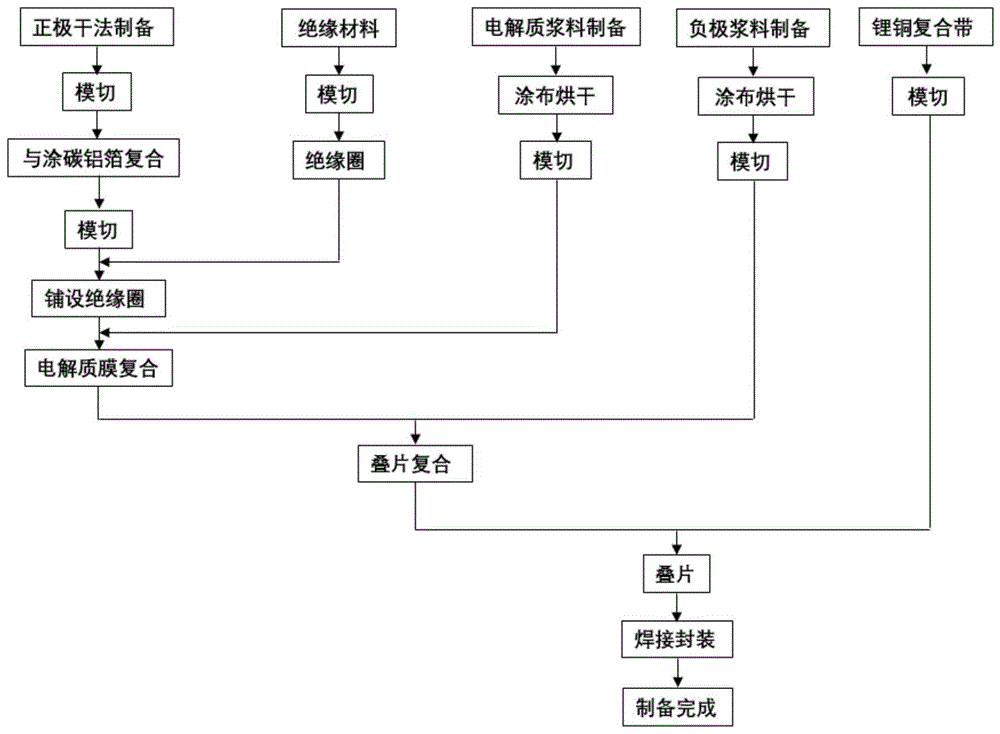
本发明属于全固态电池技术领域,涉及一种全固态电芯结构、其制备方法及全固态电芯组。
背景技术
固态电池采用不可燃的固态电解质替换了可燃性的有机液态电解质,大幅提升了电池系统的安全性,实现能量密度同步提升。在各类新型电池体系中,固态电池是距离产业化最近的下一代技术,这已成为产业与科学界的共识。其中,硫化物电解质具有比较高的锂离子电导率。主要包括thio-LISICON、Li6PS5Cl、Li10GeP2S12、Li6PS5Cl,Li10SnP2S12、Li2S-P2S5、Li2S-SiS2、Li2S-B2S3等,室温离子电导率可以达到10-3~10-2S/cm,接近甚至超过有机电解液,同时具有热稳定高、安全性能好、电化学稳定窗口宽(达5V以上)的特点,在高功率以及高低温固态电池方面优势突出。
但当采用硫化物固体电解质制备全固态电芯体系时,由于硫化物电解质属于陶瓷类材料,颗粒与颗粒之间粘合力差,形状不规则,不易制成有韧性的低孔隙率的独立电解质膜,而且为了使得制备的电解质膜有较高的电导率,使用的粘结剂含量越少越好,这就使得想制备一张既有高电导率又有好的机械强度的电解质膜形成了自身的矛盾,且硫化无电解质膜属于陶瓷类隔膜,膜韧性和强度差,抗剪切力能力低,全固态电池各层内部和各层之间均为固固接触,为保证能量密度优势,全固态电池负极通常会采用含硅负极或锂金属负极,目前锂金属负极的应用成本及技术难度依然很高,由于硅基负极材料具有很高的质量比容量和体积比容量,成本低廉、无毒无污染,嵌锂平台较低的优势,因此发展硅基负极是提高锂离子电池能量密度的最有效的方法之一。为减小固固接触及充放电过程体积膨胀对带来的影响,确保全固态电池容量发挥,通常在全固态电池测试或使用过程中需要约1MPa至10MPa的高外加压力来保压,有时候为保证性能发挥甚至要大到几十兆帕的压力,由于硫化物、卤化物等电解质对水分极不稳定,只要使用了这些电解质的部件(正极、负极或电解质膜),均需要在手套箱内惰性气体环境中或超低露点温度环境中制造,量产难度大,目前硫化物全固态电池连续化生产技术公开少之又少。
全固态电池在手套箱内制备流程和操作复杂,生产效率低下,且全固态电池测试或工作中通常加有较大压力,硫化物电解质膜抗剪切力能力差,传统的多层叠片制备大容量全固态电芯(多层叠片)较易出现边缘微短路现象,且由于电池内结构通常是负极面积大于正极面积(负极集流体大于正极集流体),多出的负极及电解质膜面积束缚力或压力小于与正极复合部分,负极集流体大于正极集流体,因此多出的面积会因剪切力及充放电过程膨胀收缩而出现掉料粉化现象,如果搭配使用硅基负极片,其成分一般由硫化物电解质(离子导体)、硅材料、导电剂、石墨材料或合金等组成,硅材料本身的电导率低,作为活性物质,硅在充电/放电周期内嵌入和脱出锂时,体积变化达到270~400%,循环寿命差,这个体积膨胀会导致硅颗粒的粉碎,极片在充放电过程中反复开裂,以及极片涂层从铜集流体上分离,继而粉化衰减,最终导致锂离子电池的失效。且硅负极片在无补锂情况下首效低,降低了电池的容量发挥,此外,为了降低成本和提高电池整体性能,研发人员在固态电池上使用干法制备的正极片,避免实用溶剂,但干法正极片与相关部件制备电池又会带来一系列技术问题,成熟技术少之又少,以上问题累加给高能量高性能能量密度全固态电池的制备和应用带来显著困难,使得全固态电池的安全性、电性能及制备能力降低。
技术实现要素:
针对现有技术存在的不足,本发明的目的在于提供一种全固态电芯结构、其制备方法及全固态电芯组,本发明采用干法制备正极片,相比湿法工艺,干法工艺制备得到的正极片可拥有更高的面容量及倍率性能,通过组装过程中的预锂能够有效提高电池首效和使用硅负极片电池的循环性能,简化制备流程,提高制造效率和一致性。
为达此目的,本发明采用以下技术方案:
第一方面,本发明提供了一种全固态电芯结构的制备方法,所述制备方法包括:
采用干法制备正极活性层,将正极活性层与正极集流体叠片复合得到正极片,在正极活性层外周套设绝缘圈,得到结构Ⅰ;
制备电解质浆料,经涂布烘干后得到电解质隔膜,将电解质隔膜贴近结构Ⅰ的正极活性层,与结构Ⅰ叠片复合后得到结构Ⅱ;
制备负极浆料,经涂布烘干后得到负极活性层,将负极活性层贴近结构Ⅱ的电解质隔膜,与结构Ⅱ叠片复合后得到结构Ⅲ;
在结构Ⅲ的负极活性层表面层叠负极集流体,经过叠片和封装后得到所述全固态电芯结构。
本发明采用干法制备正极片,相比湿法工艺,干法工艺制备得到的正极片可拥有更高的面容量及倍率性能,通过组装过程中的预锂能够有效提高电池首效和使用硅负极片电池的循环性能,简化制备流程,提高制造效率和一致性。本发明提供的制备方法可以制备得到一种正极活性层、负极活性层和电解质隔膜层间接近全面积接触的全固态电芯,不仅能防止负极活性层及电解质隔膜边缘掉料,并且大大减小电池内部剪切力的存在,各部件平行面积可抑制膨胀,可有效增加安时级大容量大面积全固态硫化物电芯的循环性能、安全性和成品率,并且采用交叉叠片方式,可连续化生产,成本低,效率高,组装便捷,推进高安全高性能硫化物全固态电池尽早应用。
作为本发明一种优选的技术方案,所述正极活性层的干法制备过程包括:
正极活性材料、正极电解质、导电剂和正极粘结剂混合后依次经过球磨和热辊压后得到所述正极活性层。
优选地,所述正极活性材料、正极电解质、导电剂和正极粘结剂的质量比为(40~90):(5~55):(0.1~10):(0.1~10),例如可以是40:55:2:3、50:40:1:4、60:30:5:5、70:20:9.9:0.1、80:10:0.1:9.9或90:5:2:3,但并不仅限于所列举的数值,该数值范围内其他未列举的数值同样适用。
优选地,所述热辊压的温度为50~200℃,例如可以是50℃、60℃、70℃、80℃、90℃、100℃、110℃、120℃、130℃、140℃、150℃、160℃、170℃、180℃、190℃或200℃,但并不仅限于所列举的数值,该数值范围内其他未列举的数值同样适用。
优选地,所述正极活性材料为核壳结构,包括正极颗粒和包覆于所述正极颗粒表面的包覆层。
优选地,所述正极颗粒的化学通式为LiNixCoyMzO2,x≥0,y≥0,z≥0,且x y z=1,其中M选自Mn、Al、Zr、Ti、V、Mg、Fe或Mo中的任意一种或至少两种的组合。
优选地,所述包覆层的材料为离子导体,进一步优选为Li2TiO3、LiNbO3、Li3BO3、Li2ZrO3、LiCoO3、LiPO3、Li2MnO4、Al(PO3)3、La(PO3)3或NaPO3中的任意一种或至少两种的组合。
优选地,所述包覆层的厚度为1~10nm,例如可以是1nm、2nm、3nm、4nm、5nm、6nm、7nm、8nm、9nm或10nm,但并不仅限于所列举的数值,该数值范围内其他未列举的数值同样适用。
优选地,所述正极电解质包括硫化物电解质和/或卤化物电解质。
优选地,所述硫化物电解质包括thio-LISICON、Li10GeP2S12、Li6PS5Cl、Li10SnP2S12、Li2S-P2S5、Li2S-SiS2、LiI-LiBr-Li2S-P2S5或Li2S-B2S3中的任意一种或至少两种的组合。
优选地,所述卤化物电解质包括Li3YCl6、Li3BrY6、Li3ErCl6、Li3YbCl6、LiInxSc0.66-xCl4、Li2.5Y0.5Zr0.5Cl6或Li3ErI6中的任意一种或至少两种的组合。
优选地,所述导电剂包括零维导电剂、一维导电剂和二维导电剂。
优选地,所述零维导电剂为点状导电剂,进一步优选地,所述零维导电剂包括导电炭黑和/或AB。
优选地,所述一维导电剂为线状导电剂和/或管状导电剂,进一步优选地,所述一维导电剂包括碳纳米管和/或碳纤维。
优选地,所述二维导电剂包括石墨烯。
优选地,所述正极粘结剂包括PTFE。
作为本发明一种优选的技术方案,所述正极活性层的厚度为10~200μm,例如可以是10μm、20μm、40μm、60μm、80μm、100μm、110μm、120μm、130μm、140μm、150μm、160μm、170μm、180μm、190μm或200μm,但并不仅限于所列举的数值,该数值范围内其他未列举的数值同样适用。
优选地,将制备得到的正极活性层进行模切,随后与正极集流体叠片后进行平压或等静压复合,得到正极片。
优选地,模切后的正极活性层的长宽比为1~10,例如可以是1、2、3、4、5、6、7、8、9或10,但并不仅限于所列举的数值,该数值范围内其他未列举的数值同样适用。
优选地,所述正极集流体为涂碳铝箔,包括铝箔以及涂覆于所述铝箔至少一侧表面的碳层。
优选地,所述铝箔的长度两侧为空箔区,所述铝箔的中部区域为涂碳区,所述空箔区内留白,所述涂碳区内设置有碳层。
优选地,单侧空箔区的宽度为1~5cm,例如可以是1.0cm、1.5cm、2.0cm、2.5cm、3.0cm、3.5cm、4.0cm、4.5cm或5.0cm,但并不仅限于所列举的数值,该数值范围内其他未列举的数值同样适用。
优选地,正极活性层与正极集流体的叠片复合过程包括:
将若干正极活性层沿涂碳铝箔的长度方向并排间隔设置于所述碳层表面,辊压复合后,将各正极活性层连带相应的正极集流体裁切下来得到正极片,涂碳铝箔的空箔区裁切形成正极极耳。
优选地,相邻两个正极活性层之间的间隙宽度为3~50mm,例如可以是3mm、5mm、10mm、15mm、20mm、25mm、30mm、35mm、40mm、45mm或50mm,但并不仅限于所列举的数值,该数值范围内其他未列举的数值同样适用。
优选地,所述正极极耳的宽度为所在正极片边长的10~30%,例如可以是10%、12%、14%、16%、18%、20%、22%、24%、26%、28%或30%,但并不仅限于所列举的数值,该数值范围内其他未列举的数值同样适用。
优选地,所述正极极耳的长宽比为1~3,例如可以是1.0、1.2、1.4、1.6、1.8、2.0、2.2、2.4、2.6、2.8或3.0,但并不仅限于所列举的数值,该数值范围内其他未列举的数值同样适用。
优选地,在裁切得到的正极片中,所述正极集流体的各边边长大于所述正极活性层的各边边长,从而在正极活性层外周形成环形的正极集流体空白区域。
优选地,所述正极集流体的各边边长比所述正极活性层的各边边长大1.5~6mm,例如可以是1.5mm、2mm、2.5mm、3mm、3.5mm、4mm、4.5mm、5mm、5.5mm或6mm,但并不仅限于所列举的数值,该数值范围内其他未列举的数值同样适用。
作为本发明一种优选的技术方案,所述绝缘圈的材质为聚合物材料或电解质隔膜材料。
优选地,所述聚合物材料包括PET、PI、PP或PE。
优选地,所述电解质隔膜材料包括氧化物电解质膜或硫化物电解质膜,进一步优选为硫化物电解质膜。
优选地,所述绝缘圈的厚度为正极活性层厚度的50~100%,例如可以是50%、55%、60%、65%、70%、75%、80%、85%、90%、95%或100%,但并不仅限于所列举的数值,该数值范围内其他未列举的数值同样适用。
优选地,所述绝缘圈套设于正极活性层外周的环形正极集流体空白区域。
优选地,所述绝缘圈的内圈长宽尺寸与正极活性层的长宽尺寸相同,所述绝缘圈的外圈长宽尺寸与正极片的最大外缘尺寸相同或大于正极片的最大外缘尺寸。
优选地,所述绝缘圈的外圈长宽尺寸比正极片的最大外缘尺寸大0~1mm,例如可以是0mm、0.1mm、0.2mm、0.3mm、0.4mm、0.5mm、0.6mm、0.7mm、0.8mm、0.9mm或1mm,但并不仅限于所列举的数值,该数值范围内其他未列举的数值同样适用。
本发明在正极活性层外周套设绝缘圈的目的在于起到整平作用,预防因电解质隔膜和负极活性层大于正极活性层的部分与正极活性层产生较大的高度落差而产生的剪切力,从而避免此处剪切破碎掉料导致电池失效。
作为本发明一种优选的技术方案,所述电解质浆料包括硫化物、电解质粘结剂和电解质溶剂。
优选地,所述电解质粘结剂和硫化物的质量比为(0.1~10):(90~99.9),例如可以是0.1:99.9、1:99、2:98、3:97、4:96、5:95、6:94、7:93、8:92、9:91或10:90,但并不仅限于所列举的数值,该数值范围内其他未列举的数值同样适用。
优选地,所述电解质粘结剂包括PVDF5130、PVDF75130、PVDF21216、PVD、F6020、PVDF-HVS900、PVDF-HFP、PVDF-LBG、NBR、HNBRSBR、SBS、SEBS或PTFE中的任意一种或至少两种的组合。
优选地,所述电解质溶剂包括二氯甲烷、四氢呋喃、正己烷、正庚烷、甲苯、2,4-二甲基-3-戊酮、一氯代苯、二甲苯、苯甲醚、环己酮、1,3,5-三甲苯、正癸烷或甲基甲酰胺中的任意一种或至少两种的组合。
优选地,所述电解质浆料的涂布过程采用的基材包括PET、PI、铝箔或不锈钢,进一步优选为铝箔。
优选地,涂布烘干后得到的电解质隔膜包括基材和位于基材表面的电解质层。
优选地,所述电解质隔膜的厚度为10~50μm,例如可以是10μm、15μm、20μm、25μm、30μm、35μm、40μm、45μm或50μm,但并不仅限于所列举的数值,该数值范围内其他未列举的数值同样适用。
优选地,对电解质隔膜进行模切,模切后的电解质隔膜的长宽尺寸与正极片的最大外缘尺寸相同或大于正极片的最大外缘尺寸。
优选地,所述电解质的长宽尺寸比正极片的最大外缘尺寸大0~1mm,例如可以是0.1mm、0.2mm、0.3mm、0.5mm、0.6mm、0.7mm、0.8mm、0.9mm或1mm,但并不仅限于所列举的数值,该数值范围内其他未列举的数值同样适用。
优选地,所述电解质隔膜的电解质层一侧贴近结构Ⅰ的正极活性层,与结构Ⅰ叠片后进行平压或等静压复合,随后去除基材,电解质层保留在正极活性层表面,得到结构Ⅱ。
作为本发明一种优选的技术方案,所述负极浆料中包括硅材料、电解质、负极粘结剂、导电剂和负极溶剂。
优选地,所述负极浆料中还包括合金材料和/或碳材料。
优选地,所述碳材料包括硬碳、软碳或石墨。
优选地,所述合金材料包括Si合金和/或Sn合金。
优选地,所述负极粘结剂包括PAA、Li-PAA、SBR、NBR、HNBR、SBS、SEBS、PTFE或PEO中的任意一种或至少两种的组合。
优选地,所述负极溶剂包括纯水、二氯甲烷、四氢呋喃、正己烷、正庚烷、甲苯、2,4-二甲基-3-戊酮、一氯代苯、二甲苯、苯甲醚、环己酮、1,3,5-三甲苯、正癸烷或甲基甲酰胺中的任意一种或至少两种的组合。
优选地,所述硅材料、合金材料、碳材料、电解质、负极粘结剂和导电剂的质量比为(5~90):(1~30):(0~80):(0~60):(0.1~15):(0.1~15),例如可以是90:5:2:1:1:1、80:10:5:4:0.5:0.5、50:5:10:30:2:3、30:20:20:20:5:5或5:30:60:3:1:1,但并不仅限于所列举的数值,该数值范围内其他未列举的数值同样适用。
优选地,制备得到的负极活性层经过模切后与结构Ⅱ叠片复合。
优选地,模切后的负极活性层的各边边长小于正极片中正极集流体的各边边长,同时大于正极片中正极活性层的各边边长。
优选地,模切后的负极活性层的各边边长比正极片中正极集流体的各边边长小0.5~4mm,模切后的负极活性层的各边边长比正极片中正极活性层的各边边长大0.5~4mm,例如可以是0.5mm、0.6mm、0.7mm、0.8mm、0.9mm、1.0mm、1.1mm、1.2mm、1.3mm、1.4mm、1.5mm、1.6mm、1.7mm、1.8mm、1.9mm、2.1mm、2.4mm、2.7mm、3mm、3.3mm、3.7mm或4.0mm,但并不仅限于所列举的数值,该数值范围内其他未列举的数值同样适用。
优选地,将模切后的负极活性层层叠至电解质隔膜表面,经过平压复合或等静压复合后得到结构Ⅲ。
优选地,所述负极活性层的厚度为10~150μm,例如可以是10μm、20μm、30μm、40μm、50μm、60μm、70μm、80μm、90μm、100μm、110μm、120μm、130μm、140μm或150μm,但并不仅限于所列举的数值,该数值范围内其他未列举的数值同样适用。
作为本发明一种优选的技术方案,所述负极集流体为锂铜复合带,包括铜箔以及涂覆于铜箔至少一侧表面的锂层。
优选地,所述锂铜复合带中的锂层厚度为1~50μm,例如可以是1μm、2μm、3μm、5μm、10μm、15μm、20μm、25μm、30μm、35μm、40μm、45μm或50μm,但并不仅限于所列举的数值,该数值范围内其他未列举的数值同样适用。
优选地,所述锂铜复合带的面容量不超过负极活性层面容量的25%。
优选地,所述锂铜复合带一侧边缘设置有负极极耳,所述负极极耳的宽度为所在锂铜复合带边长的10~30%,例如可以是10%、12%、14%、16%、18%、20%、22%、24%、26%、28%或30%,但并不仅限于所列举的数值,该数值范围内其他未列举的数值同样适用。
优选地,所述负极极耳的长宽比为1~3,例如可以是1.0、1.2、1.4、1.6、1.8、2.0、2.2、2.4、2.6、2.8或3.0,但并不仅限于所列举的数值,该数值范围内其他未列举的数值同样适用。
优选地,所述锂铜复合带的锂层一侧朝向结构Ⅲ的负极活性层,贴合于负极活性层表面。
本发明提供的制备方法中,将锂铜复合带置于负极活性层非接触电解质隔膜的一侧实现预锂(负极活性层底部预锂),有利于负极充分预锂和预防短路。
作为本发明一种优选的技术方案,所述等静压复合采用温等静压复合或冷等静压复合。
本发明采用温等静压的目的主要为了增加正极活性层、电解质隔膜和负极活性层各层本身的颗粒及他们之间的界面接触,减小界面阻抗,提高电池机械强度,有利于全固态电芯在循环过程中结构稳定和性能发挥,本发明制备的全固态电芯过程可全程在符合要求露点的干燥房流水线式制备,整个过程仅等静压和模切次数少,可大规模连续化生产,对现有设备利用率高,有利于控制成本,促进高性能全固态电池量产。
优选地,所述温等静压复合的温度为40~120℃,例如可以是40℃、50℃、60℃、70℃、80℃、90℃、100℃、110℃或120℃,但并不仅限于所列举的数值,该数值范围内其他未列举的数值同样适用。
优选地,所述温等静压复合的压强为5~700MPa,例如可以是5MPa、50MPa、100MPa、150MPa、200MPa、250MPa、300MPa、350MPa、400MPa、450MPa、500MPa、550MPa、600MPa、650MPa或700MPa,但并不仅限于所列举的数值,该数值范围内其他未列举的数值同样适用。
优选地,所述温等静压复合的保压时间为1~720min,例如可以是1min、50min、100min、150min、200min、250min、300min、350min、400min、450min、500min、550min、600min、650min、700min或720min,但并不仅限于所列举的数值,该数值范围内其他未列举的数值同样适用。
优选地,所述温等静压复合的施压次数为1~3次,例如可以是1次、2次和3次,但并不仅限于所列举的数值,该数值范围内其他未列举的数值同样适用。
优选地,所述冷等静压复合的温度为20~30℃,例如可以是20℃、21℃、22℃、23℃、24℃、25℃、26℃、27℃、28℃、29℃或30℃,但并不仅限于所列举的数值,该数值范围内其他未列举的数值同样适用。
优选地,所述冷等静压复合的压强为5~700MPa,例如可以是5MPa、50MPa、100MPa、150MPa、200MPa、250MPa、300MPa、350MPa、400MPa、450MPa、500MPa、550MPa、600MPa、650MPa或700MPa,但并不仅限于所列举的数值,该数值范围内其他未列举的数值同样适用。
优选地,所述冷等静压复合的保压时间为1~720min,例如可以是1min、50min、100min、150min、200min、250min、300min、350min、400min、450min、500min、550min、600min、650min、700min或720min,但并不仅限于所列举的数值,该数值范围内其他未列举的数值同样适用。
优选地,所述冷等静压复合的施压次数为1~3次,例如可以是1次、2次和3次,但并不仅限于所列举的数值,该数值范围内其他未列举的数值同样适用。
第二方面,本发明提供了一种采用第一方面所述的制备方法制备得到的全固态电芯结构,所述全固态电芯结构包括依次层叠的负极集流体、负极活性层、电解质隔膜、正极活性层和正极集流体。
所述正极活性层外周套设有绝缘圈。
第三方面,本发明提供了一种全固态电芯组,所述全固态电芯组包括依次堆叠的若干全固态电芯结构,所述全固态电芯结构中的正极集流体为双面均设置有碳层的铝箔,所述负极集流体为双面均设置有锂层的铜箔,相邻两个全固态电芯结构之间共用同一正极集流体或同一负极集流体。
所述全固态电芯结构为第二方面所述的全固态电芯结构。
示例性地,本发明提供的全固态电芯结构的制备方法具体包括如下步骤:
(1)取一定质量比分别称取正极活性材料、正极电解质、正极导电剂和正极粘结剂,依次经过球磨混料、研磨和热辊压后得到正极活性层,随后进行模切;将模切后的正极活性层与涂碳铝箔辊压复合,再次模切得到正极片,模切时,正极活性层外缘保留一定宽度的涂碳铝箔,涂碳铝箔的空箔区经模切后形成正极极耳,正极极耳位于正极片的短边上;在正极活性层外周套设绝缘圈,得到结构Ⅰ;
(2)将电解质粘结剂和电解质溶剂混合制胶,得到混合胶液;将混合胶液与硫化物按比例球磨混合制浆,得到电解质浆料,将电解质浆料涂布于基材表面,烘干压实后模切备用;
(3)按照一定质量比称取硅材料、合金材料、碳材料、电解质和导电剂,使用负极溶剂溶解负极粘结剂得到混合胶液,将混合胶液与其他组分搅拌混合匀浆后得到负极浆料,将负极浆料涂布于基材表面,烘干压实后模切备用;
(4)将步骤(2)制备得到的复合层结构叠片于结构Ⅰ表面,复合层结构中的电解质隔膜贴合于正极活性层表面,进行平压或等静压复合后去除基材,将电解质隔膜留于正极活性层表面,得到结构Ⅱ;
(5)将步骤(3)制备得到的复合层结构叠片于结构Ⅱ表面,复合层结构中负极活性层的贴合于电解质隔膜表面,进行平压或等静压复合后去除基材,将负极活性层留于电解质隔膜表面,得到结构Ⅲ;
(6)在结构Ⅲ的负极活性层表面层叠锂铜复合带,锂铜复合带的锂层一侧贴合于负极活性层表面,锂铜复合带的短边一侧设置有负极极耳,经过叠片和封装后得到所述全固态电芯结构。
与现有技术相比,本发明的有益效果为:
本发明采用干法制备正极片,相比湿法工艺,干法工艺制备得到的正极片可拥有更高的面容量及倍率性能,通过组装过程中的预锂能够有效提高电池首效和使用硅负极片电池的循环性能,简化制备流程,提高制造效率和一致性。本发明提供的制备方法可以制备得到一种正极活性层、负极活性层和电解质隔膜层间接近全面积接触的全固态电芯,不仅能防止负极活性层及电解质隔膜边缘掉料,并且大大减小电池内部剪切力的存在,各部件平行面积可抑制膨胀,可有效增加安时级大容量大面积全固态硫化物电芯的循环性能、安全性和成品率,并且采用交叉叠片方式,可连续化生产,成本低,效率高,组装便捷,推进高安全高性能硫化物全固态电池尽早应用。
附图说明
图1为本发明一个具体实施方式提供的全固态电芯的组装工艺流程图;
图2为本发明一个具体实施方式提供的正极活性层的结构示意图;
图3为本发明一个具体实施方式提供的模切后的正极活性层的结构示意图;
图4为本发明一个具体实施方式提供的正极片与涂碳铝箔的辊压复合示意图;
图5为本发明一个具体实施方式提供的模切后的正极片的结构示意图;
图6为本发明一个具体实施方式提供的绝缘圈的结构示意图;
图7为本发明一个具体实施方式提供的锂铜复合带和负极活性层的叠层结构示意图;
图8为本发明一个具体实施方式提供的全固态电芯结构的结构示意图;
图9为本发明一个具体实施方式提供的全固态电芯结构的截面结构示意图;
图10为本发明一个具体实施方式提供的全固态电芯组的结构示意图。
其中,1-铜箔;2-锂层;3-负极活性层;4-电解质隔膜;5-绝缘圈;6-正极活性层;7-铝箔;8-正极极耳;9-负极极耳;10-碳层。
具体实施方式
下面通过具体实施方式来进一步说明本发明的技术方案。
实施例1
本实施例提供了一种全固态电芯结构的制备方法,如图1所示,所述制备方法包括:
(1)取NCM811@Li2TiO3(NCM811正极颗粒表面包覆5nm厚的Li2TiO3)为正极活性物质,Li6PS5Cl为正极电解质,CNT为导电剂,PTFE为正极粘结剂,按照质量85:12:2:1的质量比混合,依次经球磨混料和研磨后热辊压至88μm,得到正极活性层6(如图2所示),模切为90×180mm的薄片(如图3所示);将模切后的正极活性层6与涂碳铝箔7辊压复合(如图4所示),再次模切为93×183mm的薄片得到正极片,模切时,正极活性层6外缘保留1.5mm宽度的涂碳铝箔7(如图5所示),涂碳铝箔7的空箔区经模切后形成正极极耳8,正极极耳8位于正极片的短边上,正极极耳8的尺寸为15×18mm;
(2)将三甲苯和SBS混合制胶,得到混合胶液;将混合胶液与Li6PS5Cl按比例球磨混合制浆,其中SBS与Li6PS5Cl质量比为3:97,得到电解质浆料,将电解质浆料涂布于基材表面,烘干在基材表面形成电解质隔膜4,压实至厚度为25μm,模切为95×185mm的薄片,备用;
(3)将步骤(2)中SBS与Li6PS5Cl质量比调整至1:9,烘干压实至厚度为75μm,模切为绝缘圈5(如图6所示),绝缘圈5的内圈尺寸为90×180mm,外圈尺寸为95×185mm,备用;
(4)取纳米硅、Ag、Li6PS5Cl、CNT和SBR,质量比为60:15:20:2.5:2.5,使用三甲苯溶解SBR得到混合胶液,将混合胶液与其他组分搅拌混合匀浆后得到负极浆料,将负极浆料涂布于基材表面,烘干后在基材表面形成负极活性层3,压实至厚度为45μm,模切为92×182mm的薄片,备用;
(5)将锂铜复合带(铜箔1厚8μm,锂层2厚3μm)模切为92×182mm的薄片并在锂铜复合带的一侧短边预留出负极极耳9,负极极耳9的尺寸为15×18mm;
(6)将步骤(3)中制备得到的绝缘圈5套设于步骤(1)得到的正极片的正极活性层6外周,得到结构Ⅰ;
(7)将步骤(2)制备得到的复合层结构叠片于结构Ⅰ表面,复合层结构中的电解质隔膜4贴合于正极活性层6表面,在200MPa、60℃下进行等静压10min,随后去除基材,将电解质隔膜4留于正极活性层6表面,得到结构Ⅱ;
(8)将步骤(4)制备得到的复合层结构叠片于结构Ⅱ表面,复合层结构中负极活性层3的贴合于电解质隔膜4表面,在200MPa、60℃下进行等静压8min,随后去除基材,将负极活性层3留于电解质隔膜4表面,得到结构Ⅲ(如图7所示);
(9)在结构Ⅲ的负极活性层3表面层叠步骤(5)中的锂铜复合带,锂铜复合带的锂层2一侧贴合于负极活性层3表面,经过叠片和封装后得到所述全固态电芯结构,最终制备得到的全固态电芯结构如图8和图9所示,包括依次层叠的负极集流体、负极活性层3、电解质隔膜4、正极活性层6和正极集流体,正极活性层6外周套设有绝缘圈5。
将制备得到的全固态电芯结构依次堆叠后得到全固态电芯组,如图10所示,所述全固态电芯结构中的正极集流体为双面均设置有碳层10的铝箔7,所述负极集流体为双面均设置有锂层2的铜箔1,相邻两个全固态电芯结构之间共用同一正极集流体或同一负极集流体。
所述全固态电芯组的设计容量为5Ah,将上述全固态电芯组在1MPa下保压,在25℃下,0.1C充放电首效达97.8%;0.33C充放电,200次循环容量保持率为96.8%。
实施例2
本实施例提供了一种全固态电芯结构的制备方法,所述制备方法包括:
(1)取NCM811@LiNbO3(NCM811正极颗粒表面包覆1nm厚的LiNbO3)为正极活性物质,Li10GeP2S12为正极电解质,导电炭黑为导电剂,PTFE为正极粘结剂,按照质量40:40:10:10的质量比混合,依次经球磨混料和研磨后热辊压至88μm,得到正极活性层6,模切为90×180mm的薄片;将模切后的正极活性层6与涂碳铝箔7辊压复合,再次模切为93×183mm的薄片得到正极片,模切时,正极活性层6外缘保留1.5mm宽度的涂碳铝箔7,涂碳铝箔7的空箔区经模切后形成正极极耳8,正极极耳8位于正极片的短边上,正极极耳8的尺寸为15×18mm;
(2)将二氯甲烷和PVDF5130混合制胶,得到混合胶液;将混合胶液与Li10GeP2S12按比例球磨混合制浆,其中PVDF5130与Li10GeP2S12质量比为0.1:99.9,得到电解质浆料,将电解质浆料涂布于基材表面,烘干在基材表面形成电解质隔膜4,压实至厚度为25μm,模切为95×185mm的薄片,备用;
(3)将步骤(2)中PVDF5130与Li10GeP2S12质量比调整至2:8,烘干压实至厚度为80μm,模切为绝缘圈5,绝缘圈5的内圈尺寸为90×180mm,外圈尺寸为95×185mm,备用;
(4)取纳米硅、Li10GeP2S12、PAA和CNT,质量比为80:10:5:5,使用二氯甲烷溶解PAA得到混合胶液,将混合胶液与其他组分搅拌混合匀浆后得到负极浆料,将负极浆料涂布于基材表面,烘干后在基材表面形成负极活性层3,压实至厚度为45μm,模切为92×182mm的薄片,备用;
(5)将锂铜复合带(铜箔1厚8μm,锂层2厚3μm)模切为92×182mm的薄片并在锂铜复合带的一侧短边预留出负极极耳9,负极极耳9的尺寸为15×18mm;
(6)将步骤(3)中制备得到的绝缘圈5套设于步骤(1)得到的正极片的正极活性层6外周,得到结构Ⅰ;
(7)将步骤(2)制备得到的复合层结构叠片于结构Ⅰ表面,复合层结构中的电解质隔膜4贴合于正极活性层6表面,在500MPa、40℃下进行等静压60min,随后去除基材,将电解质隔膜4留于正极活性层6表面,得到结构Ⅱ;
(8)将步骤(4)制备得到的复合层结构叠片于结构Ⅱ表面,复合层结构中负极活性层3的贴合于电解质隔膜4表面,在700MPa、40℃下进行等静压60min,随后去除基材,将负极活性层3留于电解质隔膜4表面,得到结构Ⅲ;
(9)在结构Ⅲ的负极活性层3表面层叠步骤(5)中的锂铜复合带,锂铜复合带的锂层2一侧贴合于负极活性层3表面,经过叠片和封装后得到所述全固态电芯结构。
实施例3
本实施例提供了一种全固态电芯结构的制备方法,所述制备方法包括:
(1)取NCM811@Li2ZrO3(NCM811正极颗粒表面包覆3nm厚的Li2ZrO3)为正极活性物质,Li10SnP2S12为正极电解质,碳纤维为导电剂,PTFE为正极粘结剂,按照质量50:40:5:5的质量比混合,依次经球磨混料和研磨后热辊压至88μm,得到正极活性层6,模切为90×180mm的薄片;将模切后的正极活性层6与涂碳铝箔7辊压复合,再次模切为93×183mm的薄片得到正极片,模切时,正极活性层6外缘保留2mm宽度的涂碳铝箔7,涂碳铝箔7的空箔区经模切后形成正极极耳8,正极极耳8位于正极片的短边上,正极极耳8的尺寸为15×18mm;
(2)将正己烷和PVDF21216混合制胶,得到混合胶液;将混合胶液与Li10SnP2S12按比例球磨混合制浆,其中PVDF21216与Li10SnP2S12质量比为1:99,得到电解质浆料,将电解质浆料涂布于基材表面,烘干在基材表面形成电解质隔膜4,压实至厚度为25μm,模切为95×185mm的薄片,备用;
(3)将步骤(2)中PVDF21216与Li10SnP2S12质量比调整至0.5:9.5,烘干压实至厚度为75μm,模切为绝缘圈5,绝缘圈5的内圈尺寸为90×180mm,外圈尺寸为95×185mm,备用;
(4)取纳米硅、硅氮化物、Li10SnP2S12、导电炭黑和NBR,质量比为50:10:35:2:3,使用四氢呋喃溶解NBR得到混合胶液,将混合胶液与其他组分搅拌混合匀浆后得到负极浆料,将负极浆料涂布于基材表面,烘干后在基材表面形成负极活性层3,压实至厚度为45μm,模切为92×182mm的薄片,备用;
(5)将锂铜复合带(铜箔1厚8μm,锂层2厚3μm)模切为92×182mm的薄片并在锂铜复合带的一侧短边预留出负极极耳9,负极极耳9的尺寸为15×18mm;
(6)将步骤(3)中制备得到的绝缘圈5套设于步骤(1)得到的正极片的正极活性层6外周,得到结构Ⅰ;
(7)将步骤(2)制备得到的复合层结构叠片于结构Ⅰ表面,复合层结构中的电解质隔膜4贴合于正极活性层6表面,在50MPa、100℃下进行等静压180min,随后去除基材,将电解质隔膜4留于正极活性层6表面,得到结构Ⅱ;
(8)将步骤(4)制备得到的复合层结构叠片于结构Ⅱ表面,复合层结构中负极活性层3的贴合于电解质隔膜4表面,在50MPa、120℃下进行等静压180min,随后去除基材,将负极活性层3留于电解质隔膜4表面,得到结构Ⅲ;
(9)在结构Ⅲ的负极活性层3表面层叠步骤(5)中的锂铜复合带,锂铜复合带的锂层2一侧贴合于负极活性层3表面,经过叠片和封装后得到所述全固态电芯结构。
实施例4
本实施例提供了一种全固态电芯结构的制备方法,所述制备方法包括:
(1)取NCM811@LiPO3(NCM811正极颗粒表面包覆7nm厚的LiPO3)为正极活性物质,Li2S-SiS2为正极电解质,石墨烯为导电剂,PTFE为正极粘结剂,按照质量70:20:6:4的质量比混合,依次经球磨混料和研磨后热辊压至88μm,得到正极活性层6,模切为90×180mm的薄片;将模切后的正极活性层6与涂碳铝箔7辊压复合,再次模切为93×183mm的薄片得到正极片,模切时,正极活性层6外缘保留4mm宽度的涂碳铝箔7,涂碳铝箔7的空箔区经模切后形成正极极耳8,正极极耳8位于正极片的短边上,正极极耳8的尺寸为15×18mm;
(2)将甲苯和SEBS混合制胶,得到混合胶液;将混合胶液与Li2S-SiS2按比例球磨混合制浆,其中SEBS与Li2S-SiS2质量比为5:95,得到电解质浆料,将电解质浆料涂布于基材表面,烘干在基材表面形成电解质隔膜4,压实至厚度为25μm,模切为95×185mm的薄片,备用;
(3)将步骤(2)中SEBS与Li2S-SiS2质量比调整至2:8,烘干压实至厚度为85μm,模切为绝缘圈5,绝缘圈5的内圈尺寸为90×180mm,外圈尺寸为95×185mm,备用;
(4)取纳米硅、硅碳化物、Li2S-SiS2、CNT和SBS,质量比为90:3:5:1:1,使用二甲苯溶解SBS得到混合胶液,将混合胶液与其他组分搅拌混合匀浆后得到负极浆料,将负极浆料涂布于基材表面,烘干后在基材表面形成负极活性层3,压实至厚度为45μm,模切为92×182mm的薄片,备用;
(5)将锂铜复合带(铜箔1厚8μm,锂层2厚3μm)模切为92×182mm的薄片并在锂铜复合带的一侧短边预留出负极极耳9,负极极耳9的尺寸为15×18mm;
(6)将步骤(3)中制备得到的绝缘圈5套设于步骤(1)得到的正极片的正极活性层6外周,得到结构Ⅰ;
(7)将步骤(2)制备得到的复合层结构叠片于结构Ⅰ表面,复合层结构中的电解质隔膜4贴合于正极活性层6表面,在100MPa、50℃下进行等静压120min,随后去除基材,将电解质隔膜4留于正极活性层6表面,得到结构Ⅱ;
(8)将步骤(4)制备得到的复合层结构叠片于结构Ⅱ表面,复合层结构中负极活性层3的贴合于电解质隔膜4表面,在120MPa、60℃下进行等静压120min,随后去除基材,将负极活性层3留于电解质隔膜4表面,得到结构Ⅲ;
(9)在结构Ⅲ的负极活性层3表面层叠步骤(5)中的锂铜复合带,锂铜复合带的锂层2一侧贴合于负极活性层3表面,经过叠片和封装后得到所述全固态电芯结构。
实施例5
本实施例提供了一种全固态电芯结构的制备方法,所述制备方法包括:
(1)取NCM811@Al(PO)3(NCM811正极颗粒表面包覆10nm厚的Al(PO)3)为正极活性物质,Li2S-B2S3为正极电解质,导电炭黑为导电剂,PTFE为正极粘结剂,按照质量90:5:2:3的质量比混合,依次经球磨混料和研磨后热辊压至88μm,得到正极活性层6,模切为90×180mm的薄片;将模切后的正极活性层6与涂碳铝箔7辊压复合,再次模切为93×183mm的薄片得到正极片,模切时,正极活性层6外缘保留6mm宽度的涂碳铝箔7,涂碳铝箔7的空箔区经模切后形成正极极耳8,正极极耳8位于正极片的短边上,正极极耳8的尺寸为15×18mm;
(2)将环己酮和NBR混合制胶,得到混合胶液;将混合胶液与Li2S-B2S3按比例球磨混合制浆,其中NBR与Li2S-B2S3质量比为6:94,得到电解质浆料,将电解质浆料涂布于基材表面,烘干在基材表面形成电解质隔膜4,压实至厚度为25μm,模切为95×185mm的薄片,备用;
(3)将步骤(2)中NBR与Li2S-B2S3质量比调整至3:7,烘干压实至厚度为85μm,模切为绝缘圈5,绝缘圈5的内圈尺寸为90×180mm,外圈尺寸为95×185mm,备用;
(4)取纳米硅、硅氧化物、Li2S-B2S3、CNT和PEO,质量比为70:18:10:1:1,使用甲基甲酰胺溶解PEO得到混合胶液,将混合胶液与其他组分搅拌混合匀浆后得到负极浆料,将负极浆料涂布于基材表面,烘干后在基材表面形成负极活性层3,压实至厚度为45μm,模切为92×182mm的薄片,备用;
(5)将锂铜复合带(铜箔1厚8μm,锂层2厚3μm)模切为92×182mm的薄片并在锂铜复合带的一侧短边预留出负极极耳9,负极极耳9的尺寸为15×18mm;
(6)将步骤(3)中制备得到的绝缘圈5套设于步骤(1)得到的正极片的正极活性层6外周,得到结构Ⅰ;
(7)将步骤(2)制备得到的复合层结构叠片于结构Ⅰ表面,复合层结构中的电解质隔膜4贴合于正极活性层6表面,在300MPa、80℃下进行等静压100min,随后去除基材,将电解质隔膜4留于正极活性层6表面,得到结构Ⅱ;
(8)将步骤(4)制备得到的复合层结构叠片于结构Ⅱ表面,复合层结构中负极活性层3的贴合于电解质隔膜4表面,在300MPa、80℃下进行等静压80min,随后去除基材,将负极活性层3留于电解质隔膜4表面,得到结构Ⅲ;
(9)在结构Ⅲ的负极活性层3表面层叠步骤(5)中的锂铜复合带,锂铜复合带的锂层2一侧贴合于负极活性层3表面,经过叠片和封装后得到所述全固态电芯结构。
对比例1
本对比例提供了一种全固态电芯的制备方法,所述制备方法与实施例1的区别在于:
步骤(1)采用了湿法涂布工艺制备得到正极活性层6,正极集流体的各边边长与正极活性层6相同,且未在正极活性层6外周套设绝缘圈5。其余操作步骤及工艺参数与实施例1完全相同,最终
对制备得到的全固态电芯组进行电性能测试,全固态电芯组在25℃下,0.1C充放电首效78%;0.33C充放电,28次循环容量保持率为88.6%。第29圈短路,将全固态电芯组拆解后,负极活性层3-电解质隔膜4大于正极片的部分粉化掉料。
申请人声明,以上所述仅为本发明的具体实施方式,但本发明的保护范围并不局限于此,所属技术领域的技术人员应该明了,任何属于本技术领域的技术人员在本发明揭露的技术范围内,可轻易想到的变化或替换,均落在本发明的保护范围和公开范围之内。
本文用于企业家、创业者技术爱好者查询,结果仅供参考。