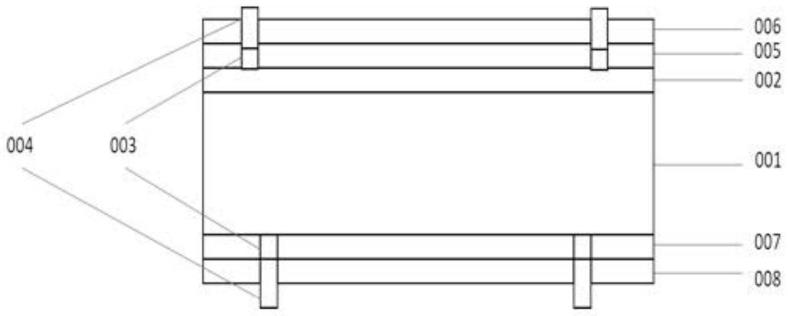
1.本技术涉及晶硅太阳电池生产技术领域,具体而言,涉及一种金属电极、晶硅太阳电池及制备方法。
背景技术:
2.目前,由于能源危机和环境危机,世界各国纷纷加大可再生清洁能源的开发力度。在众多的可再生清洁能源中,太阳能清洁环保,资源丰富,分布广泛,因而倍受研究者青睐,有望成为未来清洁可再生能源中最重要的能源;晶硅太阳电池作为转化利用太阳能的器件,成为研究重点。
3.在量产晶硅太阳电池中,perc电池(passivated emitterand rear cell,发射极和背面钝化电池)占据光伏市场的85%以上。在perc电池中非硅成本占比较大的工序是制备金属电极,约占perc电池总成本的45%;在新型太阳能电池hit(heterojunction withintrinsic thin-layer,本征薄膜异质结电池)中,银浆料成本占比非硅成本的50%。现在量产工艺中制备电极使用最广泛的为丝网印刷工艺,其是使用丝网印刷银浆料,再经过高温或低温烧结形成半导体与金属的欧姆接触银电极以导出光生载流子。
4.近年来,随着太阳能电池生产成本的不断下降,价格昂贵的银浆料的成本在电池总成本中的占有比例不断上升;且银电极的宽度和高宽比受到丝网印刷工艺和浆料物化性能的限制,常规丝网印刷银电极的高宽比在30%~35%,阻碍了晶硅太阳电池效率的提升。为了进一步降低太阳能电池成本和提升电池效率,使用湿法电镀法制作太阳能电池的金属电极成为了量产研究热点,湿法电镀法可使用便宜的镍、铜等金属去部分或者全部替代银制备电极来实现成本降低。但是现有的湿法电镀法中化学溶液处理成本高,电镀溶液质量要求高,电镀电极的均匀性难以解决,而且制得电极的高宽比仍比较小,电池效率较低。
技术实现要素:
5.本技术实施例的目的在于提供一种金属电极、晶硅太阳电池及制备方法,电极品质优异,高宽比高,电池的效率高。
6.第一方面,本技术实施例提供了一种金属电极的制备方法,其主要是在基片的表面刮涂正性光刻胶,定形形成正性光刻胶层;对正性光刻胶层进行光刻,形成对应图形的凹槽;使用磁控溅射技术或反应等离子体沉积(rcactivc plasma deposition,rpd)技术在凹槽内依次形成种子层和铜电极,且种子层和铜电极的总高度低于正性光刻胶层的高度。
7.在上述技术方案中,通过刮涂正性光刻胶和光刻形成凹槽,使用磁控溅射技术或反应等离子体沉积技术制备金属电极,该金属电极是由种子层和铜电极组成,种子层具有抗腐蚀的作用,起到粘结基片和铜电极的作用,铜电极用于收集载流子。同时使金属电极的高度低于正性光刻胶的高度,最终规则形状的凹槽未填充满,留有一定间距,方便后续刮涂负性光刻胶来保护金属电极,防止后续工艺破坏铜电极栅线。
8.本技术实施例的金属电极的制备方法能够解决丝网印刷银浆制备银电极而带来
的制造成本昂贵等问题,还能解决湿法化学溶液电镀技术产生的废水处理成本高问题,最为重要的是,相比丝网丝印银电极和电化学溶液电镀铜电极,本技术实施例的制备方法能够精确控制栅线的高度和宽度,从而制备得到品质优异的电极,铜电极的高宽比高,降低正面入射光的栅线的遮阴面积,增加入射光的光通量,对应电池的效率高。
9.在一种可能的实现方式中,种子层的材质为钛、镍、镍钒合金或钛钨合金。
10.在一种可能的实现方式中,种子层的宽度为10~20μm,高度为2~5μm;铜电极的宽度为10~20μm,高度为5~15μm。
11.在上述技术方案中,种子层和铜电极组成的金属电极满足使用需求,成本相对较低,而且保证铜电极的高宽比高。
12.在一种可能的实现方式中,定形的方法为:先刮涂正性光刻胶,刮涂厚度为10~20μm,再进行软烘实现正性光刻胶的均匀定形,软烘温度为80~120℃,时间为60~200s。
13.在一种可能的实现方式中,光刻的方法为:采用紫外光源对正性光刻胶层对应图形的区域进行微米级别光源曝光,再在显影溶液进行曝光图形的显影,显影时间为3~10min。
14.第二方面,本技术实施例提供了一种晶硅太阳电池,其包括硅衬底,依次叠加设置于硅衬底正面的磷源掺杂层、正面sinx减反射层、sio2层,依次叠加设置于硅衬底背面的al2o3钝化层、背面sinx减反射层;sio2层和正面sinx减反射层中镶嵌有正面金属电极,正面金属电极包括由内至外依次叠加的种子层和铜电极,铜电极的高宽比为40%~50%,且种子层与磷源掺杂层接触,铜电极伸出sio2层;背面sinx减反射层和al2o3钝化层中镶嵌有背面金属电极,背面金属电极包括由内至外依次叠加的种子层和铜电极,铜电极的高宽比为40%~50%,且种子层与硅衬底接触,铜电极伸出背面sinx减反射层。
15.在上述技术方案中,晶硅太阳电池为perc电池结构,其中,具有抗腐蚀和粘结作用的种子层和用于收集载流子的铜电极共同组成金属电极,铜电极的高宽比高,降低了电池正面入射光的阴影面积,提高了电池的光电转化效率,降低了perc电池的制造成本。
16.在一种可能的实现方式中,正面sinx减反射层的厚度为50~80nm,折射率为2.0~2.3;sio2层的厚度为10~30nm,折射率为1.6~1.8。
17.在上述技术方案中,折射率小的sio2层在最上面,折射率大的sinx减反射层在其下面,一定厚度和折射率的正面sinx减反射层和sio2层组成正面叠层减反射膜,能够增加电池正面的光通量,提高短路电流,最终提高电池光电转化效率。
18.在一种可能的实现方式中,硅衬底为p型掺镓硅衬底,硅衬底的电阻率为0.4~1.1ω
·
cm,硅衬底的大小为156.75
×
156.75mm2~230
×
230mm2,厚度为80~170μm;
19.和/或,al2o3钝化层的厚度为3~10nm;
20.和/或,背面sinx减反射层的厚度为90~110nm。
21.在上述技术方案中,背面sinx减反射层的设置厚度大,比正面sinx减反射层的厚度更大,目的降低背面负性光刻胶移除液和表面活性剂造成的损伤。
22.第三方面,本技术实施例提供了一种第二方面提供的晶硅太阳电池的制备方法,其包括以下步骤:
23.在硅衬底的正面形成磷源掺杂层,采用第一方面提供的金属电极的制备方法在磷源掺杂层表面形成正面金属电极,采用第一方面提供的金属电极的制备方法在硅衬底背面
形成背面金属电极;
24.分别在正面金属电极和背面金属电极上刮涂负性光刻胶至填满对应凹槽,定形形成负性光刻胶层,将整体浸入正性光刻胶移除液中以移除正性光刻胶层;
25.在硅衬底的正面依次形成正面sin
x
减反射层和sio2层,在硅衬底的背面依次形成al2o3钝化层、背面sinx减反射层;
26.分别使用负性光刻胶移除液浸润正面和背面的负性光刻胶层以移除负性光刻胶层。
27.在上述技术方案中,在磷源扩散形成发射极的硅衬底上,正面和背面刮涂正性光刻胶,均匀定形完成后,正面和背面进行相应图形的光刻形成凹槽;在凹槽处使用磁控溅射或rpd技术进行正面金属电极和背面金属电极的制备,并在凹槽处刮涂负性光刻胶保护金属电极,使用正性光刻胶移除液清洗掉未曝光区域,再制备正面叠层减反射膜和背膜钝化保护膜,最后使用负性光刻胶移除液去除掉金属电极表面的负性光刻胶。先形成种子层的目的是粘结硅衬底,增加铜电极拉力,其次是为了抵抗正性光刻胶移除液腐蚀,避免粘结硅衬底形成空洞,造成接触电阻增大,影响电池的光电转化效率。正面叠层减反射膜包括sio2层和正面sin
x
减反射层,sio2层可以保护正面sin
x
减反射层,降低正面的负性光刻胶移除液和表面活性剂的损伤;制备的晶硅太阳电池能够具有优异的高宽比,降低正面入射光的阴影面积。
28.在一种可能的实现方式中,在移除负性光刻胶层后,还包括在氮气气氛围中进行退火的步骤,退火温度为150~180℃,退火时间为10~20min。
附图说明
29.为了更清楚地说明本技术实施例的技术方案,下面将对本技术实施例中所需要使用的附图作简单地介绍,应当理解,以下附图仅示出了本技术的某些实施例,因此不应被看作是对范围的限定,对于本领域普通技术人员来讲,在不付出创造性劳动的前提下,还可以根据这些附图获得其他相关的附图。
30.图1为本技术实施例提供的一种晶硅太阳电池的结构示意图;
31.图2为本技术实施例提供的一种晶硅太阳电池的制备过程中的结构示意图。
32.图标:001-硅衬底;002-磷源掺杂层;003-种子层;004-铜电极;005-正面sinx减反射层;006-sio2层;007-al2o3钝化层;008-背面sinx减反射层。
具体实施方式
33.为使本技术实施例的目的、技术方案和优点更加清楚,下面将对本技术实施例中的技术方案进行清楚、完整地描述。实施例中未注明具体条件者,按照常规条件或制造商建议的条件进行。所用试剂或仪器未注明生产厂商者,均为可以通过市售购买获得的常规产品。
34.下面对本技术实施例的金属电极、晶硅太阳电池及制备方法进行具体说明。
35.本技术实施例提供了一种金属电极的制备方法,其包括以下步骤:
36.(1)在基片的表面刮涂正性光刻胶,定形形成正性光刻胶层;作为一种实施方式,定形的方法可以为:先刮涂正性光刻胶,刮涂厚度为10~20μm,再进行软烘实现正性光刻胶
的均匀定形,软烘温度为80~120℃,时间为60~200s。
37.(2)对正性光刻胶层进行光刻,形成对应图形的凹槽;作为一种实施方式,光刻的方法为:在曝光机采用紫外光源对正性光刻胶层对应图形的区域进行微米级别光源曝光,再在显影溶液进行曝光图形的显影,显影时间为3~10min。
38.(3)使用磁控溅射技术或反应等离子体沉积技术在凹槽内依次形成种子层和铜电极,且种子层和铜电极的总高度低于正性光刻胶层的高度,即凹槽未被种子层和铜电极填满。种子层的材质可以为钛、镍、镍钒合金或钛钨合金;种子层的宽度可以为10~20μm,高度可以为2~5μm;铜电极的宽度可以为10~20μm,高度可以为5~15μm。
39.本技术实施例提供一种新型物理制备高品质的铜电极金属化方案,该金属电极的制备方法是用于制备形成包括种子层和铜电极的金属电极,只要是具有该金属电极的晶硅太能电池都可以采用上述金属电极的制备方法,比如perc电池。
40.请参看图1,本技术实施例提供了一种晶硅太阳电池,属于同质结电池,具体为perc电池,该晶硅太阳电池包括硅衬底001,依次叠加设置于硅衬底001正面的磷源掺杂层002、正面sinx减反射层005、sio2层006,依次叠加设置于硅衬底001背面的al2o3钝化层007、背面sinx减反射层008;sio2层006和正面sinx减反射层005中镶嵌有正面金属电极,正面金属电极包括由内至外依次叠加的种子层003和铜电极004,且种子层003与磷源掺杂层002接触,铜电极004伸出sio2层006;背面sinx减反射层008和al2o3钝化层007中镶嵌有背面金属电极,背面金属电极包括由内至外依次叠加的种子层003和铜电极004,且种子层003与硅衬底001接触,铜电极004伸出背面sinx减反射层008。
41.其中,硅衬底001可以为p型掺镓硅衬底001,硅衬底001的电阻率为0.4~1.1ω
·
cm,硅衬底001的大小为156.75
×
156.75mm2~230
×
230mm2,厚度为80~170μm,且表面经过清洗制绒形成金字塔尺寸,金字塔尺寸1~5μm。
42.从硅衬底001的正面看,磷源掺杂层002是在硅衬底001的正面进行磷源扩散形成pn结;正面sinx减反射层005的厚度为50~80nm,折射率为2.0~2.3;sio2层006的厚度为10~30nm,折射率为1.6~1.8。
43.从硅衬底001的背面看,al2o3钝化层007的厚度为3~10nm;背面sinx减反射层008的厚度为90~110nm。
44.请参看图2,本技术实施例提供了一种上述的晶硅太阳电池的制备方法,其包括以下步骤:
45.(1)选择p型掺镓的硅衬底001,其电阻率0.4-1.1ω
·
cm,大小范围在为156.75
×
156.75mm2~230
×
230mm2,厚度范围为80~170μm,先使用hf/naoh溶液,进行清洗制绒形成金字塔尺寸,金字塔尺寸1~5μm。在制绒后的硅衬底001表面进行磷源扩散形成pn结,湿法刻蚀洗除硅衬底001背面的磷源和硅片四周的磷源,防止电池漏电,形成在硅衬底001正面的磷源掺杂层002。
46.(2)在硅衬底001正面的磷源掺杂层002上刮涂正性光刻胶,刮涂厚度10~20μm,再进行软烘,软烘温度为80~120℃,时间为60~200s实现正性光刻胶的均匀定形得到正性光刻胶层,目的是为后续制备正面均匀的种子层003和铜电极004做准备。定形完后通过翻转轮进行翻转,在硅衬底001背面刮涂正性光刻胶,刮涂厚度10~20μm,再进行软烘,软烘温度为80~120℃,时间为60~200s实现正性光刻胶的均匀定形得到正性光刻胶层,目的是制备
为后续制备背面均匀的种子层003和铜电极004做准备,具体结构如图2中的a部分所示。
47.(3)将经过涂胶定形的硅衬底001置于曝光机中,采用紫外光源分别对正面和背面的正性光刻胶层对应图形的区域进行微米级别光源曝光,正面曝光和背面曝光时调节光源能量至50~150kkz;曝光结束后,在显影溶液中进行正面和背面曝光图形的显影,显影时间为3~10min,曝光区域形成对应栅线图像、规则形状的凹槽,正面凹槽下面的磷源掺杂区域形成了重掺杂区域,具体结构如图2中的b部分所示。
48.(4)利用磁控溅射技术或rpd技术对应的设备,安装种子层003靶材,在正面和背面的凹槽里形成种子层003,凹槽的宽度为10~20μm,种子层003可以为镍,种子层003的宽度10~20μm,高度为2~5μm,具体结构如图2中的c部分所示。
49.(5)再利用磁控溅射技术或rpd技术对应的设备,安装铜靶材,在正面和背面的凹槽内的种子层003上制备铜电极004,铜电极004的宽度10~20μm,高度为5~15μm,具体结构如图2中的d部分所示,正面凹槽内的种子层003和铜电极004组成正面金属电极,背面凹槽内的种子层003和铜电极004组成背面金属电极,正面金属电极和背面金属电极均位于对应凹槽内,即未填满对应凹槽。
50.(6)分别在正面金属电极的铜电极004和背面金属电极的铜电极004上刮涂负性光刻胶至填满对应凹槽以保护金属电极,定形形成负性光刻胶层,具体结构如图2中的e部分所示。负性光刻胶为购买市售产品即可,例如负性光刻胶为成分按质量百分数计为30%的环化橡胶、65%的二甲苯、5%的交联剂的产品。
51.(7)将整体浸入正性光刻胶移除液中以移除未曝光区域的正性光刻胶层,而负性光刻胶不溶于正性光刻胶移除液,涂负性光刻胶保护金属电极不受影响,具体结构如图2中的f部分所示。正性光刻胶为购买市售产品即可,例如正性光刻胶为成分按质量百分数计为73%的丙二醇单甲醚醋酸酯108-65-6、21%的甲酚甲醛酚醛树脂9016-83-5、6%的6-地藻-5,6-二氢-5-氧代-1-萘磺酸酯68510-93-0的产品。
52.(8)在硅衬底001的正面采用pecvd依次形成正面sin
x
减反射层005和sio2层006,正面sin
x
减反射层005的厚度为50~80nm,折射率为2.0~2.3;sio2层006的厚度为10~30nm,折射率为1.6~1.8。
53.(9)在硅衬底001的背面采用原子层沉积技术依次形成al2o3钝化层007、背面sinx减反射层008,al2o3钝化层007的厚度为3~10nm,背面sinx减反射层008的厚度为90~110nm,具体结构如图2中的g部分所示。
54.(10)分别使用负性光刻胶移除液和表面活性剂浸润正面和背面的负性光刻胶层截面,去除掉金属电极上面的负性光刻胶层。在负性光刻胶移除液中加入表面活性剂,能够快速去除掉金属电极的表面的负性光刻胶,具体结构如图2中的h部分所示。
55.(11)在氮气气氛围中进行退火的步骤,退火温度为150~180℃,退火时间为10~20min。
56.以下结合实施例对本技术的特征和性能作进一步的详细描述。
57.实施例1
58.本实施例提供一种perc电池,其包括硅衬底,依次叠加设置于硅衬底正面的磷源掺杂层、正面sinx减反射层、sio2层,依次叠加设置于硅衬底背面的al2o3钝化层、背面sinx减反射层。其中,硅衬底为p型掺镓硅衬底,电阻率为0.8ω
·
cm,硅衬底的大小为230
×
230mm2,厚度为120μm,且表面经过清洗制绒形成金字塔尺寸,金字塔尺寸3μm。正面sinx减反射层的厚度为60nm,折射率为2.2;sio2层的厚度为20nm,折射率为1.7,正面sinx减反射层和sio2层组成的叠层减反射膜的折射率达2.12;al2o3钝化层的厚度为5nm;背面sinx减反射层的厚度为100nm。
59.sio2层和正面sinx减反射层中镶嵌有正面金属电极,正面金属电极包括由内至外依次叠加的种子层和铜电极,且种子层与磷源掺杂层接触,铜电极伸出sio2层。其中,种子层的材质为镍,种子层的宽度为15μm,高度为5μm;铜电极的宽度为20μm,高度为8.6μm,正面的铜电极的高宽比为43%。
60.背面sinx减反射层和al2o3钝化层中镶嵌有背面金属电极,背面金属电极包括由内至外依次叠加的种子层和铜电极,且种子层与硅衬底接触,铜电极伸出背面sinx减反射层。其中,种子层的材质为镍,种子层的宽度为15μm,高度为5μm;铜电极的宽度为20μm,高度为8.6μm,背面的铜电极的高宽比为43%。
61.该perc电池通过以下步骤制备而成:
62.(1)选择硅衬底,先使用hf/naoh溶液,进行清洗制绒形成金字塔尺寸,在制绒后的硅衬底表面进行磷源扩散形成pn结,湿法刻蚀洗除硅衬底背面的磷源和硅片四周的磷源,形成在硅衬底正面的磷源掺杂层。
63.(2)在硅衬底正面的磷源掺杂层上刮涂正性光刻胶(lg化学),刮涂厚度15μm,再进行软烘,软烘温度为100℃,时间为120s实现正性光刻胶的均匀定形得到正性光刻胶层。定形完后通过翻转轮进行翻转,在硅衬底背面刮涂正性光刻胶,刮涂厚度15μm,再进行软烘,软烘温度为100℃,时间为120s实现正性光刻胶的均匀定形得到正性光刻胶层。
64.(3)将经过涂胶定形的硅衬底置于曝光机中,采用紫外光源分别对正面和背面的正性光刻胶层对应图形的区域进行微米级别光源曝光,正面曝光和背面曝光时调节不同的光源能量;曝光结束后,在显影溶液中进行正面和背面曝光图形的显影,显影时间为8min,曝光区域形成对应栅线图像、规则形状的凹槽,正面凹槽下面的磷源掺杂区域形成了重掺杂区域。
65.(4)利用磁控溅射技术对应的设备,安装种子层靶材,在正面和背面的凹槽里形成种子层。
66.(5)再利用磁控溅射技术对应的设备,安装铜靶材,在正面和背面的凹槽内的种子层上制备铜电极,正面凹槽内的种子层和铜电极组成正面金属电极,背面凹槽内的种子层和铜电极组成背面金属电极,正面金属电极和背面金属电极均位于对应凹槽内,即未填满对应凹槽。
67.(6)分别在正面金属电极的铜电极和背面金属电极的铜电极上刮涂负性光刻胶(lg化学)至填满对应凹槽以保护金属电极,定形形成负性光刻胶层。
68.(7)将整体浸入正性光刻胶移除液(lg化学)中以移除未曝光区域的正性光刻胶层。
69.(8)在硅衬底的正面采用pecvd依次形成正面sin
x
减反射层和sio2层。
70.(9)在硅衬底的背面采用原子层沉积技术依次形成al2o3钝化层、背面sinx减反射层。
71.(10)分别使用负性光刻胶移除液(lg化学)和表面活性剂浸润正面和背面的负性
光刻胶层截面,去除掉金属电极上面的负性光刻胶层。
72.(11)在氮气气氛围中进行退火的步骤,退火温度为150℃,退火时间为15min。
73.实施例2
74.本实施例提供一种perc电池,其与实施例1的不同之处在于:种子层的材质为钛,正面的铜电极的高宽比为45%。
75.实施例3
76.本实施例提供一种perc电池,其与实施例1的不同之处在于:正面的铜电极的高宽比为48%。
77.实施例4
78.本实施例提供一种perc电池,其与实施例1的不同之处在于:正面sinx减反射层的厚度为80nm,折射率为2.3;sio2层的厚度为30nm,折射率为1.8,正面的铜电极的高宽比为50%。
79.对比例1
80.本对比例提供一种perc电池,其与实施例1的不同之处在于:本对比例中的金属电极为银电极,宽度45μm,高度为14μm。
81.以下对上述的perc电池进行性能检测,结果如下表所示:
[0082] 效率短路电流/a高宽比实施例123.5%11.3843%实施例223.55%11.4245%实施例323.72%11.4848%实施例423.85%11.5550%对比例123.2%11.2831%
[0083]
综上所述,本技术实施例的金属电极、晶硅太阳电池及制备方法,电极品质优异,高宽比高,电池的效率高。
[0084]
以上所述仅为本技术的实施例而已,并不用于限制本技术的保护范围,对于本领域的技术人员来说,本技术可以有各种更改和变化。凡在本技术的精神和原则之内,所作的任何修改、等同替换、改进等,均应包含在本技术的保护范围之内。
再多了解一些
本文用于企业家、创业者技术爱好者查询,结果仅供参考。