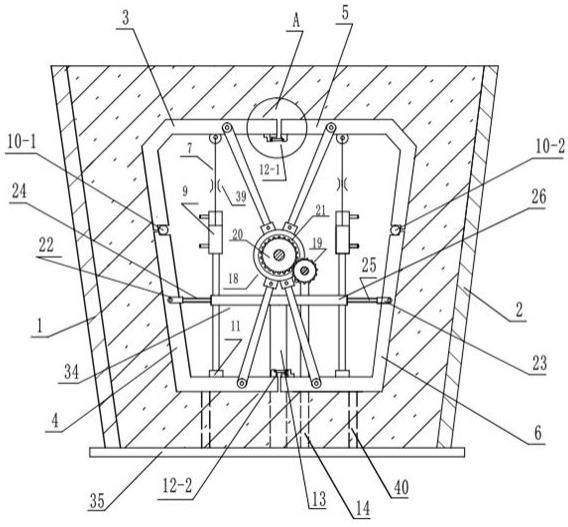
1.本发明涉及建筑技术,特别是建筑构件浇筑模板的自动装拆。
背景技术:
2.目前,在建筑技术领域,大量使用着各种槽、管、箱类的构件,用这些构件来输送水或其他各种液体的管路。制备大型槽管类构件一般在施工现场浇筑,用于构件浇筑成型的模板由外模板和内模板构成,在内外模板之间预先配置好预应力钢筋,钢筋绑扎结实后在内外模板的间隙中浇筑搅拌好的混凝土,待混凝土凝固后将模板拆掉,槽、管类构件即制备完成。由于浇筑混凝土的操作比较简单,所用时间也很短,因此决定槽、管类构件制备周期的长短主要取决于模板的装配时间。然而,由于大型内模的支撑结构较为复杂,其装配、拆卸繁琐,需要完全依靠人工将构成内模的多种板材、角铁、管材、异型构件等通过不同的连接件组装在一起,费时费力,远不能满足争时间抢进度的速度要求。而且,由于装配空间狭小,人在其中操作,极易碰伤,存有安全隐患。因此,研究内模的快速装配,即成为妥善解决这类建筑构件的关键因素。
3.中国专利cn2020107108313号、名称为“一种模板化自适应门窗洞口可调模板系统及其施工方法”,它公开了一种封闭框型建筑构件的混凝土浇筑模板,但其模板支撑系统仍需人工搭建,且这种模板结构难以支持大型厚重的混凝土浇筑。又如中国专利cn202022960366.7、名称为“一种用于雨污水检查井流槽施工的定制模板”,它公开的这种模板为“所述矩形定型模板包括方形内支撑,所述方形内支撑相对两侧固定安装有方形模板,所述弧形定型模板包括弧形内支撑,所述弧形内支撑外侧固定安装有弧形模板;所述矩形定型模板与弧形定型模板之间为拆卸连接”。但其构件分为矩形定型模板和弧形定型模板两部分,其截面形状为开口式结构,并不适用于封闭的建筑构件,且在装配时仍需人工操作,不能解决模板装配自动化的问题。
4.另外,在建筑物的突发事故中,需要快速完成损毁建筑物或城市水气电公共服务系统的搭建,建筑恢复时间紧、任务重,现场快速浇筑槽、管、箱类成为第一关键要素,而模板装配又成为耗时最多的工序。有鉴于此,业内普遍要求开发出一种建筑浇筑模板、这种模板适于自动化装拆来代替人工装配,以高效完成建筑构件的浇筑。
技术实现要素:
5.本发明的目的在于提供一种混凝土浇筑模板的自动装拆方法,它以机械动力为驱动力,可以在单片机的控制下,自动控制浇筑模板各部件的收放,完成混凝土浇筑模板的组装。另外,在混凝土浇筑完毕后,又能自动收缩,减少粘结阻力,迅速使模板与混凝土层脱离,完成内模拆除操作。本发明的浇筑模板可反复拆装,具有结构简单、装配效率高、可重复使用、无废料排放的优点。
6.本发明所述问题是以下述技术方案解决的:一种混凝土浇筑模板的自动拆装方法,所述方法使用一个自动拆装模板,所述自
动拆装模板包括外模、内模和控制部分,所述控制部分用于控制内模的装配;所述外模由左外模板和右外模板构成;所述内模设有四块模板,分为左上模板、左下模板、右上模板和右下模板,四块模板拼接成构件浇筑所需内模的截面形状;所述内模上与外模相对的面上均铺设钢板;四块模板均为由水平梁和竖直梁构成的角形;处于上下位置的模板的竖直梁铰接,铰接的竖直梁在装配完成后,处于一条直线上,处于左右位置的模板的水平梁搭接,搭接的水平梁在装配完成后位于一条水平线上;水平梁在其水平铰接点上由其对应的驱动部分驱动旋转,当左上模板、右上模板、左下模板和右下模板的水平梁被各自的驱动部分驱动分别围绕各自的铰接点进行放开或收紧操作,即完成内模的装配或拆卸作业。
7.上述混凝土浇筑模板的自动拆装方法,在进行内模水平梁的撑开操作时,在内模中增设驱动盘和驱动部分,所述驱动部分分为四个结构相同的驱动构件,分别是左上驱动构件、左下驱动构件、右上驱动构件和右下驱动构件,四个驱动构件分别与驱动盘传动连接;其中,左上驱动构件包括左上推拉杆和左上卡爪,所述左上模板与左上推拉杆的一端铰接,铰接点靠近水平梁的搭接处,左上推拉杆的另一端连接在左上卡爪上;其余三个驱动构件与左上驱动构件的结构相同;驱动盘壳体通过机架支柱支承在构件制作平台上;所述驱动盘为固定在从动轴上的圆盘,驱动盘的一个侧面设有单头螺旋,单头螺旋为1-4圈矩形螺纹,所述矩形螺纹与所述左上卡爪的啮合部分构成螺纹副;其余左下卡爪、右上卡爪、右下卡爪也与单头螺旋构成螺纹副,但啮合点分布在单头螺旋的不同方位;从动轴上还设置从动齿轮,从动齿轮与设置在主动轴上的主动齿轮啮合,主动轴由电机驱动,完成驱动四块模板的收或放操作。
8.上述混凝土浇筑模板的自动拆装方法,在模板装配时,在内模的水平梁完成撑开操作后,在内模中增设液压支撑杆,所述液压支撑杆为两个,分别竖直设置在左上模板和左下模板之间、以及右上模板和右下模板之间;所述液压支撑杆中设有液压缸,所述液压支撑杆为液压缸的活塞杆;在液压支撑杆和左下模板之间、或者液压支撑杆和右下模板之间设有第一压力传感器;当液压支撑杆被驱动时,第一压力传感器输出油压信号,若油压达到阈值后,液压缸停止供油,液压支撑杆即支撑到位。
9.上述混凝土浇筑模板的自动拆装方法,在模板装配时,在内模的水平梁完成撑开操作时,在内模中增设螺杆锁紧微调机构,所述螺杆锁紧微调机构设置在左下模板和右下模板之间;螺杆锁紧微调机构包括:锁紧螺母、左安装座、右安装座、左旋螺杆和右旋螺杆;所述左安装座设置在左下模板侧边的中上部,左旋螺杆与左安装座连接,右安装座设置在右下模板侧边的中上部,右旋螺杆与右安装座连接,锁紧螺母的两端分别与左旋螺杆和右旋螺杆构成旋向相反的螺纹副;螺杆锁紧微调机构撑开竖直梁,防止模板竖直梁的铰接点内移。
10.上述混凝土浇筑模板的自动拆装方法,在模板装配时,在内模增设锁栓机构,所述锁栓机构构成中包括左栓座、右栓座、栓板、栓轴,所述左栓座分别固定在左下模板或左上模板的水平梁的端部,所述右栓座分别固定在右下模板或右上模板的水平梁的端部,栓板的一端铰接在左栓座的开口槽内,栓板的另一端插入右栓座的开口槽内并被栓轴所锁紧,防止水平梁意外移位。
11.上述混凝土浇筑模板的自动拆装方法,在模板装配时,在内模增设水平位置检测传感器,所述水平位置检测传感器为两个,其中,第一水平位置检测传感器由第一磁钢和第
一霍尔传感器组成,第一磁钢和第一霍尔传感器分别固定在左上模板的水平梁的端部和右上模板的水平梁的端部;第二水平位置检测传感器中的第二磁钢和第二霍尔传感器分别固定在左下模板的水平梁的端部和右下模板的水平梁的端部;所述第一磁钢和第一霍尔传感器之间、第二磁钢和第二霍尔传感器之间,均处于各自最接近的相对位置上;两个水平位置检测传感器用于检测水平梁装配是否到位。
12.上述混凝土浇筑模板的自动拆装方法,在模板装配时,所有操作由控制部分进行控制,所述控制部分包括cpu、启动按钮、第一水平位置检测传感器、第二水平位置检测传感器、第一压力传感器、电磁阀和电机控制芯片;所述启动按钮连接在cpu的p0.0端口,所述第一水平位置检测传感器、第二水平位置检测传感器和第一压力传感器分别连接在cpu的p1.0端口-p1.2端口,所述电机控制芯片的两个信号输入端分别连接在cpu的p2.3端口—p2.4端口,所述电磁阀的两个线圈控制输入端分别连接在cpu的p2.1端口—p2.2端口。
13.上述混凝土浇筑模板的自动拆装方法,所述方法涉及的内模的截面形状为长方形、梯形或圆形。
14.上述混凝土浇筑模板的自动拆装方法,所述方法按下述步骤进行:a. 将内模构件移动至构件制作平台上,使驱动盘转动,与驱动盘的单头螺旋啮合的四个卡爪向远离轴心的方向移动,四块模板被支起,完成内模的装配;b. 第一水平位置检测传感器检测到第一霍尔传感器与第一磁钢位于一条直线上、第二水平位置检测传感器检测到第二霍尔传感器与第二磁钢位于一条直线上,则说明装配到位;第一水平位置检测传感器和第二水平位置检测传感器向cpu发出驱动盘停止转动的信号,使电机断电,继而停止驱动盘的转动;c. 第一水平位置检测传感器和第二水平位置检测传感器给cpu发出给液压支撑杆的液压缸供油,驱动液压支撑杆移动到位;第一压力传感器输出油压信号,由cpu与预存的压力阈值比较后,判断达标后,液压缸停止供油;d. 将锁栓机构中的栓板一端插入右栓座的开口槽内,用栓轴锁紧;e. 调整螺杆锁紧微调机构中的锁紧螺母,对左下模板和右下模板之间的间距作精确的微调,使内模装配的预紧力达到最佳状态;f. 内模装配完成,进行混凝土浇筑、振捣,完成后进入凝固和养护阶段;g、拆模时,与上述操作顺序相反,完成卸模操作。
15.有益效果本发明将预制构件的内模设置成四块活动的模板,四块模板通过铰接构成可开合的机构,通过设置具有单头螺旋的驱动盘,使四个卡爪上的啮合齿在单头螺旋的槽中作径向移动实现四个卡爪向轴心聚拢或分散,从而带动四块模板上的水平梁转动,完成整个预制构件内模的收紧或打开。由于设置了一个带有单头螺旋的驱动盘,控制一个驱动盘即可控制四个推拉杆的动作,从而使操作简单化、自动化,大大减少了装配所需工时。本发明除使装配驱动动作简单化外,还通过设置液压支撑杆,提供进一步的支撑力,使模板的稳定性和安全性得到第二级保障;通过设置锁栓机构,提供第三级安全保证,从而使本发明的目的实现获得三级保证。除此之外,本发明还可根据预制构件长度的需求将多个内模利用法兰盘连接在一起,可以适应更多类型构件制备的需要。
16.除此之外,本发明可以采用统一规格的模板和传动支承构件,拆除后,可重复使
用,避免了已有技术中完全依靠人工将多种板材、角铁、管材、异型构件等通过不同的连接件组装在一起,拆除后,无法重复使用,造成大量钢材的废弃和浪费,节省了材料消耗,避免了废料的污染,也免除了废物后续处理的投入。
17.总之,本发明使构件浇筑模板具有装配速度快、结构整体性能好的优点,在抢险或突发事故中能够快速完成桥梁模板的搭建,解决了现有人工装配模板费事费力、工时多、周期长及材料浪费的缺点。
附图说明
18.下面结合附图对本发明作进一步详述。
19.图1是本发明的模板结构示意图;图2是图1的左视图;图3是驱动部分示意图;图4是图3的剖视图;图5是卡爪与驱动盘位置关系示意图;图6是卡爪外形示意图;图7是驱动盘的单头螺旋示意图;图8是驱动盘壳体的剖视图;图9 是锁栓机构的结构示意图;图10是控制部分电原理图。
20.图中各标号分别表示为: 1、左外模板,2、右外模板,3、左上模板,4、左下模板,5、右上模板,6、右下模板,7、液压支撑杆,9、液压缸,10-1、左铰接点,10-2、右铰接点,11、液压缸座,p1、第一压力传感器,12-1、上部锁栓机构,12-2、下部锁栓机构,13、机架支柱,14、主动轴支座,15、从动轴支座,16、主动轴,17、从动轴,18、驱动盘壳体,19、主动齿轮,20、从动齿轮,21、驱动盘,21-1、挡块,21-2、单头螺旋,22、左安装座,23、右安装座,24、左旋螺杆,25、右旋螺杆,26、锁紧螺母,27、左栓座,28、右栓座,29、栓板,30、栓轴,31、电机,32、电机座,34、螺杆锁紧微调机构,35、构件制作平台,36、钢板,s1、第一水平位置检测传感器,37-1、第一磁钢,38-1、第一霍尔传感器,s2、第二水平位置检测传感器,37-2、第二磁钢,38-2、第二霍尔传感器,39、导向滑轨,40、模板支腿,101、左上卡爪,102、左上推拉杆,201、左下卡爪,202、左下推拉杆,301、右上卡爪,302、右上推拉杆,401、右下卡爪,402、右下推拉杆。
具体实施方式
21.本发明提供了一种用于混凝土浇筑的自动拆装模板及拆装方法,用于解决预制构件生产过程中因内模结构复杂,拆装费时费力、材料浪费的问题。它主要由外模及内模组成,外模和内模之间为中空的腔室,混凝土即浇筑在腔室内,凝固后即成为建筑物的构件。
22.图1-图10是本发明的模板构成图纸,它包括外模和内模,所述外模由左外模板1和右外模板2构成;所述内模上与外模相对的面上均铺设钢板36。内模由四块模板构成,分为左上模板3、左下模板4、右上模板5和右下模板6,其中,所述左上模板3的竖直梁和左下模板4的竖直梁铰接于左铰接点10-1,右上模板5的竖直梁和右下模板6的竖直梁铰接于右铰接点10-2,左上模板3的水平梁和右上模板5的水平梁在装配完成后位于一条水平线上,左下
模板4的水平梁和右下模板6的水平梁在装配完成后位于一条水平线上,由所述四块模板拼接成构件浇筑所需内模的截面形状。本发明实施例涉及的构件为一个左右对称的多边形,所述左上模板3的形状为平顶角形,即上部的两个角为平顶,是一个倾斜的平面,这样的设计可以减少尖角处的应力集中,使构件受力更为均匀,不易损毁。左上模板3的角形中的水平梁与其对应的驱动部分铰接,铰接点靠近拼接处一端。之所以将铰接点选择在靠近拼接处一端,是为了减少装配时所需力矩,使驱动部分更容易驱动左上模板3就位(下同)。另外,在内模板的收放动作中,为防止水平梁在铰接点处出现卡顿,可将水平梁的铰接孔设置成长圆孔或较大直径的孔(本发明中其他部位使用的铰接关系也如此处理)。
23.所述左下模板4的形状为角形,角形中的水平梁与其对应的驱动部分铰接,铰接点靠近拼接处方向一端;所述左上模板3和左下模板4构成内模的左半部分;所述右上模板5的形状为平顶角形,角形中的水平梁与其对应的驱动部分铰接,铰接点靠近拼接处一端;所述右下模板6的形状为角形,角形中的水平梁与其对应的驱动部分铰接,铰接点靠近拼接处的一端;所述右上模板5和右下模板6构成内模的右半部分,内模的右半部分和左半部分对称。水平梁可采用角钢、槽钢或矩形钢管制造。
24.本发明提供的实施例是要制造一个多边形的构件,相应地所需内模的形状也要与之相配。如果构件的截面形状为长方形、梯形、圆形或其他任意形状,则内外模的形状也将随之改变。
25.所述内模的装配是由四个驱动构件完成的,这四个驱动构件分别是左上驱动构件、左下驱动构件、右上驱动构件和右下驱动构件,它们共同配合完成模具的开合装配。四个驱动构件又分别与驱动盘21传动连接,它们的结构相同;其中,左上驱动构件包括左上推拉杆102和左上卡爪101,所述左上模板3与左上推拉杆102的一端铰接,左上推拉杆102的另一端连接在左上卡爪101上,左上模板3与左上推拉杆102的铰接处设置成长圆孔,可以吸纳模板在拆卸时出现的径向和切向的偏移。其余三个驱动构件与左上驱动构件的结构相同;驱动盘21的外缘套有驱动盘壳体18,驱动盘壳体18的形状是与驱动盘21的外缘匹配的圆筒状,它支承在机架支柱13上,所述机架支柱13设置在构件制作平台35上;所述驱动盘21为固定在从动轴17上的圆盘,其一个侧面设有单头螺旋21-2,单头螺旋21-2(也可采用多头螺旋,例如二头螺旋)为1-4圈矩形螺纹(也可采用梯形或其他形状),所述矩形螺纹与所述左上卡爪101构成螺纹副。当驱动盘21旋转时,它会带动左上卡爪101做径向移动,完成左上卡爪101的驱动;其余左下卡爪201、右上卡爪301、右下卡爪401也与驱动盘21的矩形螺纹构成螺纹副,它们也会像左上卡爪101一样做径向移动,完成卡爪的驱动。由于这四个卡爪都啮合在一条螺旋上,螺距相同,所以它们作径向移动的距离也就相同;如果四个驱动构件的径向移动距离出现不同,或者需要人为设置不同,则可通过在卡爪上设置的长度调节机构进行调节。在从动轴17上还设置从动齿轮20,从动齿轮20与设置在主动轴16上的主动齿轮19啮合,主动轴16由电机31驱动,完成驱动左上模板3-右下模板6的四块模板的收放操作。
26.所述主动齿轮19、从动齿轮20均为直齿齿轮(当然也可采用其他齿形,相应的结构会发生变化),主动齿轮19与从动齿轮20相互啮合。
27.本发明驱动盘21的单头螺旋21-2采用阿基米德螺线或圆的渐开线曲线,利用这类曲线的极径等进性使径向位移相等。挡块21-1用于防止啮合件意外脱落。
28.由于驱动模板装配需要较高力矩和自锁,因此,本发明使用异步电机和减速机共
同作用,且采用较大的减速比,可稳定而缓慢地转动驱动盘21,以较大旋转力矩转动四个驱动构杆。
29.进一步地,为了解决四个驱动构件径向移动距离的误差,可以在四个推拉杆(即左上推拉杆102、左下推拉杆202、右上推拉杆302、右下推拉杆402)中设置长度微调机构,长度微调机构由左旋螺杆、螺母套筒和右旋螺杆组成,在螺母套筒内的两端分别设置与左旋螺杆和右旋螺杆构成的旋向相反的螺纹副,利用螺母套筒的锁紧或松开操作,即可对推拉杆的移动长度作精确的微调,并进而调节四个推拉杆所需的径向移动距离。
30.本发明为了确保卡爪只做径向移动,所述驱动盘壳体18上设四个t型槽,所述左上卡爪101、左下卡爪201、右上卡爪301、右下卡爪401的形状均为t型,其t型与驱动盘壳体18上的四个t型槽构成滑动配合。
31.本发明为确保装配时左上模板3、左下模板4、右上模板5和右下模板6能够获得足够稳定可靠的支撑力,还增设了液压支撑杆7,所述液压支撑杆7为两个,分别竖直设置在左上模板3和左下模板4之间、以及右上模板5和右下模板6之间;所述液压支撑杆7中设有液压缸9,利用液压缸9的压力分担模板受到的压力。本发明在液压支撑杆7机构中还增设了导向滑轨39,以防支撑杆顶偏;导向滑轨39固定在机架上。
32.第一压力传感器p1设置在液压缸座11内,当然,也可设置在液压支撑杆7和左下模板4之间的其他地方.第一压力传感器p1输出给cpu的压力数值达到设定的阈值时,即说明内模装配的操作已经就位。
33.本发明还增设了螺杆锁紧微调机构34,所述螺杆锁紧微调机构34设置在左下模板4和右下模板6之间;螺杆锁紧微调机构包括锁紧螺母26、左安装座22、右安装座23、左旋螺杆24和右旋螺杆25;所述左安装座22设置在左下模板4侧边的中上部,左旋螺杆24与左安装座22连接,右安装座23设置在右下模板6侧边的中上部,右旋螺杆25与右安装座23连接,锁紧螺母26的两端分别与左旋螺杆24和右旋螺杆25构成旋向相反的螺纹副。利用锁紧螺母26的锁紧或松开操作,即可人工对左下模板4和右下模板6之间的间距作精确的微调,使内模装配的预紧力达到最佳状态。
34.本发明在左上模板3和右上模板5之间、在左下模板4和和右下模板6之间增设了锁栓机构,分别是上部锁栓机构12-1、下部锁栓机构12-2,锁栓机构可以在装配完成后,锁定内模,这样,无论出现何种意外情况,当栓板29的一端插入右栓座28的开口槽内、并被栓轴30锁紧后,都可以确保内模的装配状态不会发生意外改变。
35.本发明还在左上模板3和右上模板5之间增设了第一水平位置检测传感器s1,在左下模板4和和右下模板6之间增设了第二水平位置检测传感器s2,第一水平位置检测传感器s1的第一霍尔传感器38-1如果检测到第一磁钢37-1与其位于一条直线上,第二水平位置检测传感器s2的第二霍尔传感器38-2如果检测到第二磁钢37-2与其位于一条直线上,这个信号给cpu发出了可以将驱动盘21停止转动的信号。
36.需要说明的是,本发明的第二水平位置传感器s2的结构与第一水平位置传感器s1的结构相同,只是安装在左下模板4和和右下模板6之间,因此,第二水平位置传感器s2的结构并未在附图中画出,而是仅仅在图10的控制电路中画出了它的电连接关系。
37.本发明的控制部分包括cpu、启动按钮qa、第一水平位置检测传感器s1、第二水平位置检测传感器s2、第一压力传感器p1、电磁阀dcf和电机控制芯片ic1;所述第一水平位置
检测传感器s1、第二水平位置检测传感器s2和第一压力传感器p1分别连接在cpu的三个端口上,分别输入两个模板的水平位置信号和两个压力数值信号,所述电机控制芯片ic1的两个信号输入端分别连接在cpu的两个输出端口上,用于接受电机31转向和转动信号,所述电磁阀dcf的两个线圈控制输入端分别连接在cpu的两个输出端口上,接受cpu输出的信号以控制电磁阀dcf的液压走向。
38.在本发明的电原理图中,cpu的输出直接连接被控元器件,但若需要较大的驱动信号,可以在两者之间加入中继,比如三极管放大电路、中间继电器、转换电路,等等。
39.本发明的cpu可采用stc89c52,电机控制芯片ic1采用mc33886,电磁阀dcf可选择k35hd2-6。
40.霍尔传感器输出的这个电信号还给cpu发出了可以给液压支撑杆7的液压缸9供油,驱动液压支撑杆7移动到位,顶紧左上模板3和左下模板4、以及右上模板5和右下模板6。顶紧力可以从第一压力传感器p1的输出的油压数值中获得,由cpu与预存的压力阈值比较后,判断是否达标。控制液压缸9进出油是由电磁阀dcf完成的,电磁阀dcf可采用普通的三位五通阀来控制支撑杆的动作方向。
41.本发明在左上模板3和右上模板5、左下模板4和右下模板6搭接处的间隙d做了设定,其数值为(0.7-1.4)h,其中,h为模板中水平梁的厚度。之所以预留间隙,是因为当两个模板同时移动时,有可能发生干涉,造成无法同时动作。预留间隙后,就可以避免这种情况。倘若考虑到钢板的厚度,预留的间隙也可作适当调整。另外,因间隙引起的混凝土流淌,可以通过预先铺设条状薄钢板来解决,所述条状薄钢板的厚度可选择1-3mm,预留的间隙应能保证内模收缩时不会卡顿,条状薄钢板覆盖模板之间的间隙,防止混凝土泥浆从间隙漏入内模内。当然,也可使用密封剂堵塞间隙,此处不再赘述。
42.本发明给出的内模装配构件,涉及的构件长度一般为1-2.5米,如果构件较长,则可根据预制构件的长度将多个上述内模构件利用轴和法兰盘连接在一起,同时换用更大功率的电机,以满足构件现场装配和制作的需要。
43.本发明的装配操作按如下程序进行:1、将内模构件移动至构件制作平台35上,就绪后,启动电机31,主动轴16上的主动齿轮19带动从动齿轮20旋转,驱动盘21上的单头螺旋21-2随之转动,与单头螺旋21-2啮合的四个卡爪就向从动轴17的轴心方向聚拢或分散,当四个卡爪向远离轴向的方向移动时,四块模板被支起,完成内模形状的装配;当卡爪向轴心方向聚拢时,卡爪带动固定在其上的推拉杆向从动轴17的轴心方向移动,同时四块模板也向轴心方向移动,内模模板外壁和预制构件脱离,便于内模整体从构件中脱出。
44.2、在内模装配时,四块模板被支起后是否到位,是由两个水平位置检测传感器完成的,如果第一水平位置检测传感器s1检测到第一霍尔传感器38-1与第一磁钢37-1位于一条直线上,或者第二水平位置检测传感器s2检测到第二霍尔传感器38-2与第二磁钢37-2位于一条直线上,则说明装配到位;第一水平位置检测传感器s1和第二水平位置检测传感器s2向cpu发出驱动盘停止转动的信号,使电机31断电,停止驱动盘21转动。
45.3、与此同时,第一霍尔传感器38-1、第二霍尔传感器38-2输出的信号还给cpu发出了可以给液压支撑杆7的液压缸9供油,驱动液压支撑杆7移动到位,顶紧左上模板3和左下模板4、以及右上模板5和右下模板6。第一压力传感器p1输出的油压数值给出了顶紧力的数
值信号,由cpu与预存的油压阈值比较后,判断是否达标,若已经达标,则液压缸9停止供油。
46.4、然后,将锁栓机构中的栓板29一端插入右栓座28的开口槽内,用栓轴30锁紧。
47.5、调整螺杆锁紧微调机构34锁紧螺母26,对左下模板4和右下模板6之间的间距作精确的微调,使内模装配的预紧力达到最佳状态。
48.6、内模装配完成,进行混凝土浇筑、振捣,完成后进入凝固和养护阶段。
49.7、养护工序完成后,进行拆模。打开锁栓机构中的栓板29;松开锁紧螺母26;cpu发出给液压支撑杆7的液压缸9泄油的指令,液压支撑杆7回缩;令电机31反转,驱动盘21反转,单头螺旋21-2随之转动,与单头螺旋21-2啮合的四个卡爪就向从动轴17 的轴心方向聚拢,卡爪带动推拉杆向轴心方向移动,四块模板也随之向轴心方向移动,内模模板外壁和混凝土脱离,内模即可整体从构件制作平台35上脱出、完成卸模操作。
再多了解一些
本文用于企业家、创业者技术爱好者查询,结果仅供参考。