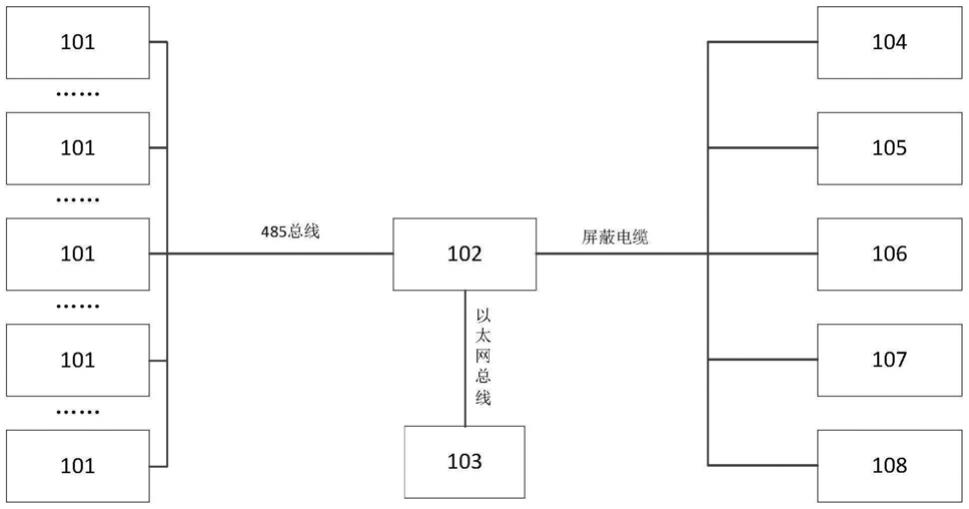
1.本技术涉及热处理技术领域,特别涉及一种淬火感应加热系统和方法。
背景技术:
2.感应加热处理工艺是提高零件机械性能的主要手段之一,而感应加热时最常用的是表面电磁感应加热淬火方法,而电压、电流波动对淬火质量以及产品在淬火深度、硬度的影响较大,难以保证零件淬火质量以及整批产品在淬火深度、硬度的一致性,难以避免出现淬火质量问题。
3.而现有的感应加热设备能量监控该系统无法获取淬火零件的实时能量数据或不同运行速度曲线对应的能量情况,从而导致无法精确控制电能的使用,也不能根据电能的变化情况做出相应的措施,以减少电网电压降低,引起的淬火不合格。
4.因此,如何实现对感应加热设备进行能量监控,是本领域技术人员迫切需要解决的问题。
技术实现要素:
5.本技术的目的在于提供一种淬火感应加热系统和方法,以解决或缓解上述现有技术中存在的问题。
6.为了实现上述目的,本技术提供如下技术方案:
7.本技术提供了一种淬火感应加热系统,用于对待加工工件进行淬火处理,包括:淬火感应加热电源,用于对所述待加工工件进行感应加热;数据采集单元,对所述待加工工件淬火时的淬火感应加热数据进行采集;plc控制单元,与所述数据采集单元通讯连接,接收所述数据采集单元发送的所述淬火感应加热数据,并对所述淬火感应加热电源进行调控;能量监控单元,与所述plc控制单元通讯连接,接收所述plc控制单元发送的淬火感应加热数据,对所述淬火感应加热数据进行校验,并将校验结果反馈至所述plc控制单元,以由所述plc控制单元根据所述淬火感应加热数据中的加热能量,对所述待加工工件的淬火感应加热电源进行控制。
8.优选的,所述数据采集单元包括:环境数据采集单元和状态数据采集单元,所述环境数据采集单元和状态数据采集单元均与所述plc控制单元电连接;其中,所述环境数据采集单元用于对所述待加工工件的淬火环境数据进行采集并发送至所述plc控制单元,所述状态数据采集单元用于对所述待加工工件的淬火状态数据进行采集发送至所述plc控制单元;所述淬火环境数据包括所述待加工工件淬火时的冷却水压、淬火水压、冷却水温、淬火水温、冷却水流量和淬火液流量;所述淬火状态数据包括所述淬火感应加热电源的淬火电压、淬火电流、淬火时间和淬火能量。
9.优选的,所述环境数据采集单元包括压力传感器、温度传感器和流量计;其中,所述压力传感器设置于所述待加工工件的淬火水路中,以对所述待加工工件淬火时的冷却水压、淬火水压进行监测;所述温度传感器设置于所述待加工工件的淬火水管、集水器、水盒
处,以对所述待加工工件淬火时的冷却水温、淬火水温进行监测;所述流量计设置于所述待加工工件的淬火水路中,以对所述待加工工件淬火时的冷却水流量、淬火液流量进行监测。
10.优选的,所述plc控制单元对所述淬火环境数据与预设淬火环境阈值进行比对,并根据比对结果确定是否发出淬火环境报警信号;以及,所述plc控制单元对淬火状态数据和预设淬火状态阈值进行比对,并根据比对结果确定是否发出所述淬火感应加热电源的工作状态报警信号。
11.优选的,所述数据采集单元与所述plc控制单元通过屏蔽电缆连接;所述plc控制单元与所述能量监控单元通过以太网总线连接。
12.本技术实施例还提供一种淬火感应加热方法,采用上述任一实施例所述的淬火感应加热系统对待加工工件进行淬火处理,包括:对所述待加工工件的淬火感应加热数据进行采集;基于预设校验算法,对所述淬火感应加热数据进行校验;响应于所述淬火感应加热数据校验正确,根据所述淬火感应加热数据中的加热能量,对所述待加工工件的淬火感应加热电源进行控制。
13.优选的,所述对所述待加工工件的淬火感应加热数据进行采集包括:按照预设的采集周期对所述待加工工件的淬火环境数据和淬火状态数据进行采集;其中,所述淬火环境数据包括所述待加工工件淬火时的冷却水压、淬火水压、冷却水温、淬火水温、冷却水流量和淬火液流量;所述淬火状态数据包括所述淬火感应加热电源的淬火电压、淬火电流、淬火时间和淬火能量。
14.优选的,所述基于预设校验算法,对所述淬火感应加热数据进行校验包括:由plc控制单元基于预设校验算法,根据所述淬火感应加热数据生成第一计算数据;以及,由能量监控单元基于预设校验算法,根据所述淬火感应加热数据生成第二计算数据;其中,所述plc控制单元用于对所述待加工工件的淬火感应加热数据进行采集并发送至所述能量监控单元;由所述能量监控单元对所述第一计算数据和所述第二计算数据进行比对校验,根据比对结果向所述plc控制单元发送数据判断信息,以由所述plc控制单元根据所述数据判断信息确定是否重新向所述能量监控单元发送所述淬火感应加热数据。
15.优选的,所述由所述能量监控单元对所述第一计算数据和所述第二计算数据进行比对校验,根据比对校验结果向所述plc控制单元发送数据判断信息,以由所述plc控制单元根据所述数据判断信息确定是否重新向所述能量监控单元发送所述淬火感应加热数据包括:由所述能量监控单元对所述第一计算数据和所述第二计算数据进行比对校验,响应于所述比对校验结果一致,所述能量监控单元向所述plc控制单元发送数据正确信息;响应于所述比对校验结果不一致,所述能量监控单元丢弃接收到的所述淬火感应加热数据,并向所述plc控制单元发送数据错误信息,以由所述plc控制单元重新向所述能量监控单元发送所述淬火感应加热数据,直至所述比对校验结果一致。
16.优选的,所述响应于所述淬火感应加热数据校验正确,根据所述淬火感应加热数据中的加热能量,对所述待加工工件的淬火感应加热电源进行控制,包括:响应于所述淬火感应加热数校验正确,且所述淬火感应加热数据中的加热能量达到预设能量阈值,停止所述淬火感应加热电源对所述待加工工件的感应加热。
17.有益效果:
18.本技术实施例提供的淬火感应加热方案中,通过淬火感应加热电源对代加工工件
进行感应加热,由数据采集单元对待加工工件淬火时的淬火感应加热数据进行采集并发送至plc控制单元,plc控制单元将淬火感应加热数据发送至能量监控单元,由能量监控单元对淬火感应加热数据进行校验,并将校验结果反馈至plc控制单元,以由plc控制单元根据淬火感应加热数据中的加热能量,对代加工工件的淬火感应加热电源进行控制。籍此,利用数据采集单元、plc控制单元和能量监控单元实现对待加工工件进行感应加热过程的实时监控及调整,降低外界因素对淬火过程的影响,有效提高待加工工件的淬火处理质量。
附图说明
19.构成本技术的一部分的说明书附图用来提供对本技术的进一步理解,本技术的示意性实施例及其说明用于解释本技术,并不构成对本技术的不当限定。其中:
20.图1为根据本技术的一些实施例提供的一种淬火感应加热系统的结构示意图;
21.图2为根据本技术的一些实施例提供的一种淬火感应加热方法的流程示意图。
22.附图标记说明:
23.101、淬火感应加热电源;102、plc控制单元;103、能量监控单元;104、压力传感器;105、温度传感器;106、流量计;107、编码器;108、光电开关。
具体实施方式
24.下面将参考附图并结合实施例来详细说明本技术。各个示例通过本技术的解释的方式提供而非限制本技术。实际上,本领域的技术人员将清楚,在不脱离本技术的范围或精神的情况下,可在本技术中进行修改和变型。例如,示为或描述为一个实施例的一部分的特征可用于另一个实施例,以产生又一个实施例。因此,所期望的是,本技术包含归入所附权利要求及其等同物的范围内的此类修改和变型。
25.图1为根据本技术的一些实施例提供的一种淬火感应加热系统的结构示意图;如图1所示,该淬火感应加热系统用于对待加工工件进行淬火处理,包括:淬火感应加热电源101,用于对待加工工件进行感应加热;数据采集单元,对待加工工件淬火时的淬火感应加热数据进行采集;plc控制单元102,与数据采集单元通讯连接,接收数据采集单元发送的淬火感应加热数据,并对淬火感应加热电源101进行调控;能量监控单元103,与plc控制单元102通讯连接,接收plc控制单元102发送的淬火感应加热数据,并对淬火感应加热数据进行校验,并将校验结果反馈至plc控制单元102,以由plc控制单元102根据淬火感应加热数据中的加热能量,对待加工工件的淬火感应加热电源101进行控制。
26.在本技术实施例中,淬火感应加热电源101在对待加工工件进行感应加热过程中,由数据采集单元对待加工工件在淬火时的电压、电流、功率、频率、能量、电源运行、冷却水压、冷却水温、淬火水压、淬火水温、工件的行走速度、合格工件数量、不合格工件数量等数据进行采集并发送至plc控制单元102。
27.在本技术实施例中,通过plc控制单元102对淬火感应加热电源101进行控制,具体的,每台plc控制单元102最多可支持与20台淬火感应加热电源101进行通信。即,可以同时监控调整的淬火感应加热电源101的状态为20台。籍此,实现同时对多个淬火感应加热电源101的同步监测、调控,进一步提高待加工工件的淬火效率。
28.具体的,数据采集单元包括环境数据采集单元和状态数据采集单元,环境数据采
集数据和状态数据采集单元均与plc控制单元102电连接;其中,环境数据采集源用于对待加工工件的淬火环境数据进行采集并发送至plc控制单元102,状态数据采集单元用于对待加工工件的淬火状态数据进行采集并发送至plc控制单元102。在此,淬火环境数据包括待加工工件淬火时的冷却水压、淬火水压、冷却水温、淬火水温、冷却水流量和淬火液流量;淬火状态数据包括淬火感应加热电源101的淬火电压、淬火电流、淬火时间和淬火能量。籍此,实现对待加工工件在淬火过程中的实时监控,以便及时调整淬火状态,提高待加工工件的淬火质量。
29.进一步的,环境数据采集单元包括压力传感器104、温度传感器105和流量计106;其中,压力传感器104设置于待加工工件的淬火水路中,以对待加工工件淬火时的冷却水压、淬火水压进行监测;温度传感器105设置于待加工工件的淬火水管、集水器、水盒处,以对待加工工件淬火时的冷却水温、淬火水温进行监测;流量计106设置于待加工工件的淬火水路中,以对待加工工件淬火时的冷却水流量、淬火液流量进行监测。在此,需要说明的是,本技术中,还可以通过设置在待加工工件的传送带附近的编码器107对待加工工件的行走速度进行实时监测并发送至plc控制单元102,通过该设置在待加工工件的传送带附近的光电开关108对待加工工件的数量进行实时监测并发送至plc控制单元102。
30.在此,需要说明的是,冷却水和淬火液具有相互独立的水路,冷却水路可采用纯净水、自来水等,进一步的,可以在冷却水中添加防冻剂。在淬火水管、集水器、水盒处分别串联设置有温度传感器105,该温度传感器105采用常闭机械式,当淬火水管、集水器、水盒处中的一个温度传感器105的监测数据超过预设温度阈值,则plc控制单元102发出高温预警信号,以提醒工作人员及时进行处理。
31.在本技术实施例中,plc控制单元102对淬火环境数据与预设淬火环境阈值进行比对,并根据比对结果确定是否发出淬火报警信号;以及,plc控制源对淬火状态数据和预设淬火状态阈值进行比对,并根据比对结果确定是否发出淬火感应加热电源101的工作状态报警信号。具体的,当淬火环境数据如冷却水温、冷却水压、淬火液温度、淬火液流量等低于或者超过对应的预设阈值时,发出淬火环境报警;在感应加热过程中,如果淬火感应加热电源101的电压、电流、加热时间、加热能量等超过对应的预设阈值时,则产生电源报警,即发出淬火感应加热电源101的工作状态报警信号。在此,淬火环境报警和电源报警独立运行,且当淬火环境数据中的一个或者淬火状态数据中的一个发生异常,即刻产生对应的淬火环境报警或电源报警。
32.在本技术实施例中,数据采集单元与plc控制单元102通过屏蔽电缆连接,plc控制单元102与能量监控单元103通过以太网总线连接。具体的,能量监控系统与plc控制单元102之间采用以太网总线按照tcp/ip协议通信,实现数据的通讯传输;数据采集单元与plc控制单元102之间通过屏蔽电缆连接,可以有效保证数据在传输过程中的干扰,提高数据传输的稳定性。
33.籍此,利用数据采集单元、plc控制单元102和能量监控单元103实现对待加工工件进行感应加热过程的实时监控及调整,降低外界因素对淬火过程的影响,有效提高待加工工件的淬火处理质量。
34.图2为根据本技术的一些实施例提供的一种淬火感应加热方法的流程示意图;如图2所示,该淬火感应加热方法中,采用上述任一实施例的淬火感应加热系统对待加工工件
进行淬火处理,包括:
35.步骤s201、对待加工工件的淬火感应加热数据进行采集;
36.在本技术实施例中,对待加工工件的工件数据和淬火感应加热数据进行采集。其中,工件数据包括待加工工件的加工日期、加工时间、产品编号、规格型号、供应商、设备编号、唯一识别码等。在此,产品编号、规格型号、供应商、设备编号由人工输入,唯一识别码则由淬火感应加热系统根据淬火感应加热数据自动生成,以便对待加工工件进行追源溯本。
37.在本技术实施例中,采用基于access的数据库存储技术,提供功能参数化查询;其中,功能参数化查询和access表格可以通过ado访问参数化的存储过程。具体的,自动将采集到的待加工工件的工件数据和淬火感应加热数据按照日期建立链表,把待加工工件的概况信息生成access表格,在access表格中包括时间(年月日时分秒),操作人员姓名、工件型号、种类、合规与否,并根据待加工工件的加工时间生成唯一识别码。
38.在一些可选实施例中,对待加工工件的淬火感应加热数据进行采集具体为:按照预设的采集周期对待加工工件的淬火环境数据和淬火状态数据进行采集;其中,淬火环境数据包括待加工工件淬火时的冷却水压、淬火水压、冷却水温、淬火水温、冷却水流量和淬火液流量;淬火状态数据包括淬火感应加热电源101的淬火电压、淬火电流、淬火时间和淬火能量。
39.在本技术实施例中,按照一定的采集周期收集待加工工件的淬火感应加热数据,且采集周期可根据待加工工件的工作环境进行设定、更改。具体的,采集周期的取值范围为大于等于0.01秒且小于等于1秒;进一步的,采集周期的调节步长为0.01秒。即,在0.01秒至1秒之间,将采集周期划分为100个档次,根据待加工工件的加工时间、待加工工件的体积、加工速度等确定合适的采集周期。其中,采集周期与待加工工件的加工时间成反比,与待加工工件的体积成正比,与待加工工件的加工速度呈正比。即待加工工件的加工时间短、体积小、加工速度快,则采集周期小,反之,则采集周期长。
40.步骤s202、基于预设校验算法,对淬火感应加热数据进行校验;
41.在本技术实施例中,淬火感应加热电源101的电压、电流、功率、频率、运行信息等模拟信号,由淬火感应加热电源101内部的ad模块将其转换为数字信号,并按照数据传输协议传送给plc控制单元102。
42.在本技术实施例中,每台淬火感应加热电源101通过485总线与plc控制单元102通讯连接,由plc控制单元102,将淬火感应加热电源101的电压、电流、功率、频率、运行信息等淬火状态数据以及淬火环境数据合成一个数据包,并根据预设校验算法对数据包生成一个校验码,并将校验码附在数据包末尾,传输给能量监控系统;由能量监控系统对接收到的数据包进行校验,若数据正常,则采用数据包中的数据,若数据不正常,则由淬火感应加热电源101重新发送数据。
43.具体的,在基于预设校验算法,对淬火感应加热数据进行校验时,首先,由plc控制单元102基于预设校验算法,根据淬火感应加热数据生成第一计算数据;以及,由能量监控单元103基于预设校验算法,根据淬火感应加热数据生成第二计算数据;其中,plc控制单元102用于对待加工工件的淬火感应加热数据进行采集并发送至能量监控单元103;然后,由能量监控单元103对第一计算数据和第二计算数据进行比对校验,根据比对结果向plc控制单元102发送数据判断信息,以由plc控制单元102根据数据判断信息确定是否重新向能量
监控单元103发送淬火感应加热数据。
44.在本技术实施例中,plc控制单元102、能量监控单元103均可采用工业计算机或高速数字采集分析电路。plc控制单元102与能量监控单元103之间的数据通信传输采用以太网总线,数据包发送采用tcp协议,plc控制单元102采集到的数据以每帧1000字节按照一定的时间周期发送给能量监控系统,在每帧的数据包末尾附加上预设校验算法生成的校验数据(校验码)。在能量监控系统接收到plc控制单元102发送的数据包后,按照预设校验算法校验数据的准确性,校验正确就采用数据对待加工工件的淬火处理进行分析,如果校验不正确,则丢弃该数据包,由plc控制单元102重新发送数据包。
45.进一步的,由能量监控单元103对第一计算数据和第二计算数据进行比对校验,响应于比对校验结果一致,能量监控单元103向plc控制单元102发送数据正确信息;响应于比对校验结果不一致,能量监控单元103丢弃接收到的淬火感应加热数据,并向plc控制单元102发送数据错误信息,以由plc控制单元102重新向能量监控单元103发送淬火感应加热数据,直至比对校验结果一致。
46.在本技术实施例中,plc控制单元102将收集到的一条数据(包含12个按照预设顺序排列的数据信息:冷却水压、冷却水温、淬火水压、淬火水温、工件行走速度、合格工件数量、不合格工件数量、电压、电流、功率、频率、运行信息等)按照crc16校验算法进行计算,得到第一计算数据;并将第一计算数据和收集到的该条数据(包含12个按照预设顺序排列的数据信息)一起发送给能量监控单元103,能量监控单元103同样按照crc16校验算法进行计算,得到第二计算数据;然后,由能量监控单元103将第一计算数据和第二计算数据进行比对,一样就说明数据准确并向plc控制单元102发送数据正确信息,不一样说明数据在传输过程中发生了错误,将其丢弃,并向plc控制单元102发送数据错误信息,让plc控制单元102重新传输数据。
47.在一些可选实施例中,淬火感应加热方法还包括:响应于比对校验结果一致,且plc控制单元102接收到的淬火感应加热数据的大小达到预设大小阈值,将接收到的淬火感应加热数据存储在数据库中。
48.在本技术实施例中,当能量监控系统的比对校验结果一直,且plc控制单元102接收集的淬火感应加热数据的大小达到预设大小阈值(50条数据,4k字节),将收集到的淬火感应加热额数据存入数据库的数据表中。籍此,通过减少数据存储频率,降低硬盘读写次数,有效降低了cpu资源占用,提高了系统的反映速度,避免遗漏信息,延长系统的使用寿命。
49.步骤s203、响应于淬火感应加热数据校验正确,根据淬火感应加热数据中的加热能量,对待加工工件的淬火感应加热电源101进行控制。
50.具体的,响应于淬火感应加热数据校验正确,且淬火感应加热数据中的加热能量达到预设能量阈值,停止淬火感应加热电源101对待加工工件感应加热。
51.在本技术实施例中,当达到设定的加热能量(预设能量阈值)时,系统主动停止淬火感应加热电源101输出,停止淬火,优化待加工工件的淬火处理,实现能量的优化利用。
52.在本技术实施例中,各单元之间采用多线程技术,tcp通信、485通信、采集数据、保存数据、显示当前数据、查看历史数据等分别各自使用1个线程进行处理,各单元之间可同时执行,互补干扰。一方面,在查看数据时,按照待加工工件的加热时间(月份和日期)作为
分类,也可以直接按照工件类型、操作者分类进行搜索,搜索出来的信息在列表中显示,通过点击相应的列表信息即可在加工数据表格中列出相应的淬火感应加热数据。另一方面,查询出来的数据,根据需要可以将单个工件的加工数据(淬火感应加热数据)或者一天内的加工数据,或者一个月内的加工数据导出,以供查看比对分析。
53.需要说明的是,在待加工工件加热前,淬火感应加热电源101将淬火工位的开关量信号传递给能量监控单元103;在感应加热过程中,淬火感应加热电源101的感应加热启动同步信号一直保持触点闭合状态。其中,开关量信号包括:淬火环境报警、淬火失败报警、淬火失败停机、加热能量正点停机;且开关量信号由plc控制单元102转化为数字信号传递给能量监控单元103。
54.在本技术实施例中,在生产过程中可选取加热效果最佳的历史数据来制作模板。在功率上限输入框输入0—100数值,下限输入框输入0—100数值。即在加热效果最佳的那次功率曲线上下限区域内是功率适中的区域。在正常运行时以绿色区域显示,功率高于上限的区域为红色高温区域,低于下限的区域为蓝色低温区域。根据需要可储存模板、删除模板和使用模板。
55.在本技术实施例中,每次设备运行时采集到的功率数据,按时间先后降序排列,在图表窗口中显示功率曲线,以一条白色曲线显示实时功率;人工标定待加工工件的型号参数(型号、材料、尺寸)工件淬火前要先选择正确的工件型号。
56.在本技术实施例中,能够对待加工工件进行加热时的功率、逆变电压、逆变电流、加热总能量等参数进行实时显示;以及,能够对报警参数进行标定,使系统具有实时功率报警(不报警)、实时能量报警(不报警)和能量超出模板能量报警(不报警)时停机等功能。
57.本技术实施例提供的淬火感应加热方法能够通过上述任一淬火感应加热系统的操作实现,并达到相同的技术效果,在此不再一一赘述。
58.以上所述仅为本技术的优选实施例,并不用于限制本技术,对于本领域的技术人员来说,本技术可以有各种更改和变化。凡在本技术的精神和原则之内,所作的任何修改、等同替换、改进等,均应包含在本技术的保护范围之内。
再多了解一些
本文用于企业家、创业者技术爱好者查询,结果仅供参考。