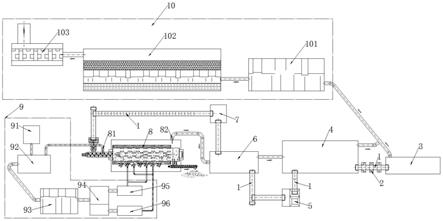
1.本实用新型涉及到垃圾环保处理技术领域,具体涉及一种基于热裂解釜的混合焦油可燃气再利用系统。
背景技术:
2.随着全球经济和工业化的快速发展,城市规模的不断扩大,城市生活垃圾产生总量与日俱增,在工业化处理城市生活垃圾的过程中,为达到减量化和完整处理垃圾,都是以焚烧和填埋二种方式进行处理。但同时带来了无法根除的隐患:废水、废气、废渣二次污染问题。尤其是中国大多数城市目前正遭受生活垃圾无法有效处置所带来的困扰,垃圾处置已成为中国可持续发展所面临的巨大挑战。
3.生物质热裂解技术是使生物质在基本无氧气(与空气隔绝)的情形下,通过热化学转换,生成炭、液体和气体产物的过程。根据气相滞留期、升温速率、最高温度的不同,生成的炭、气体和液体组成比例也不同。现有的生物质物料热裂解技术按顺序主要包括“物料的粉碎
→
烘干成型
→
热裂解
→
冷却分离”,其中热裂解是其中的核心工艺,该工艺的处理水平直接关系到产率和生成物的质量,因此至关重要。热裂解是在热裂解釜中进行的,成型原料放入热裂解釜中,对热裂解釜进行加热,使其内部发生化学变化,从而得到气固生成物。
4.然而,现有热裂解装置存在的缺点有:
①
焦油与石油焦易结圬,5天需停机清除维护(易爆炸),
②
加热室的尾气余热白白浪费,
③
热裂解产生的焦油与可燃气不能循环利用,
④
任由废渣填埋,
⑤
任以水降温脱尘,废水处理难度大。
技术实现要素:
5.针对现有技术的不足,本实用新型的目的是提供一种基于热裂解釜的混合焦油可燃气再利用系统,能够实现生活垃圾无氧热辐射炭化处理过程中产生的焦油、可燃气的二次能源化利用。
6.为达到上述目的,本实用新型采用的技术方案如下:
7.一种基于热裂解釜的混合焦油可燃气再利用系统,其关键在于:包括通过输送机逐级相连的垃圾储存池、垃圾分选子系统、烘干设备、破碎装置、预烘干装置、造粒装置与热裂解炭化装置,所述热裂解炭化装置的热裂解混合可燃气排出口上连接有混合可燃气处理子系统,该混合可燃气处理子系统对混合焦油可燃气进行处理后输送至热裂解炭化装置进行燃烧供能。
8.进一步的,所述热裂解炭化装置包括旋转固定在密闭的隔热壳内的热裂解釜,在所述隔热壳的顶部开设有高温尾气排出口,在所述热裂解釜下方的隔热壳内分别设置有燃烧机构,所述热裂解釜的进料端设置有螺旋输送机构,所述螺旋输送机构的中部开设所述热裂解混合可燃气排出口,在所述螺旋输送机构的进料口上连接有锁风进料机构,所述热裂解釜的出料端连接有水冷螺旋出料机构。
9.进一步的,所述燃烧机构包括相间设置的主燃烧组件与辅助燃烧组件。
10.进一步的,所述辅助燃烧组件包括焦油燃烧结构与混合可燃气燃烧结构,所述焦油燃烧结构与混合可燃气燃烧结构的进料端均连接至所述混合可燃气处理子系统。
11.进一步的,所述混合可燃气处理子系统包括蒸汽发生装置、蒸汽混合装置、冷却装置、脱焦脱水装置,所述蒸汽发生装置通过蒸汽管道与所述蒸汽混合装置相连,所述蒸汽混合装置用于利用蒸汽将混合可燃气进行充分混合和降温,所述蒸汽混合装置的混合可燃气进口与所述热裂解炭化装置的热裂解混合可燃气排出口相连,所述蒸汽混合装置的出气口经所述冷却装置输送至所述脱焦脱水装置对冷却降温后的混合气体进行脱焦、脱水处理,所述脱焦脱水装置形成的液态焦油输送至焦油超声波乳化装置,所述焦油超声波乳化装置将脱下的含焦油废水升温后按比例添加入脱水后的液态焦油中,利用液哨超声波技术形成油包水结构并输送至所述热裂解炭化装置,所述脱焦脱水装置形成的可燃气输送至可燃气稳压装置,所述可燃气稳压装置将可燃气进行稳压处理后输送至所述热裂解炭化装置。
12.进一步的,所述蒸汽混合装置与冷却装置均采用不接触冷媒热交换式冷却器。
13.进一步的,所述蒸汽混合装置具有220根dn38薄壁不锈钢换热管;所述冷却装置具有60根dn38薄壁不锈钢换热管。
14.本实用新型的显著效果是:
15.1.本系统不仅实现了生活垃圾无氧热辐射炭化处理过程中焦油、可燃气的二次能源化利用,相较于传统技术,从根本上有效避免了管道自然冷却堵管、喷淋法产生大量废水且其废水解决成本奇高以及直排降温中的结焦、堵塞和爆炸等诸多问题缺陷;
16.2.热裂解炭化装置的炉温较低,为500-600度,且不使用传统喷淋法,免去大量生产性废稀酸、焦油、臭气的混合废水;
17.3.蒸汽混合装置与冷却装置采用蒸汽协同降温处理,在蒸汽混合冷却时焦油凝结在热交换器壁上温度不低于80℃,在冷却装置二次冷却脱焦时进入小型热交换器,由于总的横截面减小,混合可燃气体又因前端有雾化蒸汽喷淋,焦油在二次降温和向下的惯性作用下更彻底脱除,此过程中既保持了焦油的流动性、低酸性、能源化的再利用,又减小了设备腐蚀、保证了设备使用寿命、降低了后期维护成本;
18.4.在脱焦脱水装置中,所采用的降温、聚凝焦油技术,相较于传统冷水喷淋法技术,实现了高温饱合焦油气体由蒸汽降温凝油法,使焦油既保持了流动性、又保障了低酸腐蚀性;
19.5.物热辐射处理后的混合生物质炭,其减容90%以上,减容效果相当显著;完全炭化的炭灰为土壤改良基础肥,反应产生的颗粒物用作制砖原料,实现了生活垃圾彻底变废为宝。
附图说明
20.图1是本实用新型的结构示意图;
21.图2是所述热裂解炭化装置的结构示意图。
具体实施方式
22.下面结合附图对本实用新型的具体实施方式以及工作原理作进一步详细说明。
23.如图1所示,一种基于热裂解釜的混合焦油可燃气再利用系统,包括通过输送机1
逐级相连的垃圾储存池2、垃圾分选子系统3、烘干设备4、破碎装置5、预烘干装置6、造粒装置7与热裂解炭化装置8,所述热裂解炭化装置8的热裂解混合可燃气排出口81上连接有混合可燃气处理子系统9,该混合可燃气处理子系统9对混合焦油可燃气进行处理后输送至热裂解炭化装置8进行燃烧供能,所述热裂解炭化装置8的高温尾气排出口82通过管道与所述预烘干装置6的进风口相连,所述预烘干装置6的臭气排放口与所述烘干设备4的进气口连通,所述烘干设备4的臭气排放口与垃圾储存池2的臭气排放口均连接至臭气处理子系统10,所述臭气处理子系统10对臭气进行净化处理后达标排放。
24.所述垃圾分选子系统3通过精细化分选技术对生活垃圾进行分类,所述烘干设备4对生活垃圾进行烘干处理,所述破碎装置5对生活垃圾进行5mm标准化破碎,所述预烘干装置6利用热裂解炭化装置8的高温尾气的余热对垃圾进行预烘干,所述造粒装置7用于对预烘干后的垃圾进行均质化和标准化脱水造粒处理,所述热裂解炭化装置8用于按照设定的运行参数将生活垃圾逐步受热裂解,将垃圾进行吸热无氧气化炭化,固体物碳化成生物质可燃炭。垃圾混合物在无氧气炭化过程中,由于富含植物纤维、淀粉、糖、各有机酸脂、絮凝剂酯等物质,在无氧高温热裂解环境中形成大量的可然气、粉尘和焦油,因此排出的混合焦油可燃气至混合可燃气处理子系统9,所述混合可燃气处理子系统9用于将混合焦油可燃气与蒸汽充分混合后进行两级脱焦脱水处理,并将生成的液态焦油和混合可燃气进行处理后输送至热裂解炭化装置8进行燃烧供能,所述烘干设备4的臭气排放口与垃圾储存池2的臭气排放口均连接至臭气处理子系统10,所述臭气处理子系统10对臭气进行净化处理后达标排放。
25.热裂解炭化装置8的运行参数包括升温速度、内胆旋转速度、内胆壳体运行温度,所述运行参数根据生活垃圾的热裂解炭化、气化参数进行确定,生活垃圾的热裂解炭化、气化参数包括混合废塑料含量、杂质纤维量、含水率、质量密度。
26.所述混合焦油可燃气包括:升温至100℃排出的水蒸气,升温至200-350℃排出的焦油气,升温至400-550℃排出的石油制品混合气。
27.参见附图2,所述热裂解炭化装置8包括旋转固定在密闭的隔热壳83内的热裂解釜84,在所述隔热壳83的顶部开设有高温尾气排出口82,在所述热裂解釜84下方的隔热壳83内分别设置有燃烧机构85,所述热裂解釜84的进料端设置有螺旋输送机构86,所述螺旋输送机构86的中部开设所述热裂解混合可燃气排出口81,在所述螺旋输送机构86的进料口上连接有锁风进料机构88,所述热裂解釜84的出料端连接有水冷螺旋出料机构87。
28.进一步的,所述燃烧机构85包括相间设置的主燃烧组件851与辅助燃烧组件852,从而保证热裂解炭化装置8始终具有足够的能量进行垃圾的热裂解炭化,所述辅助燃烧组件852包括焦油燃烧结构852a与混合可燃气燃烧结构852b,所述焦油燃烧结构852a与混合可燃气燃烧结852b构的进料端均连接至所述混合可燃气处理子系统9。所述焦油燃烧结构852a用于燃烧混合可燃气处理子系统9 产生的液态焦油,所述混合可燃气燃烧结构852b用于燃烧混合可燃气处理子系统9输出的可燃气,从而实现对所述混合可燃气处理子系统9产生的焦油和混合可燃气的二次能源燃烧利用零排放,完整实现了生活垃圾的全部资源化利用、无害化处置、零排放生产。
29.从图2中还可以看出,所述热裂解釜84的内壁上均匀分布有若干拨料块810,拨料块810能够使得热裂解釜84的垃圾颗粒搅动翻转,使得垃圾颗粒均匀受热,确保热裂解炭化
的效果和效率;在所述热裂解釜84的内壁上还固定有沿着热裂解釜84的径向并排设置的若干导料块811,能够使得垃圾颗粒沿着输料方向移动,从而确保后续的垃圾颗粒顺利进入热裂解釜84内的同时已受热裂解炭化的垃圾颗粒顺利输送至水冷螺旋出料机构87,从而排出热裂解釜84。
30.从图1中可以看出,所述混合可燃气处理子系统9包括蒸汽发生装置91、蒸汽混合装置92、冷却装置93、脱焦脱水装置94,所述蒸汽发生装置91通过蒸汽管道与所述蒸汽混合装置92相连,所述蒸汽混合装置92用于利用蒸汽将混合可燃气进行充分混合和降温,所述蒸汽混合装置92的混合可燃气进口与所述热裂解炭化装置8的热裂解混合可燃气排出口81相连,所述蒸汽混合装置92 的出气口经所述冷却装置93输送至所述脱焦脱水装置94对冷却降温后的混合气体进行脱焦、脱水处理,所述脱焦脱水装置94形成的液态焦油输送至焦油超声波乳化装置95,所述焦油超声波乳化装置95将脱下的含焦油废水升温后按比例添加入脱水后的液态焦油中,利用液哨超声波技术形成油包水结构并输送至所述热裂解炭化装置8,所述脱焦脱水装置94形成的可燃气输送至可燃气稳压装置 96,所述可燃气稳压装置96将可燃气进行稳压处理后输送至所述热裂解炭化装置8。
31.所述蒸汽发生装置91用于根据混合焦油可燃气的参数测定的蒸汽添加量,向所述混合可燃气预混合系统内输入适量的蒸汽;所述蒸汽添加量依据水蒸气饱和度、混合焦油可燃气湿度、混合焦油可燃气粘度、混合焦油可燃气氢含量进行测定。所述蒸汽混合装置92利用蒸汽将各类废气充分混合、降温,形成混合可燃气;所述冷却装置93将混合可燃气进行两次冷却降温,将其中的气态焦油液化凝聚,然后对焦油进行升温,对液态焦油进行脱水处理,并将脱下的含焦油废水与脱水后的液态焦油输出至焦油超声乳化处理装置,焦油超声乳化处理装置将脱下的含焦油废水升温后按比例添加入脱水后的液态焦油中,利用液哨超声波技术形成油包水结构后输送至热裂解炭化装置8进行燃烧处理,同时,产生的混合可燃气经可燃气稳压装置96稳压后输送至热裂解炭化装置8进行燃烧处理。
32.本例中,所述蒸汽混合装置92与冷却装置93均采用不接触冷媒热交换式冷却器,所述蒸汽混合装置92具有220根dn38薄壁不锈钢换热管;由于是220 根大通道换热管,增加了横截换热面积,所以换热管道内气体流动速度减缓,有利于通道四周管壁外的冷却水进行充分热交换(事先用蒸汽对冷却水加温到 40-50℃左右),此时经蒸汽初降温的混合可燃气,在管道内进行快速冷却降温,附于管壁冷却后的焦油由于在80℃左右、且又有重力和向下风速双带动而向下流趟。所述蒸汽混合装置92由于是向下的负压,水雾凝结焦油雾在重量增大和运动加速度下,随惯性原理,80℃的恒温焦油呈液化状态流至保温盛油容器储存,随后由重油泵从保温盛油容器中抽出二次能源化利用;所述冷却装置93具有60 根dn38薄壁不锈钢换热管,通过换热器管壁再次对混合可燃气冷却降温,由于是再次冷疑,且通道横截面积减少,空气流动速度加快,二次疑结的焦油随速度使重量叠加和同样向下运动加速度惯性原理,呈液化状的80℃恒温焦油再次快速流至保温盛油容器中储存,随后由重油泵从罐体中抽出二次能源化利用。
33.所述冷却装置93设有雾化冷却区、管道换热冷却区、混合区,所述雾化冷却区用于对混合可燃气进行雾化冷却,所述管道换热冷却区采用预热到40-50℃的冷却水对混合可燃气进行冷却降温,所述混合区采用多点雾化热水喷淋技术对混合可燃气进行冷却降温。
34.从图1中还可以看出,所述臭气处理子系统10包括通过管道依次连接的循环冷却
器101、生物菌噬滤床除臭装置102以及uv光解与等离子组合除臭装置 103,所述循环冷却器101用于将所述垃圾储存池2与烘干设备4排出的臭气采用不接触冷媒热交换方式进行冷凝降温与脱水处理;所述生物菌噬滤床除臭装置 102用于将所述循环冷却器101处理后的无尘臭气经碱洗、脱尘、脱酸后送入自洁式循环生物菌噬滤床进行生物代谢除臭;所述uv光解与等离子组合除臭装置 103用于将所述生物菌噬滤床除臭装置102排出的臭气中遗漏的异味分子体进行快速氧化除臭后达标排放。
35.烘干脱水垃圾产生的臭气主要是水蒸气为主,夹杂着里面的h2s、co2、co、甲硫醇等等各类异味废气,采用不接触冷媒热交换方式进行冷凝降温与脱水处理,将臭气的温度降至35℃;
36.本例中,循环冷却器101的冷媒选用水为钙、镁离子稳定正负电荷水,换热媒介选用不锈钢加散热翅片,并以不锈钢耐压基数及取材厚薄决定热交换常数,从而以此依据换算冷凝换热总量、所需时间和需水量,进行热交换后将无尘臭气的温度降至60℃,恶臭蒸汽因降温冷凝产生极少量冷凝臭水,经电絮凝处理后送入污水循环净化系统处理后无害排放,或用于免烧制砖用水。
37.生物菌噬滤床除臭装置102将冷凝降温、脱水、且温度达到60℃控制点的无尘臭气,再次进行碱水洗涤净尘、脱酸,并将臭气更进一步降至35度,然后进入自洁式循环生物菌噬滤床,通过生物活性菌丝毛结构体层层过滤,并确保 h2s、co2、co、nh3等废臭气从入口至出口滞留36秒以上,这一段时间由菌噬体分秘胶原体,将通过其周边的有机碳链、氨氮的异味分子吸附,并通过各类菌种自身特殊消化酶,以臭气为碳源进行生命维持系统的循环代谢,从而完成对臭气的去除;
38.将脱水臭气冷凝至35℃左右的无尘臭气,再次进行水洗净尘、脱酸后进行生物菌噬除臭,基本反应式为:恶臭气体 o
2微生物
细胞代谢物 co2 h2o。然而由于恶臭气体成分不同,其分解产物不同,不同种类的微生物,分解代谢的产物也不一样。因此,无尘臭气必须滞留36秒以上,以保证菌噬体分秘的丝毛胶原体能够尽量吸附臭气分子。与此同时,长期循环利用的脱酸溶液ph在4-6之间时,该溶液经加碱中和、净化处理后循环利用。
39.在此过程中,臭气按照反应式-恶臭 o
2微生物
细胞代谢物 co2 h2o-进行反应,菌噬体分秘丝毛胶原体吸附之后,经其特殊酶以碳为基础生命代谢能源,箱内微生物菌群、虫群进行自我循环代谢,一段时间后虫群代谢物沉积超标探测仪报警时,自动控制营养液和自循环喷淋进行水洗,洗下含有虫群各种代谢物混合溶液,代谢物经菌群自我繁殖修复又循环使用。进入生物菌噬滤床处理器的臭气,经弱碱洗涤、脱尘、脱酸后,产生的废水经沉淀池沉淀后重复使用,该洗涤液不够时自动添加,沉淀池的污泥进入烘干器烘培脱水,后进入碳化系统处理,彻底无生产性固废产生。
40.在具体实施时,由于恶臭气体成分不同,其分解产物不同,不同种类的微生物,分解代谢的产物也不一样。对于不含氮的有机物质如苯酚、羧酸、甲醛等,其最终产物为二氧化碳和水;对于硫类恶臭成分,在好氧条件下被氧化分解为硫酸根离子和硫;对于像胺类这样的含氮恶臭物质经氨化作用放出nh3,nh3可被亚硝化细菌氧化为亚硝酸根离子,再进一步被硝化细菌氧化为硝酸根离子,最终生成h2o、co2。
41.能量代谢方式:
[0042][0043][0044][0045]
所述uv光解与等离子组合除臭装置103将自洁式循环生物菌噬滤床未捕捉到排出气中,遗漏的各类异味分子体,通过产生的臭氧,在负压风的推送下送入高能等离子除臭设备,高能等离子除臭设备每1cm3/s可以产生1000万个正离子和800万个负离子,通道中少量臭氧分子散布通道空中,与同等释放空中的大量正、负离子碰撞,使之产生二次激活,臭氧受激活产出更多离子氧在空气中,形成空间内大量正、负离子及活性氧离子场环境,使其对通过该空间的异味有机分子进行氧化分解,还对蛋白分子团体具有破壁氧化性,能充分解空气中的各种团或链式异味污染物,将其氧化为无害、无味co2、h2o、no分子,从而彻底实现消除空气中异味分子体的目的。
[0046]
tio2反应产生的臭氧,oh(羟基自由基)对恶臭气体(硫化氢、氨气、硫醇) 进行协同分解氧化反应,同时,恶臭气体分子链在紫外线作用下结构断全链,使其转化为“无臭味”的小分子化合物或矿化、生成水和co2;光解反应方式:
[0047]
有机废气
→
溦波 光解 o2→
o- o*(活性氧)o o2→
co2 h2o。
[0048]
本例中,所述异味分子体为臭气中未被破坏的各类单分子体、小孢子、单细胞等异味小分子体。
[0049]
本系统彻底放弃传统对高温废气采用的喷淋法技术,喷淋法优点在降温快、成本低,缺点在于废水量大、且臭气不减,并含焦油产生腐蚀性亚硫酸,废水处理费用高,缺点远大于优点。本实施例首创蒸汽脱焦油技术,蒸汽以精确比例与含焦油高温废气在管道内混合,采用特殊设计的高低二种流速的热交换器,快速降温且又衡温模式,充分防止焦油在降温过程中因粘稠度变化与颗粒物粘合结垢发生,恒温焦油呈液态流入专用搜集器。经过油水分离器后,解决了废气中焦油问题。实现生产中无大量添加性废水。净化后的可燃气经脱酸、脱白、稳压存储后,进入热裂解釜84加温燃烧系统二次循环使用。从而不仅实现了生活垃圾无氧热辐射炭化处理过程中焦油、可燃气的二次能源化利用,而且实现了高热混合废气分段净化且二次能源燃烧利用零排放,完整实现了生活垃圾的全部资源化利用、无害化处置、零排放生产,相较于传统技术,从根本上有效避免了管道自然冷却堵管、喷淋法产生大量废水,且其废水解决成本奇高以及直排降温中的结焦、堵塞和爆炸等诸多问题缺陷。同时臭气处理放弃了传统喷淋法脱酸、脱焦、脱尘产生大量废水、浪费资源的工艺技术和先进的干法脱酸、脱焦技术(混合钙焦油粉需炉燃烧、废布袋需处理),创新的采用了余热旋窑烘干脱水技术、生物滤床技术、uv光解 高能等离子氧化技术等一系列除臭技术进行组合臭气去除,实现了垃圾最终处理热裂解釜84排出高温臭气脱焦脱尘净化、余热利用、臭气再处理,并最终实现了排放出的气体达到国家标准,且实现了整个过程的固、液、气全零排放。
[0050]
以上对本实用新型所提供的技术方案进行了详细介绍。本文中应用了具体个例对本实用新型的原理及实施方式进行了阐述,以上实施例的说明只是用于帮助理解本实用新型的方法及其核心思想。应当指出,对于本技术领域的普通技术人员来说,在不脱离本实用新型原理的前提下,还可以对本实用新型进行若干改进和修饰,这些改进和修饰也落入本
实用新型权利要求的保护范围内。
再多了解一些
本文用于企业家、创业者技术爱好者查询,结果仅供参考。