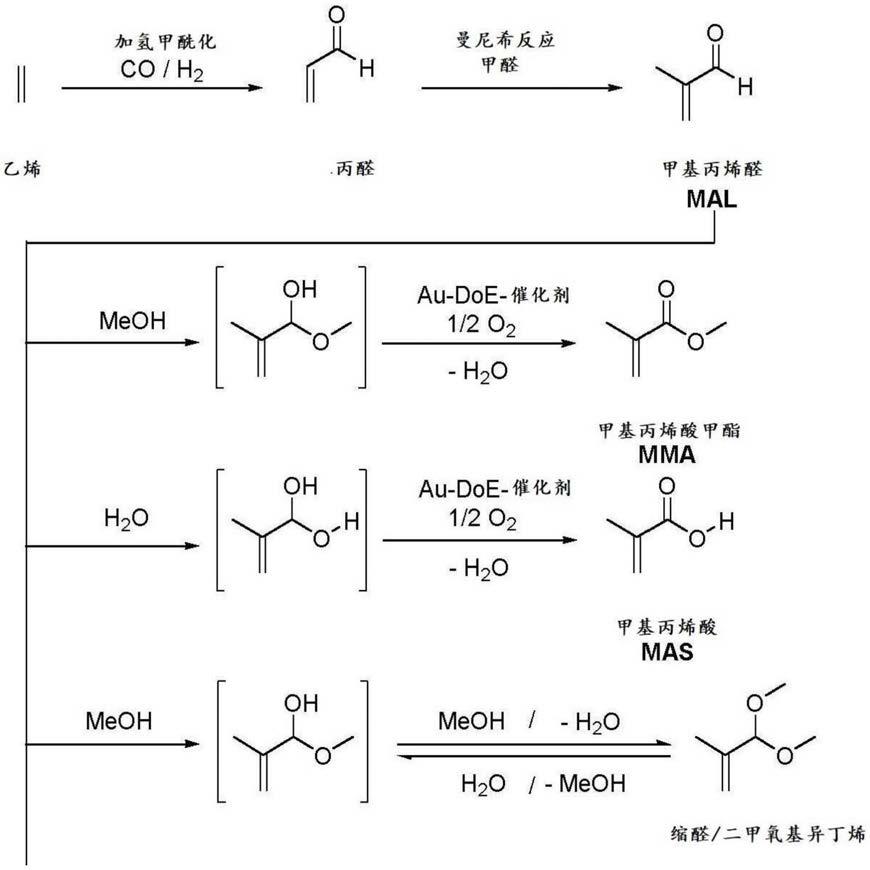
1.本发明涉及制备甲基丙烯酸烷基酯,特别是甲基丙烯酸甲酯(mma)的方法,该方法包括在第一反应阶段制备甲基丙烯醛(mal),在第二反应阶段用醇(优选甲醇)将所述甲基丙烯醛直接氧化酯化(doe)以提供甲基丙烯酸烷基酯,和对得自所述第二反应阶段的甲基丙烯酸烷基酯粗产物进行后处理。
2.本发明尤其涉及对得自甲基丙烯醛的氧化酯化的反应器输出物进行的优化后处理,其中通过所产生的工艺水料流的优化再循环,所用水的量、所用酸的量和/或水性废物料流的量被最小化。
背景技术:
3.甲基丙烯酸甲酯大量用于制备聚合物和与其它可聚合化合物制备共聚物。此外,甲基丙烯酸甲酯(mma)是多种基于甲基丙烯酸(mas)的特种酯的重要合成单元,所述特种酯可通过酸与相应醇进行的酯化或mma与相应醇进行的酯交换来制备。因此,对于制备这种起始材料的尽可能简单、经济且环境友好的方法有着很大的兴趣。
4.目前,甲基丙烯酸甲酯(mma)是通过从c
2-、c
3-或c
4-合成单元开始的多种方法制备的。在这些方法之一中,通过以下方式获得mma:在非均相催化剂上用大气氧将异丁烯或叔丁醇在气相中氧化成甲基丙烯醛(mal),和随后利用甲醇进行甲基丙烯醛的氧化酯化反应。这种由asahi开发的方法尤其描述在出版物us 5,969,178和us 7,012,039中。这种方法的缺点特别是非常高的能量需求。
5.根据所谓的asahi方法制备mma是从c4(异丁烯或叔丁醇)开始进行的,其中将mal进行中间分离,和随后利用甲醇进行mal的直接氧化酯化(缩写为“doe”)以提供mma,其中通过与水反应形成甲基丙烯酸(mas)作为副产物。
6.在所述方法的进一步开发中,在第一阶段中由丙醛和福尔马林获得甲基丙烯醛。这种方法描述在wo 2014/170223中。
7.以下方案1显示了用于制备mma的反应矩阵,其中示例性地描述了从乙烯、合成气和甲醛开始制备甲基丙烯醛。如上文解释的,甲基丙烯醛也可从异丁烯或叔丁醇开始获得。
[0008][0009]
方案1:用于制备mma的c2方法的反应矩阵。
[0010]
在所述氧化酯化(doe反应)中,在水的存在下形成甲基丙烯酸,所述水当连续进行反应时通常以2重量%至20重量%的稳态浓度存在于氧化酯化反应器中。如果所述doe反应是在恒定ph下进行的,则所得甲基丙烯酸至少部分地被含碱的或碱性的助剂(在最简单情况下被碱金属化合物)所中和。
[0011]
得自氧化酯化的粗产物通常含有作为主反应产物的甲基丙烯酸烷基酯,未转化的反应物,特别是甲基丙烯醛和醇,少量的水和多种副产物,例如甲基丙烯酸(mas)及其盐(例如甲基丙烯酸钠)、缩醛(例如二甲氧基异丁烯,dmib)以及其它高沸点组分,例如加成产物和狄尔斯-阿尔德(diels-alder)产物,例如羟基异丁酸及其相应的酯,二聚体甲基丙烯醛(dimal)及其酯(dimal酯)。所述高沸点副产物必须经常被移除,以获得希望的具有适合于聚合的纯度的甲基丙烯酸烷基酯产物(例如mma),所述纯度通常显著大于99重量%。
[0012]
us 5 969 178和其中引用的现有技术描述了用于将异丁烯或叔丁醇氧化转化成甲基丙烯醛和随后氧化酯化成mma的方法变型方案。在第一蒸馏阶段,在塔顶之下从氧化酯化反应的粗产物中移除甲基丙烯醛和甲醇的混合物,同时经由塔顶移除低沸点成分。然后将含mma的塔底物与不饱和烃一起导引入到第二蒸馏阶段中,在该阶段中经由塔顶移除由
甲醇和饱和烃形成的共沸物。将包含粗mma的塔底物送去进一步后处理,同时借助于相分离器和第三蒸馏塔将甲醇从经塔顶获得的级分中分离出来,并将其再循环到反应器中。在此必须考虑的是,由于形成了共沸物,所述甲醇可能含有相对大量的水并且因此需要将其送去脱水。
[0013]
作为这种方法的备选方案,us 5,969,178公开了仅在一个塔中进行后处理,其中在所述塔中进料必须位于塔底物上方。在这个塔中,经塔顶将低沸点成分从反应器输出物中移除。在塔底物中残留的是粗mma和水的混合物,其必须被送去进一步后处理。最后将用于再循环到反应器中的甲基丙烯醛和甲醇的混合物经由侧料流从所述塔中取出。文献us 5,969,178指出,由于多种共沸物,这种方法是难以进行。对于从在所描述的方法模式中必然产生的含有甲基丙烯酸盐的水溶液中移除mma,us 5,969,178没有提供任何解决方案。
[0014]
us 7,012,039公开了得自氧化酯化的反应器输出物的稍微不同的后处理。使用也明显释放铅到反应溶液中的含铅催化剂使得随后的后处理尤其更加复杂,因为在所述方法中形成了不可溶的铅盐而且需要在高成本和复杂性下将其另行移除。在此,在第一蒸馏阶段中,经由筛板在塔顶蒸馏出甲基丙烯醛,并将含mma的水性混合物从塔底导引入到相分离器中。在所述相分离器中,通过添加硫酸将所述混合物调节到ph值为约2。然后借助于离心将被硫酸酸化的水与有机/油相分离。将这个有机相在进一步蒸馏中分离成高沸点成分和在塔顶抽出的包含mma的相。然后在第三蒸馏中将所述包含mma的相与低沸点成分分离。随后甚至进行第四蒸馏以进行最终的纯化。
[0015]
根据us 7,012,039的方法的问题是硫酸,其必须大量添加,而其可能对设备的部件具有腐蚀作用。因此,这些部件,例如尤其是相分离器,或者另外是第二蒸馏塔,必须由对此合适的材料制备。根据该公开内容不能推知对于本领域技术人员显而易见的含酸的水性料流的循环控制。另外,根据us 7,012,039的方法没有提供回收甲基丙烯酸或留在产物中的残留甲醇的可能性。
[0016]
wo 2014/170223描述了与us 7,012,039类似的方法。区别在于,通过将氢氧化钠甲醇溶液添加到循环体系中而调节在所述氧化酯化中的ph值。所述ph调节尤其用于保护催化剂。另外,由于含有盐,在相分离中移除水相是更简单的。然而,另一个结果是所形成的甲基丙烯酸作为钠盐存在,并且随后与水相一起被移除和弃去。尽管在其中于相分离过程中添加硫酸的变型方案中回收了游离酸,但代价是产生了硫酸(氢)钠,其在处置时可能导致其它问题。
[0017]
wo 2017/046110描述了制备mma的方法,其中通过蒸馏得自萃取的水相(其含有甲醇、至少一种碱金属盐、甲基丙烯酸和强无机酸)而对得自氧化酯化的粗产物进行后处理。得自这个蒸馏阶段的低沸点级分(其主要含有甲醇)被再循环到所述氧化酯化中。将水性塔底级分排出并处置掉。可将含有水和甲基丙烯酸的得自所述蒸馏的侧料流送去萃取。通过在萃取所述粗产物的过程中添加强酸中和了甲基丙烯酸的盐,在此使得能够方便地获得游离甲基丙烯酸。
[0018]
文献wo 2019/042807描述了制备pmma树脂的方法,该方法包括最初制备单体。在反应器中进行氧化酯化后,通过添加有机和/或无机酸对mma粗产物进行后处理,以通过水解进行副产物二甲氧基异丁烯的裂解。
[0019]
对得自氧化酯化的粗产物进行后处理的现有技术方法的缺点在于:在多个点将相
对大量的酸和水供应到工艺中,并且因此还产生相对大比例的水性废物料流,该料流被酸和/或有机组分污染并且必须被处置掉。添加强酸还要求升高对应工艺部件的设备成本和复杂性,例如尤其是要设置耐腐蚀材料。
技术实现要素:
[0020]
要解决的技术问题
[0021]
因此,鉴于现有技术,本发明要解决的问题是,提供一种在技术上改进的用于氧化酯化甲基丙烯醛的方法,该方法不具有传统方法的上述缺点。本发明要解决的问题尤其是提供对得自甲基丙烯醛的氧化酯化的粗产物进行的改进的后处理,其中所用的水的量和所用的酸的量以及水性废物料流的量可以被降低。尤其要提供的方法是:提供能够在尽可能低的处置成本和复杂性的情况下操作的方法,特别是通过降低水性和有机成分和酸在废物料流中的产生。
[0022]
所述方法与现有技术相比还应是成本有效的,例如关于待用于构造设备的材料方面。所述方法还应使得能够实现甲基丙烯酸烷基酯的尽可能大的产率,以及能够回收甲基丙烯酸系副产物,例如甲基丙烯酸。所述方法原则上应当使得能够转化和再循环尽可能大比例的副产物。
[0023]
问题的解决方案
[0024]
已经令人惊奇地发现,通过对产生的工艺水料流的优化管理,可以使酸和水的输入以及水性废水的量最小化。尤其已经发现,得自用于回收醇的蒸馏阶段的水性塔底物的最佳的和有目的的分布可实现所用的水和/或所用的酸的节约和使需要从所述方法中取出的废水料流减少。
[0025]
根据本发明,通过以下的用于制备甲基丙烯酸烷基酯的方法解决了上述问题,其中在第一反应阶段中在反应器i中制备甲基丙烯醛(mal),并将其在第二反应阶段中在反应器ii中在含氧气体的存在下在液相中用醇(优选甲醇)进行氧化酯化,其中形成了反应水,从而提供甲基丙烯酸烷基酯,优选提供甲基丙烯酸甲酯(mma),该方法的特征在于:
[0026]
a.对得自反应器ii的反应混合物进行后处理,以提供甲基丙烯酸烷基酯的过程包括至少一个蒸馏和至少一个萃取;
[0027]
b.在塔ii中的至少一个蒸馏(蒸馏阶段ii)中对得自萃取的含有醇和布朗斯台德酸的碱金属盐和/或碱土金属盐的水相进行处理,以使得在所述塔ii底部形成含有反应水和布朗斯台德酸的碱金属盐和/或碱土金属盐的工艺水料流(塔底级分w4),其中在该工艺水料流中,醇和甲基丙烯酸烷基酯的含量为基于总工艺水料流计的小于5重量%,和
[0028]
c.将这个得自所述塔ii底部的工艺水料流(塔底级分w4)部分地从所述方法中排出,并送去处置,和部分地再循环到对得自反应器ii的反应混合物进行的后处理中。
[0029]
发明详述
[0030]
在本发明的上下文中,表述“料流”、“相”或“级分”(其含有所要求保护的方法的反应物、产物和/或副产物)要被理解为意思是指:可在各自料流中发现所引述的化合物,例如可以在相应料流中发现主要比例的所述反应物、产物和/或副产物。除了所引述的化合物外,原则上也可存在其它成分。所述成分的提及经常用于阐明各自的方法步骤。
[0031]
优选的是,在蒸馏塔中进行根据本发明的方法的至少一个蒸馏,例如下文描述的蒸馏阶段i、ii、iii和iv。所述蒸馏塔对应于蒸馏阶段而被称为i、ii、iii、iv等。蒸馏塔的典型实施方案是本领域技术人员已知的。通常可以采用板式塔,其例如配备有筛板、阶梯式板、穿流栅板和/或条形板,或者填料塔,例如无规填料塔(例如具有得自raschig的超级拉西环(raschig superring))或具有规整填充材料(例如得自sulzer的mellapak)的塔。所述蒸馏阶段中通常获得至少一个高沸点塔底级分和至少一个低沸点塔顶级分。在不同蒸馏阶段中的蒸馏温度由本领域技术人员根据蒸馏压力、待分离的混合物的组成、所述蒸馏塔的塔板数量和构造以及其它因素进行选择。蒸馏温度优选在20℃至120℃范围内。
[0032]
优选的是,所述醇是甲醇,和所述甲基丙烯酸烷基酯是甲基丙烯酸甲酯(mma)。
[0033]
优选的是,所述布朗斯台德酸(下文中也被称为酸s)是强酸,特别是具有的pka值小于甲基丙烯酸的pka值的酸。所述布朗斯台德酸优选具有小于3,特别优选小于2的pka值。可以采用强无机酸,例如硫酸或磷酸,或强有机酸,例如甲磺酸或甲苯磺酸。所述布朗斯台德酸优选是硫酸。
[0034]
根据本发明的方法优选是以连续或半连续的方式操作的。除了不连续排出废物料流外,所述方法优选以连续方式操作。
[0035]
优选的是,得自塔ii底部的工艺水料流被部分再循环到所述萃取中,其中在所述萃取中使这个再循环的工艺水料流与含有甲基丙烯酸烷基酯和醇的有机相(特别是有机相p1)接触。
[0036]
优选的是,得自塔ii底部的工艺水料流是得自下文所述的优选方法的塔底级分w4。
[0037]
优选的是,得自塔ii底部的工艺水料流被部分地再循环到反应器iii(特别是缩醛裂解器iii,其中在料流w1中存在的缩醛被裂解)中,其中使这个再循环的工艺水料流在反应器iii中与含有甲基丙烯酸烷基酯和醇的有机相(特别是塔底级分w1)接触,所述有机相具有的甲基丙烯醛缩醛(特别是二甲氧基异丁烯)的含量为基于所述有机相计的小于3重量%。
[0038]
所述萃取优选在萃取塔中和/或在一系列相继连接的至少两个混合器-沉降器设备中进行,并且在所述萃取塔塔顶之下或者在混合器-沉降器设备的混合器区域中添加经得自塔ii底部的工艺水料流,和任选在所述萃取塔的顶部区域中添加水,特别是去矿物质水。
[0039]
供应到根据本发明的方法中的水特别是去矿物质水。
[0040]
优选的是,在添加得自塔ii底部的工艺水料流之上将水和任选的布朗斯台德酸添加到所述萃取中。
[0041]
优选在反应器iii中实施布朗斯台德酸的添加,并且选择这种添加使得在连续操作中,在得自塔ii底部的工艺水料流(特别是塔底级分w4)中建立在1.5至2.5范围内的ph值。
[0042]
在一个优选的实施方案中,将布朗斯台德酸添加到根据本发明的方法中的过程仅经由在反应器iii中的添加实施。还可想到在所述方法中的不同的点处进行酸的添加,以使得可以对于不同方法操作更精确地调整不同的ph值。
[0043]
所述萃取优选提供含有甲基丙烯酸烷基酯和甲基丙烯酸的有机相,并将得自所述
萃取的有机相(特别是有机相p1或得自蒸馏阶段iii的塔顶级分w5)在蒸馏阶段iv(塔iv)中分离成含有甲基丙烯酸烷基酯的塔底级分(特别是塔底级分w8),和较低沸点的塔顶级分(特别是塔顶级分w7)。
[0044]
优选将得自塔iv的级分与水混合,并随后在相分离器i中分离成有机相(特别是有机相p3)和水相(特别是水相p4)。
[0045]
优选的是,将得自相分离器i的水相(特别是水相p4)与至少一种布朗斯台德酸在反应器iv中混合,其中存在于得自相分离器i的水相中的酯副产物被裂解,和醇被回收,并且其中任选地,得自塔ii底部的工艺水料流被部分地送入到反应器iv中。
[0046]
优选的是,将得自反应器iv的产物完全或部分地送入到塔ii中。
[0047]
在一个可另选的实施方案中,在反应器iii中的缩醛水解(dmib 水
→
mal至meoh)和在反应器iv中进行的部分酯水解可合并在一个反应容器中。
[0048]
优选的是,将得自相分离器i的水相完全或部分地送入到塔ii中。
[0049]
优选的是,将得自反应器ii的反应混合物在蒸馏阶段i(塔i)中进行分离,其中经由塔顶级分移除甲基丙烯醛和部分醇,并将其再循环到反应器ii中。
[0050]
优选的是,将甲基丙烯醛完全或部分地添加到蒸馏阶段i中,并经由得自蒸馏阶段i的塔顶级分送入到反应器ii中。
[0051]
优选的是,所述醇是甲醇,和所述甲基丙烯酸烷基酯是甲基丙烯酸甲酯。所述布朗斯台德酸优选是硫酸。
[0052]
第一反应阶段(mal制备)
[0053]
在第一反应阶段中,根据本发明的方法包括在反应器i中制备甲基丙烯醛(mal)。在此,根据本发明,用于合成甲基丙烯醛的方法的第一阶段可自由选择。所述方法的第一反应阶段可既包括基于叔丁醇或异丁烯的第一阶段合成,又包括基于丙醛和福尔马林的第一阶段合成。
[0054]
在基于丙醛和福尔马林制备甲基丙烯醛(mal)的情况下,原则上存在两种合适的提供具有一定品质的甲基丙烯醛的方法变型方案,所述具有一定品质的甲基丙烯醛可在第二反应阶段(直接氧化酯化,doe反应)中使用。一方面,丙醛和福尔马林可以在搅拌反应器或泵循环反应器中,在20℃至120℃的温度下,在1巴至10巴的压力下进行反应。这通常需要大于10分钟的反应时间以实现足够的转化率。另一方面,丙醛和福尔马林也可以进行反应以提供mal,其中在10至100巴之间的平均压力下以及在120℃至250℃之间的相对高的温度下,所述反应在反应时间为2秒至20秒的情况下实现了希望的高产率。
[0055]
用于制备甲基丙烯醛的方法是本领域技术人员已知的,并且例如描述在ullmanns encyclopedia of industrial chemistry(乌尔曼工业化学大全),2012,wiley-vch verlag gmbh,weinheim(doi:10.1002/14356007.a01_149.pub2)中。
[0056]
所述第一反应阶段也可以是从c4原材料开始的方法,尤其是叔丁醇和/或异丁烯的氧化。在此,异丁烯或叔丁醇通常在气相中,在非均相催化剂上,在高于300℃的温度下与含氧气体和优选与水蒸气进行反应。相关的现有技术中描述了大量的子变型方案和可用的催化剂体系以及分离方案。对于此的综述可例如在以下文献中找到:“trends and future of monomer-mma technologies(单体mma技术的趋势与未来)”,k.nagai和t.ui,sumitomo chemical co.,ltd.,basic chemicals research laboratory,2005(http://
www.sumitomo-chem.co.jp/english/rd/report/theses/docs/20040200_30a.pdf)。
[0057]
优选的是,在反应器i中的第一反应阶段是丙醛与福尔马林的反应。所述第一反应阶段可任选包含用于移除低沸物(例如剩余的丙醛)和/或移除高沸物(例如二聚甲基丙烯醛)的蒸馏塔。
[0058]
第二反应阶段(直接氧化酯化doe)
[0059]
在第二反应阶段中,根据本发明的方法包括在反应器ii中用醇(优选甲醇)将甲基丙烯醛氧化酯化(doe反应),其中获得了甲基丙烯酸烷基酯,优选甲基丙烯酸甲酯(mma)。
[0060]
所述直接氧化酯化(doe反应)优选在液相中,在2至100巴的压力下,优选在2至50巴范围内的压力下,和在10℃至200℃范围内的温度下,采用非均相催化剂进行。所述非均相催化剂通常是负载型含金纳米粒子,其具有小于20nm,优选在0.2至20nm范围内的粒子尺寸。
[0061]
所述直接氧化酯化通常在控制ph值的情况下进行,以保证所述催化剂的最佳活性;优选将所述ph值控制到6-8的ph,特别优选控制到ph为7。
[0062]
所述第二反应阶段优选包括在含氧气体的存在下,在20℃至150℃之间的中等温度下,在1至20巴的中等压力下,在非均相颗粒状含贵金属催化剂(优选具有1至300μm的粒子尺寸,其中也可以使用更大的粒子)的存在下甲基丙烯醛和醇的反应。
[0063]
现有技术描述了多种用于这种用甲醇将mal氧化酯化以提供mma的催化剂。us 6,040,472描述了在氧化物载体上的含pd-pb催化剂;ep 1 393 800描述了含金催化剂,其包含分布在氧化硅或tio2/sio2载体上的金粒子;ep 2 177 267和ep 2 210 664描述了具有壳结构的含镍催化剂;ep 2 210 664公开了一种包含在载体上的氧化镍和金纳米粒子的催化剂;wo 2017/084969描述了基于两种或更多种混合氧化物作为载体的催化剂体系,其同样除了氧化钴外还包含纳米粒子状金作为活性组分。
[0064]
所述反应器ii通常包含甲基丙烯醛(mal)的进料、醇(特别是甲醇)的进料、氧气和/或空气的引入和碱的进料。
[0065]
可任选将所述反应物或者所述反应物的一部分(特别是碱和meoh)在任选的混合器中混合,然后再引入到所述反应器ii中。
[0066]
用于将甲基丙烯醛直接氧化酯化的方法是本领域技术人员已知的。关于所述第二反应阶段的进一步的细节例如描述在us 5,969,178、us 7,012,039、wo 2014/170223和wo 2019/042807中。
[0067]
在一个优选的实施方案中,得自反应器ii的反应混合物的后处理包括以下步骤:
[0068]
i.将得自反应器ii的氧化酯化的粗产物在蒸馏阶段i中进行分离,其中在塔顶级分中移除甲基丙烯醛和部分醇,并将它们再循环到反应器ii中,和其中获得了含有甲基丙烯酸烷基酯、甲基丙烯酸和/或其盐、醇和水的塔底级分w1;
[0069]
ii.任选将所述塔底级分w1引入到反应器iii中,并添加至少一种酸s,其中在料流w1中存在的缩醛被裂解,和其中获得了料流w2;
[0070]
iii.用水萃取料流w1或w2,并分离成含有甲基丙烯酸烷基酯和甲基丙烯酸的有机相p1和含有水、酸s和/或其盐、醇、甲基丙烯酸和/或其盐的水相p2。
[0071]
iv.将得自所述萃取的水相p2在蒸馏阶段ii中进行分离,其中获得主要含有醇的塔顶级分w3和含有水、酸s和/或其盐和甲基丙烯酸和/或其盐的塔底级分w4;
[0072]
v.将得自所述萃取的有机相p1在蒸馏阶段iii中进行分离,其中获得含有甲基丙烯酸烷基酯的塔顶级分w5和含有甲基丙烯酸的塔底级分w6;
[0073]
vi.将得自蒸馏阶段iii的塔顶级分w5在蒸馏阶段iv中进行分离,其中获得塔顶级分w7和含有甲基丙烯酸烷基酯的塔底级分w8;
[0074]
vii.将得自蒸馏阶段iv的塔顶级分w7与水混合,并在相分离器i中分离成有机相p3和水相p4;
[0075]
viii.任选将得自相分离器i的水相p4与至少一种酸s在反应器iv中混合,其中存在于p4中的酯副产物被裂解,和醇被回收,和其中获得了水相p5;
[0076]
其中将得自蒸馏阶段ii的塔底级分w4完全或部分地送入到一个或多个选自反应器iii、萃取、相分离器i和反应器iv的方法部件中。
[0077]
通常,所述水相,例如p2和p4,是各自分离的较重的相,而所述有机相,例如p1和p3,是各自分离的较轻的相。
[0078]
下文中更具体地描述得自反应器ii的反应混合物的后处理的优选步骤。
[0079]
蒸馏阶段i(步骤i)
[0080]
根据本发明的方法优选包括将得自反应器ii的氧化酯化的反应混合物在蒸馏阶段i中(特别是在蒸馏塔i中)进行分离,其中甲基丙烯醛和部分醇被移除,并被再循环到反应器ii中,和其中获得了含有甲基丙烯酸烷基酯、甲基丙烯酸和/或其盐、醇和水的料流w1。
[0081]
在根据本发明的方法的一个优选实施方案中,不将或仅部分将所述甲基丙烯醛直接送入到反应器ii中,而是将其经由蒸馏阶段i引入到所述方法中。优选的是,将甲基丙烯醛完全或部分地添加到蒸馏阶段i中,并经由得自蒸馏阶段i的低沸点塔顶级分送入到反应器ii中。
[0082]
反应器iii—缩醛裂解器(任选的步骤ii)
[0083]
根据本发明的方法优选包括将得自蒸馏阶段i的塔底级分w1引入到反应器iii(缩醛裂解器)中,并添加至少一种酸s,其中在所述料流w1中存在的缩醛被裂解,和其中获得了料流w2。
[0084]
优选地,在反应器iii中,缩醛副产物二甲氧基异丁烯(dmib)被裂解成甲基丙烯醛(mal)和甲醇(meoh)。缩醛裂解例如描述在wo 2019/042807和jp 11-302224a中。尤其是,通过在任选的方法步骤ii)中移除所述缩醛副产物可降低甲基丙烯酸烷基酯的派生产物(例如聚合物和模塑料)的着色。
[0085]
此外,在反应器iii中通常将甲基丙烯酸的盐(例如尤其是碱金属甲基丙烯酸盐)中和,其中形成游离的甲基丙烯酸。
[0086]
通常在反应器iii中进行塔底级分w1与至少一种酸s和任选的水的混合。可以本领域技术人员已知的方式配置反应器iii,例如作为优选装配有静态混合器的管式反应器,作为搅拌反应器或作为它们的组合。
[0087]
反应器iii优选包括酸进料i,其中供入至少一种酸s,优选硫酸。另外可能的是,所述至少一种酸s(完全或部分)经由得自蒸馏阶段ii的塔底级分w4的再循环而被供入。反应器iii除了酸进料i外,可任选还包括水进料。
[0088]
在反应器iii中的ph值优选在0至7.0,优选0.5至5.0范围内。
[0089]
通常选择将所述至少一种酸s(优选硫酸)添加到反应器iii中,使得在所述萃取中
的水相p2具有在小于或等于ph 4,优选ph 1.5至ph 3范围内的ph值。
[0090]
在一个优选的实施方案中,实现任选的方法步骤ii)并选择在反应器iii中添加酸s(优选硫酸),尤其是经由酸进料i添加所述酸s,使得在连续操作中,在得自蒸馏阶段ii的塔底级分w4中建立在0至3范围内,优选为2的ph值。
[0091]
在一个优选的实施方案中,实现任选的方法步骤ii),并仅经由进入到反应器iii中的进料,优选经由酸进料i,将新鲜的酸s(优选硫酸)添加到根据本发明的方法中。
[0092]
萃取(步骤iii)
[0093]
根据本发明的方法包括至少一个萃取。
[0094]
所述方法优选包括用水萃取料流w1(无任选的步骤ii))或w2(有任选的步骤ii)),和分离成含有甲基丙烯酸烷基酯和甲基丙烯酸的有机相p1(通常是轻相)和含有水、酸s和/或其盐、醇、甲基丙烯酸和/或其盐的水相p2(通常是重相)。优选在所述塔的上部进行水的添加。
[0095]
所述有机相p1通常主要含有甲基丙烯酸烷基酯和反应的有机副产物,例如甲基丙烯酸和其它高沸点副产物,以及较少量的水和甲醇。水相p2通常含有少许有机产物,并主要含有水和甲醇以及得自所述中和的碱金属盐或碱土金属盐,和甲基丙烯酸的盐,特别是甲基丙烯酸的碱金属盐。
[0096]
优选的是,在所述萃取过程中添加至少一种酸s。优选选择在所述萃取中添加所述至少一种酸s(优选硫酸),使得在所述萃取中的水相p2具有的ph值范围为大于或等于3。在所述萃取中添加酸s通常中和了甲基丙烯酸的盐,例如特别是甲基丙烯酸碱金属盐。
[0097]
可任选经由任选的进料ii将水添加到所述萃取中。可任选将酸s添加到所述萃取中,例如经由任选的酸进料和/或与水进料ii一起添加。另外可能的是,所述水和任选的所述酸s(完全或部分地)经由得自蒸馏阶段ii的塔底级分w4的再循环供应到所述萃取中。
[0098]
在步骤iii)中的萃取优选在萃取塔中进行。本领域技术人员已知萃取塔的典型实施方案。通常可用板式塔或填料塔,例如无规填料塔(例如用拉西环填充)或具有规整填充材料(例如得自sulzer的mellapak)的塔。
[0099]
在一个优选的实施方案中,在蒸馏塔的上部区域经由水进料ii将水添加到所述萃取中,优选添加到第一萃取阶段中,优选在得自蒸馏阶段ii的塔底级分w4的可能的再循环之上。
[0100]
在一个优选的实施方案中,在萃取塔中进行所述萃取(步骤iii),并在所述萃取塔的中部区域,优选在第一萃取阶段之下,特别优选在第二萃取阶段之下添加得自蒸馏阶段ii的塔底级分w4。进一步优选的是,在添加得自蒸馏阶段ii的塔底级分w4之上将水和任选的酸s添加到所述萃取塔中的萃取中。
[0101]
优选经由下文描述的蒸馏阶段iii和iv和任选的v和vi进一步纯化得自所述萃取的有机相p1(其含有最大比例的希望的甲基丙烯酸烷基酯产物)。在此,从含有主要比例的甲基丙烯酸烷基酯的有机相p1中初始取出较高沸点组分(蒸馏阶段iii)和随后取出较低沸点组分(蒸馏阶段iv)。
[0102]
水相w4通常含有相应布朗斯台德酸的无机盐,其中所述盐的含量基于w4计在0.5至15重量%范围内。将所述含盐的相w4再循环到所述萃取中通常导致萃取效率的改进。通常,这个效果基于与去矿物质水相比升高的密度,并且因此基于与有机相相比更大的密度
差。
[0103]
蒸馏阶段ii—醇回收(步骤iv)
[0104]
根据本发明的方法优选包括将得自所述萃取的水相p2在蒸馏阶段ii中(优选在蒸馏塔ii中)进行分离,其中获得主要含有醇的低沸点塔顶级分w3和含有水、酸s和/或其盐和甲基丙烯酸和/或其盐的高沸点塔底级分w4。
[0105]
优选的是,将塔顶级分w3完全或部分地再循环到反应器ii中。
[0106]
根据本发明,将得自蒸馏阶段ii的水性塔底级分再循环到根据本发明的方法的一个或多个不同的点,因此节约了水和/或酸s,并降低了水性废物料流的量。根据本发明,将得自蒸馏阶段ii的塔底级分w4完全或部分地送入到一个或多个选自反应器iii、萃取、相分离器i和反应器iv的方法部件中。
[0107]
在所述方法的一个优选的实施方案中,将得自蒸馏阶段ii的塔底级分w4的一部分连续和/或不连续地从所述方法中排出(作为清除)。
[0108]
优选将得自蒸馏阶段ii的塔底级分w4完全或部分地再循环到所述萃取中(步骤iii)。上文描述了将w4添加到所述萃取中的优选实施方案。
[0109]
优选将得自蒸馏阶段ii的塔底级分w4完全或部分地送入到相分离器i中(步骤vii)。
[0110]
在一个优选的实施方案中,实现任选的方法步骤ii)(缩醛裂解器),并将得自蒸馏阶段ii的塔底级分w4完全或部分地再循环到反应器iii(缩醛裂解器)中。
[0111]
在一个优选的实施方案中,实现任选的方法步骤viii),并将得自蒸馏阶段ii的塔底级分w4完全或部分地送入到反应器iv中(酯水解)。
[0112]
在一个优选的实施方案中,将所述塔底级分w4再循环到所列举的方法部件中的两个或更多个中。
[0113]
所述水性塔底级分w4优选具有在1至3,优选1.5至2.5范围内的ph值。所述水性塔底级分w4优选含有基于w4的总重量计大于60重量%,优选大于80重量%的水。所述塔底级分w4优选含有基于w4的总重量计小于10重量%,优选小于5重量%,特别优选小于1重量%的醇,特别是甲醇。
[0114]
蒸馏阶段iii——移除高沸物(步骤v)
[0115]
根据本发明的方法优选包括将得自所述萃取的有机相p1在蒸馏阶段iii中(特别是在蒸馏塔iii中)进行分离,其中获得含有甲基丙烯酸烷基酯的低沸点塔顶级分w5和含有甲基丙烯酸的高沸点塔底级分w6。
[0116]
在一个实施方案中,可以将塔顶级分w5的一部分送入到相分离器ii中。可将所述水相供应到反应器iv中。
[0117]
在一个优选的实施方案中,可将含有甲基丙烯酸的塔底级分w6送入到任选的蒸馏阶段vi(蒸馏塔vi)中,其中在w6中的甲基丙烯酸烷基酯的量被降低,和可以将含有甲基丙烯酸烷基酯的蒸馏阶段vi的塔顶级分再循环到蒸馏阶段iii中。
[0118]
在一个优选的实施方案中,可以从塔底级分w6中和/或从得自任选的蒸馏阶段vi的塔底级分中获得甲基丙烯酸作为另外的产物。其细节例如描述在wo 2017/046110中。
[0119]
可另选地,用于纯化甲基丙烯酸烷基酯的一个或多个或所有蒸馏阶段iii、iv和v也可由结晶替代。
[0120]
蒸馏阶段iv——移除低沸物(步骤vi)
[0121]
根据本发明的方法优选包括将得自蒸馏阶段iii的低沸点塔顶级分w5在蒸馏阶段iv中(特别是在蒸馏塔iv中)进行分离,其中获得低沸点塔顶级分w7和含有甲基丙烯酸烷基酯的高沸点塔底级分w8。
[0122]
可优选将塔底级分w8送入到另一个任选的蒸馏阶段v(特别是蒸馏塔v)中,其中进行所述甲基丙烯酸烷基酯的最终纯化,并将所述甲基丙烯酸烷基酯作为得自任选的蒸馏阶段v的塔顶级分作为产物从所述方法中排出。
[0123]
可任选将得自任选的蒸馏阶段v的塔底级分送入到蒸馏阶段iii和/或蒸馏阶段vi中。
[0124]
相分离器i(步骤vii)
[0125]
根据本发明的方法优选包括将得自蒸馏阶段iv的塔顶级分w7与水混合,并在相分离器i中分离成有机相p3(通常是轻相)和水相p4(通常是重相)。
[0126]
相分离器的典型构造是本领域技术人员已知的。
[0127]
可优选将得自相分离器i的有机相p3完全或部分地,连续或不连续地从所述方法中排出作为有机废物料流。优选的是,将得自相分离器i的有机相p3完全或部分地送入到任选的蒸馏阶段vii中(mal回收),其中回收甲基丙烯醛并将其送到反应器ii中的氧化酯化中。
[0128]
在一个可另选的实施方案中,将得自相分离器i的水相p4完全或部分地送入到蒸馏塔ii中(醇回收)。如果尚未实现任选的方法步骤viii),则特别进行这个过程。
[0129]
还可以将得自相分离器i的水相p4完全或部分地,连续和/或不连续地排出作为水性废水料流。
[0130]
相分离器i优选包含水进料iii。另外可能的是,所述水(完全或部分)经由得自蒸馏阶段ii的塔底级分w4的再循环供入。
[0131]
反应器iv—酯水解(任选的步骤viii)
[0132]
根据本发明的方法优选包括将得自相分离器i的水相p4与至少一种酸s在反应器iv(酯水解)中混合,其中存在于p4中的酯副产物被裂解,和醇被回收,和其中获得了水相p5。
[0133]
通常在任选的反应器iv中,具有低于甲基丙烯酸甲酯的沸点的酯副产物,特别是饱和酯,例如异丁酸烷基酯和丙酸烷基酯,例如异丁酸甲酯、丙酸甲酯被水解,在此可回收醇,优选甲醇。
[0134]
在所述方法的一个优选的实施方案中,实现任选的方法步骤viii),并将得自反应器iv(酯水解)的水相p5完全或部分地送入到蒸馏塔ii。在此,通常在所述酯水解中回收的醇经由塔顶级分w3供应到反应器ii中。
[0135]
还可以将得自反应器iv的水相p5的一部分作为水性废水料流连续和/或不连续地排出。
[0136]
反应器iv优选包括酸进料iv,其中供入至少一种酸s,优选硫酸。另外可能的是,所述至少一种酸s(完全或部分地)经由得自蒸馏阶段ii的塔底级分w4的再循环供入。任选地,反应器iv除了酸进料iv外,可还包括水进料。
附图说明
[0137]
图1示例性说明了用于制备甲基丙烯酸烷基酯的根据本发明的方法的第二方法步骤(mal的氧化酯化和产物料流的后处理)的可能的示意性流程图。用于mal合成的根据本发明的方法的反应器i没有示出。
[0138]
附图标记列表
[0139]
(1)进入到反应器ii中的mal进料
[0140]
(2)用于氧化酯化mal的反应器ii
[0141]
(3)进入到反应器ii中的醇(特别是甲醇)进料
[0142]
(4)进入到反应器ii中的氧气和/或空气引入
[0143]
(5)进入到反应器ii中的碱进料
[0144]
(6)用于移除mal的蒸馏塔i
[0145]
(7)含有mal和醇的低沸点级分,其用于再循环到反应器ii中(再循环料流)
[0146]
(8)用于裂解缩醛副产物(例如二甲氧基异丁烯(dmib)以提供mal和meoh)的反应器iii(缩醛裂解器)(任选的)
[0147]
(9)萃取
[0148]
(10)任选的进入到(8)中的酸进料i
[0149]
(11)任选的进入到(9)中的水进料ii
[0150]
(12)用于回收醇的蒸馏塔ii
[0151]
(13)含有醇的得自蒸馏塔ii的低沸点级分,其用于再循环到反应器ii中
[0152]
(14)得自蒸馏塔ii的塔底级分,其含有水、酸和烷基甲基丙烯酸和/或其盐
[0153]
(15)用于移除高沸物的蒸馏塔iii
[0154]
(16)用于移除低沸物的蒸馏塔iv
[0155]
(17)用于最终纯化mma的蒸馏塔v
[0156]
(18)用于降低在得自(15)的底部料流中的甲基丙烯酸烷基酯的量的蒸馏塔vi(任选的)
[0157]
(19)用于后处理得自塔iv(16)的低沸点级分的相分离器i
[0158]
(20)用于从得自相分离器i(19)的有机相中回收mal的蒸馏塔vii(任选的)
[0159]
(21)反应器iv(酯裂解器),其用于从酯副产物(例如饱和酯,例如异丁酸烷基酯、丙酸烷基酯)中回收醇(任选的)
[0160]
(22)用于混合反应物的设备,混合器i(任选的)
[0161]
(23)水后处理(任选的)
[0162]
(24)进入到(19)中的水进料iii(任选的)
[0163]
(25)进入到(21)中的酸进料iv(任选的)
[0164]
(26)甲基丙烯酸烷基酯产物料流
[0165]
(27)含有mal的再循环料流
[0166]
(a1)/(a2)水性废物料流
[0167]
(b1)/(b2)有机废物料流
具体实施方式
[0168]
实验部分
[0169]
实施例1—其中将w4再循环到萃取(9)中
[0170]
在反应器ii中,在液相中,在含氧气体的存在下,使甲基丙烯醛与甲醇反应以提供甲基丙烯酸甲酯(mma)。得自反应器ii的反应器输出物具有以下组成:meoh 43.1重量%,mal 8.8重量%,mma 37.0重量%,h2o 6.6重量%,mal缩醛360ppm,其余物4.4重量%。
[0171]
将得自反应器ii的输出物(2)直接供应到萃取(9)中。在萃取塔中进行所述萃取。实施进入到所述萃取中的部分水进料ii(11)。将得自所述萃取的水相p2送入到塔ii(12)中。从得自塔ii的底部料流中排出水性废水料流a1。部分地,将得自塔ii的底部料流(w4)再循环到萃取(9)中。
[0172]
在实验3的情况下,在萃取塔(9)的顶部添加w4和水。在实验4的情况下,在所述萃取塔顶部之下添加w4,和在萃取塔(9)的顶部添加水。
[0173]
使用塔iii(15)、iv(16)和v(17)进行得自所述萃取的有机相的后处理。在塔v中,将mma产物料流(26)作为塔顶级分取出。
[0174]
下表1中总结了进入到萃取(9)中的进料和水性废物料流的量。
[0175][0176]
表1:实验1-4的总结
[0177]
实施例2—其中将w4再循环到反应器iii/缩醛裂解器中
[0178]
在反应器ii中,在液相中,在含氧气体的存在下,使甲基丙烯醛与甲醇反应以提供甲基丙烯酸甲酯(mma)。得自反应器ii的反应器输出物具有以下组成:meoh 43.1重量%,mal 8.8重量%,mma 37.0重量%,h2o 6.6重量%,mal缩醛360ppm,其余物4.4重量%。
[0179]
将得自反应器ii(2)的输出物送入到反应器iii(8)中以进行后处理。反应器iii的形式是连续操作的搅拌釜,其具有下游的倾析器。部分地,经由酸进料i(10)将96%硫酸(酸s)进料到反应器iii中。将得自反应器iii的输出物供应到萃取(9)中。
[0180]
在萃取塔中进行所述萃取。实施进入到所述萃取中的部分水进料ii(11)。将得自
所述萃取的水相p2送入到塔ii(12)中。从得自塔ii的底部料流中排出水性废水料流a1。部分地,将得自塔ii的底部料流(w4)再循环到反应器iii和/或萃取(9)中。
[0181]
使用塔iii(15)、iv(16)和v(17)进行得自所述萃取的有机相的后处理。在塔v中,将mma产物料流(26)作为塔顶级分取出。
[0182]
下表2中总结了进入到反应器iii和所述萃取中的进料。
[0183][0184]
表2:实验5-7的总结
[0185]
实施例3—其中将w4再循环到相分离器i中
[0186]
如实施例1中描述的那样实施。经由水进料iii(24)将得自塔iv的塔顶级分与水混合,并随后在相分离器i(19)中分离成有机相p3和水相p4。将水相p4再循环到塔ii(12)中。
[0187]
将得自塔ii的底部料流(w4)部分地再循环到相分离器i和/或到所述萃取中。下表3中总结了进入到相分离器i和萃取中的进料。
[0188][0189]
表3:实验8-10的总结
[0190]
实施例4—其中将w4再循环到反应器iv/酯裂解器中
[0191]
如实施例3中描述的那样实施。经由水进料iii(24)向相分离器i中提供水。使得自相分离器i(19)的水相p4送入到反应器iv(酯裂解器)(21)中,并经由酸进料iv与96%硫酸(酸s)混合。将得自反应器iv的水相p5再循环到塔ii(12)中。
[0192]
将得自塔ii的底部料流(w4)部分地再循环到反应器iv和/或到所述萃取中。下表4中总结了进入到反应器iv和所述萃取中的进料。
[0193][0194]
表4:实验11-13的总结
[0195]
已经表明,通过根据本发明的方法控制,可以在保持相同的产物品质和产率下,节约水和/或酸进料,并且使水性废水料流a1最小化。
再多了解一些
本文用于企业家、创业者技术爱好者查询,结果仅供参考。