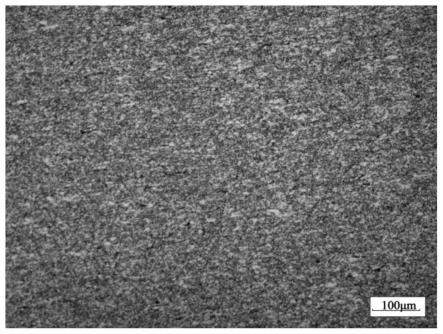
一种薄规格s550nh车厢用高强耐候钢及其制备方法
技术领域
1.本发明属于车厢用高强耐候钢领域,具体涉及一种薄规格s550nh车厢用高强耐候钢及其制备方法。
背景技术:
2.高强耐候钢是指屈服强度在400mpa级以上具有良好的耐大气腐蚀性能的高强钢,在集装箱制造行业应用比较广泛,但在商用车车厢上极少应用,且大多采用含有贵重金属ni元素的成分体系,加之冷轧工序流程较长,钢材整体生产成本很高。目前商用车车厢用钢主要以235mpa和345mpa级别的低强度低耐候性的普钢为主、400mpa级以上高强度低耐候性钢有部分应用,薄规格钢一般指2.0mm以下规格的钢板,目前热轧态厚度规格主要集中在2.0mm以上规格,不仅强度偏低、规格较厚、耐候性能也差。随着钢铁企业及汽车制造厂对汽车板耐候性、高强轻量化以及以热代冷认识的不断加深,近些年钢厂开始对短流程低成本高强耐候汽车板进行开发及推广,高强度耐候性汽车板在商用车车厢上的应用已成为重要的发展方向之一。
3.专利cn110318006b公开了一种冷轧耐候钢及其制备方法,采用连铸
→
热轧
→
卷取
→
酸洗
→
冷连轧
→
卷取
→
连续退火
→
平整
→
卷取,所述产品屈服强度≥350mpa、抗拉强度≥500mpa、a50延伸率≥30%,适用于薄规格集装箱用耐候钢的生产,但热轧后需要经过冷轧、退火及平整工序,工艺流程长,生产成本高、能源消耗大,加之成分设计含有贵重金属ni元素,使得钢材成本进一步增加。
4.现有技术550mpa级及以上高强耐候钢热轧态可生产厚度主要集中在2.0mm以上规格,基于客户薄规格、表面质量的需求,热轧后一般需要经过后续的冷轧及退火工艺,具体生产流程主要为连铸
→
铸坯二次加热
→
粗轧
→
精轧
→
层流冷却
→
卷取
→
酸洗
→
冷轧
→
卷取
→
退火
→
平整
→
卷取,这种工艺工序流程长、设备组成复杂、生产效率低、检修维护及生产成本高、能源消耗大。现有技术冷轧产品大多为普通车厢用钢,强度级别普遍较低,加之耐候成分设计大多采用贵重金属元素ni,使得整体成本进一步增加。
5.当前,世界能源、资源和环境保护问题日趋严峻,商用车车厢用钢铁材料实现高强减薄轻量化、耐候化及节能降耗已成为迫切需要。目前薄规格耐候钢生产工艺流程长、生产效率低、能耗大、成本高。
技术实现要素:
6.因此,本发明要解决的技术问题在于克服现有技术中薄规格耐候钢成本高、生产工艺流程长等缺陷,从而提供一种薄规格s550nh车厢用高强耐候钢及其制备方法。
7.为此,本发明提供了以下技术方案。
8.第一方面,本发明提供了一种薄规格s550nh车厢用高强耐候钢,成分以质量百分比计包括c:0.05~0.08%、si:0.25~0.35%、mn:0.45~0.65%、p:0.04~0.06%、cu:0.25~0.45%、cr:0.45~0.65%、ti:0.055~0.075%、s≤0.005%,其余为铁元素和不可避免
的杂质元素;同时满足cr/cu=1.2~1.7、耐候指数i≥6。
9.各元素作用及原理:
10.c为提高钢材强度的重要元素,但c含量过高会使钢的塑性下降,影响钢的成型及焊接性能。为了使产品具有良好的性能匹配,本发明中c含量控制在0.05~0.08%。
11.si为铁素体形成元素,可提高钢中固溶体的强度,对提高钢的抗拉强度更为显著。而且当si与cu、cr、p配合时,可以提高钢的耐腐蚀性能,当硅含量比较多时,有利于细化腐蚀产物α-feooh,促进钢材表面形成致密的富硅保护性锈层从而提高耐腐蚀性能,但过高则会使钢的焊接性能恶化。故本发明中si含量控制在0.25~0.35%。
12.mn是钢中重要的固溶强化元素之一,也是奥氏体稳定化元素,能扩大铁碳相图中的奥氏体区,促进钢的中温组织转变,得到以针状组织为主的微观组织,这种组织具有较好的均匀性,优良的耐候性能,高的强度和韧性。但mn含量过高不但会降低延伸率、有损钢的韧性,还会降低钢的抗腐蚀性能及焊接性能,同时提高制造成本。故本发明中mn含量控制在0.45~0.65%。
13.p是提高钢材的耐大气腐蚀性能最有效最经济的合金元素之一,还具有较强的固溶强化作用。p元素作为阳极去极化剂可以显著提高钢的耐大气腐蚀能力。但是p容易在晶界偏聚降低钢材的韧性,增加焊接裂纹敏感性,为了保证焊接性,不宜采用增加磷的方法来提高钢的耐蚀性。故本发明确定磷含量的最佳范围为0.04~0.06%。
14.s是钢中的有害元素,易与mn元素形成mns夹杂而恶化钢的塑韧性及耐大气腐蚀性能,易与ti结合生成ti4c2s2,降低有效ti的含量,从而影响微合金元素ti的强化效果。因此本发明将s含量控制在≤0.005%。
15.cu为提高耐候钢耐大气腐蚀性能的最为普遍的合金元素。在大气腐蚀过程中主要以cus的形式分布于外层腐蚀产物膜,阻止了腐蚀气体向内层的渗透,同时对基体产生钝化。但cu的熔点较低,含量过高容易导致“铜脆”现象的产生。故本发明cu含量控制在0.25~0.45%。
16.cr能够显著地提高钢的耐腐蚀性能,cr的加入有利于在钢的表面形成细而致密的内层腐蚀产物膜α-feooh,可有效抑制腐蚀性离子,当cr与cu同时加入时,效果更为显著。但cr含量过高会恶化钢材的焊接性能、降低钢的塑性和韧性,故本发明cr含量控制在0.45~0.65%。
17.ti为强碳氮化物形成元素,是提高钢材强度最经济的微合金元素。在高温下未溶的tin可显著抑制奥氏体晶粒的长大,从而细化相变之后的铁素体晶粒。钛的碳化物tic比较稳定,当加热温度高于1000℃时开始溶解,在热轧及层冷低温降温过程中tic可大量析出起到析出强化的作用。故本发明将ti含量控制在0.055~0.075%。
18.当cr与cu同时加入,且铬铜比cr/cu=1.0~2.0范围时,可有效促进细而致密的α-feooh稳定锈层的形成,且当α-feooh中cr质量分数超过5%时可有效抑制腐蚀性阴离子特别是cl-的侵入,两者协同作用使钢的耐大气腐蚀性能得以极大提高,因去ni而造成的耐候性损失得到有效弥补,同时cr为碳化物形成元素,可有效地阻碍奥氏体晶粒粗化,能显著提高钢的强度、硬度和耐磨性等。
19.通过legault-leckie公式计算钢材的耐候指数i,当i值≥6时,钢材具有良好的耐大气腐蚀性能,且随着i值的增加耐候性能增加。
20.i=26.01(%cu) 3.88(%ni) 1.20(%cr) 1.49(%si) 17.28(%p)-7.29(%cu)
×
(%ni)-9.10(%ni)
×
(%p)-33.39(%cu)221.进一步的,高强耐候钢厚度为1.0mm~2.0mm。
22.第二方面,本发明提供了一种高强耐候钢的制备方法,包括冶炼
→
连铸
→
热坯高温快烧
→
粗轧
→
精轧
→
层流冷却
→
卷取。
23.进一步的,所述连铸拉速1.0~1.5m/min,铸坯厚度170~200mm。
24.进一步的,热坯高温快烧为:将连铸获得的铸坯直装入炉,入炉温度≥800℃,在炉时间控制在60~150min,出炉温度≥1250℃。
25.进一步的,粗轧出口温度≥990℃,粗轧后得到中间坯,中间坯厚度25~35mm,精轧出口温度830~900℃。
26.进一步的,层流冷却采用两段冷却:前段冷却-保温-后段冷却;优选地,前段冷却速率50~60℃/s,保温温度为650~700℃,保温时间5~10s,后段冷却速率10~20℃/s。
27.两段冷却具体为:精轧后的钢进入前段冷却区域,前段冷却为密集冷却,喷水较大,冷却强度大;冷却到一定温度后进入无喷水区域保温;保温一段时间后,进入后段冷却区域,后段冷却区域为疏水冷却,冷却强度较小。
28.进一步的,卷取温度550~650℃。
29.进一步的,还包括酸洗平整。
30.进一步的,所述酸洗前原料温度<45℃,酸液浓度30~200g/l,酸液温度70~85℃;
31.酸洗后采用漂洗液去除酸液:漂洗液温度40~65℃,出口槽漂洗水ph值>6.0;
32.平整机延伸率0.8~3.0%。
33.具体的,酸洗介质为工业盐酸。
34.本发明技术方案,具有如下优点:
35.1.本发明提供的一种薄规格s550nh车厢用高强耐候钢,成分以质量百分比计包括c:0.05~0.08%、si:0.25~0.35%、mn:0.45~0.65%、p:0.04~0.06%、cu:0.25~0.45%、cr:0.45~0.65%、ti:0.055~0.075%、s≤0.005%,其余为铁元素和不可避免的杂质元素;同时满足cr/cu=1.2~1.7、i≥6。
36.本发明采用“去ni、单ti微合金化”成分体系,去除了贵重金属ni,且ti含量仅为0.055~0.075%,可降低钢材成本,同时,在高温下未溶的tin可显著抑制奥氏体晶粒的长大,从而细化相变之后的铁素体晶粒。钛的碳化物tic比较稳定,当加热温度高于1000℃时开始溶解,在热轧及层冷低温降温过程中tic可大量析出起到析出强化的作用,微ti协同细晶强化和析出强化作用进行强化,采用cr和cu协同加入、且铬铜比cr/cu=1.2~1.7,来弥补去ni造成的耐候性损失,同时可有效提高钢的综合力学性能。
37.2.本发明提供的高强耐候钢的制备方法包括冶炼
→
连铸
→
热坯快烧
→
粗轧
→
精轧
→
层流冷却
→
卷取。一方面,本发明缩减了冷轧及退火工序,缩短了工艺流程,节能降本;另一方面本发明采用“热坯高温快烧”加热工艺及“去ni、单ti微合金化”成分体系,节能降耗降本,同时也可有效避免“铜脆”现象的产生。本发明可生产薄规格热轧酸洗s550nh车厢用高强耐候钢,最薄可达到1.0mm,实现商用车车厢用钢高强减薄轻量化、耐候化。
38.本发明可稳定轧制1.0~2.0mm厚度规格,产品耐候及焊接性能良好,表面质量满
足客户需求,产品性能满足屈服强度rel:≥550mpa,抗拉强度rm:≥600mpa,金相组织为珠光体 铁素体(如图1所示),实现商用车车厢用钢高强减薄轻量化、耐候化、以热代冷及节能降耗的目的,具有很高的社会经济效益。
39.3.本发明提供的高强耐候钢的制备方法层流冷却为两段冷却,本发明钢的成分结合两段冷却控制工艺,包括前段冷却-保温-后段冷却,前段冷却的冷却速率快、过冷度大,可提高相变时铁素体的形核率,并抑制相变后铁素体晶粒长大,保温阶段和后段冷却阶段是为了促进tic等的析出,提高析出强化效果,并得到所需的珠光体 铁素体金相组织。两段冷却工艺使得细晶强化和析出强化得到充分发挥以保证钢具有良好的强韧性,满足产品所需性能要求。
40.4.本发明提供的高强耐候钢的制备方法还包括酸洗平整,提高热轧薄规格耐候钢表面质量,实现以热代冷,满足客户需求。
41.本发明钢为商用车车厢专用钢,采用热轧酸洗流程,短流程,可实现以热代冷、节能降本;且本技术钢屈服强度≥550mpa,属于高强度钢范畴,可实现高强减薄轻量化。随着交通运输业的发展,为提高车辆运输承载能力及满足安全节能的需求,高强减薄及以热代冷是车辆车厢用钢产品的发展方向之一。采用热轧酸洗薄规格车厢用高强耐候钢,不仅可以使车辆制造企业降低钢材使用量及生产成本,同时还可降低交通运输企业的能耗成本及增加车辆车厢的使用寿命。
附图说明
42.为了更清楚地说明本发明具体实施方式或现有技术中的技术方案,下面将对具体实施方式或现有技术描述中所需要使用的附图作简单地介绍,显而易见地,下面描述中的附图是本发明的一些实施方式,对于本领域普通技术人员来讲,在不付出创造性劳动的前提下,还可以根据这些附图获得其他的附图。
43.图1是本发明实施例1制得的高强耐候钢金相组织图。
具体实施方式
44.提供下述实施例是为了更好地进一步理解本发明,并不局限于所述最佳实施方式,不对本发明的内容和保护范围构成限制,任何人在本发明的启示下或是将本发明与其他现有技术的特征进行组合而得出的任何与本发明相同或相近似的产品,均落在本发明的保护范围之内。
45.实施例中未注明具体实验步骤或条件者,按照本领域内的文献所描述的常规实验步骤的操作或条件即可进行。所用试剂或仪器未注明生产厂商者,均为可以通过市购获得的常规试剂产品。
46.实施例1
47.本实施例提供一种薄规格s550nh车厢用高强耐候钢,其化学成分及质量百分比为c:0.061%,si:0.27%,mn:0.53%,p:0.059%,s:0.005%,cu:0.36%,cr:0.49%,ti:0.059%,余量为fe和不可避免杂质,如表1所示。
48.其生产工艺流程为:连铸
→
热坯快烧
→
粗轧
→
精轧
→
层流冷却
→
卷取
→
酸洗平整
→
卷取,具体包括下述步骤:
49.1.冶炼:将原料冶炼成上述成分钢水;
50.2.连铸:连铸拉速1.4m/min,铸坯厚度170mm;
51.3.铸坯热直装入炉,入炉温度910℃,加热时间107min,出炉温度1271℃,热轧粗轧出口温度1123℃,中间坯厚度27mm,精轧出口温度881℃,层冷采用两段冷却,前段冷却速率51℃/s,保温温度695℃,保温时间6s,后段冷却速率为13℃/s,卷取温度605℃;
52.4.酸洗前热轧原料温度<45℃,酸洗介质为工业盐酸,酸液浓度110g/l,酸液温度75℃,漂洗液温度50℃,出口槽漂洗水ph值>6.0、出口槽漂洗水电导率≤50,平整机延伸率3.0%。
53.所得s550nh热轧酸洗高强耐候钢产品厚度为1.2mm,金相组织如图1所示,力学性能如表2所示。
54.实施例2
55.本实施例提供一种薄规格s550nh车厢用高强耐候钢,其化学成分及质量百分比为c:0.053%,si:0.32%,mn:0.60%,p:0.054%,s:0.002%,cu:0.38%,cr:0.55%,ti:0.063%,余量为fe和不可避免杂质,如表1所示。其生产工艺流程为:连铸
→
热坯高温快烧
→
粗轧
→
精轧
→
层流冷却
→
卷取
→
酸洗平整
→
卷取,具体包括下述步骤:
56.1.冶炼:将原料冶炼成上述成分钢水;
57.2.连铸:连铸拉速1.5m/min,铸坯厚度170mm;
58.3.铸坯热直装入炉,入炉温度900℃,加热时间105min,出炉温度1265℃,热轧粗轧出口温度1115℃,中间坯厚度27mm,精轧出口温度879℃,层冷采用两段冷却,前段冷却速率53℃/s,保温温度675℃,保温时间7s,后段冷却速率13℃/s,卷取温度590℃;
59.4.酸洗前热轧原料温度<45℃,酸洗介质为工业盐酸,酸液浓度110g/l,酸液温度80℃,漂洗液温度55℃,出口槽漂洗水ph值>6.0、出口槽漂洗水电导率≤50,平整机延伸率2.8%。
60.所得s550nh热轧酸洗高强耐候钢产品厚度为1.4mm,力学性能如表2所示。
61.实施例3
62.本实施例提供一种薄规格s550nh车厢用高强耐候钢,其化学成分及质量百分比为c:0.059%,si:0.26%,mn:0.55%,p:0.055%,s:0.003%,cu:0.39%,cr:0.62%,ti:0.061%,余量为fe和不可避免杂质,如表1所示。其生产工艺流程为:连铸
→
热坯高温快烧
→
粗轧
→
精轧
→
层流冷却
→
卷取
→
酸洗平整
→
卷取,具体包括下述步骤:
63.1.冶炼:将原料冶炼成上述成分钢水;
64.2.连铸:连铸拉速1.5m/min,铸坯厚度170mm;
65.3.铸坯热直装入炉,入炉温度915℃,加热时间105min,出炉温度1275℃,热轧粗轧出口温度1120℃,中间坯厚度27mm,精轧出口温度890℃,层冷采用两段冷却,前段冷却速率56℃/s,保温温度670℃,保温时间9s,后段冷却速率14℃/s,卷取温度570℃;
66.4.酸洗前热轧原料温度<45℃,酸洗介质为工业盐酸,酸液浓度110g/l,酸液温度80℃,漂洗液温度60℃,出口槽漂洗水ph值>6.0,平整机延伸率2.5。
67.所得s550nh热轧酸洗高强耐候钢产品厚度为1.6mm,力学性能如表2所示。
68.对比例1
69.本对比例的钢为cn110318006b实施例2的钢。
70.表1各实施例及对比例化学成分及耐候指数
[0071][0072]
表2各实施例力学性能
[0073][0074]
本发明缩减了冷轧及退火工序,缩短了工艺流程,节能降本。采用“热坯高温快烧”加热工艺及“去ni、单ti微合金化”成分体系,节能降耗降本,同时也可有效避免“铜脆”现象的产生,产品屈服强度rel:≥550mpa,抗拉强度rm:≥600mpa。
[0075]
显然,上述实施例仅仅是为清楚地说明所作的举例,而并非对实施方式的限定。对于所属领域的普通技术人员来说,在上述说明的基础上还可以做出其它不同形式的变化或变动。这里无需也无法对所有的实施方式予以穷举。而由此所引申出的显而易见的变化或变动仍处于本发明创造的保护范围之中。
再多了解一些
本文用于企业家、创业者技术爱好者查询,结果仅供参考。