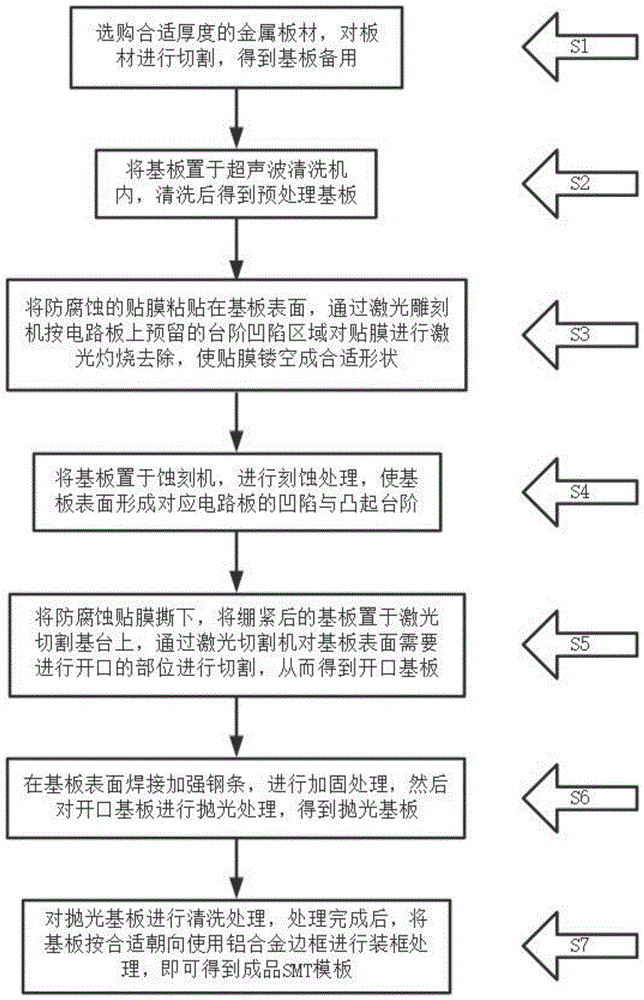
本发明涉及SMT模板技术领域,尤其涉及一种SMT模板的制备方法。
背景技术
SMT模板的主要功能是帮助锡膏的沉积,能够通过模板上的开口将准确数量的材料转移到PCB板上准确的位置,以便后续的加工,模板上的凹陷或是凸起台阶能够增大或减少锡膏沉积在PCB板上的量,因此大部分模板表面会在预定位置设有凹陷或凸起台阶,但模板在进行表面台阶的加工过程中,往往是通过在钢制基板表面形成照像制版,将图形转移到钢板的两面,两面图像转移并用工艺销钉精确定位,通过图形曝光显影,形成抗蚀膜图形,然后将两面带有抗蚀膜图形的钢板放入化学液体中腐蚀成形,这一过程操作繁琐,且需要花费较长时间,难以达到较好的加工使用效果。
中国专利号CN104760404A公开了一种SMT印刷模板的生产工艺,该制备工艺包括化学腐蚀、激光切割、电铸、混合和模板成形,所述化学腐蚀工艺是用照像制版将图形转移到钢板的两面,两面图像转移并用工艺销钉精确定位,图形曝光显影,更重要的是不锈钢丝网与非金属丝网相比,热膨胀系数与不锈钢片及铝合金框非常匹配,特别适合日益普及的模板自动清洗机在清洗过程中的高温/高压及超声波的冲击,但采用图形曝光显影,形成抗蚀膜图形的方式,操作较为繁琐,需要进行改进。
技术实现要素:
本发明的目的是为了解决现有技术中存在的缺点,而提出的一种SMT模板的制备方法。
为了实现上述目的,本发明采用了如下技术方案:一种SMT模板的制备方法,包括以下步骤:
S1:选购合适厚度的金属板材,并使用切割机对板材进行切割,使其形成合适尺寸形状的金属薄板,即可得到基板备用;
S2:将基板置于超声波清洗机内,进行超声波清洗,清洗后得到预处理基板;
S3:将防腐蚀的贴膜粘贴在基板表面,并将带有贴膜的基板置于激光雕刻机下方,通过激光雕刻机按电路板上预留的台阶凹陷区域对贴膜进行激光灼烧去除,使贴膜镂空成合适形状,且不对基板造成伤害;
S4:然后将基板置于蚀刻机内,进行刻蚀处理,对基板表面贴膜被镂空的部位进行刻蚀,使基板表面形成对应电路板的凹陷与凸起台阶,凹陷与凸起台阶厚度为0.03-0.08mm;
S5:然后将基板表面的防腐蚀贴膜撕下,并对基板进行绷紧处理,然后将绷紧后的基板置于激光切割基台上,通过激光切割机对基板表面需要进行开口的部位进行切割,从而得到开口基板;
S6:在基板表面位于开口外侧以及蚀刻台阶外侧合适位置处焊接加强钢条,进行加固处理,然后通过抛光机对开口基板进行抛光处理,处理完成后,得到抛光基板;
S7:使用超声波清洗机对抛光基板进行清洗处理,处理完成后,将基板按合适朝向使用铝合金边框进行装框处理,即可得到成品SMT模板。
为了使基板具有良好强度,本发明的改进有,所述步骤S1中金属板材的材质为镍、黄铜和不锈钢中的一种,优选材质为不锈钢。
为了使基板易于加工,本发明的改进有,所述步骤S1中金属板材厚度为0.2-0.3mm。
为了使开口能够易于释放锡膏,本发明的改进有,所述步骤S5中开口形状为矩形、方形和圆形中的一种。
为了使锡膏能够易于移出开口,本发明的改进有,所述步骤S5中开口壁种类为垂直开口或喇叭开口中的一种。
为了对开口达到较好的抛光效果,本发明的改进有,所述步骤S6中使用的抛光机为研磨流体抛光机。
为了达到较好的清洗效果,本发明的改进有,所述步骤S2与S7超声波清洗过程中,需要加入清洗剂进行清洗,清洗完成后,需使用清水冲洗3-5次。
为了达到较好的加强效果,本发明的改进有,所述步骤S6中焊接的加强钢条厚度为0.3-0.4mm。
与现有技术相比,本发明的优点和积极效果在于,
本发明中,通过对基板进行切割,使其形成合适的尺寸形状,然后进行超声波清洗,清完成后在基板表面粘贴防腐蚀贴膜,然后通过激光雕刻机,按预形状将贴膜进行激光灼烧去除,使贴膜镂空成合适形状,然后即可通过蚀刻机对基板进行蚀刻处理,使基板表面形成凹陷与凸起台阶,这一过程操作简单,同时节省了操作所需的时间,易于整个模板的生产制造,然后即可将贴膜撕下,并通过激光切割机进行切割开口,然后通过焊接加强钢条,防止基板在后续使用过程中轻易变形,并对基板进行抛光处理,使锡膏能够更加容易的从开口释放,以便达到较好的使用效果。
附图说明
图1为本发明提出一种SMT模板的制备方法的流程图。
具体实施方式
为了能够更清楚地理解本发明的上述目的、特征和优点,下面结合附图和实施例对本发明做进一步说明。需要说明的是,在不冲突的情况下,本申请的实施例及实施例中的特征可以相互组合。
在本发明的描述中,需要理解的是,术语“长度”、“宽度”、“上”、“下”、“前”、“后”、“左”、“右”、“竖直”、“水平”、“顶”、“底”“内”、“外”等指示的方位或位置关系为基于附图所示的方位或位置关系,仅是为了便于描述本发明和简化描述,而不是指示或暗示所指的装置或元件必须具有特定的方位、以特定的方位构造和操作,因此不能理解为对本发明的限制。此外,在本发明的描述中,“多个”的含义是两个或两个以上,除非另有明确具体的限定。
请参阅图1,本发明提供一种SMT模板的制备方法,包括以下步骤:
S1:选购合适厚度的金属板材,并使用切割机对板材进行切割,使其形成合适尺寸形状的金属薄板,即可得到基板备用;
S2:将基板置于超声波清洗机内,进行超声波清洗,清洗后得到预处理基板;
S3:将防腐蚀的贴膜粘贴在基板表面,并将带有贴膜的基板置于激光雕刻机下方,通过激光雕刻机按电路板上预留的台阶凹陷区域对贴膜进行激光灼烧去除,使贴膜镂空成合适形状,且不对基板造成伤害;
S4:然后将基板置于蚀刻机内,进行刻蚀处理,对基板表面贴膜被镂空的部位进行刻蚀,使基板表面形成对应电路板的凹陷与凸起台阶,凹陷与凸起台阶厚度为0.03-0.08mm;
S5:然后将基板表面的防腐蚀贴膜撕下,并对基板进行绷紧处理,然后将绷紧后的基板置于激光切割基台上,通过激光切割机对基板表面需要进行开口的部位进行切割,从而得到开口基板;
S6:在基板表面位于开口外侧以及蚀刻台阶外侧合适位置处焊接加强钢条,进行加固处理,然后通过抛光机对开口基板进行抛光处理,处理完成后,得到抛光基板;
S7:使用超声波清洗机对抛光基板进行清洗处理,处理完成后,将基板按合适朝向使用铝合金边框进行装框处理,即可得到成品SMT模板。
步骤S1中金属板材的材质为镍、黄铜和不锈钢中的一种,优选材质为不锈钢,镍、黄铜和不锈钢均具有良好的强度,但不锈钢模板在硬度、承受应力、蚀刻质量、印刷效果和使用寿命等方面都优于黄铜模板,而镍电铸模价格最高,因此,优选使用不锈钢模板,步骤S1中金属板材厚度为0.2-0.3mm,步骤S5中开口形状为矩形、方形和圆形中的一种,步骤S5中开口形状为矩形、方形和圆形中的一种,矩形开口比方形和圆形开口具有更好的脱模效率,开口垂直或喇叭口向下时焊膏释放顺利,以便达到较好的使用效果,步骤S6中使用的抛光机为研磨流体抛光机,研磨流体抛光机能够对开口起到来良好的抛光效果,使焊膏释放顺利,以便达到较好的使用效果。
步骤S2与S7超声波清洗过程中,需要加入清洗剂进行清洗,清洗完成后,需使用清水冲洗3-5次,清洗剂能够去除基板表面的油质,以便基板的后续加工,步骤S6中焊接的加强钢条厚度为0.3-0.4mm,加强钢条能够提高基板的强度,防止基板轻易变形,使基板能够具有较长使用寿命。
实施例一
一种SMT模板的制备方法,包括以下步骤:
S1:选购合适厚度的金属板材,金属板材的材质为镍,金属板材厚度为0.25mm,并使用切割机对板材进行切割,使其形成合适尺寸形状的金属薄板,即可得到基板备用;
S2:将基板置于超声波清洗机内,进行超声波清洗,清洗过程中,加入清洗剂,清洗完成后,使用清水冲洗4次,清洗后得到预处理基板;
S3:将防腐蚀的贴膜粘贴在基板表面,并将带有贴膜的基板置于激光雕刻机下方,通过激光雕刻机按电路板上预留的台阶凹陷区域对贴膜进行激光灼烧去除,使贴膜镂空成合适形状,且不对基板造成伤害;
S4:然后将基板置于蚀刻机内,进行刻蚀处理,对基板表面贴膜被镂空的部位进行刻蚀,使基板表面形成对应电路板的凹陷与凸起台阶,凹陷与凸起台阶厚度为0.05mm;
S5:然后将基板表面的防腐蚀贴膜撕下,并对基板进行绷紧处理,然后将绷紧后的基板置于激光切割基台上,通过激光切割机对基板表面需要进行开口的部位进行切割,开口形状为矩形,开口壁种类为垂直开口,从而得到开口基板;
S6:在基板表面位于开口外侧以及蚀刻台阶外侧合适位置处焊接加强钢条,进行加固处理,加强钢条厚度为0.35mm,然后通过研磨流体抛光机对开口基板进行抛光处理,处理完成后,得到抛光基板;
S7:使用超声波清洗机对抛光基板进行清洗处理,清洗过程中,加入清洗剂,清洗完成后,使用清水冲洗3次,处理完成后,将基板按合适朝向使用铝合金边框进行装框处理,即可得到成品SMT模板。
实施例二
一种SMT模板的制备方法,包括以下步骤:
S1:选购合适厚度的金属板材,金属板材的材质为黄铜,金属板材厚度为0.22mm,并使用切割机对板材进行切割,使其形成合适尺寸形状的金属薄板,即可得到基板备用;
S2:将基板置于超声波清洗机内,进行超声波清洗,清洗过程中,加入清洗剂,清洗完成后,使用清水冲洗3次,清洗后得到预处理基板;
S3:将防腐蚀的贴膜粘贴在基板表面,并将带有贴膜的基板置于激光雕刻机下方,通过激光雕刻机按电路板上预留的台阶凹陷区域对贴膜进行激光灼烧去除,使贴膜镂空成合适形状,且不对基板造成伤害;
S4:然后将基板置于蚀刻机内,进行刻蚀处理,对基板表面贴膜被镂空的部位进行刻蚀,使基板表面形成对应电路板的凹陷与凸起台阶,凹陷与凸起台阶厚度为0.04mm;
S5:然后将基板表面的防腐蚀贴膜撕下,并对基板进行绷紧处理,然后将绷紧后的基板置于激光切割基台上,通过激光切割机对基板表面需要进行开口的部位进行切割,开口形状为方形,开口壁种类为垂直开口,从而得到开口基板;
S6:在基板表面位于开口外侧以及蚀刻台阶外侧合适位置处焊接加强钢条,进行加固处理,加强钢条厚度为0.36mm,然后通过研磨流体抛光机对开口基板进行抛光处理,处理完成后,得到抛光基板;
S7:使用超声波清洗机对抛光基板进行清洗处理,清洗过程中,加入清洗剂,清洗完成后,使用清水冲洗4次,处理完成后,将基板按合适朝向使用铝合金边框进行装框处理,即可得到成品SMT模板。
实施例三
一种SMT模板的制备方法,包括以下步骤:
S1:选购合适厚度的金属板材,金属板材的材质为不锈钢,金属板材厚度为0.3.mm,并使用切割机对板材进行切割,使其形成合适尺寸形状的金属薄板,即可得到基板备用;
S2:将基板置于超声波清洗机内,进行超声波清洗,清洗过程中,加入清洗剂,清洗完成后,使用清水冲洗5次,清洗后得到预处理基板;
S3:将防腐蚀的贴膜粘贴在基板表面,并将带有贴膜的基板置于激光雕刻机下方,通过激光雕刻机按电路板上预留的台阶凹陷区域对贴膜进行激光灼烧去除,使贴膜镂空成合适形状,且不对基板造成伤害;
S4:然后将基板置于蚀刻机内,进行刻蚀处理,对基板表面贴膜被镂空的部位进行刻蚀,使基板表面形成对应电路板的凹陷与凸起台阶,凹陷与凸起台阶厚度为0.06mm;
S5:然后将基板表面的防腐蚀贴膜撕下,并对基板进行绷紧处理,然后将绷紧后的基板置于激光切割基台上,通过激光切割机对基板表面需要进行开口的部位进行切割,开口形状为圆形,开口壁种类为垂直,从而得到开口基板;
S6:在基板表面位于开口外侧以及蚀刻台阶外侧合适位置处焊接加强钢条,进行加固处理,加强钢条厚度为0.3mm,然后通过研磨流体抛光机对开口基板进行抛光处理,处理完成后,得到抛光基板;
S7:使用超声波清洗机对抛光基板进行清洗处理,清洗过程中,加入清洗剂,清洗完成后,使用清水冲洗4次,处理完成后,将基板按合适朝向使用铝合金边框进行装框处理,即可得到成品SMT模板。
本发明,通过对基板进行切割,使其形成合适的尺寸形状,然后进行超声波清洗,清完成后在基板表面粘贴防腐蚀贴膜,然后通过激光雕刻机,按预形状将贴膜进行激光灼烧去除,使贴膜镂空成合适形状,然后即可通过蚀刻机对基板进行蚀刻处理,使基板表面形成凹陷与凸起台阶,这一过程操作简单,同时节省了操作所需的时间,易于整个模板的生产制造,然后即可将贴膜撕下,并通过激光切割机进行切割开口,然后通过焊接加强钢条,防止基板在后续使用过程中轻易变形,并对基板进行抛光处理,使锡膏能够更加容易的从开口释放,以便达到较好的使用效果。
以上,仅是本发明的较佳实施例而已,并非是对本发明作其它形式的限制,任何熟悉本专业的技术人员可能利用上述揭示的技术内容加以变更或改型为等同变化的等效实施例应用于其它领域,但是凡是未脱离本发明技术方案内容,依据本发明的技术实质对以上实施例所作的任何简单修改、等同变化与改型,仍属于本发明技术方案的保护范围。
本文用于企业家、创业者技术爱好者查询,结果仅供参考。