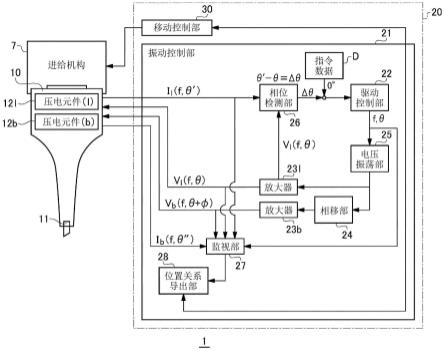
振动切削装置以及接触检测程序
1.本技术是申请日为2018年08月29日,申请号为201880055188.6,发明名称为“振动切削装置以及接触检测程序”的中国专利申请的分案申请。
2.本技术基于在2017年8月29日申请的日本发明专利申请2017-164699号,主张其优先权的利益,通过引用将该专利申请的全部内容并入本说明书中。
技术领域
3.本公开涉及一种在使刀具振动的同时切削被切削材料(工件)的振动切削装置。
背景技术:
4.近年来,要求对各种被切削材料实施精密的切削加工。专利文献1公开了一种具备使切削刀具的刀尖相对于被切削材料椭圆振动的振动装置的切削装置,该切削装置可以对铁系材料、脆性材料实施精密微细加工。
5.(现有技术文献)
6.(专利文献)
7.专利文献1:日本特开2008-221427号公报
技术实现要素:
8.(发明所要解决的问题)
9.在通过更换等将切削刀具重新安装于切削装置时,为了维持高的加工精度,需要准确地测定切削刀具的刀尖位置。因此,以往通过在切削装置上附加测定器来测定切削刀具的刀尖位置,但是成本变高,并且存在以下问题:如果切削装置的坐标原点与测定器的坐标原点的相对位置关系由于热变形等而发生变化,则难以准确地测定刀尖位置。
10.另外,作为另一种方法,利用了以下方法:用切削刀具加工一次被切削材料,根据加工后的被切削材料的形状测定的结果来修正刀尖位置。此时,也需要测定器来测定被切削材料的形状,因此不可否认成本会变高。
11.本公开是鉴于上述情况而完成的,其目的之一在于,提供一种无需附加测定器而确定刀具刀尖与被切削材料等的对象物的相对位置关系的技术、或者为了确定两者的相对位置关系而所需的技术、或者确定与设计上的切削环境的误差的技术。
12.(解决问题所采取的措施)
13.为了解决上述课题,本发明的一个实施方式的振动切削装置具备:振动装置,安装有切削刀具,并包括产生振动的致动器;移动控制部,对使振动装置相对于对象物相对移动的进给机构进行控制;以及振动控制部,对振动装置的致动器的振动进行控制。振动控制部获取表示振动的控制状况的状况值并根据状况值的变化来检测切削刀具与对象物的接触。对象物可以是被切削材料、安装有被切削材料的部件或者具有已知形状的物体。
14.本发明的另一个实施方式也是一种振动切削装置。该装置具备:振动装置,安装有切削刀具,并包括产生振动的致动器;以及控制部,对使振动装置相对于被切削材料或部件
相对移动的进给机构进行控制。控制部具有:对进给机构进行控制而使振动装置相对移动,而获取切削刀具与被切削材料或部件接触时的坐标值的功能。控制部根据切削刀具在与车削加工时的切削刀具的旋转角度位置不同的至少两个位置与基准面接触时的坐标值来确定切削刀具与被切削材料的旋转中心的相对位置关系,基准面与车削加工后的被切削材料或与被切削材料的旋转中心的相对位置关系是已知的。
15.本发明的另一个实施方式也是一种振动切削装置。该装置具备:振动装置,安装有切削刀具,并包括产生振动的致动器;以及控制部,对使振动装置相对于被切削材料或部件相对移动的进给机构进行控制。控制部具有:对进给机构进行控制而使振动装置相对移动,而获取切削刀具与被切削材料或部件接触时的坐标值的功能。控制部根据基准面上的接触位置的坐标值来确定切削刀具与被切削材料的安装面、被切削材料的进给运动方向、被切削材料的旋转中心中的至少一方的相对位置关系,其中,基准面与被切削材料的安装面、被切削材料的进给运动方向、被切削材料的旋转中心中的至少一方的相对位置关系是已知的。
16.本发明的另一个实施方式也是一种振动切削装置。该装置具备:振动装置,安装有切削刀具,并包括产生振动的致动器;以及控制部,对使振动装置相对于对象物相对移动的进给机构进行控制。控制部具有:对进给机构进行控制而使振动装置相对于具有已知形状的物体相对移动,而获取切削刀具的刀尖与物体的已知形状部分接触时的坐标值的功能。控制部根据切削刀具的刀尖在物体的已知形状部分的至少三个位置接触时的坐标值来确定与切削刀具的刀尖相关的信息。
17.本发明的另一个实施方式也是一种振动切削装置。该装置具备:振动装置,安装有切削刀具,并包括产生振动的致动器;以及控制部,对使振动装置相对于被切削材料相对移动的进给机构进行控制。控制部具有:对进给机构进行控制而使振动装置相对移动,而获取切削刀具与被切削材料接触时的坐标值的功能。控制部利用在切削加工时未利用的移动方向的进给机构的进给功能而使振动装置相对于切削加工后的被切削材料相对移动,根据切削刀具在至少两个位置接触时的坐标值,来确定切削刀具的安装误差、刀具刀尖的形状误差、切削刀具相对于被切削材料的相对移动方向的偏差中的至少一个。
18.需要说明的是,以上的构成要素的任意组合、将本公开的表现形式在方法、装置、系统、记录介质、计算机程序等之间进行变换后的实施方式,作为本公开的实施方式也是有效的。
19.(发明的效果)
20.根据本公开,能够提供一种确定刀具刀尖与对象物的相对位置关系的技术、或者为了确定两者的相对位置关系而所需的技术。
附图说明
21.图1是示出实施方式的振动切削装置的概略结构的图。
22.图2是示出振动切削装置的功能结构的图。
23.图3是示出椭圆振动的切削刀具切削被切削材料的情况的图。
24.图4是用于说明切削被切削材料的过程的图。
25.图5是示意性地示出在椭圆振动的切削刀具与被切削材料之间作用的力的图。
26.图6是用于说明对工件的切削实验的概要的图。
27.图7是示出相对于非接触时的挠曲振动方向的功率消耗变化量的时间变化的图。
28.图8是示出切削痕的最大切入深度和工件的横向位置的测定结果的图。
29.图9是示出挠曲振动方向的功率消耗变化量与切削痕的最大切入深度的关系的图。
30.图10是示出表示回归直线和其置信区间的直线的图。
31.图11是用于说明确定切削刀具与被切削材料旋转中心的相对位置关系的方法的图。
32.图12是示出a点坐标的导出方法的图。
33.图13是用于说明基准面的图。
34.图14是示出将振动装置以能够c轴旋转的方式安装的振动切削装置的一例的图。
35.图15是示出刀尖与基准块的已知形状部分接触的情况的图。
36.图16是示出刀尖与基准块的位置关系的图。
37.图17是示意性地示出与基准块的上表面接触时的切削刀具的倾斜状态的图。
38.图18是示出接触位置的高度变化的图。
39.图19是示出将振动装置以能够c轴旋转的方式安装的振动切削装置的另一例的图。
40.图20是示出刀尖与基准块的已知形状部分接触的情况的图。
41.图21是示出刀尖与基准块的位置关系的图。
42.图22是示出使基准块的已知形状的部分与刀尖接触的状态的图。
43.图23是示出对被切削材料进行加工的情况的图。
44.图24是用于说明导出刀具中心的安装误差的方法的图。
45.图25是用于说明确定刀具刀尖的形状误差的方法的图。
46.图26是用于说明确定被切削材料旋转轴与刀具直进轴的平行度的方法的图。
47.图27是用于说明确定被切削材料旋转轴与刀具直进轴的正交度的方法的图。
48.图28是用于说明推定刀具中心的安装误差的方法的图。
49.图29是用于说明推定刀具中心的安装误差的方法的图。
50.图30是用于说明推定刀具中心的安装误差的方法的图。
51.图31是用于说明导出b轴旋转中心的方法的图。
52.图32是概念性地示出扫描线加工中的切削进给方向和周期进给方向的图。
53.图33是用于说明推定刀具中心的安装误差的方法的图。
54.图34是用于说明推定刀具中心的安装误差的方法的图。
55.图35是示出测定刀尖形状误差的方法的图。
56.图36是示出由直线切削刃进行加工的情况的图。
57.图37是用于说明识别方法(identify method)的图。
58.图38是用于说明坐标变换的图。
59.图39是示出在加工面上接触了刀尖的状态的图。
具体实施方式
60.实施方式的振动切削装置具有如下功能:即使发生由切削负荷的变化、振动而引起的发热等的情况,也能够一边执行将振动装置的振动维持为大致恒定的振动控制,一边监视表示振动的控制状况的状况值。进行监视的振动控制状况值是振动所需的能量消耗量、进行跟踪的共振频率,振动切削装置对振动控制状况值进行监视而能够推测施加于振动装置的负荷等。实施方式的振动切削装置提出了以下技术:利用振动控制状况值的监视功能而检测刀具刀尖与被切削材料(或安装被切削材料的部件)的接触并确定接触位置,据此测定切削刀具的安装位置。
61.图1示出实施方式的振动切削装置1的概略结构。振动切削装置1是使切削刀具11的刀尖相对于被切削材料6椭圆振动而进行车削类型的加工的切削装置。实施方式的振动切削装置1是对圆筒状的被切削材料6进行车削而加工轧制用轧辊的轧辊车床,但也可以是车削类型以外的其他类型的切削装置。如下所述,本发明人使用刨床进行利用了控制状况值的监视功能的刀尖位置测定方法的验证实验,实施方式的振动切削装置1只要是使刀具刀尖椭圆振动而进行振动切削加工的切削装置即可。
62.振动切削装置1在床身5上具有可旋转地支承被切削材料6的主轴台2及尾座3、以及支承安装有切削刀具11的振动装置10的刀架4。另外,振动切削装置1至少具备使尾座3相对于主轴台2移动的进给机构(未图示)、以及使刀架4在x轴、y轴、z轴方向移动的进给机构7。在图1中,x轴方向是水平方向且与被切削材料6的轴方向正交的切入方向,y轴方向是作为铅直方向的切削方向,z轴方向是与被切削材料6的轴方向平行的进给方向。需要说明的是,在图1中,x轴、y轴、z轴的正负表示从切削刀具11侧观察的方向,但由于在切削刀具11与被切削材料6之间正负的方向是相对的,因此在本说明书中,并没有特别严格地定义各轴的正负方向,在提及正负方向时遵循各图所示的方向。在切削加工中,被切削材料6在设置在主轴台2的主轴2a的作用下旋转。
63.振动装置10安装有切削刀具11,并具备使切削刀具11的刀尖椭圆振动的振动件。振动件具备产生振动的致动器,致动器可以是压电元件。在实施方式中,致动器通过产生x轴方向的振动和y轴方向的振动,使切削刀具11的刀尖在椭圆轨道上进行振动。x轴方向和y轴方向的振动的频率并没有特别限定,但优选为10khz以上,更优选为超声波区域以上。超声波区域的频率是指超出一般人类听觉范围的频率,例如可以是16khz以上的频率。振动切削装置1通过利用超声波频带来实现静音性优异的加工。控制部20分别控制振动装置10的致动器的振动、由进给机构7进行的振动装置10的移动、主轴2a的旋转。
64.需要说明的是,在图1中,进给机构7使切削刀具11相对于被切削材料6移动,但进给机构7也可以为使被切削材料6相对于切削刀具11移动的机构。即,进给机构7具有使切削刀具11相对于被切削材料6等的对象物相对移动的功能即可,在实施方式中,使切削刀具11移动还是使被切削材料6等的对象物移动可由振动切削装置1的种类确定。
65.另外,进给机构7并不限于x轴、y轴、z轴的平移方向的进给功能,还可以具有a轴、b轴、c轴的旋转方向的进给功能。优选地,实施方式的进给机构7不仅具有切削加工时所需的移动方向的进给功能,还具有在切削加工时未被利用的移动方向的进给功能。即,进给机构7可构成为除了在切削加工时所利用的方向的进给功能以外,还具有在切削加工中不需要的(所谓的冗余的)移动方向的进给功能。冗余的方向的进给功能可以在使切削刀具11相对
于后述的预加工面相对移动时利用。
66.图2示出振动切削装置1的功能结构。振动装置10具有产生振动的压电元件12l、12b,在下部前端可安装切削刀具11。压电元件12l使振动装置10在x轴方向(切入方向)振动。以下,有时也将x轴方向的振动称为“纵向振动”。在本说明书中,对与纵向振动相关的部件的符号或记号附加“longitudinal”的首字母“l”。
67.压电元件12b使振动装置10以在y轴方向往复的方式挠曲而使切削刀具11在y轴方向(切削方向)振动。以下,有时也将y轴方向的振动(横向振动)称为“挠曲振动”。在本说明书中,对与挠曲振动相关的部件的符号或记号附加“bending”的首字母“b”。
68.控制部20具备:移动控制部30,用于控制使振动装置10相对于被切削材料6相对移动的进给机构7;以及振动控制部21,用于控制振动装置10的压电元件12l、12b的振动。移动控制部30也可以具有振动切削装置1中的三维坐标的原点,利用切削刀具11的刀尖位置的坐标来控制振动装置10的移动。需要说明的是,控制部20也可以构成为还具备同于控制主轴台2的主轴2a的旋转的控制部(未图示)。以下,对振动控制部21控制振动装置10的振动的方法进行说明。
69.振动控制部21具备产生施加于压电元件12l、12b的周期性电压的电压振荡部25。电压振荡部25由驱动控制部22控制,并产生纵向振动的共振频率f和追随基于驱动控制部22的指令的相位θ的电压。共振频率f由振动装置10的形状、重量分布确定,并且可以根据切削负荷、振动装置10的温度变化等而变化。
70.电压振荡部25所产生的电压由第一放大器23l放大而作为追随共振频率f、相位θ的电压v
l
(f,θ)而被施加到压电元件12l。压电元件12l被施加电压v
l
(f,θ)而被驱动,并产生振动装置10的纵向振动。
71.另外,电压振荡部25所产生的电压经由相移部24由第二放大器23b放大而作为追随共振频率f、相位的电压而被施加到压电元件12b。压电元件12b被施加电压而被驱动,并产生振动装置10的挠曲振动。放大器23l、23b例如可以是开关放大器。
72.相移部24将电压振荡部25所产生的电压相位从θ偏移到在不设置相移部24的情况下,电压v
l
、vb的相位差消失而纵向振动与挠曲振动的相位差消失,切削刀具11采取直线振动轨道,但由于相移部24使电压相位偏移的量,由此切削刀具11将在因纵向振动和挠曲振动而所生成的椭圆状的振动轨道移动。需要说明的是,如果相位差是可变的,则可以可变地生成振动轨道。需要说明的是,通常振动相对于电压的相位延迟在纵向振动和挠曲振动中稍有不同,因此相移部24也起到对纵向振动的相位延迟和挠曲振动的相位延迟的差进行调整的作用。
73.振动装置10形成为具有随着接近切削刀具11而变细的锥形形状。作为锥形形状的种类,有锥形喇叭(conical horn)形状、指数曲线形喇叭(exponential horn)形状、台阶喇叭(step horn)形状等。振动装置10形成为纵向振动和挠曲振动中的节(振动变为最小的部分)的位置在一处以上一致,优选地在两处以上一致,并在一致的节的位置上被支承。
74.纵向振动的次数取决于振动装置10中的“山”(振幅大的部分)的出现次数。例如,如果纵向振动的“山”位于刀具侧端部、中央部、相反侧端部这三处,则为二次的纵向振动。
在挠曲振动中,也可以大致同样地确定次数,例如,如果挠曲振动的“山”在三处,则为一次的挠曲振动。振动装置10被设计为使得两个振动的共振频率大致一致,但在切削加工中会因负荷等而变为不一致。因此,振动控制部21跟踪对于提高加工精度相对重要的纵向振动的共振频率f,并实施基于纵向振动的共振频率f的振动控制。需要说明的是,在振动控制时,可以利用挠曲振动的共振频率,也可以跟踪两者的共振频率的平均值。
75.振动控制部21具有与压电元件12l连接的相位检测部26。相位检测部26检测流过压电元件12l的电流i
l
的相位θ’。压电元件12l的电流i
l
(f,θ’)由频率f和压电元件12l中的实际的相位θ’表示。相位检测部26将相位θ’与放大器23l的电压v
l
(f,θ)的相位θ进行比较,并计算它们的差δθ(=θ
’‑
θ)。在共振频率(在电学上为反共振频率)的附近,具有电压v
l
与电流i
l
的相位差为零的特性,在实施方式中,利用该特性,在以使相位差δθ接近零的方式控制频率f的反馈控制下进行共振频率的跟踪。
76.实际的共振频率因各种因素(例如由于切削的负荷、振动的持续而导致的振动装置10的发热等)而变化,因此电压的相位θ与电流的相位θ’的相位差δθ也会变化。因此,相位检测部26将所测定的相位差δθ与作为由指令数据d表示的目标的相位差(在此为零)进行比较,并将该差(误差)传递给驱动控制部22。驱动控制部22变更电压振荡部25的振荡频率而使得相位差δθ变为0
°
,来跟踪共振频率。实施方式的振动控制部21进行将振动幅度保持为恒定的控制。在该振幅控制中,当负荷增加时,功率消耗(能量消耗)将会增加。振动控制部21具有锁相环(phase lock loop;pll),用于跟踪纵向振动的共振频率f(挠曲振动的共振频率也在其附近)。
77.控制部20具备用于监视表示振动的控制状况的状况值的监视部27。与正在跟踪的共振频率f对应的电压被输入到监视部27,进而电压v
l
(f,θ)和电流i
l
(f,θ’)也被输入。监视部27根据积(v
l
×il
)计算与纵向振动消耗的能量消耗对应的功率p
l
。需要说明的是,由于电压v
l
和电流i
l
周期性地变化,所以将这些积的(至少遍及一个周期)积分除以积分时间而得到的平均值(离散地将累计除以累计数而得到的平均值)为纵向振动消耗的功率。
78.以下的(式1)示出利用时间t时的瞬时电压v
l
(t)和瞬时电流i
l
(t)来计算功率(能量消耗)p
l
的式子。利用连续时间,功率p
l
由(式1)表示。其中,t是振动的周期,为频率f的倒数,m是1以上的整数,将t=0作为积分开始时间。
79.[数学式1]
[0080][0081]
在数字测量的情况下,若将(式1)离散化,则成为以下的(式2)。在此,n是累计次数,δt是采样间隔,优选地以nδt准确成为整数周期的方式选择n。
[0082]
[数学式2]
[0083][0084]
同样地,电压vb(f,θ)和电流ib(f,θ”)被输入到监视部27。其中,θ”是压电元件12b中的实际的相位。监视部27根据时间t时的瞬时电压vb(t)和瞬时电流ib(t)的积(vb×
ib)来计算在挠曲振动中消耗的功率pb。
[0085]
与(式1)、(式2)同样地,计算功率pb的式子由以下的(式3)、(式4)表示。需要说明
的是,这些功率可以利用数字测量结果通过数值运算来计算,也可以近似地通过利用进行瞬时电流与瞬时电压的乘法和其结果的平均化的模拟电路来计算。由于这些能量消耗(功率消耗)是在规定时间内消耗的能量(功率),因此也可以视为能量消耗率(功率消耗率)。
[0086]
[数学式3]
[0087][0088]
[数学式4]
[0089][0090]
位置关系导出部28在被切削材料6未被切削刀具11接触的非接触时(无负荷时),预先从监视部27获取作为表示振动的控制状况的状况值的功率p
l
、pb、共振频率f。位置关系导出部28将监视部27在非接触时所获取的功率p
l
、pb、共振频率f与在切削刀具11与被切削材料6接触的接触时(施加负荷时)所获取的功率p
l
、pb、共振频率f进行比较而计算各状况值的变化量也可。需要说明的是,实施方式的振动控制部21在电压振荡部25的pll控制中不使用电流ib、相位θ”,但也可以使用其中的至少一方。
[0091]
图3、图4示出因振动装置10而椭圆振动的切削刀具11切削被切削材料6的情况(在大约振动一个周期的极短时间内的微观的情况),图5示意性地示出在切削刀具11与被切削材料6之间作用的力。在图4中,v
tool
表示切削刀具11的速度,v
chip
表示切屑h的速度。
[0092]
在挠曲振动的作用下向与被切削材料6的切削方向同方向侧(y轴正方向侧)后退的切削刀具11(图3(a)),由于纵向振动而接近被切削材料6(x轴正方向),并与被切削材料6(工件)接触而开始切削(图3(b))。切削刀具11的刀尖在微观上在前端具有圆角部分,另外具有相对于前端从被切削材料6远离的后刀面l(图4)。
[0093]
切削刀具11若在移动方向比较接近y轴负方向的状态下相对于被切削材料6向x轴正方向相对地接近(图3(a)~图3(b)),则刀尖的圆角部分按压被切削材料6,并摩擦刚由后刀面l加工过的表面(加工面u)(图4(a))。该加工过程被称为抛光过程或磨光过程。
[0094]
接下来,切削刀具11在移动方向比较接近x轴负方向的状态下相对于被切削材料6向y轴负方向相对接近(图3(c)~图3(d))。此时,切削刀具11对被切削材料6进行摩擦并适当地拉起切屑h(图4(b))。该加工过程被称为材料去除过程。然后,若切削刀具11从被切削材料6离开,则结束一个周期的材料去除过程,并返回到图3(a)的状态(但位置前进了一个周期的量)。
[0095]
在抛光过程(图4(a))中,切削刀具11将被切削材料6向切入方向(x轴正方向)按压而从切削材料6受到向切入方向(x轴负方向)被按压的反作用力f
lp
。力f
lp
以纵向振动中的下死点为中心而以将纵向振动推回的方式起作用。因此,力f
lp
作为对于纵向振动的附加的弹簧δk
l
起作用。
[0096]
另外,切削刀具11在摩擦被切削材料6时,从被切削材料6受到切削方向(y轴正方向)的力f
bp
。力f
bp
以挠曲振动中的速度最快的中立点为中心,以阻碍挠曲振动的方式起作用。因此,力f
bp
作为对于挠曲振动的附加的衰减(阻尼器)δcb起作用。
[0097]
在材料去除过程(图4(b))中,切削刀具11将被切削材料6的切屑h拉起,从切屑h受到向切入方向下拉的(x轴正方向)反作用力f
lc
。力f
lc
以纵向振动中的速度最快的中立点为
中心,以阻碍纵向振动的方式起作用。因此,力f
lc
作为对于纵向振动的附加的衰减(阻尼器)δc
l
起作用。
[0098]
另外,切削刀具11在切削方向上相对地按压切屑h(y轴负方向)而从切屑h受到力f
bc
(y轴正方向)。力f
bc
以挠曲振动中的左侧的死点作为中心,以将挠曲振动推回的方式起作用。因此,力fbc作为对于挠曲振动的附加的弹簧δkb起作用。
[0099]
由于加工过程中的弹簧δk
l
、δkb和衰减δcb、δc
l
的存在,在加工中,表示振动切削装置1的振动控制状况的状况值发生变动,具体而言共振频率f、功率p
l
、pb的值发生变动。需要说明的是,实际的振动根据加工条件、振动条件而可发生各种变化,但通过考虑弹簧δk
l
、δkb、衰减δcb、δc
l
,可以掌握状况值的变化的倾向。
[0100]
例如,关于纵向振动的共振频率f,在抛光过程中,切入方向的力f
lp
越大,则越强烈地受到弹簧δk
l
的弹性作用,因此共振频率f会变高。另外,在材料去除过程中,即使超过左侧的死点,拉起切屑h的力f
lc
持续得越长,则共振频率f越高。另一方面,如果在经过左侧的死点之前拉起切屑h的力f
lc
持续得更长,则对于想要朝向纵向的中立点复原的切削刀具11成为使复原力(弹力)变弱的力,因此共振频率f会变低。
[0101]
另外,关于功率p
l
,衰减δc
l
的存在使得与不存在时相比,纵向振动所需的能量增加。纵向振动所需的能量是由功率p
l
提供的,因此功率p
l
的增加与衰减δc
l
的增加相关。衰减δc
l
的增加意味着材料去除过程中的力f
lc
的增加,因此如果通过监视部27确认到功率p
l
的增加,则可以得知切削刀具11拉起切屑h的力增加的情况。
[0102]
同样地,关于功率pb,衰减δcb的存在使得与不存在时相比,挠曲振动所需的能量增加。挠曲振动所需的能量是由功率pb提供的,因此功率pb的增加与衰减δcb的增加相关。衰减δcb的增加意味着抛光过程中的力f
bp
的增加,因此如果通过监视部27确认到功率pb的增加,则可以得知切削刀具11从被切削材料6受到的y轴方向的力增加的情况。
[0103]
这样,实施方式的监视部27具有在被切削材料6的切削中监视表示振动的控制状况的状况值的功能。例如,如果切削刀具11的磨损加剧,则存在抛光过程中的力f
bp
变大的倾向。因此,监视部27监视加工中的功率pb而在增加量超过了规定值的情况下能够检测出切削刀具11的磨损正在加剧的情况。
[0104]
以上的监视部27的监视功能监视表示加工中的振动的控制状况的状况值,但在实施方式的振动切削装置1中,在无负荷时、具体而言在测定切削刀具11的安装位置时利用该监视功能。
[0105]
在更换刀具时等将切削刀具11重新安装于振动装置10时,为了使移动控制部30发挥高的移动精度(加工精度),需要确定刀尖位置的准确的坐标值。在作为表示振动的控制状况的状况值的功率p
l
、pb、共振频率f中,特别是挠曲振动的功率消耗pb会响应于y轴方向(切削方向)的力的增加,因此对于切削刀具11与被切削材料6的接触以高灵敏度增加。于是,在以下的例子中示出利用功率消耗pb的变化(上升)来进行接触检测的情况,但也可以利用其他的状况值、例如共振频率f的变化来进行接触检测。
[0106]
本发明人进行了利用控制状况值的监视功能的刀尖位置测定方法的验证实验。在该实验中,将振动装置10安装于刨床,监视部27获取了对进给运动的工件进行刨削时的振动控制状况值。需要说明的是,该实验的目的在于,检测刀具刀尖与工件的接触而确定接触位置,还进行了与基于实验条件的接触位置的误差相关的考察。
[0107]
图6是用于说明对工件w的切削实验的概要的图。图6(a)示出从上方朝倾斜方向对工件w进行切削的情况,图6(b)示出在工件w的上表面观测的切削痕的状态。切削痕为在切削方向上逐渐变深且变宽的形状。
[0108]
该实验是在以下条件下实施的。
[0109]
切削刀具:单晶金刚石(刀尖半径(nose radius)0.8mm)
[0110]
工件w:淬火钢(hardened steel)53hrc
[0111]
振动条件:17khz 10μm(p-p)。
[0112]
振动控制部21使振动装置10椭圆振动,移动控制部30以使切入量逐渐增加的方式使振动装置10向切入方向移动,监视部27测量了挠曲振动的功率消耗pb。在实验中,预先以线la进行工件w的切削,接着以使刀具刀尖比线la下降了1.5μm的线lb对工件w进行切削,监视部27记录了此时的控制状况值。需要说明的是,在该实验中,从保护切削刀具11的观点出发,使工件w在切削方向进给运动而进行了切削,但即使不使工件w进给运动,也能够进行接触检测。
[0113]
图7示出挠曲振动方向的功率消耗pb的时间变化。需要说明的是,纵轴示出了从测定的功率消耗减去无负荷时的功率后的δpb。
[0114]
在图7中,可以得到以下的测定结果:从时间t1开始δpb上升,在时间t2时δpb的上升结束。这意味着这样的情况:在时间t1的附近刀具刀尖与工件w接触而开始切削,在时间t2的附近到工件w的右端为止的切削结束而刀具刀尖从负荷中被解放。位置关系导出部28对时间t1附近的功率消耗变化进行直线(曲线)近似而求出近似的回归直线(曲线)零交叉(zero cross,过零)的位置(t1’)。如果位置关系导出部28将所求出的时间t1’提供给移动控制部30,则移动控制部30将时间t1’时的振动装置10的控制位置坐标返回给位置关系导出部28。该控制位置坐标表示出切削刀具11与工件w的接触位置,因此位置关系导出部28能够确定接触位置。
[0115]
需要说明的是,在δpb的检测值中重叠有干扰(noise)。如果为了求出本实验的位置检测精度而计算出认为是接触前的区间的功率消耗pb的干扰的标准差σ,则能够求得以下的实验值。
[0116]
平均值m:-0.00096872[w]
[0117]
标准差σ:0.0033
[0118]
置信区间(confidence interval)95%:
±
2σ=
±
0.0066
[0119]
图8示出切削痕的最大切入深度和工件w的横向位置的测定结果。在本实验中,通过对工件w从上方朝倾斜方向切削来得到图8所示的测定结果。
[0120]
图9示出挠曲振动方向的功率消耗pb的变化与切削痕的最大切入深度的关系。切入深度越深切削宽度越增加,切削负荷越大,因此成为δpb随着切入深度而上升的关系。在本实验中,根据图9所示的关系,对接触时的功率消耗变化进行直线(曲线)近似而求出近似的回归直线(曲线)零交叉的位置,从而计算出接触位置的检测精度。
[0121]
图10示出利用零点附近的采样点而导出的回归直线和表示其置信区间的直线。在此,利用最小二乘法求得以下的回归直线。
[0122]
y=14.975x-0.0025
[0123]
需要说明的是,在该例子中求出了回归直线,但也可以求出多次函数的回归曲线。
在本实验中,如图所示,导出了接触位置的检测误差e
p
为0.6μm的情况。需要说明的是,为了减小位置检测误差,只要缩短采样周期而增加采样数并进行移动平均即可。
[0124]
这样,在实验中,监视部27获取并记录挠曲振动方向的功率消耗pb的变化(增量),位置关系导出部28确定发生了变化的瞬间(时间t’)、即刀具刀尖与工件w接触的瞬间的刀具位置。该确定方法有多种,作为一例,通过利用最小二乘法而能够高精度地确定刀具位置。需要说明的是,为了提高刀具位置的确定精度,只要通过缩短采样周期而增加采样数并增加移动平均的点数来提高精度即可。
[0125]
这样,振动切削装置1在无负荷时获取表示振动的控制状况的状况值,并基于状况值的变化来检测切削刀具与被切削材料(工件)的接触而确定接触位置。在上述实验中,利用了挠曲振动所需的能量消耗、具体而言,利用了挠曲振动所需的功率消耗,但也可以通过解析纵向振动的共振频率f的变动值,来检测切削刀具与被切削材料的接触。
[0126]
这样,控制部20具有这样的功能:控制进给机构7使振动装置10相对移动而获取切削刀具11与被切削材料6等的接触对象物接触时的坐标值。以下,以具有该功能为前提,对在进行车削类型的加工的振动切削装置1中确定切削刀具11与对象物的相对位置关系的方法进行说明。需要说明的是,在实施例1中,被切削材料6的旋转中心与主轴2a的旋转中心意思相同。
[0127]
《实施例1》
[0128]
图11是用于说明确定切削刀具与被切削材料旋转中心的相对位置关系的方法的图。以下,对计算被切削材料6的旋转轴中心a(x,y)的方法进行说明。在该例子中,被切削材料6为经过一次车削加工后的状态。需要说明的是,从防止锋利的刀具切削刃的缺损的观点出发,优选地通过主轴2a使被切削材料6旋转,但被切削材料6也可以不旋转。
[0129]
首先,移动控制部30使刀具刀尖从下方向上方(y轴正方向)缓慢地移动而在p1点与车削加工完毕的被切削材料6接触。需要说明的是,p1点的x轴方向的坐标x1是事先设定的,y轴方向的坐标为变量。接触检测可以由振动控制部21通过上述方法来进行。需要说明的是,根据上述接触检测方法,位置关系导出部28根据接触后的功率消耗变化来生成回归直线,在事后确定接触位置。因此,在移动控制部30使刀具刀尖在p1点接触的瞬间,位置关系导出部28还不能确定接触位置,虽然实际上已在p1点接触,但移动控制部30需要使刀具刀尖向比p1点稍靠上方移动(进行与此相应的切削)。需要说明的是,如果δpb的上升量超过规定值,则位置关系导出部28检测切削刀具11与被切削材料6的接触,例如通过检测干扰振幅以上的δpb的上升来检测切削刀具11与被切削材料6的接触即可。
[0130]
如果位置关系导出部28利用回归直线而导出接触时刻(timing),移动控制部30则将接触时刻的坐标、即p1点坐标(x1,y1)提供给位置关系导出部28。也可以是,如果位置关系导出部28导出接触的时刻,则相对于移动控制部30使振动装置10的移动停止。需要说明的是,严格地说,移动控制部30并不是管理切削刀具11的刀尖的坐标,而是管理振动装置10的坐标,但是由于刀尖坐标与振动装置坐标为一对一的关系,因此以下根据刀尖坐标进行说明。
[0131]
需要说明的是,如上所述,被切削材料6使用已经车削加工完毕的工件。这是为了在以被切削材料6的旋转轴、即主轴2a的旋转轴为中心的相同直径的圆的圆周上检测p1点和后述的p2点坐标、p3点坐标。因此,位置关系导出部28使刀具刀尖在p1点与车削加工后的
被切削材料6接触,但也可以将作为预加工而进行的车削加工时的x轴和y轴的坐标值设为p1点。
[0132]
接着,移动控制部30使刀具刀尖向下方(图11中的y轴负方向)下降足够的距离而向x轴正方向前进已知的距离d。然后,移动控制部30使刀具刀尖向上方(y轴正方向)缓慢地移动而在p2点与被切削材料6接触。如果位置关系导出部28检测到接触而导出接触时刻,移动控制部30则将接触时刻的坐标、即p2点坐标(x2,y2)提供给位置关系导出部28。
[0133]
接着,移动控制部30使刀具刀尖向下方(y轴负方向)下降足够的距离而向x轴正方向前进已知的距离d。需要说明的是,前进的距离只要是已知的距离即可,与p1点坐标和p2点坐标之间的x轴方向距离(d)不同也可。然后,移动控制部30使刀具刀尖向上方(y轴正方向)缓慢地移动而在p3点与被切削材料6接触。如果位置关系导出部28检测到接触而导出接触时刻,移动控制部30则将接触时刻的坐标、即p3点坐标(x3,y3)提供给位置关系导出部28。需要说明的是,在一边使主轴2a旋转一边进行接触检测的情况下,由于在接触时进行了轻微的切削而半径减小,因此p1点、p2点以及p3点各自的接触检测在不同的z轴方向位置进行为好。
[0134]
位置关系导出部28根据切削刀具11在与车削加工时的切削刀具11的旋转角度位置不同的至少两个位置接触时的坐标值,来确定切削刀具11与被切削材料6的旋转中心的相对位置关系。例如,在将作为预加工而进行的车削加工时的x轴和y轴的坐标值设为p1点时,位置关系导出部28根据与p1点成为分别不同的旋转角度位置的p2点、p3点的坐标值,来确定切削刀具11与被切削材料6的旋转中心的相对位置关系。需要说明的是,在实施例1中,位置关系导出部28根据三个旋转角度位置分别不同的接触点、即p1点、p2点、p3点的坐标值,来确定切削刀具11与被切削材料6的旋转中心的相对位置关系。位置关系导出部28利用确定一个通过三点的圆,来计算作为被切削材料6的旋转中心的a点的坐标(x,y)和半径r。
[0135]
图12(a)、(b)示出a点坐标的导出方法。如图12(a)所示,能够通过计算线l1与线l2的交点来求出坐标a。线l1、l2分别由以下的(式5)、(式6)表示。
[0136]
[数学式5]
[0137][0138]
[数学式6]
[0139][0140]
根据(式5)、(式6),导出(式7)。
[0141]
[数学式7]
[0142][0143]
其中,
[0144]
x
1-x2=-d
[0145]
x
2-x3=-d,
[0146]
如果将p2点坐标(x2,y2)定义为(0,0),则可以由[数学式8]
[0147][0148]
导出a点的x坐标。
[0149]
另外,图12(b)所示的线l3由以下的(式9)表示。
[0150]
[数学式9]
[0151][0152]
如果将由(式8)求得的x代入(式9),有下式:
[0153]
[数学式10]
[0154][0155]
由此导出a点的y坐标。
[0156]
需要说明的是,被切削材料6的旋转半径如下式求出。
[0157]
[数学式11]
[0158][0159]
这样,位置关系导出部28导出将p2点坐标(x2,y2)设为(0,0)时的a点坐标。由此,位置关系导出部28根据三个接触位置的坐标值,来确定切削刀具11与被切削材料6的旋转中心的相对位置关系。
[0160]
以下,对a点坐标和半径r的计算精度进行考察。在实施例1中,在图10中,计算出了接触检测中的接触位置检测误差e
p
,以下,对该检测误差e
p
对a点坐标和半径r的精度所带来的影响进行验证。
[0161]
x坐标的误差设为e
x
,y坐标的误差设为ey,半径r的误差设为er。
[0162]
则按下式考虑误差。
[0163]
[数学式12]
[0164][0165]
在这样考虑了误差的情况下,由(式8)表示的a点的x坐标值、由(式10)表示的a点的y坐标值、由(式11)表示的半径r表示如下。
[0166]
[数学式13]
[0167][0168][0169]
按下式求出误差e
x
:
[0170]
[数学式14]
[0171][0172]
其中,
[0173]
因为可以近似为下式:
[0174]
[数学式15]
[0175][0176]
因此可导出误差e
x
如下。
[0177]
[数学式16]
[0178][0179]
同样地,按下式求出误差ey:[数学式17]
[0180][0181]
其中,因为可以近似为下式:[数学式18]
[0182][0183]
所以可导出误差ey如下。
[0184]
[数学式19]
[0185]ey
≈e
p
[0186]
误差er由下式表示。
[0187]
[数学式20]
[0188][0189]
这样,x坐标的误差e
x
、y坐标的误差ey、半径r的误差er均可以用接触位置检测误差e
p
来表示,确认了通过减小接触位置检测误差e
p
来提高加工精度的情况。
[0190]
如在实施例1中说明的那样,如果能够确定切削刀具11与被切削材料6的旋转中心(主轴中心)的相对位置,则在圆筒面的加工时能够精加工成准确的直径,在加工端面时,由于刀具刀尖的中心高度不会波动,因此不会残留所谓的凹陷,对于球面、非球面加工也能够实现高的加工精度。
[0191]
《实施例2》
[0192]
在实施例1中,位置关系导出部28检测切削刀具11与车削加工后的被切削材料6的接触而确定了该接触位置。在实施例2中,位置关系导出部28检测切削刀具11与在安装被切削材料6的部件上设置的基准面的接触而确定切削刀具11相对于部件基准面的相对位置也可。作为部件的例子,例如可以是支承被切削材料6的主轴2a,通过使切削刀具11与设置于主轴2a的端面、周面的基准面接触,来位置关系导出部28确定切削刀具11与主轴2a的接触位置,由此可以导出切削刀具11与被切削材料6的安装面、旋转中心等的相对位置关系。
[0193]
图13是用于说明基准面的图。对于基准面,可设定与工件w的安装面、旋转中心等的相对位置关系已知的面。在该例子中,在使工件w绕中心轴线旋转而进行车削加工的切削装置中,将用于固定工件w的主轴2b的端面设定为基准面1,将主轴2b的周面设定为基准面2。即,基准面1是与主轴旋转轴垂直的平面,基准面2是以主轴旋转中心为中心的圆筒面。位置关系导出部28根据与工件w的安装面、旋转中心等的相对位置关系已知的基准面上的接触位置的坐标值,来确定切削刀具与工件w的安装面、旋转中心等的相对位置关系。
[0194]
如上所述,位置关系导出部28检测切削刀具11与作为部件的主轴2b的接触而能够确定该接触位置。
[0195]
在此,位置关系导出部28通过对基准面1进行刀具刀尖的接触检测,能够准确地获知工件w的长度方向(图的左右方向)的刀具刀尖原点(工件w的安装面、即刀具刀尖相对于工件w的左端的面的相对位置)。由此,在对工件w的端面(图中的右端的面)进行加工时,能够准确地精加工出工件w的长度(左右方向的长度)。
[0196]
另外,位置关系导出部28通过在与实施例1同样地在y轴位置不同的三点(如果直径已知则两点即可)对基准面2进行刀具刀尖的接触检测,能够准确地获知工件w的半径方向的刀具刀尖原点(刀具刀尖相对于工件w的旋转中心的相对位置)。由此,在加工工件w的圆筒面时,能够准确地精加工出工件w的直径。
[0197]
基准面也可以设定于工件w的一部分上。例如,在图13中,在基准面1是工件w的一部分的情况下,能够准确地精加工出从该面到工件w的右端面为止的长度。需要说明的是,在图13中示出了车削加工的例子,但如果是刨削加工,则只要在基准面(准确的平面)上的三点进行接触检测就能够确定该平面,因此能够以准确的高度精加工出与基准面平行的面。另外,如果基准面是与z轴准确地垂直的平面,则仅通过在一点进行接触检测,就能够以准确的高度精加工出与底面(与基准面接触的工件w的面)平行的面。
[0198]
在以下的实施例3~13中,主要对应用了在实施例1中说明的三点接触检测的技术进行说明。在以下说明所使用的附图中,a轴是指以x轴为中心的旋转轴,b轴是指以y轴为中心的旋转轴,c轴是指以z轴为中心的旋转轴。另外,在本说明书和附图中,关于带有尖角(caret)(帽形(hat))的记号,例如当记号为“y”时,需要注意的是,为了表记上的方便,按如下方式表示。
[0199]
[数学式21]
[0200][0201]
即,在记号y的上方附加尖角(帽形)的记号和在相同记号y的旁边附加尖角的记号表示相同的变量。在实施例中,带有尖角的记号是指应求出的变量。需要说明的是,上方附加有尖角的记号在数学式中使用,而在旁边附加有尖角的记号在文章中使用。另外需要注意的是,在不同的实施例的附图中重复使用的记号是为了便于理解各个实施例。
[0202]
《实施例3》
[0203]
在实施例1中,控制部20根据车削加工后的、换言之预加工后的被切削材料6上的三点的坐标值,来确定切削刀具11与被切削材料6的旋转中心的相对位置关系。在实施例3中,控制部20利用用于设定刀尖的原点而高精度地加工的具有已知形状的物体,来确定切削刀具11与具有已知形状的物体的相对位置关系,从而确定与切削刀具11的刀尖相关的信息。以下,将为了确定与切削刀具11的刀尖相关的信息而使用的物体称为“基准块”。控制部
20通过使切削刀具11的刀尖与基准块接触来识别(identify)刀尖位置,因此作为其前提,至少掌握要去接触的基准块的形状。
[0204]
图14示出将振动装置10以能够c轴旋转的方式安装的振动切削装置1的一例。图14(a)示出从x轴方向观察的振动切削装置1的情况,图14(b)示出从z轴方向观察的振动切削装置1的情况。在振动装置10的前端安装有切削刀具11,振动装置10由支承装置42支承。支承装置42以能够c轴旋转的方式固定于安装轴41。
[0205]
在b轴工作台43上配置有作为具有已知形状的物体的基准块40。在实施例3中,为了将切削刀具11安装于振动装置10之后确定切削刀具11的刀尖位置,控制部20使刀尖与基准块40至少接触三次,并利用该接触点的位置坐标来确定与切削刀具11的安装位置相关的信息。在实施例3中,进给机构7具有使b轴工作台43移动的功能,移动控制部30使b轴工作台43移动而使切削刀具11的刀尖11a与基准块40的已知形状部分在多个点接触。基准块40由高硬度的材料形成,以便不易因刀尖11a的接触而损伤。在实施例3中,刀尖11a的刀尖半径、刀尖圆角的中心坐标、刀尖形状的误差未知,对确定这些信息的方法进行说明。以下,设定为刀尖11a的前端具有恒定的曲率(刀尖半径),刀尖圆角的中心也称为“刀具中心”。
[0206]
在图14(a)所示的yz平面中,求出刀尖半径r^和yz平面中的刀具中心(z^,y^)。
[0207]
图15示出刀尖11a与基准块40的已知形状部分在一点接触的情况。如上所述,刀尖11a具有恒定的曲率,并具有刀尖半径r^的圆弧面。需要说明的是,刀尖半径r^未知。另一方面,基准块40在形状已知的部分上与刀尖11a接触。在实施例3中形状已知是指,位置关系导出部28知道刀尖11a有可能接触的部位的形状的情况。
[0208]
基准块40只要至少在与刀尖11a接触的部位具有已知的形状即可,位置关系导出部28不需要知道不可能与刀尖11a接触的部位的形状。在图15所示的例子中,基准块40具有以“ ”示出的位置为中心的半径为rw的圆弧面,在进行刀尖11a的原点设定时,位置关系导出部28知道刀尖11a与该圆弧面接触的情况。换言之,在原点设定时,移动控制部30控制进给机构7而使b轴工作台43移动,以使刀尖11a与作为基准块40的已知形状的圆弧面接触。该圆弧面的形状数据可以记录于未图示的存储器中。
[0209]
移动控制部30使b轴工作台43朝向切削刀具11的刀尖11a从下方向上方(y轴正方向)缓慢地移动。在图15中,刀尖11a与基准块40在用
○
表示的接触点接触。位置关系导出部28将此时的基准块40中的圆弧的旋转中心位置“ ”的坐标定义为(0,0)。接触检测可以由振动控制部21通过上述方法来进行。
[0210]
然后,移动控制部30以初始的接触位置为基准,使基准块40在z轴方向移动了 δz、-δz的位置与刀尖11a接触。无论在哪种情况下,基准块40的刀尖11a接触的位置均位于半径为rw的圆弧面上。具体而言,移动控制部30从图15所示的状态开始,使基准块40向y轴负方向下降足够的距离之后向z轴负方向移动δz,并从该位置起向y轴正方向缓慢地移动,从而使基准块40的圆弧面与刀尖11a接触。此时的接触点在图中用
△
表示。接着,移动控制部30使基准块40向y轴负方向下降足够的距离之后向z轴正方向移动2δz,从该位置起向y轴正方向缓慢地移动,从而使基准块40的圆弧面与刀尖11a接触。此时的接触点图中用
□
表示。需要说明的是,在第二次移动时,也可以省略y轴负方向的移动。
[0211]
这样,移动控制部30使切削刀具11的刀尖11a与基准块40的已知形状部分至少在三点接触,并将接触位置的坐标值提供给位置关系导出部28。位置关系导出部28根据各个
接触位置的坐标值来确定与切削刀具11的安装位置相关的信息。
[0212]
图16示出刀尖11a与基准块40的位置关系。在图15中,在用
□
表示的接触点接触的情况下,已知圆弧中心的坐标为(δz,h2)。h2是移动控制部30的检测值。另外,在图15中,在用
△
表示的接触点接触的情况下,已知圆弧中心的坐标为(-δz,-h1)。h1也是移动控制部30的检测值。
[0213]
如图16所示,将第一次接触时的基准块40中的圆弧面的半径中心设为(0,0),将刀具中心设为(z^,y^)时,有下式。
[0214]
[数学式22]
[0215][0216][0217][0218]
联立后,有下式。
[0219]
[数学式23]
[0220][0221][0222]
利用由上式得到的z^、y^来求出r^。
[0223]
[数学式24]
[0224][0225]
如上所述,位置关系导出部28根据在三个位置接触时的坐标值,来确定与切削刀具11的安装位置相关的信息。具体而言,作为与安装位置相关的信息,位置关系导出部28求出刀尖的刀尖半径r和刀具中心坐标(z,y)。
[0226]
需要说明的是,如果对具有已知的圆弧形状的基准块40在除了上述三个接触位置以外的圆弧上的点中至少一个点以上接触,则利用如上所求得的刀尖半径r和刀具中心坐标(z,y)而预测的从接触位置的偏差,作为刀具刀尖的从上述刀尖半径r的圆弧的偏差(误差)来被求出。
[0227]
接下来,位置关系导出部28进行在图14(b)所示的xy平面中求出从c轴旋转中心到刀尖11a前端的距离l^和初始的安装角度θ^的计算。例如在加工复杂的自由曲面形状的情况下,有时重复进行同时控制xyc轴的切削进给和z轴方向的周期进给(pick feed)。这样,在c轴包含于切削进给运动中的情况下,如果从c轴旋转中心到刀尖11a前端的距离l^与初始的安装角度θ^存在误差,则会导致加工精度下降。因此,位置关系导出部28根据将刀尖11a在xy平面移动时的、与基准块40的已知形状部分的至少三点的接触坐标值,来确定与切削刀具11的安装位置相关的信息。
[0228]
图17示意性地示出使切削刀具11逆时针旋转而使刀尖11a与基准块40的上表面(y
基准面)接触时的切削刀具11的倾斜状态。移动控制部30控制进给机构7而使切削刀具11绕c轴旋转。基准块40的上表面与y轴的垂直面平行,如图14(b)所示,基准块40的上表面位置已知。
[0229]
移动控制部30使b轴工作台43朝向切削刀具11的刀尖11a从下方向上方(y轴正方向)缓慢地移动而使基准块40的上表面与刀尖11a接触。然后,移动控制部30使基准块40向y轴负方向下降足够的距离之后使切削刀具11向逆时针方向旋转δc,然后使基准块40向y轴正方向缓慢地移动而使基准块40的上表面与刀尖11a接触。接着,移动控制部30使基准块40向y轴负方向下降足够的距离之后使切削刀具11向逆时针方向进一步旋转δc,然后使基准块40向y轴正方向缓慢地移动而使基准块40的上表面与刀尖11a接触。由此,位置关系导出部28获取三点的接触位置的y轴方向的高度(y位置)。
[0230]
图18示出从初始的接触位置(初始y位置)旋转δc时的接触位置的高度变化δy1。以初始的接触位置为基准,进一步旋转δc时的接触位置的高度变化为δy2。此时,关于δy1、δy2,有以下式子成立。
[0231]
[数学式25]
[0232][0233][0234]
联立后从两式消去l^,
[0235]
[数学式26]
[0236][0237][0238]
利用得到的θ^来求出l^。
[0239]
[数学式27]
[0240][0241]
如上所述,关于c轴旋转,位置关系导出部28根据在三个位置接触时的坐标值,来获取与切削刀具11的初始的安装位置相关的信息。具体而言,位置关系导出部28作为与安装位置相关的信息来导出从c轴旋转中心到刀尖11a的距离l和初始的安装角度θ。这样,在实施例3中,通过使用基准块40来位置关系导出部28能够高精度地确定与安装位置相关的信息。
[0242]
《实施例4》
[0243]
在实施例4中也采用:控制部20利用用于刀尖的原点而高精度地加工的具有已知形状的物体(基准块40),来确定切削刀具11与基准块40的相对位置关系,从而确定与切削刀具11的安装位置相关的信息。
[0244]
图19示出将振动装置10以能够c轴旋转的方式安装的振动切削装置1的另一例。图19(a)示出从x轴方向观察的振动切削装置1的情况,图19(b)示出从z轴方向观察的振动切削装置1的情况。在振动装置10的前端安装有切削刀具11,振动装置10由支承装置42支承。支承装置42以能够c轴旋转的方式固定于安装轴41。
[0245]
在b轴工作台43上配置有作为具有已知形状的物体的基准块40。在实施例4中也采用:为了将切削刀具11安装于振动装置10之后确定切削刀具11的刀尖位置,控制部20使刀尖与基准块40至少接触三次,并利用该接触点的位置坐标来确定与切削刀具11的安装位置相关的信息。实施例4也与实施例3同样地,移动控制部30使b轴工作台43移动而使切削刀具11的刀尖11a与基准块40的已知形状部分在多个点接触。
[0246]
首先对求出刀尖半径r^和xy平面的刀具中心(x^,y^)的方法进行说明。
[0247]
图20示出刀尖11a与基准块40的已知形状部分在一点接触的情况。刀尖11a具有一定的曲率,并具有刀尖半径r^的圆弧面。刀尖半径r^未知。基准块40在形状已知的部分上与刀尖11a接触。需要说明的是,形状已知是指,位置关系导出部28知道刀尖11a有可能接触的部位的形状的情况。
[0248]
在图20所示的例子中,基准块40具有以“ ”所示的位置为中心的半径为rw的圆弧面,在进行刀尖11a的原点设定时,位置关系导出部28知道刀尖11a与该圆弧面接触的情况。换言之,在原点设定时,移动控制部30控制进给机构7而使b轴工作台43移动,以使刀尖11a与作为基准块40的已知形状的圆弧面接触。该圆弧面的形状数据可以记录于未图示的存储器中。
[0249]
移动控制部30使b轴工作台43朝向切削刀具11的刀尖11a从下方向上方(y轴正方向)缓慢地移动。在图20中,刀尖11a与基准块40在用
○
表示的接触点接触。位置关系导出部28将此时的基准块40中的圆弧的旋转中心位置“ ”的坐标定义为(0,0)。
[0250]
然后,移动控制部30以初始的接触位置为基准,使基准块40在向x轴方向移动了 δx、-δx的位置与刀尖11a接触。无论在哪种情况下,基准块40的与刀尖11a接触的位置均位于半径为rw的圆弧面上。具体而言,移动控制部30从图20所示的状态开始,使基准块40向y轴负方向下降足够的距离之后向x轴负方向移动δx,并从该位置起向y轴正方向缓慢地移动,从而使基准块40的圆弧面与刀尖11a接触。此时的接触点图中用
△
表示。接着,移动控制部30使基准块40向y轴负方向下降足够的距离之后向x轴正方向移动2δx,从该位置起向y轴正方向缓慢地移动,从而使基准块40的圆弧面与刀尖11a接触。此时的接触点图中用
□
表示。需要说明的是,在第二次移动时,也可以省略y轴负方向的移动。
[0251]
这样,移动控制部30使切削刀具11的刀尖11a与基准块40的已知形状部分至少在三点接触,并将接触位置的坐标值提供给位置关系导出部28。位置关系导出部28根据各个接触位置的坐标值来确定与切削刀具11的安装位置相关的信息。
[0252]
图21示出刀尖11a与基准块40的位置关系。在图20中,在用
□
表示的接触点接触的情况下,已知圆弧中心的坐标为(δx,h2)。h2是移动控制部30的检测值。另外,在图20中,在用
△
表示的接触点接触的情况下,已知圆弧中心的坐标为(-δx,-h1)。h1也是移动控制部30的检测值。
[0253]
如图21所示,将第一次接触时的基准块40中的圆弧面的半径中心设为(0,0),将刀具中心设为(x^,y^)时,有下式。
[0254]
[数学式28]
[0255][0256][0257][0258]
联立后,有下式。
[0259]
[数学式29]
[0260][0261][0262]
利用由上式得到的x^、y^来求出r^。
[0263]
[数学式30]
[0264][0265]
如上所述,位置关系导出部28根据在三个位置接触时的坐标值,来确定与切削刀具11的安装位置相关的信息。具体而言,作为与安装位置相关的信息,位置关系导出部28求出刀尖的刀尖半径r和刀具中心坐标(x,y)。
[0266]
接下来,位置关系导出部28求出刀尖11a的z坐标。
[0267]
图22示出使基准块40的已知形状的部分与切削刀具11的刀尖11a接触的状态。位置关系导出部28通过获取此时的z坐标值来确定刀尖的前端点。
[0268]
需要说明的是,移动控制部30需要移动基准块40而使基准块40中的已知的圆弧面与刀尖11a接触。例如在移动了基准块40时,会有在基准块40的圆弧面与刀尖11a接触之前与切削刀具11的前刀面接触的情况。在图示的例子中,在初始安装状态下的前刀面的角度相对于z轴小于90度的情况下,因基准块40的z轴方向的位置,会有基准块40的圆弧面与切削刀具11的前刀面接触而基准块40的圆弧面不能与刀尖11a接触的情况。此时,移动控制部30使基准块40向y轴负方向偏移而使刀尖11a在已知圆弧面的上部侧接触为好。
[0269]
这样,在实施例4中,通过使用基准块40来位置关系导出部28能够高精度地确定与安装位置相关的信息。
[0270]
《实施例5》
[0271]
在切削刀具11存在安装误差的情况下,切削加工后的被切削材料6则成为具有与本来预定的形状不同的形状。因此,在实施例5中,利用实际车削加工后的被切削材料6的加工面与理想车削加工时的被切削材料6的加工面(即设计上的加工面)的差量,来确定刀具中心的安装误差(δx^,δy^、δz^)。如果能够确定刀具中心的安装误差,则能够计算对所确定的安装误差进行修正的切削刀具11的进给路径。在实施例5中,移动控制部30利用在切削加工时未利用的移动方向的进给机构7的进给功能而使振动装置10相对于切削加工后的被切削材料6相对移动,并根据切削刀具11在至少两个位置接触时的坐标值来确定刀具刀
尖的安装误差。
[0272]
以下,有时将为了导出误差而进行了车削加工后的被切削材料6的加工面称为“预加工面”或“已加工面”。需要说明的是,通过预先将预加工面形成为比最终精加工面的厚度厚,在加工最终精加工面时,能够以修正后的进给路径进行精加工。即,在最终的精加工前的中间精加工后,利用该加工面来确定安装误差即可。
[0273]
控制部20根据被切削材料6的预加工面上的至少三点的坐标值,来求出切削刀具11的安装误差。在利用在预加工面的切削加工时所获取的一个点的坐标值的情况下,控制部20也可以获取使切削刀具11在与在车削加工时的切削刀具11的旋转角度位置不同的位置与预加工面接触的至少两点的坐标值,来求出切削刀具11的安装误差。即,控制部20也可以获取使切削刀具11在不同的y位置与预加工面接触的至少两点的坐标值,来求出切削刀具11的安装误差。
[0274]
需要说明的是,考虑到在预加工时获取的坐标值与通过与预加工面接触而获取的坐标值的精度稍微不同的可能性,控制部20也可以不使用在预加工时所获取的坐标值,而利用使切削刀具11在不同的y位置与预加工面接触的至少三点的坐标值,来求出切削刀具11的安装误差。
[0275]
需要说明的是,如在实施例1中说明的那样,在获取接触点坐标值时,从防止刀尖11a缺损的观点出发,有时使被切削材料6旋转。在此情况下,由于在接触点产生细微的开槽的情况,因此在获取下一个接触点坐标值时,将z位置在可视为实质上相同的范围内稍微偏移为好。以下,示出控制部20利用三点的坐标值来求出安装误差的例子,但为了提高安装误差的检测精度,也可以利用四点以上的坐标值。
[0276]
图23(a)示出将被切削材料6加工成具有圆筒面和半球面的形状的情况。被切削材料6以能够旋转的方式支承于安装轴41。在实施例5中,切削刀具11以(δx^,δy^、δz^)的安装误差安装于振动装置10。
[0277]
图23(b)示出zx平面上的安装误差(δx^,δz^)。c2表示理想的刀具中心位置,c1表示包含误差的刀具中心位置。图23(c)示出xy平面上的安装误差(δx^,δy^)。
[0278]
在图23(a)中,箭头所示的进给路径是理想中心c2所通过的路径。在nc机床中,以刀具中心位于c2为前提,计算进给路径。移动控制部30利用进给机构7的z轴平移方向的进给功能和c轴旋转方向的进给功能而利用切削刀具11对被切削材料6进行加工。在图23(a)中,虚线表示刀具中心位于c2时的理想的加工面。在该车削加工中,加工半径为rw的圆筒面的情况被确定为设计值。
[0279]
然而,在实际的刀具中心包含安装误差而位于c1的情况下,如果移动控制部30使切削刀具11按照所计算出的进给路径移动,则成为形成实线所示的加工面的情况。
[0280]
图24(a)(b)是用于说明导出刀具中心的安装误差(δx^,δy^)的方法的图。由于xy平面上的安装误差(δx^,δy^),圆筒面的半径不是rw,而是rw’。移动控制部30利用在切削加工时未利用的移动方向的进给机构7的进给功能而使振动装置10相对于切削加工后的被切削材料6相对移动,从而获取切削刀具11在至少两个位置接触时的坐标值。在实施例5中,移动控制部30利用进给机构7的x轴平移方向和y轴平移方向的进给功能而获取多个接触坐标值。
[0281]
利用与预加工时相同的移动方向的进给机构7的进给功能而使切削刀具11与预加
工面接触,理论上也会成为在与加工时相同的坐标位置接触的情况。因此,在实施例5中,为了通过预加工面与切削刀具11的接触来导出刀具中心的安装误差,利用与在预加工时所利用的移动方向的进给机构7的进给功能不同的移动方向的进给功能而使切削刀具11与预加工面接触。即,利用预加工时所需的移动方向的进给功能以外的进给功能而导出切削刀具11的接触位置。如上所述,移动控制部30在预加工时利用了zc轴的进给功能,但在安装误差的推定处理时,利用xy轴的进给功能来获取接触点坐标。
[0282]
如在实施例1中说明的那样,位置关系导出部28获取圆筒面上的三点的坐标值。
[0283]
图中,
□
表示圆筒面上的点,
[0284]
点1:(rw δx^,δy^)
[0285]
点2:(rw δx^-δx1,-δy δy^)
[0286]
点3:(rw δx^-δx2,-2δy δy^)
[0287]
δx1、δx2是由移动控制部30检测的值。
[0288]
需要说明的是,在该例子中,作为点1示出的坐标值利用了在预加工时所获取的坐标,但移动控制部30也可以通过在三点使刀尖11a与圆筒面接触来获取三点的坐标值。此时,在从防止刀尖11a缺损的观点出发而使被切削材料6旋转的情况下,移动控制部30使刀尖11a在圆筒面上的不同的z位置接触而获取三点的接触坐标值为好。
[0289]
位置关系导出部28进行以下计算。
[0290]
[数学式31]
[0291]
[式-1]
[0292]
[式-2]
[0293]
[式-3]
[0294]
将[式-1]和[式-2]联立:
[0295][0296]
根据[式-2]和[式-3]得:
[0297][0298]
由两式按δy^进行联立:
[0299][0300][0301]
如上所述,位置关系导出部28能够导出(δx^,δy^)。
[0302]
如在实施例2中说明的那样,z轴方向的安装误差δz^可以利用例如安装轴41的基准面而由位置关系导出部28导出。如此,确定刀具中心的安装误差(δx^,δy^、δz^)。这样,在实施例5中,通过利用预加工面与作为目标的设计加工面的差量来确定刀具中心的安装误差(δx^,δy^、δz^),并且移动控制部30能够重新计算修正了安装误差的进给路径。
[0303]
《实施例6》
[0304]
在实施例6中,对测定刀尖11a的形状走样的方法进行说明。
[0305]
如在实施例3中说明的那样,在刀尖11a上有时存在凹凸。于是,以下示出如下的方法:测定刀尖的形状被转印到预加工面的凸凹,并根据加工面的凸凹来确定刀具刀尖的形状误差。在实施例6中,在可以推定因刀尖的形状走样以外的形状误差因素所引起的形状误差的情况下,在切削加工时未利用的移动方向的进给机构7的进给运动设为准确的动作且利用一个刃尖点而测定预加工面的形状,因此通过所推定的预加工面上的各点的位置与检测的位置的差量来确定刀具刀尖的形状误差。在实施例6中,移动控制部30利用在切削加工时未利用的移动方向的进给机构7的进给功能而使振动装置10相对于切削加工后的被切削材料6相对移动,并根据切削刀具11在至少两个位置接触时的坐标值,来确定刀具刀尖的安装误差。
[0306]
图25(a)示出加工半球面的情况。移动控制部30利用进给机构7的x轴和z轴平移方向的进给功能以及c轴旋转方向的进给功能而利用切削刀具11对被切削材料6进行加工。图25(a)示出了没有刀具中心的安装误差而以理想的进给路径进行加工的情况。需要说明的是,在存在刀具中心的安装误差的情况下,在推定刀具刀尖的形状误差之前,如实施例5中说明的那样预先测量好安装误差(δx^,δy^、δz^)为好。以下,位置关系导出部28根据与半球面的理想的预加工面的形状的偏差而推定刀尖的形状误差。
[0307]
如图25(a)所示,在该球面加工中,进行了不使切削刀具11进行b轴旋转的车削加工。参照图25(a)和(c),刀尖11a的a点的形状被转印为被切削材料6上的a点的形状,刀尖11a的b点的形状被转印为被切削材料6上的b点的形状,刀尖11a的c点的形状被转印为被切削材料6上的c点的形状。这样,在被切削材料6的从a到c的预加工面上被转印刀尖11a的从a到c的形状。
[0308]
此时,如果从a到c的形状具有理想的圆弧形状,则所加工的球面的截面具有理想的圆弧。然而,如图25(c)所示,在刀尖11a上存在凹凸的情况下,该凹凸被转印到被切削材料6的加工面上。
[0309]
图25(b)示出测定被切削材料6的球面形状的情况。移动控制部30利用进给机构7的y轴和z轴平移方向的进给功能而获取多个接触坐标值。移动控制部30在使刀具中心与c轴旋转中心一致后,不改变x位置(x=0)并使θn偏移,同时使刀尖11a朝向半球面原点方向移动,从而使其在多个点接触。通过减小θn的偏移量,能够增加接触点。位置关系导出部28通过获取多个接触点的坐标来确定x=0时的球面上的圆弧的形状。位置关系导出部28通过获取被切削材料6的实际的球面形状,能够获取与所推定的球面形状的偏差量,从而能够导出刀尖11a的走样形状。图25(d)示出θn处的球面的偏差量的检测值为δr
w,n
,但此时刀尖11a上的半径方向走样为δrn^(=-δr
w,n
)(参照图25(c))。这样,位置关系导出部28能够测定刀尖形状。
[0310]
根据实施例6,移动控制部30对切削后的被切削材料6利用在切削加工时未利用的y轴平移方向的进给功能,由此位置关系导出部28能够根据从理想形状时应该接触的位置的偏差量来确定刀尖形状的轮廓。位置关系导出部28确定刀尖形状的轮廓,由此移动控制部30能够计算加入了刀尖形状的轮廓的进给路径。或者,在推定为其他的加工误差因素小的情况下,直接以实施例6中所测定的形状误差的量修正刀具移动路径而进行最终精加工
也可。
[0311]
《实施例7》
[0312]
在实施例5中,对在切削刀具11存在安装误差的情况下导出刀具中心的安装误差(δx^,δy^、δz^)的方法进行了说明。在实施例7中,对不仅切削刀具11存在安装误差,而且在刀具的进给方向上也存在误差的情况下导出这些误差的方法进行说明。
[0313]
在实施例7中也采用:移动控制部30利用在切削加工时未利用的移动方向的进给机构7的进给功能而使振动装置10相对于切削加工后的被切削材料6相对移动,并根据切削刀具11在至少两个位置接触时的坐标值,来确定刀具刀尖的安装误差。
[0314]
图26(a)示出使切削刀具11在z轴方向移动而进行了预加工时的情况。移动控制部30利用进给机构7的z轴平移方向的进给功能和c轴旋转方向的进给功能而利用切削刀具11对被切削材料6进行加工。在该车削加工中,沿着与z轴平行的线l1进给切削刀具11,结果,由于存在实施例5中说明的刀具中心的安装误差以及z轴与c轴旋转中心不平行等理由,因此在作为目标的圆筒面产生了加工误差。附带说一下线l1,在nc机床中,线l1沿着z轴,因此以与c轴旋转中心平行为前提,计算了切削刀具11的进给路径,结果,由于z轴与c轴旋转中心实际上不平行,因此移动控制部30使刀尖11a按照作为进给路径的以实线箭头所示的路径移动。因此,制成了与目标不同形状的预加工面。
[0315]
需要说明的是,关于该平行度的误差因素,除了机床制造时的组装误差以外,还考虑了设置时、进给机构移动时、安装被切削材料时的重量分布变化引起的变形、加工力引起的变形、气温/加工热量引起的热变形等。其中,在考虑加工力引起的变形的情况下,优选为设定在预加工时和最终精加工时加工力程度相同的加工条件。
[0316]
在误差导出处理中,移动控制部30利用进给机构7的x轴平移方向、y轴平移方向以及z轴平移方向的进给功能而获取多个接触坐标值。移动控制部30导出在作为z位置的z1、z2分别使y位置变化并在x方向各移动三次时的刀尖11a的接触坐标值。通过导出三点的接触坐标值,来如在实施例5中说明的那样导出与作为理想的刀具中心位置的位置偏差量(δx^1,δy^1)、(δx^2,δy^2)。
[0317]
位置关系导出部28通过导出(δx^1,δy^1,z1)、(δx^2,δy^2,z2)而能够计算进给路径的轨道。在此,在任意的z中,将预想为对于c轴旋转中心相对地具有的位置误差设为(δx^,δy^),则有下式。
[0318]
[数学式32]
[0319][0320]
因此有下式。
[0321]
[数学式33]
[0322][0323]
需要说明的是,在此对两个z位置的位置偏差进行了线性插值,但也可以测定三个以上的z位置的位置偏差来增加插值的次数。
[0324]
这样,根据实施例7,移动控制部30对于切削后的被切削材料6利用在切削加工时
未利用的x轴和y轴平移方向的进给功能,由此位置关系导出部28能够根据与理想形状时应该接触的位置的偏差量来推定相对于c轴的切削刀具11的进给方向的平行度。在实施例7中,通过推定相对于c轴的切削刀具11的进给方向的平行度,来位置关系导出部28能够确定相对于被切削材料6的切削刀具11的相对移动方向的偏差。如上式所示,通过求出任意的z的位置误差,移动控制部30能够计算出修正了该位置误差的进给路径。
[0325]
《实施例8》
[0326]
图27示出使切削刀具11在x轴方向和z轴方向移动而对球面进行了预加工时的情况。在该车削加工中,x轴应与c轴正交,但因正交性被破坏而在球面产生了加工误差。在nc机床中,计算成为用于以x轴为基准而加工球面的线l2的进给路径,结果,由于用于刀具控制的x轴与成为被切削材料6的旋转轴的c轴的正交性被破坏,因此移动控制部30使刀尖11a按照作为进给路径以实线箭头所示的路径移动。
[0327]
在误差导出处理中,移动控制部30使刀尖11a在与某个加工点p1相对于c轴成为对称的点p2接触。根据此时的x方向的移动距离(2δx)与y方向检测值(δz)的差量,来通过以下的式子求出表示c轴与x轴间的正交度的θ^。
[0328]
[数学式34]
[0329][0330]
这样,如果表示正交度的θ^被求出,移动控制部30则计算出该θ^为0的刀具的进给路径而进行修正。
[0331]
需要说明的是,该方法也可以应用于球面以外的面(包括平面、非球面)。
[0332]
在实施例8中也移动控制部30利用在切削加工时未利用的移动方向的进给机构7的进给功能而使振动装置10相对于切削加工后的被切削材料6相对移动,并根据切削刀具11在至少两个位置接触时的坐标值,来确定刀具刀尖的安装误差。
[0333]
这样,在实施例8中,通过推定相对于c轴的x轴的正交度,来位置关系导出部28能够确定相对于被切削材料6的切削刀具11的相对移动方向的偏差量。
[0334]
《实施例9》
[0335]
在实施例5中,利用使刀尖11a与圆筒面接触时的坐标值来推定了刀具中心的安装误差(δx^,δy^、δz^)。在实施例9中,对利用使刀尖11a与预加工后的球面接触时的坐标值来推定刀具中心的安装误差(δx^,δy^、δz^)的方法进行说明。预加工后的球面可以是例如从图23所示的被切削材料6除去圆筒面后的球面。移动控制部30利用进给机构7的x轴平移方向的进给功能、z轴平移方向的进给功能以及c轴旋转方向的进给功能而利用切削刀具11对被切削材料6进行预加工。
[0336]
在实施例9所示的方法中,以使刀尖11a与位于相同的z位置的三点接触的方式对刀尖11a进行移动控制。在误差导出处理中,移动控制部30利用进给机构7的x轴平移方向、y轴平移方向以及z轴平移方向的进给功能而获取多个接触坐标值。
[0337]
图28(a)示出刀尖11a正在加工p1的情况。nc机床上的刀具中心坐标已知,为(x1,0,z1)。另外,连结工件中心oc和p1的线段相对于xy平面的角度为θ1。如果将刀尖11a的刀尖半径设为r,则也作为加工点的p1的坐标如下。
[0338]
p1:(x
1-rcosθ1,0,z
1-rsinθ1)
[0339]
如果p1的坐标被确定,则在位于与p1相同的z位置(z
1-rsinθ1)(参照图28(b))并从p1向y轴负方向位移了δy、2δy的位置(参照图28(c))上设定应要接触的p2、p3。另外,在xy面内,将连结c轴旋转中心和p1的线段与连结c轴旋转中心和p2的线段间的角度设为α,将连结c轴旋转中心和p1的线段与连结c轴旋转中心和p3的线段间的角度设为β(参照图28(b))。
[0340]
图29示出对于xy平面的、连结工件中心oc和接触点的线段的角度。其中,将与p2的线段的角度设为θ2,将与p3的线段的角度设为θ3。
[0341]
因此,如下计算用于与p2接触的刀具中心坐标(c2)、用于与p3接触的刀具中心坐标(c3)。
[0342]
c2:(x2 rcosθ2,-δy,z
1-rsinθ1 rsinθ2)
[0343]
c3:(x3 rcosθ3,-2δy,z
1-rsinθ1 rsinθ3)
[0344]
位置关系导出部28通过以下的几何学关系式来计算x2、x3、α、β、θ1、θ2、θ3。
[0345]
[数学式35]
[0346][0347]
各坐标值的原点是oc,oc是位于c轴旋转中心线上且具有与加工点的轨迹(为圆弧且在与xz面平行的平面上)的中心(在存在刀具安装误差的情况下,相应地从c轴旋转中心线偏离)相同的z坐标值的点。
[0348]
移动控制部30使刀尖11a与p2、p3接触。此时,移动控制部30使刀尖11a的中心坐标的(y,z)分别与c2、c3的上述坐标值一致,然后在x方向移动而使刀尖11a与球面接触。此时,如果以与计算值相同的x坐标值进行接触,则判定为没有中心坐标的安装误差。另一方面,如果在与计算值不同的nc机床上的刀具中心的x位置进行接触,则x方向的移动量作为误差来被检测。
[0349]
检测c2:(x2 δx2 rcosθ2,-δy,z
1-rsinθ1 rsinθ2)
[0350]
检测c3:(x3 δx3 rcosθ3,-2δy,z
1-rsinθ1 rsinθ3)
[0351]
δx2、δx3是检测值。
[0352]
根据检测值,可以按下式近似地导出p2、p3。
[0353]
检测p2:(x2 δx2,-δy,z
1-rsinθ1)
[0354]
检测p3:(x3 δx3,-2δy,z
1-rsinθ1)
[0355]
需要说明的是,就z位置的误差而言,刀具刀尖半径相对于加工面半径一般较小,
即使假设有安装误差,加工点的轨迹形状(在与xz面平行的平面上)也仅平行移动了安装误差的量,在y方向观察的曲率是准确的(在z方向观察xy截面的曲率具有误差),因此与x位置相比,z位置的偏差小。因此可以忽略z位置的偏差。
[0356]
图30(a)示出由p1、p2和p3形成的初始圆与利用从初始圆导出的误差(δx2、δx3)而形成的假想圆的关系。假想圆通过p1、检测p2、检测p3。(δx’,δy’)是假想圆的中心。
[0357]
图30(b)示出将假想圆的中心坐标还原到原点后的坐标系。此时,通过下式推定刀具安装误差(δx^,δy^)。
[0358]
(δx^,δy^)=(-δx’,-δy’)
[0359]
位置关系导出部28利用所推定出的刀具安装误差(δx^,δy^)并通过以下的几何学关系式,重新计算x2、x3、α、β、θ1(对于第一个接触点来说,保持与加工时相同,与初始的接触时没有变化。因此,与x1、z1相同地θ1也没有变化,不一定必须重新计算)、θ2、θ3。
[0360]
[数学式36]
[0361][0362]
由此导出下式。
[0363]
c2:(x
2-δx^ rcosθ2,-δy,z
1-rsinθ1 rsinθ2)
[0364]
c3:(x
3-δx^ rcosθ3,-2δy,z
1-rsinθ1 rsinθ3)
[0365]
移动控制部30利用所导出的c2、c3而使刀尖11a与新的p2、p3接触。移动控制部30使刀尖11a的中心坐标的(y,z)分别与c2、c3的上述坐标值一致,然后在x方向移动而使刀尖11a与球面接触。此时,如果以与计算值相同的中心坐标进行接触,则判定为中心坐标的安装误差的推定值没有推定误差。通过重复进行该处理,在可视为与计算值相同的中心坐标处,刀尖11a与被切削材料6的球面接触,即推定误差变得足够小,从而可以求出准确的安装误差。
[0366]
在实施例9中也采用:移动控制部30利用在切削加工时未利用的移动方向的进给机构7的进给功能而使振动装置10相对于切削加工后的被切削材料6相对移动,并根据切削刀具11在至少两个位置接触时的坐标值,来确定刀具刀尖的安装误差。
[0367]
这样,在实施例9中,通过反复计算而使预加工后的球面与作为目标的设计加工面的差量收敛,由此确定刀具中心的安装误差(δx^,δy^、δz^)。
[0368]
《实施例10》
[0369]
在实施例5~9中,对使切削刀具11不进行b轴旋转的车削加工进行了说明,在实施例10中,对使切削刀具11进行b轴旋转并且仅利用刀尖11a的一个点的加工进行说明。
[0370]
图31(a)示出在加工时刀尖11a的一个点被用于切削中的情况。在这样的加工中,如果相对于b轴中心ob的相对的刀具中心c的安装位置存在误差,则会产生加工误差。
[0371]
图31(b)是用于说明求出b轴中心ob与刀具中心c间的距离l^和初始的安装角度θ^的说明图。如图所示,移动控制部30在规定的y坐标、z坐标中将安装角度变更 δb、-δb的量而检测刀尖11a的接触点上的x坐标的增量δx1、δx2,并利用它们按下式进行计算。
[0372]
[数学式37]
[0373]
[式-1]
[0374]
[式-2]
[0375]
利用[式-1]和[式-2]而按θ^整理l^:
[0376][0377][0378]
再将l^代入[式-1]:
[0379][0380]
如上所述,求出相对于b轴旋转中心的相对的刀具中心c的安装位置,即距离l^和角度θ^。
[0381]
《实施例11》
[0382]
在实施例11中,利用基于扫描线加工的预加工面而首先识别c轴旋转中心的误差。在实施例11中也使刀尖11a与预加工面在多个点接触而导出与理想轮廓的差量,由此识别从刀具中心观察的相对的c轴旋转中心位置的误差。
[0383]
图32概念性地示出扫描线加工中的xz面内的切削进给方向和yz面内的周期进给(pick feed)方向。为了识别c轴旋转中心的误差,可以利用yz平面内的工件形状和xz平面内的工件形状。
[0384]
《利用yz平面内的工件形状》
[0385]
图33(a)示出加工时的刀尖11a的情况。在图33(a)中,虚线表示加工时的刀具中心的周期进给(pick feed)轮廓,实线表示预加工面轮廓。理想的刀具中心的周期进给轮廓和预加工面轮廓已知。
[0386]
图33(b)示出将c轴(在此,在刀具侧安装有c轴)从加工时的姿态旋转90度后使刀尖11a与预加工面在多个点接触的情况。在图33(b)中,实线表示连接接触点的接触面轮廓。
[0387]
位置关系导出部28通过数值解析来识别c轴旋转中心的y方向误差(c轴旋转后、旋转前的x方向误差),以使接触面轮廓与预加工面轮廓最为匹配。具体而言,位置关系导出部28在通过预加工面轮廓来推定出各接触位置的基础上,导出与实际接触的检测位置的误差,并以该误差的总和变为最小的方式识别c轴旋转中心坐标。
[0388]
《利用xz平面内的工件形状》
[0389]
图34(a)示出加工时的刀尖11a的情况。在图34(a)中,虚线表示加工时的刀具中心的切削运动轮廓,实线表示预加工面轮廓。理想的刀具中心的切削运动轮廓和预加工面轮廓已知。
[0390]
图34(b)示出将c轴从加工时的姿态旋转90度后使刀尖11a与预加工面在多个点接触的情况。在图34(b)中,实线表示连接接触点的接触面轮廓。
[0391]
位置关系导出部28通过数值解析来识别c轴旋转中心的x方向误差(c轴旋转后、旋转前的y方向误差),以使接触面轮廓与预加工面轮廓最为匹配。具体而言,位置关系导出部28在通过预加工面轮廓来推定出各接触位置的基础上,导出与实际接触的检测位置的误差,并以该误差的总和变为最小的方式识别c轴旋转中心坐标。
[0392]
如图33(b)或图34(b)所示,从刀具中心观察的相对的c轴旋转中心位置被识别。如果c轴旋转中心位置被识别,则利用该位置能够测定刀尖11a的形状误差。
[0393]
图35示出测定刀尖形状误差的方法。移动控制部30使c轴从加工时的姿态旋转90度而在预加工面上使刀尖11a以相同的刀尖位置接触的方式沿着曲线在多个点接触。图35表示沿着虚线所示的脊线在刀尖的z方向最低点与预加工面接触的情况。位置关系导出部28根据各接触点处的计算上的接触位置与所检测出的接触位置的偏差量来与实施例6相同地测定刀尖形状的走样。
[0394]
《实施例12》
[0395]
在实施例12中,利用基于等高线加工的预加工面来确定c轴旋转中心的误差。在此情况下,位置关系导出部28如在实施例9中说明的那样不改变c轴和z轴的位置,而是利用改变xy位置而接触的两点以上的坐标值,由此能够识别c轴旋转中心与刀尖11a的xy相对位置。
[0396]
另外,在c轴旋转位置与预加工时相差90度的姿态下,通过在相同的刀尖位置接触的曲线上进行多点接触,能够测定刀具刀尖的形状误差。另外,如在实施例7中说明的那样,改变z位置而在c轴旋转位置与预加工时相差90度的姿态下进行两点以上的接触,据此能够识别c轴旋转中心与z轴的平行度(倾斜)。
[0397]
《实施例13》
[0398]
在实施例13中,对利用转印了直线切削刃的加工面而识别刀具的安装角度和b轴旋转中心位置的方法进行说明。
[0399]
图36示出作为直线切削刃的刀尖11a正在进行加工的情况。以下,对识别由刀具的安装角度决定的已加工面的微细沟槽的主要倾斜面的倾斜b轴旋转中心与刀尖前端的距离l^、相对于z轴的倾斜β^的方法进行说明。倾斜是以从-x轴开始逆时针旋转为正的角度,倾斜β^是从-z轴开始的角度。
[0400]
图37是用于说明识别方法的图。移动控制部30使刀尖11a以任意的角度θ1与预加工面在p1接触,并检测作为p1的z位置的z1。移动控制部30保持相同的姿态下使刀尖11a在与预加工面偏移了dx的p2接触,并检测作为p2的z位置的z2。
[0401]
由此,如果设dz=z
2-z1,则可按下式计算。
[0402]
[0403]
在该倾斜角度与目标形状的倾斜角度偏离的情况下,通过利用b轴修正该差量来能够在最终精加工中进行具有更准确的倾斜面的微细沟槽加工。
[0404]
图38是用于说明坐标变换的图。
[0405]
刀尖前端点与b轴旋转中心的相对关系表示如下。
[0406]
[数学式38]
[0407][0408]
为了使切削位置的z坐标为0,利用变换坐标系后如下。
[0409]
[数学式39]
[0410][0411]
图39(a)(b)分别示出使刀尖11a的姿态变化而与预加工面接触的状态。
[0412]
图39(a)示出在使b轴旋转了θ1的状态下使刀尖11a在与倾斜垂直的方向(与z’轴平行)移动而与预加工面接触的状态。图39(b)示出在使b轴旋转了θ2的状态下使刀尖11a在与倾斜垂直的方向(与z’轴平行)移动而与预加工面接触的状态。θ1、θ2以逆时针旋转的角度为正。此时,作为z值,分别检测出z
’1和z
’2。
[0413]
于是,有以下关系成立。
[0414]
[数学式40]
[0415][0416][0417]
需要说明的是,x’1
、x’2
是适当的偏移量,也可以不偏移。
[0418]
上述两个接触点的z’坐标按下式求出。
[0419]
[数学式41]
[0420][0421][0422]
联立求解后,有下式。
[0423]
[数学式42]
[0424][0425]
因此,
[0426]
[数学式43]
[0427][0428][0429]
因此,按以下方式计算。
[0430]
[数学式44]
[0431][0432]
从计算出:
[0433][0434][0435]
这样,根据实施例13,在转印了直线切削刃的加工面上通过使刀尖11a在多个点接触,能够导出b轴旋转中心。这样,例如像在自由曲面上形成微细沟槽的复杂形状那样,为了微细沟槽的倾斜面的角度发生变化而需要使b轴旋转后进行加工的情况下,通过获知准确的b轴旋转中心,能够防止刀具刀尖的xy位置偏离而加工精度降低(如果相对于刀具刀尖位置的相对的b轴旋转中心位置存在误差,则因b轴旋转而导致刀具刀尖的xy位置产生误差)的情况。
[0436]
以上,基于实施例对本公开进行了说明。本领域的技术人员应当理解,该实施例是示例,这些各构成要素和各处理过程的组合可以有各种变形例,并且这些变形例也包含在本公开的范围内。
[0437]
本公开的实施方式的概要如下。本公开的一个实施方式的振动切削装置具备:振动装置,安装有切削刀具,并包括产生振动的致动器;移动控制部,对使振动装置相对于对象物(例如被切削材料、安装有被切削材料的部件或具有已知形状的物体)相对移动的进给机构进行控制;以及振动控制部,对振动装置的致动器的振动进行控制。振动控制部具有:获取表示振动的控制状况的状况值并根据状况值的变化来检测切削刀具与对象物的接触的功能。根据该方式,振动控制部基于振动控制状况值的变化来检测切削刀具与被切削材料的接触,因此不需要另外搭载用于检测接触的传感器等。
[0438]
振动控制部可以将振动所需的能量消耗以及共振频率中的至少一个作为状况值来获取。振动控制部可以将挠曲振动所需的功率消耗作为状况值来获取。另外,振动控制部优选地确定接触位置。
[0439]
本公开的另一个实施方式的振动切削装置具备:振动装置,安装有切削刀具,并包
括产生振动的致动器;以及控制部,对使振动装置相对于被切削材料或部件相对移动的进给机构进行控制。控制部具有:对进给机构进行控制而使振动装置相对移动,从而获取切削刀具与被切削材料或部件接触时的坐标值的功能。控制部根据切削刀具在与车削加工时的切削刀具的旋转角度位置不同的至少两个位置与基准面接触时的坐标值来确定切削刀具与被切削材料的旋转中心的相对位置关系,其中,基准面与车削加工后的被切削材料或与被切削材料的旋转中心的相对位置关系是已知的。控制部根据两个以上的接触位置的坐标值来确定切削刀具与被切削材料的旋转中心的相对位置关系,因此不需要另外搭载用于测定位置关系的测定器等。
[0440]
本公开的另一个实施方式的振动切削装置具备:振动装置,安装有切削刀具,并包括产生振动的致动器;以及控制部,对使振动装置相对于被切削材料或部件相对移动的进给机构进行控制。控制部具有:对进给机构进行控制而使振动装置相对移动,从而获取切削刀具与被切削材料或部件接触时的坐标值的功能。控制部根据基准面上的接触位置的坐标值来确定切削刀具与被切削材料的安装面、被切削材料的进给运动方向、被切削材料的旋转中心中的至少一方的相对位置关系,其中,基准面与被切削材料的安装面、被切削材料的进给运动方向、被切削材料的旋转中心中的至少一方的相对位置关系是已知的。需要说明的是,被切削材料的直线进给运动及其周围的旋转运动在空间内各有三个方向,但在振动切削装置中,被切削材料的运动是与切削刀具之间的相对运动,也可以被切削材料的位置被固定而切削刀具侧运动。利用相对位置关系已知的基准面而使刀具刀尖与基准面接触,据此能够确定相对位置关系。
[0441]
本公开的另一个实施方式的振动切削装置具备:振动装置,安装有切削刀具,并包括产生振动的致动器;以及控制部,对使振动装置相对于对象物相对移动的进给机构进行控制。控制部具有:对进给机构进行控制而使振动装置相对于具有已知形状的物体相对移动,从而获取切削刀具的刀尖与物体的已知形状部分接触时的坐标值的功能。控制部根据切削刀具的刀尖在物体的已知形状部分的至少三个位置接触时的坐标值来确定与切削刀具的刀尖相关的信息。控制部通过利用与物体的已知形状部分的三个以上的接触位置的坐标值来能够确定与切削刀具的安装位置相关的信息。控制部可以将刀具刀尖的刀尖半径、刀具刀尖的中心坐标、刀具刀尖的形状误差中的至少一个作为与安装位置相关的信息来求出。
[0442]
本公开的另一个实施方式的振动切削装置具备:振动装置,安装有切削刀具,并包括产生振动的致动器;以及控制部,对使振动装置相对于被切削材料相对移动的进给机构进行控制。控制部具有:对进给机构进行控制而使振动装置相对移动,从而获取切削刀具与被切削材料接触时的坐标值的功能。控制部根据利用在切削加工时未利用的移动方向的进给机构的进给功能而使振动装置相对于切削加工后的被切削材料相对移动,根据切削刀具在至少两个位置接触时的坐标值,来可以确定切削刀具的安装误差、刀具刀尖的形状误差、切削刀具相对于被切削材料的相对移动方向的偏差中的至少一个。控制部通过确定切削加工后的被切削材料的形状与理想切削加工后的被切削材料的形状的差量,能够确定切削刀具的安装误差、刀具刀尖的形状误差、切削刀具相对于被切削材料的相对移动方向的偏差中的至少一个。
[0443]
控制部对振动装置的致动器的振动进行控制。控制部可以获取表示振动的控制状
况的状况值,并基于状况值的变化来检测切削刀具与被切削材料或基准面的接触。
[0444]
(附图标记说明)
[0445]
1:振动切削装置;6:被切削材料;7:进给机构;10:振动装置;11:切削刀具;
[0446]
12l、12b:压电元件;20:控制部;21:振动控制部;22:驱动控制部;
[0447]
23l、23b:放大器;24:相移部;25:电压振荡部;26:相位检测部;
[0448]
27:监视部;28:位置关系导出部;30:移动控制部
[0449]
(工业实用性)
[0450]
本公开可利用于在使刀具振动的同时对被切削材料(工件)进行切削的振动切削装置。
再多了解一些
本文用于企业家、创业者技术爱好者查询,结果仅供参考。