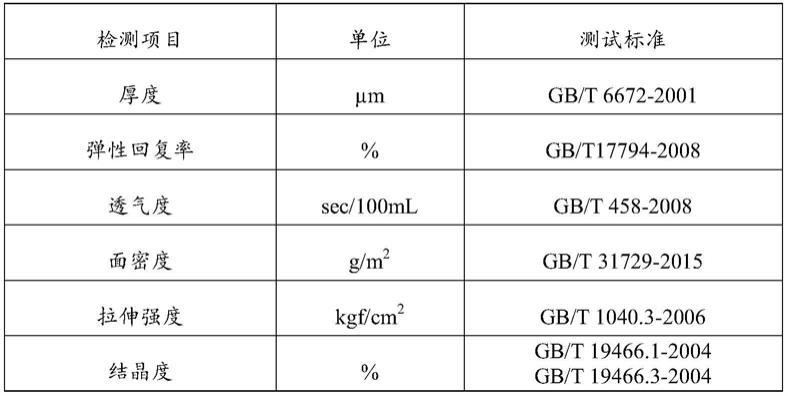
1.本技术涉及电池隔膜领域,特别是涉及一种聚丙烯微孔膜的制备方法、聚丙烯微孔膜及其应用。
背景技术:
2.电池隔膜是锂离子电池中阻隔正负极、防止短路的关键材料。干法拉伸隔膜是目前隔膜市场的主流工艺方法之一。干法拉伸和较其它工艺相比,具有安全性高、制备过程环保无污染等优点。
3.随着近年来隔膜技术的不断提升,隔膜物理性能良率得到良好的改善。隔膜的性能决定了电池的界面结构、内阻等,直接影响到电池的容量、循环以及安全性能等特性。性能优异的隔膜对提高电池的综合性能具有重要的作用。聚丙烯微孔膜具有耐高温、刚性好、高安全性等特点。目前聚丙烯微孔膜,普遍采用干法拉伸工艺制备。聚丙烯微孔膜的其中一个技术难点就是造孔。
4.研究显示,聚丙烯微孔膜的成孔原理主要是,挤出时在拉伸应力下形成片晶结构,在后续的退火、拉伸过程中,利用结晶成长、拉伸成孔。为了提高成孔的均匀性,通常会在聚丙烯原材料中添加部分成核添加剂或晶型改性剂;或者,优化退火和拉伸条件,改善结晶情况,从而起到改善微孔的作用。
5.虽然,现有的研究显示,可以通过高温退火使基膜取向片晶更完善;但是,片晶排列不规整问题仍然存在。因此,如何解决聚丙烯微孔膜片晶排列不规则导致的成孔问题仍然是本领域的研究重点和难点。
技术实现要素:
6.本技术的目的是提供一种改进的聚丙烯微孔膜的制备方法,其制备的聚丙烯微孔膜,以及聚丙烯微孔膜的应用。
7.为了实现上述目的,本技术采用了以下技术方案:
8.本技术的一方面公开了聚丙烯微孔膜的制备方法,包括将聚丙烯颗粒投入挤出系统中,熔融挤出,并在100-110℃的铸片温度下流延成膜,获得流延膜,对流延膜进行后续处理,获得聚丙烯微孔膜。
9.需要说明的是,本技术的制备方法,在较高温度下进行铸片,形成流延膜,使得形成的片晶结构排列更规则,晶体骨架更匀称,提高了流延膜的结晶度;从而,使得制备的聚丙烯微孔膜具有更均匀、且规整排列的微孔结构。
10.还需要说明的是,本技术研究发现100-110℃的铸片温度能够使流延膜具有较高的结晶度及匀称的晶体骨架;铸片温度太低,例如低于100℃,则以上效果不明显;铸片温度太高,例如高于110℃,则会导致晶体坍陷导致成孔一致性变差。因此,本技术采用100-110℃的铸片温度流延成膜。
11.本技术的一种实现方式中,聚丙烯颗粒包括a组分聚丙烯颗粒和b组分聚丙烯颗
粒;a组分聚丙烯颗粒的分子量分布为3-5,平均链长240-260nm;b组分聚丙烯颗粒的分子量分布为5-7,平均链长200-220nm;因此,本技术的制备方法,具体包括,将a组分聚丙烯颗粒投入挤出系统中,使用挤出温度200-220℃,将b组分聚丙烯颗粒投入另一挤出系统中,使用挤出温度220-240℃,共挤出双层或多层结构的复合膜,并在100-110℃的铸片温度下进行流延成膜,获得流延膜;然后,对流延膜进行退火处理,然后进行拉伸、热定型,即获得本技术的聚丙烯微孔膜。
12.其中,双层或多层结构的复合膜,具体的,可以是a组分聚丙烯颗粒层 b组分聚丙烯颗粒层形成复合膜,或a组分聚丙烯颗粒层 b组分聚丙烯颗粒层 a组分聚丙烯颗粒层形成复合膜,或b组分聚丙烯颗粒层 a组分聚丙烯颗粒层 b组分聚丙烯颗粒层形成复合膜,或a组分聚丙烯颗粒层 b组分聚丙烯颗粒层 a组分聚丙烯颗粒层 b组分聚丙烯颗粒层形成复合膜,或其他形式的层叠复合,在此不作具体限定。
13.本技术的一种实现方式中,退火处理的温度为140-150℃,退火时间为15-18h。
14.优选的,退火处理的温度为147-150℃,退火时间为15-18h。
15.本技术的一种实现方式中,在进行退火处理后,还进行了高温热处理,然后再进行拉伸、热定型;具体的,热处理的温度为150-155℃,处理时间为15min。
16.需要说明的是,本技术通过高温进行热处理,有利于结晶,利于后续的拉伸成孔,提高成孔均匀性和一致性。
17.本技术的一种实现方式中,拉伸包括冷拉和热拉;冷拉的温度为45-55℃,冷拉倍率为15-25%;热拉的温度为130-140℃,热拉比为200-230%。
18.本技术的一种实现方式中,热定型的温度为155-165℃。
19.本技术的另一面公开了一种采用本技术的制备方法制备的聚丙烯微孔膜。
20.需要说明的是,本技术的聚丙烯微孔膜,由于采用本技术的制备方法制备,因此,具有微孔均匀性好、一致性好等优点,并且,微孔排列规整。
21.本技术的再一面公开了本技术的聚丙烯微孔膜在电池隔膜中的应用。
22.本技术的再一面公开了一种采用本技术的聚丙烯微孔膜的电池。
23.由于采用以上技术方案,本技术的有益效果在于:
24.本技术的制备方法,创造性的在较高温度下进行的铸片,通过高温铸片提高流延膜的结晶度和晶体骨架均匀性,使得片晶结构更规则;从而使得制备的聚丙烯微孔膜具有更均匀、且规整排列的微孔结构。
具体实施方式
25.本技术研究发现,铸片温度与结晶方向呈正相关,即使用较高的铸片温度,能够利于结晶方向更规则、均匀,使制备的聚丙烯微孔膜具有较高的结晶度及匀称的晶体骨架。但是,进一步的研究发现,铸片温度过高又会导致晶体坍陷,从而导致成孔一致性变差。
26.因此,基于以上研究和认识,本技术创造性的提出了一种改进的聚丙烯微孔膜的制备方法,包括将聚丙烯颗粒投入挤出系统中,熔融挤出,并在100-110℃的铸片温度下流延成膜,获得流延膜,对流延膜进行后续处理,获得聚丙烯微孔膜。进一步的,聚丙烯颗粒包括a组分聚丙烯颗粒和b组分聚丙烯颗粒;a组分聚丙烯颗粒的分子量分布为3-5,平均链长240-260nm;b组分聚丙烯颗粒的分子量分布为5-7,平均链长200-220nm;将a组分聚丙烯颗
粒投入挤出系统中,使用挤出温度200-220℃,将b组分聚丙烯颗粒投入另一挤出系统中,使用挤出温度220-240℃,共挤出双层或多层结构的复合膜,并在100-110℃的铸片温度下流延成膜,获得流延膜;对流延膜进行退火处理,然后进行拉伸、热定型,即获得聚丙烯微孔膜。
27.本技术制备方法制备的聚丙烯微孔膜,具有孔径大小、分布均匀,且排列规整的优点。
28.下面通过具体实施例对本技术作进一步详细说明。以下实施例仅对本技术进行进一步说明,不应理解为对本技术的限制。
29.实施例一
30.本例采用分子量分布为3-5、平均链长240-260nm的a组分聚丙烯颗粒,和分子量分布为5-7、平均链长200-220nm的b组分聚丙烯颗粒,两种聚丙烯颗粒制备三层结构的聚丙烯微孔膜。具体如下:
31.1)流延膜的制备:将a组分聚丙烯颗粒投入至生产a挤出系统,使用挤出温度220℃,将b组分聚丙烯颗粒投入至生产b挤出系统,使用挤出温度240℃,调整排列顺序,获得b组分聚丙烯颗粒层 a组分聚丙烯颗粒层 b组分聚丙烯颗粒层的三层共挤出复合膜,并在铸片温度100℃下,以70m/min的生产速度,收取18.2微米流延膜。
32.2)退火过程:将流延膜放进烘烤箱进行退火处理,退火温度140℃,退火时间18h。
33.3)热处理复合过程:将流延膜在复合设备上进行热处理复合,热处理的温度为155℃,处理时间为15min,复合速度50m/min。
34.4)拉伸成型:将复合膜经过冷拉温度45℃,冷拉伸倍率15%,热拉温度130℃,热拉伸比为200%,回缩率25%,定型温度155℃,得到三层共挤高结晶的聚丙烯微孔膜。
35.对本例得到的三层共挤高结晶的聚丙烯微孔膜进行如下检测:流延产品厚度测试、流延产品弹性回复率测试、拉伸产品厚度测试、面密度测试、孔隙率测试、透气度测试、拉伸强度测试及结晶度测试。各测试项目及测试标准如表1所示。
36.表1测试项目及参考标准
[0037][0038]
孔隙率的测试方法如下:将膜完全浸润在电解液中1h后,取出,用吸液纸吸干隔膜表面的电解液,进行称重,孔隙率p的计算公式为:p=(ρ
c-ρe)/ρc*100%。ρc为隔膜浸润在电解液之后的密度,ρe为隔膜没有浸润电解液时的密度。
[0039]
其中,电解液由lipf6、ec(碳酸乙烯酯)、emc(碳酸甲乙酯)、dmc(碳酸二甲酯)组成,ec、emc、dmc为溶剂。电解液中lipf6的浓度为1mol/l,按体积计,ec:emc:dmc=1:1:1。
[0040]
本例的聚丙烯微孔膜的各项测试结果如表2所示。
[0041]
实施例二
[0042]
采用实施例一相同的a组分聚丙烯颗粒和b组分聚丙烯颗粒制备相同的三层结构的聚丙烯微孔膜。所不同的是,本例的具体参数相对于实施例一有所调整,具体如下:
[0043]
1)流延膜的制备:将a组分聚丙烯颗粒投入至生产a挤出系统,使用挤出温度210℃,将b组分聚丙烯颗粒投入至生产b挤出系统,使用挤出温度230℃,采用实施例一相同的方式三层共挤出复合膜,铸片温度110℃,生产速度70m/min,收取18.2微米流延膜。
[0044]
2)退火过程:将流延膜放进烘烤箱进行退火处理,退火温度150℃,退火时间15h。
[0045]
3)热处理复合过程:将流延膜在复合设备上进行热处理复合,热处理的温度为150℃,处理时间为15min,复合速度50m/min。
[0046]
4)拉伸成型:将复合膜经过冷拉温度55℃,冷拉伸25%,热拉温度140℃,热拉伸230%,回缩率25%,定型温度165℃,得到三层共挤高结晶的聚丙烯微孔膜。
[0047]
采用实施例一相同的方法对本例的聚丙烯微孔膜进行测试,结果如表2所示。
[0048]
实施例三
[0049]
采用实施例一相同的a组分聚丙烯颗粒和b组分聚丙烯颗粒制备相同的三层结构的聚丙烯微孔膜。所不同的是,本例的具体参数相对于实施例一有所调整,具体如下:
[0050]
1)流延膜的制备:将a组分聚丙烯颗粒投入至生产a挤出系统,使用挤出温度200℃,将b组分聚丙烯颗粒投入至生产b挤出系统,使用挤出温度220℃,采用实施例一相同的方式三层共挤出复合膜,铸片温度105℃,生产速度70m/min,收取18.2微米流延膜。
[0051]
2)退火过程:将流延膜放进烘烤箱进行退火处理,退火温度147℃,退火时间15h。
[0052]
3)热处理复合过程:将流延膜在复合设备上进行热处理复合,热处理的温度为152℃,处理时间为15min,复合速度50m/min。
[0053]
4)拉伸成型:将复合膜经过冷拉温度48℃,冷拉伸20%,热拉温度135℃,热拉伸220%,回缩率25%,定型温度158℃,得到三层共挤高结晶的聚丙烯微孔膜。
[0054]
采用实施例一相同的方法对本例的聚丙烯微孔膜进行测试,结果如表2所示。
[0055]
对比例一
[0056]
采用实施例一相同的a组分聚丙烯颗粒和b组分聚丙烯颗粒制备相同的三层结构的聚丙烯微孔膜。所不同的是,本例的具体参数相对于实施例一有所调整,具体如下:
[0057]
1)流延膜的制备:将a组分聚丙烯颗粒投入至生产a挤出系统,使用挤出温度220℃,将b组分聚丙烯颗粒投入至生产b挤出系统,使用挤出温度240℃,采用实施例一相同的方式三层共挤出复合膜,铸片温度95℃,生产速度70m/min,收取18.2微米流延膜。
[0058]
2)退火过程:将流延膜放进烘烤箱进行退火处理,退火温度140℃,退火时间18h。
[0059]
3)热处理复合过程:将流延膜在复合设备上进行热处理复合,热处理的温度为155℃,处理时间为15min,复合速度50m/min。
[0060]
4)拉伸成型:将复合膜经过冷拉温度45℃,冷拉伸15%,热拉温度130℃,热拉伸200%,回缩率25%,定型温度155℃,得到三层共挤高结晶的聚丙烯微孔膜。
[0061]
采用实施例一相同的方法对本例的聚丙烯微孔膜进行测试,结果如表2所示。
[0062]
对比例二
[0063]
采用实施例一相同的a组分聚丙烯颗粒和b组分聚丙烯颗粒制备相同的三层结构的聚丙烯微孔膜。所不同的是,本例的具体参数相对于实施例一有所调整,具体如下:
[0064]
1)流延膜的制备:将a组分聚丙烯颗粒投入至生产a挤出系统,使用挤出温度220℃,将b组分聚丙烯颗粒投入至生产b挤出系统,使用挤出温度240℃,采用实施例一相同的方式三层共挤出复合膜,铸片温度115℃,生产速度70m/min,收取18.2微米流延膜。
[0065]
2)退火过程:将流延膜放进烘烤箱进行退火处理,退火温度140℃,退火时间18h。
[0066]
3)热处理复合过程:将流延膜在复合设备上进行热处理复合,热处理的温度为155℃,处理时间为15min,复合速度50m/min。
[0067]
4)拉伸成型:将复合膜经过冷拉温度45℃,冷拉伸15%,热拉温度130℃,热拉伸200%,回缩率25%,定型温度155℃,得到三层共挤高结晶的聚丙烯微孔膜。
[0068]
采用实施例一相同的方法对本例的聚丙烯微孔膜进行测试,结果如表2所示。
[0069]
表2聚丙烯微孔膜性能测试结果
[0070]
检测项目实施例一实施例二实施例三对比例一对比例二流延厚度(μm)18.218.218.218.218.2弹性回复率(%)92.292.292.289.792.4拉伸厚度(μm)16.216.116.015.816.3面密度(g/m2)7.647.627.647.547.72孔隙率(%)49.850.250.448.349.2透气度(sec/100ml)150.2148.8149.6169.8143.6拉伸强度(kgf/cm2)1726.51722.31698.41700.31623.1结晶度(%)56.255.355.550.649.6
[0071]
表2的结果显示,实施例一至实施例三采用设计的工艺配方参数可制备出高结晶度聚丙烯微孔膜,结晶度都在55%以上。同时三个实施例的聚丙烯微孔膜产品都具有优异的力学性能和产品均匀性。相对于而言,对比例一制备的聚丙烯微孔膜产品虽然具有较号的力学性能,但弹性回复率较低,孔隙率偏低,透气度较高,说明聚丙烯微孔膜的成孔性能较差。对比二制备的聚丙烯微孔膜虽然具有较好的成孔性能,但结晶度下降明显。
[0072]
进一步试验分析认为,造成以上结果的原因是铸片温度与结晶方向呈正相关,在较高的铸片温度下,更利于结晶方向规则、均匀,使得制备的聚丙烯微孔膜具有较高的结晶度和匀称的晶体骨架;而铸片温度太高又会导致晶体坍陷,成孔一致性变差。因此,优选的铸片温度为100-110℃;铸片温度低于100℃,以上效果不明显;铸片温度高于110℃,会导致晶体坍陷、成孔一致性差。
[0073]
另外,在退火处理方面,高温、长时间的退火利于结晶,能够提高成孔均匀性和一致性;进一步试验研究显示,温度为140-150℃,退火时间为15-18h都能够达到以上效果;并且,退火温度为147-150℃时效果更佳。
[0074]
以上内容是结合具体的实施方式对本技术所作的进一步详细说明,不能认定本技术的具体实施只局限于这些说明。对于本技术所属技术领域的普通技术人员来说,在不脱离本技术构思的前提下,还可以做出若干简单推演或替换,都应当视为属于本技术的保护范围。
再多了解一些
本文用于企业家、创业者技术爱好者查询,结果仅供参考。