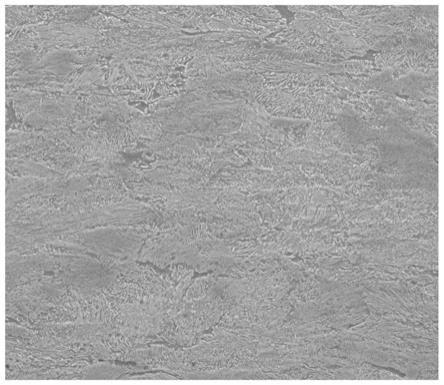
抗拉强度1050mpa级精密冲压链锯导板用冷轧钢板
技术领域
1.本发明涉及一种用于精密冲压加工的冷轧钢板,特别涉及一种抗拉强度1050mpa级精密冲压链锯导板用冷轧钢板及其制造方法,属于铁基合金技术领域。
背景技术:
2.链锯是一种主要用于森林伐木、园林修剪、家具行业的手提式动力切割工具。在林业生产中,尤其是在森林采伐领域,如伐木、打枝、造材等储木场造材、枕木截锯方面等得到了广泛应用。链锯前端的锯木结构工作端主要由驱动链轮、锯链、导板、刀头等构成,其中链锯导板又称链板、锯板,是链锯传动系统不可缺少的重要构件;主要作用是支撑锯链条,使链锯链条按照直线传动,顺畅运作,完成切割作业。因此对材料的耐磨使用性能要求较高,洛氏硬度达到31hrc以上,允许的厚度偏差≤0.060mm。
3.申请公布号为cn105018835a的专利申请公开了一种精冲性能优良的中高碳热轧带钢及生产制造方法,其化学成份重量百分比为:c:0.50~0.65%,si:0.50~1.60%,mn:0.50~1.70%,ca:0.0030~0.0070%,b:0.0008~0.0050%,al:0.015~0.030%,p≤0.015%,s≤0.008%;其余为fe和不可避免的杂质。该专利利用si元素提高碳原子活度,改善球化退火能力;并通过罩式炉进行球化退火得到精冲钢板。这里所说的是一种热轧后并进行完全球化退火的精冲钢板,虽然冲裁质量达到要求,但硬度很低;并且采用0.50%以上的高硅含量设计在钢板热轧过程产生大量的氧化铁皮,形成表面麻点和凹坑,大大降低了钢板表面质量和材料规格精度。
4.公开号为cn101597684a的专利申请公开了一种链锯导板的热处理方法,使用的材料为国标合金钢30crmo,其中材料主要元素化学成份重量百分比为:c:0.26~0.34%,si:0.17~0.37%,mn:0.4~0.7%,cr:0.80~1.10%,mo:0.15~0.25%,p≤0.025%,s≤0.025%,其余为fe和不可避免的杂质。该发明得到的导板材料用于大型森林伐木机械油锯,由于设计中添加了大量的cr及贵重合金元素mo,使原材料成本很高;同时加工过程还采用了盐浴淬火及回火热处理来保证导板最终硬度要求,工艺加工成本很高。
技术实现要素:
5.本发明目的是提供一种抗拉强度1050mpa级精密冲压链锯导板用冷轧钢板及其制造方法,主要解决现有链锯导板用钢板制造成本高、加工工艺复杂的技术问题。
6.本发明通过采用普通的中高碳钢c、mn合金元素为基础,有效添加一定量的微合金元素cr的成分设计方法,进一步控制p、s等有害元素,控制热轧工艺过程温度和冷却方式;并最终通过冷轧多道次大压下、大变形量的方法的来控制材料的最终硬度和厚度精度,得到满足高速切割支撑和运转的链锯导板用精冲钢板。
7.本发明的技术方案是,一种抗拉强度1050mpa级精密冲压链锯导板用冷轧钢板,其化学成分重量百分比:c:0.52~0.58%,si:0.10~0.30%,mn:0.70~0.80%,p≤0.015%,s≤0.003%,cr:0.15~0.35%,al:0.01~0.03%,n≤0.0060%;其余为fe和不可避免的杂
质。
8.本发明冷轧钢板的金相组织为片状珠光体 铁素体,0.80~1.60mm厚冷轧钢板的屈服强度r
p0.2
为850~1000mpa,抗拉强度rm为1050~1200mpa,屈强比为0.80~0.90,断后伸长率a
50mm
为5~8%,洛氏硬度为33~37hrc;钢板厚度偏差≤0.020mm。
9.本发明抗拉强度1050mpa级精密冲压链锯导板用冷轧钢板的化学成分限定在上述范围内的理由如下:
10.碳:碳是珠光体形成的主要合金元素,同时影响材料热轧、冷轧、退火以及零件淬火后的硬度。c含量过低,不能满足零件最终高硬度要求;c含量过高则塑性韧性下降明显,不利于复杂成型。经综合考虑,本发明设定碳含量为0.52~0.58%。
11.硅:硅作为固溶强化元素,固溶在钢板基体中有一定的强化效果,同时作为冶炼时的一种脱氧剂,对脱氧、脱硫发挥作用。但大量含有时会使铁素体相硬化,加工性能明显降低。并且si在热轧过程促进钢卷表面锈红氧化铁皮缺陷产生,影响成品外观;经综合考虑,本发明设定si含量为0.10~0.30%。
12.锰:锰是良好的脱氧剂和脱硫剂。钢中含有一定量的锰,能消除或改善钢的热加工性能,同时能明显提高淬透性。但含量过多时,会引起成分偏析,造成组织不均,材料成型性能急剧下降。经综合考虑,本发明设定mn含量为0.70~0.80%。
13.磷:磷为杂质元素,偏析于晶界使加工性能下降,希望尽可能减少其含量,提高成型性能;但考虑到工艺设备控制能力和脱磷成本,本发明限定p≤0.015%。
14.硫:硫为杂质元素,在钢中形成mns等夹杂物,影响精冲性能。希望尽可能减少其含量;考虑到实际控制能力和脱硫成本,本发明限定s≤0.003%。
15.铬:铬是碳化物形成元素,可形成多种合金碳化物;并抑制热轧后冷却过程中铁素体的生成,得到细小的铁素体晶粒和碳化物,显著提高材料强度和硬度,一般要求含量在0.15%以上,但含量过多会使合金成本增加,强度增加,同时也降低了加工性能。经综合考虑,本发明设定cr含量为0.15~0.35%。
16.铝:铝在本发明中的作用是起到脱氧以及结合游离态氮的作用,铝是强氧化性形成元素,和钢中氧形成al2o3在炼钢时去除。同时铝还具有细化晶粒,防止奥氏体晶粒的粗大的作用,随着铝含量的增加,以上效果下降显著;同时铝过高会形成过多的al2o3夹杂,在连铸浇注时容易堵塞浇注水口。经综合考虑,本发明设定al含量为0.01~0.03%。
17.氮:氮含量过高会严重恶化材料的塑性和韧性,使钢材脆性增加,还会造成连铸坯开裂。本发明限定n≤0.0060%。
18.上述抗拉强度1050mpa级精密冲压链锯导板用冷轧钢板的制造方法,该方法包括:
19.钢水经钢包精炼、真空脱气处理后进行连续浇注得到连铸板坯,其中所述钢水化学成分的重量百分比:c:0.52~0.58%,si:0.10~0.30%,mn:0.70~0.80%,p≤0.015%,s≤0.003%,cr:0.15~0.35%,al:0.01~0.03%,n≤0.0060%,其余为fe和不可避免的杂质,其余为fe和不可避免的杂质;
20.连铸板坯经加热炉加热至1180~1220℃,加热180~240min后进行热轧,所述热轧为两段式轧制工艺,粗轧为5道次连轧,在奥氏体再结晶温度以上轧制,初轧结束温度为1010~1050℃;精轧为7道次连轧,精轧结束温度为840~880℃,精轧压下率为88~95%;精轧后,控制热轧钢板厚度为1.8~3.5mm;层流冷却采用前段冷却,冷却速度为20~35℃/s,
卷取温度为600~640℃时卷取得到热轧钢卷;
21.热轧钢卷重新开卷后经酸洗、分条、冷轧、平整,得到厚度为0.80~1.60mm成品冷轧钢板,所述冷轧道次为6道次,冷轧压下率为45~60%;平整延伸率为1.5~2.5%。
22.本发明采取的生产工艺的理由如下:
23.1、连铸板坯加热温度和加热时间的设定
24.连铸板坯加热温度和时间的设定在于保证连铸坯中c、si、mn等合金元素充分扩散、固溶,粗大的碳化物颗粒溶解,在钢中均匀分布。温度过低和加热时间过短,都不能达到上述目的。采用中等的板坯加热温度,目标温度1200℃,若温度过高,加热时间过长,板坯表面氧化脱碳严重,不利于钢板最终性能和表面质量,同时也消耗能源。因此,本发明设定连铸板坯加热温度为1180℃~1220℃,加热时间为180~240min。
25.2、粗轧结束温度的设定
26.粗轧轧制过程控制在奥氏体再结晶温度以上轧制,确保得到均匀细小的奥氏体晶粒。因此本发明设定粗轧结束温度为1010~1050℃。
27.3、精轧结束温度的设定
28.本发明的精轧温度设定有两方面的作用,一方面通过材料在奥氏体未再结晶区轧制,得到内部有变形带的扁平状奥氏体晶粒,在随后的层流冷却过程中转变成细小的铁素体晶粒,起到细化晶粒,减轻带状偏析的作用;另一方面,若终轧温度过低,会导致轧制负荷过大,影响轧制稳定性。因此,本发明设定精轧结束温度为840~880℃。
29.4、层流冷却方式和冷却速度的设定
30.本发明精轧后层流冷却采用前段冷却工艺,能够促进精轧后材料组织中奥氏体快速转变为铁素体,且晶粒细化,组织均匀,冷却速度的设定20~35℃/s。
31.5、热轧卷取温度的设定
32.热轧卷取温度主要影响材料的组织、性能及后续的球化退火效果。采取中等的卷取温度,能够使晶粒细化、组织均匀,有利于后续冷轧。若卷取温度过高,则会使晶粒粗大,组织不均匀,若卷取温度过低,则会使热轧材料强度上升明显,钢卷脆性增加,不利于进一步的开卷分条和冷轧加工。因此,本发明设定热轧卷取温度为600~640℃。
33.6、冷轧压下率的设定
34.冷轧变形量是提高钢板硬度和规格尺寸精度的重要手段。随着冷轧变形量的不断增加,使材料内部位错密度大量增加,在加工硬化的作用下,材料硬度大幅增加。若冷轧变形量过小,一方面材料硬度不能达到要求;另一方面,较小的变形量只会使材料表面局部变形,造成带钢组织性能不均。但过高的变形量会使带钢硬度过高,脆性增加,轧制过程产生裂边。同时兼顾到冷轧过程各道次轧机的负荷,综合考虑,本发明优选冷轧压下率为45~60%。
35.7、平整延伸率的设定
36.为保证钢板厚度规格精度,一般平整延伸率设定在1.5~2.5%之间,平整延伸率过低则不能保证厚度精度;平整延伸率过高则使钢板表面局部硬度变化过大,影响材料使用性能。
37.本发明方法生产的冷轧钢板的金相组织为片状珠光体 铁素体,冷轧钢板的屈服强度r
p0.2
为850~1000mpa,抗拉强度rm为1050~1200mpa,屈强比为0.80~0.90,断后伸长率a50mm
为5~8%,洛氏硬度为33~37hrc;钢板厚度偏差≤0.020mm。
38.本发明相比现有技术具有如下积极效果:1、本发明通过在成分设计中采用较高的碳含量,提高材料硬度,并添加少量微合金元素cr的设计,控制热轧工艺过程温度和冷却方式;导板厚度较薄,通过冷轧多道次大压下、大变形量的方法,来达到导板的硬度要求;材料设计中取消了cr、mo贵重合金元素添加,降低了合金元素成本,制造成本低;得到了冷轧钢板的屈服强度r
p0.2
为850~1000mpa,抗拉强度rm为1050~1200mpa,屈强比为0.80~0.90,断后伸长率a
50mm
为5~8%,洛氏硬度为33~37hrc。2、本发明通过控制热轧卷取温度及轧后冷却工艺,发挥mn、cr合金元素作用;得到晶粒适度细化、强韧性适中的热轧态钢卷。同时在冷轧过程中,采用多道次和较大的累积压下率,使冷轧钢板硬度大幅增加,且韧性良好、组织均匀;满足链锯导板的耐磨性和精冲成形要求。取消了材料热处理工序,导板制造工序减少。
附图说明
39.图1为本发明实施例3热轧钢板的金相组织照片,其放大倍率为500倍。
40.图2为本发明实施例3冷轧钢板的金相组织照片,其放大倍率为1000倍。
具体实施方式
41.下面结合实施例1~5对本发明作进一步说明,如表1~5所示。
42.表1为本发明实施例钢的化学成分(按重量百分比计),余量为fe及不可避免杂质。
43.表1本发明实施例钢的化学成分,单位:重量百分比,%。
[0044][0045]
通过转炉熔炼得到符合化学成分基本要求的钢水,钢水经lf钢包精炼炉深脱硫和合金成分微调后,rh炉进行真空循环脱气处理,rh纯脱气时间大于8分钟,最后连铸机浇注得到连铸板坯;连铸板坯厚度为210~230mm,宽度为1000~1400mm,长度为8500~10500mm。
[0046]
炼钢生产的定尺板坯直接送至加热炉再加热,出炉除鳞后送至热连轧机组轧制。通过粗轧和精轧连轧机组控制轧制,经层流冷却后进行卷取,层流冷却采取前段冷却方式,产出热轧钢卷。热轧钢板的厚度为1.8~3.5mm;参见图1,热轧钢板金相组织为金相组织为片状珠光体 铁素体;热轧工艺控制参数见表2。
[0047]
表2本发明实施例热轧工艺控制参数
[0048][0049]
将本发明得到的热轧钢板按照《gb/t228.1~2010金属材料拉伸试验第1部分:室温试验方法》进行拉伸试验,钢的显微组织评定方法(gb/t 13299)检测显微组织,热轧钢板的力学性能见表3。
[0050]
表3本发明实施例热轧钢板的力学性能
[0051][0052]
将上述热轧钢卷重新开卷后进行酸洗,按照宽度规格要求分条后,在可逆轧机或单机架冷轧机上进行6道次冷轧,冷轧压下率为45~60%;冷轧后的轧硬态钢板经过平整后得到厚度为0.80~1.60mm的成品冷轧钢板,冷轧、平整工艺控制参数见表4。
[0053]
表4本发明实施例冷轧、平整工艺控制参数
[0054]
冷轧、平整参数冷轧压下率/%平整延伸率/%冷轧钢板厚度/mm本发明45~601.5~2.50.80~1.60实施例156.22.21.490实施例252.31.60.954实施例347.82.01.210实施例448.01.81.296实施例550.52.01.385
[0055]
利用上述方法得到的冷轧钢板,参见图2,冷轧钢板的金相组织为片状珠光体 铁素体,冷轧钢板的屈服强度r
p0.2
为850~1000mpa,抗拉强度rm为1050~1200mpa,屈强比为0.80~0.90,断后伸长率a
50 mm
为5~8%,洛氏硬度为33~37hrc;钢板厚度偏差≤0.020mm。
[0056]
将本发明得到的冷轧钢板按照《gb/t228.1~2010金属材料拉伸试验第1部分:室温试验方法》进行拉伸试验,钢的显微组织评定方法(gb/t 13299)检测显微组织,金属材料洛氏硬度试验方法(gb/t 230.1)进行硬度检测,冷轧钢板的力学性能见表5。
[0057]
表5本发明实施例冷轧钢板的力学性能
[0058][0059]
本发明得到的冷轧钢板具有高强度、高硬度和一定的韧性,基体以细片状珠光体为主分布均匀;满足高硬度、高耐磨性及精冲成形要求。
[0060]
除上述实施例外,本发明还可以有其他实施方式;凡采用等同替换或等效变换形成的技术方案,均落在本发明要求的保护范围内。
再多了解一些
本文用于企业家、创业者技术爱好者查询,结果仅供参考。