终产品。但是,在一次杂质去除工艺中,通过中和来减少cl(使用koh、naoh等碱性物质),但在这种中和结合去除反应中,每单位重量的碱性物质的cl去除效率并不高,因此难以制备可以引入到精炼工艺中的水平的低含量cl油馏分(数ppm的cl)。此外,催化剂的使用周期短,并且再生所使用的(中和催化剂)物质的工艺复杂,因此在简化工艺方面不优选。
5.现有技术2(日本授权专利4218857b2)涉及一种氯化合物去除剂。具体地,该现有技术2的特征在于,利用氧化锌、滑石等粘土类氯去除剂来吸附去除包含氯化合物的流体中的cl,所述吸附去除是通过结合去除cl,并且与cl去除剂结合的cl不会脱离。但是,在现有技术2中,如液态烃中的氯化合物的去除性能评价试验中的记载,将氯化合物的含量小于10ppm的含有低含量cl的油馏分用作原料物质,并且这种通常利用吸附剂去除cl的技术适于长时间吸附微量的cl。因此,将吸附技术应用于含有高含量cl的废油馏分中并不有效。
6.现有技术3(日本公开专利2019-532118a)涉及一种使用脱挥挤出和氯化物清除剂对混合塑料热解油的脱氯方法。具体地,该现有技术3的特征在于,通过使用流化床催化剂的热解反应,将塑料或塑料热解油馏分转化为bp《370℃的轻(mild)油馏分,并去除cl。但是,热解反应的同时去除cl时,主要转化为烯烃与cl结合的有机cl形式后通过在固体酸位点结合或气体(gas)的排放来去除,由于同时产生水分,因此存在装备腐蚀、反应异常、产品性状变差和产品损耗(loss)问题。
7.因此,需要一种将以高含量含有cl的废油馏分减少至可以引入到精炼工艺中的水
平的cl含量(数ppm的cl)的减少废油馏分的cl的处理技术,此时,应最小化在应用该技术的工艺中的装备腐蚀、反应异常和产品性状变差的问题。
技术实现要素:
8.要解决的技术问题
9.本发明的目的在于,为了对含有高含量cl的废油馏分应用精炼(refinery)工艺来实现高附加值(燃料、化学(chemical)转化),提供一种使用固体酸物质减少含有高含量cl的废油馏分中的cl的技术。
10.具体地,本发明的目的在于提供一种如下的技术:对于通过废塑料热解回收的含有高含量cl的热解油,通过使用固体酸物质的cl催化转化反应去除90重量%以上的cl,从而转化为可以引入到精炼工艺中的水平的cl油馏分。
11.技术方案
12.本发明的一个具体实施方案提供一种去除废油馏分中的氯的方法,其特征在于,包括以下步骤:a)制备含氯废油馏分和固体酸物质的混合物;b)在惰性气体气氛的1巴(bar)以上且100巴以下的压力下,使所述混合物反应以去除氯;以及c)分离所述去除氯的油馏分和固体酸物质的混合物以回收去除氯的油馏分,其中,相对于总重量,所述废油馏分包含50重量%以下的沸点(boiling point,bp)为150℃以上的成分,并且满足以下关系式1。
13.[关系式1]
[0014]
0.85《b/a《1.15
[0015]
在关系式1中,a是相对于所述废油馏分的总重量的bp为150℃以上的成分的重量%,b是相对于所述去除氯的油馏分的总重量的bp为150℃以上的成分的重量%。
[0016]
所述废油馏分可以包含废塑料热解油、生物质(biomass)热解油、再生润滑油、含有高含量氯的原油(crude oil)或它们的混合物。
[0017]
所述废油馏分中的氯含量可以为10ppm以上。
[0018]
所述固体酸物质可以是沸石(zeolite)、粘土(clay)、磷酸硅铝(silica-alumina-phosphate,sapo)、磷酸铝(aluminum phosphate,alpo)、金属有机框架物(metal organic framework,mof)、二氧化硅-氧化铝(silica-alumina)或它们的混合物。
[0019]
在所述步骤a)中,相对于所述混合物的总重量,固体酸物质的含量可以为5-10重量%。
[0020]
所述步骤b)的反应可以是所述废油馏分中含有的氯直接结合在所述固体酸物质的活性位点而被去除和/或在活性位点转化为盐酸(hcl)而被去除的催化转化反应。
[0021]
所述步骤b)的反应可以在超过280℃且低于380℃的温度下进行。
[0022]
所述去除废油馏分中的氯的方法还可以包括以下步骤:d)将所述步骤a)、步骤b)和步骤c)至少重复1次以上。
[0023]
所述去除氯的油馏分中的氯含量可以小于10ppm。
[0024]
所述去除氯的油馏分中的氯与所述废油馏分中的氯的重量比可以为0.01-0.1。
[0025]
有益效果
[0026]
对于含有高含量cl的油馏分,去除90重量%以上的cl,从而可以转化为可以引入
到精炼工艺中的水平的cl油馏分。
[0027]
不仅可以去除油馏分中的cl,而且可以同时去除n、s等引发大气污染物质的杂质和as、na、ca等对精炼工艺催化活性产生不利影响的金属成分。
[0028]
可以直接或进行简单处理来将石油化工工艺中使用后废弃的废固体酸物质(废沸石、废粘土等)用作用于去除cl的固体酸物质,因此在环境方面优选。
[0029]
由于在油馏分性状没有实质性变化的情况下去除氯,可以防止低聚(oligomerization)引起的产品性状变差和裂化引起的产品损耗(loss)。
附图说明
[0030]
图1至图2是示出一个具体实施方案的去除氯的方法的示意图。
[0031]
图3至图4是示出不同反应温度下的残余n含量和残余s含量的图表。
[0032]
图5是示出不同反应温度下的油馏分组成变化的图表。
[0033]
图6至图7是示出不同反应时间的残余cl含量和cl减少率的图表。
[0034]
图8至图9是示出不同反应时间的残余n含量和残余s含量的图表。
[0035]
图10是示出不同反应时间的油馏分组成变化的图表。
[0036]
图11至图12是示出不同催化剂量的残余cl含量和cl减少率的图表。
[0037]
图13至图14是示出不同催化剂量的残余n含量和残余s含量的图表。
[0038]
图15是示出不同催化剂量的油馏分组成变化的图表。
具体实施方式
[0039]
除非另有定义,否则本说明书中使用的所有术语(包括技术术语和科学术语)可以以与本发明所属技术领域的技术人员通常理解的含义相同的含义使用。此外,除非另有相反的特别说明,否则说明书全文中描述某部分“包含”或“包括”某构成要素是指还可以包含其它构成要素,而不是排除其它构成要素。此外,除非在文中另有特别说明,否则单数形式还包括复数形式。
[0040]
除非另有特别定义,否则本说明书中“a-b”表示“a以上且b以下”。
[0041]
此外,除非另有特别定义,否则“a和/或b”表示选自a和b中的至少一种。
[0042]
除非另有定义,否则本说明书中废油馏分和去除氯的油馏分的沸点(bp)是指在常压(1atm)下测量的沸点。
[0043]
根据本发明的一个具体实施方案,提供一种去除废油馏分中的氯的方法。所述方法的特征在于,包括以下步骤:a)制备含氯废油馏分和固体酸物质的混合物;b)在惰性气体气氛的1巴以上且100巴以下的压力下,使所述混合物反应以去除氯;以及c)分离所述去除氯的油馏分和固体酸物质的混合物以回收去除氯的油馏分,其中,相对于总重量,所述废油馏分包含5-50的重量%的沸点(bp)低于150℃的成分,并且满足以下关系式1。
[0044]
[关系式1]
[0045]
0.85《b/a《1.15
[0046]
在关系式1中,a是相对于所述废油馏分的总重量的bp为150℃以上的成分的重量%,b是相对于所述去除氯的油馏分的总重量的bp为150℃以上的成分的重量%。
[0047]
在本发明中,为了对含有高含量cl的废油馏分应用精炼工艺来实现高附加值(燃
料、化学转化),可以提供一种使用固体酸物质减少含有高含量cl的废油馏分中的cl的技术。
[0048]
所述去除废油馏分中的氯的方法中,首先a)制备含氯废油馏分和固体酸物质的混合物。
[0049]
所述废油馏分可以包含废塑料热解油、生物质热解油、再生润滑油、含有高含量氯的原油或它们的混合物。在通过废塑料热解油等废料的裂化、热解反应形成的废油馏分中包含来自废料的大量的杂质,因此使用该废油馏分时会存在排放大气污染物质的可能性,特别是存在cl成分在高温氧化过程中转化为hcl并排放的问题,因此有必要对废油馏分进行预处理以去除杂质。
[0050]
所述废油馏分中的氯可以是无机(inorganic)cl、有机(organic)cl或它们的组合,废油馏分中的氯的含量可以为10ppm以上、20ppm以上。另外,废油馏分中的氯含量的上限不受特别限制,但是例如可以为600ppm以下,优选可以为500ppm以下。需要一种减少废油馏分中的cl的处理技术,该技术中通过处理所述含有高含量cl的废油馏分而将cl含量减少至可以引入到精炼工艺中的水平的cl含量(数ppm的cl)。
[0051]
另外,所述废油馏分中的杂质可能会包含使用燃料时会存在排放so
x
、no
x
等废气污染物质的可能性的n、s和o以及作为对精炼工艺催化活性产生不利影响的金属成分的fe、na、ca和al等。具体地,就n、s和o而言,相对于废油馏分的总重量,n含量可以为100wppm以上或500-8000wppm,s含量可以为10wppm以上或20-1000wppm,o含量可以为2000wppm以上或3000wppm至3重量%,就fe、na、ca和al而言,相对于废油馏分的总重量,fe含量可以为1wppm以上或1-10wppm,na含量可以为1wppm以上或1-10wppm,ca含量可以为0.1wppm以上或0.1-5wppm,al含量可以为0.1wppm以上或0.1-5wppm。
[0052]
相对于总重量,所述废油馏分包含5-50的重量%的bp低于150℃的成分,例如可以包含5-45重量%、5-40重量%、5-35重量%、5-30重量%、5-25重量%、5-20重量%或5-15重量%的bp低于150℃的成分。此外,可以包含10-50重量%、15-50重量%、20-50重量%、25-50重量%、30-50重量%、35-50重量%或40-50的重量%的bp低于150℃的成分。即使本发明的废油馏分中的轻油馏分的含量高,可以在实质上没有油馏分性状变化的情况下去除氯,从而防止低聚引起的产品性状变差和过度的裂化引起的产品损耗。
[0053]
此外,相对于总重量,所述废油馏分可以包含10-35重量%的bp为150-265℃的成分,例如可以包含10-30重量%、10-29重量%、11-28重量%、12-27重量%、13-26重量%、14-26重量%或15-25重量%的bp为150-265℃的成分。
[0054]
此外,相对于总重量,所述废油馏分可以包含10-35重量%的bp为265-340℃的成分,例如可以包含10-30重量%、10-29重量%、11-28重量%、12-27重量%、13-26重量%、14-26重量%或15-25重量%的bp为265-340℃的成分。
[0055]
此外,相对于总重量,所述废油馏分可以包含20-65重量%的bp超过340℃的成分,例如可以包含25-60重量%、25-55重量%、25-50重量%、30-50重量%、32-48重量%、35-45重量%的bp超过340℃的成分。
[0056]
此外,相对于总重量,所述废油馏分可以包含30-70重量%的烯烃,优选可以包含40-60重量%的烯烃。如下所述,通过利用本发明的固体酸物质在高温操作工艺条件下去除热解油中的cl,分析出由于发生裂化反应,平均分子量小幅降低的现象。由于在裂化过程中
产生烯烃(olefin),特别是形成高反应性的低碳烯烃(light olefin),与cl结合转化为有机cl,从而与固体酸结合或以气体排放到外部,或者由于在裂化过程中c-cl键断裂,可以提高去除cl的效果,但存在产品损耗和产品性状变差的问题,因此过度的裂化反应是不优选的。
[0057]
所述固体酸物质包含布朗斯台德酸、路易斯酸或它们的混合物,具体是存在布朗斯台德酸(bronsted acid)位点或路易斯酸位点(lewis acid site)的固体物质,并且所述固体酸物质可以为沸石、粘土、磷酸硅铝(sapo)、磷酸铝(alpo)、金属有机框架物(mof)、二氧化硅-氧化铝或它们的混合物。
[0058]
所述固体酸物质是具有可以提供h
(布朗斯台德酸)或接受非共用电子对的(路易斯酸)位点的固体物质,在酸性位点(acid site)可以根据能量引发裂化、烷基化(alkylation)和中和(neutralization)等各种反应。在本发明中,在特定工艺条件下使所述固体酸物质活化,从而可以进行将cl转化为hcl的催化转化反应。
[0059]
作为所述固体酸物质,可以直接使用在石油化工工艺中使用后废弃的废沸石、废粘土等,或者可以经过用于进一步改善活性的简单的处理来使用。
[0060]
例如,在将渣油转化为轻馏分/中间馏分(light/middle distillate)的rfcc工艺中使用流化床催化剂,为了保持一定的rfcc工艺的整体活性,每天将一定量的操作中的催化剂更换为新鲜(fresh)催化剂,此时将更换的催化剂命名为rfcc平衡催化剂(equilibrium cat.,e-cat),并全部处理为废弃物。可以将rfcc平衡催化剂用作本发明的固体酸物质,并且所述rfcc平衡催化剂可以由30-50重量%的沸石、40-60重量%的粘土和0-30重量%的其它物质(铝胶(alumina gel)、硅胶(silica gel)、功能材料(functional material)等)组成。将这种rfcc平衡催化剂用作用于减少高含量cl废油馏分的cl的固体酸物质,从而与新鲜催化剂相比,裂化活性差异少,并且在环境保护和通过再利用降低成本方面具有优点。
[0061]
为了将所述废沸石、废粘土等用作本发明的工艺的固体酸物质,可能需要简单的处理,如果诸如焦炭(coke)、油(oil)等的物质物理地遮挡固体酸物质的活性位点时,还可以将其去除并使用。为了去除焦炭,可以进行空气燃烧(air burning),或者为了去除油,可以用溶剂(solvent)处理。根据需要,金属成分影响固体酸物质的活性位点而使其失活时,可以应用通过用弱酸或稀释的过氧化氢进行中温处理以去除金属成分的德梅特过程(demet process)。
[0062]
所述固体酸物质还可以包含载体或粘合剂,所述载体包含碳、碱土金属氧化物、碱金属氧化物、氧化铝、二氧化硅、二氧化硅-氧化铝、氧化锆、二氧化钛、碳化硅、氧化铌、磷酸铝或它们的混合物。
[0063]
在所述步骤a)中,相对于所述混合物的总重量,固体酸物质的含量可以为5-10重量%,优选可以为7-10重量%,更优选可以为8-10重量%。在上述范围内,随着增加固体酸物质的引入量,可以提高去除cl的效果,并且当固体酸物质的含量为10重量%以下时,可以抑制油馏分中的裂化反应,因此优选。
[0064]
b)在制备所述废油馏分和固体酸物质的混合物后,在惰性气体气氛的1巴以上且100巴以下的压力下,使所述混合物反应以去除氯。
[0065]
预计从包含高含量氯的油馏分中去除氯的反应主要有两种方向,一种方向是烃结
构内的氯通过固体酸催化剂的活性位点引起的反应转化为hcl,然后以hcl或转化为一部分有机cl并排放,或者另一种方向是直接结合在固体酸物质的活性位点而被去除的反应。在加氢处理(hdt)工艺中通过供给(feeding)h2来去除cl的现有技术的情况下,废油馏分发生裂化,从而易于以有机cl形式去除。特别地,气体的产生增加,因此产品损耗大,并且可能会增加废油馏分中包含的烯烃成分的含量,在这一方面不优选。本发明的去除cl的反应中也可能引发裂化反应。但是,本发明的特征在于,与530℃以上的普通裂化条件相比,在超过280℃且低于380℃的低温下进行反应,并且应用脱铝沸石(dealuminated zeolite)为主要成分的作为弱酸位点物质的平衡催化剂。作为其结果,不仅可以抑制裂化反应本身,而且相比于转化为诸如气体的小单位分子,选择性地形成轻度裂化(mild cracking)引起的石脑油(naphtha)/煤油(kero)水平的中度裂化,从而可以防止上述问题。
[0066]
所述反应条件可以是惰性气体气氛的1巴以上且100巴以下的压力和超过280℃且低于380℃的温度条件。具体地,就所述工艺条件而言,可以在n2的1-100巴、n2的1-60巴或n2的1-40巴的压力条件下进行。在小于1巴的低真空或高真空条件下进行反应时,发生催化热解反应,因此热解油的粘度和分子量减小,并且油馏分产品的组成发生变化。特别地,cl与烯烃结合形成被去除的有机cl,因此发生产品的损耗。另一方面,当压力超过100巴时,难以操作反应器,并且工艺成本增加,因此不优选。
[0067]
工艺条件并不需要必须在n2等的惰性状态(inert condition)下进行,但惰性状态下的减少cl的操作在操作稳定性和经济性方面是有利的。在空气(air)条件下也显示出相似的减少cl的性能,但在超过280℃的高温操作条件下发生泄露(leak)时,发生火灾的可能性高,并且在h2条件下虽然cl减少效率提高,但与n2下的操作相比,存在使用h2所引起的经济性降低的问题。
[0068]
所述工艺条件具体可以为超过280℃且低于380℃的温度、290-360℃的温度,优选可以在290-340℃的温度条件下进行,最优选可以在295-335℃的温度条件下进行。在上述温度范围内,随着温度增加,减少cl的效果提高,但为了最小化由于裂化反应的增加引起的废油馏分的气体类转化而导致的液体(liquid)收率减小的问题,需要协调催化剂含量和反应温度/时间等。但是,这是快速处理含有高含量cl的废油馏分的合适的处理方法。并且,在上述数值范围内,随着反应温度上升,n、s和金属杂质的去除率也会提高,因此可以期待用于引入到精炼工艺中的脱硫(sweetening)效果。
[0069]
另外,所述步骤b)的反应可以在固定床(fixed bed)催化反应器或间歇式(batch)反应器中进行,但本发明并不限定于此。
[0070]
可以使用流化床反应器制备再生油馏分,但为了去除废油馏分中的cl,催化剂和油馏分的接触时间要长,但与催化剂和油馏分之间的接触时间无限长的间歇式反应器相比,接触时间非常短至数秒以下的流化床反应器具有cl等杂质的减少效率低的缺点。
[0071]
与流化床反应器相比,固定床反应器和连续式反应器在催化剂接触时间方面也有利,并且与间歇式反应器相比,在确保易操作性和安全性方面有利,但存在对于去除cl的反应的长期稳定性低并且cl减少效率低的缺点。
[0072]
例如,在间歇式反应器中进行cl减少反应时,可以以30-2000rpm,优选以200-1000rpm,更优选以300-700rpm和/或以0.1-48小时或0.5-24小时,优选以1-12小时或2-12小时,更优选以3-5小时的反应时间进行搅拌操作。
[0073]
此外,在固定床催化反应器中进行时,可以以0.1-10/小时(hr-1
),优选以0.3-5/小时,更优选以1-3/小时的液时空速(lhsv)和/或以50-2000,优选以200-1000,更优选以350-700的气油比(gas over oil ratio,gor)进行操作。
[0074]
c)接着,分离所述去除氯的油馏分和固体酸物质的混合物以回收去除氯的油馏分。
[0075]
所述混合物的分离应用公知的过滤方法即可,并且本发明并不限定于此。
[0076]
还可以进行再生所述分离的废固体酸物质的步骤,例如,可以将使用过的固体酸物质放入烧成炉中,并且在空气气氛的400-700℃下,优选在500-600℃的温度下热处理2-4小时,但本发明并不限定于此。
[0077]
d)接着,还可以进行将所述步骤a)、步骤b)和步骤c)至少重复1次以上的步骤。通过重复处理可以限制后续的精炼工艺中被允许的严格标准的cl含量(1wppm水平),并且通过抑制过度的裂化反应本身来保持废油馏分组分的平均分子量和/或粘度,从而可以防止反应异常、产品性状变差和产品损耗。
[0078]
本发明的一个具体实施方案的所述去除氯的油馏分的特征在于,满足以下关系式1。
[0079]
[关系式1]
[0080]
0.85《b/a《1.15
[0081]
关系式1的特征在于,a是相对于所述废油馏分的总重量的bp为150℃以上的成分的重量%,b是相对于所述去除氯的油馏分的总重量的bp为150℃以上的成分的重量%。
[0082]
具体地,所述b/a例如可以为0.9-1.1或0.95-1.05。此外,所述b/a例如可以为0.85-1.15、0.85-1.1或0.85-1.05。此外,所述b/a例如可以为0.90-1.15或0.95-1.15。
[0083]
所述去除氯的油馏分的氯含量可以小于10ppm,具体可以为8ppm以下、6ppm以下,优选可以为1-5ppm或1-4ppm。去除所述废油馏分中的cl时,抑制裂化反应,并且引发轻度裂化反应而不是过度的裂化反应,因此通过所形成的烯烃与因c-cl链断裂而产生的cl的结合产生的有机cl可以结合在固体酸物质的酸性位点而被去除,或者可以以气体排放。此外,还可以通过转化为hcl而以hcl形式排放到外部。
[0084]
相对于总重量,所述去除氯的油馏分包含5-60重量%的bp低于150℃的成分,例如可以包含5-55重量%、5-50重量%、5-45重量%、5-40重量%、5-35重量%、5-30重量%、5-25重量%、5-20重量%或5-15重量%的bp低于150℃的成分。此外,例如可以包含10-60重量%、15-60重量%、20-60重量%、25-60重量%、30-60重量%、35-60重量%、40-60重量%、45-60重量%或50-60重量%的bp低于150℃的成分。在本发明中,即使所述废油馏分的轻油馏分的含量高,可以在实质上没有油馏分性状变化的情况下去除氯,因此去除氯的油馏分防止低聚引起的产品性状变差和过度的裂化引起的产品损耗。
[0085]
此外,相对于总重量,所述去除氯的油馏分可以包含10-45重量%的bp为150-265℃的成分,例如可以包含10-40重量%或10-35重量%的bp为150-265℃的成分。
[0086]
此外,相对于总重量,所述去除氯的油馏分可以包含10-35重量%的bp为265-340℃的成分,例如可以包含10-30重量%、10-29重量%、11-28重量%、12-27重量%、13-26重量%、14-26重量%或15-25重量%的bp为265-340℃的成分。
[0087]
此外,相对于总重量,所述去除氯的油馏分可以包含20-60重量%的bp超过340℃
的成分,例如可以包含20-55重量%、20-50重量%、20-45重量%或25-40重量%的bp超过340℃的成分。
[0088]
本发明的一个具体实施方案中,所述去除氯的油馏分中的氯与所述废油馏分中的氯的重量比可以为0.01-0.5,例如可以为0.01-0.4、0.01-0.3或0.01-0.2,优选可以为0.01-0.1,更优选可以为0.01-0.09、0.01-0.08、0.01-0.07、0.01-0.06或0.01-0.05。
[0089]
另外,一个具体实施方案的去除废油馏分中的氯的方法表现出除了去除所述废油馏分中含有的氯之外还去除fe、na、ca和al等杂质的以往不可预测的效果。例如,相对于所述去除氯的油馏分的总重量,fe含量可以小于10ppm,优选可以为7ppm以下或5ppm以下,更优选可以为3ppm以下,na含量可以小于10ppm,优选可以为7ppm以下或5ppm以下,更优选可以为3ppm以下,ca含量可以小于5ppm,优选可以为3ppm以下或1ppm以下,更优选可以为0.5ppm以下或0.3ppm以下,al含量可以小于3ppm,优选可以为1ppm以下或0.5ppm以下,更优选可以为0.3ppm以下或0.1ppm以下。
[0090]
此外,所述去除氯的油馏分中的fe与所述废油馏分中的fe的重量比可以为0.1-0.7,例如可以为0.1-0.6,优选可以为0.5以下,所述去除氯的油馏分中的na与所述废油馏分中的na的重量比可以为0.1-0.7,例如可以为0.1-0.5,优选可以为0.45以下,所述去除氯的油馏分中的ca与所述废油馏分中的ca的重量比可以为0.1-0.8,例如可以为0.2-0.7,优选可以为0.6以下,所述去除氯的油馏分中的al与所述废油馏分中的al的重量比可以为0.1-0.7,例如可以为0.1-0.5,优选可以为0.4以下。
[0091]
另外,一个具体实施方案的去除废油馏分中的氯的方法表现出除了去除所述废油馏分中含有的氯之外还去除n、s和o等杂质的以往不可预测的效果。例如,相对于所述去除氯的油馏分中的总重量,n含量可以小于300ppm,优选可以为250ppm以下或200ppm以下,更优选可以为170ppm以下,s含量可以小于20ppm,优选可以为19ppm以下或18ppm以下,更优选可以为17ppm以下,o含量可以小于0.2重量%,优选可以为0.15重量%以下或0.1重量%以下,更优选可以小于0.1重量%。
[0092]
此外,所述去除氯的油馏分中的n与所述废油馏分中的n的重量比可以为0.1-0.7,例如可以为0.1-0.6,优选可以为0.5以下,所述去除氯的油馏分中的s与所述废油馏分中的s的重量比可以小于1,例如可以为0.1-0.9,优选可以为0.8以下,所述去除氯的油馏分中的o与所述废油馏分中的o的重量比可以小于1,例如可以为0.1-0.9,优选可以为0.8以下、0.7以下、0.6以下或0.5以下。
[0093]
以下,记载本发明的优选的实施例和比较例。但是,以下实施例仅仅是本发明的优选的一个实施例,本发明并不限定于以下实施例。
[0094]
实施例1.含有cl的废油馏分(塑料热解油)的组成的分析
[0095]
回收通过塑料废弃物的热解转化的废油馏分(塑料热解油),并用作cl去除反应的原料。为了确认通过反应去除杂质的效果和分子量是否变化,进行以下分析。为了确认塑料热解油中的分子量分布,进行gc-simdis分析(ht 750)。就杂质而言,进行对cl、s、n、o、fe、ca、na、al、si、p等的分析,为此进行icp、tns、ea-o、xrf分析。此外,为了分析烯烃含量,进行gc-msd分析。通过分析结果,下表1和表2中示出用作原料的热解油的组成和杂质特性。
[0096]
[表1]
[0097]
简称(cut name)预计的碳范围(carbon range)沸点(℃)收率(重量%)
重石脑油(h-naph.)-c8《1508.1煤油(kero)c9-c17150-26524.4lgoc18-c26265-34022.7lgo-2/uco-1c20-340《44.8总和(sum)
‑‑
100
[0098]
[表2]
[0099]
mg/kgclnso热解油b67348200.2
[0100]
实施例2.使用rfcc平衡催化剂减少cl的反应特性的分析
[0101]
实施例2-1.温度影响的分析
[0102]
根据固体酸催化剂的减少cl的特性的确认,为了由此得出最佳减少cl的操作条件,确认了不同反应变量的cl减少趋势。
[0103]
所述实施例1的热解油也是固相,因此在70℃的烘箱(oven)中保持3小时以上后转化为液相并使用。
[0104]
用于减少包含cl的杂质的固体酸物质是使用rfcc平衡催化剂。如下表3和表4所示,确认了所使用的rfcc平衡催化剂的物理特性。
[0105]
[表3]
[0106][0107]
(所述表3中,tsa是总比表面积,zsa是沸石比表面积,msa是介孔比表面积,z/m是沸石比表面积(zsa)与介孔比表面积(msa)之比,pv是孔隙体积,apd是平均孔隙尺寸。)
[0108]
[表4]
[0109]
重量%nanivfemgpla2o3ceo2tio2sio2al2o3rfcc平衡催化剂0.130.531.210.650.070.560.690.100.784053
[0110]
使用的rfcc平衡催化剂是总比表面积为112m2/g、孔隙体积为0.20毫升/g、平均颗粒尺寸为79μm的催化剂。
[0111]
将120g的所述液相的热解油和12g的rfcc平衡催化剂依次引入到反应器内部体积为300毫升(cc)的高压釜(autoclave)中。连接反应器,并进行n2吹扫(purge)。之后,在n2的1巴条件下以500rpm搅拌,并将反应器温度以1℃/分钟的速度升温至目标温度。保持反应3小时后终止。
[0112]
反应终止后,将反应器温度保持在80℃,然后解除与高压釜的结合,并且测量包含热解油处理油和平衡催化剂的混合物的反应器的重量,从而计算回收率。
[0113]
通过滤纸(filter paper)分离反应器内的热解油处理油和平衡催化剂的混合物。分析了回收的热解油处理油的组成变化和杂质含量变化,并将其结果示于下表5至表7和图3至图5中。
[0114]
[表5]
[0115][0116][0117]
[表6]
[0118]
反应温度(℃)cl,wppmcl减少率(%)300494.03330395.52350297.01
[0119]
随着反应温度上升,回收率从96.6%持续降低至86.5%。另一方面,cl减少率(每单位平衡催化剂的cl减少量)从94.03%增加至97.01%,从而确认了随着反应温度上升,去除cl的性能得到改善。
[0120]
不仅是cl含量,随着反应温度上升,确认了n、s的去除率也提高。n的情况下,确认了随着反应温度上升,去除率急剧增加,但s的情况下,虽然随着温度上升,减少率也增加,但没有观察到如同cl、n的急剧的减少效果。
[0121]
[表7]
[0122][0123]
参考表7和图5时,在300℃的反应温度下,与供给相比,组成变化并不大,但随着温度上升,由于裂化反应,vgo、lgo的比例降低,石脑油、煤油的比例增加,特别是在350℃下,vgo含量仅为20%的水平,含量非常低,煤油以下的含量为57.6%,确认了轻馏分(light fraction)比例大幅增加的现象,从而确认了可能存在操作稳定性和运输时的危险可能性。
[0124]
实施例2-2.时间影响性分析
[0125]
为了确认固体酸催化剂的减少cl的特性,在实施例2-1中得出的组成差异小且cl减少效率高的330℃的操作条件下,确认了根据时间的cl减少趋势。催化剂量、搅拌速度等其它反应变量和分析方法是在与实施例2-1相同的条件下进行。并且,分析结果示于下表8至表10和图6至图10中。
[0126]
[表8]
[0127][0128]
[表9]
[0129]
时间(小时)cl,wppmcl减少率(%)0.081774.60.51085.11691.03395.551.797.5
[0130]
参考表8至表9和图6至图9时,确认了包含cl在内的s、n、o随着时间而减少。随着时间的流逝,由于裂化反应,回收率也逐渐减小。对于包含67wppm的cl含量的原料,确认了可以通过增加处理时间来提高cl减少效率,并且仅处理5小时就可以减少全部的97.5重量%的cl。
[0131]
如同cl,n在操作时间初期被去除50%以上,并且确认了随着时间的流逝,减少率增加,但n的减少率的增加率逐渐降低。另一方面,s的情况下,与n、cl相比,减少活性也非常低,但随着时间的流逝,确认了减少一定程度的现象。
[0132]
[表10]
[0133][0134]
参考表10和图10时,随着反应时间的流逝,确认了石脑油、煤油的比例增加,lgo、vgo减少的倾向。由此,可以推导出随着裂化反应性增加,包括cl减少率在内的杂质减少率
增加。
[0135]
实施例2-3.催化剂引入量的分析
[0136]
为了确认固体酸催化剂的减少cl的特性,在实施例2-1和实施例2-2中得出的与原料相比组成差异小且cl减少效率高的330℃、3小时的操作条件下,确认了根据催化剂引入量的cl减少趋势。搅拌速度等其它反应变量和分析方法是在与实施例2-1相同的条件下进行。分析结果如下表11至表13和图11至图15所示。
[0137]
[表11]
[0138][0139]
参考表11和图11至图14时,确认了将催化剂引入量逐渐增加至10重量%时,随着催化剂量的增加,cl减少率上升。此外,确认了n、s和o的含量也一同被去除。n和s显示出与催化剂引入量的增加量成比例地被去除的倾向,n的情况下,如同cl,确认了大幅减少了全部的65%的水平。另一方面,确认了s的减少率为30%的水平,与cl、n相比,减少率相对低,并且随着催化剂量的增加,s的减少率的增加幅度也小。
[0140]
[表12]
[0141][0142]
参考表12和图15时,确认了随着将催化剂引入量增加至10重量%,石脑油的比例逐渐增加,vgo的比例降低。判断在发生裂化反应的操作条件下,随着催化剂引入量的增加,裂化副反应也增加,从而发生组成的变化。
[0143]
[表13]
[0144]
mg/kgfenacaal热解油b2.95.70.50.3实施例2-1(330℃)1.22.50.30.1
[0145]
为了确认除了去除cl、n、s、o等杂质之外,是否还可以去除fe、na、ca等金属杂质,对在组成没有变化且cl减少效率高的实施例2-1的330℃的操作条件下回收的样品进行金属杂质分析。确认了fe、na、ca、al均同时被去除60%以上。
[0146]
综合上述实施例的结果,确认了通过用本发明的固体酸物质进行处理,可以在馏分的组成几乎没有变化的情况下选择性地去除杂质。
[0147]
以上,对本发明的实施方案进行了说明,但本发明并不限定于上述实施方案,而是可以通过彼此不同的各种实施方案进行制备,本发明所属技术领域的技术人员可以理解在不改变本发明的技术思想或必要特征的情况下可以通过其它具体的实施方案实施。因此,应理解上述实施方案在所有方面是示例性,而不是限定性。
再多了解一些
本文用于企业家、创业者技术爱好者查询,结果仅供参考。