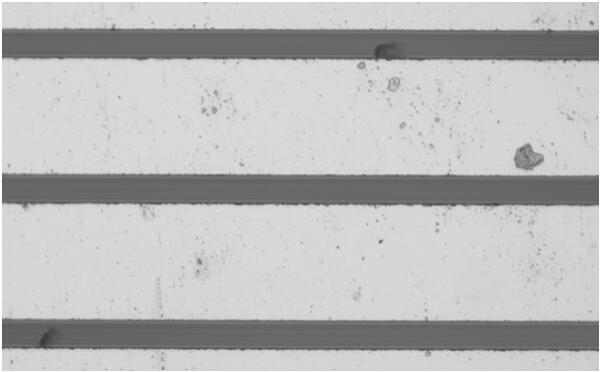
1.本发明属于切割工具技术,具体涉及一种硅片切割用金属烧结超薄切割刀及制备方法。
背景技术:
2.现有技术公开了一种超硬金刚石砂轮的制备方法,该工艺包括按照重量份称取原料、制备混合料a、制备混合料b;、制备坯体、制备砂轮基体、制备喷涂用的熔液、完成对砂轮基体表面镀膜处理等步骤,制备的金刚石砂轮具有硬度和强度高,韧性好,耐磨损,自锐性好等特点,适合大范围推广。现有技术公开了一种短切碳纤维增强树脂结合剂超硬磨料砂轮及其制备方法,基体采用短切碳纤维增强的铝粉基体压制而成,磨削层采用短切碳纤维增强的树脂结合剂与磨料压制而成;砂轮的树脂结合剂采用高温树脂和低温树脂混合的方式;超硬磨料采用镀覆金刚石和立方氮化硼混合的方式。本发明公布的超硬磨料砂轮,与常规砂轮相比,极限线速度较高,砂轮的转速得到提高,从而提高了生产效率。硅片作为太阳能以及电子信息的基础上材料,切割分小为其必要步骤,由于硅片比较脆且强度低并且上面有一层玻璃又要求刀片有一定的强度,因此常规切割刀切割效果还需改善;针对带玻璃硅片,市场上的切割刀为多孔电铸刀,未见金属基刀片的使用。
技术实现要素:
3.本发明公开了一种硅片切割用金属烧结超薄切割刀及制备方法,采用低浓度的锡结合铜配方,金刚石粒度在1200#-2000#之间,且部分金刚石采用碳化硅取代,同时添加碳纤维,这样既能保证玻璃的切割,同时又能保证下层硅片背崩满足客户要求,目前可以完美取代多孔电铸刀。
4.本发明采用如下技术方案:一种硅片切割用金属烧结超薄切割刀,其制备方法包括以下步骤,将物料过筛后冷压,得到冷压坯体;然后将冷压坯体烧结,得到切割刀粗品;最后将切割刀粗品进行常规加工,得到一种硅片切割用金属烧结超薄切割刀;所述物料包括金属胎体与金刚石。
5.本发明中,金属胎体包括铜粉、锡粉、碳化硅、碳纤维,优选的,金属胎体由铜粉、锡粉、碳化硅、碳纤维组成,进一步优选的,金属胎体中,铜粉的质量百分数为45~60%,锡粉的质量百分数为20~30%,碳化硅的质量百分数为5~15%,余量为碳纤维;最优选的,金属胎体中,铜粉的质量百分数为50~55%,锡粉的质量百分数为23~28%,碳化硅的质量百分数为8~12%,余量为碳纤维。金属胎体与金刚石中,金刚石的质量百分数为1.5~3%,优选为2~2.5%。
6.本发明中,将铜粉、锡粉混合,然后加入碳化硅混合,再加入碳纤维混合,然后加入金刚石,混合后过200~500目筛,取筛下物为物料;冷压为2~3吨/cm2压力保压3~7秒;烧结是,升温速率为40~55℃/min,最终烧结温度为450~500℃,保温10~20分钟,随炉冷却至室温。常规加工为现有技术,具体为内孔和外圆加工、双端面减薄加工,加工至图纸要求
尺寸精度。
7.由于硅片比较脆且强度低并且上面有一层玻璃又要求刀片有一定的强度,现有刀具很难兼顾两者的有效切割,导致成品率低,目前市场上大都采用多孔电铸刀,因为烧结砂轮综合性能很难符合切割需求,按照本发明方法制备的划片刀采用低浓度的锡结合铜配方,金刚石粒度在1200#-2000#之间,部分金刚石采用碳化硅取代,同时添加碳纤维,从而得到锋利性好的切割刀,这样既能保证玻璃的切割,同时又能保证下层硅片背崩满足客户要求,目前可以完美取代多孔电铸刀。
附图说明
8.图1为实施例一切割刀加工效果图;图2为现有切割刀加工效果图;图3为实施例四切割刀加工效果图;图4为对比例一切割刀加工效果图;图5为对比例二切割刀加工效果图。
具体实施方式
9.本发明的原料都为切割刀常规原料,其中铜粉粒径为3-5μm,锡粉粒径为3-5μm,碳化硅粒径为w1.5,碳纤维长度为150-300μm、直径为7μm,金刚石为1500#-1800#。具体指操作以及加工实验为现有技术。加工实验中,加工对象为玻璃和硅片贴合,其中玻璃厚度0.5
㎜
,硅层厚度0.5
㎜
;加工参数主轴转速rpm30000,进刀速度5mm/s,切入uv膜60μm。
10.实施例一一种硅片切割用金属烧结超薄切割刀,其金属基胎体组分和含量如下:铜粉
ꢀꢀꢀꢀꢀꢀ
55%锡粉
ꢀꢀꢀꢀꢀꢀ
25%碳化硅
ꢀꢀ
10%碳纤维
ꢀꢀꢀ
10%(1)物料混合:按照配方要求,将精确称重的铜粉、锡粉依次放入混料罐内混合1小时,再加入碳化硅混合1小时,然后加入碳纤维混合2小时,最后加入金刚石混合1小时,得到混合均匀的物料,金属胎体为1960g、金刚石40g;(2)压制成型:将步骤(1)中物料过300目筛网,取筛下物投料压制并施加压力3吨/cm2,保压5秒,从而制得冷压坯体;(3)烧结成型:将步骤(2)中冷压好的坯体连同模具一同放置入烧结炉内,升温速率50℃/min,室温升温至最终烧结温度500℃,保温10分钟,随炉冷却至室温取出,去毛刺后备用;(4)内孔和外圆加工:加烧结成型的坯体慢走丝线切割至图纸要求尺寸精度,然后用油石去除电加工毛刺;(5)双端面减薄加工:将内外圆加工后的坯体置于双端面减薄机内,减薄用砂轮盘加工至图纸要求尺寸精度,得到56
㎜
(o.d)x0.1
㎜
(t)x40
㎜
(i.d)的划片刀。加工实验发现,寿命为38片,加工效果见图1。
11.以现有生产上认为效果好的多孔电铸刀作为对照,寿命为32片,加工效果见图2,较实施例一稍差。
12.实施例二一种硅片切割用金属烧结超薄切割刀及制备,其金属基胎体组分和含量如下:铜粉50%锡粉23%碳化硅12%碳纤维15%(1)物料混合:按照配方要求,将精确称重的铜粉、锡粉依次放入混料罐内混合1小时,再加入碳化硅混合1小时,然后加入碳纤维混合2小时,最后加入金刚石混合1小时,得到混合均匀的物料;金属胎体为1950g、金刚石50g;(2)压制成型:将步骤(1)中物料过300目筛网,取筛下物投料压制并施加压力2吨/cm2,保压5秒,从而制得冷压坯体;(3)烧结成型:将步骤(2)中冷压好的坯体连同模具一同放置入烧结炉内,升温速率45℃/min,升温至最终烧结温度450℃,保温20分钟,随炉冷却至室温取出,去毛刺后备用;(4)内孔和外圆加工:加烧结成型的坯体慢走丝线切割至图纸要求尺寸精度,然后用油石去除电加工毛刺;(5)双端面减薄加工:将内外圆加工后的坯体置于双端面减薄机内,减薄用砂轮盘加工至图纸要求尺寸精度,得到56
㎜
(o.d)x0.1
㎜
(t)x40
㎜
(i.d)的划片刀。
13.实施例三一种硅片切割用金属烧结超薄切割刀及制备,其金属基胎体组分和含量如下:铜粉45%锡粉30%碳化硅15%碳纤维10%(1)物料混合:按照配方要求,将精确称重的铜粉、锡粉依次放入混料罐内混合1小时,再加入碳化硅混合1小时,然后加入碳纤维混合2小时,最后加入金刚石混合1小时,得到混合均匀的物料,金属胎体为1960g、金刚石40g;(2)压制成型:将步骤(1)中物料过300目筛网,取筛下物投料压制并施加压力3吨/cm2,保压5秒,从而制得冷压坯体;(3)烧结成型:将步骤(2)中冷压好的坯体连同模具一同放置入烧结炉内,升温速率50℃/min,室温升温至最终烧结温度500℃,保温10分钟,随炉冷却至室温取出,去毛刺后备用;(4)内孔和外圆加工:加烧结成型的坯体慢走丝线切割至图纸要求尺寸精度,然后用油石去除电加工毛刺;(5)双端面减薄加工:将内外圆加工后的坯体置于双端面减薄机内,减薄用砂轮盘加工至图纸要求尺寸精度,得到56
㎜
(o.d)x0.1
㎜
(t)x40
㎜
(i.d)的划片刀。加工实验发现,寿命为31片。
14.实施例四一种硅片切割用金属烧结超薄切割刀及制备,其金属基胎体组分和含量如下:铜粉
ꢀꢀꢀꢀ
60%锡粉
ꢀꢀꢀꢀ
20%碳化硅
ꢀꢀ
10%碳纤维
ꢀꢀ
10%(1)物料混合:按照配方要求,将精确称重的铜粉、锡粉依次放入混料罐内混合1小时,再加入碳化硅混合1小时,然后加入碳纤维混合2小时,最后加入金刚石混合1小时,得到混合均匀的物料,金属胎体为1960g、金刚石40g;(2)压制成型:将步骤(1)中物料过300目筛网,取筛下物投料压制并施加压力3吨/cm2,保压5秒,从而制得冷压坯体;(3)烧结成型:将步骤(2)中冷压好的坯体连同模具一同放置入烧结炉内,升温速率50℃/min,室温升温至最终烧结温度500℃,保温10分钟,随炉冷却至室温取出,去毛刺后备用;(4)内孔和外圆加工:加烧结成型的坯体慢走丝线切割至图纸要求尺寸精度,然后用油石去除电加工毛刺;(5)双端面减薄加工:将内外圆加工后的坯体置于双端面减薄机内,减薄用砂轮盘加工至图纸要求尺寸精度,得到56
㎜
(o.d)x0.1
㎜
(t)x40
㎜
(i.d)的划片刀。加工实验发现,寿命为41片,加工效果见图3,偏差。
15.实施例五一种硅片切割用金属烧结超薄切割刀及制备,其金属基胎体组分和含量如下:铜粉
ꢀꢀꢀꢀ
45%锡粉
ꢀꢀꢀꢀ
35%碳化硅
ꢀꢀ
10%碳纤维
ꢀꢀ
10%(1)物料混合:按照配方要求,将精确称重的铜粉、锡粉依次放入混料罐内混合1小时,再加入碳化硅混合1小时,然后加入碳纤维混合2小时,最后加入金刚石混合1小时,得到混合均匀的物料,金属胎体为1960g、金刚石40g;(2)压制成型:将步骤(1)中物料过300目筛网,取筛下物投料压制并施加压力3吨/cm2,保压5秒,从而制得冷压坯体;(3)烧结成型:将步骤(2)中冷压好的坯体连同模具一同放置入烧结炉内,升温速率50℃/min,室温升温至最终烧结温度500℃,保温10分钟,随炉冷却至室温取出,去毛刺后备用;(4)内孔和外圆加工:加烧结成型的坯体慢走丝线切割至图纸要求尺寸精度,然后用油石去除电加工毛刺;(5)双端面减薄加工:将内外圆加工后的坯体置于双端面减薄机内,减薄用砂轮盘加工至图纸要求尺寸精度,得到56
㎜
(o.d)x0.1
㎜
(t)x40
㎜
(i.d)的划片刀。
16.对比例一一种硅片切割用金属烧结超薄切割刀及制备,其金属基胎体组分和含量如下:
铜粉
ꢀꢀꢀꢀ
55%镍粉
ꢀꢀꢀꢀ
25%碳化硅
ꢀꢀ
10%碳纤维
ꢀꢀ
10%(1)物料混合:按照配方要求,将精确称重的铜粉、镍粉依次放入混料罐内混合1小时,再加入碳化硅混合1小时,然后加入碳纤维混合2小时,最后加入金刚石混合1小时,得到混合均匀的物料,金属胎体为1960g、金刚石40g;(2)压制成型:将步骤(1)中物料过300目筛网,取筛下物投料压制并施加压力3吨/cm2,保压5秒,从而制得冷压坯体;(3)烧结成型:将步骤(2)中冷压好的坯体连同模具一同放置入烧结炉内,升温速率50℃/min,室温升温至最终烧结温度500℃,保温10分钟,随炉冷却至室温取出,去毛刺后备用;(4)内孔和外圆加工:加烧结成型的坯体慢走丝线切割至图纸要求尺寸精度,然后用油石去除电加工毛刺;(5)双端面减薄加工:将内外圆加工后的坯体置于双端面减薄机内,减薄用砂轮盘加工至图纸要求尺寸精度,得到56
㎜
(o.d)x0.1
㎜
(t)x40
㎜
(i.d)的划片刀。加工实验发现,寿命为29片,加工效果见图4。
17.对比例二一种硅片切割用金属烧结超薄切割刀及制备,其金属基胎体组分和含量如下:铜粉
ꢀꢀꢀꢀ
55%锡粉
ꢀꢀꢀꢀ
25%氧化铝
ꢀꢀ
10%碳纤维
ꢀꢀ
10%(1)物料混合:按照配方要求,将精确称重的铜粉、锡粉依次放入混料罐内混合1小时,再加入氧化铝混合1小时,然后加入碳纤维混合2小时,最后加入金刚石混合1小时,得到混合均匀的物料,金属胎体为1960g、金刚石40g;(2)压制成型:将步骤(1)中物料过300目筛网,取筛下物投料压制并施加压力3吨/cm2,保压5秒,从而制得冷压坯体;(3)烧结成型:将步骤(2)中冷压好的坯体连同模具一同放置入烧结炉内,升温速率50℃/min,室温升温至最终烧结温度500℃,保温10分钟,随炉冷却至室温取出,去毛刺后备用;(4)内孔和外圆加工:加烧结成型的坯体慢走丝线切割至图纸要求尺寸精度,然后用油石去除电加工毛刺;(5)双端面减薄加工:将内外圆加工后的坯体置于双端面减薄机内,减薄用砂轮盘加工至图纸要求尺寸精度,得到56
㎜
(o.d)x0.1
㎜
(t)x40
㎜
(i.d)的划片刀。加工实验发现,寿命为33片,加工效果见5,较差。
18.对比例三一种硅片切割用金属烧结超薄切割刀及制备,其金属基胎体组分和含量如下:铜锡合金粉(30%锡)
ꢀꢀ
80%
碳化硅
ꢀꢀ
10%碳纤维
ꢀꢀ
10%(1)物料混合:按照配方要求,将精确称重的铜锡合金粉放入混料罐内混合1小时,再加入碳化硅混合1小时,然后加入碳纤维混合2小时,最后加入金刚石混合1小时,得到混合均匀的物料,金属胎体为1960g、金刚石40g;(2)压制成型:将步骤(1)中物料过300目筛网,取筛下物投料压制并施加压力3吨/cm2,保压5秒,从而制得冷压坯体;(3)烧结成型:将步骤(2)中冷压好的坯体连同模具一同放置入烧结炉内,升温速率50℃/min,室温升温至最终烧结温度500℃,保温10分钟,随炉冷却至室温取出,去毛刺后备用;(4)内孔和外圆加工:加烧结成型的坯体慢走丝线切割至图纸要求尺寸精度,然后用油石去除电加工毛刺;(5)双端面减薄加工:将内外圆加工后的坯体置于双端面减薄机内,减薄用砂轮盘加工至图纸要求尺寸精度,得到56
㎜
(o.d)x0.1
㎜
(t)x40
㎜
(i.d)的划片刀。加工实验发现,寿命为26片。
19.对比例四一种硅片切割用金属烧结超薄切割刀及制备,其金属基胎体组分和含量如下:铜粉
ꢀꢀꢀꢀ
55%锡粉
ꢀꢀꢀꢀ
20%银粉
ꢀꢀꢀꢀ
5%碳化硅
ꢀꢀ
10%碳纤维
ꢀꢀ
10%(1)物料混合:按照配方要求,将精确称重的铜粉、锡粉、银粉依次放入混料罐内混合1小时,再加入碳化硅混合1小时,然后加入碳纤维混合2小时,最后加入金刚石混合1小时,得到混合均匀的物料,金属胎体为1960g、金刚石40g;(2)压制成型:将步骤(1)中物料过300目筛网,取筛下物投料压制并施加压力3吨/cm2,保压5秒,从而制得冷压坯体;(3)烧结成型:将步骤(2)中冷压好的坯体连同模具一同放置入烧结炉内,升温速率50℃/min,室温升温至最终烧结温度500℃,保温10分钟,随炉冷却至室温取出,去毛刺后备用;(4)内孔和外圆加工:加烧结成型的坯体慢走丝线切割至图纸要求尺寸精度,然后用油石去除电加工毛刺;(5)双端面减薄加工:将内外圆加工后的坯体置于双端面减薄机内,减薄用砂轮盘加工至图纸要求尺寸精度,得到56
㎜
(o.d)x0.1
㎜
(t)x40
㎜
(i.d)的划片刀。加工实验发现,寿命为36片。
再多了解一些
本文用于企业家、创业者技术爱好者查询,结果仅供参考。