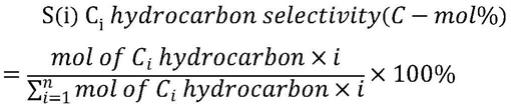
1.本技术涉及一种催化剂的成型方法及其应用,属于催化剂制备领域。
背景技术:
2.二氧化碳等温室气体导致全球变暖、海洋酸化等一系列重大环境问题。在自然界中,绿色植物可从空气中吸收二氧化碳,经光合作用转化为有机物和氧气,但该过程缓慢,所以一直以来科学家们努力想通过化学转化的方式回收利用二氧化碳。二氧化碳虽然是主要的温室气体,但同时也是一种自然界大量存在的“碳资源”,若能借助可再生能源获取电能分解水制得的氢气,将二氧化碳转化为化学品或燃料,不仅能实现温室气体的减排,而且有助于解决对化石燃料的过度依赖以及可再生能源的存储问题。然而,二氧化碳的活化与选择性转化仍面临巨大挑战。相比于更活泼的孪生兄弟一氧化碳,二氧化碳分子非常稳定,难以活化,与经典的费托合成路线相比,二氧化碳与氢分子的催化反应更易生成甲烷、甲醇、甲酸等小分子化合物,而很难生成长链的液态烃燃料。
3.近年来,铁基催化剂被发现可通过辅以合适的助剂或第二组分高效催化二氧化碳和氢气生成c2以上甚至c5以上的长链液体燃料,在此过程中,铁催化剂可以催化逆水汽变换反应生成一氧化碳中间体,之后可继续加氢生成类似费托合成的长链产物,从而实现高碳烃的合成。然而,铁催化剂在规模化放大和长时间高温二氧化碳加氢反应过程中,存在颗粒强度不够,导致催化剂粉化而稳定性下降等问题。相比费托合成反应,在二氧化碳加氢中应用的铁催化剂需要更好的机械强度以保证在温度更高的条件下满足大规模应用的需要。因此,针对二氧化碳加氢反应,开发一种新型高效的铁基催化剂成型方法对于工业应用显得尤为重要。
技术实现要素:
4.根据本技术的一个方面,提供了一种催化剂的成型方法,成型方法包括:(1)将催化剂进行造粒,得到0.5~5mm的催化剂颗粒;(2)将所述步骤(1)得到的催化剂颗粒进行粉碎和筛选,得到30~80目的催化剂颗粒;(3)将所述步骤(2)得到的催化剂颗粒与粒度为30~80目的粘结剂进行混合,然后进行压片成型,即可得到成型后的催化剂;所述催化剂包括活性组分;所述活性组分包括铁元素。本发明使用硅溶胶或水、高纯石墨与铁形成强相互作用,强化二氧化碳加氢特定反应过程的原料分子吸附与催化过程,大幅提升了反应效率且保证了长时间高温反应条件下催化剂颗粒强度和性能的稳定。
5.本发明针对二氧化碳加氢反应条件下对沉淀型无载体铁基催化剂的特点,开发了一种适应于规模化生产和应用的催化剂成型方法。本发明的目的是解决二氧化碳加氢催化剂铁催化剂在规模化放大和长时间高温二氧化碳加氢反应过程中,存在颗粒强度不够,导致催化剂粉化而稳定性下降等问题。
6.根据本技术的第一方面,提供了一种催化剂的成型方法,所述成型方法包括:
7.(1)将催化剂进行造粒,得到0.5~5mm的催化剂颗粒;
8.(2)将所述步骤(1)得到的催化剂颗粒进行粉碎和筛选,得到30~80目的催化剂颗粒;
9.(3)将所述步骤(2)得到的催化剂颗粒与粒度为30~80目的粘结剂进行混合,然后进行压片成型,即可得到成型后的催化剂;
10.所述催化剂包括活性组分;所述活性组分包括铁元素。
11.可选地,所述粘结剂选自石墨、石墨与水的混合物i、石墨与硅溶胶的混合物ii中的至少一种。
12.可选地,所述石墨为高纯石墨,纯度大于99.9%。
13.可选地,在所述混合物i中,所述石墨和水的质量比为10:1-50:1;
14.在所述混合物ii中,所述石墨和所述硅溶胶的质量比为10:1-50:1。
15.可选地,在所述步骤(3)中,得到的催化剂为圆柱形;
16.圆柱形催化剂的直径为4~6mm;高度为4~8mm。
17.可选地,圆柱形工业催化剂的直径
×
高度的规格为5
×
4mm~5
×
8mm,优选5
×
5mm~5
×
6mm。
18.可选地,在所述步骤(3)中,粘结剂与所述步骤(2)得到的催化剂颗粒的质量比为99:1
–
80:20。
19.本技术中,催化剂的活性组分为fe3o4。
20.可选地,压片成型的压力为0.5~3.0mpa。
21.根据本技术的第二方面,提供了一种催化剂i,所述催化剂i选自根据上述成型方法制备得到的催化剂中的任一种。
22.根据本技术的第三方面,提供了一种二氧化碳加氢制备烃类化合物的方法,将含有二氧化碳和氢气的原料气,在催化剂的存在下反应,制备得到烃类化合物;
23.所述催化剂选自上述催化剂i中的任一种。
24.可选地,在所述原料气中,二氧化碳和氢气的体积比为1:1~1:6。
25.可选地,所述反应的条件为:反应温度为260~350℃;原料气的体积空速为500~20000h-1
;反应压力为0.5~4.0mpa。
26.本技术中,采用高纯石墨与硅溶胶的混合物共同作为粘结剂,石墨和硅可对铁系催化剂形成协同作用,促进二氧化碳加氢反应的进行,此外,还可大幅提高催化剂的成型强度,尤其是侧压强度。
27.本技术能够产生的有益效果包括:
28.本发明中使用硅溶胶或水、高纯石墨与铁形成强相互作用,强化二氧化碳加氢特定反应过程的原料分子吸附与催化过程,大幅提升了反应效率且保证了长时间高温反应条件下催化剂颗粒强度和性能的稳定,符合工业化过程的需求。
具体实施方式
29.下面结合实施例详述本技术,但本技术并不局限于这些实施例。
30.如无特别说明,本技术的实施例中的原料和试剂均通过商业途径购买。
31.铁催化剂制备方法采用专利(zl201610830043.1)中描述的过程通过铁盐的沉淀法制得,助剂可选为钾、钠、锌中的一种或两种。
32.本发明所采用的催化剂反应性能评价过程如下:
33.采用流动的固定床反应器(反应器内直径为30mm)进行二氧化碳催化加氢的反应过程,并以在线及离线的气相色谱仪分析产物组成。反应前,将新鲜催化剂在400℃氢气或合成气条件下原位活化10小时以上。还原后将温度降至催化反应温度280~320℃。反应中原料气配比为co2/h2=1:3,体积空速控制为2000~10000h-1
,压力控制在1~4mpa。冷阱中加入辛烷做溶剂,用来捕捉重质烃。气相产物中co、co2及ch4组分由装有tcd检测器的在线气相色谱进行含量分析,而轻烃组分(c
1-c7)的含量可由另一台装有fid检测器的在线气相色谱分析。反应结束后,收集辛烷冷阱中的重质烃组分,并加入十二烷作为内标。液体组分由装有fid检测器的离线气相色谱进行分析。将气液相分析后的结果进行归一化,得到产物co选择性s(co)、烃组分选择性s(i)以及转化率x(co2)。计算公式如下:
[0034][0035][0036][0037]
co
2in
和co
2out
分别代表进出口的co2摩尔数。
[0038]
本发明中使用到的压片机和造粒机型号分别为:上海天凡药机制造厂,旋转式压片机,zp9a;张家港艾国生物科技有限公司,实验室干法制粒机,glz-25型(半自动款)。
[0039]
实施例1
[0040]
催化剂成型过程如下所述:(a)将前述专利沉淀法制得的含钠(质量比2%)的铁催化剂进行干法造粒(下同),得到5mm的催化剂颗粒;(b)将得到的催化剂颗粒进行粉碎和筛选,得到80目的催化剂颗粒;(c)将(b)得到的催化剂颗粒,与同等目数的粘结剂进行混合,然后进行压片成型(压力2mpa,下同),得到圆柱形工业催化剂。
[0041]
采用高纯石墨(纯度》99.9%)为粘结剂;
[0042]
圆柱形工业催化剂的直径x高度的规格为5x4 mm;
[0043]
将(b)得到的催化剂颗粒,与同等目数的粘结剂进行混合时,按照99:1dd190228i-5的质量比进行。
[0044]
经强度测试(ypd-200c型片剂硬度仪,下同),由上述步骤制得的催化剂正压强度350n/cm,侧压强度90n/cm,在200小时的反应评价(反应条件为320℃,3mpa,sv=4000h-1
,h2/co2(vol)=3)后,催化剂强度变为正压强度300n/cm,侧压强度85n/cm,强度略微变小,但依然满足工业需要。同时200小时前后的反应性能差异很小(反应结果对比如下),说明由上述步骤制得的成型催化剂性能基本无明显衰减,符合工业放大要求。
[0045]
表1成型铁催化剂反应200小时前后的二氧化碳加氢反应结果
[0046][0047]
注:反应初始指的是反应开始后的1h,下同。
[0048]
实施例2
[0049]
催化剂成型过程如下所述:(a)前述沉淀法制得的含钠(质量比2%)的铁催化剂进行干法造粒,得到0.5mm的催化剂颗粒;(b)将得到的催化剂颗粒进行粉碎和筛选,得到80目的催化剂颗粒;(c)将(b)得到的催化剂颗粒,与同等目数的粘结剂进行混合,然后进行压片成型,得到圆柱形工业催化剂。
[0050]
采用高纯石墨(纯度》99.9%)为粘结剂;
[0051]
圆柱形工业催化剂的直径x高度的规格为5x4 mm;
[0052]
将(b)得到的催化剂颗粒,与同等目数的粘结剂进行混合时,按照99:1的质量比进行。
[0053]
经强度测试,由上述步骤制得的催化剂正压强度390n/cm,侧压强度100n/cm,在200小时的反应评价(反应条件同实施例1)后,催化剂强度变为正压强度330n/cm,侧压强度95n/cm,强度略微变小,但依然满足工业需要。同时200小时前后的反应性能差异很小(反应结果对比如下),说明由上述步骤制得的成型催化剂性能基本无明显衰减,符合工业放大要求。
[0054]
表2成型铁催化剂反应200小时前后的二氧化碳加氢反应结果
[0055][0056]
实施例3
[0057]
催化剂成型过程如下所述:(a)前述沉淀法制得的含钾(质量比2%)的铁催化剂进行干法造粒,得到5mm的催化剂颗粒;(b)将得到的催化剂颗粒进行粉碎和筛选,得到40目的催化剂颗粒;(c)将(b)得到的催化剂颗粒,与同等目数的粘结剂进行混合,然后进行压片成型,得到圆柱形工业催化剂。
[0058]
采用高纯石墨(纯度》99.9%)为粘结剂;
[0059]
圆柱形工业催化剂的直径x高度的规格为5x4 mm;
[0060]
将(b)得到的催化剂颗粒,与同等目数的粘结剂进行混合时,按照99:1的质量比进行。
[0061]
经强度测试,由上述步骤制得的催化剂正压强度290n/cm,侧压强度70n/cm,在200小时的反应评价(反应条件同实施例1)后,催化剂强度变为正压强度280n/cm,侧压强度65n/cm,强度略微变小,但依然满足工业需要。同时200小时前后的反应性能差异很小(反应结果对比如下),说明由上述步骤制得的成型催化剂性能基本无明显衰减,符合工业放大要
求。
[0062]
表3成型铁催化剂反应200小时前后的二氧化碳加氢反应结果
[0063][0064]
实施例4
[0065]
催化剂成型过程如下所述:(a)前述沉淀法制得的含钠和锌(质量比各1%)的铁催化剂进行干法造粒,得到5mm的催化剂颗粒;(b)将得到的催化剂颗粒进行粉碎和筛选,得到80目的催化剂颗粒;(c)将(b)得到的催化剂颗粒,与同等目数的粘结剂进行混合,然后进行压片成型,得到圆柱形工业催化剂。
[0066]
采用高纯石墨与水按质量比10:1的混合为粘结剂;
[0067]
圆柱形工业催化剂的直径x高度的规格为5x4 mm;
[0068]
将(b)得到的催化剂颗粒,与同等目数的粘结剂进行混合时,按照99:1的质量比进行。
[0069]
经强度测试,由上述步骤制得的催化剂正压强度360n/cm,侧压强度90n/cm,在200小时的反应评价(反应条件同实施例1)后,催化剂强度变为正压强度358n/cm,侧压强度90n/cm,强度几乎无变化,完全满足工业需要。同时200小时前后的反应性能差异很小(反应结果对比如下),说明由上述步骤制得的成型催化剂性能基本无明显衰减,符合工业放大要求。
[0070]
表4成型铁催化剂反应200小时前后的二氧化碳加氢反应结果
[0071][0072]
实施例5
[0073]
催化剂成型过程如下所述:(a)前述沉淀法制得的含钾和锌(质量比各1%)的铁催化剂进行干法造粒,得到5mm的催化剂颗粒;(b)将得到的催化剂颗粒进行粉碎和筛选,得到80目的催化剂颗粒;(c)将(b)得到的催化剂颗粒,与同等目数的粘结剂进行混合,然后进行压片成型,得到圆柱形工业催化剂。
[0074]
采用高纯石墨与硅溶胶按质量比10:1的混合为粘结剂;
[0075]
圆柱形工业催化剂的直径x高度的规格为5x4mm;
[0076]
将(b)得到的催化剂颗粒,与同等目数的粘结剂进行混合时,按照99:1的质量比进行。
[0077]
经强度测试,由上述步骤制得的催化剂正压强度380n/cm,侧压强度95n/cm,在200小时的反应评价(反应条件同实施例1)后,催化剂强度变为正压强度378n/cm,侧压强度90n/cm,强度几乎无变化,完全满足工业需要。同时200小时前后的反应性能差异很小(反应
结果对比如下),且反应转化率达到35%,达到最优,说明由上述步骤制得的成型催化剂性能基本无明显衰减,完全符合工业放大要求。同时硅溶胶、石墨与铁形成了强相互作用,利用二氧化碳加氢特定反应过程的原料分子吸附与催化过程,大幅提升了反应效率。
[0078]
表5成型铁催化剂反应200小时前后的二氧化碳加氢反应结果
[0079][0080]
实施例6
[0081]
催化剂成型过程如下所述:(a)前述沉淀法制得的含钠(质量比2%)的铁催化剂进行干法造粒,得到5mm的催化剂颗粒;(b)将得到的催化剂颗粒进行粉碎和筛选,得到80目的催化剂颗粒;(c)将(b)得到的催化剂颗粒,与同等目数的粘结剂进行混合,然后进行压片成型,得到圆柱形工业催化剂。
[0082]
采用高纯石墨与水按质量比10:1的混合为粘结剂;
[0083]
圆柱形工业催化剂的直径x高度的规格为5x6 mm;
[0084]
将(b)得到的催化剂颗粒,与同等目数的粘结剂进行混合时,按照99:1的质量比进行。
[0085]
经强度测试,由上述步骤制得的催化剂正压强度310n/cm,侧压强度70n/cm,在200小时的反应评价(反应条件同实施例1)后,催化剂强度变为正压强度300n/cm,侧压强度65n/cm,强度几乎无变化,满足工业需要。同时200小时前后的反应性能差异很小(反应结果对比如下),说明由上述步骤制得的成型催化剂性能基本无明显衰减,符合工业放大要求。
[0086]
表6成型铁催化剂反应200小时前后的二氧化碳加氢反应结果
[0087][0088]
实施例7
[0089]
催化剂成型过程如下所述:(a)前述沉淀法制得的含钠(质量比2%)的铁催化剂进行干法造粒,得到5mm的催化剂颗粒;(b)将得到的催化剂颗粒进行粉碎和筛选,得到80目的催化剂颗粒;(c)将(b)得到的催化剂颗粒,与同等目数的粘结剂进行混合,然后进行压片成型,得到圆柱形工业催化剂。
[0090]
采用高纯石墨与水按质量比10:1的混合为粘结剂;
[0091]
圆柱形工业催化剂的直径x高度的规格为5x6 mm;
[0092]
将(b)得到的催化剂颗粒,与同等目数的粘结剂进行混合时,按照80:20的质量比进行。
[0093]
经强度测试,由上述步骤制得的催化剂正压强度260n/cm,侧压强度60n/cm,在200小时的反应评价(反应条件同实施例1)后,催化剂强度变为正压强度260n/cm,侧压强度
58n/cm,强度几乎无变化,基本满足工业需要。同时200小时前后的反应性能差异很小(反应结果对比如下),说明由上述步骤制得的成型催化剂性能基本无明显衰减,符合工业放大要求。
[0094]
表7成型铁催化剂反应200小时前后的二氧化碳加氢反应结果
[0095][0096]
实施例8
[0097]
催化剂成型过程如下所述:(a)前述沉淀法制得的含钠(质量比2%)的铁催化剂进行干法造粒,得到5mm的催化剂颗粒;(b)将得到的催化剂颗粒进行粉碎和筛选,得到80目的催化剂颗粒;(c)将(b)得到的催化剂颗粒,与同等目数的粘结剂进行混合,然后进行压片成型,得到圆柱形工业催化剂。
[0098]
采用高纯石墨与水按质量比30:1的混合为粘结剂;
[0099]
圆柱形工业催化剂的直径x高度的规格为5x6mm;
[0100]
将(b)得到的催化剂颗粒,与同等目数的粘结剂进行混合时,按照80:20的质量比进行。
[0101]
经强度测试,由上述步骤制得的催化剂正压强度280n/cm,侧压强度65n/cm,在200小时的反应评价(反应条件同实施例1)后,催化剂强度变为正压强度270n/cm,侧压强度62n/cm,强度几乎无变化,基本满足工业需要。同时200小时前后的反应性能差异很小(反应结果对比如下),说明由上述步骤制得的成型催化剂性能基本无明显衰减,符合工业放大要求。
[0102]
表8成型铁催化剂反应200小时前后的二氧化碳加氢反应结果
[0103][0104]
实施例9
[0105]
催化剂成型过程如下所述:(a)前述沉淀法制得的含钠(质量比2%)的铁催化剂进行干法造粒,得到5mm的催化剂颗粒;(b)将得到的催化剂颗粒进行粉碎和筛选,得到80目的催化剂颗粒;(c)将(b)得到的催化剂颗粒,与同等目数的粘结剂进行混合,然后进行压片成型,得到圆柱形工业催化剂。
[0106]
采用高纯石墨与水按质量比50:1的混合为粘结剂;
[0107]
圆柱形工业催化剂的直径x高度的规格为5x6mm;
[0108]
将(b)得到的催化剂颗粒,与同等目数的粘结剂进行混合时,按照80:20的质量比进行。
[0109]
经强度测试,由上述步骤制得的催化剂正压强度285n/cm,侧压强度70n/cm,在200
小时的反应评价(反应条件同实施例1)后,催化剂强度变为正压强度275n/cm,侧压强度65n/cm,强度几乎无变化,基本满足工业需要。同时200小时前后的反应性能差异很小(反应结果对比如下),说明由上述步骤制得的成型催化剂性能基本无明显衰减,符合工业放大要求。
[0110]
表9成型铁催化剂反应200小时前后的二氧化碳加氢反应结果
[0111][0112]
实施例10
[0113]
催化剂成型过程如下所述:(a)前述沉淀法制得的含钾和锌(质量比各1%)的铁催化剂进行干法造粒,得到5mm的催化剂颗粒;(b)将得到的催化剂颗粒进行粉碎和筛选,得到80目的催化剂颗粒;(c)将(b)得到的催化剂颗粒,与同等目数的粘结剂进行混合,然后进行压片成型,得到圆柱形工业催化剂。
[0114]
采用高纯石墨与硅溶胶按质量比30:1的混合为粘结剂;
[0115]
圆柱形工业催化剂的直径x高度的规格为5x4mm;
[0116]
将(b)得到的催化剂颗粒,与同等目数的粘结剂进行混合时,按照99:1的质量比进行。
[0117]
经强度测试,由上述步骤制得的催化剂正压强度390n/cm,侧压强度95n/cm,在200小时的反应评价(反应条件同实施例1)后,催化剂强度变为正压强度385n/cm,侧压强度90n/cm,强度几乎无变化,完全满足工业需要。同时200小时前后的反应性能差异很小(反应结果对比如下),且反应转化率达到38%,达到最优,说明由上述步骤制得的成型催化剂性能基本无明显衰减,完全符合工业放大要求。同时硅溶胶、石墨与铁形成了强相互作用,利用二氧化碳加氢特定反应过程的原料分子吸附与催化过程,大幅提升了反应效率。
[0118]
表10成型铁催化剂反应200小时前后的二氧化碳加氢反应结果
[0119][0120]
实施例11
[0121]
催化剂成型过程如下所述:(a)前述沉淀法制得的含钾和锌(质量比各1%)的铁催化剂进行干法造粒,得到5mm的催化剂颗粒;(b)将得到的催化剂颗粒进行粉碎和筛选,得到80目的催化剂颗粒;(c)将(b)得到的催化剂颗粒,与同等目数的粘结剂进行混合,然后进行压片成型,得到圆柱形工业催化剂。
[0122]
采用高纯石墨与硅溶胶按质量比50:1的混合为粘结剂;
[0123]
圆柱形工业催化剂的直径x高度的规格为5x4mm;
[0124]
将(b)得到的催化剂颗粒,与同等目数的粘结剂进行混合时,按照99:1的质量比进
行。
[0125]
经强度测试,由上述步骤制得的催化剂正压强度395n/cm,侧压强度95n/cm,在200小时的反应评价(反应条件同实施例1)后,催化剂强度变为正压强度385n/cm,侧压强度90n/cm,强度变化较小,满足工业需要。同时200小时前后的反应性能差异很小(反应结果对比如下),且反应转化率达到36%,达到最优,说明由上述步骤制得的成型催化剂性能基本无明显衰减,完全符合工业放大要求。同时硅溶胶、石墨与铁形成了强相互作用,利用二氧化碳加氢特定反应过程的原料分子吸附与催化过程,大幅提升了反应效率。
[0126]
表11成型铁催化剂反应200小时前后的二氧化碳加氢反应结果
[0127][0128]
实施例12
[0129]
本实施例中的催化剂成型过程同实施例11,将实施例11中的催化剂反应评价条件由(320℃,3mpa,sv=4000h-1
,h2/co2(vol)=3)变更为(320℃,3mpa,sv=4000h-1
,h2/co2(vol)=6),200小时之后,反应后催化剂强度变化与实施例11相同。反应性能差异很小(反应结果对比如下),且反应转化率达到41%,说明由上述步骤制得的成型催化剂性能基本无明显衰减,在高氢碳比反应条件下,依然符合工业放大要求。同时硅溶胶、石墨与铁形成了强相互作用,利用二氧化碳加氢特定反应过程的原料分子吸附与催化过程,大幅提升了反应效率。
[0130]
表12成型铁催化剂反应200小时前后的二氧化碳加氢反应结果
[0131][0132]
实施例13
[0133]
本实施例中的催化剂成型过程同实施例11,将实施例11中的催化剂反应评价条件由(320℃,3mpa,sv=4000h-1
,h2/co2(vol)=3)变更为(270℃,3mpa,sv=4000h-1
,h2/co2(vol)=3),200小时之后,催化剂强度变为正压强度388n/cm,侧压强度91n/cm,强度变化更小,满足工业需要。反应性能差异很小(反应结果对比如下),且反应转化率维持在24%,说明由上述步骤制得的成型催化剂性能基本无明显衰减,在低温反应条件下,依然符合工业放大要求。同时硅溶胶、石墨与铁形成了强相互作用,利用二氧化碳加氢特定反应过程的原料分子吸附与催化过程,大幅提升了反应效率。
[0134]
表13成型铁催化剂反应200小时前后的二氧化碳加氢反应结果
[0135][0136]
实施例14
[0137]
本实施例中的催化剂成型过程同实施例11,将实施例11中的催化剂反应评价条件由(320℃,3mpa,sv=4000h-1
,h2/co2(vol)=3)变更为(320℃,3mpa,sv=20000h-1
,h2/co2(vol)=3),200小时之后,催化剂强度变为正压强度380n/cm,侧压强度86n/cm,强度变化依然满足工业需要。反应性能差异很小(反应结果对比如下),且反应转化率20%,说明由上述步骤制得的成型催化剂性能基本无明显衰减,在高空速反应条件下,依然符合工业放大要求。同时硅溶胶、石墨与铁形成了强相互作用,利用二氧化碳加氢特定反应过程的原料分子吸附与催化过程,大幅提升了反应效率。
[0138]
表14成型铁催化剂反应200小时前后的二氧化碳加氢反应结果
[0139][0140]
实施例15
[0141]
本实施例中的催化剂成型过程同实施例11,将实施例11中的催化剂反应评价条件由(320℃,3mpa,sv=4000h-1
,h2/co2(vol)=3)变更为(320℃,1mpa,sv=20000h-1
,h2/co2(vol)=3),200小时之后,催化剂强度变为正压强度389n/cm,侧压强度90n/cm,强度变化小,满足工业需要。反应性能差异很小(反应结果对比如下),且反应转化率基本不变,说明由上述步骤制得的成型催化剂性能基本无明显衰减,在其他压力反应条件下,依然符合工业放大要求。同时硅溶胶、石墨与铁形成了强相互作用,利用二氧化碳加氢特定反应过程的原料分子吸附与催化过程,大幅提升了反应效率。
[0142]
表15成型铁催化剂反应200小时前后的二氧化碳加氢反应结果
[0143][0144]
对比例1
[0145]
催化剂成型过程如下所述:(a)前述沉淀法制得的含钠(质量比2%)的铁催化剂进行干法造粒,得到5mm的催化剂颗粒;(b)将得到的催化剂颗粒进行粉碎和筛选,得到80目的催化剂颗粒;(c)将(b)得到的催化剂颗粒进行压片成型,得到圆柱形工业催化剂。
[0146]
无粘结剂;
[0147]
圆柱形工业催化剂的直径x高度的规格为5x5mm;
[0148]
经强度测试,由上述步骤制得的催化剂正压强度380n/cm,侧压强度80n/cm,在200小时的反应评价后,催化剂强度变为正压强度200n/cm,侧压强度40n/cm,机械强度发生大幅降低,无法满足长时间工业需要。同时200小时前后的反应性能下降明显(反应结果对比如下),说明由上述步骤制得的成型催化剂性能无法符合工业放大要求。
[0149]
表16成型铁催化剂反应200小时前后的二氧化碳加氢反应结果
[0150][0151]
对比例2
[0152]
催化剂成型过程如下所述:(a)前述沉淀法制得的含钠(质量比2%)的铁催化剂进行干法造粒,得到5mm的催化剂颗粒;不进行前述(b)步骤;(c)将得到的催化剂颗粒,与同等目数的粘结剂进行混合,然后进行压片成型,得到圆柱形工业催化剂。
[0153]
采用高纯石墨与水按质量比10:1的混合为粘结剂;
[0154]
圆柱形工业催化剂的直径x高度的规格为5x6mm;
[0155]
将(b)得到的催化剂颗粒,与同等目数的粘结剂进行混合时,按照80:20的质量比进行。
[0156]
经强度测试,由上述步骤制得的催化剂正压强度170n/cm,侧压强度50n/cm,在200小时的反应评价后,催化剂强度变为正压强度110n/cm,侧压强度30n/cm,强度明显下降,且初始强度无法满足工业需要。同时200小时前后的反应性能也明显衰减,无法符合工业放大要求。
[0157]
表17成型铁催化剂反应200小时前后的二氧化碳加氢反应结果
[0158][0159]
以上所述,仅是本发明的几个实施例,并非对本发明做任何形式的限制,虽然本发明以较佳实施例揭示如上,然而并非用以限制本发明,任何熟悉本专业的技术人员,在不脱离本发明技术方案的范围内,利用上述揭示的技术内容做出些许的变动或修饰均等同于等效实施案例,均属于技术方案范围内。
再多了解一些
本文用于企业家、创业者技术爱好者查询,结果仅供参考。