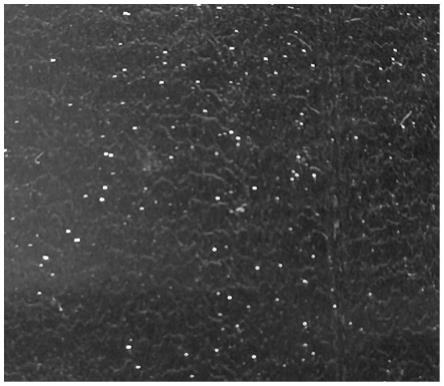
1.本发明涉及磁性功能材料领域中的软磁材料研究领域,特别涉及一种具有良好表面质量的非晶纳米晶合金带材及其制造方法。
背景技术:
2.非晶纳米晶合金是近年来迅速发展起来的一类软磁材料,与传统的电工钢、铁氧体等软磁材料相比具有更高的磁导率、更低的交流损耗,已经广泛应用于变压器、电感器、互感器、电机定子等磁性元器件中的铁芯。在用于变压器、电感器、互感器、电机定子等场合时,一般是将厚度仅有约0.025mm左右的非晶纳米晶合金带材卷绕或堆叠成铁芯。对于宽度在50mm以上的带材,经常首先将其分剪成窄条,然后再进行铁心卷绕等。
3.非晶纳米晶带材一般采用平面流技术制造,其方法是:将一定配比的原料用冶炼炉熔化成合金液;然后,将合金液浇入底部带有狭缝喷嘴的喷嘴包中;喷嘴包中的合金液从喷嘴中流出,铺展在喷嘴下方的高速旋转的铜合金冷却辊外圆周表面,并在冷却辊表面与喷嘴底面之间形成一定尺寸的合金液熔潭,合金液迅速地被抽出并快速冷却,同时喷嘴缝中的合金液持续补充到熔潭中,从而形成具有非晶或纳米晶结构的连续薄带。薄带紧贴冷却辊外表面随冷却辊高速旋转,并在冷却辊外表面的适当位置由高压气体或机械装置剥离,最后由卷取装置将薄带卷绕成卷。
4.对于用平面流技术制造非晶纳米晶合金带材,其贴辊面有时存在麻点缺陷,即:在带材的部分区域,存在一些肉眼可见的点状缺陷,如图1,图1示出了现有技术中用平面流技术制造非晶纳米晶合金带材时带材贴辊面的麻点示意图。在显微镜下观察,可以发现这种缺陷有各种形状,如长条形、多边形及其它不规则形状,而大多为拖有长尾的近似l形,其尾部的长度可达50~500μm左右,如图2,图2示出了现有技术中用平面流技术制造非晶纳米晶合金带材时带材贴辊面麻点的微观形貌示意图。这种麻点既可能高出带材表面,也可能低于带材表面。如果这种麻点高出带材表面,则会明显降低后续加工的铁心的叠片系数;如果这种麻点低于带材表面,则会因未能贴辊而局部冷却不足,造成局部脆点,成为带材在加工过程中的断裂源。此外,带材的麻点还容易引起带材生产过程中断带,中断带材的卷取,严重降低生产效率。
5.中国专利cn103155054b公开了一种铁磁非晶合金带材,在贴辊面具有高度3μm以上的突起,并通过调整合金液的表面张力减少表面凸起的数量。然而,合金液表面张力只能通过合金液成分、温度、环境气氛等手段调节,过于繁复;而且,这种方法并未从根源上彻底消除带材表面凸起的形成原因——辊面缺陷。
6.中国专利cn1116137c披露了一种制造非晶微晶合金带材用的冷却辊套材料,其采用铜合金制成,其平均晶粒尺寸小于200μm,并且没有尺寸大于500μm的晶粒,晶粒尺寸具有紧凑的高斯分布,其目的是通过改善辊套材料的微观结构和力学性能来减少辊面缺陷的产生。然而,该专利对于如何在非晶合金带材生产工艺上减少辊面缺陷没有提出改善措施。
7.总之,非晶纳米晶带材的贴辊面麻点缺陷对带材质量和韧性有明显的不利影响,
但现有技术主要从改善辊套材料质量和合金液特性方面采取措施,而在非晶合金带材生产工艺方面尚无较好的解决方法。
技术实现要素:
8.针对上述问题,本发明提出一种非晶纳米晶合金带材,所述方法包括以下步骤:
9.将一定配比的原料用冶炼炉熔化成合金液;
10.将合金液浇入底部带有喷嘴的喷嘴包中;
11.合金液从喷嘴中流出,铺展在喷嘴下方的高速旋转的冷却辊外圆周表面,进入熔潭之前的冷却辊外圆周表面温度控制在70~150℃;
12.并快速冷却形成具有非晶或纳米晶结构的连续薄带,带材在剥离冷却辊外圆周表面时的剥离温度范围控制在120~200℃。
13.进一步的,所述进入熔潭之前的冷却辊外圆周表面温度控制在90~120℃。
14.进一步的,所述带材在剥离冷却辊外圆周表面时的剥离温度控制在140~180℃。
15.进一步的,所述冷却辊外圆周表面采用砂纸轮、砂布轮、金属毛刷轮或含有研磨颗粒的树脂毛刷轮对其进行修磨,并且使冷却辊外圆周表面粗糙度ra不大于0.5μm。
16.本发明还提供一种非晶纳米晶合金带材,所述带材贴辊面上长度大于100μm的麻点的密度不大于每100cm2十个。
17.进一步的,所述带材贴辊面上长度大于100μm的麻点的密度不大于每100cm2两个。
18.进一步的,所述非晶纳米晶合金带材主要成分具有如下的一般表达式:
19.xaybzc20.x为金属元素,总含量a在65~85at%之间;y为过渡金属元素,总含量b在0~10at%之间;z为非晶形成元素,总含量c在15~30at%之间,此外,合金中还含有总量不超过0.5at%的杂质元素。
21.进一步的,x为铁磁性金属元素。
22.进一步的,x包括fe、co、ni中的至少一种。
23.进一步的,y包括ti、zr、hf、v、nb、ta、cr、mo、w、mn、cu、ag、au、zn、及al、sn中的至少一种。
24.进一步的,z包括si、b、p、c中的至少一种。
25.进一步的,所述带材宽度为50~300mm,厚度为10~50μm。
26.本发明还提供一种铁芯,所述铁芯包含本发明的带材。
27.本发明还提供一种磁性元器件,磁性元器件包含所述铁芯,所述磁性元器件包括:变压器、电感器、互感器和电机定子。
28.本发明通过控制辊面温度范围和带材剥离温度范围,减小了热应力的变化幅度,有效地减轻了热疲劳程度,从而减轻了裂纹的产生和扩展,减小了带材收缩应力减少了辊面材料剥落,最终减少了带材贴辊面的麻点。
29.本发明的其它特征和优点将在随后的说明书中阐述,并且,部分地从说明书中变得显而易见,或者通过实施本发明而了解。本发明的目的和其他优点可通过在说明书、权利要求书以及附图中所指出的结构来实现和获得。
附图说明
30.为了更清楚地说明本发明实施例或现有技术中的技术方案,下面将对实施例或现有技术描述中所需要使用的附图作一简单地介绍,显而易见地,下面描述中的附图是本发明的一些实施例,对于本领域普通技术人员来讲,在不付出创造性劳动的前提下,还可以根据这些附图获得其他的附图。
31.图1示出了现有技术中用平面流技术制造非晶纳米晶合金带材时带材贴辊面的麻点示意图;
32.图2示出了现有技术中用平面流技术制造非晶纳米晶合金带材时带材贴辊面麻点的微观形貌示意图。
具体实施方式
33.为使本发明实施例的目的、技术方案和优点更加清楚,下面将结合本发明实施例中的附图,对本发明实施例中的技术方案进行清楚、完整地说明,显然,所描述的实施例是本发明一部分实施例,而不是全部的实施例。基于本发明中的实施例,本领域普通技术人员在没有做出创造性劳动前提下所获得的所有其他实施例,都属于本发明保护的范围。
34.在用平面流技术制造非晶纳米晶合金带材时,所制造的带材的贴辊面有时存在麻点,即:在带材的部分区域,存在一些肉眼可见的点状缺陷(简称麻点)。这种麻点缺陷在显微镜下为不规则形状,其尺寸约为50~500μm左右,既可能高出带材表面,也有可能低于带材表面。这种麻点如果高出带材表面,则会明显降低后续加工的铁心的叠片系数;这种麻点如果低于带材表面,则会因未能贴辊而局部冷却不足,造成局部脆点,成为带材的断裂源。
35.经过发明人的研究,发现带材贴辊面麻点是由冷却辊表面缺陷引起的。
36.一方面,在非晶纳米晶带材制备过程中,约1300℃的合金液与仅有100℃左右的冷却辊表面的某一点接触时,该点会急剧升温。随后,随着冷却辊的转动,该点移出熔潭,由于合金液即带材所携带的热量被迅速向冷却辊内部传导,使该点又快速冷却降温。在冷却辊转动一周后,该点再次与合金液接触,再一次承受“急剧升温-快速降温”的过程。因此,辊面材料受到了周期性的冷热循环作用。由于辊套材料的热胀冷缩特性,辊套外层材料的内部会受到周期性的“压应力-拉应力”循环交替作用。
37.另一方面,冷却辊表面虽然经过预先的修磨,并且在带材制备过程中持续不断地打磨,但表面始终存在一些打磨纹路。这些纹路实际上是具有一定深度的纵向(带材长度方向)或斜向沟槽。这些沟槽在周期性的“压应力-拉应力”循环交替作用下,会由于应力集中效应而产生微小的裂纹并不断扩展。这个过程称为热疲劳。
38.随着热疲劳的不断持续,疲劳裂纹不断扩展,裂纹附近的表面辊套材料发生松动,在带材的粘附作用下,疲劳裂纹附近部位的辊套材料在松动后会随带材一起被从辊面剥落,使辊面形成凹坑。当辊面上的凹坑部位再次接触合金液时,如果合金液进入到凹坑内部,则带材的相应部位会产生凸起状的麻点。如果凹坑内部存留有气体或其它污染物,则带材的相应部位会形成凹下的麻点,并且该部位带材的冷却速率会严重降低,产生局部脆性甚至局部晶化。总之,带材贴辊面麻点的产生原因是:辊面层因热疲劳产生裂纹,继而产生局部的材料松动和局部剥落,形成辊面凹坑,使带材的对应位置产生高出或低于带材表面的缺陷。
39.因此,为了减少麻点的产生,除了现有技术从辊套材料质量方面采取改进措施以外,需要从带材生产工艺上采取配套措施,以减轻辊面因热疲劳导致的辊套材料剥落。本发明通过控制非晶纳米晶带材生产过程中的辊面温度和带材剥离温度来减小辊套表面热应力和带材收缩,从而减轻辊面缺陷和带材麻点的产生。
40.具体地,一方面是控制辊面温度,使进入熔潭之前的冷却辊外表面温度控制在70~150℃之间;优选地,冷却辊表面温度控制在90~120℃之间。辊面温度的调节可通过改变冷却辊内部冷却水的温度和/或流量、冷却辊套材料的导热率、冷却辊套的厚度等措施来实现。
41.另一方面是将带材在剥离冷却辊表面时的温度(剥离温度)控制在120~200℃之间;优选地,带材的剥离温度控制在140~180℃之间。剥离温度的调节通过改变带材剥离点的位置(即带材与辊面的接触长度)、冷却辊套材料的导热率、冷却辊套的厚度等措施来实现。
42.本发明通过对辊面温度和带材剥离温度的控制,减小了辊面的热应力变化幅度,有效地减轻了热疲劳程度,从而减轻了裂纹的产生和扩展,减少了辊面材料剥落,最终减少了带材贴辊面麻点,本发明的目的是提供一种具有良好表面质量的非晶纳米晶合金带材及其制造方法,将带材贴辊面上长度大于100μm的麻点的密度减少到每100cm2不多于10个,进而改善带材的表面质量。
43.本发明还提供一种非晶纳米晶合金带材制造方法,本发明的非晶纳米晶合金带材采用平面流快速凝固工艺制造。
44.本发明所采用的原料均为工业级纯单质或者合金。
45.首先,将一定配比的原料用冶炼炉熔化成合金液。
46.具体的,本发明的非晶纳米晶合金带材的主要成分具有如下的一般表达式:
47.xaybzc48.其中,x为金属元素,总含量a在65~85at%之间,具体的,x为铁磁性金属元素,x包括fe、co、ni中的至少一种,本发明实施例中只是通过fe、co、ni进行举例说明,实际操作过程中并不仅限于这几种元素,其他金属元素均在本发明的保护范围之内;
49.y为过渡金属元素,总含量b在0~10at%之间,具体的,y包括ti、zr、hf、v、nb、ta、cr、mo、w、mn、cu、ag、au、zn、及al、sn中的至少一种,本发明实施例中只是通过ti、zr、hf、v、nb、ta、cr、mo、w、mn、cu、ag、au、zn、al、sn进行举例说明,实际操作过程中并不仅限于这几种元素,其他过渡金属元素均在本发明的保护范围之内;
50.z为非晶形成元素,总含量c在15~30at%之间,具体的,z包括si、b、p、c中的至少一种,本发明实施例中只是通过si、b、p、c进行举例说明,实际操作过程中并不仅限于这几种元素,其他非晶形成元素均在本发明的保护范围之内。
51.此外,合金中还可含有总量不超过0.5at%的杂质元素。
52.冶炼好的合金液可浇入中间包进行温度调节及生产节奏缓冲。在小规模或实验室制备带材时也可省去中间包。
53.然后,将合金液浇入底部带有狭缝喷嘴的喷嘴包中。喷嘴包中的合金液从喷嘴中流出,铺展在喷嘴下方的高速旋转的铜合金冷却辊外圆周表面,并迅速地被冷却而形成具有非晶或纳米晶结构的连续薄带。
54.喷嘴包中合金液的温度在1250~1450℃之间;更优选地,该温度在1300~1420℃之间。
55.喷嘴包底部带有一条狭缝喷嘴,其宽度在0.2~0.5mm之间。
56.喷嘴处合金液的静压力在20~50kpa之间;更优选地,在25~40kpa之间。
57.喷嘴下方设置一只高速旋转的、具有铜合金外圆周表面的冷却辊,其表面线速度在15~30m/s之间。冷却辊的内部可用流动液体(如水)冷却。
58.喷嘴底部边缘与冷却辊表面之间的距离(辊嘴间距)在0.1~0.7mm之间。
59.冷却辊外圆周表面预先经过加工,使其表面粗糙度ra不大于0.5μm。
60.喷嘴与冷却辊表面之间的空间用ar、n2、co或co2等的至少一种或者其混合气体进行气氛保护,以防止合金液氧化、减少空气裹入、调节熔潭中的合金液温度等。
61.用砂纸(布)轮、金属毛刷轮或含有研磨颗粒的树脂毛刷轮对冷却辊表面连续修磨,以去除表面积累的残余物,并且使其表面粗糙度ra不大于0.5μm。
62.进入熔潭之前的冷却辊外表面温度控制在70~150℃之间。优选地,冷却辊表面温度控制在90~120℃之间。如果辊面温度过低,则一方面会增大辊套表面层的热疲劳应力的波动幅度,加剧辊面微观裂纹的产生和扩展;另一方面也会使带材在冷却过程中的收缩应力过大,容易发生较大幅度的收缩,并将因热疲劳而产生的辊面局部松动材料从辊面撕扯掉,形成辊面缺陷。但如果辊面温度过高,则会严重影响带材的冷却速率、使带材脆化,甚至会使带材发生晶化。辊面温度的调节可通过改变冷却辊内部冷却水的温度和/或流量、冷却辊套材料的导热率、冷却辊套的厚度等措施来实现。
63.带材在剥离冷却辊表面时的温度(剥离温度)控制在120~200℃之间。优选地,带材的剥离温度控制在140~180℃之间。如果带材剥离温度过低,则会使带材在冷却过程中的收缩应力过大,容易发生较大幅度的收缩,并将因热疲劳而产生的辊面局部松动材料从辊面撕扯掉,形成辊面缺陷。但如果剥离温度过高,则会使带材在卷取成卷后温度过高而脆化,甚至发生晶化。剥离温度的调节通过改变带材剥离点的位置(即带材与辊面的接触长度)、冷却辊套材料的导热率、冷却辊套的厚度等措施来实现。
64.用本发明的方法,所制造的非晶纳米晶带材具有良好的表面质量,其贴辊面上长度大于100μm的麻点的密度不大于每100cm2十个。优选地,其贴辊面上长度大于100μm的麻点的密度不大于每100cm2两个,所制造非晶纳米晶合金带材的宽度为50~300mm,厚度为10~50μm。
65.具体的,本发明的高叠片系数非晶纳米晶合金带材可应用于各种电力或电子变压器类磁性元器件。例如:变压器、电感器、互感器、电机定子等场合。
66.为了进一步说明采用本发明的制备方法制备出的非晶纳米晶带材表面质量良好,本发明实施例中还设置了多个实施例和比较例予以说明。
67.用工业纯的原料冶炼不同成分的母合金液。用平面流技术制造不同宽度和厚度的铁基非晶合金及纳米晶合金带材。表1为制造带材所采用的工艺参数,其中,合金液温度用热电偶连续测量;喷嘴处合金液压力用合金液在喷嘴包中的液位高度换算;辊面温度和带材剥离温度用红外测温仪或热成像仪连续测量,其中辊面温度测量点为带材铸造反方向四分之一圆周处辊面的制带中间位置,带材剥离温度测量点为带材从辊面脱离点的宽度中间位置;辊面粗糙度ra用粗糙度测试仪测量。为了获得本发明所希望的带材,分别对辊面温
度、带材剥离温度等参数进行设置。作为对比,还分别设置了不符合本发明范围的工艺参数作为比较例。
68.表1
[0069][0070][0071]
用金相显微镜观察和测量各实施例和比较例炉次制带贴辊面麻点的长度及其密度。测量数据见表2。可以看出,当采用本发明所规定的技术方案时,带材贴辊面上的麻点密度可达到本发明的目的。
[0072]
表2
[0073][0074]
对比实施例1与比较例1,在合金液原料冶炼成分相同、喷嘴包合金液温度、喷嘴处合金液压力、冷却辊表面线速度均一致的情况下,同时在满足冷却辊表面粗糙度ra不大于0.5μm,实施例1中,进入熔潭之前的冷却辊外圆周表面温度控制在90~120℃,具体为95℃,带材在剥离冷却辊外圆周表面时的剥离温度控制在140~180℃,具体为155℃,比较例1中,进入熔潭之前的冷却辊外圆周表面温度控制在90~120℃,具体为97℃,带材在剥离冷却辊外圆周表面时的剥离温度控制在132℃,不在本发明实施例中的范围之内,制带结束后,实施例1与比较例1的带材的宽度均保持在143mm,实施例1中带材厚度为24μm,比较例中带材厚度为25μm,分别观察实施例1和比较例1所制备带材每100cm2面积中的麻点数量,实施例1中,每100cm2面积中长度大于100μm的麻点数量为1,而比较例1中每100cm2面积中长度大于100μm的麻点数量为25。综上,在只满足进入熔潭之前的冷却辊外圆周表面温度在本发明的实施例温度范围内,而将带材在剥离冷却辊外圆周表面时的剥离温度脱离本发明实施例中的温度范围,不能够得到表面质量和韧性良好的带材,本发明实施例1制备方法制备出的带材,减小了热应力的变化幅度,有效地减轻了热疲劳程度,从而减轻了裂纹的产生和扩展,减小了带材收缩应力减少了辊面材料剥落,最终减少了带材贴辊面的麻点。
[0075]
对比实施例3与比较例2,在合金液原料冶炼成分相同、喷嘴包合金液温度、喷嘴处合金液压力、冷却辊表面线速度均一致的情况下,同时在满足冷却辊表面粗糙度ra不大于0.5μm,实施例3中,进入熔潭之前的冷却辊外圆周表面温度控制在90~120℃,具体为101℃,带材在剥离冷却辊外圆周表面时的剥离温度控制在140~180℃,具体为171℃,比较例2中,进入熔潭之前的冷却辊外圆周表面温度控制在65℃,不在本发明实施例中的范围之内,带材在剥离冷却辊外圆周表面时的剥离温度控制在140~180℃,具体为164℃,制带结束后,实施例3与比较例2的带材的宽度均保持在213mm,厚度均为29μm,分别观察实施例3和比较例2所制备带材每100cm2面积中的麻点数量,实施例3中,每100cm2面积中长度大于100μm的麻点数量为2,而比较例2中每100cm2面积中长度大于100μm的麻点数量为18。综上,在只满足带材在剥离冷却辊外圆周表面时的剥离温度控制在本发明的实施例温度范围内,而将进入熔潭之前的冷却辊外圆周表面温度脱离本发明实施例中的温度范围,不能够得到表面质量和韧性良好的带材,本发明实施例3制备方法制备出的带材,减小了热应力的变化幅度,有效地减轻了热疲劳程度,从而减轻了裂纹的产生和扩展,减小了带材收缩应力减少了辊面材料剥落,最终减少了带材贴辊面的麻点。
[0076]
对比实施例4与比较例3,在合金液原料冶炼成分相同、喷嘴包合金液温度、喷嘴处合金液压力、冷却辊表面线速度均一致的情况下,同时在满足冷却辊表面粗糙度ra不大于0.5μm,实施例4中,进入熔潭之前的冷却辊外圆周表面温度控制在90~120℃,具体为99℃,带材在剥离冷却辊外圆周表面时的剥离温度控制在140~180℃,具体为168℃,比较例3中,进入熔潭之前的冷却辊外圆周表面温度控制在59℃,不在本发明实施例中的范围之内,带材在剥离冷却辊外圆周表面时的剥离温度控制在127℃,不在本发明实施例中的范围之内,制带结束后,实施例4与比较例3的带材的宽度均保持在120mm,实施例4和比较例3中带材厚度均为18μm,分别观察实施例4和比较例3所制备带材每100cm2面积中的麻点数量,实施例4中,每100cm2面积中长度大于100μm的麻点数量为0,而比较例3中每100cm2面积中长度大于100μm的麻点数量为22。综上,带材在剥离冷却辊外圆周表面时的剥离温度脱离本发明实施例中的温度范围140~180℃,进入熔潭之前的冷却辊外圆周表面温度脱离本发明实施例中的温度范围90~120℃,不能够得到表面质量和韧性良好的带材,本发明实施例4制备方法制备出的带材,减小了热应力的变化幅度,有效地减轻了热疲劳程度,从而减轻了裂纹的产生和扩展,减小了带材收缩应力减少了辊面材料剥落,最终减少了带材贴辊面的麻点。
[0077]
实施例2中,即便带材的合金液原料冶炼成分与实施例1、实施例3、实施例4不同,但实施例2与实施例1、实施例3、实施例4相比,同时在满足冷却辊表面粗糙度ra不大于0.5μm,在满足进入熔潭之前的冷却辊外圆周表面温度控制在90~120℃之间,带材在剥离冷却辊外圆周表面时的剥离温度控制在140~180℃之间,可以得到表面质量良好的带材。
[0078]
尽管参照前述实施例对本发明进行了详细的说明,本领域的普通技术人员应当理解:其依然可以对前述各实施例所记载的技术方案进行修改,或者对其中部分技术特征进行等同替换;而这些修改或者替换,并不使相应技术方案的本质脱离本发明各实施例技术方案的精神和范围。
再多了解一些
本文用于企业家、创业者技术爱好者查询,结果仅供参考。