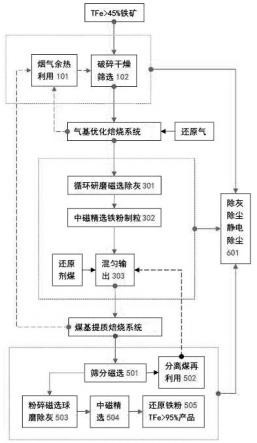
1.本发明属矿物资源节能综合利用直接还原技术领域,涉及矿物优选方法;具体涉及一种气基优化煤基还原磁选低品位铁矿的方法。
背景技术:
2.直接还原铁是冶炼优质钢最佳的、不可或缺的残留元素稀释剂;现有直接还原铁-磁选工艺,一般要求还原铁原材料含铁fe》68.5%,自然界原料奇缺,自然原料难以满足规模生产直接还原铁原料需求;其次,现有气基竖炉还原工艺虽然能耗355千克/吨<高炉炼铁能耗的392千克/吨,但是,由于烟气对还原气体稀释没有构成充分直接还原氛围,而是提高温度还原,造成炉内结块、下料不畅通、热工难控、运行不稳定,已成现有气基竖炉还原工艺的致命弱点,致使气基竖炉工艺工业化生产应用屡屡受挫;在焙烧工艺之后的分选工艺中,磨细电耗高、杂质难分离,常出现杂质分离不彻底,导致最后产品的铁含量不高。
技术实现要素:
3.本发明克服了现有技术的不足,提出一种气基优化煤基还原磁选低品位铁矿的方法。以用低品位铁矿生产铁产品,并提高产品的铁含量。
4.为了达到上述目的,本发明是通过如下技术方案实现的。
5.气基优化煤基还原磁选低品位铁矿的方法,其特征在于,包括以下步骤:1)铁矿处理:将tfe》45%的铁矿经过破碎干燥筛选后得到粒径3~30mm的干燥铁矿颗粒物料。
6.2)铁矿颗粒物料进入气基直接还原焙烧窑进行一次还原焙烧:所述焙烧窑中的焙烧还原段烟道内的焙烧温度为900~960℃开始下料,下料速度为v1,并通入还原气;加热升温速度≤2℃/分钟,还原段烟道内的焙烧温度为960~1100℃时,下料速度为v2,v2为v1的4~6倍;焙烧结束后冷却得到还原焙烧料。
7.3)循环研磨优化制粒:将还原焙烧料经过循环研磨磁选抽灰除尘装置得到》300目还原物料;再经过中磁精选优化铁粉制粒装置得到粒径10~20mm优化制粒;将优化制粒与还原煤混合制备得到优化混料。
8.4)将得到的优化混料送入煤基直接还原焙烧窑进行二次还原焙烧:煤基直接还原焙烧窑的焙烧还原段烟道内的焙烧温度为900~960℃开始下料,下料速度为v3;还原段烟道内的焙烧温度为960~1140℃时,下料速度为v4,v4为v3的6~8倍;焙烧结束后冷却得到二次还原焙烧料。
9.5)将二次还原焙烧料经过筛分磁选机去除还原剂煤,经粉碎磁选球磨除灰装置,得到》300目二次还原物料;所述》300目二次还原物料经中磁精选,得到》300目还原铁粉产品。
10.优选的,所述还原气为煤气或h
2 、co。
11.优选的,所述铁矿处理、循环研磨优化制粒、以及中磁精选均连接有除灰除尘装
置。
12.更优的,所述除灰除尘装置为袋式除灰静电除尘装置。
13.优选的,所述一次还原焙烧和二次还原焙烧的烟气余热通过烟气余热利用装置为铁矿干燥处理提供热量。
14.优选的,所述的煤基直接还原焙烧窑设置有蛇形烟道,蛇形烟道自上而下依次为预热段、加热段、还原段和保温还原连接段。
15.更优的,所述的气基直接还原焙烧窑设置有还原段还原后气体溢流口;还原段还原后气体溢流口与蛇形烟道相连通;所述还原后气体从溢流口溢入蛇形烟道,过剩还原气与蛇形烟道内过剩空气充分燃烧。
16.本发明相对于现有技术所产生的有益效果为:本发明自优化铁矿,优化tfe》45%的铁矿,优化铁精粉品位tfe》76%,解决了还原铁原材料要求tfe》68.5%的问题;气基优化焙烧还原气体中有害杂质极少,有害物进入产品风险降低、污染减少、还原成本降低,优化还原效率明显提高;tfe》76%优化制粒再经过煤基还原焙烧-磁选,得到的还原铁粉品位tfe》95%,解决了现有煤基还原-磁选工艺处理低品位铁矿能耗高效率低、热工难控、产品质量不稳定的问题。
17.与现有国内外煤基还原-磁选工艺相比,本发明生产还原铁工艺,工艺流程简短灵活实用节能高效、不粘结不结块、铁回收率高处理量大、产品质量稳定、相对投资小见效快,可边生产边发展,最后形成集约化大规模生产等优点。
附图说明
18.图1为本发明气基优化焙烧系统采用的气基直接还原焙烧窑的主剖视结构示意图。
19.图2为图1中a-a面剖视示意图。
20.图3为本发明煤基提质焙烧系统采用的煤基直接还原焙烧窑的主剖视结构示意图。
21.图4为图3中a-a面剖视示意图。
22.图5是本发明的气基优化煤基还原磁选低品位铁矿的方法的流程图。
23.101-烟气余热利用装置、102-破碎干燥筛选装置;201-窑体、202-预热料池、203-预热料管、204-落料通道、205-焙烧预热段、206-焙烧加热段、 207-还原段、208-保温还原连接段、209-风冷管、210-导料叶轮、211-导料平台、212-料仓、213-输出装置、214-保温密封缝隙、215-送风预热器、216-冷却热风收集器、217-支撑梁、218-垫环、219-支撑柱、220-布料机、221-蛇形烟道、222-温度监测装置、223-观火孔、224-燃烧室、225-还原段还原后气体溢流口、226-还原气体预热还原装置。
24.301-循环研磨磁选除灰装置、302-中磁精选铁粉制粒装置、303-混匀输出装置;501-筛分磁选机、502-煤再利用装置、503-粉碎磁选球磨除灰装置、504-中磁精选装置、505-还原铁粉仓;601-袋式除灰静电除尘装置。
具体实施方式
25.为了使本发明所要解决的技术问题、技术方案及有益效果更加清楚明白,结合实施例和附图,对本发明进行进一步详细说明。应当理解,此处所描述的具体实施例仅仅用以解释本发明,并不用于限定本发明。下面结合实施例和附图详细说明本发明的技术方案,但保护范围不被此限制。
26.如图1-5所示,为气基优化煤基还原磁选低品位铁矿的方法流程图及装置结构示意图,主要包括6个部分:铁矿处理烟气余热利用系统、气基优化焙烧系统、循环研磨优化制粒系统、煤基还原焙烧系统、煤分离粉碎球磨精选系统、除灰除尘系统。
27.气煤双还原磁选低品位铁矿生产还原铁粉的方法为:s1.烟气余热利用铁矿处理:烟气余热利用装置101将气基优化焙烧和煤基还原焙烧产生的烟气收集对原料加热干燥;将铁矿经过破碎干燥筛选102处理,得到粒径φ3~30mm干燥铁矿颗粒物料;s2.气基优化焙烧:所述气基优化焙烧系统为气基直接还原焙烧窑,使用过程中,将粒径φ3~30mm铁矿颗粒物料装满煤气优化焙烧窑,在预热料池202中平铺堆积厚度为200~300mm;启动燃烧室224的火咀,加热升温速度≤2℃/分钟,待还原段207烟气温度达900~960℃时,启动导料叶轮210开始下料,下料速度为v1;同时开启还原气预热还原装置226的气阀开始向落料通道204通入还原气;待还原段207烟气温度升至960~1100℃时,下料速度为v2;v2为v1的4~6倍;铁矿物料经过优化焙烧后落入风冷管209冷却至45~55℃,在导料叶轮210控制下穿过导料平台211落入焙烧料仓212,得到优化还原焙烧料。
28.s3.循环研磨优化制粒:所述优化还原焙烧料经过循环研磨磁选除灰装置301,得到》300目还原物料;所述》300目还原物料经过中磁精选铁粉制粒装置302,得到粒径10~20mm优化制粒;所述优化制粒与还原煤按质量百分比8%和分离煤再利用装置502处理得到的φ2~8mm分离煤粒按质量百分比16%,再经混匀输出装置303得到优化混料。
29.s4.煤基还原焙烧:所述煤基还原焙烧系统为煤基直接还原焙烧窑,使用过程中,将优化混料装满煤基还原焙烧窑;在预热料池202中平铺堆积厚度为300~400mm;启动燃烧室224的火咀,待还原段207烟气温度为900~960℃时,启动导料叶轮210开始下料,下料速度为v3,优化混料在导料叶轮210控制下,沿预热料池202、预热料管203和落料通道204缓慢下行;待还原段207烟气温度达960~1140℃时,下料速度为v4;v4为v3的6~8倍;优化混料还原焙烧后落入风冷管209冷却至45~55℃,在导料叶轮210控制下穿过导料平台211落入焙烧料仓212,得到二次还原焙烧料。
30.s5.煤分离粉碎球磨精选:所述二次还原焙烧料经过筛分磁选机501将煤分离落入煤再利用装置502处理,得到粒径φ2~8mm再利用煤粒返回混匀输出装置303循环利用,同时得到二次还原物料;所述二次还原物料经过粉碎磁选球磨抽灰除尘装置503,得到》300目二次还原物料;所述》300目二次还原物料经中磁精选504,得到》300目还原铁粉产品。
31.s6.除灰除尘:所述袋式除灰静电除尘装置601分别与烟气余热利用铁矿处理系统、循环研磨中磁精选铁粉制粒系统、煤分离粉碎球磨精选系统相连接。
32.煤基直接还原焙烧窑与气基直接还原焙烧窑201—224结构相同,不同之处为气基直接还原焙烧窑还设置有预热段还原后气体溢流口225和还原气体预热还原装置226。
33.具体的:
实施例1:某铁矿tfe45.73%。按以下步骤进行:
①
烟气余热利用铁矿处理:将tfe45.73%铁矿经过破碎干燥筛选处理,得到粒径φ3~30mm干燥铁矿颗粒物料。
34.②
气基优化焙烧:将铁矿颗粒物料装满气基优化焙烧试验窑,在预热料池平铺200~300mm;启动燃烧室火咀,加热升温≤2℃/分钟,待还原段烟气温度达900~960℃时,开启导料叶轮以1转/小时下料;同时开启还原气预热还原装置的气阀开始向落料通道通入还原煤气,煤气管路内气压高于标注气压600~1200pa;待还原段烟气温度升至960~1080℃时,下料速度调至4~6转/小时;铁矿物料优化焙烧后落入风冷管冷却至45~55℃落入料仓,得到优化还原焙烧料。
35.③
循环研磨优化制粒:所述优化还原焙烧料经过循环研磨磁选除灰装置,得到》300目还原物料;所述》300目还原物料经过中磁精选得到》300目tfe76.94%的优化铁精粉,各项指标化验合格后再制粒,得到粒径φ10~20mm优化制粒;所述优化制粒与还原煤按质量百分比8%和分离煤再利用装置处理得到的粒径φ2~8mm分离煤粒按质量百分比16%,再经过混匀输出装置303得到优化混料。
36.④
煤基还原焙烧:将优化混料装满煤基还原焙烧试验窑,在预热料池中平铺堆积厚度为300~400mm;启动燃烧室的火咀,待焙烧还原段烟气温度为900~960℃时,启动导料叶轮开始下料,下料速度为v3,优化混料在导料叶轮控制下,沿预热料池、预热料管和落料通道缓慢下行;待焙烧还原段烟气温度达960~1140℃时,下料速度为v4;v4为v3的6~8倍;优化混料还原焙烧后落入风冷管冷却至45~55℃,在导料叶轮控制下穿过导料平台落入焙烧料仓,得到二次还原焙烧料。
37.⑤
煤分离粉碎球磨精选:所述二次还原焙烧料经过筛分磁选机将煤分离落入煤再利用装置处理,得到粒径φ2~8mm再利用煤粒返回混匀输出装置循环利用,同时得到二次还原物料;所述二次还原物料经过粉碎磁选球磨抽灰除尘装置,得到》300目二次还原物料,再经中磁精选得到》300目tfe95.43%还原铁粉产品。
38.实施例2:某铁矿tfe48.32%。按以下步骤进行:
①
烟气余热利用铁矿处理:将tfe48.32%铁矿经过破碎干燥筛选处理,得到粒径φ3~30mm干燥铁矿颗粒物料。
39.②
气基优化焙烧:将铁矿颗粒物料装满气基优化焙烧试验窑,在预热料池平铺200~300mm;启动燃烧室火咀,加热升温≤2℃/分钟,待还原段烟气温度达900~960℃时,开启导料叶轮以1转/小时下料;同时开启还原气预热还原装置的气阀开始向落料通道通入还原煤气,煤气管路内气压高于标注气压600~1200pa;待还原段烟气温度升至960~1080℃时,下料速度调至4~6转/小时;铁矿物料优化焙烧后落入风冷管冷却至45~55℃落入料仓,得到优化还原焙烧料。
40.③
循环研磨优化制粒:所述优化还原焙烧料经过循环研磨磁选除灰装置,得到》300目还原物料;所述》300目还原物料经过中磁精选得到》300目tfe77.31%的优化铁精粉,各项指标化验合格后再制粒,得到粒径φ10~20mm优化制粒;所述优化制粒与还原煤按质量百分比8%和分离煤再利用装置处理得到的粒径φ2~8mm分离煤粒按质量百分比16%,再经过混匀输出装置303得到优化混料。
41.④
煤基还原焙烧:将优化混料装满煤基还原焙烧试验窑,在预热料池中平铺堆积
厚度为300~400mm;启动燃烧室的火咀,待焙烧还原段烟气温度为900~960℃时,启动导料叶轮开始下料,下料速度为v3,优化混料在导料叶轮控制下,沿预热料池、预热料管和落料通道缓慢下行;待焙烧还原段烟气温度达960~1140℃时,下料速度为v4;v4为v3的6~8倍;优化混料还原焙烧后落入风冷管冷却至45~55℃,在导料叶轮控制下穿过导料平台落入焙烧料仓,得到二次还原焙烧料。
42.⑤
煤分离粉碎球磨精选:所述二次还原焙烧料经过筛分磁选机将煤分离落入煤再利用装置处理,得到粒径φ2~8mm再利用煤粒返回混匀输出装置循环利用,同时得到二次还原物料;所述二次还原物料经过粉碎磁选球磨抽灰除尘装置,得到》300目二次还原物料,再经中磁精选得到》300目tfe96.18%还原铁粉产品。
43.关于本发明具体结构需要说明的是,本发明采用的各部件模块相互之间的连接关系是确定的、可实现的,除实施例中特殊说明的以外,其特定的连接关系可以带来相应的技术效果,并基于不依赖相应软件程序执行的前提下,解决本发明提出的技术问题,本发明中出现的部件、模块、具体元器件的型号、连接方式除具体说明的以外,均属于本领域技术人员在申请日前可以获取到的已公开专利、已公开的期刊论文、或公知常识等现有技术,无需赘述,使得本案提供的技术方案是清楚、完整、可实现的,并能根据该技术手段重现或获得相应的实体产品。
再多了解一些
本文用于企业家、创业者技术爱好者查询,结果仅供参考。