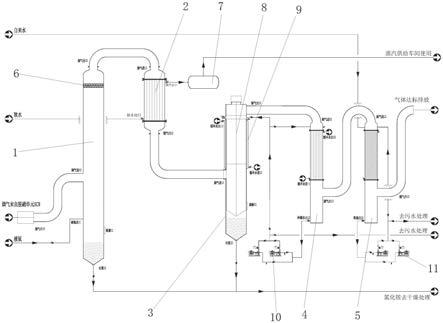
1.本发明涉及化工废液无害化处理领域,具体涉及一种解决三氯蔗糖废液处理过程中盐酸产量过大的装置与方法。
背景技术:
2.目前三氯蔗糖(cas号:56038-13-2)是一种新型的甜味剂,具有甜度高(约为蔗糖的600倍),极易溶于水,热量低,安全性高,人体几乎不吸收等优点,市场前景非常广阔。目前工业上合成三氯蔗糖的方法为:以蔗糖为原料,蔗糖经酯化反应制得蔗糖-6-乙酯,然后对蔗糖-6-乙酯进行氯化得到三氯蔗糖-6-乙酯,最后对三氯蔗糖-6-乙酯进行脱酯得到三氯蔗糖。
3.在三氯蔗糖生产过程中产生了大量废液,氯含量约在20%-26%之间,山东康宝生化科技有限公司目前采用焚烧的工艺处理三氯蔗糖废液,将三氯蔗糖废液输入到焚烧炉中进行焚烧,焚烧产生的烟气进行降温、除尘、脱硝、脱氯化氢,氯化氢气体被水吸收形成盐酸。
4.该焚烧工艺存在两个问题:
5.一是焚烧产生大量的氯化氢气体,最终成为副产盐酸。按照氯含量20%计算,100吨三氯蔗糖废液焚烧会产生氯化氢20.56吨,盐酸(hcl含量为30%)68.54吨。这些盐酸都需要妥善处理,否则容易对环境造成污染。
6.二是盐酸对装置的腐蚀问题。
7.上述问题正是烟气湿法脱氯化氢的弊端,因此避免烟气湿法脱氯化氢成为解决上述问题的唯一途径。
8.申请号为202011006202.9的专利公开了一种高含氯危险废物的焚烧处理方法,通过将高氯危险废物与脱氯剂氧化钙氧化镁等混合,使得氯元素固定在氯化钙氯化镁的灰渣中,达到减少烟气中氯化氢含量的目的。该方法目的是在焚烧阶段就使得氯化氢被脱氯剂固定下来,但是仍然存在两个问题:
9.一是脱氯剂氧化钙氧化镁难以运用于三氯蔗糖废液焚烧炉中,原因是投入固体氧化钙或者氧化镁的量过大,经过计算,100吨(氯含量为20%)三氯蔗糖废液需要投入15.77吨氧化钙或者11.77吨氧化镁才能将氯元素平衡,氯元素完全反应生成氯化钙或者氯化镁,这些氯化钙或者氯化镁变成灰渣,处理量巨大使得锅炉平稳运行收到较大影响。
10.二是无机氯化物焚烧前很容易与碱性的脱氯剂反应成为盐类,焚烧后成灰渣。但是三氯蔗糖废液中的氯元素多集中在分子上,焚烧前不与碱性脱氯剂发生反应,焚烧时产生的高温氯化氢气体与碱性脱氯剂反应活性很差,大部分氯化氢仍然存在于烟气中。
11.申请号为200710097522.8的专利提出了一种高温烟气中hci气体净化技术,属于干法脱氯化氢,将钙铝硅反应剂以粉末形式喷入烟气中,或者做成填料固定床,可以将烟气中的氯化氢气体脱除。该方法有两个问题:
12.一是,该方法属于气固反应,反应效率会比较低。而三氯蔗糖废液的焚烧烟气量一般大于10万立方米每小时,氯化氢通过反应器停留时间短,难以与固体脱氯剂充分反应。
13.二是,该方法属于气固反应,脱氯剂以及生成的氯盐都是固体状态,在烟气的速度冲击下会造成粉尘分散在烟气中,继而影响后续设备的正常运行。
14.山东康宝生化科技有限公司通过研究发现,利用氨气与氯化氢的气气反应可以将烟气中的氯化氢反应成氯化铵,该反应效率高,速度快,并且反应过程中释放可观的热量可加以利用。需要解决的一个问题是反应生成物氯化铵颗粒的直径非常小,在烟气中成为气溶胶,需要将其捕集,从烟气中分离出来。
技术实现要素:
15.本发明的目的在于克服现有技术存在的缺点,提供一种解决三氯蔗糖废液处理过程中盐酸产量过大的装置与方法。
16.为了实现上述目的,本发明的技术方案是:一种解决三氯蔗糖废液处理过程中盐酸产量过大的方法,其特征在于,包括以下步骤:
17.(1)气气反应:三氯蔗糖废液焚烧、脱硝后的烟气与液氨分别进入气气反应器,烟气中的氯化氢与氨气发生反应生成氯化铵颗粒,氯化铵颗粒在烟气中分散开呈气溶胶状态,随着烟气上升,一部分氯化铵颗粒生长变大,烟气经气气反应器顶部筛网过滤进入换热器管程,氯化铵气溶胶随烟气进入换热器管程,大颗粒氯化铵被过滤沉降至气气反应器底部排出进行干燥处理,得氯化铵副产物;
18.(2)烟气换热产生蒸汽:换热器壳程中的软化水,被烟气加热,形成蒸汽,进入蒸汽汽包,烟气经换热器管程换热后进入捕集器;
19.(3)氯化铵捕集:烟气在捕集器内进行降温、喷淋,烟气中的氯化铵气溶胶被水雾吸收沉降到捕集器底部,捕集器内的螺旋刮板搅拌器,将贴壁的氯化铵与水糊状物刮至捕集器底部,将捕集器底部的氯化铵浆料排出进行干燥处理,得氯化铵副产物,降温及脱除氯化铵气溶胶的烟气经捕集器烟气出口排出,进入降膜冷凝器;
20.(4)降膜冷凝:烟气在降膜冷凝器中冷却降温,烟气中的气态水冷凝成液态水,冷凝后的烟气进入填料吸收器;
21.(5)烟气净化:进入填料吸收器的烟气经过水循环吸收达到环保排放标准,排放至大气。
22.进一步地;步骤(1)中所述烟气与液氨分别切线进入气气反应器,所述液氨进入气气反应器后升温成氨气,所述烟气与氨气在气气反应器内部做螺旋运动,且相逆错开旋转,接触程度最大化。
23.进一步地;步骤(1)中所述三氯蔗糖废液焚烧、脱硝后的烟气温度为180-250℃,发生反应后烟气温度上升至250-300℃,并进入换热器管程,氯化氢与氨气反应释放可观的热量(如表1所示),能够导致烟气温度上升。
24.进一步地;步骤(2)中所述蒸汽的压力0.3-0.6mpa,温度133-159℃。
25.进一步地;步骤(2)中烟气经换热器管程换热后温度为140-170℃,换热后的烟气温度过低则会导致烟气中的气态水冷凝成液体与氯化铵形成浆料物影响换热器运行,温度过高则蒸汽产量会相应变少。
26.进一步地;步骤(3)中捕集器烟气出口排出的烟气温度为100-120℃,温度过低则大量的水气冷凝为液体在捕集器底部富集,得到的氯化铵浆料就会比较稀,同时后续降膜冷凝器得到的冷凝水就会比较少;温度过高则会增加降膜冷凝器的负荷。
27.表1
[0028] 数值单位备注日焚烧废液量200.000t 日产生氯化氢量41.127t按氯含量20%计氯化氢流量1713.615kg/h 氨气流量798.122kg/h 水气流量4746.667kg/h 二氧化碳流量4913.333kg/h 氧气流量675.000kg/h 氮气流量160000.000kg/h 烟气合计172846.737kg/h 反应热14084507.042kj氯化铵生成热按300kj/mol计气体比热1.100kj/(kg
·
℃) 温度上升74.078℃ [0029]
表1数据说明,在每天焚烧200t三氯蔗糖废液的情况下,每小时产生1713.615kg氯化氢,消耗798.122kg氨气来生成氯化铵,反应热按300kj/mol计算,每小时氯化氢和氨气反应放出的热量为1713.615
×
1000
÷
36.5
×
300=14084507.042kj,氮气比热1.038kj/(kg
·
℃),烟气的比热估计值调高至1.10kj/(kg
·
℃),那么氯化氢与氨气的反应热能够导致烟气上升的温度是14084507.042
÷
1.10
÷
173846.737=74.078℃。
[0030]
由此可见,氯化氢与氨气的反应热非常可观,这些热量会使得烟气温度显著上升,给蒸汽的产生提供了必要条件。
[0031]
本发明的另一技术方案是:一种解决三氯蔗糖废液处理过程中盐酸产量过大的装置,其特征在于:包括依次连接的气气反应器、换热器、捕集器、降膜冷凝器和填料吸收器,所述气气反应器壁设有烟气进口和液氨进口,所述烟气进口和液氨进口均设置在气气反应器壁切线方向,且烟气进口与液氨进口的切线方向相反,所述换热器壳程中的蒸汽出口连接蒸汽汽包,供给车间使用,所述降膜冷凝器底部设有冷凝水出口,所述冷凝水出口连接第一循环泵组,所述第一循环泵组出口管线分成三部分:一部分回到所述降膜冷凝器顶部,另一部分进入捕集器顶部,第三部分进入污水处理;所述填料吸收器顶部设有洗涤水入口,所述洗涤水入口连接自来水管线,所述填料吸收器底部设有料液出口,所述料液出口连接第二循环泵组,所述第二循环泵组出口管线分成两部分:一部分回到填料吸收器顶部,另一部分进入污水处理。
[0032]
进一步地;所述气气反应器顶部设有筛网。
[0033]
进一步地;所述捕集器内设有螺旋刮板搅拌器,可将贴壁的氯化铵与水糊状物刮至捕集器底部,所述捕集器外部设有冷却夹套。
[0034]
本发明的有益效果:本发明公开了一种解决三氯蔗糖废液处理过程中盐酸产量过大的装置与方法,属于化工废液无害化处理领域,通过将脱硝后烟气中的氯化氢与氨气在
气气反应器中生成氯化铵,并经过烟气换热、氯化铵捕集等步骤分离氯化铵副产,同时将可观的反应热利用起来成为蒸汽供给车间使用,解决了盐酸产量过大以及装置腐蚀等问题,具有重要的经济效益和环保效益。
[0035]
本发明的工艺简单可行,有效解决三氯蔗糖废液处理过程中盐酸产量过大的问题,将烟气中的氯化氢与氨气反应生成氯化铵,不产生盐酸,治污成本与难度进一步降低。
[0036]
本发明巧妙地利用氯化氢与氨气的反应热,产生蒸汽供给车间使用。
[0037]
本发明中的捕集器解决了氯化铵气溶胶造成的回收氯化铵难问题。
[0038]
本发明中的填料吸收器使用水代替液碱进行烟气净化,降低治污成本。
附图说明
[0039]
图1是本发明装置结构示意图;
[0040]
图2为尾气达标排放经过在线监测仪器时的分析数据截图。
[0041]
图中:1、气气反应器;2、换热器;3、捕集器;4、降膜冷凝器;5、填料吸收器;6、筛网;7、蒸汽汽包;8、螺旋刮板搅拌器;9、冷却夹套;10、第一循环泵组;11、第二循环泵组。
具体实施方式
[0042]
为使本发明实施例的目的、技术方案和优点更加清楚,下面将对本发明实施例中的技术方案进行清楚、完整地描述。实施例中未注明具体条件者,按照常规条件或制造商建议的条件进行。所用试剂或仪器未注明生产厂商者,均为可以通过市售购买获得的常规产品。
[0043]
实施例1:
[0044]
一种解决三氯蔗糖废液处理过程中盐酸产量过大的方法,包括以下步骤:
[0045]
(1)气气反应:三氯蔗糖废液焚烧、脱硝后201℃的烟气通过烟气进口切线进入气气反应器1,液氨通过液氨进口切线进入气气反应器1,所述液氨进入气气反应器1后升温成氨气,所述烟气与氨气在气气反应器1内部做螺旋运动,且相逆错开旋转,烟气中的氯化氢与氨气发生反应生成氯化铵颗粒,氯化氢与氨气的反应热使烟气温度上升,氯化铵颗粒在烟气中分散开呈气溶胶状态,烟气上升经筛网6过滤后进入换热器2管程,氯化铵气溶胶随烟气进入换热器2管程,大颗粒氯化铵被过滤沉降至气气反应器1底部排出进行干燥处理,得氯化铵副产物;
[0046]
(2)烟气换热:253℃烟气进入换热器2管程,换热器2壳程中的软化水,被烟气加热,形成蒸汽,所述蒸汽的压力0.32mpa,温度136℃,蒸汽进入蒸汽汽包7,供给生产车间使用,烟气经换热器2管程换热后温度降至142℃,并进入捕集器3;
[0047]
(3)氯化铵捕集:烟气在捕集器3内进行降温、喷淋,烟气中的氯化铵气溶胶被水雾吸收沉降到捕集器3底部,捕集器3内的螺旋刮板搅拌器8,将贴壁的氯化铵与水糊状物刮至捕集器3底部,将捕集器3底部的氯化铵浆料排出进行干燥处理,得氯化铵副产物,降温及脱除氯化铵气溶胶的103℃烟气经捕集器3烟气出口排出,并进入降膜冷凝器4;
[0048]
(4)降膜冷凝:烟气在降膜冷凝器4中冷却降温至48℃,烟气中的气态水冷凝成液态水,冷凝后的烟气进入填料吸收器5,液态水从降膜冷凝器4冷凝水出口排出进入第一循环泵组10,第一循环泵组10将冷凝水分成三部分,一部分返回到降膜冷凝器4顶部;第二部
分喷入捕集器3顶部,将烟气中的气溶胶状态的氯化铵颗粒捕集到水中沉降至捕集器3底部;第三部分进入污水处理管线;
[0049]
(5)烟气净化:进入填料吸收器5的烟气经过水循环吸收达到环保排放标准,排放至大气。填料吸收器5底部料液通过料液出口进入第二循环泵组11,第二循环泵组11将料液分成两部分,一部分返回填料吸收器5顶部,另一部分进入污水处理管线。
[0050]
烟气最终排放,氮氧化合物(nox)浓度降至100mg/m3以下,so2浓度降至50mg/m3以下,粉尘浓度降至10mg/m3以下,hcl浓度降至60mg/m3以下,二噁英浓度降至0.5ng teq/m3以下。以上污染物排放限值,为标态、干基、11%基准氧的值。
[0051]
实施例2~8:
[0052]
一种解决三氯蔗糖废液处理过程中盐酸产量过大的方法,与实施例1步骤相同,记录各阶段数据如表2所示。
[0053]
表2实施例1~8的参数设置
[0054][0055]
备注:三氯蔗糖废液焚烧处理量越大,则产生氯化氢的量越大,对应需要的氨气量越大,氯化氢与氨气发生反应产生的热量就会越多,气气反应之后烟气的温度就会升的越高。
[0056]
实施例9:
[0057]
如图1所示,一种解决三氯蔗糖废液处理过程中盐酸产量过大的装置,包括依次连接的气气反应器1、换热器2、捕集器3、降膜冷凝器4和填料吸收器5。所述气气反应器1壁设有烟气进口和液氨进口,所述烟气进口和液氨进口均设置在气气反应器壁1切线方向,且烟气进口与液氨进口的切线方向相反,所述气气反应器1顶部设有筛网6。
[0058]
所述换热器2壳程中的蒸汽出口连接蒸汽汽包7,供给车间使用。所述捕集器3内设有螺旋刮板搅拌器8,可将贴壁的氯化铵与水糊状物刮至捕集器3底部,所述捕集器3外部设有冷却夹套9。所述降膜冷凝器4底部设有冷凝水出口,所述冷凝水出口连接第一循环泵组10,所述第一循环泵组10出口管线分成三部分:一部分回到所述降膜冷凝器4顶部;另一部
分进入捕集器3顶部喷淋,将烟气中的气溶胶状态的氯化铵颗粒捕集到水中沉降至捕集器3底部;第三部分去污水处理。
[0059]
所述填料吸收器5顶部设有洗涤水入口,所述洗涤水入口连接自来水管线,所述填料吸收器5底部设有料液出口,所述料液出口连接第二循环泵组11,所述第二循环泵组11出口管线分成两部分:一部分回到填料吸收器5顶部,另一部分去污水处理。所述第一循环泵组10和第二循环泵组11均有两个并列的循环泵组成。
[0060]
在本发明的描述中,需要理解的是,指示方位或位置关系的术语为基于附图所示的方位或位置关系,仅是为了便于描述本发明和简化描述,而不是指示或暗示所指的设备或元件必须具有特定的方位、以特定的方位构造和操作,因此不能理解为对本发明的限制。
再多了解一些
本文用于企业家、创业者技术爱好者查询,结果仅供参考。