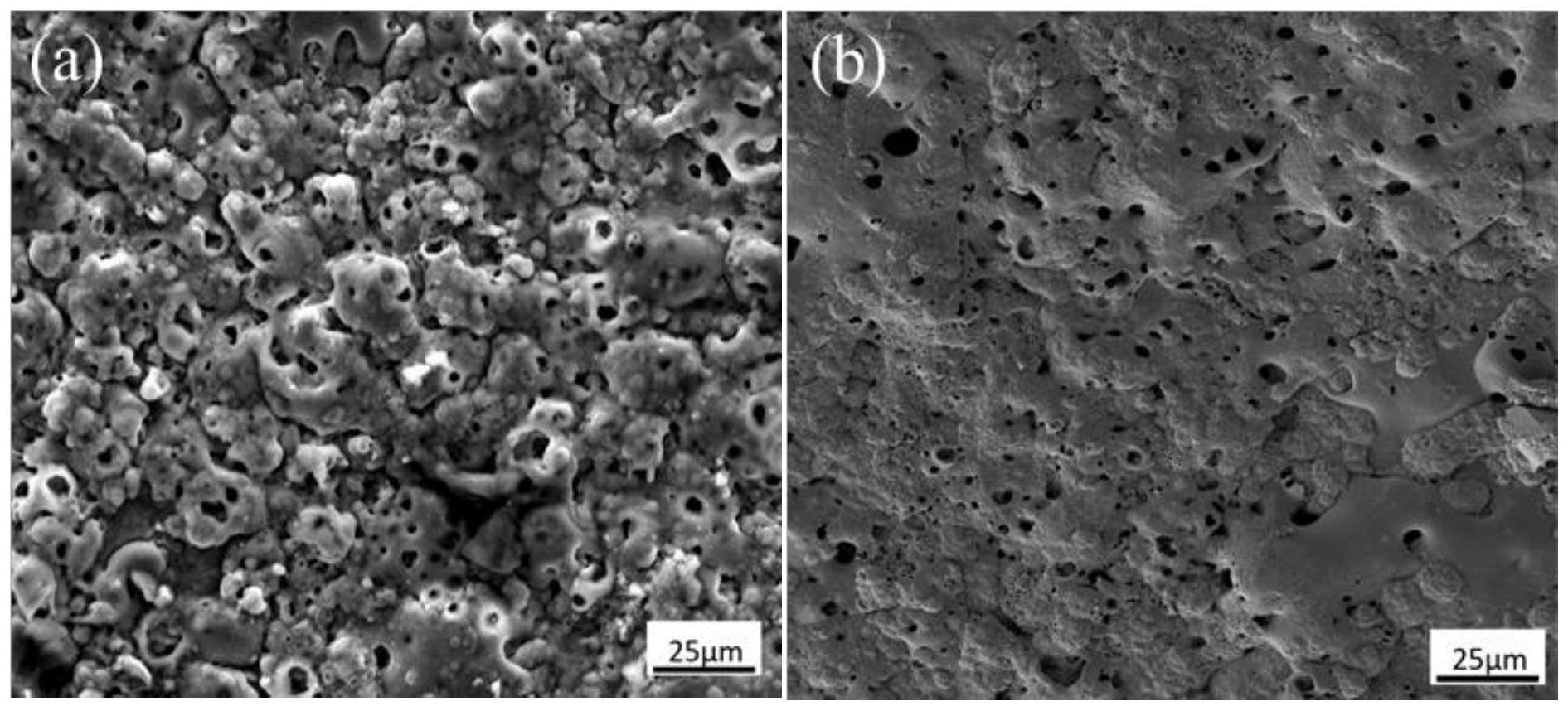
1.本发明属于材料表面处理技术领域,具体涉及一种铜及其合金的表面微弧氧化-高温氧化方法。
背景技术:
2.纯铜具有良好的导电性、导热性、延展性和耐蚀性。纯铜价格低廉使用广泛,主要应用在发电机、母线、电缆、开关装置、变电器等电工器材和热交换器材中。纯铜在这些应用场景时往往会与空气中的二氧化碳和水蒸气相接触,但纯铜易和水、二氧化碳反应生成碱式碳酸铜,为了延长铜器件的使用寿命,减少事故的发生,因此提高铜的耐蚀、耐磨性能极其重要。在众多的处理方式中,表面处理有着应用范围广、跨度大、价格低廉等优势,应用在铜及其合金的表面处理方法主要有等离子喷涂、激光熔覆、激光合金化和激光表面淬火和重熔。
3.等离子喷涂是一种材料表面强化和表面改性的技术,具有操作简单,设备维护成本低,调节性能好等优点,但铜及铜合金材料高导热特性放大了基体与涂层结合力差的缺点,导致所得涂层的耐磨性大大降低。激光熔覆利用高功率激光束快速融化金属基体与覆层粉末,快速凝固后与基体冶金结合。这种手段适用于在极端条件下应用的关键铜部件表面强化,但由于铜及铜合金高热导率、高红外反射率、高热膨胀率的特点,导致表面激光熔覆容易出现熔池形成困难、熔覆层与铜基体结合差、覆层应力开裂等问题。激光表面合金化是利用高能量激光束熔化基材表面与合金元素、陶瓷等粉末,在基体表面形成合金层。激光合金化技术依靠预置粉末等手段,克服铜及铜合金基体高激光反射率限制,实现基体表面与合金原料粉末的冶金结合,但由于制备预置层工艺流程长、技术复杂度高的限制并没有得到广泛的应用。激光表面淬火和重熔是依靠激光高能量密度带来的快速熔凝效应实现。在铜合金表面激光淬火与重熔技术可使表面尺寸近乎无变化、深度可控、加工流程短,但在快速熔凝的同时,也会使材料表层的内应力提高、并使组织出现垂直于扫描方向的周期性变化,造成激光淬火与重熔区域开裂。因此,传统工艺不能兼顾铜及其合金表面生成的膜的耐蚀性和附着力。
技术实现要素:
4.本发明的目的在于,针对现有技术的不足,提供一种铜及其合金的表面微弧氧化-高温氧化方法,先使用微弧氧化处理方式使铜及其合金表面得到耐蚀性良好的膜层,后进行高温氧化处理,使气体通过膜层的孔隙进入到基体与膜层之间的孔隙中形成一层过渡层,这种方式在保留了金属在微弧氧化处理后膜层的耐蚀性的,同时,极大的提高膜层的附着力。
5.本发明的目是提供一种铜及其合金的表面微弧氧化-高温氧化方法,包括如下步骤:
6.s1、对试样进行切割后进行逐级打磨,然后进行清洗、烘干;
7.s2、以s1得到的试样作为阳极,石墨板作为阴极,置于的电解液中进行微弧氧化处理,然后进行冲洗、烘干;
8.s3、将s2得到的试样在氧气气氛中进行高温处理,然后冷却至室温。
9.优选的,s1中,所述打磨的方式为依次用240#、400#、600#、1000#和2000# 的sic砂纸打磨。
10.优选的,s1中,所述清洗的溶剂为乙醇或丙酮。
11.优选的,s2中,所述电解液为na2sio3·
9h2o和naoh的混合溶液。
12.优选的,na2sio3·
9h2o溶液的浓度为15-35g/l,naoh溶液的浓度为2-6g/l。
13.优选的,s2中,所述微弧氧化的工艺参数为:电压650-750v,电流密度2-6 a/cm2,脉冲频率100-500hz,占空比20-60%。
14.优选的,s2中,所述微弧氧化处理的时间为10-50min。
15.优选的,s2中,所述冲洗采用去离子水冲洗后吹干。
16.优选的,s3中,所述氧气的气体流量为0-600ml/min。
17.优选的,s3中,所述高温处理的工艺参数为:先进行升温5-10min,升至目标温度后,进行保温30-60min,再进行降温,降温的速率为5-10℃/min。
18.本发明与现有技术相比,其有益效果在于:
19.本发明通过微弧氧化处理方式使铜及其合金表面得到耐蚀性良好的膜层,然后进行高温氧化处理,使气体通过膜层的孔隙进入到基体与膜层之间的孔隙中形成氧化膜,将孔隙填充,保留了金属在微弧氧化处理后膜层的耐蚀性,同时极大的提高膜层的附着力。
附图说明
20.图1为实施例1制备的铜表面膜的宏观样貌图;
21.图2为实施例1及对比例1制备的铜表面膜的表面电镜扫描图;其中,(a) 为对比例1,(b)为实施例1;
22.图3为实施例1及对比例1制备的铜表面膜的截面电镜扫描图;其中,(a) 为对比例1,(b)为实施例1;
23.图4为实施例1制备的铜表面膜的x射线衍射图;
24.图5为实施例1制备的铜表面膜的动电位极化曲线图;
25.图6为实施例1制备的铜表面膜和对比例1制备的铜表面膜的摩擦系数图;
26.图7为实施例1制备的铜表面膜和对比例1制备的铜表面膜的附着力测试图;其中,(a)为对比例1,(b)为实施例1。
具体实施方式
27.下面将结合本发明实施例中的数据,对本发明实施例中的技术方案进行清楚、完整地描述,显然,所描述的实施例仅是本发明一部分实施例,而不是全部的实施例。基于本发明中的实施例,本领域普通技术人员在没有做出创造性劳动前提下所获得的所有其他实施例,都属于本发明保护的范围。
28.需要说明的是,本发明中所使用的专业术语只是为了描述具体实施例的目的,并不是旨在限制本发明的保护范围,除非另有特别说明,本发明以下各实施例中用到的各种
原料、试剂、仪器和设备均可通过市场购买得到或者通过现有方法制备得到。
29.实施例1
30.一种铜及其合金的表面微弧氧化-高温氧化方法,包括如下步骤:
31.s1、将纯铜切割成15*15*5mm的大小,依次用240#、400#、600#、1000# 和2000#的sic砂纸打磨,然后乙醇进行清洗后进行吹干;
32.s2、首先配置28.42g/l的na2sio3·
9h2o和4g/l的naoh的电解液,体积为5l,然后以s1得到的试样作为阳极,石墨板作为阴极,置于的电解液中进行微弧氧化处理,采用恒流模式进行处理,其中,脉冲电源的电压为500v,电流密度为4.44a/cm2,脉冲频率为200hz,占空比正50%负30%,微弧氧化25min,束后将试样取出用去离子水冲洗并吹干;
33.s3、将s2得到的试样放入管式退火炉中,通入氧气,调节气体流量为 300ml/min进行高温氧化处理,设置升温时间为10min,加热温度为150℃,然后保温时间为30min,再室温降温,其降温的速率为5℃/min,待样品室温冷却后拿出。
34.实施例2
35.一种铜及其合金的表面微弧氧化-高温氧化方法,包括如下步骤:
36.s1、将纯铜切割成15*15*5mm的大小,依次用240#、400#、600#、1000# 和2000#的sic砂纸打磨,然后乙醇进行清洗后进行吹干;
37.s2、首先配置35g/l的na2sio3·
9h2o和6g/l的naoh的电解液,体积为 5l,然后以s1得到的试样作为阳极,石墨板作为阴极,置于的电解液中进行微弧氧化处理,采用恒流模式进行处理,其中,脉冲电源的电压为550v,电流密度为4.44a/cm2,脉冲频率为200hz,占空比正60%负40%,微弧氧化30min,束后将试样取出用去离子水冲洗并吹干;
38.s3、将s2得到的试样放入管式退火炉中,通入氧气,调节气体流量为 400ml/min进行高温氧化处理,设置升温时间为8min,加热温度为200℃,然后保温时间为30min,再室温降温,其降温的速率为5℃/min,待样品室温冷却后拿出。
39.实施例3
40.一种铜及其合金的表面微弧氧化-高温氧化方法,包括如下步骤:
41.s1、将纯铜切割成15*15*5mm的大小,依次用240#、400#、600#、1000# 和2000#的sic砂纸打磨,然后乙醇进行清洗后进行吹干;
42.s2、首先配置40g/l的na2sio3·
9h2o和8g/l的naoh的电解液,体积为 5l,然后以s1得到的试样作为阳极,石墨板作为阴极,置于的电解液中进行微弧氧化处理,采用恒流模式进行处理,其中,脉冲电源的电压为600v,电流密度为4.44a/cm2,脉冲频率为200hz,占空比正70%负30%,微弧氧化40min,束后将试样取出用去离子水冲洗并吹干;
43.s3、将s2得到的试样放入管式退火炉中,通入氧气,调节气体流量为 300ml/min进行高温氧化处理,设置升温时间为10min,加热温度为600℃,然后保温时间为40min,再室温降温,其降温的速率为10℃/min,待样品室温冷却后拿出。
44.实施例4
45.一种铜及其合金的表面微弧氧化-高温氧化方法,包括如下步骤:
46.s1、将纯铜切割成15*15*5mm的大小,依次用240#、400#、600#、1000# 和2000#的sic砂纸打磨,然后乙醇进行清洗后进行吹干;
47.s2、首先配置45g/l的na2sio3·
9h2o和10g/l的naoh的电解液,体积为5l,然后以s1
得到的试样作为阳极,石墨板作为阴极,置于的电解液中进行微弧氧化处理,采用恒流模式进行处理,其中,脉冲电源的电压为750v,电流密度为4.44a/cm2,脉冲频率为200hz,占空比正50%负50%,微弧氧化40min,束后将试样取出用去离子水冲洗并吹干;
48.s3、将s2得到的试样放入管式退火炉中,通入氧气,调节气体流量为 600ml/min进行高温氧化处理,设置升温时间为5min,加热温度为250℃,然后保温时间为60min,再室温降温,其降温的速率为8℃/min,待样品室温冷却后拿出。
49.对比例1
50.一种铜及其合金的表面微弧氧化-高温氧化方法,包括如下步骤:
51.s1、将纯铜切割成15*15*5mm的大小,依次用240#、400#、600#、1000# 和2000#的sic砂纸打磨,然后乙醇进行清洗后进行吹干;
52.s2、首先配置28.42g/l的na2sio3·
9h2o和4g/l的naoh的电解液,体积为5l,然后以s1得到的试样作为阳极,石墨板作为阴极,置于的电解液中进行微弧氧化处理,采用恒流模式进行处理,其中,脉冲电源的电压为500v,电流密度为4.44a/cm2,脉冲频率为200hz,占空比正50%负30%,微弧氧化25min,束后将试样取出用去离子水冲洗并吹干。
53.图1为实施例1制备的铜表面膜的宏观样貌图,如图1所示,铜表面膜的膜层颜色为黑色。
54.图2为实施例1及对比例1制备的铜表面膜的表面电镜扫描图;其中,(a) 为对比例1,(b)为实施例1。如图2(b)所示,与仅做微弧氧化后图2(a) 对比例1相比,实施例1铜表面经过微弧氧化-高温氧化方法处理纯铜试样表面膜的孔隙尺寸、密度均明显减小。
55.图3为实施例1及对比例1制备的铜表面膜的截面电镜扫描图;其中,(a) 为对比例1,(b)为实施例1。如图3(b)所示,实施例1制备的膜层与基体的界面处结合的十分紧密,铜表面经过微弧氧化-高温氧化方法处理纯铜试样表面的膜层约20μm。
56.图4为实施例1制备的铜表面膜的x射线衍射图,如图4所示,实施例1 经过微弧氧化处理方式,然后进行高温氧化处理后,铜表面膜的膜层的主要成分是cuo。
57.图5为实施例1制备的铜表面膜的动电位极化曲线图,如图5所示,实施例1经过微弧氧化处理方式,然后进行高温氧化处理后,腐蚀电流密度与cu相比明显下降,由5.6
×
10-6
a/cm2(cu)降到1.6
×
10-6
a/cm2。
58.图6为实施例1制备的铜表面膜和对比例1制备的铜表面膜的摩擦系数图,经过微弧氧化和高温氧化处理的铜表面膜与只经过微弧氧化处理的相比,摩擦系数有一定程度上的减少,并且采用拉拔法测试附着力时,如图7为实施例1 制备的铜表面膜和对比例1制备的铜表面膜的附着力测试图,在相同的实验条件下实施例1经过微弧氧化-高温氧化方法得到表面膜的约有一半没有拉拔下来如图7(b)所示,而对比例1只通过微弧氧化方法得到表面膜完全拉拔下来如图7(a)所示,说明经过微弧氧化-高温氧化方法得到的膜层的附着力有明显的提升,表面耐磨性有所提高。
59.需要说明的是,本发明中涉及数值范围时,应理解为每个数值范围的两个端点以及两个端点之间任何一个数值均可选用,由于采用的步骤方法与实施例相同,为了防止赘述,本发明描述了优选的实施例。尽管已描述了本发明的优选实施例,但本领域内的技术人员一旦得知了基本创造性概念,则可对这些实施例做出另外的变更和修改。所以,所附权利要求意欲解释为包括优选实施例以及落入本发明范围的所有变更和修改。
60.显然,本领域的技术人员可以对本发明进行各种改动和变型而不脱离本发明的精神和范围。这样,倘若本发明的这些修改和变型属于本发明权利要求及其等同技术的范围之内,则本发明也意图包含这些改动和变型在内。
再多了解一些
本文用于企业家、创业者技术爱好者查询,结果仅供参考。