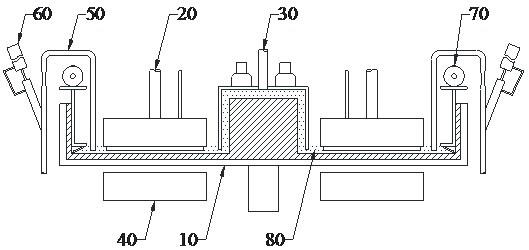
1.本发明涉及一种碳化硅晶体高效抛光方法,属于碳化硅晶体抛光技术领域。
背景技术:
2.目前碳化硅晶体的抛光方法主要有:机械抛光、磁流变抛光、化学机械抛光(cmp)、电化学抛光(ecmp)、催化剂辅助抛光或催化辅助刻蚀(cacp/care)、摩擦化学抛光(tcp,又称无磨料抛光)和等离子辅助抛光(pap)等。化学机械抛光(cmp)技术是目前半导体加工的重要手段,也是目前能将单晶硅表面加工到原子级光滑最有效的工艺方法,是能在加工过程中同时实现局部和全局平坦化的唯一实用技术。cmp的加工效率主要由工件表面的化学反应速率决定。通过研究工艺参数对sic材料抛光速率的影响,结果表明:旋转速率和抛光压力的影响较大;温度和抛光液ph值的影响不大。为提高材料的抛光速率应尽量提高转速,虽然增加抛光压力也可提高去除速率,但容易损坏抛光垫,同时,也易影响sic材料的表面质量。
3.目前的碳化硅抛光方法存在着材料去除率低、表面外观质量低的问题。
技术实现要素:
4.本发明针对现有技术存在的不足,提供了一种碳化硅晶体高效抛光方法,具体技术方案如下:一种碳化硅晶体高效抛光方法,利用环聚型超声振动工作流体电化学抛光设备对碳化硅晶体试件进行抛光,所述环聚型超声振动工作流体电化学抛光设备包括用来对碳化硅晶体试件进行机械抛光的抛光盘、用来施加超声振动的倒扣式超声波清洗槽、用来对碳化硅晶体试件进行电化学加工的电化学组件、辅助振动组件、位于抛光盘内部的工作流体、用来将抛光盘内工作流体排到抛光盘外的n形绝缘排料管、用来驱动绝缘排料管进行排料的驱动机构。
5.上述技术方案的进一步优化,所述抛光盘包括金属旋转槽、套设在金属旋转槽外部的绝缘槽、固定安装在绝缘槽底部的转轴,所述金属旋转槽与绝缘槽连接为一体,所述金属旋转槽的中央设置有圆柱状凸台,所述金属旋转槽的槽底与槽壁交界处设置有多块排列成圆圈状金属弹片,所述金属弹片呈倾斜状设置,所述金属弹片的下端与金属旋转槽固定连接,所述金属弹片的上端指向凸台。
6.上述技术方案的进一步优化,所述电化学组件包括导电套、与负压源相连的绝缘负压管,所述导电套的下端设置有阶梯槽,所述阶梯槽的槽底设置有与绝缘负压管下端相连通的第一通孔,所述阶梯槽包括下半槽和上半槽,所述下半槽与碳化硅晶体试件之间为间隙配合,所述碳化硅晶体试件与下半槽的槽底之间设置有弹性垫圈。
7.上述技术方案的进一步优化,所述倒扣式超声波清洗槽包括槽口朝下的槽体、固定安装在槽体顶部的超声波换能器、用来输送工作流体的绝缘输料管,所述槽体的顶部设置有与绝缘输料管下端相连通的第二通孔;所述槽体套设在凸台的外部,所述槽体的侧壁
与凸台的侧壁之间以及槽体的顶部与凸台的顶部之间均设置有间隙,所述槽体的下端与金属旋转槽的槽底之间设置有间隙。
8.上述技术方案的进一步优化,所述绝缘排料管包括第一竖管体、位于绝缘槽外部的第二竖管体、用来连通第一竖管体和第二竖管体的横管体,所述第一竖管体的下端设置在金属旋转槽的内部且第一竖管体的下端与金属旋转槽的槽底之间设置有间隙。
9.上述技术方案的进一步优化,所述驱动机构包括气缸、与第二竖管体呈倾斜设置的绝缘缸筒、设置在绝缘缸筒内部的绝缘活塞,所述气缸设置有活塞杆,所述第二竖管体的侧壁设置有与绝缘缸筒下端相连通的第三通孔,所述绝缘缸筒的上端设置有供活塞杆活动的第四通孔,所述活塞杆的末端与绝缘活塞固定连接,所述第二竖管体的侧壁还设置有位于第三通孔上方的缩径部,所述缩径部的内壁为单叶双曲面结构,所述缩径部内壁横截面积小于第二竖管体内壁横截面积。
10.上述技术方案的进一步优化,所述辅助振动组件包括导电筒、圆环形绝缘圈、设置在绝缘圈上方且与绝缘圈相接触的多组凸轮,所述导电筒的外侧壁与金属旋转槽的内侧壁之间为间隙配合,所述导电筒的下端设置有向导电筒内部翻折的圆环状内翻边,所述内翻边设置在金属弹片的上方;所述绝缘圈的中部与导电筒的上端固定连接且呈垂直设置,所述凸轮包括轮体,所述轮体的圆周处设置有横截面为弧形的凸起;所述导电筒电连接至直流电源的负极,直流电源的正极与导电套电连接。
11.上述技术方案的进一步优化,所述工作流体是dbu类铁基离子液体与羰基铁粉混合后构成,工作流体中羰基铁粉的质量分数为53%~59%;dbu类铁基离子液体的制备方法为:将1,8-二氮杂双环[5.4.0]十一碳-7-烯与氯代正丁烷按照摩尔比1:1的比例在80~85℃下反应得到中间体;中间体经过洗涤、干燥后,溶于乙腈得到中间体的乙腈溶液,乙腈的使用量按照质量计是中间体的5~8倍;对中间体的乙腈溶液进行搅拌,边搅拌边逐滴加入无水三氯化铁,无水三氯化铁的加入量以摩尔计是氯代正丁烷的4倍,在50~55℃下搅拌反应12h后,使用滤纸过滤,经过旋转蒸发、真空干燥后即得到dbu类铁基离子液体。
[0012]
上述技术方案的进一步优化,所述抛光盘的下方还设置有与导电套呈一一对应设置的电磁铁,电磁铁与直流电源电连接。
[0013]
上述技术方案的进一步优化,利用环聚型超声振动工作流体电化学抛光设备对碳化硅晶体试件进行抛光,抛光总时间为t,抛光盘的作业时间等于t,倒扣式超声波清洗槽进行间歇式超声振动,电化学组件进行间歇式作业,辅助振动组件进行间歇式作业,电磁铁进行间歇式作业;当环聚型超声振动工作流体电化学抛光设备对碳化硅晶体试件进行精抛光,抛光盘的转速为为40r/min,碳化硅晶体试件与金属旋转槽的槽底之间的间隙为3mm,t=nt1,n为正整数,t1为单个精抛周期,t1=t1 t2;在t1时间段内,电化学组件与辅助振动组件在8v的直流电压下电化学加工,t1=8~12s;在t2时间段内,倒扣式超声波清洗槽、辅助振动组件和电磁铁均对碳化硅晶体试件进行抛光作业,倒扣式超声波清洗槽在超声振动时,振动频率为18khz,振幅为28~43μm,k
s1
为振幅随t2的变化斜率,1.4μm/s≤k
s1
≤1.5μm/s;电磁铁与碳化硅晶体试件之间的间距
为5cm,电磁铁与绝缘槽底部之间的间距为3mm,电磁铁在12a的直流电源下进行电磁辅助加工;当环聚型超声振动工作流体电化学抛光设备对碳化硅晶体试件进行超精抛光,抛光盘的转速为为25r/min,碳化硅晶体试件与金属旋转槽的槽底之间的间隙为2mm,t=nt2,n为正整数,t2为单个超精抛周期,t2=t3 t4;在t3时间段内,电化学组件与辅助振动组件在6v的直流电压下电化学加工,t3=6~8s;在t4时间段内,倒扣式超声波清洗槽、辅助振动组件和电磁铁均对碳化硅晶体试件进行抛光作业,倒扣式超声波清洗槽在超声振动时,振动频率为15khz,振幅为25~37μm,k
s2
为振幅随t4的变化斜率,1.2μm/s≤k
s2
≤1.3μm/s;电磁铁与碳化硅晶体试件之间的间距为5cm,电磁铁与绝缘槽底部之间的间距为3mm,电磁铁在9a的直流电源下进行电磁辅助加工。
[0014]
本发明的有益效果:本发明通过对整合现有的机械抛光、超声辅助振动抛光、磁场辅助抛光、电化学辅助加工,使用特制的工作流体作为抛光液,能够对碳化硅晶体的表面进行精抛光和超精抛光,抛光所需时间短,抛光效率高,对亚表面损伤层的伤害小;抛光后的表面无凹坑和划痕,平坦区域面积大。在精抛光作业时,去除率可达到3.91μm/h,表面粗糙度降至7.8nm。在超精抛光作业时,去除率达到0.72μm/h,表面粗糙度降至0.19nm。
附图说明
[0015]
图1为本发明所述环聚型超声振动工作流体电化学抛光设备的结构示意图;图2为本发明所述环聚型超声振动工作流体电化学抛光设备的半剖示意图;图3为本发明所述抛光盘的结构示意图(俯视状态);图4为本发明所述电化学组件的结构示意图;图5为本发明所述辅助振动组件的结构示意图;图6为本发明所述绝缘排料管与驱动机构的连接示意图;图7为本发明所述驱动机构与第二竖管体的连接示意图;图8为实施例2中倒扣式超声波清洗槽的振幅与抛光总时间之间的曲线图;图9为实施例3中倒扣式超声波清洗槽的振幅与抛光总时间之间的曲线图;图10为实施例4中倒扣式超声波清洗槽的振幅与抛光总时间之间的曲线图。
具体实施方式
[0016]
为了使本发明的目的、技术方案及优点更加清楚明白,以下结合附图及实施例,对本发明进行进一步详细说明。应当理解,此处所描述的具体实施例仅仅用以解释本发明,并不用于限定本发明。
[0017]
实施例1如图1所示,所述碳化硅晶体高效抛光方法,利用环聚型超声振动工作流体电化学抛光设备对碳化硅晶体试件90进行抛光,所述环聚型超声振动工作流体电化学抛光设备包括用来对碳化硅晶体试件90进行机械抛光的抛光盘10、用来施加超声振动的倒扣式超声波
清洗槽30、用来对碳化硅晶体试件90进行电化学加工的电化学组件20、用来与电化学组件20配合构成外加电场且与倒扣式超声波清洗槽30协同配合的辅助振动组件70、位于抛光盘10内部的工作流体80、用来将抛光盘10内工作流体80排到抛光盘10外的n形绝缘排料管50、用来驱动绝缘排料管50进行排料的驱动机构60。
[0018]
如图2、3所示,所述抛光盘10包括金属旋转槽11、套设在金属旋转槽11外部的绝缘槽12、固定安装在绝缘槽12底部的转轴13,所述金属旋转槽11与绝缘槽12连接为一体,所述金属旋转槽11的中央设置有圆柱状凸台14,所述金属旋转槽11的槽底与槽壁交界处设置有多块排列成圆圈状金属弹片15,所述金属弹片15呈倾斜状设置,所述金属弹片15的下端与金属旋转槽11固定连接,所述金属弹片15的上端指向凸台14。
[0019]
其中,金属旋转槽11优选合金铸铁制成,绝缘槽12可选环氧树脂制成,在本实施例中,电化学组件20无需旋转,只依靠旋转的抛光盘10即可对碳化硅晶体试件90进行机械抛光;在本实施例中,抛光盘10的转速为40r/min,该转速较低,同时,碳化硅晶体试件90本身不旋转;其带来的去除率(利用称重法测量)肯定不如转速大于40r/min,且碳化硅晶体试件90本身旋转的技术方案;但是,其对碳化硅晶体试件90的表面损伤小,其表面外观质量好。绝缘槽12的设置,能够提高绝缘性。转轴13可由电极驱动。
[0020]
如图4所示,所述电化学组件20包括导电套21、与负压源相连的绝缘负压管22,所述导电套21的下端设置有阶梯槽211,所述阶梯槽211的槽底设置有与绝缘负压管22下端相连通的第一通孔212,所述阶梯槽211包括下半槽和上半槽,所述下半槽与碳化硅晶体试件90之间为间隙配合,所述碳化硅晶体试件90与下半槽的槽底之间设置有弹性垫圈23。
[0021]
所述导电套21优选铜套制成,导电套21外接有导线24;阶梯槽211的横截面为倒t形结构;所述电化学组件20最少有一组,所述导电套21和碳化硅晶体试件90均设置在金属旋转槽11的内部。负压源可以为真空泵,通过负压管22、第一通孔212对阶梯槽211的内部进行抽真空,利用弹性垫圈23可选导电橡胶或导电硅胶制成,主要提高密封,同时在一定压力下,具有良好的导电性。采用真空吸附的方式来固定碳化硅晶体试件90,对碳化硅晶体试件90的表面损伤小;另外,碳化硅晶体试件90与导电套21之间电连接。
[0022]
如图2所示,所述倒扣式超声波清洗槽30包括槽口朝下的槽体31、固定安装在槽体31顶部的超声波换能器32、用来输送工作流体80的绝缘输料管33,所述槽体31的顶部设置有与绝缘输料管33下端相连通的第二通孔;所述槽体31套设在凸台14的外部,所述槽体31的侧壁与凸台14的侧壁之间以及槽体31的顶部与凸台14的顶部之间均设置有供工作流体80流动的间隙(小于或等于1cm),所述槽体31的下端与金属旋转槽11的槽底之间设置有供工作流体80流动的间隙(小于或等于1cm)。
[0023]
首先,通过绝缘输料管33向槽体31的内部输送工作流体80,槽体31与凸台14之间的间隙会很快填满工作流体80,并流到金属旋转槽11的内部;金属旋转槽11的内部为环形槽结构。通过绝缘排料管50将金属旋转槽11内在进行清洗所得含有杂质的工作流体80排放到金属旋转槽11的外部,控制在绝缘排料管50处的排放速率以及在绝缘输料管33处的输入速率,能使得金属旋转槽11内的工作流体80处于动态平衡中;同时,清洗所产生的一部分废渣会被排出,源源不断流入“洁净”的工作流体80,使得金属旋转槽11内的工作流体80能够保持足够的“纯度”,从而避免废渣过多带来的抛光质量下降的事情发生。
[0024]
如图5所示,所述辅助振动组件70包括导电筒71、圆环形绝缘圈72、设置在绝缘圈
72上方且与绝缘圈72相接触的多组凸轮,所述导电筒71的外侧壁与金属旋转槽11的内侧壁之间为间隙配合,所述导电筒71的下端设置有向导电筒71内部翻折的圆环状内翻边73,所述内翻边73设置在金属弹片15的上方;所述绝缘圈72的中部与导电筒71的上端固定连接且呈垂直设置,即横截面为t形结构,所述凸轮包括轮体74,所述轮体74的圆周处设置有横截面为弧形的凸起75;所述导电筒71电连接至直流电源的负极,直流电源的正极与导电套21电连接。
[0025]
其中,导电筒71与直流电源的负极之间以及直流电源的正极与导电套21之间的电连接均采用柔性导线24来电连接;导电筒71可采用铜合金制成。在初始状态下,内翻边73正好压着金属弹片15,所述轮体74也压着绝缘圈72,随着轮体74的转动,当凸起75开始碰触绝缘圈72并最终离开绝缘圈72的过程,所述导电筒71会向下运动,并会对金属弹片15进行压紧,从而产生弹力,轮体74所在高度固定不变;随着轮体74的不断转动,所述导电筒71会不断的上下振动,同时会带动内翻边73也不断的上下振动,所述金属弹片15起到提供弹力、缓冲的作用;最优选的是内翻边73与导电筒71之间的横截面为l形结构,在内翻边73上下振动的过程中,内翻边73在初始时刚好与金属旋转槽11内工作流体80液面齐平,从而促使工作流体80的液面源源不断的产生波纹,一方面,能够促使一部分工作流体80内的磨料流向碳化硅晶体试件90的一侧,碳化硅晶体试件90的另一侧在超声波换能器32和槽体31所提供的超声振动作用下,碳化硅晶体试件90的两侧会有大量的磨料聚集并集中在碳化硅晶体试件90与金属旋转槽11的槽底之间,碳化硅晶体试件90与金属旋转槽11的槽底之间的间隙优选为3-5mm,最优选为3mm;从而解决由于间隙所带来的机械抛光效果不高的缺陷。同时,利用超声振动,能够进一步提高抛光效果。
[0026]
所述辅助振动组件70的结构简单,无法将辅助振动组件70替换为另一个超声波清洗槽,同时,辅助振动组件70的结构简单。所述辅助振动组件70不但能够与电化学组件20配合构成外加电场,而且还能与倒扣式超声波清洗槽30协同配合对碳化硅晶体试件90的两侧施加振动,从而进一步提高抛光效果。
[0027]
所述导电筒71电连接至直流电源的负极,也就使得金属旋转槽11与直流电源的负极相连;直流电源的正极与导电套21电连接,与就使得碳化硅晶体试件90与直流电源的正极相连。当碳化硅晶体试件90与工作流体80接触时,工作流体80为导电型非牛顿流体,构成闭合回路形成外加电场,从而在电化学作用下,进一步提高抛光效果。
[0028]
如图6所示,所述绝缘排料管50包括第一竖管体51、位于绝缘槽12外部的第二竖管体53、用来连通第一竖管体51和第二竖管体53的横管体52,所述第一竖管体51的下端设置在金属旋转槽11的内部且第一竖管体51的下端与金属旋转槽11的槽底之间设置有间隙。
[0029]
所述第一竖管体51、第二竖管体53和横管体52均采用绝缘材料制成,初始时,可利用虹吸原理来进行排料;也可以利用驱动机构60所产生的驱动力将金属旋转槽11内的工作流体80通过绝缘排料管50排放至金属旋转槽11外。
[0030]
如图7所示,所述驱动机构60包括气缸62、与第二竖管体53呈倾斜设置的绝缘缸筒61、设置在绝缘缸筒61内部的绝缘活塞64,所述气缸62设置有活塞杆621,所述第二竖管体53的侧壁设置有与绝缘缸筒61下端相连通的第三通孔532,所述绝缘缸筒61的上端设置有供活塞杆621活动的第四通孔,所述活塞杆621的末端与绝缘活塞64固定连接,所述第二竖管体53的侧壁还设置有位于第三通孔532上方的缩径部531,所述缩径部531的内壁为单叶
双曲面结构,所述缩径部531内壁横截面积小于第二竖管体53内壁横截面积。
[0031]
其中,气缸62与绝缘缸筒61之间通过设置连杆固定连接。当绝缘活塞64在气缸62的驱动下向远离第三通孔532的方向运动时,此时相当于进行“抽吸”作业,能够促使将金属旋转槽11内的工作流体80通过第一竖管体51、横管体52、第二竖管体53给抽出;当绝缘活塞64在气缸62的驱动下向靠近第三通孔532的方向运动时,此时相当于进行“挤压”作业,使得第二竖管体53和绝缘缸筒61内的工作流体80,一部分从第二竖管体53的下端排出,另一部分会逆流向上,由于设置缩径部531,逆流向上的那部分工作流体80的量减少。尤其是工作流体80为非牛顿流体时,逆流向上的阻力会进一步加大,从而使得向下排出的量显著提高。
[0032]
本实施例中,采用驱动机构60来促使绝缘排料管50进行排料,在解决绝缘性的同时,最大限度保证安全性;相对于直接使用泵来驱动排料,容易因为导电导致安全问题,甚至泵被损坏。
[0033]
相对于二次锥面来说,内壁为单叶双曲面结构的缩径部531,其流动阻力较小,同时,从上而下的流动连续性更好。
[0034]
工作流体80是dbu类铁基离子液体与羰基铁粉混合后构成,工作流体80中羰基铁粉的质量分数为53%~59%,羰基铁粉的平均粒径为5μm,含fe纯度大于97%,有效磁导率大于3;dbu类铁基离子液体的制备方法为:将0.35mol的1,8-二氮杂双环[5.4.0]十一碳-7-烯与0.35mol的氯代正丁烷在80~85℃下反应得到中间体,对中间体洗涤、干燥;取0.7mol的中间体,溶于800~1200g乙腈得到中间体的乙腈溶液,乙腈的使用量按照质量计是中间体的5~8倍;对中间体的乙腈溶液进行搅拌,边搅拌边逐滴加入1.4mol无水三氯化铁,在50~55℃下搅拌反应12h后,使用滤纸过滤,经过旋转蒸发、真空干燥后即得到dbu类铁基离子液体。
[0035]
1,8-二氮杂双环[5.4.0]十一碳-7-烯的简称是dbu,其分子式为c9h
16
n2。dbu类铁基离子液体的简称为[c4dbu]cl/2fecl3,可采用dbu-fe-il来标识。其中,dbu-fe-il中存在阴离子fecl4(-)、fe2cl7(-),括号内是电荷数。
[0036]
当工作流体80中的离子液体为dbu-fe-il时,该工作流体80标记为流体ld;对流体ld进行《非牛顿流体检测》,方案如下:方案a利用旋转式在线粘度计测量流体ld在不同转速(50r/min、100r/min、150r/min、200r/min)下的粘度,测量温度为25
±
0.5℃;结果发现,在初始时,初始粘度为1260~1370mpa
·
s;在50r/min、100r/min、150r/min、200r/min的转速下,随着转速的增加,与初始粘度之间的粘度差越来越大,差值最小都在500mpa
·
s以上。这说明,流体ld具有剪切变稠的变化。
[0037]
方案b将500ml流体ld倒入烧杯中,使用搅拌杆在烧杯中的流体ld中转动,当转速在75r/min以上时,发现流体ld沿着搅拌杆向上爬;当转速在130r/min时,会很明显发现烧杯内流体ld的液面处有凸起。
[0038]
经过工作流体80是dbu类铁基离子液体与羰基铁粉混合后构成,易形成类似“磁浆”;通过方案a、b可知,流体ld同时具有剪切变稠和爬杆性;因此,判定流体ld为非牛顿流
体。
[0039]
由于流体ld具有剪切变稠的性能,因此,在逆流至缩径部531时,阻力会变大;同时,在超声振动以及辅助振动组件70所产生的振动作用下,再加上是间歇式振动,相当于对碳化硅晶体试件90施加持续的脉冲式冲击;碳化硅晶体试件90一端施加的超声振动更为“密集”,另一端使用辅助振动组件70所施加的振动较为“稀疏”,能够从总体上,保证工作流体80从碳化硅晶体试件90的一端流动至另一端,从而使得被抛光下来的颗粒被带走,从而保证被抛光的区域的洁净度;同时,碳化硅晶体试件90的两端都存在机械振动,这就促使有更多的抛光颗粒和碳化硅晶体试件90的表面为接触,该接触柔性接触,对碳化硅晶体试件90进行非常小的幅度切削,防止碳化硅晶体试件90产生较大的破坏层和产生较大的裂纹,导致外观质量显著下降。在幅度较强且频率很大的振动作用下,会产生较大幅度和速率的剪切,从而使得工作流体80变为类似固体的性质;当停止时,又恢复其流动特性的现象。
[0040]
而在磁场的作用下,工作流体80的流变特性发生急剧的转变,表现为类固体的性质,撤掉磁场时又恢复其流动特性的现象。铁粉相当于柔性磨料,其与化硅晶体试件90之间具有快速的相对运动,使碳化硅晶体试件90表面受到很大的剪切力,从而使碳化硅晶体试件90表面材料被去除。
[0041]
实施例2在实施例1的基础上,如图1所示,所述抛光盘10的下方还设置有与导电套21呈一一对应设置的电磁铁40,电磁铁40与直流电源电连接。
[0042]
所述碳化硅晶体高效抛光方法,包括:利用环聚型超声振动工作流体电化学抛光设备对碳化硅晶体试件90进行抛光,抛光总时间为t,抛光盘10的作业时间等于t,倒扣式超声波清洗槽30进行间歇式超声振动,电化学组件20进行间歇式作业,辅助振动组件70进行间歇式作业,电磁铁40进行间歇式作业。
[0043]
在本实施例中,利用环聚型超声振动工作流体电化学抛光设备对碳化硅晶体试件90进行精抛光,抛光盘10的转速为为40r/min,碳化硅晶体试件90与金属旋转槽11的槽底之间的间隙为3mm,t=nt1,n为正整数,t1为单个精抛周期,t1=t1 t2,如图8所示,在t1时间段内,电化学组件20与辅助振动组件70在8v的直流电压下电化学加工,t1=8~12s,本实施例中优选t1=8s;t2=10~15s,本实施例中优选t2=10s;在t2时间段内,倒扣式超声波清洗槽30、辅助振动组件70和电磁铁40均对碳化硅晶体试件90进行抛光作业,倒扣式超声波清洗槽30在超声振动时,振动频率为18khz,振幅为28~43μm,k
s1
为振幅随t2的变化斜率,1.4μm/s≤k
s1
≤1.5μm/s,优选地,图8中的k
s1
=1.5μm/s,电磁铁40与碳化硅晶体试件90之间的间距为5cm,电磁铁40与绝缘槽12底部之间的间距为3mm,电磁铁40在12a的直流电源下进行电磁辅助加工。
[0044]
在本实施例中,碳化硅晶体试件90在初始时,其表面粗糙度为720~860nm,表面存在尖峰、凹坑等表面损伤。抛光总时间t=30min时,即可使去除率达到3.91μm/h,表面粗糙度降至7.8nm,表面无凹坑和划痕,平坦区域面积大。
[0045]
实施例3在实施例1的基础上,如图1所示,所述抛光盘10的下方还设置有与导电套21呈一
一对应设置的电磁铁40,电磁铁40与直流电源电连接。
[0046]
所述碳化硅晶体高效抛光方法,包括:利用环聚型超声振动工作流体电化学抛光设备对碳化硅晶体试件90进行抛光,抛光总时间为t,抛光盘10的作业时间等于t,倒扣式超声波清洗槽30进行间歇式超声振动,电化学组件20进行间歇式作业,辅助振动组件70进行间歇式作业,电磁铁40进行间歇式作业。
[0047]
在本实施例中,环聚型超声振动工作流体电化学抛光设备对碳化硅晶体试件90进行超精抛光,抛光盘10的转速为为25r/min,碳化硅晶体试件90与金属旋转槽11的槽底之间的间隙为2mm,t=nt2,n为正整数,t2为单个超精抛周期,t2=t3 t4;在t3时间段内,电化学组件20与辅助振动组件70在6v的直流电压下电化学加工,t3=6~8s,本实施例中优选t3=6s;t4=9~12s,本实施例中优选t4=9s;在t4时间段内,倒扣式超声波清洗槽30、辅助振动组件70和电磁铁40均对碳化硅晶体试件90进行抛光作业,倒扣式超声波清洗槽30在超声振动时,振动频率为15khz,振幅为25~37μm,k
s2
为振幅随t4的变化斜率,1.2μm/s≤k
s2
≤1.3μm/s,优选地,图9中的k
s2
=1.33μm/s,电磁铁40与碳化硅晶体试件90之间的间距为5cm,电磁铁40与绝缘槽12底部之间的间距为3mm,电磁铁40在9a的直流电源下进行电磁辅助加工。
[0048]
在本实施例中,碳化硅晶体试件90在初始时,其表面粗糙度为720~860nm,在本实施例中,碳化硅晶体试件90在初始时,其表面粗糙度为120~200nm,表面存在尖峰、凹坑等表面损伤。抛光总时间t=30min时,即可使去除率达到0.72μm/h,表面粗糙度降至0.19nm。
[0049]
实施例4在实施例1的基础上,如图1所示,所述抛光盘10的下方还设置有与导电套21呈一一对应设置的电磁铁40,电磁铁40与直流电源电连接。
[0050]
所述碳化硅晶体高效抛光方法,包括:利用环聚型超声振动工作流体电化学抛光设备对碳化硅晶体试件90进行抛光,抛光总时间为t,抛光盘10的作业时间等于t,倒扣式超声波清洗槽30进行间歇式超声振动,电化学组件20进行间歇式作业,辅助振动组件70进行间歇式作业,电磁铁40进行间歇式作业。
[0051]
在本实施例中,利用环聚型超声振动工作流体电化学抛光设备对碳化硅晶体试件90进行精抛光,抛光盘10的转速为为40r/min,碳化硅晶体试件90与金属旋转槽11的槽底之间的间隙为3mm,t=nt3,n为正整数,t3为单个抛光周期,t1=t5 t6,如图10所示:在t5时间段内,电化学组件20与辅助振动组件70在8v的直流电压下电化学加工,t5=8s;t6=10s;在t2时间段内,倒扣式超声波清洗槽30、辅助振动组件70和电磁铁40均对碳化硅晶体试件90进行抛光作业,倒扣式超声波清洗槽30在超声振动时,振动频率为18khz,振幅始终保持为35.5
±
0.2μm,电磁铁40与碳化硅晶体试件90之间的间距为5cm,电磁铁40与绝缘槽12底部之间的间距为3mm,电磁铁40在12a的直流电源下进行电磁辅助加工。
[0052]
在本实施例中,碳化硅晶体试件90在初始时,其表面粗糙度为720~860nm,表面存
在尖峰、凹坑等表面损伤。抛光总时间t=30min时,去除率为4.03μm/h,表面粗糙度为26.5nm;即使随着抛光总时间的延长,表面粗糙度的下降幅度不超过8.2%;但是,随着振幅从35.5μm增加至43μm的过程中,亚表面损伤层深度从43.221nm增加至71.819nm。
[0053]
实施例5在实施例1的基础上,如图1所示,所述抛光盘10的下方还设置有与导电套21呈一一对应设置的电磁铁40,电磁铁40与直流电源电连接。
[0054]
所述碳化硅晶体高效抛光方法,包括:利用环聚型超声振动工作流体电化学抛光设备对碳化硅晶体试件90进行抛光,抛光总时间为t,抛光盘10的作业时间等于t,倒扣式超声波清洗槽30、电化学组件20、辅助振动组件70、电磁铁40的作业时间均等于t;抛光盘10的转速为为40r/min,碳化硅晶体试件90与金属旋转槽11的槽底之间的间隙为3mm,电化学组件20与辅助振动组件70在8v的直流电压下电化学加工,倒扣式超声波清洗槽30在超声振动时,振动频率为18khz,振幅始终保持为35.5
±
0.2μm,电磁铁40与碳化硅晶体试件90之间的间距为5cm,电磁铁40与绝缘槽12底部之间的间距为3mm,电磁铁40在12a的直流电源下进行电磁辅助加工。
[0055]
在本实施例中,碳化硅晶体试件90在初始时,其表面粗糙度为720~860nm,表面存在尖峰、凹坑等表面损伤。抛光总时间t=30min时,去除率超过22.1μm/h,表面粗糙度大于或等于187nm,表面存在尖峰、凹坑等表面损伤。
[0056]
实施例6试验x在使用利用环聚型超声振动工作流体电化学抛光设备对碳化硅晶体试件90进行抛光时,不开启电磁铁40;也就是说,本试验与实施例2的区别在于,电磁铁40在抛光作业时不工作。
[0057]
在本实施例中,碳化硅晶体试件90在初始时,其表面粗糙度为720~860nm,表面存在尖峰、凹坑等表面损伤。抛光总时间t=30min时,去除率只有1.34μm/h,表面粗糙度为41.3nm。
[0058]
试验y在使用利用环聚型超声振动工作流体电化学抛光设备对碳化硅晶体试件90进行抛光时,将工作流体80中的dbu类铁基离子液体替换为去离子水;也就是说,本试验与实施例2的区别在于,工作流体80中是否使用dbu类铁基离子液体。
[0059]
在本实施例中,碳化硅晶体试件90在初始时,其表面粗糙度为720~860nm,表面存在尖峰、凹坑等表面损伤。抛光总时间t=30min时,去除率只有1.06μm/h,表面粗糙度为78.7nm。
[0060]
试验z在使用利用环聚型超声振动工作流体电化学抛光设备对碳化硅晶体试件90进行抛光时,将工作流体80中的dbu类铁基离子液体替换为铁基离子液体bmim[fecl4],bmim[fecl4]的中文名为1-丁基-3-甲基咪唑四氯铁酸盐。
[0061]
在本实施例中,碳化硅晶体试件90在初始时,其表面粗糙度为720~860nm,表面存在尖峰、凹坑等表面损伤。抛光总时间t=30min时,去除率只有0.77μm/h。
[0062]
试验p
在使用利用环聚型超声振动工作流体电化学抛光设备对碳化硅晶体试件90进行抛光时,将工作流体80中的dbu类铁基离子液体替换为铁基离子液体[c8mim]cl.fecl3,[c8mim]cl.fecl3的中文名为1-辛基-3-甲基咪唑四氯铁酸盐。
[0063]
在本实施例中,碳化硅晶体试件90在初始时,其表面粗糙度为720~860nm,表面存在尖峰、凹坑等表面损伤。抛光总时间t=30min时,去除率只有0.69μm/h。
[0064]
在上述实施例中,使用白光干涉仪进行表面粗糙度的测量。亚表面损伤层深度采用非接触式干涉仪进行检测。
[0065]
由实施例3-5可知,在采用超声辅助振动、磁场辅助抛光时,必须采用间歇式作业,在超声辅助振动以及磁场辅助抛光停止作业时,必须使用电化学组件20与辅助振动组件70进行电化学加工,从而最大限度减小亚表面损伤层深度,改善抛光的表面质量。
[0066]
工作流体80中只有离子液体与羰基铁粉,并无表面活性剂,同时不含有腐蚀性强的强碱、强酸,成分简单,该工作流体80需要现配现用。工作流体80中的[c4dbu]cl/2fecl3、bmim[fecl4]、[c8mim]cl.fecl3都选用西安齐岳生物科技有限公司所生产。
[0067]
羰基铁粉在[c4dbu]cl/2fecl3、bmim[fecl4]、[c8mim]cl.fecl3中的抗沉降性各不相同。
[0068]
采用自然沉降法测试磁流变抛光液的沉降稳定性,沉降率=h1/(h1 h2),h1为上层清液高度,h2为下沉浊液高度。
[0069]
采用[c4dbu]cl/2fecl3所制成的工作流体80,其沉降率为7.25%;而使用bmim[fecl4]、[c8mim]cl.fecl3所对应的沉降率为28.73%、33.43%。这说明,本发明所使用的工作流体80,具有更好抗沉降作用,稳定性好,不易发生颗粒的沉降、团聚和生锈现象,不影响抛光性能。
[0070]
如果直接在碳化硅晶体试件90的上方施加超声振动,然后使得碳化硅晶体试件90的表面与金属旋转槽11之间接触,无论其之间是否放置抛光垫,都会导致破碎断裂情况严重,表面颗粒脱落、剥落等表面损伤较多,亚表面损伤层的裂纹数量、深度都较严重。
[0071]
本发明采用在碳化硅晶体试件90的一侧施加超声振动,在另一侧施加普通机械振动,发现会使碳化硅晶体试件90的破碎断裂情况得到改善,表面颗粒脱落、剥落等表面损伤减少,亚表面损伤层的裂纹数量、深度等都有较大程度降低,最终获得非常优异的表观质量。
[0072]
以上所述仅为本发明的较佳实施例而已,并不用以限制本发明,凡在本发明的精神和原则之内所作的任何修改、等同替换和改进等,均应包含在本发明的保护范围之内。
再多了解一些
本文用于企业家、创业者技术爱好者查询,结果仅供参考。