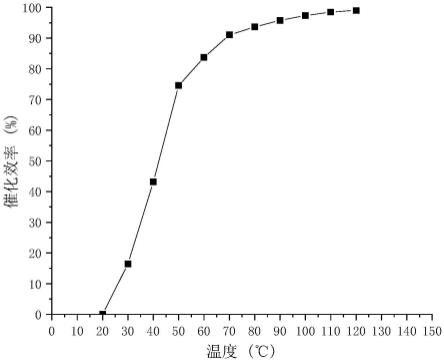
1.本发明涉及co催化领域,具体而言,涉及一种蜂窝体成型催化剂及其制备方法、应用。
背景技术:
2.钢铁烧结烟气co含量高,通常浓度可达6000~20000ppm(7500~25000mg/m3),但目前尚未有具体净化手段或明确环保指标及监管措施对烧结烟气co进行减排管控。烟气co直接排空,导致钢厂内部及相关区域环境大气中co浓度水平普遍偏高。co是剧毒气体,当空气中co含量达到12000ppm时,会在1~3min内致人死亡。国家《工业企业设计卫生标准》(tj 36~1979)中要求居住区大气中有害物质的最高co容许浓度为3.00mg/m3(2.4ppm,一次值);《职业性接触毒物危害程度分级》(gbz230~2010)中职业接触限值最高co容许浓度为20mg/m3(16ppm)。
3.开发针对烧结烟气中co的高效净化脱除技术较为迫切。烧结烟气流量大(100~200万nm3/h)、温度较低(50~130℃)、湿度高(rh》90%),成分复杂,高效且适配的co净化技术有限。在众多方法中,基于促进co与烟气中o2(浓度约15%)反应转化形成co2原理的低温催化氧化法因净化效率高、操作温度低、易于操作和环境友好等特点而备受青睐。然而,催化剂的长期应用实践证实,较低操作温度会造成较低催化效率,高湿度则会导致常见贵金属基或非贵金属基催化剂严重失活,复杂烟气成分亦会进一步加剧催化剂的失活速率。此外,大流量烟气会在有限催化剂填装占地空间条件下引起较大的风阻,提高风机能耗;对应较高速气流的长期冲击则会引起成型催化剂粉化,被吹入管路中造成堵塞问题。因此,在烧结烟气严苛条件下保持催化剂催化活性及机械性能的长期稳定,并同时兼顾解决能耗、占地、管路堵塞等工程问题,成为当前烧结烟气co低温催化氧化技术应用所面临的最大挑战。
4.在一氧化碳的选择性氧化反应中,研究较多的催化剂有金、铂和铑等贵金属体系,但由于储量有限和成本较高限制了此类催化剂的发展。目前广泛用于净化co净化的主要由霍加拉特颗粒催化剂与铂、钯等贵金属整体式催化剂。霍加拉特催化剂极其怕水,使用时需要配用大量干燥剂;铂、钯贵金属整体式催化剂具有较好的抗水性,但是成本高,使用温度一般需要300℃以上,且贵金属易烧结失活。该类催化剂具有优异的催化活性及稳定性,但是价格昂贵;非贵金属一氧化碳催化剂主要为霍加拉特剂,矿井避难洞室以及其他密闭空间普遍采用将大量霍加拉特催化剂放在通风管道中的方式进行一氧化碳气体净化,这种净化方式对一氧化碳净化效率极低、并造成催化剂浪费。因此研究一种用于一氧化碳净化的非贵金属整体式催化剂具有重要社会意义。
5.此外,传统co氧化催化剂载体均为粉末颗粒,使得催化剂的存在如下缺点(1)装卸麻烦;(2)不易成型且机械强度不能达到要求;(3)传质传热受阻很大,降低处理效率;(4)催化剂床层前后压降相差大,增加能耗。
6.有鉴于此,特提出本发明。
技术实现要素:
7.本发明的第一目的在于提供一种蜂窝体成型催化剂,该蜂窝体成型催化剂为整体床蜂窝结构的催化剂,克服了采用传统颗粒物状催化剂所造成的诸多缺陷(气流压阻大、所需鼓风机能耗高、催化剂颗粒机械强度不够易导致粉化等),稳定性以及催化效果均比较优异。
8.本发明的第二目的在于提供上述蜂窝体成型催化剂的制备方法,该制备方法通过多段焙烧以及多段干燥的方式,显著提高了催化剂稳定性、抗压性,以及催化剂本身的催化效果。
9.为了实现本发明的上述目的,特采用以下技术方案:
10.本发明提供了一种蜂窝体成型催化剂,主要由氧化锰、氧化铜为主要成分,其他金属氧化物为辅助成分制备得到;其中所述氧化铜、氧化锰以及其他金属氧化物之间的质量比为(5~50):(50~90):(1~10)。
11.上述催化剂属于整体式催化剂,克服了现有技术中的颗粒结构催化剂存在的诸多缺陷,并通过对催化剂活性成分的有效配比,提高了催化剂的催化效果。
12.优选地,本发明的蜂窝体成型催化剂中,其他金属氧化物可包括氧化铈、氧化锡、氧化钴、氧化镧、氧化镨、氧化钐、氧化铕、氧化钆、氧化钾、氧化钙、氧化锌、氧化镁以及氧化镍中的任意一种或几种。上述金属氧化物通过与氧化锰、氧化铜等主要成分的配合提高了整体催化剂的催化效果。
13.为了解决颗粒状催化剂在使用中的问题,优化非均相催化反应,本发明提供了一种整体式催化剂,该类型催化剂兼有催化剂和反应器两者的性能与特点,相比于颗粒状催化剂有如下优点:1)催化剂床层局部孔隙率呈均匀分布;2)催化剂床层的压降低;3)传质速率快,反应迅速;4)催化剂的活性和选择性较高;5)不易粉化;6)机械强度高,稳定性强;7)催化剂装卸简便,其反应器也易于维护,减少了操作费用,由于成型蜂窝体催化剂整体都是由催化剂组成,更加有助于提高催化效率。
14.本发明除了提供了一种蜂窝体成型催化剂产品,还提供了上述蜂窝体成型催化剂的制备方法,包括如下步骤:
15.将催化剂原粉与粘结剂、胶溶剂、助挤剂、造孔剂、成型助剂混合形成混合物;
16.所述混合物加水混匀后,依次经过捏合、老化、挤出成型、干燥以及焙烧;
17.其中,所述干燥为分段干燥,每段干燥保持恒温恒湿,湿度保持在50~90%,所述焙烧为分段焙烧。
18.发明人通过长期实践发现,整体式催化剂在实际应用中也存在问题,催化剂活性与稳定性欠佳,尤其抗压性能不佳。
19.因此为了解决上述技术问题,本发明提供了一种蜂窝体成型催化剂的制备方法,该制备方法通过分段干燥以及分段焙烧的方式提高了催化剂本身的稳定性,降低脱落率,使得催化剂粉末更为均匀。在干燥的过程中需要保证环境的恒温恒湿,之所以需要维持恒温恒湿的状态也是为了降低催化剂成型过程中的开裂,提高催化剂的稳定性。
20.优选地,催化剂原粉的质量为所述混合物质量的40~80wt%,通过控制适量的催化剂原粉含量以保证制备得到的成型催化剂的催化效果。优选地,混合物加水混匀过程中,加入水的质量为混合物质量的0.5~1.5倍,通过配合适量的水保证混合物的分散均匀。优
选地,所述干燥过程的分段数为2~10段,第1段的干燥温度为15~20℃,后续每段温度依次高10~15℃,最后一段的干燥温度为100~110℃。
21.具体实际操作时,对于二段、三段、四段、五段、六段、七段、八段、九段以及十段干燥的工艺过程分别按照以下方式操作:
22.二段:先在20℃进行干燥,干燥至水分含量小于10wt%后在再将胚体缓慢升温至110℃至干燥完全;
23.三段:先在20℃进行干燥,干燥至水分含量小于20wt%后,在将胚体缓慢升温至30℃进行干燥,干燥至水分含量小于10wt%后在再将胚体缓慢升温至110℃至干燥完全;
24.四段:先在20℃进行干燥,干燥至水分含量小于30wt%后,在将胚体缓慢升温至30℃进行干燥,干燥至水分含量小于20wt%后,在将胚体缓慢升温至40℃进行干燥,干燥至水分含量小于10wt%后在再将胚体缓慢升温至110℃至干燥完全;
25.五段:先在20℃进行干燥,干燥至水分含量小于40wt%后,在将胚体缓慢升温至30℃进行干燥,干燥至水分含量小于30wt%后,将胚体缓慢升温至40℃进行干燥,干燥至水分含量小于20wt%后,在将胚体缓慢升温至50℃进行干燥,干燥至水分含量小于10wt%后在再将胚体缓慢升温至110℃至干燥完全;
26.六段:先在20℃进行干燥,干燥至水分含量小于50wt%后,在将胚体缓慢升温至30℃进行干燥,干燥至水分含量小于40wt%后,将胚体缓慢升温至40℃进行干燥,干燥至水分含量小于30wt%后,在将胚体缓慢升温至50℃进行干燥,干燥至水分含量小于20wt%后,在将胚体缓慢升温至60℃进行干燥,干燥至水分含量小于10wt%后在再将胚体缓慢升温至110℃至干燥完全;
27.七段:先在20℃进行干燥,干燥至水分含量小于60wt%后,在将胚体缓慢升温至30℃进行干燥,干燥至水分含量小于50wt%后,将胚体缓慢升温至40℃进行干燥,干燥至水分含量小于40wt%后,在将胚体缓慢升温至50℃进行干燥,干燥至水分含量小于30wt%后,在将胚体缓慢升温至60℃进行干燥,干燥至水分含量小于20wt%后,在将胚体缓慢升温至70℃进行干燥,干燥至水分含量小于10wt%后在再将胚体缓慢升温至110℃至干燥完全;
28.八段:先在20℃进行干燥,干燥至水分含量小于70wt%后,在将胚体缓慢升温至30℃进行干燥,干燥至水分含量小于60wt%后,将胚体缓慢升温至40℃进行干燥,干燥至水分含量小于50wt%后,在将胚体缓慢升温至50℃进行干燥,干燥至水分含量小于40wt%后,在将胚体缓慢升温至60℃进行干燥,干燥至水分含量小于30wt%后,在将胚体缓慢升温至70℃进行干燥,干燥至水分含量小于20wt%后,在将胚体缓慢升温至80℃进行干燥,干燥至水分含量小于10wt%后在再将胚体缓慢升温至110℃至干燥完全;
29.九段:先在20℃进行干燥,干燥至水分含量小于80wt%后,在将胚体缓慢升温至30℃进行干燥,干燥至水分含量小于70wt%后,将胚体缓慢升温至40℃进行干燥,干燥至水分含量小于60wt%后,在将胚体缓慢升温至50℃进行干燥,干燥至水分含量小于50wt%后,在将胚体缓慢升温至60℃进行干燥,干燥至水分含量小于40wt%后,在将胚体缓慢升温至70℃进行干燥,干燥至水分含量小于30wt%后,在将胚体缓慢升温至80℃进行干燥,干燥至水分含量小于20wt%后,在将胚体缓慢升温至90℃进行干燥,干燥至水分含量小于10wt%后在再将胚体缓慢升温至110℃至干燥完全;
30.十段:先在20℃进行干燥,干燥至水分含量小于90wt%后,在将胚体缓慢升温至30
℃进行干燥,干燥至水分含量小于80wt%后,将胚体缓慢升温至40℃进行干燥,干燥至水分含量小于70wt%后,在将胚体缓慢升温至50℃进行干燥,干燥至水分含量小于60wt%后,在将胚体缓慢升温至60℃进行干燥,干燥至水分含量小于50wt%后,在将胚体缓慢升温至70℃进行干燥,干燥至水分含量小于40wt%后,在将胚体缓慢升温至80℃进行干燥,干燥至水分含量小于30wt%后,在将胚体缓慢升温至90℃进行干燥,干燥至水分含量小于20wt%后,在将胚体缓慢升温至100℃进行干燥,干燥至水分含量小于10wt%后在再将胚体缓慢升温至110℃至干燥完全。
31.优选地,所述焙烧过程的分段数为2~4段,前1~3段的每段焙烧升温速率控制在0.5~2℃/min,温度控制在200~300℃,焙烧时间为2~12h,最后一段的升温速率控制在2~10℃/min,温度控制在400~700℃,焙烧时间为2~12h。
32.具体操作时,对于实际的二段、三段、四段焙烧工艺过程具体按照如下操作进行:
33.二段:从室温以0.5~2℃/min升温到200~300℃焙烧2~12h后以2~10℃/min升温到300~700℃焙烧2~12h,焙烧完成后,逐渐冷却至室温。
34.三段:从室温以0.5~2℃/min升温到200~300℃焙烧2~12h后,在以0.5~2℃/min升温到300~400℃焙烧2~12h,在以2~10℃/min升温到400~700℃焙烧2~12h,焙烧完成后,逐渐冷却至室温。
35.四段:从室温以0.5~2℃/min升温到100~200℃焙烧2~12h后,在以0.5~2℃/min升温到200~300℃焙烧2~12h,在以0.5~2℃/min升温到300~400℃焙烧2~12h,在以2~10℃/min升温到400~700℃焙烧2~12h,焙烧完成后,逐渐冷却至室温。
36.优选地,粘结剂为所述混合物质量的10~50wt%;
37.所述粘结剂的类型为云石胶和ab胶、淀粉、聚乙烯醇、高岭土、水滑石、硅溶胶、硅酸钠、铝溶胶、聚丙烯酰胺、甲基纤维素、羧甲基纤维素钠、羧乙基纤维素、羧丙基纤维素、玉米油、羧丙基甲基纤维素、妥尔油、硬脂酸钠、淀粉、磷酸二氢铝溶液、硅铝酸盐、拟薄水铝石、莫来石纤维、锂辉石、锂霞石、甲基纤维素铵、沥青、煤焦油、纤维素中的任意一种或几种。
38.优选地,所述胶溶剂为所述混合物质量的1~15wt%;
39.所述胶溶剂的类型为硝酸、盐酸、乙酸、甲酸、柠檬酸、三氯乙酸、丙二酸中的任意一种或几种;
40.优选地,所述助挤剂为所述混合物质量的1~15wt%;
41.所述助挤剂的类型为田菁粉、甘油、色拉油、草酸、酒石酸、柠檬酸、聚丙烯酰胺、硬脂酸、丙三醇、玉米油、妥尔油、硬脂酸钠、棕榈油、豆油、蓖麻油、乙酸中的任意一种或几种。
42.优选地,所述造孔剂为所述混合物质量的1~10wt%;
43.所述造孔剂的类型为活性碳、木屑、木棉、淀粉、聚乙二醇、尿素、纤维素、聚氧化乙烯、田菁粉、海绵中的任意一种或几种。
44.优选地,所述成型助剂为所述混合物质量的0.1~5wt%;
45.所述成型助剂包括玻璃纤维、纸浆纤维、乳酸和乙醇胺中的任意一种或几种。
46.通过对成型过程中的助剂的种类以及加量进行优化,以提高整体式催化剂的成型度以及稳定性。
47.本发明的蜂窝体成型催化剂在烧结烟气领域中的co催化氧化方面具有很强的应
用,可以在130℃使钢铁烧结烟气co的浓度降低到小于等于1000ppm。
48.烧结烟气co含量一般为6000~8000ppm,除尘、脱硫、脱硝后烟气温度为130℃左右,其中含有n2\o2\co2\h2o等主要气体成分,还有少量的so2\nox\nh3\cl2等。最终净化的目标是将co含量从6000~8000ppm降低到小于等于1000ppm。
49.与现有技术相比,本发明的有益效果为:
50.(1)本发明通过对活性成分的合理配比提高了催化剂本身的催化效果,并同时提高催化剂的稳定性。
51.(2)本发明通过分段干燥以及分段焙烧的方式提高了催化剂的稳定性以及抗压性,降低脱落率,使得催化剂粉末更为均匀。
52.(3)本发明的蜂窝体成型催化剂具有较强的应用效果,可以在空速为200000h-1
,温度为110~150℃时使钢铁烧结烟气co的浓度降低到小于等于1000ppm,并且具有很好的稳定性,可长时间保持高净化效率。
附图说明
53.通过阅读下文优选实施方式的详细描述,各种其他的优点和益处对于本领域普通技术人员将变得清楚明了。附图仅用于示出优选实施方式的目的,而并不认为是对本发明的限制。而且在整个附图中,用相同的参考符号表示相同的部件。在附图中:
54.图1为本发明实施例1提供的蜂窝体成型催化剂随着温度变化的催化效率变化曲线图。
具体实施方式
55.下面将结合实施例对本发明的实施方案进行详细描述,但是本领域技术人员将会理解,下列实施例仅用于说明本发明,而不应视为限制本发明的范围。实施例中未注明具体条件者,按照常规条件或制造商建议的条件进行。所用试剂或仪器未注明生产厂商者,均为可以通过市售购买获得的常规产品。
56.实施例1
57.蜂窝体成型催化剂的制备方法按照如下步骤进行:
58.1)将80wt%的催化剂粉末,10wt%的羧甲基纤维素,7wt%的田菁粉,1wt%的活性炭,1wt%的玻璃纤维,1wt%的稀硝酸配置成泥状体,其中催化剂粉末的有效成分为氧化铜、氧化锰以及其他金属氧化物之间的质量比为50:90:1,其他金属氧化物为氧化锡、氧化钴、氧化镧的混合物;
59.2)往泥状体中加入混合物一半质量的水混匀后转移至捏合机内以36转/min搅拌60min使泥料混合均匀;
60.3)将泥料用保鲜膜包严放于环境温度为20℃,环境湿度为50%的条件下老化24h。
61.4)将老化后的泥料放入挤条机中压制产生蜂窝状成型催化剂;挤出压力为20mpa。
62.5)二段干燥:先在20℃进行干燥,干燥在恒温恒湿箱中进行,湿度为50%,干燥至水分含量小于10wt%后在再将胚体缓慢升温至110℃至干燥完全;干燥过程中定时将催化剂翻转保证催化剂的整体性良好。
63.6)二段焙烧:从室温以0.5℃/min升温到300℃焙烧12h后以2℃/min升温到400℃
焙烧2h,焙烧完成后,逐渐冷却至室温。
64.实施例2
65.蜂窝体成型催化剂的制备方法按照如下步骤进行:
66.1)40wt%的催化剂粉末,50wt%的羧甲基纤维素,1wt%的田菁粉,3wt%的活性炭,5wt%的玻璃纤维,1wt%的稀硝酸配置成泥状体,其中催化剂粉末的有效成分为氧化铜、氧化锰以及其他金属氧化物之间的质量比为5:50:10,其他金属氧化物为氧化镨、氧化钐、氧化铕、氧化钆、氧化钾、氧化钙的混合物;
67.2)往泥状体中加入混合物1倍质量的水混匀后转移至捏合机内以36转/min搅拌60min使泥料混合均匀;
68.3)将泥料用保鲜膜包严放于环境温度为20℃,环境湿度为50%的条件下老化24h。
69.4)将老化后的泥料放入挤条机中压制产生蜂窝状成型催化剂;挤出压力为20mpa。
70.5)四段干燥:先在20℃进行干燥,干燥在恒温恒湿箱中进行,湿度为60%,干燥至水分含量小于30wt%后,在将胚体缓慢升温至30℃进行干燥,干燥至水分含量小于20wt%后,在将胚体缓慢升温至40℃进行干燥,干燥至水分含量小于10wt%后在再将胚体缓慢升温至110℃至干燥完全;干燥过程中定时将催化剂翻转保证催化剂的整体性良好。
71.6)四段焙烧:从室温以2℃/min升温到100℃焙烧2h后,在以1℃/min升温到200℃焙烧2h,在以0.5℃/min升温到400℃焙烧10h,在以10℃/min升温到700℃焙烧5h,焙烧完成后,逐渐冷却至室温。
72.实施例3
73.蜂窝体成型催化剂的制备方法按照如下步骤进行:
74.1)将58.9wt%的催化剂粉末,10wt%的羧甲基纤维素,15wt%的田菁粉,1wt%的活性炭,0.1wt%的玻璃纤维,15wt%的稀硝酸配置成泥状体,其中催化剂粉末的有效成分为氧化铜、氧化锰以及其他金属氧化物之间的质量比为20:70:3,其他金属氧化物为氧化镨、氧化钐、氧化铕、氧化钆、氧化钾、氧化钙的混合物;
75.2)往泥状体中加入混合物1.5倍质量的水混匀后转移至捏合机内以36转/min搅拌60min使泥料混合均匀;
76.3)将泥料用保鲜膜包严放于环境温度为20℃,环境湿度为90%的条件下老化24h。
77.4)将老化后的泥料放入挤条机中压制产生蜂窝状成型催化剂;挤出压力为20mpa。
78.5)五段干燥:先在15℃进行干燥,干燥在恒温恒湿箱中进行,湿度为90%,干燥至水分含量小于40wt%后,在将胚体缓慢升温至30℃进行干燥,干燥至水分含量小于30wt%后,将胚体缓慢升温至40℃进行干燥,干燥至水分含量小于20wt%后,在将胚体缓慢升温至50℃进行干燥,干燥至水分含量小于10wt%后在再将胚体缓慢升温至100℃至干燥完全;干燥过程中定时将催化剂翻转保证催化剂的整体性良好。
79.6)三段焙烧:从室温以1℃/min升温到200℃焙烧4h后,在以0.8℃/min升温到400℃焙烧10h,在以8℃/min升温到500℃焙烧9h,焙烧完成后,逐渐冷却至室温。
80.比较例1
81.具体操作步骤与实施例1一致,只是干燥过程为一段干燥:干燥在恒温恒湿箱中进行,湿度为40%,升温至110℃至干燥完全,干燥过程中定时将催化剂翻转保证催化剂的整体性良好。
82.比较例2
83.具体操作步骤与实施例1一致,只是焙烧过程为一段焙烧:从室温以0.5℃/min升温到400℃焙烧12h,焙烧完成后,逐渐冷却至室温。
84.比较例3
85.具体操作步骤与实施例1一致,只是干燥的过程中,湿度为20%。
86.比较例4
87.具体操作步骤与实施例1一致,只是干燥的过程中,湿度为10%。
88.比较例5
89.具体操作步骤与实施例1一致,只是干燥过程不维持一定的湿度,在完全干燥的环境下进行干燥。
90.实施例4
91.具体操作步骤与实施例1一致,只是催化剂粉末的有效成分为氧化铜、氧化锰以及其他金属氧化物之间的质量比为20:70:5。
92.实施例5
93.具体操作步骤与实施例1一致,只是催化剂粉末的有效成分为氧化铜、氧化锰以及其他金属氧化物之间的质量比为20:70:7。
94.实验例1
95.将实施例1~3以及比较例1~8的催化剂效果进行评价,具体实验评价方法为:
96.将烧结烟气流过制备好的蜂窝体催化剂(尺寸为50mm
×
50mm
×
50mm),co初始浓度:7900ppm,其他气体成分:20%o2,8%h2o,5co2,n2为平衡气。烟气流量为25m3/h,空速为200000h-1
,测量流过前后co的浓度。co去除率=(进口气浓度-出口气浓度)/(进口气的浓度)。
97.该催化剂的稳定性,制备完以后在jp-020plus超声波清洗机中以180w的功率(超声波频率为40khz)超声处理10min/30min/60min后,干燥,称重。脱落率=(处理前的质量-处理后的质量)/处理前的质量。
98.催化72h后对催化剂进行称重,使用72h后的脱落率=(使用前的质量-使用后的质量)/使用前的质量。
99.抗压强度:分别截取每种制备条件下两块50mm
×
50mm
×
50mm的试块,用压力试验机测试轴向和横向抗压强度。
100.表1催化剂效果评价结果
[0101][0102]
从上述实施例1与实施例4~5的对比数据可以看出,本发明的催化剂有效成分除了氧化锰以及氧化铜之外,还额外添加了其他金属氧化物,但是其他金属氧化物的质量需要控制在比较适宜的范围内,因为这些金属的添加在一定程度上提高了催化剂的催化效果,也提高了催化剂本身的抗水性。
[0103]
从上述实施例1与比较例1~2的对比数据可以看出,当为单段焙烧或者单段干燥的状态下,其对催化性能以及催化剂稳定性均有影响,因此本发明通过实践发现特意采用的分多次干燥以及分多次焙烧的方式。
[0104]
从上述实施例1与比较例3~5的对比数据可以看出,干燥过程中是需要在恒湿且湿度适宜的条件下进行,否则完全干燥的状态对催化剂本身的稳定性是极为不利的。
[0105]
另外,从图1的催化效率曲线也可以看出,在较低温度下本发明的蜂窝体成型催化剂即可呈现出较优异的催化效果,其他实施例的催化剂进行相应的实验也得到相类似的结果。
[0106]
总之,通过采用上述方法制备得到的蜂窝体成型催化剂具有如下效果:
[0107]
①
该蜂窝催化剂具有很好的抗水性,在含水1~20%的烟气中可以具有较高的co催化效率。
[0108]
②
该蜂窝催化剂可以在空速为200000h-1
,温度为130℃的低温条件下使钢铁烧结烟气co的浓度降低到小于等于1000ppm。
[0109]
③
该蜂窝催化剂具有很好的稳定性,使用过程中,连续使用72h,可保证烧结烟气中co的去除率≥90%。
[0110]
④
该蜂窝催化剂具有很好的稳定性,使用过程中,连续使用72h,催化剂粉末的脱落率≤1%。
[0111]
⑤
该蜂窝催化剂具有很好的抗压强度。抗压强度:分别截取两块50mm
×
50mm
×
50mm的试块,用压力试验机测试轴向和横向抗压强度。
[0112]
尽管已用具体实施例来说明和描述了本发明,然而应意识到,在不背离本发明的
精神和范围的情况下可以作出许多其它的更改和修改。因此,这意味着在所附权利要求中包括属于本发明范围内的所有这些变化和修改。
再多了解一些
本文用于企业家、创业者技术爱好者查询,结果仅供参考。