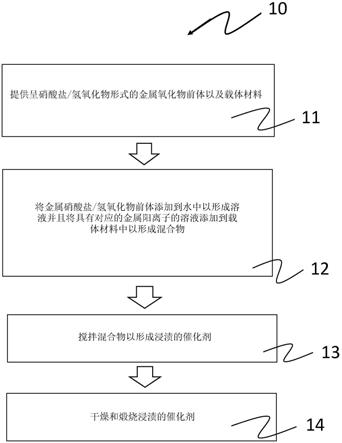
1.本发明涉及一种催化剂组合物。更具体地,本发明涉及一种用于一氧化碳生产的催化剂组合物和其制备方法。
背景技术:
2.二氧化碳可能是所有温室气体中最臭名昭著的气体。co2通过燃烧化石燃料(煤、天然气和油)、固体废物、树木以及木制品并且还由于某些化学反应而进入大气。二氧化碳对人体健康的危害相对较小,但是已证明二氧化碳会导致目前面临的如极端天气和全球变暖等其它方面(michael2017)。因此,需要更少的形成能的气体有助于其稳定性并且其在现有大气中的浓度。由于工业革命,通过能源驱动消耗化石燃料已经导致了co2排放的快速增长。这将通过破坏全球碳循环而导致行星变暖影响。co2排放对于地球大气中co2的浓度有着显著影响。在过去的2000年中,直至18世纪,已表明co2的浓度为百万分之270-285(ppm)(hannah和max 2018)。因此,为了稳定或者减少大气co2浓度,不仅要稳定排放还需要显著减少排放。
3.大气层中co2的浓度可以减少约40%,这通过将co2转化成可以用作用于生产合成燃料的工业原料的co(feng,2014)来进行。若干研究人员已经研究了这些co2分解催化剂。这些研究人员已经发现了能够当气体在存在电流的情况下从水中冒泡时进行第一阶段分解co2的许多催化剂。然而,比起分解co2,催化剂要分解更多的水,从而制备分子氢(h2)和能量更少的化合物(robert,2017)。二氧化碳到co的电化学还原通常描述为:co2 2h
2e-→
co h2o(aaron等人,2012)。然而,这些研究人员发现另外的研究需要集中于开发创新的复合和纳米结构的催化剂材料以克服催化活性不足、产物选择性和催化剂稳定性的挑战,co2的电解还原技术将在不久的将来更加实用(jinli等人,2014)。总之,此系统具有一些缺点和挑战如:co2电解还原的慢反应动力学,即使施加了电催化剂和高电极还原电势亦如此,由于溶剂在高还原电势下的寄生反应或分解反应而导致的此过程的低能量效率以及3)高能耗。
4.还有其它现有技术公开了用于一氧化碳生产的催化剂的参与,并且将提及us5830425、gb 2053947a、us 20070259976和us 20100160464a1。具体而言,us5830425公开了用盐溶液浸渍的铁催化剂,gb 2053947a公开了用若干种溶液浸渍的催化剂,us 20070259976公开了结晶硅酸铝中湿法浸渍的钌,us 20100160464a1公开了用钴盐浸渍沸石挤出物。虽然催化剂的存在设法减少了反应中涉及的能量,但最好找到能够显著降低能量并且同时维持所产生一氧化碳的质量和有效性使得可以高效节省大量能源、成本和时间的其它替代方案。此外,同样重要的是找到能够选择性地促进一氧化碳生产而不会使最终产物有毒或将在反应过程中堵塞的催化剂。
5.因此,仍然需要改进催化剂,以证明具有更好质量和有效性的更好的生产一氧化碳的方法。
技术实现要素:
6.本发明的一方面是提供一种用于生产一氧化碳的浸渍的催化剂组合物,所述浸渍的催化剂组合物包括:30wt%-50wt%的金属氧化物;以及50wt%-70wt%的载体材料。
7.因此,本发明的所述金属氧化物选自氧化钙、氧化镁和其组合、氧化铁和氧化镧。
8.因此,所述金属氧化物的来源选自煅烧白云石、煅烧碳酸盐、煅烧硝酸盐和煅烧氢氧化物。
9.因此,所述载体材料选自活性炭。
10.因此,所述浸渍的催化剂产生范围为33.0%-65.5%的一氧化碳。
11.因此,所述浸渍的催化剂的高性能稳定性在4小时到20小时的范围内。
12.本发明的另一方面是提供一种制备用于一氧化碳生产的浸渍的催化剂的方法,所述方法包括以下步骤:(i)提供前体和载体材料;(ii)将所述前体添加到水中以形成溶液并且将具有对应的金属阳离子的所述溶液添加到所述载体材料中以形成混合物;(iii)搅拌所述混合物以形成浸渍的催化剂;以及(iv)干燥和煅烧所述浸渍的催化剂。
13.因此,步骤(i)中的所述前体选自硝酸盐和氢氧化物。
14.因此,步骤(i)中的所述载体材料选自活性炭。
15.因此,步骤(iii)中的所述搅拌步骤在40℃-80℃下进行3-5小时。
16.因此,步骤(iv)中的所述干燥步骤在110℃-150℃的温度下进行过夜。
17.因此,步骤(iv)中的所述煅烧步骤在400℃-850℃的温度下进行。
18.因此,所述浸渍的催化剂以以下的比率制备:30wt%-50wt%的前体;以及50wt%-70wt%的载体材料。
19.因此,所述所产生的浸渍的催化剂产生范围为33.0%到65.5%的一氧化碳。
20.因此,所述所产生的浸渍的催化剂的高性能稳定性在4小时到20小时的范围内。
21.本发明的又另一方面是提供一种用于生产一氧化碳的方法,所述方法包括以下步骤:(i)将根据权利要求1到权利要求5所述的浸渍的催化剂装载到反应器中;(ii)在以所选流速流动的氮气下加热所述浸渍的催化剂,直至达到所选温度为止;(iii)使经加热的浸渍的催化剂与以所选流速流动的二氧化碳气体进行反应以产生一氧化碳;以及(iv)重新获得所述浸渍的催化剂以供重复使用;其中所述步骤在所述反应器内同时发生,由此在700℃-850℃的温度范围内选择性地收集所述一氧化碳。
22.因此,所述反应器选自流化床反应器或固定床反应器。
23.因此,氮气的所选流速和一氧化碳气体范围各自为50-100毫升/分钟和16%-99.9%。
24.因此,一种催化剂用于一氧化碳生产的用途,其中反应温度减少1倍。
25.因此,一种催化剂用于一氧化碳生产的用途,其中反应温度范围为700℃-850℃。
26.有利地,本发明的催化剂能够将反应温度降低1倍,其中反应温度范围为700℃-850℃。
27.有利地,本发明能够减少能源的使用,但维持其良好的生产质量。
28.有利地,本发明的选择性高,因此能够生产高纯度的一氧化碳。
附图说明
29.所呈现的实例仅用于说明本发明的优选实施例,并且不旨在以任何方式限制本发明的范围。
30.图1展示了制备用于一氧化碳生产的浸渍的催化剂的方法;
31.图2展示了一氧化碳生产的方法;
32.图3展示了通过x3催化剂的反应性能;
33.图4展示了通过用物理混合方法的x3的co2转化;
34.图5展示了在100毫升/分钟的co2气体流速下,以10g催化剂量在850℃的反应温度下的x3催化剂的性能;
35.图6展示了在50毫升/分钟的co2气体流速下,以10g催化剂量在850℃的反应温度下的x3催化剂的性能;
36.图7展示了在50毫升/分钟的co2气体流速下,以10g催化剂量在750℃的反应温度下的x3催化剂的性能;
37.图8展示了在850℃和50毫升/分钟下通过d3催化剂的co产率;
38.图9展示了在850℃和50毫升/分钟下通过d4催化剂的co产率;并且
39.图10展示了在850℃和50毫升/分钟下通过d5催化剂的co产率。
具体实施方式
40.本发明的一方面是提供一种用于生产一氧化碳的浸渍的催化剂组合物,所述浸渍的催化剂组合物包括:30wt%-50wt%的金属氧化物以及50wt%-70wt%的载体材料。
41.因此,金属氧化物选自氧化钙、氧化镁和其组合、氧化铁和氧化镧。
42.因此,金属氧化物的来源可能选自煅烧白云石、煅烧碳酸盐、煅烧硝酸盐和煅烧氢氧化物。为进一步解释,来自煅烧白云石的金属氧化物可以通过煅烧过程回收。具体而言,碳酸钙和碳酸镁的组合将形成已知为白云石的金属碳酸盐。然后金属碳酸盐在850℃下的煅烧过程之后形成金属氧化物。
43.因此,载体材料选自活性炭或如木炭、煤和石油焦等碳质材料。具体而言,活性炭起着载体材料的作用并且同时作为碳源用于co2到co的转化反应。
44.在本发明的一个实施例中,根据本发明的浸渍的催化剂设法产生范围为33.0%-65.5%的一氧化碳。具体而言,含有50%的白云石和活性炭的浸渍的催化剂产生57.2%的一氧化碳,含有40%的白云石和活性炭的浸渍的催化剂产生63.7%的一氧化碳,含有30%的白云石和活性炭的浸渍的催化剂产生62.2%的一氧化碳,含有30%的氧化钙和活性炭的浸渍的催化剂产生65.5%的一氧化碳和通过物理混合的53.0%的一氧化碳。对于含有氧化镧和活性炭的浸渍的催化剂产生52.0%的一氧化碳,含有氧化铁和活性炭的浸渍的催化剂产生58.0%的一氧化碳并且含有氧化镁和活性炭的浸渍的催化剂产生33.0%的一氧化碳。
45.因此,所述浸渍的催化剂的高性能稳定性在4小时到20小时的范围内。
46.本发明的另一方面涉及一种制备用于一氧化碳生产的浸渍的催化剂的方法(10)。图1详细地示出了制备用于一氧化碳生产的浸渍的催化剂的方法(10)。如参考图1,本发明的方法(10)包括提供前体和载体材料的步骤(11)。
47.前体选自氢氧化物或硝酸盐。载体材料选自活性炭或如木炭、煤和石油焦等碳质
材料。
48.浸渍的催化剂以以下的比率制备:30wt%-50wt%的前体以及50-70wt%的载体材料。
49.然后,此方法继续将前体添加到水中以形成溶液并且将具有对应的金属阳离子的所述溶液添加到载体材料中以形成混合物(12)。
50.之后,搅拌所述混合物以形成浸渍的催化剂(13),其中搅拌步骤在40℃-80℃下持续4-5小时。最终,在110℃-150℃温度下干燥所述浸渍的催化剂过夜并且在400℃-850℃温度下煅烧所述浸渍的催化剂(14)。
51.因此,所述所产生的浸渍的催化剂产生范围为33.0%到65.5%的一氧化碳。具体而言,含有50%的白云石和活性炭的浸渍的催化剂产生57.2%的一氧化碳,含有40%的白云石和活性炭的浸渍的催化剂产生63.7%的一氧化碳,含有30%的白云石和活性炭的浸渍的催化剂产生62.2%的一氧化碳,含有30%的氧化钙和活性炭的浸渍的催化剂产生65.5%的一氧化碳和通过物理混合的53.0%的一氧化碳。对于含有氧化镧和活性炭的浸渍的催化剂产生52.0%的一氧化碳,含有氧化铁和活性炭的浸渍的催化剂产生58.0%的一氧化碳并且含有氧化镁和活性炭的浸渍的催化剂产生33.0%的一氧化碳。
52.因此,所述所产生的浸渍的催化剂的高性能稳定性在4小时到20小时的范围内。
53.本发明的另一方面是提供一种用于一氧化碳生产的方法。图2详细地示出了用于一氧化碳生产的方法(20)。如参考图2,用于本发明的一氧化碳生产的方法(20)包括以下步骤:将浸渍的催化剂装载到反应器中(21)。所述反应器选自流化床反应器或固定床反应器。
54.此方法继续在以选自范围为50-100毫升/分钟的流速流动的氮气下加热所述浸渍的催化剂,直至达到范围为700-850℃的所选温度为止(22)。然后,使经加热的浸渍的催化剂与以范围为50-100毫升/分钟的所选流速流动的二氧化碳气体反应以产生一氧化碳(23)。最终,重新获得所述浸渍的催化剂以供重复使用;其中所述步骤在所述反应器内同时发生,由此在700℃-850℃的温度范围内选择性地收集所述一氧化碳(24)。
55.根据本发明的用于一氧化碳生产的催化剂,其中反应温度减少1倍。
56.根据本发明的用于一氧化碳生产的催化剂,其中反应温度范围为700℃-850℃。
57.将通过以下实例更详细地解释本发明。所呈现的实例仅用于说明本发明的优选实施例,并且不旨在以任何方式限制本发明的范围。
58.实例1
59.通常,本发明的催化剂是与木炭混合的所选金属以开发金属-木炭催化剂并且应用于将co2转化成co。此等式已知为波多反应(boudouardreaction),co2可以转化成co,其中固体碳(c)与co2反应。与电化学催化相比,此系统是用于co2还原、100%选择性百分比和更少的能耗的直接途径。开发本发明的目标是提供针对此过程合适且实用的新的催化剂配方,因为还没有发现更好的催化剂。所选金属催化剂是fe(过渡金属)、la(稀土金属)和mg(碱土金属)、ca(碱土金属),并且这些催化剂分别通过浸渍方法用活性炭合成。所制备的催化剂将使用若干技术特征化。所制备的催化剂的催化活性将使用流化床反应器和气相色谱法(gc)在co产率生产方面进行讨论。
60.方法
61.在这项研究中,使用硝酸盐前体使用湿法浸渍方法制备若干类型的催化剂。通过
使用流化床反应器完成co转化,其中第一步是将10g所制备的催化剂样品装载到2cm石英管中。以20℃/分钟的速率将样品加热直至实现850℃的最终温度,其中99.9%的氮气(n2)流动,然后接着是250毫升/分钟的流速的99.9%的二氧化碳以研究催化co2转化。以1小时间隔将所得气态产物收集并且通过气相色谱法进行分析。
62.结果和讨论
63.在这项工作中,基于活性炭的若干催化剂起着载体材料的作用并且同时作为碳来源以用于进行co2到co的转化反应。在活性炭上具有不同元素和活性金属含量的催化剂,如30%cao、30%白云石和50%白云石分别表示为x3、d3和d5。所有催化剂使用湿法浸渍方法合成以产生催化剂与载体之间的化学相互作用。然后将使用简单的物理混合制备的x3催化剂样品与其它催化剂进行比较以评估催化剂与载体相互作用对co产率和选择性的影响。金属氧化物与载体碳之间的相互作用的改善改变了催化剂的热力学特性并且成功改善了反应,在所述反应中获得了更多的co产率。在这项工作中已经研究了如催化剂类型、反应时间和co2流速等若干参数。co2到co的转化中所有催化剂的性能总结于表1。与其它系列催化剂相比,x3催化剂成功地产生了高达65.5%的最高co产率。选择了催化剂x3和d系列以用于另外的反应参数研究。在白云石中cao与cao/mgo的混合物之间没有显著的co产率差异。然而,40%dol-ac与30%dol-ac相比显示出微弱的co产率增长。
64.表1:co2转化成co的催化剂性能
[0065][0066]
从图3中,示出了co2转化成co的反应中x3催化剂的性能。还对h2气体的某些量进行了定量,其在850℃下时明显降低。反应还一直持续3小时直至在100ml co2流速下实现50%co产率。在图4中,示出了通过使用简单混合方法的物理混合x3催化剂的反应性能。明显可见物理混合x3催化剂与使用浸渍方法合成的其它催化剂相比给出显著更低的co产率。示出在反应4小时后co产率降低了1倍。碳载体材料与活性金属氧化物之间产生的化学相互作用有助于催化剂表面对co2的强吸附,从而在同一反应时间达到高co产率。用浸渍方法的x3催化剂在反应早期给出了高达65.5%的最高co产率并且持续高性能稳定性至多10小时或更长时间。
[0067]
另一个主要参数是co2作为原料的流速。在这项工作中,研究了50和100毫升/分钟的两个不同co2流速(参考图5和6)。co2的流速有助于不同的反应物停留时间和随后的作用
反应性能。在100毫升/分钟的co2流速下,以10g x3催化剂重量并在850℃的反应温度下成功获得了64%的最高co产率。在反应后仅3小时co产率减半。然而,在相同条件和催化剂类型下,50毫升/分钟的不同co2流速在反应9小时后显示出相当稳定的co产率。这可能是由于短停留时间,这可以促进反应物与催化剂之间的更好的相互作用并且随后增强co产率和co2转化。从产物流中没有分析到任何氧含量。
[0068]
反应温度起着重要作用,其中co产率已经随着反应温度上升而增加。在750℃下,记录了39%的最高co产率。在反应温度增高到至多850℃之后,所述产率增加到至多64%(参考图6和图7)。如表2所示甚至在700℃的更低温度下仍可以获得co产率。
[0069]
表2:反应温度对使用x3催化剂的co产率的作用
[0070][0071]
实例2
[0072]
白云石(d)基催化剂的性能:
[0073]
xrd图案示出了在反应期间引入到co2前后的催化剂相的变化。d3、d4和d5由cao和mgo的混合物组成,其在活性炭载体上的百分比分别为30%、40%和50%。在反应完成之后,所有d4和d5催化剂变成被称为caco3的其它结晶相并且mgo中的一些保留在系统中。富含co2的条件下cao高度活性并且对于co2高度吸引并且在低于850℃的温度下化学结合以形成caco3。然而,mgo相对于co2活性更低,其中在低温下具有低分子间引力。d系列催化剂d3、d4和d5中的不同含量cao示出了分别为62.2%、63.7%和57%的急剧变化的co产率(参考图8-10)。注意,通过将活性炭载体上的cao/mgo含量从30%增加到40%,没有显示出显著的改善。
[0074]
根据此结果,示出了与碳物理混合的cao或白云石相比高得多的性能。d3或x3与活性炭反应物之间的强介质相互作用明显影响着co产率并且随后控制催化剂在最佳碳和co2到2摩尔co的转化的稳定性。在图9中,示出了d4催化剂具有甚至在反应后21小时仍可以保持38%的co产率的良好稳定性。同时,d3催化剂可以在反应后17小时获得相同的co产率。其在稳定性和co产率方面还比x3催化剂更好,其中如图6所示x3在反应后9小时仅能保持38.8%产率。
再多了解一些
本文用于企业家、创业者技术爱好者查询,结果仅供参考。