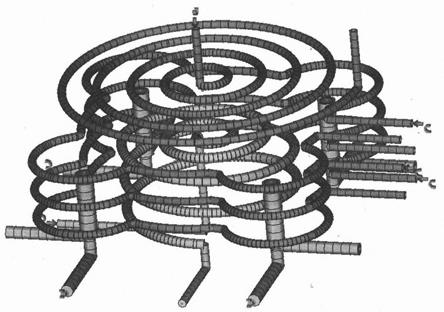
1.本发明涉及注塑模设计领域,具体地说是注塑模组合式冷却系统设计,该冷却系统为多维度贴合塑件内外表面分层次设置的冷却机构。
背景技术:
2.在塑料的注射成型中,模具的温度直接影响着塑件的质量,随着人们对生活中使用塑料产品的外观、尺寸精度和使用性能要求越来越高,这使得模具的温度控制需要更加严格;在普通的冷却水道不能达到设定温度范围的控制精度时,可以将冷却管道设计成多形式的组合冷却系统;冷却系统的冷却效果受很多因素影响,越来越多的企业选择使用模流分析技术来预测冷却精度信息,这些信息用实验的方法测定较困难的,获得冷却分析结果可以进一步优化冷却设计方案,减少模具研发成本和试模次数,提高生产效率和产品的质量。
3.现有一盒体塑件如图2所示,其结构较为复杂,主体结构为大圆柱壳体,厚度为3mm,在大圆柱壳体圆周侧壁均布有4个小圆柱壳体,厚度为3mm,塑件要求较高装配精度,外观要求不能有溢边、气孔和银纹等缺陷。
4.目前传统的制造工艺对冷却管道的加工采用直钻式通孔或盲孔的形式,直线形式的孔与圆柱表面的距离不能实现同步,难以等距离均匀地覆盖在制品表面进行冷却,容易导致热量局部堆积,使制品得不到有效冷却,从而影响塑件质量和生产效率;对于曲面类产品的冷却,采用随形冷却管道并用低熔点合金浇注固定的冷却装置具有十分明显的优势,其冷却效果的主要相关影响因素包括工艺参数和设计参数,运用moldflow软件实现塑料熔体在模具内冷却过程的模拟仿真,可以在冷却管道设计完成后预测工艺参数和设计参数的合理性,使设计方案尽快实施生产。
技术实现要素:
5.本发明所要解决的技术问题是:针对现有技术的不足,提供一种注塑模组合式冷却系统,提高了塑件的成型质量和生产效率。
6.根据第一方面,本发明涉及用于塑件注射成型的模具设计中冷却系统的结构,含定模冷却装置和动模冷却装置,为组合式冷却系统;所述组合式冷却系统为多维度贴合塑件内外表面分层次设置的冷却机构,在盒体实施方案中,包括至少一组螺旋状连接涡旋状混合冷却管道、一组多段圆弧连接多段直线混合冷却管道、一组喷流管冷却管道、一组涡旋状冷却管道或圆弧冷却管道。
7.根据第二方面,本发明涉及用于塑件注射成型的模具设计中冷却系统的结构,所述冷却管道的尺寸设计是基于moldflow软件平台的冷却分析,模拟冷却过程的流动行为和传热行为,对该冷却分析的结果解析并结合经验获得其对产品成型冷却效果,以判断其对产品成型影响因素,实现合理的冷却系统设计。
8.根据第三方面,本发明涉及第一方面或第二方面所述多维度贴合塑件设置的冷却
机构在模具设计中的应用。
9.根据第四方面,本发明涉及包含第一方面或第二方面所述的螺旋状冷却管道、平面涡旋状冷却管道、圆弧冷却管道、直线冷却管道、喷流管冷却管道。
10.根据第五方面,本发明涉及由第四方面所述的冷却管道串联组成及连通方式。
11.根据第六方面,本发明涉及第五方面所述的冷却管道组合成的冷却系统在模具设计中的应用。
12.根据第七方面,本发明涉及第一方面或第二方面所述基于moldflow软件平台的冷却分析在模具设计中的应用。
13.根据第八方面,本发明涉及第七方面所述在moldflow平台上运用添加方式创建组合式冷却管道,进行冷却分析时各工艺参数设置方法以及对模流结果的解析和运用。
14.本发明比现有技术具有以下优点:(1)本发明的注塑模组合式冷却系统中冷却管道路径是沿着型腔表面以等高线的形式布局,能实现均匀、精准且快速地调控模具温度,大幅提升企业的注塑生产能力和塑件质量,具有广泛的应用前景和实际意义;(2)通过构建注塑模流分析模型,应用mpi软件进行塑件cae分析,获得充填、流动和冷却的可视化结果,运用评判机制进行解析和优化,建立完整的注塑模冷却系统设计流程,为实际生产提供参考和借鉴。
附图说明
15.图1是实施例注塑模组合式冷却系统。
16.图2是塑件结构示意图。
17.图3a是冷却系统分解之一结构示意图。
18.图3b是冷却系统分解之二结构示意图。
19.图3c是冷却系统分解之三结构示意图。
20.图3d是冷却系统分解之四结构示意图。
21.图4是填充分析中最佳注射时间图。
22.图5冷却分析中网格单元温度分布曲线。
具体实施方式
23.下面将结合本发明实施例中的附图,对本发明实施例中的技术方案进行清楚、完整地描述,但并不因此将本发明限制在所述的实施例范围之中。
24.本发明提供了一种注塑模组合式冷却系统,含模具的定模冷却装置和动模冷却装置,该冷却系统为多维度贴合塑件内外表面分层次设置的冷却机构,定膜和动模实现同时均衡冷却,紊流状态的冷却介质的流动能及时有效将充满模腔的熔融物料的温度降低到顶出温度,维持成型周期内的热平衡,每一条冷却回路固定安装有带密封圈的进水接头和带密封圈的出水接头。
25.本发明注塑模组合式冷却系统的尺寸设计是基于moldflow软件平台的冷却分析,模拟冷却过程的流动行为和传热行为,对该冷却分析的结果解析并结合经验获得其对产品成型冷却效果,以判断其对产品成型影响因素,实现合理的冷却系统设计。
26.本发明注塑模组合式冷却系统中冷却介质可以是冷却水和压缩空气,水作为介质的温度可以是环境温度,也可以高于或低于环境温度,模具与冷却介质的温度差δθ=10℃~30℃,合理的温差才能保障制品尺寸精度和内部的应力稳定性,获得高质量塑件。
27.本发明注塑模组合式冷却系统中冷却管道截面形状可以是圆形,在某些实施方式中冷却管道截面形状可以是梯形或u形或半圆形或矩形或其它形状,截面尺寸用当量直径来换算,管道长度<1500mm,在管道中冷却介质的流动为湍流状态,雷诺数re>6000,通常设置为104。
28.本发明注塑模组合式冷却系统包括螺旋状冷却管道、平面涡旋状冷却管道、圆弧冷却管道、喷流管冷却管道,所述管道依据塑件内外表面形状等距环绕设置,管道中心轴线与塑件表面的距离均为管道直径的2倍;注塑模组合式冷却系统还包括直线型进出介质管道,所述管道连接时均采取串联方式组合,连接的各管道从冷却介质供应歧管到冷却介质收集歧管之间为单一流路,连接的各管道具有相同的管径,管道中出口和入口冷却介质的温差在3℃以内。
29.实施例1
30.如图1-3所示,塑件外表面由配置在定模的型腔成型,外表面中圆形端面配置平面涡旋状冷却管道,管道的两端串联着进出介质管道,进出管道垂直于端面贯穿模板,另一端与穿过相邻模板上的介质进出横孔连接,连接处采用密封圈密封并保证不泄露,冷却介质从浇口附近端横孔进入,从远离浇口另一端横孔流出。
31.塑件外表面中侧面配置贴合外周形状的多条组合式冷却管道,每条管道轴线位于参考平面内,参考平面与外周侧面垂直,每条管道包括多段大直径圆弧管道、多段小直径圆弧管道和进出介质管道,所有管道均串联相接,各圆弧管道间采用圆弧相切连接,每段圆弧管路与塑件表面均保持等距,组合式冷却管道的配置数量依据塑件侧面的高度来计算,多条串联组合式冷却管道间的排列形式为平行布局,每组间管道轴线间距为管道直径的4倍。
32.涡旋状冷却管道、圆弧管道和进出介质管道均由铜管成型后用低熔点合金浇注固定嵌入模板内部,模板上冷却介质进出横孔采用普通机加工直接成型。
33.实施例2
34.塑件壳体内表面由配置在动模的型芯成型,大直径圆柱壳体内表面配置螺旋状管道连接平面涡旋状管道组合成串联冷却管路,螺旋状管道与涡旋状管道旋向相同,管道连接形式采用圆弧相切连接,螺旋状管道的中心轴与涡旋状管道所在平面处于互相垂直位置,涡旋状冷却管道对塑件内表面圆形平面部分实施冷却,螺旋状冷却管道对塑件内表面圆周部分实施冷却,涡旋状管道一端连接介质进入管道,介质进入管道与涡旋状管道所在平面垂直,进口管道与涡旋状管道平面垂直,螺旋状管道一端连接介质流出管道,出口管道与进口管道平行,均与穿过相邻模板上的介质进出横孔连接,连接处采用密封圈密封并保证不泄露。
35.螺旋状冷却管道、涡旋状冷却管道、进出介质管道均由铜管成型后用低熔点合金浇注固定嵌入模板内部,模板上冷却介质进出横孔采用普通机加工直接成型。
36.实施例3
37.塑件壳体内表面中小直径圆柱壳体内表面配置喷流管冷却管道,对塑件内表面圆形平面部分和圆周部分实施冷却,冷却介质从喷流管顶端喷出,向四周分流冷却型芯壁,喷
流管内小口径的内管直径与外管直径比值为0.707,内管与外管具有相同的流动助力,喷流管采用螺纹旋入型芯中,介质进出口与相邻模板上冷却介质进出横孔相连接,喷管件采用铜管,在与穿过模板上的介质进出横孔的连接时采用密封圈密封并保证连接处不泄露。
38.实施例4
39.实施例1-3所述注塑模组合式冷却系统尺寸的设计是基于moldflow软件平台模拟冷却过程的流动行为和传热行为,对该冷却分析的结果解析获得,包括以下步骤:(1)在moldflow平台新建分析项目,运用solidworks创建塑件3d模型并保存为.stl格式,对导入项目的模型进行双层面网格划分,整个模型网格密度取厚度的1/3~1/2,根据网格统计结果进行网格缺陷诊断和修复,使网格质量优化达到moldflow分析标准后,具体为:自由边为0、多重边为0、无单元交叉、连通区域为1、最大纵横比为8、单元匹配率高于85%,保存网格方案;(2)打开网格方案进行浇口位置分析,设置材料类型如sp-6/chi mei corportion,注射机和工艺参数设置为默认,以分析计算获得最佳浇口位置为实际浇口位置设计直浇口浇注系统;(3)运用moldflow平台建模工具创建浇注系统,进行成型窗口分析,分析结果“质量(成型窗口):xy图”确定最佳注射时间;继续进行填充和保压分析,成型工艺设置中充填控制选择注射时间,并输入最佳注射时间为总注射时间,其他参数采用默认,参照结果设定保压模式;(4)moldflow平台冷却系统的创建方式有2种:运用建模工具直接创建和运用3d软件建模添加后间接创建,moldflow的建模工具可以创建节点、直线、圆弧线、样条曲线、柱体单元等,本实施例中喷流管、圆弧和进出口直线管可以运用建模工具直接创建进行网格划分,涡旋状和螺旋状管道运用建模工具无法直接准确创建,须运用3d建模软件间接创建,在方案中才添加冷却系统3d模型并进行网格划分,运行冷却分析;(5)导出每个阶段的分析结果进行评判解析,制作分析报告。
40.实施例5
41.实施例4所述组合式冷却管道的模流分析模型创建方法,具体步骤为:(1)启动solidworks,先绘制圆形草图,再运用曲线工具栏中螺旋线/涡状线工具创建平面涡旋状管道,定义方式为涡状线创建涡状线,然后在贯穿端点的垂直平面内按管道直径绘制圆形,运用扫描工具使涡状线成为涡旋体,完成后另存为stl文件;(2)打开moldflow平台的塑件项目,调用添加工具将绘制的管道零件涡旋体加入到项目中,调用创建菜单的节点工具找出管道零件和塑件的各自中心点坐标,运用实用程序下属的移动工具将管道零件和塑件的中心坐标调节到一致,调用柱体单元工具将3d实体管道转化为柱体,并在选择选项中设置属性为管道,截面形状是圆形,直径为10mm,管道热传导系数为1,管道粗糙度为0.05mm,“模具属性”中模具材料选择为铜,将涡旋体转化为涡旋状冷却水道后,进行网格划分并对图层进行归集和删除整理。
42.实施例6
43.实施例4所述组合式冷却管道的模流分析模型创建方法,具体步骤为:(1)启动pro/e,调用螺旋扫描中伸出项指令,在属性菜单选择常数-穿过轴-右手定则-完成,继续在草图平面中选择正向-缺省,须将长度10mm直线约束与圆柱轮廓边重合,
输入节距值,调用伸出项-螺旋扫描,创建螺旋体,并另存为iges文件;(2)打开moldflow平台的塑件项目,调用添加工具将绘制的管道零件螺旋体加入到项目中,调用创建菜单的节点工具找出管道零件和塑件的各自中心点坐标,运用实用程序下属的移动工具将管道零件和塑件的中心坐标调节到一致,调用柱体单元工具将3d实体管道转化为柱体,并在选择选项中设置属性为管道,截面形状是圆形,直径为10mm,管道热传导系数为1,管道粗糙度为0.05mm,模具属性中模具材料选择为铜,将螺旋体转化为螺旋状冷却水道后,进行网格划分并对图层进行归集和删除整理。
44.实施例7
45.实施例4所述组合式冷却管道的模流分析工艺条件设置包括以下几个参数:(1)熔体温度:根据选定的材料的性能参数设定,材料为sp-6/chi mei corportion,推荐熔体温度为230℃;材料为ppu 1752 s1/targor,推荐熔体温度为230℃;材料为calibre im 401-11/styron na-la,推荐熔体温度为300℃,材料为abs hf380/lg chemical,推荐熔体温度为235℃,依此设置;(2)开模时间:包括模具打开、塑件顶出以及和合模几个步骤共用的时间,可采用默认值或自行设定如6s、8s、9s、10s、11s、20s
……
;(3)注射 保压 冷却时间:此为冷却分析重要参数,有两种选项,指定选项是指根据经验和冷却系统简单计算公式预设一个数值,自动选项中需要编辑顶出条件,包括模具表面温度、顶出温度和顶出温度下的最小零件冻结百分比,材料为sp-6/chi mei corportion,推荐模温为50℃,顶出温度为88℃,材料为ppu 1752 s1/targor,推荐模温为50℃,顶出温度为93℃,材料为calibe im 401-11/styron na-la,推荐模温为100℃,顶出温度为127℃,材料为abs hf380/lg chemical,推荐模温为60℃,顶出温度为89℃,依此设置;同时制品冻结到80%,流道系统冻结到60%时塑件就可以顶出了,顶出温度下的最小零件冻结百分比设置默认100%;(4)冷却求解器参数:包括模具温度收敛公差和最大模温迭代次数,模具温度收敛公差数值范围为0.00001∶0.5,理论上缩小收敛公差可提高精准度,但会增加求解时间和导致出现收敛问题,通常设置0.1即可,最大模温迭代次数范围为10∶10000,默认值为50,当存在太多集成警告(即,单元距离太近)时,边界单元求解器无法收敛于当前输入条件所确定的解,分析日志会提示“**警告**700990收敛之前已达到解决方案迭代限制”,此警告信息出现3次之后,分析即会终止,因此需要更新网络参数才能得到收敛解;(5)高级选项:包括成型材料、工艺控制器、模具材料和求解器参数,依据浇口位置分析和成型窗口分析和填充分析结果设置。
46.实施例8
47.实施例4所述组合式冷却管道的模流分析结果包括:回路冷却介质温度、回路流动速率、回路雷诺数、回路管壁温度、冷流道表面温度、零件到达顶出温度的时间、零件最高温度、零件平均温度、零件最高温度位置、零件冻结百分比、零件温度曲线、模具温度,冷却分析结果与以下条件进行比对:(1)塑件平均温度与设置模具温度差值默认为1℃,此为使零件完全冷却或达到顶出温度时间,在分析结果后可允许调整;(2)使用“塑件温度曲线”的二维xy图查看模型中网格单元的温度曲线,确定塑件
上下表面的温度之间差值最大不超过10℃;(3)塑件厚度截面的温度差须根据局部硬度以及冷冻层百分比解析,采用塑件材料硬度指标和产品顶出的质量要求来确定塑件上下表面壁厚的冷却百分比最小值;(4)塑件温度曲线:与充填分析的冷却层因子联合一起评估;(5)回路流动速率和回路雷诺数与冷却介质供应泵有关,冷却介质的循环压力须小于供应泵的额定压力,否则须调整管道长度或直径或结构或供应泵;(6)塑件温度分布结果中各节点温度差值大小表征零件成型时温度分布的均匀程度,判断冷却系统布局的合理性和冷却效果优劣;(7)在保证质量的同时,冷却时间或成型周期ipo时间越短越好。
48.通过上述冷却计算结果解析,判定冷却系统方案优于传统的水道方案,解决了局部冷却不均匀和容易发生翘曲等缺陷的问题,达到了更好的冷却效果。
49.以上显示和描述了本发明的基本原理、主要特点,所述的实施例是本发明的优选实施方式,应当指出的是,对于本技术领域的普通技术人员来说,在不脱离本发明原理的前提下,在没有作出创造性劳动前提下所获得的所有其他实施例,都属于本发明保护的范围。
再多了解一些
本文用于企业家、创业者技术爱好者查询,结果仅供参考。